Top 31 Clutch Specialist Interview Questions and Answers [Updated 2025]
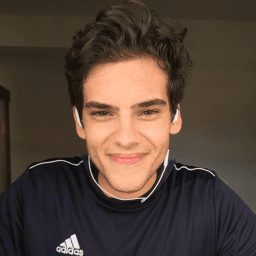
Andre Mendes
•
March 30, 2025
Preparing for a Clutch Specialist interview can be daunting, but we're here to streamline your process. This post covers the most common interview questions tailored for this specialized role, complete with example answers and insightful tips on how to respond effectively. Dive in to enhance your understanding and boost your confidence, ensuring you stand out as a top candidate in any interview setting.
Download Clutch Specialist Interview Questions in PDF
To make your preparation even more convenient, we've compiled all these top Clutch Specialistinterview questions and answers into a handy PDF.
Click the button below to download the PDF and have easy access to these essential questions anytime, anywhere:
List of Clutch Specialist Interview Questions
Behavioral Interview Questions
Can you describe a challenging clutches repair situation you faced and how you resolved it?
How to Answer
- 1
Select a specific repair incident that was challenging.
- 2
Clearly outline the problem and why it was difficult.
- 3
Describe the steps you took to diagnose the issue.
- 4
Explain how you implemented the solution.
- 5
Conclude with the results and any lessons learned.
Example Answers
In one instance, I was repairing a clutch that was slipping significantly. The challenge was that the vehicle had an unusual setup, making access difficult. I began by carefully diagnosing the hydraulic system and discovered a leak which was not initially obvious. After replacing the faulty seal, I reassembled the components and tested the clutch thoroughly, ensuring it functioned properly. This taught me to always check the hydraulic system first in similar situations.
Tell me about a time when you had to work closely with another technician to troubleshoot a clutch issue. What was your role?
How to Answer
- 1
Choose a specific incident to describe clearly.
- 2
Highlight your role and contributions in the troubleshooting process.
- 3
Mention the steps taken and the collaboration with the other technician.
- 4
Emphasize the outcome and what was learned from the experience.
- 5
Keep your answer focused on teamwork and problem-solving.
Example Answers
In my previous role, I worked with a fellow technician to troubleshoot a clutch issue in a customer's vehicle. I first gathered all the relevant information from the customer and diagnosed the symptoms. Together, we inspected the clutch assembly and discovered a worn-out pressure plate. I took the lead on replacing the pressure plate, while my colleague focused on checking the hydraulic system. We resolved the issue efficiently, and the customer was satisfied with the quick turnaround.
Don't Just Read Clutch Specialist Questions - Practice Answering Them!
Reading helps, but actual practice is what gets you hired. Our AI feedback system helps you improve your Clutch Specialist interview answers in real-time.
Personalized feedback
Unlimited practice
Used by hundreds of successful candidates
Describe a scenario where you had to explain a complicated clutch repair process to a customer. How did you ensure they understood?
How to Answer
- 1
Use analogies to relate complex processes to everyday experiences
- 2
Break down the repair process into simple steps
- 3
Ask the customer if they have any questions throughout
- 4
Use visual aids or diagrams if possible
- 5
Summarize the key points at the end to reinforce understanding
Example Answers
I once had a customer who was concerned about their clutch slipping. I explained it by comparing the clutch to a bicycle brake. I broke down the repair into three steps: diagnosis, parts replacement, and testing. After each step, I checked if they had questions, using a diagram to illustrate the process, and summarized everything at the end to ensure they understood.
Provide an example of a time you identified a root cause of a recurring clutch issue. What steps did you take?
How to Answer
- 1
Recall a specific incident with a clutch problem you've dealt with.
- 2
Describe how you approached diagnosing the issue systematically.
- 3
Mention the tools or methods you used for root cause analysis.
- 4
Explain the solution you implemented to resolve the problem permanently.
- 5
Discuss any follow-up actions to ensure the issue did not recur.
Example Answers
In my previous job, we had consistent clutch slippage issues. I first collected data on failure frequency and analyzed driving patterns. I used a root cause analysis technique to investigate the wear on the clutch plates. After identifying that overheating was the main issue due to improper adjustment, I recalibrated the clutch release mechanism. I then monitored the clutches over the next few months to confirm the issue was resolved.
Have you ever trained a new technician on clutch repairs? What approach did you take?
