Top 27 Die Designer Interview Questions and Answers [Updated 2025]
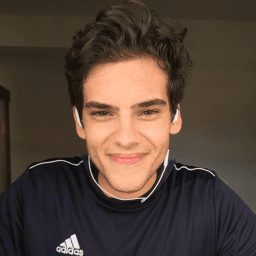
Andre Mendes
•
March 30, 2025
Preparing for a die designer interview can be daunting, but we're here to help you shine. In this blog post, we've compiled a list of the most common interview questions for the die designer role. You'll find example answers and practical tips to help you craft your responses effectively. Dive in to boost your confidence and ensure you're ready to impress potential employers with your expertise and insight.
Download Die Designer Interview Questions in PDF
To make your preparation even more convenient, we've compiled all these top Die Designerinterview questions and answers into a handy PDF.
Click the button below to download the PDF and have easy access to these essential questions anytime, anywhere:
List of Die Designer Interview Questions
Behavioral Interview Questions
Can you describe a challenging project you worked on as a die designer and how you overcame the obstacles?
How to Answer
- 1
Identify a specific project with clear challenges.
- 2
Describe the obstacles faced and their impact on the project.
- 3
Explain the strategies you implemented to overcome these challenges.
- 4
Highlight any collaboration or resources that aided your solutions.
- 5
Conclude with the positive outcome or lessons learned from the experience.
Example Answers
In a recent project, I designed a die for a complex product line requiring precision. The challenge was ensuring the die could withstand high pressure without distortion. I collaborated closely with the engineering team, using advanced materials to improve durability. This led to a successful production run with minimal defects, ultimately enhancing client satisfaction.
Tell me about a time you collaborated with other departments (e.g., production or engineering) to enhance a die design.
How to Answer
- 1
Choose a specific project where cross-department collaboration was key
- 2
Describe your role and contributions clearly
- 3
Mention the departments involved and how you interacted with them
- 4
Highlight the outcome and its impact on the final die design
- 5
Keep it concise but insightful, focusing on teamwork and results
Example Answers
In a recent project, I worked with the engineering team to redesign a die for better heat distribution. By sharing our insights during weekly meetings, we identified critical changes that improved durability. The final design led to a 20% increase in production efficiency.
Don't Just Read Die Designer Questions - Practice Answering Them!
Reading helps, but actual practice is what gets you hired. Our AI feedback system helps you improve your Die Designer interview answers in real-time.
Personalized feedback
Unlimited practice
Used by hundreds of successful candidates
Describe an instance where you took the lead on a die design project. What was the outcome?
How to Answer
- 1
Start with a clear project overview and your role in it
- 2
Highlight the specific design challenges you faced
- 3
Discuss the strategies you implemented to overcome those challenges
- 4
Share the measurable outcomes or impacts of your leadership
- 5
Reflect on what you learned and how it influenced future projects
Example Answers
In my last position, I led a project to design a complex die for a new product line. We faced challenges with material suitability and precision. I coordinated with engineers and suppliers, resulting in a 20% reduction in production time.
Give an example of how you have implemented new technologies or materials into your die designs.
How to Answer
- 1
Identify a specific technology or material you used.
- 2
Explain the problem it solved or improvement it made.
- 3
Describe the process of integrating it into your design.
- 4
Include measurable outcomes, if possible.
- 5
Stay focused on your role and contributions.
Example Answers
In my last project, I implemented a 3D printing technology to create die prototypes. This allowed for rapid iteration and reduced lead time by 30%, making the design phase much more efficient.
Have you ever had to adapt your design based on client feedback? How did you handle it?
How to Answer
- 1
Start with a specific example of client feedback.
- 2
Explain your initial design and the feedback received.
- 3
Detail the steps you took to adapt your design.
- 4
Highlight the positive outcome or learning from the experience.
- 5
Conclude with how it improved your relationship with the client.
Example Answers
In one project, the client wanted a more vibrant color palette than my original choice. After discussing their vision, I created three new options reflecting their preferences. They appreciated the adjustments, leading to a successful launch and ongoing collaboration.
How do you prioritize your tasks when faced with tight deadlines in your die design projects?
How to Answer
- 1
Identify critical tasks that directly affect project success
- 2
Break down large tasks into manageable steps and set mini-deadlines
- 3
Use project management tools to visualize task progress and bottlenecks
- 4
Communicate with team members about priorities and deadlines
- 5
Assess and adjust priorities regularly based on feedback and changing needs
Example Answers
I identify the critical tasks that have the biggest impact on the project's success and focus on them first. By breaking down larger tasks into smaller steps, I can set mini-deadlines and track my progress easily.
Tell me about a time when you had to explain a complex die design to a non-technical stakeholder.
How to Answer
- 1
Identify the main concept and simplify it for easy understanding.
