Top 28 Equipment Installer Interview Questions and Answers [Updated 2025]
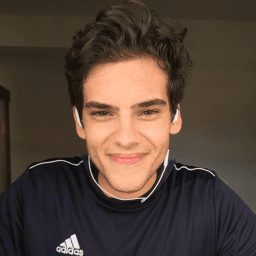
Andre Mendes
•
March 30, 2025
Navigating an interview for an Equipment Installer position can be daunting, but with the right preparation, you can stand out from the crowd. In this post, we cover the most common interview questions for this role, providing you with example answers and practical tips to craft your responses effectively. Whether you're a seasoned professional or new to the field, these insights will help you shine in your next interview.
Download Equipment Installer Interview Questions in PDF
To make your preparation even more convenient, we've compiled all these top Equipment Installerinterview questions and answers into a handy PDF.
Click the button below to download the PDF and have easy access to these essential questions anytime, anywhere:
List of Equipment Installer Interview Questions
Behavioral Interview Questions
Can you describe a time when you encountered a major issue during an equipment installation? How did you resolve it?
How to Answer
- 1
Choose a specific situation demonstrating your problem-solving skills
- 2
Explain the nature of the issue clearly and concisely
- 3
Discuss the steps you took to address the problem
- 4
Highlight the outcome and what you learned from the experience
- 5
Keep your answer focused on your contribution and actions
Example Answers
During an installation of a complex HVAC system, I discovered that a key component was damaged upon arrival. I quickly contacted the supplier for a replacement, while also modifying the installation plan to temporarily work around the issue. The supplier expedited the part, and we completed the installation ahead of schedule. I learned the importance of double-checking equipment before it arrives.
Tell me about a time when you worked as part of a team to complete an installation project. What was your role and how did you contribute?
How to Answer
- 1
Select a specific project that showcases teamwork.
- 2
Explain your specific role and responsibilities clearly.
- 3
Highlight how you communicated with the team members.
- 4
Discuss challenges faced and how you overcame them together.
- 5
Mention the outcome of the project and any feedback received.
Example Answers
In my last job, we installed a new HVAC system in a commercial building. I was the lead installer, coordinating with electricians and plumbers. I held daily meetings to ensure everyone was on the same page. We faced unexpected wiring issues but quickly devised a plan to solve it as a team. The project was completed ahead of schedule, and the client praised our teamwork.
Don't Just Read Equipment Installer Questions - Practice Answering Them!
Reading helps, but actual practice is what gets you hired. Our AI feedback system helps you improve your Equipment Installer interview answers in real-time.
Personalized feedback
Unlimited practice
Used by hundreds of successful candidates
Describe a situation where you had to prioritize safety while installing equipment. What steps did you take?
How to Answer
- 1
Identify a specific installation project.
- 2
Explain potential safety risks you recognized.
- 3
Detail the safety measures you implemented.
- 4
Mention tools or equipment used for safety.
- 5
Highlight the outcome of prioritizing safety.
Example Answers
During an HVAC installation at a commercial site, I noticed exposed electrical wires. I immediately shut off the power supply and used insulated tools to ensure safety while securing the wires. This prevented any potential shocks and allowed a smooth installation.
Give an example of a time you had to communicate complex installation instructions to a client or co-worker. How did you ensure understanding?
How to Answer
- 1
Start with a brief context of the situation.
- 2
Explain the complexity of the installation instructions.
- 3
Describe the methods you used to simplify the communication.
- 4
Highlight any feedback received from the client or co-worker.
- 5
Conclude with the outcome of the interaction.
Example Answers
In a recent project, I had to explain the setup of a complex HVAC system to a technician. I created a step-by-step visual guide and walked him through each phase, confirming understanding with questions after each step. This ensured he felt confident and followed the instructions correctly, leading to successful installation.
Can you provide an example of a time you took the initiative to improve an installation process? What was the outcome?
How to Answer
- 1
Identify a specific installation challenge you faced.
- 2
Describe the initiative you took to address it.
- 3
Explain the steps you followed to implement your solution.
- 4
Highlight the positive outcome and any metrics or feedback you received.
- 5
Reflect on what you learned and how it can apply to future situations.
Example Answers
In my previous job, we often faced delays due to equipment setup. I proposed a new layout for our tools and training sessions for our team. I created a checklist that streamlined the process. As a result, installation times decreased by 20% and customer satisfaction improved.