How to Answer
- 1
Describe your training strategy clearly
- 2
Mention hands-on techniques or shadowing
- 3
Include how you assessed their understanding
- 4
Discuss any resources or materials you used
- 5
Emphasize the outcome or improvements achieved
Example Answers
I trained a new technician by first explaining the basic theory behind clutch repairs. Then, I had them shadow me during a few repairs, before letting them try it with me supervising. I used a checklist to assess their progress and provided feedback after each attempt. They were able to independently complete repairs within a week.
Describe a time when you took the initiative to improve a process related to clutch services.
How to Answer
- 1
Think of a specific example where you identified an issue in clutch services.
- 2
Explain the steps you took to analyze and improve the process.
- 3
Include the outcome of your initiative, such as increased efficiency or customer satisfaction.
- 4
Use the STAR method: Situation, Task, Action, Result.
- 5
Highlight how your initiative benefited the team or company.
Example Answers
In my previous job, I noticed that we often experienced extended turnaround times for clutch replacements. I analyzed the workflow, identified that we lacked clear documentation for each step. I created a standardized checklist, which streamlined the process. As a result, we reduced the turnaround time by 20% and improved customer feedback on service speed.
What motivates you to excel as a Clutch Specialist?
How to Answer
- 1
Reflect on personal achievements to showcase motivation.
- 2
Connect your motivations to the role of Clutch Specialist.
- 3
Emphasize teamwork as a key driver of your success.
- 4
Include specific examples from past experiences.
- 5
Mention any passion for enhancing customer experiences.
Example Answers
I am motivated by the satisfaction of helping my team achieve tight deadlines and successful outcomes. For example, in my last role, I led a project that turned a month-long delay into a successful launch within two weeks, which felt incredibly rewarding.
Give an example of how your attention to detail has helped you in your work with clutches.
How to Answer
- 1
Choose a specific instance where attention to detail made a difference.
- 2
Describe the problem or task you faced regarding the clutch.
- 3
Explain the actions you took that reflect your attention to detail.
- 4
Highlight the positive outcome or results from your careful work.
- 5
Keep it concise and focused on the relevance to the clutch specialist role.
Example Answers
In my previous role, I noticed that the clutch cable adjustment was not properly set, which led to slippage. I meticulously recalibrated the adjustment to manufacturer specifications, which eliminated the issue and improved vehicle performance.
Technical Interview Questions
What are the key components of a hydraulic clutch, and how do they function together?
How to Answer
- 1
Identify major components like the master cylinder, slave cylinder, hydraulic line, and clutch disc.
- 2
Explain the role of each component in the clutch operation clearly.
- 3
Discuss how the components work together to engage and disengage the clutch.
- 4
Use simple language to describe hydraulic principles involved in this system.
- 5
Keep the explanation structured to show the flow of action from pressing the pedal to engaging the clutch.
Example Answers
The key components of a hydraulic clutch include the master cylinder, which generates pressure, the slave cylinder that receives this pressure, and the hydraulic line that connects them. When the pedal is pressed, the master cylinder creates hydraulic pressure that pushes the slave cylinder, which then disengages the clutch, allowing for smooth gear changes.
Can you explain the process of replacing a clutch in a manual transmission?
How to Answer
- 1
Start by detailing the importance of safety measures.
- 2
Explain the steps to remove the transmission from the vehicle.
- 3
Describe how to take out the old clutch assembly.
- 4
Mention how to install the new clutch and reassemble the transmission.
- 5
Conclude with a brief note on testing the new clutch after installation.
Example Answers
To replace a clutch, first ensure safety by disconnecting the battery. Then, lift the vehicle and remove the transmission. Next, take out the old clutch by unbolting it. Install the new clutch carefully, ensuring it is aligned, and then reattach the transmission. Finally, test the clutch by driving the vehicle.
Don't Just Read Clutch Specialist Questions - Practice Answering Them!
Reading helps, but actual practice is what gets you hired. Our AI feedback system helps you improve your Clutch Specialist interview answers in real-time.
Personalized feedback
Unlimited practice
Used by hundreds of successful candidates
How do you diagnose a slipping clutch? What tests do you perform?
How to Answer
- 1
Check for signs of slipping under acceleration
- 2
Observe engine RPM vs vehicle speed to identify a mismatch
- 3
Perform a clutch pedal height check to assess proper engagement
- 4
Conduct a visual inspection for oil leaks on the clutch housing
- 5
Test drive the vehicle to confirm slipping symptoms during load.
