Top 30 Dial Maker Interview Questions and Answers [Updated 2025]
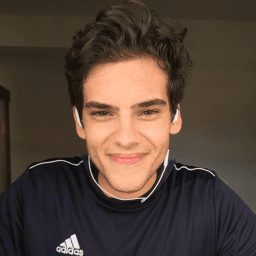
Andre Mendes
•
March 30, 2025
Preparing for a Dial Maker interview can be daunting, but we've got you covered with the most common questions you might encounter. In this updated 2025 guide, you'll find not just the questions but also example answers and valuable tips to help you respond effectively. Whether you're a seasoned professional or new to the field, this post will equip you with the confidence to succeed.
Download Dial Maker Interview Questions in PDF
To make your preparation even more convenient, we've compiled all these top Dial Makerinterview questions and answers into a handy PDF.
Click the button below to download the PDF and have easy access to these essential questions anytime, anywhere:
List of Dial Maker Interview Questions
Behavioral Interview Questions
Can you describe a time when you improved the dial-making process? What changes did you implement?
How to Answer
- 1
Identify a specific instance when you noticed inefficiencies in the process.
- 2
Explain the changes you proposed or implemented clearly.
- 3
Mention any tools or methods you used to track improvements.
- 4
Discuss the results of your changes and how they benefited the team or production.
- 5
Keep it concise and focus on your direct actions and their impact.
Example Answers
In my previous role, I noticed that the dial assembly process was taking longer due to manual measurements. I implemented a template for measuring that reduced setup time. As a result, we improved our production speed by 15%.
Tell me about a situation where you had to work closely with a team to meet deadlines in dial production.
How to Answer
- 1
Choose a specific project you worked on with your team.
- 2
Describe your role and how you contributed to the team's efforts.
- 3
Highlight the challenges you faced and how you overcame them together.
- 4
Emphasize the importance of communication and collaboration.
- 5
Conclude with the successful outcome and what you learned.
Example Answers
In my last project, we had to produce a new batch of dials for a product launch. My role was to oversee the quality control process. We faced a tight deadline due to unexpected supplier delays. I organized daily meetings to communicate progress, and we coordinated shifts to maximize production. We met the deadline with an excellent quality report, which reinforced the value of teamwork.
Don't Just Read Dial Maker Questions - Practice Answering Them!
Reading helps, but actual practice is what gets you hired. Our AI feedback system helps you improve your Dial Maker interview answers in real-time.
Personalized feedback
Unlimited practice
Used by hundreds of successful candidates
Give an example of how you handled a quality control issue with a dial. What steps did you take?
How to Answer
- 1
Identify the specific quality issue with the dial clearly.
- 2
Describe the tools or methods used to assess the quality problem.
- 3
Explain the immediate actions you took to resolve the issue.
- 4
Discuss the follow-up steps to prevent future occurrences.
- 5
Highlight any positive outcomes from your actions.
Example Answers
During a quality check, I noticed that some dials had inconsistent printing. I used a magnifying glass to assess the extent of the misalignment. I immediately stopped the production line, rectified the printer settings, and re-tested the printing process. I also documented the incident and trained the team to check alignment regularly. As a result, the overall defect rate dropped significantly.
Describe a challenging problem you encountered while making dials. How did you resolve it?
How to Answer
- 1
Identify a specific problem related to dial making.
- 2
Explain the context and what made the problem challenging.
- 3
Describe the steps you took to resolve the issue.
- 4
Highlight any tools or techniques you used.
- 5
Conclude with the positive outcome and what you learned.
Example Answers
During a production rush, the dials I was making had incorrect color matching. I realized the issue was due to a faulty calibration of the color mixing machine. I stopped production, recalibrated the machine, and ran tests to ensure accuracy. As a result, we were back on track within a few hours, and I learned the importance of equipment checks.
Recall a time when you had to adapt to a sudden change in production requirements for dials. How did you handle it?
How to Answer
- 1
Think of a specific situation where production requirements changed unexpectedly.
- 2
Describe your immediate reaction and assessment of the situation.
- 3
Explain the steps you took to adapt, including communication and re-prioritization.
- 4
Highlight any collaboration with team members to meet the new requirements.
- 5
End with the outcome and what you learned from the experience.
