Top 28 Batch Plant Operator Interview Questions and Answers [Updated 2025]
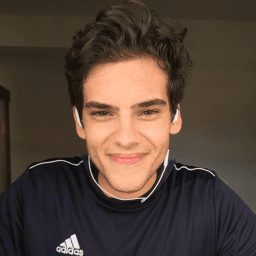
Andre Mendes
•
March 30, 2025
Preparing for a Batch Plant Operator interview? This blog post has you covered with the most common questions asked in the field, complete with example answers and tips for responding effectively. Whether you're a seasoned professional or new to the industry, these insights will help you confidently navigate your interview and showcase your skills. Dive in to enhance your preparation and ace that interview!
Download Batch Plant Operator Interview Questions in PDF
To make your preparation even more convenient, we've compiled all these top Batch Plant Operatorinterview questions and answers into a handy PDF.
Click the button below to download the PDF and have easy access to these essential questions anytime, anywhere:
List of Batch Plant Operator Interview Questions
Technical Interview Questions
What quality control measures do you implement while operating a batch plant?
How to Answer
- 1
Describe specific testing procedures you follow.
- 2
Mention routine maintenance checks you perform.
- 3
Highlight how you monitor ingredient quality before use.
- 4
Discuss the importance of calibration of equipment.
- 5
Explain how you document and analyze batch results.
Example Answers
I implement a strict testing protocol where I check the quality of raw materials before processing. Additionally, I perform daily maintenance checks on all equipment to ensure everything is operating correctly.
What steps do you take to ensure the accuracy of the batching process?
How to Answer
- 1
Thoroughly calibrate all batching equipment regularly
- 2
Double-check measurements before addition
- 3
Utilize quality control samples to verify material consistency
- 4
Log all batches for traceability and analysis
- 5
Communicate effectively with team members to ensure everyone is aware of batch specifications
Example Answers
I regularly calibrate the equipment and double-check measurements before adding materials to ensure accuracy in every batch.
Don't Just Read Batch Plant Operator Questions - Practice Answering Them!
Reading helps, but actual practice is what gets you hired. Our AI feedback system helps you improve your Batch Plant Operator interview answers in real-time.
Personalized feedback
Unlimited practice
Used by hundreds of successful candidates
What types of batching equipment are you familiar with, and how have you used them?
How to Answer
- 1
List specific types of batching equipment you have experience with.
- 2
Briefly describe a task where you utilized each equipment type.
- 3
Mention any maintenance or troubleshooting you performed on the equipment.
- 4
Emphasize your understanding of how batching equipment impacts production quality.
- 5
Speak confidently about your role and contributions in past positions.
Example Answers
I have worked with both stationary and mobile concrete batch plants. For example, in my last job, I operated a stationary plant to mix concrete for various construction projects, ensuring precise measurements for water and aggregates.
Can you explain the importance of understanding the properties of the materials you work with?
How to Answer
- 1
Mention how material properties affect mix design and quality control.
- 2
Explain the impact of moisture content and temperature on material performance.
- 3
Discuss how understanding properties helps in troubleshooting and problem-solving.
- 4
Highlight the importance of material compatibility for durability and safety.
- 5
Connect knowledge of materials to achieving project specifications and standards.
Example Answers
Understanding material properties is crucial because they directly influence the mix design and overall quality of the concrete. For example, knowing the moisture content can help adjust the water ratio, leading to a stronger final product.
What routine maintenance tasks do you perform to keep the batching equipment operational?
How to Answer
- 1
Describe specific tasks you conduct regularly.
- 2
Mention any checklists or logs you keep.
- 3
Include how you handle common issues and repairs.
- 4
Talk about safety checks related to maintenance.
- 5
Highlight the importance of documentation for maintenance tasks.
Example Answers
I perform daily checks on the batching scales and calibration to ensure accuracy. Weekly, I inspect the conveyors and clean the mixers. I maintain a log of all maintenance performed and any repairs needed.
Are you familiar with any batching control software? How do you use it?
How to Answer
- 1
Identify specific batching software you have used.
- 2
Describe your experience with the software in detail.
- 3
Explain how you used the software to improve efficiency or accuracy.
- 4
Mention any challenges you faced and how you resolved them.
- 5
Show your willingness to learn new systems if not familiar with current software.
Example Answers
I have experience using Command Alkon's Apollo software. I used it daily to control batch mixes for concrete production, ensuring accuracy in measurements and timely scheduling of batches.
What industry regulations do you need to comply with as a Batch Plant Operator?
How to Answer
- 1
Know key regulations such as environmental standards and safety protocols.
