Top 31 Cable Swager Interview Questions and Answers [Updated 2025]
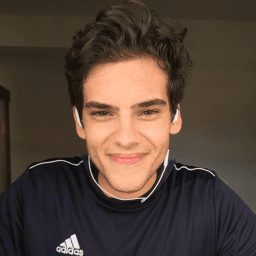
Andre Mendes
•
March 30, 2025
Preparing for a Cable Swager interview can be daunting, but our comprehensive guide has you covered. This blog post compiles the most common interview questions for the Cable Swager role, offering insightful example answers and practical tips to help you respond effectively. Whether you're a seasoned professional or a newcomer to the field, this resource is designed to boost your confidence and enhance your interview performance.
Download Cable Swager Interview Questions in PDF
To make your preparation even more convenient, we've compiled all these top Cable Swagerinterview questions and answers into a handy PDF.
Click the button below to download the PDF and have easy access to these essential questions anytime, anywhere:
List of Cable Swager Interview Questions
Behavioral Interview Questions
Can you describe a time when you had to troubleshoot a malfunctioning cable swaging machine?
How to Answer
- 1
Start by briefly describing the situation and the malfunction.
- 2
Explain the steps you took to diagnose the issue.
- 3
Discuss any tools or methods you used to assist your troubleshooting.
- 4
Share the outcome and what you learned from the experience.
- 5
Emphasize your problem-solving skills and ability to work under pressure.
Example Answers
In my previous job, the cable swager stopped functioning mid-production. I quickly assessed the machine and found that the hydraulic fluid levels were low. I refilled the fluid and checked for leaks, which resolved the issue. This taught me the importance of regular maintenance checks.
Tell me about a time you worked as part of a team to complete a cable installation project successfully.
How to Answer
- 1
Choose a specific project where teamwork was crucial.
- 2
Mention your role and responsibilities in the team.
- 3
Highlight how you communicated and collaborated with team members.
- 4
Include any challenges faced and how the team overcame them.
- 5
Conclude with the positive outcome of the project.
Example Answers
During a recent cable installation for a new office building, I worked with a team of four technicians. My role was to manage cable routing and ensure that all connections met quality standards. We held daily briefings to coordinate our tasks. When we encountered a delay due to a design change, we quickly adapted our plan, which allowed us to complete the project on time and received positive feedback from the client.
Don't Just Read Cable Swager Questions - Practice Answering Them!
Reading helps, but actual practice is what gets you hired. Our AI feedback system helps you improve your Cable Swager interview answers in real-time.
Personalized feedback
Unlimited practice
Used by hundreds of successful candidates
Describe a situation where you had to meet a tight deadline for a swaging project. How did you manage your time?
How to Answer
- 1
Identify a specific project with a tight deadline
- 2
Explain the steps you took to prioritize tasks
- 3
Mention any tools or methods used to track progress
- 4
Share how you communicated with your team or supervisors
- 5
Conclude with the outcome and any lessons learned
Example Answers
In my previous role, I had a project where we needed to complete swaging for 100 connectors in 24 hours. I created a checklist to prioritize tasks and divided the work among team members. We used a shared spreadsheet to track progress in real-time. I kept my team updated every few hours. We finished on time, and it taught me the importance of clear communication.
Have you ever had a disagreement with a coworker about how to handle a cable swaging operation? How did you resolve it?
How to Answer
- 1
Identify the disagreement clearly and what the different viewpoints were.
- 2
Focus on communication and collaboration in resolving the disagreement.
- 3
Provide specific examples of how you listened to your coworker's perspective.
- 4
Explain the solution you reached and how it benefited the operation.
- 5
End with the positive outcome and any lessons learned from the experience.
Example Answers
In a previous job, a coworker and I disagreed on the best cable pressure settings for a swaging operation. I took the time to listen to his methods, and after discussing our approaches, we decided to run tests with both settings. Ultimately, we found that combining elements of both methods led to improved results.
Can you give an example of a time when you took the lead on a cable installation or swaging project?
How to Answer
- 1
Choose a specific project you led.
- 2
Describe your role and responsibilities clearly.
- 3
Highlight the challenges you faced and how you overcame them.
- 4
Mention any positive outcomes or results from your leadership.
- 5
Reflect on what you learned from the experience.
