Top 31 Central Supply Technician Interview Questions and Answers [Updated 2025]
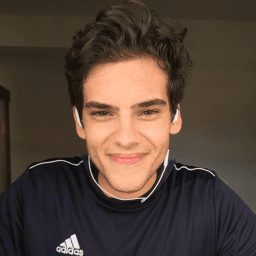
Andre Mendes
•
March 30, 2025
Preparing for a Central Supply Technician interview can be daunting, but we're here to help. In this post, you'll find the most common interview questions tailored for this essential role, complete with example answers and insights on how to respond with confidence. Whether you're a seasoned professional or new to the field, these tips will guide you in showcasing your expertise and securing your desired position.
Download Central Supply Technician Interview Questions in PDF
To make your preparation even more convenient, we've compiled all these top Central Supply Technicianinterview questions and answers into a handy PDF.
Click the button below to download the PDF and have easy access to these essential questions anytime, anywhere:
List of Central Supply Technician Interview Questions
Behavioral Interview Questions
Can you describe a time when you successfully managed inventory levels in a high-demand environment?
How to Answer
- 1
Identify a specific instance with measurable outcomes.
- 2
Explain the tools or methods you used to track inventory.
- 3
Highlight any challenges you faced and how you overcame them.
- 4
Include the results of your management, emphasizing efficiency and customer satisfaction.
- 5
Keep the response concise and focused on your role.
Example Answers
In my previous role at a medical supply company, we experienced a sudden spike in demand due to a local health crisis. I implemented a new inventory tracking system using Excel, which improved real-time visibility. I coordinated with suppliers to expedite orders and successfully maintained stock levels, resulting in a 30% reduction in backorders.
Tell me about a situation where you had to communicate clearly with a team member who was struggling to understand a process.
How to Answer
- 1
Choose a specific example with a clear problem.
- 2
Describe the initial misunderstanding and its impact.
- 3
Explain the steps you took to clarify the process.
- 4
Highlight the outcome and any positive changes.
- 5
Emphasize your communication style and patience.
Example Answers
In my last role, a colleague was having difficulty with inventory tracking. I noticed mistakes were leading to stock shortages. I took time to explain the process step-by-step, using visual aids. After that, their accuracy improved significantly, reducing errors by 30%.
Don't Just Read Central Supply Technician Questions - Practice Answering Them!
Reading helps, but actual practice is what gets you hired. Our AI feedback system helps you improve your Central Supply Technician interview answers in real-time.
Personalized feedback
Unlimited practice
Used by hundreds of successful candidates
Describe an instance where you had a disagreement with a coworker. How did you resolve it?
How to Answer
- 1
Choose a specific example that highlights the disagreement clearly.
- 2
Outline the steps you took to address the disagreement.
- 3
Emphasize communication and collaboration in your resolution approach.
- 4
Share the outcome and any lessons learned from the experience.
- 5
Keep your tone positive and show respect for the coworker's perspective.
Example Answers
In a previous role, I disagreed with a coworker about how to organize supplies. I suggested a meeting to discuss our methods, where we both presented our viewpoints. This led to a fun brainstorming session that combined our ideas, improving efficiency significantly. We both learned from the process and now have a stronger working relationship.
Give an example of a time when your attention to detail helped prevent a potential problem.
How to Answer
- 1
Use the STAR method: Situation, Task, Action, Result.
- 2
Choose a relevant example from previous work or training.
- 3
Highlight specific details you managed that led to a positive outcome.
- 4
Emphasize the importance of attention to detail in a medical supply context.
- 5
Conclude with what you learned and how it improved your performance.
Example Answers
In my previous job as a supply clerk, I noticed that the labeling on several medical supplies was incorrect before they were distributed. I took the initiative to check each item against our inventory software, corrected the labels, and documented the discrepancies. This prevented errors in patient care and ensured compliance with our safety standards.
Describe an experience where you had to train someone on supply chain processes. What approach did you take?
How to Answer
- 1
Highlight your role in the training process.
- 2
Explain the specific supply chain processes covered.
