Top 30 Button Riveter Interview Questions and Answers [Updated 2025]
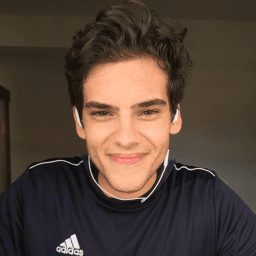
Andre Mendes
•
March 30, 2025
Navigating the interview process for a Button Riveter role can be challenging, but preparation is key. In this post, we provide you with the most common interview questions for this position, along with example answers and valuable tips to help you respond confidently and effectively. Whether you're a seasoned professional or new to the field, this guide will equip you with the insights needed to impress potential employers.
Download Button Riveter Interview Questions in PDF
To make your preparation even more convenient, we've compiled all these top Button Riveterinterview questions and answers into a handy PDF.
Click the button below to download the PDF and have easy access to these essential questions anytime, anywhere:
List of Button Riveter Interview Questions
Situational Interview Questions
If a crucial component shipment is delayed, causing a potential deadline miss, how would you handle the situation?
How to Answer
- 1
Assess the extent of the delay and its impact on production.
- 2
Communicate immediately with the team and management about the issue.
- 3
Explore options for alternative suppliers or components.
- 4
Adjust the project timeline and set new priorities if necessary.
- 5
Document the situation and present a clear plan of action.
Example Answers
I would first evaluate how much the delay affects the overall project timeline. Then, I would inform my team and management to ensure everyone is aware. Simultaneously, I would reach out to alternative suppliers to see if I can procure the necessary components quickly, and I would consider adjusting our project milestones to accommodate the delay.
How would you tackle a situation where you are consistently not meeting production goals?
How to Answer
- 1
Identify the root cause of not meeting goals.
- 2
Communicate openly with the team and supervisors.
- 3
Implement changes in workflow or techniques if necessary.
- 4
Set realistic, incremental goals to improve performance.
- 5
Regularly review progress and adjust strategies.
Example Answers
I would first analyze the production data to find any patterns or issues. If I notice specific areas where we're falling short, I'd bring this up with my team to brainstorm solutions. Communication is key, and together we can adjust our workflow or techniques to better meet our goals.
Don't Just Read Button Riveter Questions - Practice Answering Them!
Reading helps, but actual practice is what gets you hired. Our AI feedback system helps you improve your Button Riveter interview answers in real-time.
Personalized feedback
Unlimited practice
Used by hundreds of successful candidates
If tasked with training a new employee in riveting, how would you ensure they understand the job requirements?
How to Answer
- 1
Start with a clear introduction to riveting, covering tools and safety.
- 2
Use hands-on demonstrations to show effective techniques in real-time.
- 3
Encourage questions throughout the training to clarify doubts.
- 4
Provide written materials for reference that outline the steps involved.
- 5
Follow up with practice sessions to reinforce skills and monitor progress.
Example Answers
I would begin by introducing the employee to the riveting tools and explaining safety protocols. Then, I would demonstrate the riveting process step by step, allowing them to ask questions. After that, I would provide them with a manual that details the riveting procedures and ensure they practice under supervision.
What would you do if you noticed a colleague deviating from the prescribed riveting process?
How to Answer
- 1
Assess the situation calmly and ensure safety first.
- 2
Determine if it's a minor issue or a major deviation.
- 3
Approach the colleague privately to discuss your observation.
- 4
Suggest adherence to the process and explain the reasons.
- 5
If necessary, notify a supervisor only if the issue persists.
Example Answers
I would first observe to see if it's a small mistake or a major risk. If it's significant, I'd speak with them privately, expressing my concern and the importance of following the process. If they don’t respond positively, I would consider informing a supervisor.
How would you handle a situation where your primary riveting tool fails during a critical task?
How to Answer
- 1
Stay calm and assess the situation quickly
- 2
Have a backup riveting tool ready to use
- 3
Communicate with your team about the issue
- 4
Look for quick fixes or temporary solutions
- 5
Document the failure for future reference
Example Answers
If my primary riveting tool fails, I would first remain calm and quickly assess if I can troubleshoot the issue. If it's a simple fix, I would try to resolve it. If not, I would grab my backup tool that I always keep nearby and inform my supervisor about the situation.