Example Answers
In my previous job, I led a team installing a high-tensile cable for a construction site. I coordinated with the crew, ensuring everyone was aware of their tasks. We faced tight deadlines and heavy weather conditions, but I organized the workflow to keep us on track, resulting in a successful installation ahead of schedule.
Can you provide an example of a project where you improved the efficiency of a cable swaging operation?
How to Answer
- 1
Identify a specific project where you focused on cable swaging efficiency
- 2
Explain the methods you employed to improve the process
- 3
Include measurable results such as time saved or production increased
- 4
Mention any tools or technologies you used
- 5
Share feedback from team members or supervisors on the improvements
Example Answers
In my previous role, I led a project to optimize the cable swaging process. By analyzing workflow and introducing a new hydraulic press, we reduced the cycle time by 20%. This improved our overall output by 30%, and the team was able to meet increased demand without overtime.
What is a significant lesson you've learned from a mistake made while swaging cables?
How to Answer
- 1
Identify a specific mistake you made with swaging cables.
- 2
Explain how you realized it was a mistake and the impact it had.
- 3
Describe the lesson learned from that experience.
- 4
Ensure to highlight how you applied the lesson to improve your skills.
- 5
Conclude with how this lesson has shaped your approach to future swaging tasks.
Example Answers
I once miscalculated the length of cable needed for a project, resulting in a swaged connection that was too short. I realized this after attempting to fit the cable during installation. The lesson was to always double-check measurements before swaging. Since then, I’ve developed a system to verify lengths to prevent this mistake from happening again.
How do you handle constructive criticism regarding your work in cable swaging?
How to Answer
- 1
Listen actively to the feedback without interrupting.
- 2
Acknowledge the feedback and thank the person for their insights.
- 3
Reflect on the feedback and consider how it can improve your skills.
- 4
Ask clarifying questions to fully understand the criticism.
- 5
Implement relevant suggestions in future work to show growth.
Example Answers
When I receive constructive criticism, I first listen carefully and don't interrupt. I appreciate the feedback and often thank the person for pointing out areas I can improve. Then, I take some time to reflect on how I can apply those suggestions, and in my next project, I make sure to incorporate what I've learned.
Technical Interview Questions
What types of cable swaging machines have you operated, and what are the key features you consider when using them?
How to Answer
- 1
Identify specific machines you have experience with
- 2
Mention their capabilities or features like hydraulic or manual operation
- 3
Discuss the importance of material compatibility and size limitations
- 4
Talk about safety features and ease of maintenance
- 5
Emphasize your ability to troubleshoot and handle various applications
Example Answers
I have operated both hydraulic and pneumatic cable swaging machines. I consider features like the maximum swage pressure and the compatibility with different cable materials as key when choosing which machine to use.
What types of cables and fittings are you most familiar with when it comes to swaging?
How to Answer
- 1
Identify specific types of cables you have worked with, like steel wire or fiber optic.
- 2
Mention any relevant fittings, such as swage sleeves or end fittings.
- 3
Briefly explain your experience with each type and its applications.
- 4
Focus on quality and safety standards you follow when swaging.
- 5
Share any relevant training or certifications you have related to cable swaging.
Example Answers
I have significant experience with 1/8 inch steel wire ropes and use aluminum swage sleeves for securing them. In my previous job, I swaged cables for overhead lifting applications, ensuring all fittings met industry safety standards.
Don't Just Read Cable Swager Questions - Practice Answering Them!
Reading helps, but actual practice is what gets you hired. Our AI feedback system helps you improve your Cable Swager interview answers in real-time.
Personalized feedback
Unlimited practice
Used by hundreds of successful candidates
What safety protocols do you follow when operating swaging equipment?
How to Answer
- 1
Always wear appropriate personal protective equipment such as gloves, safety glasses, and hard hats.
- 2
Ensure that the work area is clear of unnecessary personnel and obstacles before starting.
- 3
Perform a pre-operation inspection of the swaging equipment to check for any wear or damage.
- 4
Follow the manufacturer’s operating instructions carefully while using the equipment.
- 5
Be aware of the emergency stop procedures and know how to quickly disengage the machine if needed.
Example Answers
I always wear my safety gloves and goggles when operating swaging equipment. Before I start, I check the area for any hazards and ensure it's clear.
How do you ensure accuracy and precision in your swaging operations?