Example Answers
In my previous job, we suddenly received a last-minute order for 500 custom dials with unique specifications. I quickly gathered my team to discuss the new requirements, reassigned tasks based on urgency, and we worked overtime to meet the deadline. We successfully delivered the dials on time, learning the importance of flexibility and teamwork under pressure.
Tell me about a time when you introduced an innovative idea to improve dial design.
How to Answer
- 1
Choose a specific project to discuss
- 2
Describe the problem you identified with the existing design
- 3
Explain your innovative idea clearly and succinctly
- 4
Highlight any challenges you faced and how you overcame them
- 5
Conclude with the positive impact your idea had on the project
Example Answers
In a project to redesign our sports watch dial, I noticed the existing layout was cluttered and hard to read. I proposed a simplified design using larger, color-coded numbers and a more concise arrangement. The team was initially skeptical, but after showing visual prototypes, they agreed. We implemented the changes, and user feedback was overwhelmingly positive, resulting in a 20% increase in sales for that model.
Describe your experience dealing with customers regarding their preferences for dial designs.
How to Answer
- 1
Highlight specific instances where you interacted with customers about dial designs.
- 2
Show your understanding of customer preferences and how you accommodated them.
- 3
Mention any tools or software you used to visualize designs for customers.
- 4
Discuss feedback you received from customers and how it impacted design choices.
- 5
Emphasize communication skills and the importance of customer satisfaction.
Example Answers
In my previous role, I regularly met with clients to discuss their vision for custom dial designs. I took detailed notes on their preferences and used design software to create mock-ups, which helped facilitate feedback and adjustments until they were satisfied.
How have you incorporated feedback from supervisors into your work as a dial maker?
How to Answer
- 1
Reflect on specific instances when feedback was received.
- 2
Describe how you acted on that feedback in your work.
- 3
Highlight improvements or changes made as a result of the feedback.
- 4
Mention any ongoing dialogue with supervisors for continuous improvement.
- 5
Focus on measurable outcomes or enhanced skills from applying the feedback.
Example Answers
When I received feedback on my precision in dial calibrations, I started using a micrometer to ensure accuracy. As a result, the quality of my dials improved, and I received positive feedback from my supervisor regarding my enhanced precision.
Have you ever trained someone in dial making? What approach did you take?
How to Answer
- 1
Describe your experience training others in dial making clearly.
- 2
Mention any specific methods or techniques you used.
- 3
Include how you assessed the trainee's understanding and skills.
- 4
Talk about the importance of hands-on practice in mastering dial making.
- 5
Highlight any successful outcomes or improvements noted from the training.
Example Answers
Yes, I trained a new apprentice in dial making using a step-by-step approach. I started with the basics of materials and tools, then moved on to demonstrations. We worked on hands-on projects together, and I regularly checked their progress to ensure understanding.
Can you provide an example of how you managed a project related to dial making from start to finish?
How to Answer
- 1
Start by defining the project scope and objectives clearly.
- 2
Outline the steps taken, including design, materials selection, and manufacturing.
- 3
Discuss any challenges faced and how they were resolved.
- 4
Highlight collaboration with team members or stakeholders.
- 5
Conclude with the project outcome and any positive feedback received.
Example Answers
I managed a project to design a new watch dial. I started by defining the requirements with the client, then I created initial sketches and prototypes. We faced a challenge with the material selection which delayed the timeline; however, I resolved it by sourcing alternatives and negotiating with suppliers. The project was completed on time, and the client praised the quality of the final product.
Don't Just Read Dial Maker Questions - Practice Answering Them!
Reading helps, but actual practice is what gets you hired. Our AI feedback system helps you improve your Dial Maker interview answers in real-time.
Personalized feedback
Unlimited practice
Used by hundreds of successful candidates
Technical Interview Questions
What materials do you find most effective for dial making, and why?
How to Answer
- 1
Identify the primary materials used in dial making such as metals, ceramics, and plastics.
- 2
Explain the advantages of each material in terms of durability, aesthetics, and ease of manufacturing.
- 3
Discuss specific applications or examples where certain materials excel.
- 4
Mention any trends or innovations in materials that are relevant to the industry.
- 5
Be prepared to connect your material choices to quality and performance.
Example Answers
I find stainless steel to be highly effective for dial making due to its durability and resistance to tarnishing. It also allows for a polished finish that enhances aesthetics, making it ideal for luxury timepieces.
Explain your experience with the machinery used in dial manufacturing. Which equipment are you most proficient with?
