Top 30 Assembly Person Interview Questions and Answers [Updated 2025]
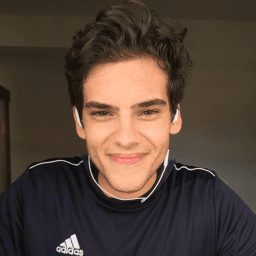
Andre Mendes
•
March 30, 2025
Navigating the job market as an Assembly Person can be challenging, but preparation is key to standing out. In this post, we spotlight the most common interview questions tailored for the Assembly Person role, providing not just example answers but also valuable tips on how to respond effectively. Dive in to enhance your interview skills and boost your confidence for your next career opportunity.
Download Assembly Person Interview Questions in PDF
To make your preparation even more convenient, we've compiled all these top Assembly Personinterview questions and answers into a handy PDF.
Click the button below to download the PDF and have easy access to these essential questions anytime, anywhere:
List of Assembly Person Interview Questions
Behavioral Interview Questions
Can you describe a time when your attention to detail prevented a potential assembly error?
How to Answer
- 1
Think of a specific example from previous work experience.
- 2
Explain the context and what the task was.
- 3
Highlight the mistake that could have happened.
- 4
Describe what you did to prevent the error.
- 5
Mention the positive outcome that resulted.
Example Answers
During my time at XYZ Manufacturing, I was assembling components for a control panel. I noticed that one of the wiring diagrams had a small discrepancy. By double-checking the wiring instructions, I corrected the error before assembly. This prevented a short circuit in the final product, ensuring safety and functionality.
Tell me about a time when you had to collaborate with a team to complete an assembly project under a tight deadline. What was the outcome?
How to Answer
- 1
Choose a specific project where teamwork was essential.
- 2
Highlight your role and contributions clearly.
- 3
Emphasize the strategies you used to meet the deadline.
- 4
Explain the outcome, focusing on success and what was learned.
- 5
Use the STAR method: Situation, Task, Action, Result.
Example Answers
In my previous role, our team was tasked with assembling a prototype for a new product with only one week to complete it. I took the lead in organizing daily stand-ups to assess progress and address roadblocks. We divided tasks based on team members' strengths, and I coordinated the workflow to ensure efficiency. We completed the project on time, and the prototype was presented successfully, receiving positive feedback from stakeholders.
Don't Just Read Assembly Person Questions - Practice Answering Them!
Reading helps, but actual practice is what gets you hired. Our AI feedback system helps you improve your Assembly Person interview answers in real-time.
Personalized feedback
Unlimited practice
Used by hundreds of successful candidates
Describe a challenging assembly problem you encountered and how you resolved it.
How to Answer
- 1
Identify a specific problem you faced during assembly.
- 2
Explain the steps you took to analyze the situation.
- 3
Describe the solution you implemented and how it worked.
- 4
Mention any lessons learned from the experience.
- 5
Keep your answer structured: situation, action, result.
Example Answers
In my last role, I encountered a recurring issue where components wouldn't fit correctly. I analyzed the blueprints and discovered a miscommunication between design and production. I proposed a redesign to accommodate the parts, which resolved the issue and improved our assembly line efficiency by 20%.
Give an example of how you communicated a technical issue to a non-technical team member or customer.
How to Answer
- 1
Identify a specific technical issue you faced.
- 2
Describe how you simplified the language used to explain it.
- 3
Highlight any tools or visuals you used to aid understanding.
- 4
Mention the outcome of your communication.
- 5
Keep your response focused and concise.
Example Answers
In my previous role, we had a software bug that caused issues in data reporting. I explained the problem to the sales team by using analogies, comparing the software to a filing cabinet. I also created a simple flowchart to illustrate the data flow. They quickly grasped the issue and were able to communicate the impact to clients effectively.
Tell me about a time when you identified a quality issue on the production line and what actions you took to address it.
How to Answer
- 1
Describe the specific quality issue clearly
- 2
Explain how you identified the issue using data or observation
- 3
Detail the steps you took to investigate the root cause
- 4
Discuss the actions implemented to resolve the issue
- 5
Highlight the positive outcome or improvement achieved
Example Answers
In my previous role, I noticed that several products were failing the final inspection due to misalignment. I reviewed the production data and discovered that the alignment tool was out of calibration. I reported the issue, calibrated the tool, and implemented regular checks. As a result, product quality improved with a 20% decrease in defects.