How to Answer
- 1
Always calibrate the swaging machine before use to ensure settings are correct.
- 2
Use high-quality materials and check for any defects before starting the operation.
- 3
Consistently monitor and measure the swaging results throughout the process.
- 4
Follow established procedures and specifications for each type of swage to avoid errors.
- 5
Document each operation to track any discrepancies and make adjustments as needed.
Example Answers
I ensure accuracy by calibrating the machine each time before starting my swaging operations, and I always check the materials for quality to avoid defects.
Can you describe the maintenance procedures you perform on swaging machines?
How to Answer
- 1
Start by outlining the daily checks you perform on the machine.
- 2
Mention specific lubrication points and maintenance schedules.
- 3
Talk about any inspections for wear and tear that you conduct regularly.
- 4
Include any calibration procedures you follow to ensure accuracy.
- 5
Emphasize the importance of safety and compliance with manufacturer guidelines.
Example Answers
I perform daily checks to ensure all moving parts are lubricated according to the schedule outlined by the manufacturer. I also inspect the dies and tooling for wear and replace them as necessary to maintain accuracy.
How do you determine the proper specifications for a swaged connection based on the cable type?
How to Answer
- 1
Identify the type of cable and its material properties.
- 2
Refer to manufacturer specifications for swaging tools and dies.
- 3
Consider the environment where the connection will be used.
- 4
Determine the load and usage requirements for the connection.
- 5
Test a sample connection if possible to ensure strength and durability.
Example Answers
To determine the proper specifications, I first identify the cable type and its material properties. For example, if it's stainless steel, I check the manufacturer's guidelines on swaging tools. I also consider the environmental factors, like exposure to moisture or chemicals.
What methods do you use to test the integrity of a cable after swaging?
How to Answer
- 1
Describe visual inspection techniques for connectors and swaged areas.
- 2
Mention using a calibrated load test to verify strength.
- 3
Explain the importance of conducting a continuity test.
- 4
Include using specialized equipment like cable testers for resistance checks.
- 5
Highlight the significance of documenting test results for quality assurance.
Example Answers
After swaging, I perform a visual inspection to check for any cracks or incomplete swages. Then, I conduct a calibrated load test to ensure the cable can handle its rated load without failure. Additionally, I do a continuity test to confirm that there are no breaks in the cable.
Describe the steps you take when calibrating a swaging machine.
How to Answer
- 1
Identify and gather all necessary tools and materials for calibration.
- 2
Review the manufacturer's specifications for swaging machine settings.
- 3
Check the machine's current calibration against a standard.
- 4
Adjust settings as needed to align with specifications.
- 5
Test the machine with a sample before finalizing calibration.
Example Answers
First, I gather all necessary tools like calipers and wrenches. Then, I review the manufacturer's settings to ensure I know the required specs. I check the current calibration using a standard sample. After making any necessary adjustments, I run a test swage to confirm accuracy.
What industry standards do you follow in your cable swaging processes?
How to Answer
- 1
Mention specific industry standards relevant to cable swaging, such as ASTM, ISO, or IEC standards.
- 2
Discuss your knowledge of safety regulations and best practices during the swaging process.
- 3
Highlight any relevant certifications you may hold that demonstrate compliance with these standards.
- 4
Explain how you ensure quality control in your swaging processes in line with these standards.
- 5
Provide examples of past experiences where you successfully adhered to these standards.
Example Answers
I follow ASTM standards for cable swaging which ensure the quality and performance of the cables. I also adhere to strict safety regulations to maintain a safe work environment.
What diagnostic techniques do you employ when troubleshooting swaging equipment?
How to Answer
- 1
Start with visual inspections to look for obvious signs of wear or damage.
- 2
Check the hydraulic pressure levels to ensure they meet specifications.
- 3
Use multimeters to test electrical connections and sensors for faults.
- 4
Review error codes or diagnostic indicators from the equipment's interface if available.
- 5
Perform operational tests to observe equipment performance under load.
Example Answers
I usually begin with a thorough visual inspection to check for any damaged components or pressure leaks. Next, I measure the hydraulic pressure to verify it's at the correct levels. If everything looks good visually, I use a multimeter to check the electrical connections. I also refer to the equipment's diagnostic codes for any errors.
