Top 30 Carburetor Specialist Interview Questions and Answers [Updated 2025]
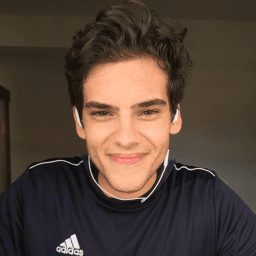
Andre Mendes
•
March 30, 2025
Looking to ace your upcoming interview for a Carburetor Specialist role? Our latest blog post compiles the most common interview questions for this specialized position, complete with example answers and insightful tips to help you respond effectively. Whether you're a seasoned professional or new to the field, this guide offers valuable strategies to confidently showcase your expertise and secure your desired job.
Download Carburetor Specialist Interview Questions in PDF
To make your preparation even more convenient, we've compiled all these top Carburetor Specialistinterview questions and answers into a handy PDF.
Click the button below to download the PDF and have easy access to these essential questions anytime, anywhere:
List of Carburetor Specialist Interview Questions
Behavioral Interview Questions
Can you describe a time when you diagnosed a complex issue with a carburetor? What steps did you take to resolve it?
How to Answer
- 1
Start with the specific problem you faced with the carburetor.
- 2
Outline the tools and methods you used for diagnosis.
- 3
Describe the steps you took to test and verify your diagnosis.
- 4
Explain the solution you implemented and why it worked.
- 5
Conclude with the outcome and any lessons learned from the experience.
Example Answers
While servicing a classic car, I noticed it had poor acceleration. I used a vacuum gauge and observed erratic readings, indicating a potential air leak. I checked the gaskets and found one was worn out. After replacing it, the car's performance improved significantly, showcasing the importance of thorough diagnostics.
Don't Just Read Carburetor Specialist Questions - Practice Answering Them!
Reading helps, but actual practice is what gets you hired. Our AI feedback system helps you improve your Carburetor Specialist interview answers in real-time.
Personalized feedback
Unlimited practice
Used by hundreds of successful candidates
Have you ever had to train a new employee on carburetor repairs? What approach did you take and what was the outcome?
How to Answer
- 1
Start with a brief context of the situation.
- 2
Explain your training methods, like hands-on demonstrations or written guides.
- 3
Mention any specific challenges you encountered.
- 4
Share the results of your training, such as improved skills or faster repairs.
- 5
Highlight any positive feedback from the new employee.
Example Answers
I trained a new hire on carburetor repairs by first providing a hands-on demonstration of the basic components. We then worked on real carburetors together. Initially, they struggled with adjustments, but after a week, their confidence grew, and they could handle repairs independently, resulting in faster turnaround times in our shop.
Describe a situation where your attention to detail made a significant difference in the carburetor service you provided.
How to Answer
- 1
Think of a specific incident where a small detail impacted the service outcome.
- 2
Highlight how noticing or correcting the detail improved performance or customer satisfaction.
- 3
Use clear and straightforward language to describe the situation.
- 4
Include any tools or methods you used to ensure accuracy.
- 5
Emphasize the positive outcome from your attention to detail.
Example Answers
While servicing a classic car's carburetor, I noticed a small crack in the float chamber. I replaced it immediately, which prevented fuel leaks and ensured optimal engine performance. The customer was thrilled with the smooth driving experience afterward.
Have you ever had to adapt to a new type of carburetor technology or repair tool? How did you manage the transition?
How to Answer
- 1
Identify the specific technology or tool you adapted to.
- 2
Explain the learning process you used to understand it.
- 3
Describe any challenges faced during the transition.
- 4
Highlight results or improvements achieved post-adaptation.
- 5
Emphasize your willingness to learn and grow professionally.
Example Answers
I recently adapted to a new electronic fuel injection system. I took online courses and read manuals to get familiarized. I encountered some initial programming challenges, but I sought help from colleagues, which helped me troubleshoot effectively. As a result, I improved my calibration speed by 30%.
Describe a time when you had a disagreement with a co-worker about the best way to repair a carburetor. How did you resolve it?
How to Answer
- 1
Describe the specific disagreement clearly.
- 2
Mention the different repair methods considered.
- 3
Discuss how you communicated with your co-worker.
- 4
Explain the outcome and what was learned from the situation.