- 2
Mention specific regulations like EPA guidelines for emissions.
- 3
Discuss compliance with OSHA standards for workplace safety.
- 4
Include any local or state regulations relevant to plant operations.
- 5
Highlight the importance of documentation and reporting compliance.
Example Answers
As a Batch Plant Operator, I comply with EPA regulations regarding air quality and emissions. I also follow OSHA standards to ensure workplace safety, which includes wearing personal protective equipment and conducting regular safety audits.
Behavioral Interview Questions
Can you describe a time when you had to work closely with a team to meet a production deadline?
How to Answer
- 1
Think of a specific project or incident where teamwork was crucial.
- 2
Describe your role and contributions clearly.
- 3
Highlight challenges faced and how the team overcame them.
- 4
Mention the outcome and how it met the deadline.
- 5
Reflect on what you learned from the experience.
Example Answers
In my last job at the concrete plant, we had a big order due in two days. I coordinated with the mix designers and machine operators to ensure everything was ready. We faced equipment issues, but we worked extra shifts and sorted it out together. We delivered on time, which impressed our client.
Tell me about a situation where you identified a problem with the batching process. How did you handle it?
How to Answer
- 1
Describe the specific problem you identified and the context.
- 2
Explain how you assessed the problem's impact on the batching process.
- 3
Outline the steps you took to resolve the issue.
- 4
Discuss any collaboration with colleagues or other departments.
- 5
Mention what you learned from the experience and any improvements implemented.
Example Answers
In one instance, I noticed that the scale used for measuring materials was consistently off by a few pounds. I reviewed the calibration logs and found that it hadn't been calibrated recently. I paused the batching process, recalibrated the scale, and then verified its accuracy by testing with known weights. This prevented potential inconsistencies in our mix and ensured quality. I suggested increasing the frequency of scale checks in our maintenance schedule based on this experience.
Don't Just Read Batch Plant Operator Questions - Practice Answering Them!
Reading helps, but actual practice is what gets you hired. Our AI feedback system helps you improve your Batch Plant Operator interview answers in real-time.
Personalized feedback
Unlimited practice
Used by hundreds of successful candidates
Describe an instance when you prioritized safety in your role. What steps did you take?
How to Answer
- 1
Think of a specific situation where safety was at risk.
- 2
Describe the hazard or potential risk clearly.
- 3
Explain the steps you took to address the safety concern.
- 4
Mention any protocols or safety measures you followed.
- 5
Conclude with the positive outcome or lessons learned.
Example Answers
At my previous job, we had a situation where a colleague was not wearing the required PPE while operating the mixer. I immediately stopped the operation and reminded everyone about the safety protocols regarding PPE. I ensured the equipment was turned off before addressing the issue. As a result, everyone became more vigilant, and we maintained a safer work environment.
How have you successfully communicated technical issues to non-technical team members in the past?
How to Answer
- 1
Identify the key technical issue clearly and simply.
- 2
Use analogies or relatable examples to explain complex concepts.
- 3
Encourage questions to ensure understanding.
- 4
Be patient and ready to repeat or rephrase information.
- 5
Follow up with a summary or a visual aid to reinforce the message.
Example Answers
In my previous job, I explained a malfunctioning mixer to the maintenance team by comparing it to a car engine that needed tuning. I encouraged them to ask questions about the troubleshooting process and summarized the key points on a whiteboard.
Give an example of how you adapted to changes in production schedules or material availability.
How to Answer
- 1
Identify a specific instance where you faced a change.
- 2
Describe your immediate actions to address the change.
- 3
Highlight the outcome of your actions and any lessons learned.
- 4
Emphasize teamwork or communication if applicable.
- 5
Keep your answer focused and avoid unnecessary details.
Example Answers
In my previous job, we received late material deliveries which affected our production schedule. I quickly adjusted by rescheduling our mixing timetables and coordinated with the supply team to prioritize critical materials. This kept us on track, reducing downtime by 30%.
Have you ever taken a leadership role during a critical project? What was the outcome?
How to Answer
- 1
Choose a specific project that had significant impact.
- 2
Clearly outline your leadership role and responsibilities.
- 3
Describe challenges faced and how you overcame them.
- 4
Highlight the positive outcomes of the project.
- 5
Mention any skills or insights gained from the experience.
Example Answers
In my previous role, I led a project to upgrade our batching software. I coordinated with the team to fix bugs and implement new features. We finished ahead of schedule and increased efficiency by 20%. This experience taught me how to manage a team effectively under pressure.
Situational Interview Questions
If you notice a sudden drop in production efficiency, how would you investigate and address the issue?