Describe a time you went above and beyond to ensure customer satisfaction during an equipment installation.
How to Answer
- 1
Select a specific installation experience.
- 2
Highlight an unexpected challenge faced during the installation.
- 3
Describe the actions you took to resolve the issue.
- 4
Emphasize the positive outcome and customer feedback.
- 5
Keep it concise and focus on your personal contribution.
Example Answers
During a recent installation, I discovered the customer's site had unexpected electrical issues. I coordinated with an electrician to resolve the problem quickly, ensuring the equipment was installed on schedule. The customer appreciated my initiative and wrote a glowing review.
Have you ever had to learn a new skill or technology for an installation? How did you approach this?
How to Answer
- 1
Identify a specific skill or technology you learned.
- 2
Explain the context of why it was necessary.
- 3
Describe your learning method, whether through courses, hands-on practice, or mentorship.
- 4
Share the outcome and how it benefited the installation process.
- 5
Highlight any ongoing learning or adaptation you continue to do.
Example Answers
In my last job, I needed to learn how to install a new type of HVAC system. I enrolled in an online course focused on the system's technology. After completing the course, I practiced with a mentor on several installations. This effort improved my efficiency and reduced installation time by 20%.
Tell us about a time when proper documentation was critical in your role as an equipment installer. What impact did it have?
How to Answer
- 1
Identify a specific project where documentation was crucial.
- 2
Explain the type of documentation used (manuals, schematics, checklists).
- 3
Highlight the consequences of having or lacking documentation.
- 4
Discuss how documentation improved efficiency or safety.
- 5
Conclude with what you learned or how it shapes your current work.
Example Answers
During an installation of a complex HVAC system, the technical manuals were essential. I followed the schematics closely, ensuring each component was placed according to the specifications. This prevented installation errors and ensured the system operated efficiently, reducing potential downtime for the client.
Technical Interview Questions
What types of equipment have you installed in the past? Can you detail the installation processes for a specific type?
How to Answer
- 1
List specific types of equipment installed
- 2
Mention any relevant certifications or training
- 3
Describe the basic steps of the installation process
- 4
Highlight safety protocols followed during installation
- 5
Share any challenges faced and how they were overcome
Example Answers
In my previous role, I installed HVAC systems, security systems, and industrial machinery. For HVAC, the installation process involved assessing the site, mounting the unit, connecting ductwork, and testing the system. I always follow safety protocols to ensure compliance and prevent accidents.
What tools and technologies do you typically use during equipment installation? Can you describe how you use them?
How to Answer
- 1
List specific tools relevant to the equipment being installed
- 2
Explain the purpose of each tool in the installation process
- 3
Mention any technologies or software you use for planning or monitoring
- 4
Provide a brief example of a recent installation
- 5
Keep your answers focused and relevant to the job
Example Answers
I typically use a cordless drill for fastening components, a level for ensuring everything is straight, and a multimeter for checking electrical connections. For each installation, I start by ensuring all tools are ready, then use the drill for assembly, and finally check with the multimeter.
Don't Just Read Equipment Installer Questions - Practice Answering Them!
Reading helps, but actual practice is what gets you hired. Our AI feedback system helps you improve your Equipment Installer interview answers in real-time.
Personalized feedback
Unlimited practice
Used by hundreds of successful candidates
How do you approach troubleshooting equipment malfunctions during or after installation?
How to Answer
- 1
Assess the situation and gather information from the user or installation notes.
- 2
Check the power source and connections first; they are often the simplest issues.
- 3
Refer to the equipment's manual for troubleshooting guidelines specific to the model.
- 4
Systematically test each component to isolate the problem area.
- 5
Document findings and solutions for future reference and easier resolution.
Example Answers
I start by gathering information from the user about the malfunction and reviewing installation notes. Then, I check the power connections as many issues stem from there. If the problem persists, I refer to the manual for specific troubleshooting steps before testing components individually to find the issue.
What regulations and standards do you follow when installing equipment? How do you ensure compliance?