- 5
Emphasize teamwork and respect for differing opinions.
Example Answers
In a previous job, a co-worker and I disagreed on whether to replace or clean a carburetor. I believed cleaning was sufficient, while he insisted on replacing it. We each presented our reasoning and the pros and cons of our methods. Ultimately, we agreed to clean it first and monitor its performance. It worked well, and I learned the importance of compromise.
What drives your passion for working with carburetors, and how has that passion influenced your career?
How to Answer
- 1
Share a personal story about your first experience with carburetors.
- 2
Explain how your passion has shaped your skills and knowledge in the field.
- 3
Discuss any relevant projects or achievements linked to your interest.
- 4
Mention how you keep updated with industry trends and advancements.
- 5
Conclude with your long-term goals related to carburetor technology.
Example Answers
My passion for carburetors began when I restored my first classic car as a teenager. That hands-on experience sparked my love for mechanical systems. Since then, I've dedicated my career to mastering carburetor tuning and have even led workshops, helping others appreciate this technology. I stay current by attending automotive seminars, which helps me bring fresh insights to my work.
Can you describe a time when you successfully educated a customer about carburetor maintenance?
How to Answer
- 1
Choose a specific incident that highlights your teaching ability
- 2
Focus on the customer's initial lack of knowledge
- 3
Explain the method you used to educate them
- 4
Share the positive outcome or feedback received
- 5
Keep it brief but detailed enough to illustrate your point
Example Answers
I had a customer who was confused about how often to clean their carburetor. I showed them the steps using a demo carburetor, explaining each part's role and importance. They appreciated the hands-on approach and went home feeling confident to maintain their equipment. Later, they returned saying their engine was running smoother than ever.
Technical Interview Questions
Can you explain how a carburetor regulates the air-fuel mixture and its impact on engine performance?
How to Answer
- 1
Start by defining the carburetor's purpose in the air-fuel mixture regulation.
- 2
Explain the main components involved, like the venturi and the float chamber.
- 3
Discuss how adjustments in the mixture affect engine operation and efficiency.
- 4
Mention the impact of a rich vs. lean mixture on performance.
- 5
Conclude with a note on tuning and its importance for optimal performance.
Example Answers
A carburetor regulates the air-fuel mixture by using the venturi effect to create a vacuum that draws fuel into the airflow. The float chamber maintains fuel levels, ensuring consistent delivery. Proper mixture tuning affects combustion efficiency, where a rich mixture can lead to power loss, while a lean mixture increases the risk of engine knocking.
What are the common symptoms of a failing carburetor and how do you go about diagnosing these issues?
How to Answer
- 1
Identify symptoms like rough idling, stalling, or poor fuel economy.
- 2
Check for fuel leaks or excess carbon build-up.
- 3
Test the fuel system pressure and inspect the air-fuel mixture.
- 4
Use diagnostic tools for error codes if available.
- 5
Perform a visual inspection for damaged components.
Example Answers
Common symptoms include rough idling and stalling. To diagnose, I check for fuel leaks and inspect the air-fuel mixture. I also use tools to measure fuel pressure and look for carbon build-up.
Don't Just Read Carburetor Specialist Questions - Practice Answering Them!
Reading helps, but actual practice is what gets you hired. Our AI feedback system helps you improve your Carburetor Specialist interview answers in real-time.
Personalized feedback
Unlimited practice
Used by hundreds of successful candidates
What specific tools and techniques do you regularly utilize when performing carburetor repairs?
How to Answer
- 1
Mention common tools like screwdrivers, wrenches, and cleaning solvents
- 2
Discuss techniques for disassembly and reassembly of carburetors
- 3
Highlight the importance of tuning and adjusting air-fuel mixtures
- 4
Include any diagnostic tools you use for troubleshooting
- 5
Share your approach to inspecting and testing carburetor components
Example Answers
I frequently use screwdrivers, various wrenches, and carburetor cleaner during repairs. When disassembling, I ensure to keep parts organized. I always adjust the air-fuel mixture to optimal levels for performance.
How do you ensure compliance with environmental regulations when working on carburetors?
How to Answer
- 1
Stay updated on local and national environmental regulations related to automotive repairs.