- 2
Use analogies relevant to the stakeholder's background.
- 3
Break down the design into key components or steps.
- 4
Visual aids can enhance understanding; consider sketches or models.
- 5
Encourage questions to ensure clarity and engagement.
Example Answers
In my previous project, I explained a new die design for a packaging solution to the marketing team. I focused on the main functionality, comparing it to a puzzle that fits together, and used a simple diagram to illustrate how the die components interact. This helped them visualize the concepts effectively.
Describe a disagreement you had with a team member regarding a die design. How did you resolve it?
How to Answer
- 1
Start with a brief context of the disagreement.
- 2
Explain the differing viewpoints clearly.
- 3
Share the steps you took to resolve the issue.
- 4
Highlight the outcome and any learning points.
- 5
Emphasize collaboration and respect throughout the process.
Example Answers
In a recent project, a colleague and I disagreed on the thickness of a die design. I believed it needed to be thicker for durability, while they favored a thinner design for cost efficiency. We scheduled a meeting to discuss our perspectives, using data from previous designs to back our claims. Ultimately, we compromised by creating a prototype of both versions and tested them. The thicker die performed better in stress tests, and we decided to go with that option. This situation improved our communication and showed us the importance of testing ideas.
Technical Interview Questions
What CAD software do you prefer for designing dies, and why?
How to Answer
- 1
Identify your preferred CAD software based on your experience.
- 2
Mention specific features that enhance die design.
- 3
Explain how the software improves your workflow or design accuracy.
- 4
Relate your choice to the company's current tools or industry standards.
- 5
Offer a brief example of a project where the software made a difference.
Example Answers
I prefer SolidWorks for die design because its parametric modeling feature allows for precise adjustments. It's user-friendly and integrates well with our existing production software. In my last project, using SolidWorks helped streamline the design phase, reducing errors significantly.
What types of materials do you commonly work with in die making, and how do you choose the right one for a project?
How to Answer
- 1
Identify common materials like steel, aluminum, and plastic.
- 2
Discuss properties such as durability, cost, and ease of machining.
- 3
Consider project requirements like volume, type of product, and production speed.
- 4
Talk about the trade-offs between material types for specific uses.
- 5
Mention past experiences where material choice impacted project outcomes.
Example Answers
I commonly work with materials like tool steel for its durability and aluminum for lighter projects. I choose based on the production volume required; for high volume, I might opt for hardened steel to ensure longevity.
Don't Just Read Die Designer Questions - Practice Answering Them!
Reading helps, but actual practice is what gets you hired. Our AI feedback system helps you improve your Die Designer interview answers in real-time.
Personalized feedback
Unlimited practice
Used by hundreds of successful candidates
Can you explain the principles of die design that ensure durability and functionality?
How to Answer
- 1
Focus on material selection; strong materials enhance durability.
- 2
Design for wear resistance; incorporate features that minimize friction.
- 3
Optimize tolerances; ensure precise fits for proper functionality.
- 4
Consider thermal management; account for heat generated during operation.
- 5
Implement maintenance features; allow easy access for repair or inspection.
Example Answers
Durability in die design starts with selecting strong materials, such as tool steels, which can withstand high wear. Additionally, designing with wear-resistant coatings can help minimize friction and prolong the die's life.
What industry standards do you adhere to when creating die designs, and how do you keep updated with changes?
How to Answer
- 1
Identify specific industry standards relevant to die design, such as ISO or ANSI standards.
- 2
Mention tools or resources you use to stay informed, like industry publications or webinars.
- 3
Highlight any professional groups or organizations you are a member of that provide updates.
- 4
Discuss regular training or certifications you pursue to enhance your knowledge.
- 5
Show how you apply this knowledge in your design processes to ensure compliance.
Example Answers
I adhere to ISO 9001 standards in my die designs to ensure quality management. I regularly read industry journals and attend webinars to stay updated on any changes. Additionally, I'm a member of the Die Designers Association, which provides me with valuable resources and networking opportunities.
Describe your experience with prototyping die designs before final production.
How to Answer
- 1
Highlight specific tools or software used for prototyping.
- 2
Mention any collaboration with engineering or production teams.
- 3
Discuss the prototyping process, including testing and modifications.
- 4
Provide examples of successful prototypes and their impact on production.
- 5
Emphasize lessons learned from prototyping failures.
Example Answers
In my previous role, I used CAD software like SolidWorks to create prototypes of die designs. I collaborated closely with the engineering team to test these prototypes, which helped us identify design flaws early. One specific project resulted in a 20% reduction in production time because we addressed issues in the prototyping phase.
How do you determine the appropriate tolerances in your die designs?
How to Answer
- 1
Consider the material properties and machining capabilities to establish realistic tolerances.
- 2
Analyze the application and end-use of the die to understand functional requirements.