Describe a situation where you had to quickly adapt to a change in assembly procedures. How did you handle it?
How to Answer
- 1
Identify a specific change in procedure you experienced.
- 2
Describe your initial reaction and how you assessed the situation.
- 3
Explain the steps you took to adapt to the new procedures.
- 4
Highlight the outcome and what you learned from the experience.
- 5
Emphasize your flexibility and problem-solving skills.
Example Answers
In my previous role, we suddenly switched to a new assembly line software. I quickly reviewed the new manual and asked for help from colleagues. I then created a quick reference guide that helped our team adapt faster. As a result, we maintained our productivity and reduced errors during the transition.
Have you ever taken the lead on an assembly project? How did you ensure the team met quality and time targets?
How to Answer
- 1
Describe a specific project where you were the team leader
- 2
Focus on your role and responsibilities during the project
- 3
Highlight your strategies for maintaining quality, such as checklists or quality control measures
- 4
Mention how you tracked progress against deadlines, like using project management tools
- 5
Explain how you motivated your team to meet targets effectively
Example Answers
In my last role, I led an assembly project for a new product. I created a detailed schedule and set milestones. To ensure quality, I implemented regular check-ins and quality inspections at each stage. By using project tracking software, I kept everyone accountable and on schedule, which helped us finish on time with zero defects.
Can you discuss a time when you had a conflict with a coworker on the assembly line? How did you resolve it?
How to Answer
- 1
Stay calm and objective when describing the conflict
- 2
Focus on your role and actions taken
- 3
Explain the resolution process clearly
- 4
Highlight any positive outcomes from the conflict
- 5
Emphasize teamwork and communication skills
Example Answers
During a tight deadline, a coworker and I disagreed on the best way to assemble a part. I suggested we take a break to cool down, then came back to discuss each of our methods. We reached a compromise that combined the strengths of both our ideas, which improved our efficiency.
Describe an initiative you took to improve the assembly process at your previous job.
How to Answer
- 1
Identify a specific problem in the assembly process.
- 2
Describe the initiative you implemented to address this problem.
- 3
Share measurable results or improvements gained from your initiative.
- 4
Highlight teamwork or collaboration in your initiative.
- 5
Conclude with what you learned from the experience.
Example Answers
At my previous job, we often faced delays due to a lack of parts on the assembly line. I initiated a weekly inventory review and set up a reorder point for critical components, which reduced downtime by 30%.
Tell us about a time when you identified a safety hazard on the job and what you did to correct it.
How to Answer
- 1
Describe the context of the situation clearly.
- 2
Explain how you recognized the safety hazard.
- 3
Detail the steps you took to address the issue.
- 4
Mention any collaboration with team members or supervisors.
- 5
Share the outcome and any improvements made.
Example Answers
At my previous job as a maintenance worker, I noticed that a section of the floor was slippery due to a recent spill. I immediately reported it to my supervisor and put up warning signs to alert others. We cleaned the area and took measures to prevent future spills. As a result, there were no accidents reported in that area after.
Don't Just Read Assembly Person Questions - Practice Answering Them!
Reading helps, but actual practice is what gets you hired. Our AI feedback system helps you improve your Assembly Person interview answers in real-time.
Personalized feedback
Unlimited practice
Used by hundreds of successful candidates
Technical Interview Questions
What specific techniques do you use to ensure accurate and efficient assembly?
How to Answer
- 1
Describe the use of checklists to prevent errors at each assembly step
- 2
Mention the importance of organizing tools and parts for easy access
- 3
Talk about implementing quality checks during and after assembly
- 4
Explain how you stay focused and minimize distractions in the workspace
- 5
Highlight any specific assembly techniques or tools you use for precision
Example Answers
I use detailed checklists to verify each step in the assembly process, which helps prevent errors. Additionally, I keep my workspace organized so I can access tools and parts quickly.
What are some essential tools you use for assembly and how do you maintain them?
How to Answer
- 1
Identify specific tools relevant to assembly like screwdrivers, wrenches, and drills.
- 2
Describe your process for regular maintenance, such as cleaning and lubrication.
- 3
Mention any record-keeping for tool usage and maintenance schedules.
- 4
Discuss how you ensure tools are safe and in good working condition before use.