Example Answers
To diagnose a slipping clutch, I first check if the engine RPM rises without a corresponding increase in vehicle speed, indicating slip. Then, I inspect the clutch pedal for proper height and feel, as well as any visible leaks around the clutch area. Finally, I perform a test drive to confirm the symptoms under load.
What industry standards do you follow when performing clutch repairs?
How to Answer
- 1
Familiarize yourself with manufacturer specifications for clutch components.
- 2
Use proper diagnostic tools to assess clutch performance before repairs.
- 3
Follow safety guidelines to prevent accidents during repairs.
- 4
Stay updated on industry certifications and best practices for clutch repairs.
- 5
Document all repairs and services performed for accountability.
Example Answers
I follow the manufacturer's specifications for each vehicle when performing clutch repairs to ensure I use the right parts and procedures.
What specialized tools do you use for clutch installation and removal?
How to Answer
- 1
Mention specific tools like clutch alignment tools, pressure plate tools, and jacks.
- 2
Explain why each tool is important for the process.
- 3
Consider discussing torque wrenches for proper tension.
- 4
Include any brand names of tools you prefer, if applicable.
- 5
Emphasize your experience using these tools effectively.
Example Answers
For clutch installation, I commonly use a clutch alignment tool to ensure proper alignment of the disc and flywheel. I also use a torque wrench to tighten the pressure plate bolts to the manufacturer's specifications, which is crucial for optimal performance. My go-to brands are OTC for alignment tools and Snap-On for torque wrenches.
What indicators suggest that a clutch is nearing the end of its life?
How to Answer
- 1
Listen for unusual noises like grinding or squeaking when engaging the clutch.
- 2
Watch for slipping during acceleration despite pressing the accelerator.
- 3
Check for difficulty in shifting gears, especially into first or reverse.
- 4
Notice if the clutch pedal feels unusually soft or has a low bite point.
- 5
Be aware of any burning smell or excessive heat when using the clutch.
Example Answers
One major indicator is a slipping clutch, where the engine revs but the car doesn't accelerate as expected. Additionally, noises like grinding when engaging the clutch can signal wear.
Explain how you would fine-tune the adjustment on a clutch cable.
How to Answer
- 1
Identify the type of clutch cable mechanism in use.
- 2
Check for the correct free play as specified by the manufacturer.
- 3
Locate the adjustment nut or mechanism on the clutch cable.
- 4
Adjust the tension in small increments and test the clutch action.
- 5
Ensure that the adjustment allows for smooth engagement and disengagement.
Example Answers
First, I would check the manufacturer's specifications for the required free play in the clutch cable. Then I'd locate the adjustment nut, loosen it slightly, and make small tweaks to the tension until the clutch engages smoothly when pressed.
What are the differences between a single disc and a multi-disc clutch?
How to Answer
- 1
Explain the basic definition of each type of clutch
- 2
Discuss the applications of each type in vehicles
- 3
Highlight the advantages and disadvantages of each system
- 4
Mention common scenarios where one might be preferred over the other
- 5
Keep the explanation technical but understandable for the interviewer.
Example Answers
A single disc clutch uses one friction disc and is typical in lighter vehicles, while a multi-disc clutch has several discs for higher torque capacity, making it suitable for performance and heavy-duty applications. The multi-disc design allows for smoother engagement and better heat dissipation but is often more complex and expensive.
What signs do you look for when inspecting a clutch pedal for wear or malfunction?
How to Answer
- 1
Check for unusual noises when pressing the pedal.
- 2
Look for a soft or spongy feeling in the pedal.
- 3
Inspect for any signs of physical damage or cracks.
- 4
Notice if the pedal engages higher or lower than normal.
- 5
Ensure the clutch pedal returns fully to its resting position.
Example Answers
When inspecting a clutch pedal, I listen for any unusual noises, check if the pedal feels soft or spongy, and look for any visible cracks. Additionally, I observe the engagement point to see if it's too high or low and ensure that the pedal returns to its resting position.
What safety precautions do you take while performing clutch repairs?
How to Answer
- 1
Always disconnect the battery before starting any repairs.
- 2
Use safety glasses and gloves to protect yourself from debris and sharp edges.
- 3
Ensure the vehicle is on a stable lift or jack stands to prevent it from falling.
- 4
Follow the manufacturer's specifications and guidelines for clutch installation.
- 5
Keep your workspace clean and organized to avoid accidents.
Example Answers
I always disconnect the battery first to prevent any electrical issues. I wear safety glasses and gloves for protection, and I ensure the car is on a stable lift to avoid accidents.