Don't Just Read Cable Swager Questions - Practice Answering Them!
Reading helps, but actual practice is what gets you hired. Our AI feedback system helps you improve your Cable Swager interview answers in real-time.
Personalized feedback
Unlimited practice
Used by hundreds of successful candidates
How do you stay updated on compliance regulations related to cable swaging?
How to Answer
- 1
Regularly check industry websites for updates on regulations.
- 2
Subscribe to newsletters or publications related to cable manufacturing and compliance.
- 3
Attend workshops or training sessions focused on compliance and safety standards.
- 4
Network with industry professionals to share insights on regulatory changes.
- 5
Review and participate in online forums or discussion groups about compliance issues.
Example Answers
I regularly check the ANSI and ISO websites to stay informed about changes in regulations affecting cable swaging. I also subscribe to trade publications that focus on compliance.
What training or certifications do you have that are relevant to your role as a Cable Swager?
How to Answer
- 1
List relevant certifications like OSHA or equipment manufacturer training
- 2
Highlight any hands-on experience during training
- 3
Mention specific skills learned that apply to cable swaging
- 4
Include any safety training you've completed
- 5
Be concise and focus on certifications directly relevant to cable swaging
Example Answers
I hold a certification in cable swaging from ABC Training Institute and have completed practical workshops that covered the operation of hydraulic swaging tools.
Situational Interview Questions
If a cable swaging machine jams during a critical operation, what steps would you take to address the situation?
How to Answer
- 1
Stay calm and assess the situation immediately
- 2
Follow the safety protocols to ensure the machine is powered down
- 3
Attempt to identify the cause of the jam without risking injury
- 4
Use the appropriate tools to clear the jam only if safe to do so
- 5
Notify a supervisor if the issue cannot be resolved quickly
Example Answers
I would first ensure that the machine is safely powered down to avoid any accidents. Then, I would inspect the area around the jam to see if I can identify what caused it. If it's safe, I would try to clear the jam with the proper tools. If not or if there’s any uncertainty, I would notify my supervisor immediately.
What would you do if you noticed a coworker not following safety guidelines while using the swaging equipment?
How to Answer
- 1
Stay calm and approach the situation without confrontation
- 2
Assess the immediate risk to yourself and others
- 3
Politely remind your coworker of the safety guidelines
- 4
If the behavior continues, report it to a supervisor
- 5
Always prioritize safety and the well-being of the team
Example Answers
I would first make sure I was safe and then approach my coworker calmly to remind them about the safety guidelines. We all need to look out for each other.
Don't Just Read Cable Swager Questions - Practice Answering Them!
Reading helps, but actual practice is what gets you hired. Our AI feedback system helps you improve your Cable Swager interview answers in real-time.
Personalized feedback
Unlimited practice
Used by hundreds of successful candidates
If you were behind schedule on a swaging project, how would you prioritize your tasks to catch up?
How to Answer
- 1
Identify critical tasks that directly impact project deadlines
- 2
Assess the available resources and workforce for task allocation
- 3
Communicate with the team to ensure everyone is aligned on priorities
- 4
Create a revised timeline for the remaining tasks, focusing on efficiency
- 5
Monitor progress closely and adjust priorities as needed
Example Answers
I would first identify which tasks are critical to the project's completion and focus on those. Then, I'd assess our resources and assign tasks to team members accordingly. Communication is vital, so I'd ensure everyone knows the new priorities. Finally, I would create a revised timeline to track our progress and adjust as necessary.
How would you handle a situation where a team member disagrees with your approach to a swaging technique?
How to Answer
- 1
Listen to the team member's perspective and acknowledge their concerns
- 2
Explain your approach and the rationale behind it clearly
- 3
Discuss the pros and cons of both techniques collaboratively
- 4
Be open to compromise or adjusting your technique if valid points are made
- 5
Maintain a positive team atmosphere regardless of differing opinions
Example Answers
I would start by listening carefully to my team member's concerns. I would then explain my swaging technique and why I believe it works well, presenting any data to support my view. Finally, we would discuss both approaches to find the best solution together.
What would you do if a customer expressed dissatisfaction with the quality of the swaged cables?
