Top 30 Boiler Technician Interview Questions and Answers [Updated 2025]
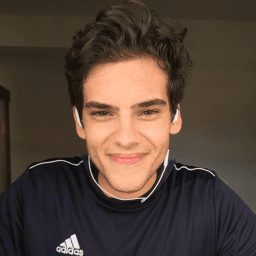
Andre Mendes
•
March 30, 2025
Preparing for a Boiler Technician interview can be daunting, but we've got you covered with this comprehensive guide. Dive into the most common interview questions for this critical role, complete with example answers and insightful tips on how to respond effectively. Whether you're a seasoned professional or just starting out, this post will equip you with the knowledge and confidence to excel in your interview.
Download Boiler Technician Interview Questions in PDF
To make your preparation even more convenient, we've compiled all these top Boiler Technicianinterview questions and answers into a handy PDF.
Click the button below to download the PDF and have easy access to these essential questions anytime, anywhere:
List of Boiler Technician Interview Questions
Technical Interview Questions
Explain the process of tuning a boiler for optimal efficiency. What factors do you consider?
How to Answer
- 1
Start with establishing the combustion air supply for optimal fuel burning.
- 2
Check and adjust the fuel-to-air ratio for complete combustion.
- 3
Monitor flue gas emissions to ensure they are within acceptable limits.
- 4
Adjust burner settings based on temperature and pressure readings.
- 5
Consider regular maintenance and cleaning to prevent efficiency losses.
Example Answers
To tune a boiler for optimal efficiency, I ensure the combustion air supply is correct and adjust the fuel-to-air ratio for complete combustion. I monitor flue gas emissions to keep them within limits and adjust burner settings based on the temperature. Regular maintenance is also crucial for maintaining efficiency.
What are the common signs of a malfunctioning boiler, and how would you diagnose them?
How to Answer
- 1
Identify typical signs like unusual noises, leaks, and inconsistent heating.
- 2
Mention the importance of checking pressure and temperature readings.
- 3
Discuss inspecting error codes or warning lights if applicable.
- 4
Talk about conducting visual inspections for wear or damage.
- 5
Explain how to perform routine tests to check efficiency.
Example Answers
Common signs of a malfunctioning boiler include strange noises like banging or hissing, leaks around the boiler, and inconsistent heating in different parts of the building. To diagnose these, I would first check the pressure and temperature readings on the gauge. If they are outside normal ranges, that indicates a problem. I would also inspect for any error codes on digital displays and perform a visual check for leaks or corrosion.
Don't Just Read Boiler Technician Questions - Practice Answering Them!
Reading helps, but actual practice is what gets you hired. Our AI feedback system helps you improve your Boiler Technician interview answers in real-time.
Personalized feedback
Unlimited practice
Used by hundreds of successful candidates
How do you ensure proper water treatment in a boiler system?
How to Answer
- 1
Regularly test water chemistry to monitor pH, hardness, and alkalinity levels
- 2
Use appropriate chemicals like oxygen scavengers and softeners based on test results
- 3
Conduct blowdown procedures to control mineral buildup and maintain water quality
- 4
Maintain accurate records of water quality tests and treatment chemicals used
- 5
Implement a routine maintenance schedule for water treatment equipment
Example Answers
I ensure proper water treatment by regularly testing the water for pH and hardness. Based on the test results, I add the necessary chemicals, like oxygen scavengers, and perform blowdowns to prevent scaling.
What is your understanding of combustion processes in boilers? How do you adjust burners for optimal performance?
How to Answer
- 1
Explain the basic combustion process including fuel, air, and ignition.
- 2
Discuss the importance of the air-to-fuel ratio for efficient combustion.
- 3
Mention common adjustments such as air registers and fuel flow settings.
- 4
Highlight the role of safety and emissions standards in burner adjustments.
- 5
Provide examples of tools used for monitoring combustion efficiency.
Example Answers
In a boiler, combustion is the process where fuel burns in the presence of air to generate heat. I ensure the correct air-to-fuel ratio is maintained for optimal combustion efficiency. This involves adjusting air registers and fuel flow valves. Additionally, I use combustion analyzers to monitor performance and comply with emissions standards.
What safety codes and standards are relevant to boiler operation and maintenance?
How to Answer
- 1
Mention specific codes like ASME and NFPA.