How to Answer
- 1
Identify specific types of machinery you've used in dial manufacturing like lathes or CNC machines
- 2
Highlight your proficiency level with each equipment
- 3
Include any relevant certifications or training you've received
- 4
Mention any successful projects where you utilized this machinery
- 5
Conclude with a brief summary of your overall experience in the field.
Example Answers
I have worked extensively with CNC machines and lathes in dial manufacturing. My proficiency with CNC programming allows me to efficiently create intricate designs. Recently, I led a project where I fabricated precision dials using a CNC mill, resulting in a 15% reduction in production time.
Don't Just Read Dial Maker Questions - Practice Answering Them!
Reading helps, but actual practice is what gets you hired. Our AI feedback system helps you improve your Dial Maker interview answers in real-time.
Personalized feedback
Unlimited practice
Used by hundreds of successful candidates
Which software tools have you used for designing dials and what are their main features?
How to Answer
- 1
Identify specific software you've used for dial design
- 2
Highlight unique features of each software
- 3
Discuss your experience level with each tool
- 4
Mention any relevant projects where you used these tools
- 5
Be ready to explain how these tools contributed to your design process
Example Answers
I have used Adobe Illustrator for dial design, which allows for vector graphics and precise control over shapes and colors. Additionally, I’m familiar with SolidWorks, known for its 3D modeling capabilities that are essential for creating functional prototypes.
What methods do you use to ensure the accuracy and precision of dial measurements during production?
How to Answer
- 1
Utilize calibrated measuring instruments regularly.
- 2
Implement a standard operating procedure for measurements.
- 3
Perform regular maintenance and checks on equipment.
- 4
Train staff on measurement techniques and practices.
- 5
Document measurements and any discrepancies for review.
Example Answers
I ensure accuracy by using calibrated tools like micrometers and calipers, and I follow strict SOPs that detail the measurement process.
What production techniques do you think are essential in creating high-quality dials?
How to Answer
- 1
Focus on precision machining and finishing techniques.
- 2
Mention the importance of materials used for durability and aesthetics.
- 3
Include the role of quality control in ensuring accuracy.
- 4
Talk about innovative designs and technology in dial creation.
- 5
Highlight the significance of craftsmanship and manual skills.
Example Answers
High-quality dials require precision machining to ensure accuracy in size and shape. Using durable materials like sapphire crystals enhances the dial's longevity and visual appeal. Quality control checks guarantee that every dial meets strict standards.
Describe the finishing processes you utilize for dials. How do they impact the final product?
How to Answer
- 1
Identify key finishing processes such as polishing, coating, and printing.
- 2
Explain how each process enhances aesthetics or functionality.
- 3
Mention any quality control measures you implement during finishing.
- 4
Discuss the materials used and their impact on durability.
- 5
Provide an example of a specific dial you finished and its outcome.
Example Answers
I usually start with polishing to enhance the surface finish, which gives the dial a shiny appearance. Then, I apply a protective coating, which improves durability and prevents scratches. Finally, I ensure that all printings are clear and crisply defined, contributing to better readability.
What troubleshooting steps do you take if a dial production machine is malfunctioning?
How to Answer
- 1
Check the machine's display for error messages.
- 2
Inspect the power supply and connections to ensure they are secure.
- 3
Examine the mechanical components for blockages or wear.
- 4
Review the production logs for any recent changes or issues.
- 5
Conduct a test run after each adjustment to identify if the issue is resolved.
Example Answers
First, I would check the machine's display for any error codes that can pinpoint the issue. Then, I would verify the power supply and ensure all connections are tight. I would look for mechanical blockages, and finally, check production logs for any irregularities.
How do you analyze a dial design for manufacturability before starting production?
How to Answer
- 1
Review the design specifications and drawings for clarity.
- 2
Identify potential manufacturing challenges related to materials.
- 3
Assess the complexity of the design and its impact on production time.
- 4
Evaluate tolerance levels and how they affect the manufacturing process.
- 5
Consult with production teams to gather feedback on feasibility.
Example Answers
I start by reviewing the design specs to ensure all details are clear and accurate. Then, I look for any materials that may pose challenges, such as those that are difficult to source. Analyzing the design's complexity is also crucial to anticipate any time constraints during production. Finally, I discuss with the production team to get their insights on any potential issues.
What factors do you consider when scheduling dial production runs?