How to Answer
- 1
Check the production logs for any discrepancies or unusual events.
- 2
Inspect the machinery and equipment for malfunctions or maintenance needs.
- 3
Talk to team members to gather their observations and insights.
- 4
Analyze raw materials for quality issues that could affect production.
- 5
Implement immediate adjustments and monitor results to see if efficiency improves.
Example Answers
I would start by reviewing the production logs to identify any unusual patterns. Then, I'd inspect the machinery for any signs of wear or recent maintenance needs. Next, I would consult with the team to gather their input on the situation. If necessary, I'd also check the quality of our raw materials before taking corrective actions.
If a key piece of equipment fails during production, what steps would you take to minimize downtime?
How to Answer
- 1
Immediately assess the situation to identify the cause of failure
- 2
Communicate with the team and inform relevant personnel about the issue
- 3
Implement emergency procedures to isolate the faulty equipment
- 4
Initiate repair or replacement procedures as quickly as possible
- 5
Document the incident for future reference and preventive measures
Example Answers
First, I would quickly assess the equipment to determine the cause of the failure. Then, I would alert my team and supervisors to keep everyone informed. Next, I would follow our emergency procedures to isolate the faulty equipment and prevent further issues. After that, I would work with maintenance to get the repairs started immediately. Lastly, I would document the failure for analysis to prevent future occurrences.
Don't Just Read Batch Plant Operator Questions - Practice Answering Them!
Reading helps, but actual practice is what gets you hired. Our AI feedback system helps you improve your Batch Plant Operator interview answers in real-time.
Personalized feedback
Unlimited practice
Used by hundreds of successful candidates
How would you handle a situation where two team members disagree on how to proceed with a batch?
How to Answer
- 1
Listen to both team members to understand their perspectives.
- 2
Encourage open communication to clarify the disagreement.
- 3
Assess the facts and data regarding the batch process involved.
- 4
Suggest finding a compromise or alternative solution that works for both.
- 5
If necessary, involve a supervisor to help mediate the discussion.
Example Answers
I would first listen to both team members to understand their viewpoints fully. Then, I would encourage them to discuss their ideas openly. I would assess the facts and determine the best approach. If they can't reach a compromise, I would involve a supervisor to help facilitate the discussion.
What would you do if you witnessed a safety violation happening in the batch plant?
How to Answer
- 1
Identify the violation clearly and assess the immediate risk.
- 2
Report the issue to your supervisor or manager without delay.
- 3
Ensure the safety of yourself and others while the incident is addressed.
- 4
Follow up to ensure appropriate actions are taken to rectify the situation.
- 5
Document the incident for future reference or training improvement.
Example Answers
If I witness a safety violation, I would first ensure everyone's safety and then report it to my supervisor immediately. I would describe what I saw and help in any way needed to remedy the situation.
If you receive a batch of raw materials that do not match specifications, how would you handle it?
How to Answer
- 1
Check the delivery documents for accuracy.
- 2
Verify the materials against the specifications.
- 3
Stop the operation and notify your supervisor immediately.
- 4
Document the discrepancies for record-keeping.
- 5
Follow the company procedure for non-conforming materials.
Example Answers
I would first compare the shipment against the delivery documents to confirm the discrepancies. Then, I'll stop all operations and immediately notify my supervisor about the issue. It's important to document what I found for our records and follow our company's protocol to handle non-conforming materials.
If a batch does not meet quality standards, how would you investigate the cause?
How to Answer
- 1
Check the raw materials used for inconsistencies.
- 2
Review the batch process for any deviations from standard procedures.
- 3
Inspect the equipment for malfunctions or calibration issues.
- 4
Consult batch records and logs for discrepancies.
- 5
Collaborate with team members to gather additional insights.
Example Answers
I would start by checking the raw materials to ensure they met specifications. Then, I'd review the batch process to see if any steps were omitted or performed incorrectly.
How would you react if a supervisor requested a batch to be produced urgently at the last minute?
How to Answer
- 1
Stay calm and positive to show willingness to help
- 2
Quickly assess current workload and flexibility
- 3
Communicate clearly with the supervisor about potential challenges
- 4
Prioritize tasks and resources to meet the urgent demand
- 5
Document the changes made to ensure smooth operations after urgent task
Example Answers
I would remain calm and assure my supervisor that I can help. I'd assess what needs to be done immediately and see if I can adjust my current tasks to prioritize the urgent batch. Communication is key, so I would update my supervisor on any potential delays caused by this change.
How would you prioritize your tasks if faced with multiple batches and limited time?