- 2
Discuss the importance of local regulations.
- 3
Highlight the role of proper training and certifications.
- 4
Emphasize adherence to manufacturer guidelines.
- 5
Reference preventive maintenance schedules.
Example Answers
Key safety codes relevant to boiler operation include the ASME Boiler and Pressure Vessel Code and NFPA 85. It's important to follow local regulations to ensure compliance and safety.
Can you explain how boiler controls operate and what maintenance they require?
How to Answer
- 1
Describe the key components of boiler controls like the thermostat, gauges, and safety valves.
- 2
Explain how these controls regulate temperature and pressure in the boiler.
- 3
Mention specific maintenance tasks such as checking calibration and inspecting safety devices.
- 4
Highlight the importance of regular inspections to prevent malfunctions.
- 5
Provide examples of problems that can occur if maintenance is neglected.
Example Answers
Boiler controls include components like thermostats that regulate temperature, and pressure gauges that monitor system levels. Regular daily checks of these controls are essential, along with monthly calibration to ensure accuracy, and inspecting safety valves quarterly to ensure they function correctly.
What are the most common repairs needed for industrial boilers, and how do you execute them?
How to Answer
- 1
Identify key common issues like leaks, scaling, and burner malfunctions.
- 2
Discuss tools and techniques used for each type of repair.
- 3
Highlight safety procedures followed during repairs.
- 4
Mention troubleshooting steps you take to diagnose problems.
- 5
Provide examples of past experiences with these repairs.
Example Answers
Common repairs for industrial boilers include fixing leaks, addressing scaling issues, and replacing burner components. I typically use hand tools for tightening fittings and chemical descalers for scaling. Safety is crucial, so I always follow lockout/tagout procedures. In one instance, I troubleshot a burner issue by checking the ignition system and found a faulty electrode.
What are the key components you inspect during a routine boiler inspection?
How to Answer
- 1
Reference safety checks as a priority.
- 2
Identify critical components like gauges, valves, and burners.
- 3
Mention the importance of checking for leaks and corrosion.
- 4
Highlight the need for water level and pressure assessments.
- 5
Discuss compliance with regulations and manufacturer standards.
Example Answers
During a routine inspection, I prioritize safety checks first. I inspect the pressure gauges and safety valves, ensuring they're functioning properly. I also look for any signs of leaks or corrosion on the boiler and check the burner and combustion system for efficiency.
What measures can be taken to improve boiler efficiency during operations?
How to Answer
- 1
Regularly monitor and maintain boiler components for optimal performance
- 2
Ensure proper water treatment to avoid scaling and fouling
- 3
Optimize combustion settings to achieve the best fuel-to-air ratio
- 4
Inspect and repair insulation to reduce heat loss
- 5
Implement a routine energy audit to identify inefficiencies
Example Answers
To improve boiler efficiency, I would focus on regular maintenance of components to prevent issues and ensure peak performance. Additionally, proper water treatment is essential to minimize scaling which can hinder heat transfer.
How do you maintain accurate records for boiler maintenance and inspections?
How to Answer
- 1
Use a standardized checklist for inspections to ensure consistency.
- 2
Document all maintenance tasks immediately after completion.
- 3
Utilize a digital logbook for easy access and backups.
- 4
Regularly review records to identify patterns and plan future maintenance.
- 5
Ensure compliance with relevant regulations and standards.
Example Answers
I use a standardized checklist for every inspection which helps me maintain consistency. After completing each task, I immediately document it in a digital logbook that I regularly back up.
Don't Just Read Boiler Technician Questions - Practice Answering Them!
Reading helps, but actual practice is what gets you hired. Our AI feedback system helps you improve your Boiler Technician interview answers in real-time.
Personalized feedback
Unlimited practice
Used by hundreds of successful candidates
How do you conduct a failure analysis on a boiler that has experienced a significant breakdown?
How to Answer
- 1
Start by gathering all relevant operational data and maintenance records.
- 2
Inspect the boiler and its components for physical signs of damage or wear.
- 3
Identify any abnormal operating conditions prior to the breakdown.
- 4
Consult with team members or operators for their observations leading up to the failure.
- 5
Use root cause analysis techniques to determine the underlying cause of the failure.