How to Answer
- 1
Assess the current inventory levels of dials
- 2
Consider customer demand and order backlog
- 3
Evaluate machine availability and maintenance schedules
- 4
Account for material availability and supplier lead times
- 5
Prioritize production of high-margin or urgent orders
Example Answers
I consider current inventory levels to ensure we meet demand without overproducing. I also look at the backlog of orders to prioritize the most urgent requests.
What is your approach to developing prototypes for new dial designs?
How to Answer
- 1
Start with concept sketching to visualize ideas
- 2
Use CAD software to create detailed designs
- 3
Select materials based on functionality and aesthetics
- 4
Build a physical prototype using rapid prototyping methods
- 5
Test and iterate based on feedback and functionality
Example Answers
I begin by sketching out my ideas to capture the initial concept. Then, I use CAD software to create a precise design. After selecting appropriate materials, I prototype using 3D printing, which allows for quick iteration based on testing.
Don't Just Read Dial Maker Questions - Practice Answering Them!
Reading helps, but actual practice is what gets you hired. Our AI feedback system helps you improve your Dial Maker interview answers in real-time.
Personalized feedback
Unlimited practice
Used by hundreds of successful candidates
Situational Interview Questions
If you have multiple orders for dials with similar deadlines, how would you prioritize your tasks?
How to Answer
- 1
Assess the complexity of each order to identify which tasks will take longer.
- 2
Identify any orders with critical requirements or specific customer needs.
- 3
Communicate with stakeholders to understand priorities and adjust if necessary.
- 4
Consider the order of operations and how delays in one task affect others.
- 5
Track your progress and adjust priorities as needed throughout the process.
Example Answers
I would first assess the complexity of each order. For instance, if one order requires a special design and others are standard, I would prioritize the more complex one. Next, I'd communicate with customers to clarify any urgent requirements.
Imagine you notice a design error in a dial shortly before production. What steps would you take?
How to Answer
- 1
Quickly assess the nature of the design error and its impact on functionality.
- 2
Communicate the issue to the design team immediately for potential solutions.
- 3
Propose a timeline for correcting the error before the production starts.
- 4
Document the error and the steps taken to address it for future reference.
- 5
Coordinate with production to delay if necessary, ensuring quality control.
Example Answers
I would first evaluate the design error to understand its implications. Then, I'd inform the design team right away so we can brainstorm potential fixes. After that, I'd suggest a feasible timeline for the corrections. I'd also document the issue and our response plan. If production needs to be delayed, I would communicate that clearly to keep everyone in the loop.
Don't Just Read Dial Maker Questions - Practice Answering Them!
Reading helps, but actual practice is what gets you hired. Our AI feedback system helps you improve your Dial Maker interview answers in real-time.
Personalized feedback
Unlimited practice
Used by hundreds of successful candidates
How would you respond if a client is unhappy with the design of a dial you created?
How to Answer
- 1
Listen actively to the client's concerns without interrupting.
- 2
Ask clarifying questions to fully understand the issue.
- 3
Acknowledge their feelings and show empathy regarding their disappointment.
- 4
Propose possible revisions or alternatives based on their feedback.
- 5
Follow up after changes to ensure client satisfaction.
Example Answers
I would start by listening to the client's specific concerns about the dial design. It's important to understand their perspective. I would show empathy and express that I value their feedback. Then, I would suggest some changes based on their input to better meet their expectations.
What would you do if you were assigned a project to create a new dial under a tight deadline?
How to Answer
- 1
Assess the requirements and scope quickly to understand what is needed.
- 2
Break the project into manageable tasks and prioritize them based on importance.
- 3
Communicate with team members to delegate responsibilities and gather input.
- 4
Set milestones and a clear timeline to monitor progress regularly.
- 5
Stay flexible and ready to adapt if challenges arise during the project.
Example Answers
First, I would gather the project requirements and clarify any uncertainties with my supervisor. Then, I would create a timeline and outline the key tasks, prioritizing critical elements. I would communicate with my team to allocate resources and responsibilities effectively, checking in regularly to ensure we stay on track under the deadline.
How would you handle a situation where a production method does not comply with safety regulations?
How to Answer
- 1
Identify the specific safety regulation that is being violated.
- 2
Assess the risks associated with the non-compliant production method.
- 3
Report the issue to the appropriate supervisor or safety officer immediately.
