Top 31 Dry Roller Interview Questions and Answers [Updated 2025]
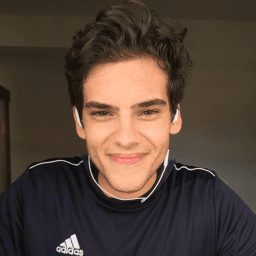
Andre Mendes
•
March 30, 2025
Preparing for a Dry Roller interview can be daunting, but with the right resources, you can walk into the room confidently. This blog post compiles the most common interview questions for the Dry Roller role, offering example answers and practical tips on how to respond effectively. Whether you're new to the industry or seeking to sharpen your interview skills, this guide will equip you for success.
Download Dry Roller Interview Questions in PDF
To make your preparation even more convenient, we've compiled all these top Dry Rollerinterview questions and answers into a handy PDF.
Click the button below to download the PDF and have easy access to these essential questions anytime, anywhere:
List of Dry Roller Interview Questions
Behavioral Interview Questions
Can you describe a time when you successfully worked as part of a team on a production line?
How to Answer
- 1
Choose a specific project or shift where teamwork was essential
- 2
Highlight your role and responsibilities within the team
- 3
Discuss how you communicated and collaborated with your teammates
- 4
Explain the outcome and any positive impact on production
- 5
Mention any challenges faced and how the team overcame them
Example Answers
During a busy production week, my team and I were tasked with increasing output. I took the lead in coordinating workstations and ensuring everyone was aligned on tasks. We communicated constantly via hand signals to minimize noise. Our teamwork resulted in a 15% increase in daily output, despite initial delays from equipment malfunctions.
Tell us about a challenging issue you faced while operating a dry roller and how you resolved it.
How to Answer
- 1
Identify a specific challenge you faced while operating the dry roller.
- 2
Explain the impact of this challenge on the work process.
- 3
Describe the steps you took to analyze and resolve the issue.
- 4
Highlight any collaboration with team members during the resolution.
- 5
Conclude with the positive outcome and what you learned from the experience.
Example Answers
While operating a dry roller, I faced a challenge with uneven terrain that was causing poor compaction. I analyzed the issue and found that adjusting the roller speed helped to better match the terrain. I communicated with my team and we worked together to regrade the area. In the end, the surface was compacted evenly, improving overall project quality.
Don't Just Read Dry Roller Questions - Practice Answering Them!
Reading helps, but actual practice is what gets you hired. Our AI feedback system helps you improve your Dry Roller interview answers in real-time.
Personalized feedback
Unlimited practice
Used by hundreds of successful candidates
Describe a situation where you had to lead a team in maintaining equipment and what was the outcome.
How to Answer
- 1
Focus on a specific instance where you demonstrated leadership.
- 2
Highlight the equipment involved and the maintenance tasks.
- 3
Explain your role and how you motivated the team.
- 4
Discuss any challenges faced and how you overcame them.
- 5
Conclude with the positive outcome or lessons learned.
Example Answers
In my previous role, I led a team during a scheduled maintenance of our production line machinery. I created a detailed checklist of tasks and assigned roles to each team member based on their strengths. We faced some unexpected equipment failures, but I encouraged open communication, which helped us troubleshoot effectively. The maintenance was completed ahead of schedule, resulting in reduced downtime and improved efficiency in our operations.
Give an example of how you prioritized safety while operating heavy machinery.
How to Answer
- 1
Start with a specific situation or task you were involved in.
- 2
Mention safety protocols you followed before operating the machinery.
- 3
Describe any training or certifications that support your knowledge of safety.
- 4
Explain how you communicated safety measures with your team.
- 5
Conclude with the positive outcomes of prioritizing safety.
Example Answers
In my previous role, I had to operate a roller for road construction. Before starting, I conducted a thorough pre-operation safety check, ensuring all safety guards were in place. I followed the safety protocols outlined in my training and communicated with my crew about blind spots during operation. As a result, we completed the project without any incidents.
Describe a time when your attention to detail helped you avoid a mistake during a production run.
How to Answer
- 1
Select a specific production run example.
- 2
Highlight the mistake that could have occurred.
- 3
Explain what detailed checks you performed.
- 4
Describe the positive outcome of your attention to detail.