- 5
Explain your approach to replacing worn or damaged tools promptly.
Example Answers
I primarily use screwdrivers, wrenches, and power drills for assembly. I maintain them by cleaning after each use, lubricating moving parts regularly, and checking for any signs of wear. I also keep a log of maintenance schedules to ensure everything stays in top condition.
Don't Just Read Assembly Person Questions - Practice Answering Them!
Reading helps, but actual practice is what gets you hired. Our AI feedback system helps you improve your Assembly Person interview answers in real-time.
Personalized feedback
Unlimited practice
Used by hundreds of successful candidates
How comfortable are you with reading and interpreting assembly blueprints or technical diagrams?
How to Answer
- 1
Explain your experience with blueprints or technical diagrams.
- 2
Mention specific tools or methodologies you are familiar with.
- 3
Discuss any relevant training or certifications.
- 4
Provide an example of a project where you used these skills.
- 5
Express a willingness to learn and improve if needed.
Example Answers
I am quite comfortable with reading and interpreting assembly blueprints. In my previous role, I worked extensively with technical diagrams using AutoCAD. I completed a workshop on blueprint reading, which helped me enhance my skills, and I successfully led a project where accurate interpretation was crucial.
What types of materials have you worked with in assembly processes, and how do you determine the best way to handle each?
How to Answer
- 1
Identify specific materials you have experience with, such as metals, plastics, or composites.
- 2
Explain how the properties of each material influence assembly methods.
- 3
Discuss any specialized tools or techniques you used for different materials.
- 4
Mention any challenges you faced with certain materials and how you overcame them.
- 5
Emphasize your adaptability and willingness to learn new assembly methods for new materials.
Example Answers
I have worked with metals like aluminum and steel, as well as plastics like polycarbonate. For metals, I focused on welding and mechanical fastening, while for plastics I used adhesives and heat sealing. Understanding the materials' strength and temperature resistance helped me select the right assembly method.
How do you approach routine maintenance of assembly equipment to ensure minimal downtime?
How to Answer
- 1
Create a detailed maintenance schedule for all equipment
- 2
Perform regular inspections and checks on critical components
- 3
Use predictive maintenance tools to identify potential issues early
- 4
Train staff on proper equipment use and basic maintenance tasks
- 5
Keep an inventory of essential spare parts for quick replacements
Example Answers
I establish a detailed maintenance schedule that outlines regular checks for each piece of equipment. This includes inspections every month and a thorough check every six months to ensure everything is running smoothly.
What steps do you take to inspect your work and ensure it meets quality standards?
How to Answer
- 1
Start by checking your work against the specifications or requirements.
- 2
Use a checklist to verify that all quality standards are met.
- 3
Take time to review your work carefully before submission.
- 4
Seek feedback from a colleague or supervisor for a fresh perspective.
- 5
Perform a self-audit by assessing the effectiveness and efficiency of your work.
Example Answers
I always compare my completed work to the original specifications to ensure compliance. Then, I use a checklist for quality criteria before I submit it. Finally, I ask a colleague to review my work to catch anything I might have missed.
How do you prioritize tasks to maintain an efficient workflow on the assembly line?
How to Answer
- 1
Identify critical tasks that impact production first
- 2
Use visual tools like charts or lists to organize tasks
- 3
Communicate with team members to gather input on priorities
- 4
Stay flexible to adjust priorities based on workflow changes
- 5
Regularly review and improve your task management process
Example Answers
I prioritize tasks based on their impact on production. I use a task list and often discuss with my team to make sure we’re all aligned on priorities.
Describe your experience with operating specific machines or equipment commonly used in assembly work.
How to Answer
- 1
Identify specific machines relevant to the position
- 2
Share hands-on experience and duration of use
- 3
Mention any training or certifications you have
- 4
Highlight safety protocols you follow
- 5
Relate your experience to the job requirements
Example Answers
I have operated CNC machines for three years in my previous assembly job, ensuring precision in manufacturing parts.
What process do you follow to troubleshoot assembly errors or machine malfunctions?
How to Answer
- 1
Start with a clear understanding of the assembly instructions and specifications.
- 2
Identify the symptoms of the error or malfunction quickly and document them.
- 3
Check for common issues such as loose connections or incorrect part placements.