- 4
Suggest interim measures to mitigate risks while a solution is found.
- 5
Collaborate with the team to develop a compliant alternative method.
Example Answers
I would first identify the specific safety regulation being violated. Then, I would assess the risks associated with the non-compliant method and report this to my supervisor. I would also suggest interim safety measures to reduce risks while we work on a compliant solution.
If a critical material for dial making is delayed, what alternative solutions would you consider?
How to Answer
- 1
Identify potential substitute materials that meet specifications.
- 2
Consider adjusting the production schedule to accommodate the delay.
- 3
Explore partnerships with other suppliers for quick sourcing.
- 4
Inform stakeholders about the delay and proposed solutions.
- 5
Evaluate impact on project timelines and communicate adjustments.
Example Answers
I would first assess the specifications of the delayed material and look for any viable substitute that meets those requirements. If no substitute is available, I would then work to adjust our production schedule to minimize disruption while seeking to source the materials from other suppliers.
How would you handle a conflict with a team member regarding design choices for a new dial?
How to Answer
- 1
Listen carefully to the team member's perspective.
- 2
Clarify the reasons behind your own design choices.
- 3
Seek common ground and explore the pros and cons of each option.
- 4
Suggest a collaborative approach to find a compromise.
- 5
If needed, involve a third party for mediation.
Example Answers
I would start by listening to the team member's viewpoint and understanding their concerns. Then, I'd explain my design choices, focusing on the rationale behind them. By discussing the benefits and drawbacks of both designs, we can identify an approach that incorporates the best of both ideas.
What would you do if you discovered a batch of dials did not meet quality standards after production?
How to Answer
- 1
Immediately isolate the affected batch to prevent further distribution.
- 2
Conduct an investigation to determine the cause of the quality issue.
- 3
Communicate with your team and management about the findings and next steps.
- 4
Implement corrective actions based on the investigation results.
- 5
Document the incident and review procedures to prevent recurrence.
Example Answers
If I discovered a batch of dials that didn't meet quality standards, I would first isolate the batch to prevent it from being sent out. Next, I would analyze the production process to find out what went wrong. I would then inform my team and management about the issue. After identifying the root cause, I'd implement corrective actions, such as adjusting our processes or retraining staff. Finally, I would document everything and review our quality control procedures to ensure it doesn't happen again.
If a client requests multiple revisions to a dial design, how would you manage the process?
How to Answer
- 1
Acknowledge the client's vision and needs clearly
- 2
Set a structured timeline for revisions to manage expectations
- 3
Maintain open communication to gather feedback effectively
- 4
Prioritize revisions based on client feedback and urgency
- 5
Document all changes to keep track of the design evolution
Example Answers
I would start by acknowledging the client's feedback and clarify their vision for the dial design. Then, I would propose a timeline for revisions to ensure we stay on track. Open communication is vital, so I would regularly check in and collect their thoughts on each version. I’d prioritize the requests based on their urgency, and finally, I'd document each change for reference.
What actions would you take if faced with a supply chain issue affecting dial components?
How to Answer
- 1
Identify the source of the supply chain issue quickly.
- 2
Communicate with suppliers to assess availability and timelines.
- 3
Explore alternative suppliers or materials if necessary.
- 4
Adjust production schedules to minimize impact on delivery.
- 5
Implement contingency plans based on potential risks.
Example Answers
First, I would determine the specific cause of the supply chain disruption by communicating directly with our suppliers. Then, I would look for alternative suppliers who can meet our quality requirements and timelines, while adjusting our production schedules to minimize any delays in delivery.
Don't Just Read Dial Maker Questions - Practice Answering Them!
Reading helps, but actual practice is what gets you hired. Our AI feedback system helps you improve your Dial Maker interview answers in real-time.
Personalized feedback
Unlimited practice
Used by hundreds of successful candidates
Dial Maker Position Details
Related Positions
- Ring Maker
- Bead Maker
- Locket Maker
- Jewelry Maker
- Bracelet Maker
- Diamond Grader
- Fabricator
- Metal Engraver
- Dialer
- Die Maker
Similar positions you might be interested in.
Ace Your Next Interview!
Practice with AI feedback & get hired faster
Personalized feedback
Used by hundreds of successful candidates
Ace Your Next Interview!
Practice with AI feedback & get hired faster
Personalized feedback
Used by hundreds of successful candidates