- 2
Use environmentally friendly cleaning products and proper disposal methods for waste materials.
- 3
Implement best practices for emissions testing and adjustments to meet regulatory standards.
- 4
Regularly train on compliance protocols and ensure all team members are aware of procedures.
- 5
Document all procedures and report any compliance issues promptly.
Example Answers
I stay informed about environmental regulations by subscribing to industry newsletters and attending workshops. I ensure waste materials are disposed of properly and use eco-friendly products during maintenance.
Describe the process you use to identify the correct replacement parts for a specific carburetor model.
How to Answer
- 1
Start by gathering the carburetor model number and specifications.
- 2
Use manufacturer databases or catalogs to find compatible parts.
- 3
Cross-reference the part numbers with trusted suppliers.
- 4
Check for updated parts or revisions that may affect compatibility.
- 5
Consult with experienced colleagues or forums for insights on rare parts.
Example Answers
I start by identifying the carburetor model number and its specifications. Then, I access the manufacturer’s database to find the compatible replacement parts and cross-check with suppliers to ensure accuracy.
What routine maintenance procedures do you recommend for carburetor longevity?
How to Answer
- 1
Regularly check and clean the air filter to prevent debris from entering the carburetor.
- 2
Inspect and clean the fuel lines to avoid clogs that can harm the carburetor function.
- 3
Use a fuel stabilizer to prevent varnish buildup when the equipment is not in use.
- 4
Adjust the carburetor settings as needed to maintain optimal fuel-air mixture.
- 5
Periodically check for leaks and replace any worn or damaged gaskets.
Example Answers
I recommend regularly checking and cleaning the air filter to prevent debris buildup. Also, cleaning fuel lines is crucial to keep the carburetor functioning smoothly.
How does the quality of fuel impact the performance of a carburetor, and what advice do you give clients on this?
How to Answer
- 1
Explain how poor fuel quality can lead to engine knocking and poor combustion.
- 2
Discuss the importance of proper octane ratings for the specific engine type.
- 3
Advise clients on using fuel additives for cleaning deposits.
- 4
Suggest regular fuel quality checks and using reputable fuel sources.
- 5
Emphasize the role of water and contaminants in fuel affecting carburetor function.
Example Answers
Fuel quality significantly impacts carburetor performance. Poor quality fuel can cause engine knocking and lead to incomplete combustion. I advise clients to check the octane rating suitable for their engine and consider using fuel additives to keep the carburetor clean.
How do you ensure that a carburetor is appropriately calibrated after repair? What metrics do you use?
How to Answer
- 1
Start with a visual inspection to check for any obvious issues
- 2
Use a carburetor synchronizer to adjust air flow between cylinders
- 3
Measure fuel delivery using a flow gauge to ensure proper fuel output
- 4
Check idle speed and mixture settings with a tachometer and exhaust gas tester
- 5
Test drive the vehicle to observe performance and make final adjustments
Example Answers
I start by visually inspecting the carburetor for any leaks or misalignments. Then, I use a carburetor synchronizer to ensure even air flow across all cylinders. After that, I measure fuel delivery with a flow gauge to confirm adequate output before setting the idle speed and mixture using a tachometer.
What are the key differences between a manual and automatic choke in carburetors?
How to Answer
- 1
Define manual and automatic chokes clearly.
- 2
Explain how each type operates during starting.
- 3
Highlight the main benefits of each choke type.
- 4
Mention common applications for both types.
- 5
Keep technical jargon to a minimum for clarity.
Example Answers
A manual choke requires the driver to pull a lever to enrich the fuel mixture during cold starts, while an automatic choke does this process automatically based on engine temperature.
How do you adjust a carburetor for optimal performance in different driving conditions?
How to Answer
- 1
Identify the specific driving conditions such as altitude or weather.
- 2
Adjust the air-fuel mixture by changing the jet size or needle position.
- 3
Tweak the idle speed screw for smooth idling under varying loads.
- 4
Consider the choke setting for cold starts and low temperatures.
- 5
Test the vehicle's performance after adjustments and make further tweaks if necessary.
Example Answers
In high-altitude conditions, I would adjust the air-fuel mixture by leaning it out to compensate for thinner air, ensuring the engine runs efficiently.