Describe how you would address a coworker who is consistently producing subpar riveting work?
How to Answer
- 1
Approach the coworker privately to avoid embarrassment.
- 2
Use specific examples of the subpar work to illustrate the issue.
- 3
Express your desire to help them improve.
- 4
Encourage open communication and ask for their perspective.
- 5
Offer to collaborate or provide support in their work.
Example Answers
I would talk to my coworker privately and mention specific instances where their riveting did not meet standards. I'd let them know I want to help them and ask if there's anything they feel they need support with.
Imagine a customer returns a product due to poor riveting. What actions would you take to investigate and prevent future occurrences?
How to Answer
- 1
Acknowledge the customer's concerns and apologize for the inconvenience.
- 2
Collect details about the returned product, including photos and specifications.
- 3
Investigate the riveting process used for that product batch to identify potential faults.
- 4
Discuss with the team any issues that may have contributed to the poor riveting.
- 5
Implement corrective actions such as additional quality checks or employee training.
Example Answers
I would first apologize to the customer for the inconvenience and request details about the product and the issues. Then, I would examine the riveting process used and check if there were any anomalies in that batch. Finally, I'd propose enhancements to our quality control steps to prevent future problems.
What would you do if you noticed a safety hazard in your workspace that others have overlooked?
How to Answer
- 1
Immediately assess the hazard and ensure your safety first
- 2
Inform your supervisor or safety officer about the hazard
- 3
Document the hazard with details and photos if possible
- 4
Suggest corrective actions or improvements
- 5
Follow up to ensure the issue is addressed
Example Answers
If I noticed a safety hazard, I would first make sure that I am safe. Then, I would inform my supervisor immediately. I would document the hazard with details and photos, to help in resolving it. I believe in proactive solutions, so I might suggest specific corrective actions based on my observations.
Technical Interview Questions
How do you estimate the time required for a riveting job on a new product type?
How to Answer
- 1
Analyze product specifications and design complexity
- 2
Consider the number of rivets and the accessibility of locations
- 3
Factor in the type of rivet being used and equipment setup time
- 4
Consult previous similar projects for time references
- 5
Account for potential challenges and adjustments during the process
Example Answers
I start by reviewing the product design to understand its complexity, then I calculate the number of rivets needed and their locations. I also look at past projects with similar designs to estimate an approximate timeline.
What are the key factors to consider when selecting the appropriate rivet and riveting technique for a job?
How to Answer
- 1
Consider the materials being joined and their thickness
- 2
Evaluate the environmental conditions the riveted joint will face
- 3
Select a rivet type that fits the load requirements of the application
- 4
Decide on a riveting technique based on accessibility and precision needed
- 5
Account for any required inspections or maintenance of the joint over time
Example Answers
When selecting a rivet, I first look at the materials and their thickness to ensure proper fit. I also consider the environment, like temperature and moisture, since that affects durability. The load capacity is crucial, so I choose a rivet type that meets the strength requirements.
Don't Just Read Button Riveter Questions - Practice Answering Them!
Reading helps, but actual practice is what gets you hired. Our AI feedback system helps you improve your Button Riveter interview answers in real-time.
Personalized feedback
Unlimited practice
Used by hundreds of successful candidates
How do you maintain and care for the riveting tools and equipment you use regularly?
How to Answer
- 1
Regularly clean tools after each use to remove debris or residue.
- 2
Inspect tools for wear or damage before every use.
- 3
Lubricate moving parts as per manufacturer's recommendations.
- 4
Store tools in a dry place to prevent rust and corrosion.
- 5
Keep an inventory of tools and schedule regular maintenance checks.
Example Answers
I always clean my riveting tools after every use to ensure they are free of debris. I inspect each tool for any signs of wear or damage before each job. Additionally, I lubricate the moving parts to keep them functioning smoothly and store them in a dry area to avoid any rust.