Example Answers
I would first collect all operations data and maintenance logs to understand what happened before the breakdown. Then I'd inspect the boiler components visually for any obvious damage. I'd also review any unusual operating conditions reported and talk to operators for their insights. Lastly, I would apply root cause analysis methods to pinpoint the exact cause of the failure.
Situational Interview Questions
If a client is unhappy with the performance of their boiler after service, how would you handle the situation?
How to Answer
- 1
Listen carefully to the client's concerns without interrupting.
- 2
Apologize for any inconvenience they experienced.
- 3
Ask specific questions to understand the issue clearly.
- 4
Provide a solution or action plan to address their concerns.
- 5
Follow up after the service to ensure client satisfaction.
Example Answers
I would start by listening to the client to understand exactly what their concerns are. I would apologize for any inconvenience and ask detailed questions to get to the root of the problem. Then, I would outline a clear plan of action to resolve the issue and ensure they are satisfied.
If you suspect a gas leak in a boiler room, what immediate actions would you take?
How to Answer
- 1
Evacuate everyone from the area immediately
- 2
Shut off the gas supply if it is safe to do so
- 3
Avoid using electrical switches or creating sparks
- 4
Ventilate the area if possible by opening doors or windows
- 5
Notify emergency services to handle the situation
Example Answers
I would first evacuate all personnel from the boiler room to ensure safety. Then I would shut off the gas supply if it is safe to do so and avoid any actions that could spark a fire. Finally, I would call emergency services for assistance.
Don't Just Read Boiler Technician Questions - Practice Answering Them!
Reading helps, but actual practice is what gets you hired. Our AI feedback system helps you improve your Boiler Technician interview answers in real-time.
Personalized feedback
Unlimited practice
Used by hundreds of successful candidates
Imagine a boiler went down unexpectedly during peak operation hours. How would you handle the situation?
How to Answer
- 1
Remain calm and prioritize safety for all personnel.
- 2
Quickly assess the issue and identify the root cause of the failure.
- 3
Communicate clearly with the team and management about the status.
- 4
Implement emergency procedures to minimize downtime.
- 5
Document the incident and repairs for future reference.
Example Answers
I would first ensure everyone's safety and then quickly assess the situation to identify the cause of the boiler failure. I would communicate the issue to my team and management and follow emergency protocols to address the problem. After resolving it, I would document the entire process for future reference.
You have multiple service requests, but limited time to address them. How would you prioritize which boilers to inspect first?
How to Answer
- 1
Assess the urgency of each service request based on safety concerns.
- 2
Consider the age and maintenance history of the boilers.
- 3
Look for service requests with the highest potential impact on operations.
- 4
Prioritize requests from clients or facilities that are critical to the business.
- 5
Use a systematic approach to categorize requests into urgent, high, and low priority.
Example Answers
I would first evaluate the safety risks and address any boilers with potential hazards. Then I'd look at the maintenance history; older boilers or those with frequent issues would get higher priority. Lastly, I would consider our key clients and prioritize their requests to minimize downtime.
If a colleague is not following safety protocols while working on a boiler, how would you address this issue?
How to Answer
- 1
Address the issue immediately to prevent accidents.
- 2
Speak to the colleague privately to avoid embarrassment.
- 3
Explain the importance of safety procedures clearly.
- 4
Encourage them to ask questions if they are unsure.
- 5
Report the issue to a supervisor if necessary.
Example Answers
I would first talk to my colleague in private to understand why they are not following the safety protocols. I would explain why these procedures are crucial for everyone's safety and encourage them to follow them. If they continue to disregard safety, I would report the situation to our supervisor.
You are troubleshooting a steam boiler that is not generating steam. What steps would you take to identify and fix the issue?
How to Answer
- 1
Check the water levels and ensure they are within operational limits
- 2
Inspect the fuel supply for blockages or issues
- 3
Examine the boiler's safety controls and sensors for faults
- 4
Look for any unusual noises or leaks during operation
- 5
Review the operating pressure settings and adjust as necessary
Example Answers
First, I would check the water levels in the boiler to make sure they are sufficient. Next, I would inspect the fuel supply for any blockages or issues that may prevent combustion. After that, I'd examine the safety controls to ensure they are functioning properly.
If you realize mid-service that you do not have the necessary parts to complete a boiler repair, what would you do?
How to Answer
- 1
Assess the situation and identify exactly what parts are missing.
