Top 30 Cementer Interview Questions and Answers [Updated 2025]
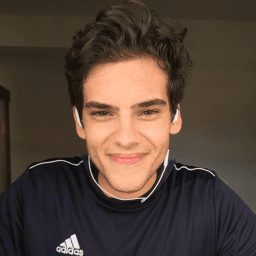
Andre Mendes
•
March 30, 2025
Preparing for a Cementer interview can be daunting, but fear not! This blog post compiles the most common interview questions for the Cementer role, complete with example answers and tips on how to respond effectively. Whether you're a seasoned professional or new to the field, this guide will help you navigate the interview process with confidence and poise, setting you up for success in your next career move.
Download Cementer Interview Questions in PDF
To make your preparation even more convenient, we've compiled all these top Cementerinterview questions and answers into a handy PDF.
Click the button below to download the PDF and have easy access to these essential questions anytime, anywhere:
List of Cementer Interview Questions
Behavioral Interview Questions
Can you describe a time when you worked as part of a team to complete a cementing job successfully?
How to Answer
- 1
Identify a specific project or job where teamwork was essential.
- 2
Highlight your role and contributions to the team.
- 3
Discuss challenges faced and how the team overcame them together.
- 4
Explain the outcome of the job and what you learned from the experience.
- 5
Keep the answer focused on teamwork and collaboration.
Example Answers
During a recent cementing job for a new well, I worked closely with a team of four. My role was to monitor the cement mixer and ensure proper consistency. We faced delays due to equipment failure, but we quickly communicated about the issue and coordinated repairs. Together, we completed the job on time, and the well has held pressure successfully since then.
Tell me about a particularly challenging issue you faced while performing cementing operations. How did you resolve it?
How to Answer
- 1
Select a specific and relevant challenging incident.
- 2
Describe the situation clearly, focusing on the difficulty involved.
- 3
Explain the actions you took to address the challenge.
- 4
Highlight the outcome and what you learned from the experience.
- 5
Use the STAR method: Situation, Task, Action, Result.
Example Answers
During a cementing operation in a challenging well with unstable formations, we faced unexpected fluid losses. I coordinated with the team to increase the density of our cement mix and adjusted the pumping rate, which helped maintain well integrity. As a result, we successfully completed the operation without further losses, and I learned the importance of flexibility in our approach.
Don't Just Read Cementer Questions - Practice Answering Them!
Reading helps, but actual practice is what gets you hired. Our AI feedback system helps you improve your Cementer interview answers in real-time.
Personalized feedback
Unlimited practice
Used by hundreds of successful candidates
Have you ever led a team during a cementing project? What was your approach to managing the team?
How to Answer
- 1
Start with a brief overview of the project context and your role.
- 2
Highlight specific leadership techniques you used, such as communication or delegation.
- 3
Discuss how you motivated your team and handled challenges.
- 4
Mention any successful outcomes or lessons learned.
- 5
Keep the focus on how your leadership influenced the project's success.
Example Answers
Yes, I led a team on a cementing project in Texas. I ensured clear communication by holding daily briefings and delegated tasks based on each member's strengths. When we faced unexpected weather, I motivated the team by encouraging collaboration and brainstorming alternatives, which helped us meet our deadline successfully.
Describe a situation where you identified a safety hazard during cementing operations. What actions did you take?
How to Answer
- 1
Start with a brief overview of the situation to set the context
- 2
Clearly identify the safety hazard you discovered
- 3
Explain the specific actions you took to address the hazard
- 4
Highlight any collaboration with team members or superiors
- 5
Conclude with the outcome and its impact on safety
Example Answers
During a cementing operation, I noticed that a pressure gauge was malfunctioning, which posed a risk of inaccurate pressure readings. I immediately reported this to my supervisor and ensured that the gauge was replaced before continuing the operation, which safeguarded our team from potential over-pressure risks.
Can you give an example of how you communicated complex technical information to a team member or client?
How to Answer
- 1
Identify the specific technical information you had to communicate.
- 2
Describe the audience's level of understanding and their background.
- 3
Use analogies or simple terms to explain complex concepts.
- 4
Share the method you used to present the information (e.g., meeting, presentation).
- 5
Mention the outcome of your communication, such as resolving an issue or fostering understanding.