- 3
Mention the training methods used, like hands-on practice or shadowing.
- 4
Discuss any challenges faced and how you overcame them.
- 5
Share the outcomes or improvements observed post-training.
Example Answers
In my previous role, I trained a new team member on our inventory management system. I showed them how to use the software and provided hands-on practice. We faced challenges with understanding the reporting features, so I created a step-by-step guide. After training, their accuracy improved by 20%.
Discuss a successful project you completed as part of a team. What was your role?
How to Answer
- 1
Choose a project that had clear goals and positive outcomes
- 2
Define your specific role and responsibilities within the team
- 3
Use quantifiable results to demonstrate success, if possible
- 4
Highlight teamwork, collaboration, and communication skills
- 5
Reflect on what you learned and how it applies to the new role
Example Answers
In a supply chain optimization project, I served as the team coordinator. My role was to streamline inventory processes, which resulted in a 20% reduction in stock discrepancies. We achieved this by enhancing communication between departments, ensuring all team members were informed of updates.
Describe a time when you identified an area for improvement in supply operations and took the initiative to implement change.
How to Answer
- 1
Choose a specific situation where you saw an inefficiency.
- 2
Explain the steps you took to analyze the issue.
- 3
Describe the action you implemented for improvement.
- 4
Share the outcome and any positive results.
- 5
Focus on your role and the impact of your initiative.
Example Answers
In my previous role, I noticed that inventory counts were often inaccurate, which led to shortages. I analyzed our counting process and developed a new checklist for periodic reviews. After implementing this, inventory accuracy improved by 30% over six months.
Technical Interview Questions
What are the key components of supply chain management that a Central Supply Technician should be aware of?
How to Answer
- 1
Understand inventory management and its role in supply chain efficiency
- 2
Know the importance of supplier relationships and communication
- 3
Be aware of logistics and distribution channels for timely delivery
- 4
Recognize the impact of compliance and regulatory standards
- 5
Stay informed on technology trends that improve supply chain processes
Example Answers
A Central Supply Technician should focus on effective inventory management to maintain optimal levels, strengthen supplier relationships for better negotiation, and ensure compliance with industry regulations.
Which inventory management software are you familiar with, and how have you used it in your previous roles?
How to Answer
- 1
Identify specific software you've used, such as SAP or Oracle.
- 2
Briefly describe how you used the software in managing inventory.
- 3
Include any achievements or improvements made using the software.
- 4
Mention any certifications or training related to the software.
- 5
Be ready to discuss any challenges faced and how you overcame them.
Example Answers
I have experience with SAP for inventory management. I used it to track stock levels and reorder supplies efficiently, reducing shortages by 20%. I completed a certification in SAP inventory management to enhance my skills.
Don't Just Read Central Supply Technician Questions - Practice Answering Them!
Reading helps, but actual practice is what gets you hired. Our AI feedback system helps you improve your Central Supply Technician interview answers in real-time.
Personalized feedback
Unlimited practice
Used by hundreds of successful candidates
Can you explain the importance of compliance with health regulations in central supply operations?
How to Answer
- 1
Highlight the role of regulations in ensuring patient safety.
- 2
Mention how compliance prevents legal and financial repercussions.
- 3
Discuss the impact on operational efficiency and inventory management.
- 4
Emphasize the importance of maintaining high standards for sterility and hygiene.
- 5
Share how adherence to regulations fosters trust with healthcare staff and patients.
Example Answers
Compliance with health regulations is crucial for ensuring patient safety by keeping all supplied materials sterile and uncontaminated. This not only protects patients but also avoids legal issues and financial penalties, allowing us to operate smoothly and efficiently.
What process do you follow for replenishing stock levels, and what factors do you consider?
How to Answer
- 1
Identify the inventory management system you use.
- 2
Consider lead times for orders and delivery schedules.
- 3
Evaluate usage rates and historical data for accurate forecasting.
- 4
Account for any upcoming events or procedures that may affect stock levels.
- 5
Maintain communication with team members to adapt to quick changes in needs.