- 2
Communicate with the customer about the delay and explain the situation.
- 3
Check for any alternative solutions or workarounds that can be applied.
- 4
Order the necessary parts and provide an estimated time of arrival.
- 5
Follow up with the customer to ensure they are informed and satisfied.
Example Answers
First, I would identify the specific parts needed for the repair. Then, I would inform the customer about the missing parts and provide them with an estimated time for when they can expect to have the service completed. If possible, I would look for alternative solutions to ensure their needs are met in the meantime.
You and a colleague disagree on the best approach to fix a boiler issue. How would you resolve this conflict?
How to Answer
- 1
Listen to your colleague's perspective fully before responding
- 2
Explain your approach clearly and provide reasons or data
- 3
Seek common ground and find a solution that incorporates both viewpoints
- 4
Suggest doing a trial of both approaches to see which works better
- 5
Maintain professionalism and focus on the goal of fixing the boiler
Example Answers
I would first listen to my colleague's viewpoint without interruption. Once they finish, I’d share my perspective and the reasoning behind it. Then, I would suggest we try a combined approach or test both methods to see which resolves the issue more effectively.
Imagine a workflow change is proposed that affects boiler maintenance procedures. How would you approach evaluating this change?
How to Answer
- 1
Identify the key aspects of the proposed change.
- 2
Assess how the change impacts safety and compliance.
- 3
Evaluate potential cost implications and savings.
- 4
Gather input from team members who will be affected.
- 5
Test the proposed change on a small scale before full implementation.
Example Answers
I would start by breaking down the proposed change to understand its key components. Next, I would evaluate its impact on safety regulations and compliance standards. After that, I would analyze the cost implications, including any potential savings or costs. I would also consult with my colleagues who perform boiler maintenance to get their insights. Finally, I would suggest a pilot program to test the change before implementing it fully.
Behavioral Interview Questions
Can you describe a time when you identified a significant issue with a boiler during maintenance? What steps did you take to resolve it?
How to Answer
- 1
Think of a specific incident from your past work experience.
- 2
Describe the issue clearly and why it was significant.
- 3
Outline the steps you took to diagnose and fix the problem.
- 4
Mention any safety protocols you followed or team collaboration.
- 5
Conclude with the outcome and what you learned from the experience.
Example Answers
During a routine maintenance check, I noticed an unusual vibration in the boiler. I inspected the bearings and found they were worn out. I promptly shut down the system for safety, replaced the bearings, and recalibrated the unit. The boiler resumed normal operation, and we avoided potential downtime.
Tell me about a situation where you had to work closely with other technicians. How did you ensure effective communication?
How to Answer
- 1
Identify a specific project or task where collaboration was key
- 2
Describe the main communication tools or methods you used
- 3
Highlight any challenges faced and how you overcame them
- 4
Emphasize the importance of regular updates and feedback loops
- 5
Conclude with the positive outcome of your collaboration
Example Answers
In my previous job, we were tasked with a boiler installation project. I ensured effective communication by setting up daily briefings using a group chat app where we shared updates and progress. When a technical issue arose, we quickly gathered for a team huddle to brainstorm solutions, which helped us complete the project on time.
Don't Just Read Boiler Technician Questions - Practice Answering Them!
Reading helps, but actual practice is what gets you hired. Our AI feedback system helps you improve your Boiler Technician interview answers in real-time.
Personalized feedback
Unlimited practice
Used by hundreds of successful candidates
Describe a complex problem you faced while servicing a boiler and how you approached solving it.
How to Answer
- 1
Identify a specific, challenging boiler issue you encountered.
- 2
Explain the steps you took to diagnose the problem.
- 3
Discuss any tools or methods used in your solution.
- 4
Highlight the outcome and any lessons learned.
- 5
Be concise and focus on your problem-solving skills.
Example Answers
I faced a situation where a commercial boiler was not maintaining pressure. I first checked the pressure gauge and valving for leaks. Using a manometer, I identified a blocked vent stack causing improper airflow. I cleared the blockage and recalibrated the pressure settings, leading to optimal performance. I learned the importance of thorough inspection in troubleshooting.
Have you ever encountered a safety hazard while working on a boiler? What actions did you take?
How to Answer
- 1
Describe a specific incident clearly and succinctly.