Example Answers
In my previous role, I had to explain a complex data model to a new team member who was unfamiliar with our software. I used simple analogies, comparing the model to a familiar concept, and created a visual diagram to illustrate the relationships between data points. This approach helped the team member understand the model quickly and led to them successfully applying it in their work.
Describe a time you had to adapt to unexpected changes during a cementing operation. What was the outcome?
How to Answer
- 1
Identify a specific incident where changes occurred unexpectedly.
- 2
Explain the actions you took to adapt to the new situation.
- 3
Highlight any teamwork or communication that was crucial.
- 4
Discuss the final outcome and what you learned from the experience.
- 5
Keep it concise and focus on your role and contributions.
Example Answers
During a cementing operation in a remote area, we encountered unexpected pressure fluctuations that required immediate adjustment. I quickly collaborated with my team to analyze the new data and modified our cement mix. Our adaptability ensured a successful bond, and we completed the job on schedule.
Can you provide an example of when you took the initiative to improve a cementing process?
How to Answer
- 1
Identify a specific process you improved.
- 2
Describe the problem you noticed with the current method.
- 3
Explain the steps you took to implement the improvement.
- 4
Highlight the positive results or feedback from your initiative.
- 5
Keep it concise and focus on your contributions.
Example Answers
In my previous role, I noticed our cement slurry had inconsistent properties, leading to variations in job quality. I researched and proposed a new mix design that optimized performance. After implementing it, we achieved a 20% reduction in job rework and received positive feedback from the team.
Tell me about a cementing job that did not go as planned. What did you learn from that experience?
How to Answer
- 1
Choose a specific incident that had clear impacts.
- 2
Describe the issue briefly and objectively.
- 3
Focus on the corrective actions taken.
- 4
Highlight the lessons learned and how you applied them later.
- 5
Keep a positive tone emphasizing growth and improvement.
Example Answers
During a cementing job offshore, we faced unexpected fluid loss due to a faulty seal. We quickly adjusted our mix design and monitored the well more closely. I learned the importance of pre-job risk assessments and have since implemented additional checks that have improved our success rates.
Provide an example of how you handled high-pressure situations in your previous cementing roles.
How to Answer
- 1
Think of a specific situation where you faced a tight deadline or unexpected issue.
- 2
Describe the actions you took to manage the situation effectively.
- 3
Highlight any teamwork or communication that helped resolve the pressure.
- 4
Mention the positive outcome or what you learned from that experience.
- 5
Be concise and focus on your role in the situation.
Example Answers
In a previous role, we had a last-minute change in a project that required immediate action. I organized a team meeting to assess our resources and delegated tasks efficiently. By maintaining clear communication, we completed the cementing job on time, ensuring customer satisfaction.
Don't Just Read Cementer Questions - Practice Answering Them!
Reading helps, but actual practice is what gets you hired. Our AI feedback system helps you improve your Cementer interview answers in real-time.
Personalized feedback
Unlimited practice
Used by hundreds of successful candidates
Technical Interview Questions
What types of cementing materials have you worked with, and how do you determine which type to use for a specific job?
How to Answer
- 1
List specific types of cementing materials you have experience with.
- 2
Explain the factors influencing your choice of cement, like well conditions and project requirements.
- 3
Mention any relevant experiences that illustrate your decision-making process.
- 4
Show understanding of industry standards and specifications.
- 5
Convey confidence in your ability to select the appropriate material.
Example Answers
I have worked with Portland cement, fly ash cement, and oil well cement. For example, I choose lightweight cement for shallow wells to reduce density and avoid fracturing, while I use high-performance cement for deeper wells under high pressures.
What are the critical pieces of equipment you use in cementing operations, and what is their function?
How to Answer
- 1
Identify key equipment used in cementing such as cement pumps, mixers, and casing accessories.
- 2
Explain the function of each piece of equipment succinctly.
- 3
Discuss how these pieces of equipment contribute to successful cementing operations.
- 4
Mention any safety equipment or monitoring devices that are critical during the process.
- 5
Tailor your answers to show understanding of the specific cementing operation you'll work with.