Example Answers
I utilize our inventory management system to monitor stock levels continuously. I consider the lead time and usage rates of items to forecast needs accurately, and I always check with my team about upcoming procedures that might require additional supplies.
How do you utilize data analysis in managing inventory and supply chains?
How to Answer
- 1
Identify key metrics like turnover rates and lead times.
- 2
Use software tools for real-time data tracking and reporting.
- 3
Analyze trends to forecast demand accurately.
- 4
Regularly review inventory levels to optimize stock.
- 5
Implement just-in-time practices based on analysis.
Example Answers
I track turnover rates and lead times to understand how quickly inventory moves. Using supply chain software, I can monitor stock levels in real-time and adjust orders based on trends to ensure we meet demand without overstocking.
What types of equipment and tools have you used in central supply operations?
How to Answer
- 1
Identify specific equipment relevant to central supply, such as sterilizers, inventory management software, and forklifts.
- 2
Mention your experience with tracking systems and inventory controls.
- 3
Highlight any specialized tools for packaging and labeling supplies.
- 4
Discuss your familiarity with personal protective equipment used during operations.
- 5
Provide examples of how you ensured efficiency and safety with these tools.
Example Answers
I have experience using sterilizers for medical instruments, inventory management software to track supplies, and forklifts for moving heavy items safely.
How often do you believe stock audits should be performed, and what is the process you follow?
How to Answer
- 1
State the frequency of audits, typically monthly or quarterly.
- 2
Mention the importance of regular audits for accuracy and compliance.
- 3
Describe the key steps in the audit process clearly.
- 4
Emphasize collaboration with team members during audits.
- 5
Highlight the use of technology or tools to streamline the process.
Example Answers
I believe stock audits should be performed monthly to ensure accuracy and compliance. The process I follow includes preparing a checklist, counting stock levels, comparing them against records, and addressing discrepancies. I engage the team for accuracy and use inventory management software to help streamline the process.
What strategies would you implement to help contain costs in a supply department?
How to Answer
- 1
Analyze inventory levels regularly to identify slow-moving items and reduce overstock.
- 2
Negotiate with suppliers for bulk purchasing discounts or better contract terms.
- 3
Implement a standardized ordering process to minimize duplicate orders and errors.
- 4
Utilize technology to track usage patterns and automate reordering.
- 5
Conduct regular training for staff on cost-saving measures and efficient supply practices.
Example Answers
To contain costs, I would analyze our inventory to identify slow-moving items and reduce excess stock. I'd also negotiate better terms with our suppliers for discounts on bulk orders.
What are the best practices for handling hazardous materials in a supply environment?
How to Answer
- 1
Always refer to Safety Data Sheets (SDS) for specific hazards and handling instructions
- 2
Use appropriate personal protective equipment (PPE) such as gloves, masks, and goggles
- 3
Ensure proper labeling and storage of hazardous materials in designated areas
- 4
Follow established protocols for spill response and disposal methods
- 5
Participate in regular training sessions on hazardous material safety
Example Answers
I follow best practices by always checking the Safety Data Sheets for proper handling and storage in our supply area. I ensure that all materials are well-labeled and use the necessary PPE when dealing with hazardous items.
How do you typically handle vendor relationships to ensure good service and product quality?
How to Answer
- 1
Communicate regularly with vendors to establish trust and transparency
- 2
Set clear expectations for service and product quality from the beginning
- 3
Provide constructive feedback to vendors on their performance
- 4
Monitor vendor performance through metrics and regular reviews
- 5
Build relationships through face-to-face meetings or site visits when possible
Example Answers
I maintain effective communication with vendors by having regular check-ins, which helps to build trust. I set clear expectations regarding product quality and service delivery from the start, and I make sure to provide feedback regularly to help them improve.
Don't Just Read Central Supply Technician Questions - Practice Answering Them!
Reading helps, but actual practice is what gets you hired. Our AI feedback system helps you improve your Central Supply Technician interview answers in real-time.
Personalized feedback
Unlimited practice
Used by hundreds of successful candidates
What steps do you take to ensure accurate order fulfillment in a central supply setting?