What are the safety procedures you follow in the process of riveting, and why are they important?
How to Answer
- 1
Start with personal protective equipment like goggles and gloves.
- 2
Mention the importance of machine safety protocols and lockout/tagout procedures.
- 3
Include routine checks of tools and materials for damage or defects.
- 4
Emphasize awareness of surroundings and communication with teammates.
- 5
Conclude with the significance of following these procedures to prevent accidents and ensure quality.
Example Answers
I always wear safety goggles and gloves to protect myself. I also follow machine safety protocols, such as lockout/tagout procedures to prevent accidental machine startups. This is crucial for maintaining a safe work environment.
What are the differences between riveting steel and aluminum? How does that affect the riveting process?
How to Answer
- 1
Identify the material properties of steel and aluminum.
- 2
Discuss differences in strength and weight between the materials.
- 3
Explain how these properties affect rivet selection and installation technique.
- 4
Mention the impact on tooling and equipment used for riveting.
- 5
Highlight any differences in finishing or corrosion resistance.
Example Answers
Steel is stronger and heavier than aluminum, which affects rivet choice; for steel, larger or stronger rivets are usually needed. The installation process may require more force for steel due to its toughness, and we also use different tools.
Can you describe a process improvement you implemented in a riveting process that led to increased efficiency?
How to Answer
- 1
Identify a specific problem in the riveting process you faced.
- 2
Explain the steps you took to analyze and address the issue.
- 3
Highlight the tools or techniques you used for the improvement.
- 4
Share measurable outcomes or results that demonstrate increased efficiency.
- 5
Keep your explanation clear and focused on your role in the improvement.
Example Answers
In my previous role, we had a bottleneck during the riveting process due to inefficient tool usage. I analyzed the workflow and introduced a revised tool setup that eliminated unnecessary steps and reduced cycle time by 15%. This change improved our output significantly and boosted team morale.
How do you ensure each rivet is at the correct specification and securely attached during the process?
How to Answer
- 1
Check the specifications before starting the job
- 2
Inspect the tooling and materials for quality
- 3
Use calibrated equipment for precision
- 4
Perform routine checks during the riveting process
- 5
Conduct a final inspection after rivets are attached
Example Answers
I start by reviewing the specifications for the rivets to ensure I understand the required dimensions. Before I begin, I check that all tools are calibrated and in good working condition. During the process, I regularly inspect the rivets as I work, and after completing each section, I do a final check to ensure everything meets the standards.
What steps do you take if the riveting machine you are using is not functioning as expected?
How to Answer
- 1
Check the machine for obvious issues such as power supply or jams
- 2
Refer to the user manual for troubleshooting tips specific to the model
- 3
Perform basic maintenance tasks like oiling and cleaning parts
- 4
Contact a supervisor or technician if the problem persists
- 5
Document the issue and any steps taken for future reference
Example Answers
If the riveting machine is not functioning, I first check for power supply and any visible jams. If everything looks normal, I consult the user manual for troubleshooting suggestions. If necessary, I perform some routine maintenance like cleaning and oiling relevant parts before escalating to my supervisor.
How does understanding the entire product assembly process help you perform your riveting tasks better?
How to Answer
- 1
Acknowledge that understanding the whole process enhances your attention to detail.
- 2
Explain how knowing upstream and downstream tasks can improve coordination.
- 3
Mention that it helps identify potential problems early on.
- 4
Highlight how it aids in maintaining quality across the assembly line.
- 5
Discuss how it can boost efficiency by optimizing your work timing.
Example Answers
By understanding the entire assembly process, I can ensure my riveting is precise and effectively fits into the workflow. This helps me catch issues early, which improves overall product quality.
What ergonomic considerations do you keep in mind to prevent injuries during work?
How to Answer
- 1
Maintain proper posture when operating the riveter to reduce strain on back and neck.
- 2
Use tools that are ergonomically designed to fit comfortably in your hand.
- 3
Keep work surfaces at the correct height to avoid bending or reaching unnecessarily.
- 4
Take regular breaks to stretch and relieve muscle tension during long hours.