- 5
Conclude with how this experience shapes your approach today.
Example Answers
During a production run of bottles, I noticed discrepancies in the labels. I double-checked them against the specifications and caught that some had incorrect batch numbers. By correcting the labels before they were applied, we avoided a costly recall and ensured product integrity.
Can you tell me about a time you had a disagreement with a colleague and how you resolved it?
How to Answer
- 1
Focus on a specific example from your experience
- 2
Explain the nature of the disagreement clearly
- 3
Describe your approach to resolving the conflict
- 4
Highlight the outcome and what you learned
- 5
Emphasize communication and collaboration in resolution
Example Answers
In my last job, I disagreed with a colleague over the best approach to a project deadline. I felt we should prioritize quality, while they wanted to rush for the deadline. I arranged a meeting to discuss our viewpoints, and we explored the implications of both strategies. Ultimately, we compromised by setting a phased deadline that allowed time for quality checks. This experience taught me the importance of balancing deadlines with project quality.
Describe a time when you took the initiative to improve the workflow or efficiency during production.
How to Answer
- 1
Identify a specific situation where you saw inefficiency.
- 2
Explain the steps you took to address the issue.
- 3
Highlight the positive outcomes of your actions.
- 4
Use numbers or metrics if possible to show improvement.
- 5
Keep the answer focused on your direct actions and their impact.
Example Answers
In my previous role, I noticed that our sorting process for incoming materials was causing delays. I suggested we implement a color-coded labeling system to speed up identification. After the change, the sorting time decreased by 30%, which improved our overall production flow.
What drives you to maintain a strong work ethic while performing repetitive tasks?
How to Answer
- 1
Link your motivation to personal goals or values.
- 2
Highlight your commitment to quality, even in routine work.
- 3
Mention the importance of teamwork and reliability.
- 4
Express how you find satisfaction in the completed work.
- 5
Share any techniques you use to stay focused and engaged.
Example Answers
I maintain a strong work ethic because I take pride in delivering consistent quality. I believe that even repetitive tasks contribute to the success of the team.
Describe an experience where you learned a new skill or process quickly to adapt to a job.
How to Answer
- 1
Choose a specific experience relevant to the role.
- 2
Highlight the skill or process you needed to learn.
- 3
Explain the urgency or reason for learning it quickly.
- 4
Describe the steps you took to learn and adapt.
- 5
Conclude with the positive outcome or impact of your adaptability.
Example Answers
In my previous role, I had to learn how to operate a new dry roller in just one week before a big project. I researched the machine's manual, watched online tutorials, and practiced daily with a mentor. I successfully completed the project on time, which impressed my supervisor.
Don't Just Read Dry Roller Questions - Practice Answering Them!
Reading helps, but actual practice is what gets you hired. Our AI feedback system helps you improve your Dry Roller interview answers in real-time.
Personalized feedback
Unlimited practice
Used by hundreds of successful candidates
Technical Interview Questions
What types of dry rollers have you operated, and what are the key maintenance tasks for these machines?
How to Answer
- 1
Identify specific models of dry rollers you have experience with.
- 2
Mention key features that differentiate these models.
- 3
List routine maintenance tasks you performed on these machines.
- 4
Explain how maintenance impacts the performance of rollers.
- 5
Provide examples of any troubleshooting or repairs you handled.
Example Answers
I have operated Hamm and Caterpillar dry rollers. Key maintenance tasks included checking and maintaining the vibratory system, oil level checks, and inspecting the drum for wear. Regular maintenance ensures optimal compaction performance.
Explain the key processes involved in the dry rolling operation and how they contribute to product quality.
How to Answer
- 1
Identify the main stages of the dry rolling process.
- 2
Discuss how each stage impacts the end product.
- 3
Highlight the importance of control parameters like temperature and pressure.
- 4
Mention the role of material preparation in achieving consistency.
- 5
Conclude with how quality checks are integrated into the process.
Example Answers
The dry rolling operation involves stages such as material preparation, rolling, and quality control. Each stage affects product consistency and quality. For instance, controlling the rolling temperature ensures proper material flow, while uniform pressure during rolling improves surface finish. Additionally, pre-rolled material preparation is crucial for achieving consistent thickness. Finally, routine quality checks help maintain the required specifications throughout production.