Example Answers
In cementing operations, I primarily use cement pumps, which are essential for transporting the cement slurry to the desired location. I also utilize cement mixers to ensure the correct consistency and mud weight, and casing accessories to support the casing during the cementing process. Monitoring devices, like pressure gauges, are critical to ensure proper flow and pressure during the operation.
Don't Just Read Cementer Questions - Practice Answering Them!
Reading helps, but actual practice is what gets you hired. Our AI feedback system helps you improve your Cementer interview answers in real-time.
Personalized feedback
Unlimited practice
Used by hundreds of successful candidates
Explain the process you follow to formulate the right cement blend for various well conditions.
How to Answer
- 1
Evaluate the well conditions including temperature and pressure.
- 2
Understand the chemical composition of the cements available.
- 3
Consider additives to enhance the properties of the cement blend.
- 4
Conduct laboratory tests to simulate well conditions before finalizing the blend.
- 5
Follow industry standards and guidelines for cement formulation.
Example Answers
First, I assess the specific temperature and pressure of the well. This helps determine the base cement. Next, I analyze the chemical composition of available cements and choose the one that best suits the conditions. I then consider using additives like retarders or accelerators based on the flow conditions. After that, I run lab tests to ensure the blend can withstand the well environment. Finally, I adhere to industry guidelines to finalize the blend.
How do you ensure the quality of the cement mixes before application?
How to Answer
- 1
Conduct regular testing of raw materials for compliance with standards
- 2
Use calibrated equipment for accurate measurements of ingredients
- 3
Implement a mixing protocol that includes proper timing and techniques
- 4
Perform consistency and workability tests on the mixed cement
- 5
Document all tests and adjustments made during the mixing process
Example Answers
I ensure the quality of cement mixes by testing raw materials for compliance with industry standards, using calibrated equipment to measure ingredients accurately, and performing consistency tests on the mix before application.
What are the implications of pressure and temperature on cementing operations?
How to Answer
- 1
Explain how pressure affects cement cure times and strength.
- 2
Discuss the role of temperature in the cement setting process.
- 3
Mention how extreme conditions can lead to cement failure.
- 4
Consider the impact of pressure on fluid loss and displacement efficiency.
- 5
Touch on the adjustment of cement composition based on expected pressure and temperature.
Example Answers
Pressure increases the rate of cement hydration but may also lead to early failure if too high. Temperature significantly affects curing time; higher temperatures speed it up, which can lead to weak cement if not managed.
What industry regulations do you consider essential when performing cementing operations?
How to Answer
- 1
Familiarize yourself with local and federal regulations regarding cementing operations.
- 2
Discuss specific standards such as API regulations and ISO certifications relevant to cementing.
- 3
Mention safety regulations that protect personnel and the environment during cementing operations.
- 4
Include examples of prevention measures to mitigate risks during cementing projects.
- 5
Show understanding of the need for compliance and regular audits.
Example Answers
I consider API standards essential, especially API 10A for cement and API 65 for cementing operations, to ensure quality and safety.
What software or tools do you use to design and plan cementing operations?
How to Answer
- 1
List specific software you are familiar with.
- 2
Explain how you use each tool in the context of cementing operations.
- 3
Mention any relevant certifications or training you have on these tools.
- 4
Highlight any experience working with cross-functional teams using these tools.
- 5
Be prepared to discuss a specific project where you successfully used these tools.
Example Answers
I primarily use Halliburton's Cimarron and Schlumberger's Cementing Software for planning cementing operations. These tools help me model the cement job and optimize the mix design based on well conditions.
How do you assess and mitigate the environmental impacts of your cementing operations?
How to Answer
- 1
Identify key environmental factors affected by cementing, such as air quality and water usage.
- 2
Use environmental impact assessments to evaluate potential hazards.
- 3
Implement measures to minimize dust and emissions during operations.
- 4
Adopt practices for water conservation and proper waste disposal.
- 5
Engage with local communities to address concerns and collaborate on environmental efforts.
Example Answers
I assess environmental impacts by conducting thorough evaluations of air and water quality before starting cementing operations, and then implement dust suppression techniques to minimize emissions.
What factors influence the bonding of cement to the formation, and how can these be optimized?
How to Answer
- 1
Identify key factors such as surface roughness, cleanliness, and moisture levels.
- 2
Discuss the importance of cement composition and additives.