How to Answer
- 1
Identify relevant industry regulations such as OSHA, ANSI, or local codes
- 2
Mention specific standards, like electrical or safety standards applicable to the equipment
- 3
Explain how you stay updated on any changes in regulations through training or resources
- 4
Describe your process for verifying compliance during and after installation
- 5
Highlight any certifications or training you have that relate to compliance
Example Answers
I follow OSHA regulations and local building codes to ensure safety and compliance during installations. I keep updated through online training and safety workshops. During installation, I conduct checklists to verify compliance, and I document all procedures for future reference.
Can you explain the safety procedures you follow when installing heavy equipment?
How to Answer
- 1
Always wear personal protective equipment like helmets, gloves, and steel-toed boots.
- 2
Conduct a thorough site assessment to identify hazards before starting work.
- 3
Follow the manufacturer's installation guidelines and safety manuals.
- 4
Use proper lifting techniques and equipment, such as hoists or forklifts when necessary.
- 5
Communicate clearly with your team to ensure everyone is aware of safety protocols.
Example Answers
I always wear the necessary PPE like helmets and gloves. Before starting, I assess the site for any hazards, and I ensure that we follow the manufacturer's installation guidelines closely.
What is the step-by-step process you follow for installing equipment and ensuring it operates correctly?
How to Answer
- 1
Start with a site assessment to understand the installation environment.
- 2
Gather and review all necessary tools and equipment before starting.
- 3
Follow the manufacturer's installation instructions carefully.
- 4
Test the equipment after installation to ensure it functions properly.
- 5
Document the installation process for future reference and troubleshooting.
Example Answers
I begin with a site assessment to ensure the space is suitable for the equipment. Then, I gather all tools and equipment I need. I proceed by following the manufacturer's guidelines for installation step by step. Once installed, I conduct thorough testing to verify everything works as expected. Finally, I document everything for future reference.
How do you go about diagnosing faults in installed equipment? Can you give an example?
How to Answer
- 1
Start with gathering information from the user about the issue.
- 2
Check for visible signs of damage or wear on the equipment.
- 3
Use diagnostic tools to run tests and analyze performance data.
- 4
Eliminate potential causes systematically until the fault is isolated.
- 5
Provide a clear example from past experience to illustrate your method.
Example Answers
I begin by talking to the user to understand the problem they are experiencing. Once I have the details, I inspect the equipment for any visible issues like loose connections. For instance, when I diagnosed a recurring malfunction in a conveyor belt system, I used a multimeter to check electrical components, eventually isolating a faulty sensor that needed replacement.
How do you ensure that equipment specifications are met during the installation process?
How to Answer
- 1
Review equipment specifications before starting the installation
- 2
Use a checklist to confirm all requirements are met
- 3
Perform a site assessment to ensure compatibility with installation location
- 4
Communicate with team members and stakeholders throughout the process
- 5
Conduct a final inspection to verify compliance with specifications
Example Answers
I always start by thoroughly reviewing the equipment specifications and using a checklist to ensure all requirements are met during the installation. This helps to avoid any oversights.
Can you explain the importance of load testing after installation and the process you follow for it?
How to Answer
- 1
Emphasize safety and compliance with regulations
- 2
Discuss how load testing ensures equipment functionality
- 3
Identify potential issues before they affect performance
- 4
Mention the specific steps you take during the testing process
- 5
Include examples of tools or methods you use for load testing
Example Answers
Load testing is crucial for ensuring safety and compliance. After installation, I check the equipment's load capacity by gradually applying weight and observing any discrepancies. My process includes using calibrated weights and monitoring for vibrations or anomalies, which helps identify issues early.
What procedures do you recommend for preventive maintenance of equipment after installation?
How to Answer
- 1
Schedule regular inspections to identify wear and tear early
- 2
Clean equipment routinely to prevent buildup of dirt and debris
- 3
Lubricate moving parts according to manufacturer's guidelines
- 4
Train operators on proper use and care to reduce damage
- 5
Keep a log of maintenance activities for tracking and compliance
Example Answers
I recommend scheduling regular inspections to catch any issues early. Cleaning the equipment frequently is also crucial to prevent dirt buildup. Additionally, lubricating moving parts as per the manufacturer's recommendations can extend the life of the equipment.
Don't Just Read Equipment Installer Questions - Practice Answering Them!
Reading helps, but actual practice is what gets you hired. Our AI feedback system helps you improve your Equipment Installer interview answers in real-time.