- 4
Use diagnostic tools or error codes to help pinpoint the problem.
- 5
Test the assembly step-by-step after making adjustments to ensure the problem is resolved.
Example Answers
First, I review the assembly instructions to ensure I follow them accurately. Then, I identify the specific error, document the symptoms, and check common issues like loose connections. I also use diagnostic tools to help locate the fault, performing tests after adjustments to confirm the issue is resolved.
Describe any experience you have with automated assembly systems or computerized controls.
How to Answer
- 1
Identify specific systems you have worked with such as robotic arms or PLCs.
- 2
Mention your role in operating or maintaining these systems.
- 3
Give an example of a project where you improved efficiency using automation.
- 4
Highlight any relevant training or certifications in automation.
- 5
Be prepared to discuss troubleshooting experiences with automated systems.
Example Answers
I have worked with robotic assembly arms in a manufacturing setting, where I operated and programmed them for various production tasks. In one project, I streamlined the assembly line, reducing cycle time by 20%.
Don't Just Read Assembly Person Questions - Practice Answering Them!
Reading helps, but actual practice is what gets you hired. Our AI feedback system helps you improve your Assembly Person interview answers in real-time.
Personalized feedback
Unlimited practice
Used by hundreds of successful candidates
Situational Interview Questions
If you noticed a defect in a batch of assembled products, how would you handle the situation to ensure it doesn't reach the customer?
How to Answer
- 1
Immediately isolate the defective batch to prevent further distribution.
- 2
Document the defect clearly with photos and descriptions.
- 3
Communicate the issue to your supervisor and the quality control team.
- 4
Investigate the root cause of the defect to prevent recurrence.
- 5
Propose a solution, such as rework or scrap, depending on severity.
Example Answers
Upon noticing a defect, I would immediately isolate the affected batch to ensure it doesn't leave the facility. Then, I would document the defect with photos and detailed descriptions for quality control. I would inform my supervisor right away and collaborate with the team to investigate the root cause.
Imagine you're given multiple assembly tasks with the same deadline. How would you prioritize them?
How to Answer
- 1
Assess the complexity and time required for each task.
- 2
Identify the importance and urgency of each task.
- 3
Consider dependencies between tasks that may affect order.
- 4
Use a quick evaluation matrix to rank tasks.
- 5
Communicate your priorities to ensure alignment with team goals.
Example Answers
I would start by listing all tasks and estimating the time each one needs. Then, I'd prioritize tasks that are critical to the overall process and have the highest impact.
Don't Just Read Assembly Person Questions - Practice Answering Them!
Reading helps, but actual practice is what gets you hired. Our AI feedback system helps you improve your Assembly Person interview answers in real-time.
Personalized feedback
Unlimited practice
Used by hundreds of successful candidates
What steps would you take if you observed a coworker not following safety procedures?
How to Answer
- 1
Assess the situation quickly to understand the risk involved
- 2
Approach the coworker calmly and privately to discuss the issue
- 3
Emphasize the importance of safety protocols for everyone's well-being
- 4
Suggest solutions or offer to help them comply with the procedures
- 5
If the behavior continues, report the incident to a supervisor
Example Answers
First, I would evaluate the situation to see if anyone is in immediate danger. Then, I would privately talk to my coworker about what I observed, explaining why following safety procedures is critical. I would offer to assist them in understanding the safety protocols better. If necessary, I would involve a supervisor to ensure everyone's safety.
Suppose you have an idea to enhance the assembly process. How would you present it to your supervisor?
How to Answer
- 1
Gather data and evidence to support your idea
- 2
Prepare a clear and concise presentation
- 3
Highlight the benefits to efficiency and productivity
- 4
Anticipate questions and concerns from your supervisor
- 5
Suggest a small pilot test or implementation plan
Example Answers
I would first gather statistics showing how my idea could reduce assembly time by 20%. Then, I would prepare a short presentation and explain the concept clearly while showing how it enhances productivity. I would also propose starting with a small pilot test to measure the impact before a full rollout.
If you're falling behind on an assembly project, what strategies would you employ to get back on track?