- 2
Explain the nature of the safety hazard and why it was a concern.
- 3
Detail the immediate actions you took to address the hazard.
- 4
Mention any long-term changes or procedures implemented afterward.
- 5
Highlight the importance of safety protocols in your response.
Example Answers
I once found a gas leak while inspecting a boiler. I immediately shut off the gas supply and evacuated the area. After informing my supervisor, we engaged our emergency protocol to ensure everyone's safety and called in a specialist to repair the leak. We later reviewed and updated our safety procedures to prevent similar issues.
Describe a time when you needed to learn a new skill or technique quickly to resolve a boiler issue. How did you adapt?
How to Answer
- 1
Start with a specific boiler issue you encountered.
- 2
Explain the urgency of the situation that required learning.
- 3
Describe the method you used to learn the new skill quickly.
- 4
Share the outcome of your efforts and how it resolved the issue.
- 5
Highlight any lessons learned that improved your skills.
Example Answers
During a routine inspection, I discovered a leak in the boiler's pressure relief valve. With only hours to make repairs before a critical process shut down, I promptly researched online manuals and video tutorials. I learned to replace the valve quickly and successfully completed the repair, ensuring minimal downtime.
Have you ever taken the lead on a boiler maintenance project? What was your approach to managing the team?
How to Answer
- 1
Briefly describe the project and your role as a leader.
- 2
Highlight how you organized the team and assigned tasks.
- 3
Emphasize communication methods you used to keep everyone informed.
- 4
Include any challenges faced and how you overcame them.
- 5
Conclude with the project's successful outcome and learning points.
Example Answers
In my previous role, I led a team on a major boiler maintenance overhaul. I organized the team by assigning specific tasks based on each member's strengths. Daily briefings ensured everyone was on the same page. We faced some unexpected equipment failures, but I coordinated quick responses to resolve them. The project finished on time, with zero safety incidents.
Have you ever trained a new technician? What methods did you find most effective?
How to Answer
- 1
Share specific experiences of training a new technician.
- 2
Mention the training methods you used, such as hands-on practice or step-by-step demonstrations.
- 3
Highlight any materials or resources that were helpful during training.
- 4
Emphasize the importance of feedback and encouragement.
- 5
Conclude with outcomes or successes resulting from your training.
Example Answers
Yes, I trained a new technician last summer. I used hands-on practice as the main method, which helped them understand the equipment better. I also provided a detailed checklist and encouraged them to ask questions. Giving positive feedback boosted their confidence, and they quickly became a valuable team member.
Describe a time when you went above and beyond in your role as a boiler technician.
How to Answer
- 1
Pick a specific example that highlights your initiative.
- 2
Focus on the impact of your actions on safety, efficiency, or customer satisfaction.
- 3
Use the STAR method: Situation, Task, Action, Result.
- 4
Quantify your results when possible to show the significance.
- 5
Show how your actions reflect your commitment to your job and responsibilities.
Example Answers
At my previous job, we had a major outage during a cold snap. The heating system failed, and I volunteered to work overtime to diagnose the issue. I discovered a malfunctioning valve, replaced it, and ensured all systems were running efficiently. Our client was able to keep their facility warm, which they greatly appreciated, and we received positive feedback.
Don't Just Read Boiler Technician Questions - Practice Answering Them!
Reading helps, but actual practice is what gets you hired. Our AI feedback system helps you improve your Boiler Technician interview answers in real-time.
Personalized feedback
Unlimited practice
Used by hundreds of successful candidates
Boiler Technician Position Details
Recommended Job Boards
CareerBuilder
www.careerbuilder.com/jobs/boiler-technicianZipRecruiter
www.ziprecruiter.com/Jobs/Boiler-TechnicianThese job boards are ranked by relevance for this position.
Related Positions
- Boiler Repairman
- Boiler Fitter
- Boiler Installer
- Boiler Maker
- Boiler Tester
- Boilermaker Journeyman
- Boilermaker Welder
- Boilermaker
- Pressure Tester
- Manufacturing Assembler
Similar positions you might be interested in.
Ace Your Next Interview!
Practice with AI feedback & get hired faster
Personalized feedback
Used by hundreds of successful candidates
Ace Your Next Interview!
Practice with AI feedback & get hired faster
Personalized feedback
Used by hundreds of successful candidates