Don't Just Read Dry Roller Questions - Practice Answering Them!
Reading helps, but actual practice is what gets you hired. Our AI feedback system helps you improve your Dry Roller interview answers in real-time.
Personalized feedback
Unlimited practice
Used by hundreds of successful candidates
How do you ensure product quality while operating a dry roller?
How to Answer
- 1
Check parameters like temperature and pressure regularly to ensure they meet specifications
- 2
Perform visual inspections of the roller and the product at different stages
- 3
Document any deviations from standard operating procedures and take corrective actions
- 4
Maintain equipment and conduct routine maintenance to prevent breakdowns
- 5
Gather feedback from quality control teams to continuously improve processes
Example Answers
I ensure product quality by regularly monitoring the temperature and pressure settings of the dry roller to stay within the required specifications. I also perform visual inspections throughout the process to check for anomalies.
What steps do you take to troubleshoot a malfunctioning dry roller?
How to Answer
- 1
Identify the symptoms of the malfunction such as noise, vibration, or uneven drying.
- 2
Check the power supply and connections to ensure the roller is receiving adequate power.
- 3
Inspect the roller for any visible wear or debris that might be obstructing its movement.
- 4
Test the settings and controls to confirm they are configured correctly for operation.
- 5
If necessary, consult the manual or technical specifications for specific troubleshooting tips.
Example Answers
First, I identify the symptoms like unusual noise or uneven drying, then check the power supply to ensure everything is properly connected.
What safety protocols must be followed when operating a dry roller?
How to Answer
- 1
Always wear the appropriate personal protective equipment like hard hats, gloves, and hearing protection.
- 2
Conduct a pre-operational inspection of the dry roller to check for any mechanical issues.
- 3
Ensure the area is clear of personnel and obstacles before starting the dry roller.
- 4
Be aware of the operating environment and avoid slopes or unstable ground.
- 5
Follow the manufacturer's guidelines for safe operation and maintenance procedures.
Example Answers
When operating a dry roller, I always wear my hard hat and gloves for protection. I also inspect the machine before use to identify any potential issues. Keeping the work area clear is crucial for safety.
Explain the procedure you follow to set up a dry roller for a new product run.
How to Answer
- 1
Start by reviewing the product specifications and requirements.
- 2
Ensure the machine is clean and free of any previous product residue.
- 3
Set the roller settings according to the product's process parameters.
- 4
Load the raw material into the hopper and check the feed mechanism.
- 5
Run a test batch to verify proper operation before full production.
Example Answers
First, I review the product specifications to understand the requirements. Then, I clean the dry roller thoroughly to remove any prior residue. Next, I adjust the roller settings as per the product parameters and load the raw material. Finally, I conduct a small test run to ensure everything is functioning correctly.
What inspections do you perform on the dry roller before and after daily operations?
How to Answer
- 1
Check for any visible damage to the body and components.
- 2
Inspect the condition of the rollers and pads for wear.
- 3
Confirm oil levels and check for leaks in the hydraulic system.
- 4
Test all operational controls and safety features for functionality.
- 5
Ensure that the operator's manual and safety gear are present and in good condition.
Example Answers
Before operations, I inspect the dry roller for any visible damage, check the rollers for wear, and verify oil levels. After use, I always test the controls to ensure everything is functional and look for any signs of leaks.
Describe your experience with routine maintenance on production equipment.
How to Answer
- 1
Start by mentioning your specific responsibilities in equipment maintenance.
- 2
Include examples of equipment you have worked with in previous roles.
- 3
Highlight any preventive maintenance schedules you followed.
- 4
Emphasize your attention to detail and commitment to safety standards.
- 5
Mention any improvements you implemented or issues you resolved.
Example Answers
In my previous job, I was responsible for routine maintenance of conveyor belts and motors. I followed a strict preventive maintenance schedule, performed inspections weekly, and addressed any wear and tear promptly. This reduced downtime by 20%.
What is your understanding of preventive maintenance in the context of dry rolling operations?
How to Answer
- 1
Define preventive maintenance clearly and specifically for dry rolling.
- 2
Mention key components of a preventive maintenance program.
- 3
Explain the importance of preventive maintenance in reducing downtime.