How to Answer
- 1
Assess the current progress and identify the key bottlenecks
- 2
Prioritize tasks that will deliver the most value in the shortest time
- 3
Communicate with team members to redistribute workload if necessary
- 4
Implement time management techniques like time blocking for focus
- 5
Consider seeking assistance or advice from more experienced colleagues
Example Answers
To get back on track, I would first assess where the bottlenecks are in my assembly process. Then, I'd prioritize the tasks that are critical for meeting our deadlines. If needed, I would communicate with my team to redistribute some tasks to balance the workload and ensure efficiency.
How would you manage a situation where an urgent assembly order comes in and you're already busy with current tasks?
How to Answer
- 1
Prioritize the urgent order based on its deadline and impact.
- 2
Assess what current tasks can be delegated or postponed.
- 3
Communicate with your team about the new priority and needs.
- 4
Organize a quick plan of action to manage both urgent and current tasks.
- 5
Use time management techniques to focus on the urgent order effectively.
Example Answers
I would first assess the urgency of the assembly order and its deadline. If it's critical, I'd delegate some of my current tasks to team members or shift less urgent tasks to a later time. Communication with my team would be key to ensure we can meet the new demands efficiently.
How would you handle a situation where your team is stressed due to high workload on the assembly line?
How to Answer
- 1
Assess the workload and identify bottlenecks
- 2
Communicate openly with the team about stress levels
- 3
Encourage breaks and provide support
- 4
Prioritize tasks and delegate effectively
- 5
Consider asking for additional resources or help
Example Answers
I would start by talking to my team to understand their specific stress points, then we could prioritize tasks and delegate items to lighten the load.
How would you approach a situation where a customer reports a quality issue with a product you assembled?
How to Answer
- 1
Listen carefully to the customer's concerns without interrupting
- 2
Acknowledge the issue and express empathy for their experience
- 3
Ask clarifying questions to understand the specifics of the problem
- 4
Explain the steps you will take to resolve the issue
- 5
Follow up with the customer to ensure their satisfaction after the resolution
Example Answers
I would start by listening to the customer and understanding their specific concerns about the product. I would assure them that I take quality seriously and will investigate the issue immediately. I would gather all relevant details and then communicate the steps I will take to resolve the matter, ensuring they feel valued in the process.
If you were asked to train a new employee on the assembly process, how would you structure the training?
How to Answer
- 1
Start with an overview of the assembly process to set context
- 2
Break down the training into clear, manageable sections or modules
- 3
Use hands-on practice to reinforce learning after each module
- 4
Incorporate visual aids or demonstrations to enhance understanding
- 5
Schedule regular check-ins to assess their progress and answer questions
Example Answers
First, I would provide an overview of the entire assembly process to give context. Then, I would break it down into sections, such as safety protocols, tools used, and specific assembly tasks. After each section, I would offer hands-on practice. I'd also use visual aids, like diagrams, to clarify instructions. Finally, I would schedule weekly check-ins to discuss their progress and clarify any doubts they might have.
How would you address a situation where you disagree with a team member about the best way to assemble a component?
How to Answer
- 1
Listen to the team member's perspective fully before responding.
- 2
Share your reasoning clearly and factually, with supporting data if possible.
- 3
Suggest a collaborative approach to test both methods and compare results.
- 4
Keep the discussion focused on the goal of the project, not personal opinions.
- 5
Be open to compromise and learning from the team member's approach.
Example Answers
I would first listen to my colleague's perspective and understand their reasoning. Then, I would explain my approach with clear facts and data. If we still disagreed, I would propose that we test both methods to see which one yields better results, ensuring we stay focused on the project's success.
Don't Just Read Assembly Person Questions - Practice Answering Them!
Reading helps, but actual practice is what gets you hired. Our AI feedback system helps you improve your Assembly Person interview answers in real-time.
Personalized feedback
Unlimited practice
Used by hundreds of successful candidates
Assembly Person Position Details
Recommended Job Boards
ZipRecruiter
www.ziprecruiter.com/Jobs/AssemblerThese job boards are ranked by relevance for this position.
Related Positions
- Assembly Member
- Assemblyman
- Legislator
- Congressman
- United States Representative
- Assemblywoman
- Delegate
- Councilman
- Selectman
- Senator
Similar positions you might be interested in.
Ace Your Next Interview!
Practice with AI feedback & get hired faster
Personalized feedback
Used by hundreds of successful candidates
Ace Your Next Interview!
Practice with AI feedback & get hired faster
Personalized feedback
Used by hundreds of successful candidates