Don't Just Read Carburetor Specialist Questions - Practice Answering Them!
Reading helps, but actual practice is what gets you hired. Our AI feedback system helps you improve your Carburetor Specialist interview answers in real-time.
Personalized feedback
Unlimited practice
Used by hundreds of successful candidates
What types of carburetor components are most prone to failure, and how can they be prevented?
How to Answer
- 1
Identify common carburetor components like jets, gaskets, and floats.
- 2
Explain specific failure causes such as clogging or deterioration.
- 3
Suggest routine maintenance practices like cleaning and inspection.
- 4
Discuss the importance of using quality fuels to avoid failures.
- 5
Highlight the role of proper installation and adjustment in prevention.
Example Answers
Common components prone to failure include jets and floats. Jets can clog due to dirty fuel, while floats may deteriorate over time. Regular cleaning and using high-quality fuel can prevent issues.
Situational Interview Questions
If a customer reports that their vehicle is stalling even after you serviced the carburetor, how would you approach resolving the issue?
How to Answer
- 1
Listen carefully to the customer to understand the symptoms and conditions of the stalling.
- 2
Verify any recent changes made during the carburetor service that could affect performance.
- 3
Check other potential causes such as ignition issues, fuel supply, or vacuum leaks.
- 4
Conduct a thorough inspection of the carburetor and related components to identify any overlooked problems.
- 5
Communicate clearly with the customer about your findings and the steps you will take to resolve the issue.
Example Answers
I would first listen to the customer to gather detailed information about when the stalling occurs. Then, I would double-check my work on the carburetor and inspect other systems like the ignition and fuel supply.
How would you handle a situation where a customer is unhappy with your carburetor service? What steps would you take to remedy the situation?
How to Answer
- 1
Listen carefully to the customer's concerns without interrupting.
- 2
Acknowledge their feelings and show empathy for the situation.
- 3
Assess the issue by asking clarifying questions.
- 4
Offer a clear solution, whether it's a repair, refund, or other compensation.
- 5
Follow up after the resolution to ensure the customer is satisfied.
Example Answers
I would first listen to the customer's concerns attentively and acknowledge their feelings. After understanding the issue, I would discuss possible solutions like a free reservice or a refund. Finally, I would follow up to ensure they feel satisfied with the outcome.
Don't Just Read Carburetor Specialist Questions - Practice Answering Them!
Reading helps, but actual practice is what gets you hired. Our AI feedback system helps you improve your Carburetor Specialist interview answers in real-time.
Personalized feedback
Unlimited practice
Used by hundreds of successful candidates
You discover that a carburetor model has been recalled due to a defect during your service. How do you proceed?
How to Answer
- 1
Immediately stop servicing the affected carburetor model.
- 2
Notify your supervisor and report the recall details.
- 3
Inform the customer about the recall and the necessary steps.
- 4
Document the incident and any customer interactions.
- 5
Follow company protocols for handling recalls and defects.
Example Answers
I would stop any ongoing service on the recalled carburetor, inform my supervisor about the recall, and communicate to the customer what the recall means for their service. Then, I would document the situation and make sure we follow the proper protocols for recall handling.
You have multiple carburetor service requests, including a rush job and a complicated repair. How would you prioritize these tasks?
How to Answer
- 1
Assess the urgency of each request based on customer needs and deadlines
- 2
Evaluate the complexity of the repairs required
- 3
Consider the potential impact on overall shop workflow and customer satisfaction
- 4
Communicate clearly with customers about expected timelines
- 5
Keep a checklist to track progress on multiple tasks
Example Answers
I would first address the rush job since it has immediate customer expectations. After completing that, I would tackle the complicated repair by breaking it down into manageable steps to ensure quality.
If you notice an ongoing issue with a carburetor that traditional diagnostics can't resolve, what alternative methods would you explore?
How to Answer
- 1
Consider using visual inspection to identify any physical damage or wear.
- 2
Look into historical data and maintenance records for repeated issues.
- 3
Analyze fuel quality and supply to rule out contamination problems.
- 4
Conduct a leak-down test to check for air leaks affecting performance.
- 5
Consult with colleagues or online forums for additional insights and experiences.