- 5
Arrange your workspace to minimize repetitive motions and awkward positions.
Example Answers
I ensure to maintain a neutral posture while using the riveter, which helps avoid strain injuries.
Don't Just Read Button Riveter Questions - Practice Answering Them!
Reading helps, but actual practice is what gets you hired. Our AI feedback system helps you improve your Button Riveter interview answers in real-time.
Personalized feedback
Unlimited practice
Used by hundreds of successful candidates
Behavioral Interview Questions
How do you handle stress and pressure when working under tight deadlines in a production environment?
How to Answer
- 1
Stay organized by prioritizing tasks based on urgency.
- 2
Maintain clear communication with team members about progress.
- 3
Take short breaks to manage stress levels effectively.
- 4
Focus on solutions rather than problems when challenges arise.
- 5
Practice time management to allocate appropriate time for each task.
Example Answers
I handle stress by prioritizing my tasks to tackle the most urgent ones first. I also communicate regularly with my team to ensure we're aligned and can assist each other if needed.
Provide an example of how you contributed to a continuous improvement initiative in your previous job.
How to Answer
- 1
Identify a specific improvement initiative you were part of.
- 2
Describe your role and actions in that initiative clearly.
- 3
Highlight the impact of your contributions with measurable outcomes.
- 4
Use the STAR method: Situation, Task, Action, Result.
- 5
Keep it relevant to the button riveter position and related skills.
Example Answers
In my previous role, we had an initiative to reduce downtime in our manufacturing line. I noticed that our button assembly area often faced delays due to tool readiness. I suggested implementing a checklist for tool preparation before shifts. This process reduced our downtime by 15%, which helped increase overall productivity.
Don't Just Read Button Riveter Questions - Practice Answering Them!
Reading helps, but actual practice is what gets you hired. Our AI feedback system helps you improve your Button Riveter interview answers in real-time.
Personalized feedback
Unlimited practice
Used by hundreds of successful candidates
Describe a time when you had to be very accurate and detail-oriented. How did you ensure precision in your work?
How to Answer
- 1
Think of a specific project that required high accuracy.
- 2
Explain the methods or tools you used to maintain detail.
- 3
Mention how you checked your work for errors.
- 4
Describe the outcome of your efforts and its impact.
- 5
Use clear examples from your previous experiences.
Example Answers
In my last role, I worked on assembling precision parts for machinery. I created a checklist to ensure each part was installed correctly, and after assembly, I double-checked everything against the specifications. This attention to detail reduced errors by 30%.
Can you give an example of a team project where you had to collaboratively solve a problem? What was your role and how did you contribute?
How to Answer
- 1
Identify a specific team project that involved problem-solving.
- 2
Explain your role and responsibilities in that project.
- 3
Describe the problem the team faced and how you contributed to solving it.
- 4
Highlight any skills or tools you used to facilitate the solution.
- 5
Conclude with the outcome of the project and what you learned.
Example Answers
In my last job, we worked on a project to improve production efficiency. I was responsible for analyzing the workflow and identifying bottlenecks. I collaborated with my teammates to brainstorm solutions, propose a new layout for the work area, and implemented changes that increased output by 20%.
How do you prioritize tasks when working under tight deadlines? Provide an example from your previous work.
How to Answer
- 1
Identify the most critical tasks that impact the project's success.
- 2
Use a simple list or a matrix to rank tasks by urgency and importance.
- 3
Communicate with the team to ensure alignment on priorities.
- 4
Break down larger tasks into manageable steps to track progress more easily.
- 5
Be flexible and ready to adjust priorities as new information arises.
Example Answers
In my last position, I faced a tight deadline on a project. I first listed all tasks and marked them by importance. I realized that two specific tasks were crucial for project completion, so I focused on those first, completing them ahead of time. This allowed me to assist my teammates with their tasks afterward.
Have you ever identified a defect in a finished product? How did you handle the situation?
How to Answer
- 1
Describe the specific defect you found clearly.
- 2
Explain how you discovered the defect during your work.