How to Answer
- 1
Verify orders against inventory lists before processing.
- 2
Use a checklist to ensure all items are included.
- 3
Double-check quantities during packing.
- 4
Implement barcode scanning for accuracy.
- 5
Conduct regular audits of inventory and orders.
Example Answers
I ensure accurate order fulfillment by first verifying each order against our inventory list. Then I use a checklist to confirm that all required items are gathered before packing.
What performance metrics do you think are critical to evaluate the success of a supply operation?
How to Answer
- 1
Identify key performance indicators like inventory turnover rate.
- 2
Discuss the importance of order accuracy and fulfillment rates.
- 3
Mention lead times and how they affect operational efficiency.
- 4
Highlight the significance of cost management in supply operations.
- 5
Emphasize customer satisfaction metrics related to supply services.
Example Answers
I believe inventory turnover rate is crucial as it shows how effectively stock is being managed. Additionally, order accuracy and fulfillment rates reflect the efficiency of the operation.
Situational Interview Questions
Imagine a scenario where essential supplies are running low unexpectedly. How would you handle this situation?
How to Answer
- 1
Assess the current inventory and identify critical items that are low.
- 2
Communicate with team members to confirm supply needs and urgency.
- 3
Prioritize restocking of essential items using established suppliers.
- 4
Consider alternative sources or substitutions for critical supplies.
- 5
Document the situation and response for future planning and improvement.
Example Answers
First, I would check our inventory to see which supplies are running low and assess their criticality. Then, I would communicate with my team to confirm their immediate needs. I would prioritize ordering the essentials from our regular suppliers while also looking for alternatives if that’s not possible.
If you notice a discrepancy between stock records and physical inventory, how would you approach your team to investigate?
How to Answer
- 1
Gather all relevant inventory data before discussing with the team
- 2
Schedule a quick meeting to address the discrepancy collectively
- 3
Encourage open communication and input from all team members
- 4
Assign specific roles or tasks for auditing the records
- 5
Document findings and establish a follow-up plan to prevent future discrepancies
Example Answers
I would first review the stock records thoroughly to identify specific discrepancies. Then, I would call a team meeting to discuss our findings and solicit input on potential causes. Assigning each member a specific area to investigate can help us resolve the issue efficiently.
Don't Just Read Central Supply Technician Questions - Practice Answering Them!
Reading helps, but actual practice is what gets you hired. Our AI feedback system helps you improve your Central Supply Technician interview answers in real-time.
Personalized feedback
Unlimited practice
Used by hundreds of successful candidates
What would you do if you received a shipment of supplies that were damaged or incorrect?
How to Answer
- 1
Immediately inspect and document the condition of the shipment
- 2
Contact the supplier to report the issue and follow their procedure
- 3
Reorganize stock to ensure usability of undamaged items
- 4
Communicate with your supervisor and team about the situation
- 5
Keep a record of damaged items for future reference and better inventory management
Example Answers
I would first inspect the shipment and document any damages or incorrect items. Then, I would contact the supplier to resolve the issue according to their return policy. I'd also update my supervisor and inform the team to adjust inventory accordingly.
Suppose you have a tight deadline to prepare supplies for an upcoming event. How would you ensure timely completion?
How to Answer
- 1
Prioritize tasks based on urgency and importance
- 2
Create a checklist to track materials and supplies needed
- 3
Communicate with team members to delegate responsibilities
- 4
Establish a timeline with specific milestones to stay on track
- 5
Conduct a final review before the deadline to ensure everything is ready
Example Answers
To ensure timely completion, I would prioritize the essential tasks, create a checklist of all supplies needed, and delegate tasks to team members based on their strengths. I would then establish a clear timeline and regularly check in to ensure we are on track.
If a supervisor gave you critical feedback about your inventory handling, how would you respond?
How to Answer
- 1
Listen carefully to the feedback without interrupting
- 2
Acknowledge the supervisor's perspective and show understanding
- 3
Ask clarifying questions if needed to understand the issue better
- 4
Express a willingness to improve and discuss a specific action plan
- 5
Thank the supervisor for the feedback and assure them of your commitment to better performance
Example Answers
I would listen to the feedback without interrupting, acknowledge the concern, and ask clarifying questions to fully understand the issue. After that, I'd express my commitment to improving and discuss steps I plan to take.