How to Answer
- 1
Listen carefully to the customer's concerns and acknowledge their feelings
- 2
Apologize for any inconvenience caused by the cable quality
- 3
Ask specific questions to understand the details of their dissatisfaction
- 4
Offer solutions, such as replacing the cables or providing a refund
- 5
Follow up to ensure the customer is satisfied with the resolution
Example Answers
I would start by listening to the customer and acknowledge their dissatisfaction. I would apologize and ask specific questions to understand the issue better. Depending on their feedback, I might offer to replace the cables or process a refund. Lastly, I'd follow up to ensure they are satisfied with the resolution.
How would you assess risks before starting a new swaging project?
How to Answer
- 1
Identify potential hazards specific to the swaging environment.
- 2
Evaluate the materials and tools for any previous performance issues.
- 3
Consult with experienced team members for insights and historical data.
- 4
Develop a risk management plan that includes mitigation strategies.
- 5
Ensure compliance with safety regulations and company policies.
Example Answers
I would start by identifying hazards related to the specific materials and tools used in swaging. Then, I'd consult with colleagues who have worked on similar projects to gather their insights. Based on this information, I'd create a risk management plan to address any potential issues.
If you were managing a swaging team, how would you motivate them to achieve production targets?
How to Answer
- 1
Set clear, achievable goals and communicate them effectively.
- 2
Recognize and reward individual and team achievements regularly.
- 3
Encourage open communication and feedback to understand team challenges.
- 4
Provide training and development opportunities to enhance skills.
- 5
Create a positive team culture that promotes collaboration and support.
Example Answers
I would set clear and specific production targets for the team and ensure everyone understands what is expected. I would also recognize achievements publicly, providing incentives for reaching targets to keep morale high.
Imagine you are assigned a high-priority swaging project with limited resources. How would you manage it?
How to Answer
- 1
Assess the project requirements and priorities immediately
- 2
Identify the key resources needed and any shortfalls
- 3
Communicate with stakeholders to set realistic expectations
- 4
Delegate tasks based on team strengths and available skills
- 5
Implement a timeline with milestones for tracking progress
Example Answers
I would start by clearly defining the project scope and priorities. Then, I would assess our available resources and identify any gaps. I would communicate with the team to set achievable goals and make sure everyone is aware of their roles. Finally, I would establish a timeline with key milestones to monitor our progress effectively.
If you had to collaborate with another department (like design) for a project, how would you approach it?
How to Answer
- 1
Identify key stakeholders in the design department.
- 2
Set clear communication channels from the start.
- 3
Schedule regular check-ins to ensure alignment.
- 4
Be open to feedback while sharing your technical insights.
- 5
Document decisions and action points for future reference.
Example Answers
I would begin by identifying the key stakeholders in the design department and establish clear communication channels. We would set up regular check-ins to ensure our work aligns with project goals, and I would be open to their feedback, while also sharing my technical expertise to help refine the project.
If you were tasked with improving the current swaging process, what innovative ideas would you propose?
How to Answer
- 1
Analyze current swaging techniques for inefficiencies.
- 2
Consider automation to enhance precision and speed.
- 3
Explore new materials that could reduce wear and tear.
- 4
Implement feedback loops from operators for practical insights.
- 5
Utilize data analysis for optimizing parameters in real-time.
Example Answers
I would start by analyzing the current processes to identify bottlenecks. Introducing automation could enhance precision, while exploring new materials could extend tool lifespan.
Don't Just Read Cable Swager Questions - Practice Answering Them!
Reading helps, but actual practice is what gets you hired. Our AI feedback system helps you improve your Cable Swager interview answers in real-time.
Personalized feedback
Unlimited practice
Used by hundreds of successful candidates
Cable Swager Position Details
Recommended Job Boards
CareerBuilder
www.careerbuilder.com/jobs?q=cable+swagerZipRecruiter
www.ziprecruiter.com/Jobs/-Cable-SwagerThese job boards are ranked by relevance for this position.
Related Positions
- Cable Strander
- Wire Bender
- Stapler
- Coiler
- Pneumatic Riveter
- Key Cutter
- Metal Worker
- Spool Winder
- Spring Coiler
- Metal Riveter
Similar positions you might be interested in.
Ace Your Next Interview!
Practice with AI feedback & get hired faster
Personalized feedback
Used by hundreds of successful candidates
Ace Your Next Interview!
Practice with AI feedback & get hired faster
Personalized feedback
Used by hundreds of successful candidates