- 3
Explain the role of temperature in cement hydration and bonding.
- 4
Suggest techniques for surface preparation to enhance bonding.
- 5
Mention testing methods to evaluate bond strength before and after application.
Example Answers
The bonding of cement to the formation is influenced by factors like the surface texture, which should be rough and clean. Additionally, using additives can improve the bond. It’s essential to ensure the surface is free of contaminants and to optimize the curing temperature for better hydration.
What are some best practices you follow to ensure successful cement job execution?
How to Answer
- 1
Conduct thorough planning including mix design and job parameters
- 2
Verify equipment calibration and functioning before the job starts
- 3
Ensure proper training and briefing for all team members involved
- 4
Monitor real-time conditions and adjust the cement job as necessary
- 5
Perform post-job evaluation to identify lessons learned for future jobs
Example Answers
I ensure successful cement job execution by planning the mix design in advance, verifying all equipment, and ensuring the team is well-trained on the process.
Don't Just Read Cementer Questions - Practice Answering Them!
Reading helps, but actual practice is what gets you hired. Our AI feedback system helps you improve your Cementer interview answers in real-time.
Personalized feedback
Unlimited practice
Used by hundreds of successful candidates
What do you consider when determining the cure time for a cement job?
How to Answer
- 1
Assess the specific cement mix and its properties.
- 2
Consider environmental conditions like temperature and humidity.
- 3
Evaluate the pressures involved in the job.
- 4
Account for any additives that affect curing time.
- 5
Understand the requirements for strength development for the job.
Example Answers
When determining the cure time, I consider the cement mix properties, the surrounding temperature and humidity, and any additives used. For instance, high temperatures can accelerate curing, while cold conditions can slow it down significantly.
Situational Interview Questions
If you encountered a severe equipment failure during a cementing job, how would you respond?
How to Answer
- 1
Stay calm and assess the situation to understand the extent of the failure.
- 2
Communicate immediately with your team and supervisor about the issue.
- 3
Prioritize safety by ensuring everyone is in a safe position.
- 4
Follow established emergency procedures for equipment failure.
- 5
Document the details of the failure for future analysis and improvement.
Example Answers
I would first take a deep breath and assess the situation carefully. Then, I would alert my team and supervisor to ensure everyone is aware of the problem. Safety is my first concern, so I would check that everyone is out of harm's way before proceeding to follow our emergency procedures. I would also take detailed notes on what went wrong for our review later.
You disagree with a colleague on the cementing technique to use for a job. How would you handle this situation?
How to Answer
- 1
Acknowledge your colleague's perspective and the reasons for their approach
- 2
Share your own viewpoint clearly and support it with data or past experiences
- 3
Suggest a discussion or a meeting to explore both methods in detail
- 4
Be open to compromise and consider testing both techniques if feasible
- 5
Keep the communication respectful and focused on the best outcome for the project
Example Answers
I would start by acknowledging my colleague's approach and the reasons they believe it's effective. Then I'd explain my perspective using data from previous projects where my method showed success. I would propose we have a meeting to discuss our ideas further, perhaps even testing both methods to see which yields better results.
Don't Just Read Cementer Questions - Practice Answering Them!
Reading helps, but actual practice is what gets you hired. Our AI feedback system helps you improve your Cementer interview answers in real-time.
Personalized feedback
Unlimited practice
Used by hundreds of successful candidates
How would you prioritize your tasks if you were facing a tight deadline for multiple cementing jobs?
How to Answer
- 1
Assess the urgency and importance of each task.
- 2
Communicate with team members about deadlines.
- 3
Identify potential bottlenecks and address them early.
- 4
Create a clear timeline for task completion.
- 5
Focus on high-impact tasks that drive progress.
Example Answers
I would first assess which cementing jobs have the tightest deadlines and greatest impact on the project. Then, I would communicate with my team to ensure everyone is aligned. I would break the tasks down and create a timeline, focusing first on critical tasks that can't be delayed.
A client is unhappy with the results of a cementing job. What steps would you take to address their concerns?
How to Answer
- 1
Listen carefully to the client's specific complaints and concerns.
- 2
Acknowledge the issue and take responsibility where appropriate.
- 3
Explain the technical aspects that may have led to the unsatisfactory results.