If you were asked to overlook a minor compliance issue to meet a deadline, how would you handle it?
How to Answer
- 1
Assess the compliance issue's impact on safety and quality
- 2
Evaluate the reasons behind the deadline pressure
- 3
Communicate with relevant stakeholders before making a decision
- 4
Propose alternative solutions that maintain compliance
- 5
Prioritize ethical standards over deadlines whenever possible
Example Answers
I would first evaluate the compliance issue's impact on patient safety. If it's minor but could wait, I would communicate with my supervisor about the potential risks and suggest a timeline to address it without compromising safety.
How would you allocate limited resources when multiple departments request supplies urgently?
How to Answer
- 1
Assess the urgency and impact of each request on patient care
- 2
Communicate transparently with departments about resource availability
- 3
Prioritize based on critical needs and departmental dependencies
- 4
Consider rotating supplies to ensure fairness among departments
- 5
Document decisions and rationale for transparency and future reference
Example Answers
I would first evaluate which requests directly impact patient care and prioritize those. Then, I would inform the departments of the situation and my decisions to maintain transparency.
If faced with conflicting priorities between a shortage in critical supplies and regular stock management, how would you decide?
How to Answer
- 1
Prioritize patient care needs and safety above all else
- 2
Assess the severity of the shortage and impact on operations
- 3
Consult with your team to gather insights and support
- 4
Communicate with management about the situation and seek guidance
- 5
Develop a temporary plan to balance urgent needs with ongoing stock management
Example Answers
I would first evaluate the critical supplies needed for patient care and prioritize those over regular stock management. If necessary, I would consult my team for their input and keep management informed about the situation.
Can you suggest an innovative solution to improve the supply chain process in your previous job?
How to Answer
- 1
Identify a specific challenge faced in the supply chain process.
- 2
Propose a technology or method that could address that challenge.
- 3
Explain how the solution would enhance efficiency or reduce costs.
- 4
Include a potential outcome or benefit to the organization.
- 5
Reflect on how the solution could be implemented and evaluated.
Example Answers
In my previous role, we struggled with inventory shortages. I proposed implementing a real-time inventory management system using RFID technology. This improved tracking and reduced stockouts by 30%, ultimately saving costs and improving service levels.
How would you analyze and improve existing workflows in a supply chain process?
How to Answer
- 1
Map out the current workflow to identify bottlenecks.
- 2
Use data analytics to measure efficiency and pinpoint areas for improvement.
- 3
Engage with team members for feedback on workflow challenges.
- 4
Implement changes on a small scale and monitor outcomes before full rollout.
- 5
Document all changes for future reference and continuous improvement.
Example Answers
I would first map the current supply chain workflow to see where delays occur. Then, I would analyze data to measure efficiency. I would also gather input from the team to understand their challenges. After identifying solutions, I'd implement them gradually and monitor results.
Don't Just Read Central Supply Technician Questions - Practice Answering Them!
Reading helps, but actual practice is what gets you hired. Our AI feedback system helps you improve your Central Supply Technician interview answers in real-time.
Personalized feedback
Unlimited practice
Used by hundreds of successful candidates
Central Supply Technician Position Details
Recommended Job Boards
These job boards are ranked by relevance for this position.
Related Positions
- Hospital Technician
- Certified Medical Technician
- Environmental Health Technician
- Sleep Technologist
- Dialysis Technician
- Respiratory Therapy Technician
- Obstetrics Technician
- Electroencephalographic Technician
- Medical Consultant
- Electroencephalogram (EEG) Technologist
Similar positions you might be interested in.
Ace Your Next Interview!
Practice with AI feedback & get hired faster
Personalized feedback
Used by hundreds of successful candidates
Ace Your Next Interview!
Practice with AI feedback & get hired faster
Personalized feedback
Used by hundreds of successful candidates