- 4
Discuss how it extends the lifespan of equipment.
- 5
Provide examples of tasks involved in preventive maintenance for dry rollers.
Example Answers
Preventive maintenance in dry rolling involves regularly scheduled inspections and servicing of equipment to prevent breakdowns. This includes tasks like lubricating moving parts and checking for wear. It minimizes unplanned downtimes and keeps operations smooth.
How do you stay informed about safety and operational regulations relevant to your work?
How to Answer
- 1
Regularly review industry publications and safety guidelines.
- 2
Attend safety training sessions and workshops.
- 3
Join professional organizations related to construction and safety.
- 4
Participate in safety meetings at your workplace.
- 5
Use online resources and government websites for the latest updates.
Example Answers
I subscribe to industry safety magazines and frequently check updates on government websites to stay informed about regulations.
Don't Just Read Dry Roller Questions - Practice Answering Them!
Reading helps, but actual practice is what gets you hired. Our AI feedback system helps you improve your Dry Roller interview answers in real-time.
Personalized feedback
Unlimited practice
Used by hundreds of successful candidates
Situational Interview Questions
If the roller begins to overheat during operation, what steps would you take to address the situation?
How to Answer
- 1
Immediately stop the roller to prevent damage
- 2
Allow the equipment to cool down before inspection
- 3
Check the coolant levels and refill if necessary
- 4
Inspect for any blockages in the cooling system
- 5
Document the incident and report it to a supervisor
Example Answers
First, I would stop the roller as soon as I notice it overheating to avoid any further damage. Then I would let it cool down before checking the coolant levels and refilling if needed. I'll also make sure there are no blockages in the cooling system before resuming operation.
Imagine your team is behind schedule on a project. How would you help motivate your team to meet the deadline?
How to Answer
- 1
Assess the current progress and identify bottlenecks
- 2
Communicate openly with the team about the urgency
- 3
Encourage collaboration and support among team members
- 4
Recognize and reward small wins to boost morale
- 5
Offer additional resources or assistance if necessary
Example Answers
I would first check in with the team to identify the reasons for the delay, then I would set clear short-term goals to motivate everyone to push towards the deadline together.
Don't Just Read Dry Roller Questions - Practice Answering Them!
Reading helps, but actual practice is what gets you hired. Our AI feedback system helps you improve your Dry Roller interview answers in real-time.
Personalized feedback
Unlimited practice
Used by hundreds of successful candidates
If you discover that the final product does not meet the quality standards, how would you handle this?
How to Answer
- 1
Assess the extent of the quality issue before taking action
- 2
Communicate the issue immediately with your supervisor or team
- 3
Identify the root cause of the quality problem
- 4
Propose a plan for corrective action to bring the product up to standard
- 5
Document the incident for future reference and improvement
Example Answers
First, I would assess how bad the quality issue is and gather all relevant data. Then, I would inform my supervisor right away to make sure we tackle the problem together. After that, I'd investigate to find out what caused the issue. Finally, I would suggest a corrective action plan and document everything to prevent future occurrences.
What would you do if you notice a significant issue with the dry roller just before a scheduled delivery?
How to Answer
- 1
Assess the issue quickly to understand its severity
- 2
Notify your supervisor immediately about the problem
- 3
Determine if temporary fixes are possible to meet delivery
- 4
Communicate with the delivery team about potential delays
- 5
Document the issue for future reference and analysis
Example Answers
I would first assess the severity of the issue to see if a quick fix is feasible. Then, I would inform my supervisor right away to discuss our options, including possibly rescheduling the delivery if needed.
If you see a colleague not following safety protocols, how would you approach the situation?
How to Answer
- 1
Observe the situation discreetly before acting.
- 2
Assess the immediate risk to safety.
- 3
Approach your colleague calmly and privately.
- 4
Express your concerns and remind them of the protocols.
- 5
Encourage teamwork by suggesting a review of safety practices together.
Example Answers
I would first observe the situation to ensure I have all the facts. If there is a risk, I would privately discuss my concerns with my colleague and remind them of the importance of following safety protocols for everyone's safety.
How would you convey important production changes to your team in a high-pressure situation?
How to Answer
- 1
Stay calm and composed to set a positive tone for the team.