How to Answer
- 1
Assess the urgency and deadlines for each batch
- 2
Identify which batches are critical for production
- 3
Communicate with team members about workload and support
- 4
Allocate resources based on batch requirements and complexity
- 5
Plan short breaks to maintain focus and efficiency
Example Answers
I would first assess which batches are due soonest and prioritize those. Then, I would check if any batches require additional support or resources and communicate with my team to ensure we handle the workload effectively.
What steps would you take if an emergency situation arises during batching operations?
How to Answer
- 1
Assess the situation quickly to identify the type of emergency.
- 2
Ensure safety of all personnel by activating emergency protocols.
- 3
Notify your supervisor and relevant emergency services if necessary.
- 4
Shut down the batching system following the established procedures.
- 5
Document the incident and actions taken for future reference.
Example Answers
In an emergency, I would quickly assess the situation to determine the issue, ensure all workers are safe by following emergency protocols, notify my supervisor, and shut down the batching equipment properly before documenting what happened.
How would you approach improving the efficiency of the batching process?
How to Answer
- 1
Analyze current batching procedures to identify bottlenecks
- 2
Implement regular maintenance checks on equipment to minimize downtime
- 3
Train staff on best practices for efficiency and safety
- 4
Utilize technology to monitor and optimize batch sizes in real time
- 5
Gather feedback from operators to adopt practical improvements
Example Answers
I would start by evaluating our current batching process to spot any slow points or inefficiencies. Regular maintenance of our equipment is crucial to prevent breakdowns. I'd also conduct training sessions for the team on efficient batching techniques.
Don't Just Read Batch Plant Operator Questions - Practice Answering Them!
Reading helps, but actual practice is what gets you hired. Our AI feedback system helps you improve your Batch Plant Operator interview answers in real-time.
Personalized feedback
Unlimited practice
Used by hundreds of successful candidates
How would you train a new operator on the essential processes and equipment?
How to Answer
- 1
Start with a comprehensive overview of the batch plant layout and key equipment.
- 2
Demonstrate the operation of each machine in a hands-on manner.
- 3
Use step-by-step guides and checklists for each process.
- 4
Encourage questions and provide scenarios for problem-solving.
- 5
Conduct follow-up assessments to ensure understanding and retention.
Example Answers
I would begin by giving the new operator a tour of the batch plant, explaining the layout and showing them each piece of equipment. Then, I would demonstrate how to operate key machines, guiding them through the process step-by-step. I would provide them with checklists to help them remember the procedures and encourage them to ask questions anytime.
You face repeated technical breakdowns. How would you assess and solve the issue?
How to Answer
- 1
Start by documenting each breakdown incident with details.
- 2
Perform root cause analysis to understand recurring issues.
- 3
Involve team members to gather insights on the breakdowns.
- 4
Implement solutions based on findings and test effectiveness.
- 5
Keep monitoring the equipment to prevent future breakdowns.
Example Answers
I would document each breakdown, looking for patterns or common factors. By doing a root cause analysis and involving my team, we could identify the underlying issue and implement a solution. I would then monitor performance closely to ensure the fix works.
How would you facilitate collaboration between your team and the quality assurance department?
How to Answer
- 1
Establish regular communication channels between teams.
- 2
Encourage joint meetings to discuss quality standards and issues.
- 3
Foster a culture of openness where feedback is welcomed.
- 4
Create a shared digital platform for tracking quality metrics.
- 5
Recognize and celebrate collaborative successes to motivate teams.
Example Answers
To facilitate collaboration, I would set up weekly meetings where both teams can discuss ongoing projects and any quality concerns, ensuring everyone is on the same page.
How would you handle a change in batching materials or suppliers that impacts your operations?
How to Answer
- 1
Assess the impact of the change on operations and product quality
- 2
Communicate with suppliers to understand the implications
- 3
Adjust batching processes or formulas as necessary
- 4
Implement testing to ensure consistent quality with the new materials
- 5
Document changes and keep stakeholders informed of updates
Example Answers
I would first evaluate how the new materials affect our current batching process. Then, I'd reach out to the supplier to clarify any concerns and gather data about the new material. I'd adjust mixing ratios if needed and run tests to ensure we meet quality standards before moving forward.
Batch Plant Operator Position Details
Recommended Job Boards
These job boards are ranked by relevance for this position.
Related Positions
Ace Your Next Interview!
Practice with AI feedback & get hired faster
Personalized feedback
Used by hundreds of successful candidates
Ace Your Next Interview!
Practice with AI feedback & get hired faster
Personalized feedback
Used by hundreds of successful candidates