Don't Just Read Clutch Specialist Questions - Practice Answering Them!
Reading helps, but actual practice is what gets you hired. Our AI feedback system helps you improve your Clutch Specialist interview answers in real-time.
Personalized feedback
Unlimited practice
Used by hundreds of successful candidates
How do you stay updated on the latest clutch technologies and trends in the industry?
How to Answer
- 1
Subscribe to industry journals and magazines focused on automotive technology.
- 2
Join online forums and social media groups for clutch professionals and enthusiasts.
- 3
Attend industry conferences and trade shows to network and learn from experts.
- 4
Take online courses or webinars that cover new clutch technologies and best practices.
- 5
Follow key influencers and companies in the clutch manufacturing space on LinkedIn and Twitter.
Example Answers
I subscribe to several automotive industry journals and I regularly read articles on new clutch technologies. Additionally, I participate in online forums where professionals discuss the latest trends and innovations.
What procedural steps do you take to ensure a clutch is installed correctly?
How to Answer
- 1
Gather all necessary tools and parts before beginning the installation
- 2
Follow the manufacturer's specifications for the clutch installation process
- 3
Ensure the flywheel is prepared and in good condition before mounting the clutch
- 4
Align the clutch plate properly using alignment tools to prevent misalignment
- 5
Test the clutch operation after installation to ensure it functions smoothly.
Example Answers
I start by making sure I have all my tools and parts ready, then I refer to the manufacturer's instructions for step-by-step guidance. I inspect the flywheel for wear, clean it if needed, and ensure everything is aligned properly before securing the clutch in place. Finally, I test the clutch operation in the vehicle before finishing up.
Situational Interview Questions
Imagine a customer calls in reporting that their clutch has failed while driving. What steps do you recommend they take?
How to Answer
- 1
Stay calm and reassure the customer that you can help them
- 2
Ask about their current location to understand how to assist
- 3
Instruct them to safely pull over to the side of the road if they haven't already
- 4
Advise them to turn off the engine to prevent further damage
- 5
Suggest contacting a tow service if they cannot drive the vehicle safely
Example Answers
I would first reassure the customer that I'm here to help. I would ask where they are and advise them to safely pull over if they haven't. After that, I would tell them to turn off the engine to avoid any further issues and recommend that they call for a tow service if the car is not drivable.
If you are unsure about a specific clutch problem during a repair, how would you proceed?
How to Answer
- 1
Assess the symptoms carefully before making assumptions.
- 2
Refer to the service manual or manufacturer guidelines for troubleshooting.
- 3
Consult with a more experienced technician if possible.
- 4
Check online resources or forums for similar issues and solutions.
- 5
Document your findings and steps taken for future reference.
Example Answers
I would start by carefully reviewing the symptoms to understand the issue better. Next, I'd consult the service manual for potential troubleshooting steps. If I'm still unsure, I'd reach out to a more experienced technician for guidance.
Don't Just Read Clutch Specialist Questions - Practice Answering Them!
Reading helps, but actual practice is what gets you hired. Our AI feedback system helps you improve your Clutch Specialist interview answers in real-time.
Personalized feedback
Unlimited practice
Used by hundreds of successful candidates
You have a disagreement with a coworker about the best method to install a clutch. How would you resolve this?
How to Answer
- 1
Listen to your coworker's perspective carefully.
- 2
Explain your method and reasoning clearly.
- 3
Propose a trial installation with both methods if possible.
- 4
Stay professional and focus on finding the best solution.
- 5
Document the final decision and rationale for future reference.
Example Answers
I would first listen to my coworker's method and the reasons behind it. Then, I would share my approach and the benefits I see. If we still disagree, I’d suggest we try both methods on a test project to see which works better.
You have multiple vehicles waiting for clutch repairs. How do you prioritize your workload?
How to Answer
- 1
Assess the urgency based on customer needs and safety issues.
- 2
Consider the complexity and time required for each repair.
- 3
Prioritize based on first-come, first-served for non-urgent cases.
- 4
Evaluate which repairs can be completed quickly to free up space.
- 5
Communicate expected timelines to customers to manage their expectations.
Example Answers
I would first evaluate each vehicle's urgency, particularly focusing on any safety concerns, and address those repairs first. Then I'd look at which vehicles have been waiting the longest before moving on to quicker repairs to optimize efficiency.
If a customer returns after a clutch installation reporting issues, how would you handle the situation?