- 3
Collaborate with manufacturing engineers to align tolerances with production processes.
- 4
Use industry standards and guidelines as a reference point for tolerances.
- 5
Test and iterate on prototypes to refine tolerance specifications based on real-world performance.
Example Answers
I determine tolerances by first analyzing the material and its properties, then I consult with manufacturing engineers to ensure our tolerances are achievable during production.
What additional tools or software have you found helpful in your die design process, and how do you utilize them?
How to Answer
- 1
Identify specific tools or software you've used in die design.
- 2
Explain how each tool enhances your design efficiency or accuracy.
- 3
Provide examples of projects where the tools were particularly beneficial.
- 4
Mention any integrations with other software you find beneficial.
- 5
Keep your response concise and focused on relevance to die design.
Example Answers
I often use AutoCAD for precise 2D layout designs, allowing me to visualize the die before production. In a recent project, it helped identify potential issues early on, saving time and resources.
Situational Interview Questions
If a client demanded significant changes to a die design just days before production, how would you approach this situation?
How to Answer
- 1
Stay calm and listen to the client's concerns.
- 2
Evaluate the feasibility of the requested changes in the given timeline.
- 3
Communicate openly about potential impacts on cost and schedule.
- 4
Collaborate with your team to identify quick solutions.
- 5
Present options to the client that meet their needs while maintaining quality.
Example Answers
First, I would listen carefully to the client's concerns to fully understand the need for changes. Then, I would assess the timeline and discuss with my team to determine if the changes are feasible. Finally, I would communicate potential impacts to the client and propose alternative solutions that balance their requests with our production capabilities.
Imagine you encounter a technical issue during the die fabrication process. What steps would you take to resolve it?
How to Answer
- 1
Identify the root cause of the issue by reviewing process parameters.
- 2
Consult with team members or experts to gather additional insights.
- 3
Test potential solutions on a small scale before full implementation.
- 4
Document the issue and the steps taken to resolve it for future reference.
- 5
Communicate with stakeholders about the issue and the resolution plan.
Example Answers
First, I would diagnose the problem by checking the fabrication parameters. Then, I would collaborate with colleagues to gain different perspectives. After identifying a possible solution, I would run a test before rolling out the fix, ensuring that I document everything for future troubleshooting.
Don't Just Read Die Designer Questions - Practice Answering Them!
Reading helps, but actual practice is what gets you hired. Our AI feedback system helps you improve your Die Designer interview answers in real-time.
Personalized feedback
Unlimited practice
Used by hundreds of successful candidates
You are managing multiple die design projects with overlapping deadlines. What strategies would you use to ensure timely delivery?
How to Answer
- 1
Prioritize projects based on deadlines and complexity
- 2
Create a detailed timeline with milestones for each project
- 3
Utilize project management software to track progress
- 4
Delegate tasks to team members based on their strengths
- 5
Hold regular check-ins to address any potential delays
Example Answers
To manage overlapping die design projects, I prioritize based on deadlines and complexity. I then create a timeline with milestones for each project, using project management software to track progress and ensure we stay on target. Delegating tasks allows us to maximize efficiency, and regular check-ins help me spot any potential issues quickly.
How would you handle a situation where a client is dissatisfied with an initial die design proposal?
How to Answer
- 1
Listen actively to the client's concerns and feedback
- 2
Acknowledge their feelings and validate their perspective
- 3
Ask clarifying questions to fully understand their dissatisfaction
- 4
Propose a follow-up meeting to discuss adjustments and improvements
- 5
Present alternative design options based on their input
Example Answers
I would first listen carefully to the client's concerns, acknowledging their feelings. Then, I'd ask specific questions to clarify their issues, and suggest a follow-up meeting to brainstorm potential improvements together.
If you noticed a lack of communication within your team impacting a design project, how would you address it?
How to Answer
- 1
Identify the specific communication gaps affecting the project
- 2
Initiate a team meeting to openly discuss the issues
- 3
Encourage team members to share their thoughts and suggestions
- 4
Establish clear roles and responsibilities for each member
- 5
Follow up regularly to ensure communication improves
Example Answers
I would first identify what aspects of our communication were lacking. Then, I’d schedule a team meeting where everyone could express their concerns and propose solutions. I believe establishing clear roles would help as well, and I’d regularly check in to ensure things are improving.
You’re tasked with designing a die for a new product that has never been done before. How would you approach this?
How to Answer
- 1
Research existing die designs to identify trends and innovations.
- 2
Define the product's target audience and their needs.
- 3
Brainstorm unique features that could enhance functionality or aesthetics.
- 4
Create sketches or prototypes to visualize ideas.
- 5
Gather feedback from potential users to refine the design.