- 3
Detail the steps you took to address the defect.
- 4
Mention any preventive measures you implemented afterward.
- 5
Conclude with the outcome and what you learned from the experience.
Example Answers
In my previous position, I noticed an incorrect rivet placement during a final inspection. I immediately flagged the issue to my supervisor and we halted production to assess the impact. Together, we corrected the placements and retrained the team on the standards. This led to a 25% reduction in similar defects in future batches.
Tell me about a time when you had to adjust to a significant change in your work environment or process.
How to Answer
- 1
Choose a specific example that highlights your adaptability.
- 2
Explain the change clearly and its impact on your work.
- 3
Describe the steps you took to adjust and any challenges faced.
- 4
Highlight the outcome and what you learned from the experience.
- 5
Relate the experience back to how it makes you suitable for this role.
Example Answers
In my last job as a production assistant, we switched to a new scheduling software that changed our workflow drastically. Initially, it was challenging as I had to learn the new features while keeping up with my tasks. I dedicated extra time after hours to explore the software and attended training sessions. After a month, I became proficient and even created a quick reference guide for my team, which improved overall productivity.
Think of a time when you solved a complex problem at work. What was the issue, and what was the outcome?
How to Answer
- 1
Choose a specific problem related to manufacturing or quality control.
- 2
Explain the steps you took to analyze the problem.
- 3
Discuss the solutions you implemented and why you chose them.
- 4
Quantify the outcomes if possible, such as reduced downtime or increased efficiency.
- 5
Reflect on what you learned from the experience.
Example Answers
At my previous job, we faced a recurring issue with our button riveter jamming during production. I analyzed the machine settings and noticed that the rivet feed mechanism was misaligned. I adjusted the alignment and recalibrated the settings, which reduced the jam rate by 70%, increasing our output and allowing us to meet our production deadlines.
Describe an instance where you took the initiative to improve a process. What challenges did you face and how did you overcome them?
How to Answer
- 1
Choose a specific process you improved.
- 2
Explain what motivated you to take initiative.
- 3
Detail the challenges you encountered during this process.
- 4
Describe the actions you took to overcome those challenges.
- 5
Conclude with the positive outcome and any measurable results.
Example Answers
In my previous job, I noticed that our button rivet application process was slow and prone to errors. Motivated by the desire to enhance efficiency, I researched new techniques and proposed a modified approach. The main challenge was resistance from team members who were used to the old way. I organized a workshop to demonstrate the benefits and successfully got their support. As a result, we improved our application speed by 30%.
Don't Just Read Button Riveter Questions - Practice Answering Them!
Reading helps, but actual practice is what gets you hired. Our AI feedback system helps you improve your Button Riveter interview answers in real-time.
Personalized feedback
Unlimited practice
Used by hundreds of successful candidates
Describe a time when you had to learn something quickly for your job. How did you approach the learning process?
How to Answer
- 1
Identify a specific time when quick learning was required.
- 2
Explain the context of the situation and what you needed to learn.
- 3
Detail the steps you took to learn quickly, such as research, practice, or asking for help.
- 4
Highlight any tools or resources you utilized in the learning process.
- 5
Conclude with the outcome and any skills gained from the experience.
Example Answers
In my previous role as a production assistant, I had to quickly learn a new software for tracking inventory that was introduced suddenly. I first explored the user manual for the software, then watched tutorial videos online. After that, I practiced using the software during breaks. I also reached out to a colleague who was familiar with it for tips. As a result, I was able to use the software effectively by the end of the week, improving our inventory accuracy.
Button Riveter Position Details
Related Positions
- Button Maker
- Belt Buckle Maker
- Valve Maker
- Cushion Maker
- Bell Maker
- Bead Stringer
- Harnessmaker
- Tap Puller
- Bow Maker
- Beader
Similar positions you might be interested in.
Ace Your Next Interview!
Practice with AI feedback & get hired faster
Personalized feedback
Used by hundreds of successful candidates
Ace Your Next Interview!
Practice with AI feedback & get hired faster
Personalized feedback
Used by hundreds of successful candidates