- 4
Discuss potential solutions or corrective actions to remedy the situation.
- 5
Follow up with the client after implementing solutions to ensure satisfaction.
Example Answers
I would first listen to the client to understand their specific concerns and acknowledge their frustration. Then, I would explain any technical factors that contributed to the results, followed by discussing corrective actions, such as a follow-up cementing job or adjustments to our process.
If you were assigned to train a new team member in cementing operations, what key areas would you focus on?
How to Answer
- 1
Highlight the importance of safety protocols and personal protective equipment.
- 2
Explain cementing materials and their properties for effective mixing.
- 3
Discuss the cementing process steps, including site preparation and equipment usage.
- 4
Emphasize troubleshooting common issues that may arise during operations.
- 5
Encourage mentorship by demonstrating techniques and encouraging questions.
Example Answers
I would first focus on safety practices, ensuring the new team member understands how to safely handle cement and the importance of PPE. Next, I'd explain the different types of cement we use and how to mix them correctly. Then, I would walk them through the step-by-step cementing process, highlighting key equipment like pumps and mixers. Lastly, I would cover troubleshooting tips for common issues so they feel prepared for any challenges.
If you identify a potential risk factor during a cementing operation, what steps would you take to mitigate it?
How to Answer
- 1
Assess the severity of the risk and its potential impact on the operation
- 2
Communicate the risk immediately to the team and management
- 3
Review and adjust the cementing plan to address the risk
- 4
Implement additional safety measures or change procedures accordingly
- 5
Document the risk and the steps taken for future reference
Example Answers
If I identify a potential risk factor, I first assess how it might impact the operation. Then, I would inform my team and management right away. I would review our cementing plan to make necessary adjustments, and implement additional safety measures if needed. Finally, I would document everything for future learning.
How would you handle a situation where a team member is not following standard safety protocols during a cementing job?
How to Answer
- 1
Assess the situation calmly and ensure safety is prioritized
- 2
Approach the team member privately to discuss the issue
- 3
Use specific examples to highlight the importance of safety protocols
- 4
Encourage open communication about concerns or misunderstandings
- 5
If the behavior continues, report it to a supervisor following company protocols
Example Answers
I would first make sure everyone is safe and the job site is secure. Then, I would speak to the team member privately and explain my concerns about not following the safety protocols, using specific examples to emphasize the importance of safety. If the issue persists, I would report it to my supervisor.
If your team consistently underperforms on cementing jobs, how would you address this issue?
How to Answer
- 1
Analyze the root causes of underperformance.
- 2
Engage the team in open discussions to gather insights.
- 3
Implement targeted training for skill gaps.
- 4
Set clear performance metrics and expectations.
- 5
Monitor progress and adjust strategies as needed.
Example Answers
First, I would analyze the data to identify patterns in our underperformance. Then, I would hold a meeting with the team to discuss these findings and encourage input on potential solutions. We could implement training sessions for areas where we lack skills and set clear KPIs to track our improvement.
How would you manage your materials and resources if you receive a last-minute request for a cementing job?
How to Answer
- 1
Quickly assess the availability of materials and equipment
- 2
Prioritize urgent requests while ensuring quality standards
- 3
Communicate clearly with the team about the new requirements
- 4
Utilize existing inventory to meet the immediate needs
- 5
Prepare a backup plan in case of supply chain issues
Example Answers
I would first check our current inventory to see what materials we have on hand. I would then communicate with my team to prioritize the request while ensuring that we maintain our quality standards. If necessary, I would look for alternative suppliers to source any additional materials quickly.
Cementer Position Details
Recommended Job Boards
ZipRecruiter
www.ziprecruiter.com/Jobs/CementerThese job boards are ranked by relevance for this position.
Related Positions
- Cager
- Caser
- Cemetery Manager
- Cemetery Worker
- Cement Worker
- Cremator
- Cement Mixer
- Concrete Foreman
- Funeral Director
- Funeral Arranger
Similar positions you might be interested in.
Ace Your Next Interview!
Practice with AI feedback & get hired faster
Personalized feedback
Used by hundreds of successful candidates
Ace Your Next Interview!
Practice with AI feedback & get hired faster
Personalized feedback
Used by hundreds of successful candidates