Example Answers
First, I'd look into current die designs for inspiration and innovations. Then, I'd identify the target audience to understand their preferences. I'd brainstorm features like customizable sides or textures. After sketching initial ideas, I'd create a prototype and seek user feedback for improvements.
How would you handle a situation where the final die output did not meet the quality standards expected?
How to Answer
- 1
Assess the issue by analyzing the specific aspects where the die falls short.
- 2
Communicate immediately with the team to understand potential causes.
- 3
Implement corrective actions based on analysis and team input.
- 4
Document the findings and changes made to prevent future occurrences.
- 5
Follow up on the adjustments to ensure the next output meets quality standards.
Example Answers
First, I would analyze the die to identify the specific quality issues. Then, I would discuss with my team to brainstorm potential causes and gather insights. Based on that information, I would implement corrective actions and document everything to refine our process for the future.
If you identified a safety issue in the die design process, what immediate actions would you take?
How to Answer
- 1
Assess the severity and potential impact of the safety issue.
- 2
Immediately report the issue to the project manager and relevant team members.
- 3
Suspend any ongoing work related to the affected die design until resolution.
- 4
Investigate the cause of the issue and gather data to support your findings.
- 5
Develop a plan for corrective measures and communicate it to the team.
Example Answers
I would first evaluate the severity of the safety issue to understand its impact. Then, I'd report it to my project manager and halt any work related to that die design. Next, I'd investigate the root cause and gather relevant information to propose corrective actions.
You're given a limited budget to complete a die project. How would you prioritize resources while maintaining quality?
How to Answer
- 1
Identify key features of the die that are essential to the project.
- 2
Allocate budget to areas with the highest impact on quality.
- 3
Consider cost-effective materials that still meet design standards.
- 4
Schedule efficient project timelines to avoid extra costs.
- 5
Seek collaboration or partnerships for shared resources or expertise.
Example Answers
I would focus on the essential features that directly affect the die’s functionality. Then, I'd allocate funds to high-impact areas like precision machining, while exploring alternative materials that can provide quality without breaking the budget.
During a project, you discover a new technique that could improve the design. What factors would you consider implementing it?
How to Answer
- 1
Evaluate how the new technique aligns with project goals
- 2
Assess the resources and skills needed for implementation
- 3
Consider the potential impact on the timeline and budget
- 4
Seek feedback from team members and stakeholders
- 5
Document the benefits and potential risks before deciding
Example Answers
I would first determine if the new technique supports our project goals. Then, I would assess if we have the right resources and skills to implement it effectively. I would also examine how this change might affect our timeline and budget, and gather feedback from my team to ensure everyone is on board.
Don't Just Read Die Designer Questions - Practice Answering Them!
Reading helps, but actual practice is what gets you hired. Our AI feedback system helps you improve your Die Designer interview answers in real-time.
Personalized feedback
Unlimited practice
Used by hundreds of successful candidates
How would you integrate feedback from the production team into your ongoing die design tasks?
How to Answer
- 1
Establish regular communication with the production team for ongoing feedback.
- 2
Create a structured feedback loop to document and prioritize suggestions.
- 3
Utilize prototyping to test recommendations quickly in your designs.
- 4
Incorporate production constraints into your design criteria from the outset.
- 5
Seek clarification on feedback to ensure accurate implementation.
Example Answers
I would set up weekly check-ins with the production team to gather their insights and ensure we're aligned on design needs. By using a feedback log, I can track their suggestions and prioritize changes for quick implementation.
When facing a backlog of die projects, how would you manage your workload to maintain both quality of work and personal well-being?
How to Answer
- 1
Prioritize projects based on deadlines and complexity.
- 2
Break tasks into manageable segments to avoid overwhelm.
- 3
Set specific, realistic daily goals for progress.
- 4
Schedule regular breaks to recharge and maintain focus.
- 5
Communicate with your team to delegate and seek support when needed.
Example Answers
I would first assess the backlog, prioritizing projects by urgency and complexity. Then, I'd break down larger tasks into smaller, achievable steps, setting daily goals to track my progress. Taking regular breaks would help me stay refreshed, and I'd communicate with my team to delegate when necessary.
Die Designer Position Details
Recommended Job Boards
ZipRecruiter
www.ziprecruiter.com/Jobs/Die-DesignerThese job boards are ranked by relevance for this position.
Related Positions
- Project Designer
- Product Designer
- AutoCAD Designer
- Technical Designer
- Body Designer
- Mold Designer
- Design Technician
- Mechanical Designer
- Pattern Drafter
- Design Checker
Similar positions you might be interested in.
Ace Your Next Interview!
Practice with AI feedback & get hired faster
Personalized feedback
Used by hundreds of successful candidates
Ace Your Next Interview!
Practice with AI feedback & get hired faster
Personalized feedback
Used by hundreds of successful candidates