How to Answer
- 1
Listen carefully to the customer's concerns and ask for specific details about the issues.
- 2
Apologize for the inconvenience and reassure them that you want to resolve the problem.
- 3
Assess the situation by asking questions about the installation and any symptoms they are experiencing.
- 4
Offer to inspect the installation and check for any errors or parts that may be malfunctioning.
- 5
Communicate clearly what steps you will take to resolve the issue and ensure they are satisfied.
Example Answers
I would listen to the customer's concerns to understand exactly what issues they are experiencing. Then I would apologize and ask them if they could describe the symptoms. After that, I would inspect the installation to ensure everything was done properly and check for any faulty parts. Finally, I would explain how I plan to fix the issue and keep them informed throughout the process.
A customer is unhappy about the cost of repairs and claims it's too high. How would you handle this?
How to Answer
- 1
Listen actively to the customer's concerns without interrupting.
- 2
Acknowledge their feelings and validate their frustration.
- 3
Explain the reasons behind the repair costs transparently.
- 4
Offer options or alternatives if possible, like payment plans.
- 5
Ensure to follow up with the customer after the conversation.
Example Answers
I would start by listening carefully to the customer's concerns and acknowledging that repairs can be costly. Then, I would explain why the repairs are priced as they are, citing quality parts and skilled labor. If suitable, I would discuss potential payment options to ease their burden.
How would you manage your time and workflow if you had a sudden influx of clutch repair jobs?
How to Answer
- 1
Prioritize jobs based on urgency and complexity
- 2
Use a scheduling tool to allocate time slots for each job
- 3
Communicate with customers about estimated wait times
- 4
Delegate tasks to team members if possible
- 5
Monitor progress and adjust schedules as needed
Example Answers
I would first prioritize the clutch jobs based on urgency, such as those needing immediate attention or simple fixes. Then, I would use a scheduling tool to effectively allocate time slots for each repair. Clear communication with customers about wait times is essential, and I would delegate tasks within my team to ensure efficiency.
If you notice a pattern of failures in a specific make and model's clutch system, what steps would you take to address this?
How to Answer
- 1
Identify the common failure points based on collected data.
- 2
Consult manufacturer service bulletins for known issues.
- 3
Engage with other technicians for shared experiences and solutions.
- 4
Implement a systematic diagnosis to pinpoint root causes.
- 5
Recommend design or material changes if necessary to address underlying issues.
Example Answers
I would first analyze repair records to identify the common failures and their symptoms. Then, I would check the manufacturer's service bulletins for any recalls or technical service issues related to the model. Engaging with my colleagues might provide additional insights that could pinpoint the root cause of the failures. If needed, I would suggest material or design improvements to prevent future issues.
How would you collaborate with the sales team to ensure they communicate accurate information about clutch services?
How to Answer
- 1
Schedule regular meetings with the sales team to discuss updates on clutch services.
- 2
Provide the sales team with comprehensive training on clutch products and services.
- 3
Create easy-to-understand reference materials that summarize key clutch information.
- 4
Encourage open communication for any questions or clarifications sales may have.
- 5
Monitor feedback from customers and sales to refine information sharing.
Example Answers
I would set up weekly meetings with the sales team to review key features of our clutch services, ensuring they have the latest information. Additionally, I would provide them with quick reference guides to use during customer interactions.
You encounter an unfamiliar clutch system. How do you approach troubleshooting it?
How to Answer
- 1
Start by gathering information about the vehicle and clutch system type.
- 2
Inspect and test the system visually for any obvious issues or leaks.
- 3
Consult the vehicle manual or technical resources for specifications and common issues.
- 4
Test individual components such as the master and slave cylinders.
- 5
Document your findings and proceed with repairs based on identified issues.
Example Answers
First, I would gather data about the vehicle model and clutch system from the manual. Then, I would visually inspect for leaks or damage. After that, I would check the components like the master and slave cylinders to diagnose the problem accurately.
Don't Just Read Clutch Specialist Questions - Practice Answering Them!
Reading helps, but actual practice is what gets you hired. Our AI feedback system helps you improve your Clutch Specialist interview answers in real-time.
Personalized feedback
Unlimited practice
Used by hundreds of successful candidates
Clutch Specialist Position Details
Related Positions
Ace Your Next Interview!
Practice with AI feedback & get hired faster
Personalized feedback
Used by hundreds of successful candidates
Ace Your Next Interview!
Practice with AI feedback & get hired faster
Personalized feedback
Used by hundreds of successful candidates