- 2
Prioritize the key changes that need immediate attention without overwhelming the team.
- 3
Use clear and direct language to ensure everyone understands the changes.
- 4
Encourage questions to clarify understanding and address any concerns.
- 5
Follow up with a summary in writing to reinforce the changes discussed.
Example Answers
In a high-pressure situation, I would first take a moment to gather my thoughts and remain calm. I would clearly state the most critical changes that need to be made, ensuring that I use straightforward language. I would then encourage the team to ask questions to clarify anything they might not understand, and finally, I'd send a follow-up email summarizing those changes for everyone.
In an emergency situation where equipment fails, what is your immediate course of action?
How to Answer
- 1
Stay calm and assess the situation immediately.
- 2
Determine if it's safe to continue working or if evacuation is necessary.
- 3
Notify the supervisor or team leader right away.
- 4
Follow the emergency procedures outlined for equipment failure.
- 5
Perform any immediate safety measures to secure the area.
Example Answers
First, I would remain calm and quickly assess the failure to understand the situation. If it's safe, I would notify my supervisor and follow the emergency protocols in place.
How would you handle a situation where a client requests last-minute changes that affect production?
How to Answer
- 1
Acknowledge the client's request and its significance
- 2
Assess the feasibility and impact of the changes quickly
- 3
Communicate clearly with the client about potential implications
- 4
Suggest alternatives or compromises if possible
- 5
Act promptly while keeping team informed of changes
Example Answers
I would first acknowledge the client's request and understand why the changes are important to them. Then, I would quickly assess if those changes can be implemented without significantly affecting the production timeline. I would communicate any potential delays and suggest possible compromises to meet their needs as best as we can.
If you were informed of a sudden deadline change, how would you adjust your current work priorities?
How to Answer
- 1
Stay calm and assess the new deadline immediately
- 2
Identify the most critical tasks that need to be accomplished to meet the new deadline
- 3
Communicate with your team about the changes and seek their input on adjusting priorities
- 4
Reorganize your workflow, focusing on high-priority tasks first
- 5
Be flexible and ready to reassess the situation as needed
Example Answers
I would first take a moment to understand the new deadline and its implications. Then, I would list the current tasks and identify which ones are urgent. After that, I would communicate with my team to ensure everyone understands the change and we can work together to adjust our priorities effectively.
How would you approach reducing waste during the dry rolling process?
How to Answer
- 1
Analyze the current rolling process to identify waste points
- 2
Implement standard operating procedures for consistent material use
- 3
Train team members on efficient techniques and waste reduction practices
- 4
Monitor and measure waste regularly to find improvement opportunities
- 5
Use quality materials that minimize excess and rework
Example Answers
I would start by mapping the dry rolling process to identify where waste commonly occurs, such as material overuse or misalignment. Then, I would develop clear SOPs to reduce variations and ensure every team member understands how to use materials efficiently.
Don't Just Read Dry Roller Questions - Practice Answering Them!
Reading helps, but actual practice is what gets you hired. Our AI feedback system helps you improve your Dry Roller interview answers in real-time.
Personalized feedback
Unlimited practice
Used by hundreds of successful candidates
What would you do if you were part of a team that was not functioning well together?
How to Answer
- 1
Identify the issues causing dysfunction and communicate them openly.
- 2
Encourage team members to share their perspectives and listen actively.
- 3
Suggest team-building activities to improve collaboration.
- 4
Work towards setting clear goals and roles for team members.
- 5
Follow up regularly to ensure progress and make adjustments as needed.
Example Answers
I would start by discussing the specific challenges the team is facing during a meeting. I would encourage everyone to express their views. Then, I would suggest some team-building exercises to improve our working relationships.
Dry Roller Position Details
Related Positions
- Grey Washer
- Roller Operator
- Roller Machine Operator
- Roller Setter
- Roller Painter
- Wool Cleaner
- Soap Mixer
- Spot Cleaner
- Wool Scourer
- Fur Cleaner
Similar positions you might be interested in.
Ace Your Next Interview!
Practice with AI feedback & get hired faster
Personalized feedback
Used by hundreds of successful candidates
Ace Your Next Interview!
Practice with AI feedback & get hired faster
Personalized feedback
Used by hundreds of successful candidates