Example Answers
I would start by performing a detailed visual inspection to check for any visible damage or wear. Next, I would review the maintenance history to see if this issue has occurred before, and consider the quality of the fuel being used. If needed, I would perform a leak-down test to identify any potential air leaks.
A carburetor is leaking fuel. Describe the step-by-step approach you would take to troubleshoot and solve this issue.
How to Answer
- 1
Inspect the carburetor for visible leaks or fuel stains
- 2
Check the float level and adjust if necessary
- 3
Examine the gasket and O-rings for wear or damage
- 4
Ensure the fuel line connections are tight and not cracked
- 5
Test the carburetor after repairs to confirm the leak is fixed
Example Answers
First, I would visually inspect the carburetor to find any obvious leaks. Then, I would check the float level and adjust it if needed. After that, I would examine the gasket and O-rings for any signs of wear. I would also ensure all fuel line connections are secure. Finally, I would test the carburetor to make sure the leak is resolved.
You have a tight deadline for completing a carburetor service. How would you ensure you meet the deadline while maintaining quality?
How to Answer
- 1
Prioritize tasks by identifying critical components that need immediate attention.
- 2
Prepare your tools and parts in advance to avoid delays.
- 3
Use a checklist to ensure all steps are completed without skipping quality checks.
- 4
Communicate with your team to delegate tasks effectively if possible.
- 5
Stay focused and avoid distractions to work efficiently.
Example Answers
I would start by prioritizing the key components of the carburetor service that need immediate attention. Preparing my tools and parts in advance would save time. I would also use a checklist to ensure quality at each step without missing any critical details.
Imagine you have multiple carburetors that each require repair work—some are more complicated than others. How would you decide which ones to tackle first?
How to Answer
- 1
Assess the severity of issues in each carburetor
- 2
Prioritize based on the complexity and time required for repairs
- 3
Consider the importance of each carburetor's application
- 4
Look for any deadlines or urgent repairs needed
- 5
Group similar repairs to optimize efficiency
Example Answers
I would first evaluate each carburetor for the severity of its issues, tackling the most critical ones first. Then, I would consider which repairs are more complex and time-consuming, scheduling them accordingly.
If you received an emergency request for carburetor service late at night, how would you decide whether to respond?
How to Answer
- 1
Assess the urgency of the request based on the situation described.
- 2
Determine if the issue is one you can fix safely and effectively without compromising quality.
- 3
Consider your own availability and ability to help at that time.
- 4
Evaluate if the customer's location is accessible and safe for you to travel at night.
- 5
Think about the impact on other commitments you have and any potential customer relationships.
Example Answers
I would first ask the customer for details about the issue to gauge its urgency. If it's a serious safety concern or a vehicle vital for work, I would prioritize going out. Next, I would ensure I can fix the problem adequately without rushing.
What would you do if you found that a colleague was not following best practices for carburetor repairs?
How to Answer
- 1
Assess the situation calmly and gather facts before taking action
- 2
Communicate directly with the colleague about your concerns
- 3
Suggest a review of best practices together
- 4
Involve a supervisor only if necessary after attempting direct communication
- 5
Document your observations in case further action is needed
Example Answers
I would first observe and gather specific examples of what my colleague is doing incorrectly. Then, I'd approach them privately to discuss my concerns and suggest we review the best practices together to ensure we're aligned.
Don't Just Read Carburetor Specialist Questions - Practice Answering Them!
Reading helps, but actual practice is what gets you hired. Our AI feedback system helps you improve your Carburetor Specialist interview answers in real-time.
Personalized feedback
Unlimited practice
Used by hundreds of successful candidates
Carburetor Specialist Position Details
Related Positions
- Powerplant Mechanic
- Jet Engine Mechanic
- Airplane Mechanic
- Jet Mechanic
- Hydraulic Mechanic
- Engineman
- Aircraft Mechanic
- Helicopter Repairer
- Aircraft Electrician
- Helicopter Mechanic
Similar positions you might be interested in.
Ace Your Next Interview!
Practice with AI feedback & get hired faster
Personalized feedback
Used by hundreds of successful candidates
Ace Your Next Interview!
Practice with AI feedback & get hired faster
Personalized feedback
Used by hundreds of successful candidates