Personalized feedback
Unlimited practice
Used by hundreds of successful candidates
Situational Interview Questions
If a client is dissatisfied with the installation of their equipment, how would you handle the situation?
How to Answer
- 1
Listen carefully to the client's concerns without interrupting
- 2
Acknowledge their feelings and show empathy
- 3
Ask clarifying questions to understand the specific issues
- 4
Offer a solution or a way to rectify the problem
- 5
Follow up with the client after the solution is implemented
Example Answers
I would start by listening to the client’s concerns and acknowledging their dissatisfaction. I would ask questions to clarify the specific issues and then propose a solution, ensuring I follow up after the installation to confirm satisfaction.
Imagine you have multiple installations scheduled for the same day but encounter delays. How would you prioritize your tasks?
How to Answer
- 1
Assess the remaining time for each installation.
- 2
Identify installations with the highest urgency or customer need.
- 3
Communicate proactively with clients about any changes.
- 4
Check if any tasks can be rescheduled to free up resources.
- 5
Use tools or systems to track progress and manage time effectively.
Example Answers
I would first evaluate how much time is left for each installation. Next, I'd prioritize the ones with urgent deadlines or critical needs. I would inform the affected clients about the delays and try to reschedule less urgent tasks.
Don't Just Read Equipment Installer Questions - Practice Answering Them!
Reading helps, but actual practice is what gets you hired. Our AI feedback system helps you improve your Equipment Installer interview answers in real-time.
Personalized feedback
Unlimited practice
Used by hundreds of successful candidates
If you were in the middle of an installation and noticed a crucial component was missing, what steps would you take?
How to Answer
- 1
Stop the installation process immediately to avoid any complications.
- 2
Check if the component is available in your inventory or on-site.
- 3
Assess whether the installation can be temporarily paused while sourcing the part.
- 4
Communicate with your team or supervisor to report the issue and discuss next steps.
- 5
Ensure to document the missing component for future reference and to prevent recurrence.
Example Answers
Immediately halt the installation and check our inventory for the missing component. If it's not available, I would inform my supervisor and see if we can source it quickly or reschedule the installation.
If a customer has unrealistic expectations about the time needed for an installation, how would you manage their expectations?
How to Answer
- 1
Acknowledge the customer's request and show understanding
- 2
Provide a realistic timeline based on previous experiences
- 3
Explain factors that can affect installation time
- 4
Discuss the importance of quality over speed
- 5
Offer to provide regular updates throughout the installation process
Example Answers
I would first listen to the customer's expectations, then explain that based on similar installations, a realistic time frame is about three days, considering all necessary preparations.
Suppose you are leading a small team for an installation project, but team members are not performing as expected. What would you do?
How to Answer
- 1
Assess the situation by observing team dynamics and individual contributions
- 2
Communicate directly with team members to identify causes of underperformance
- 3
Provide clear expectations and deadlines to ensure everyone understands their roles
- 4
Offer support and resources to help team members overcome challenges
- 5
Monitor progress closely and provide feedback to keep the team on track
Example Answers
I would start by speaking with each team member to understand any challenges they are facing. After identifying the issues, I'd clarify expectations and offer additional resources if needed. Regular check-ins would keep everyone aligned.
If a technician on your team is struggling to understand the installation procedures of a new piece of equipment, how would you assist them?
How to Answer
- 1
Identify the specific areas where the technician is having difficulty.
- 2
Provide step-by-step demonstrations of the installation process.
- 3
Encourage questions and create an open environment for learning.
- 4
Offer written resources or guides to supplement their understanding.
- 5
Set up a buddy system with a more experienced technician for ongoing support.
Example Answers
I would first talk to the technician to understand exactly where they are struggling. Then, I would provide a hands-on demonstration of the installation process, walking them through each step while encouraging them to ask questions as we go along.
If faced with an unexpected equipment failure just before an installation, how would you handle rescheduling?
How to Answer
- 1
Quickly assess the cause of the failure and potential solutions.
- 2
Communicate promptly with the client about the delay.
- 3
Coordinate with the team to find a suitable rescheduling date.
- 4
Keep the client informed of updates during the process.
- 5
Document the issue for future reference and prevention.
Example Answers
I would first identify the equipment issue and determine if it can be fixed quickly. Then, I would notify the client as soon as possible, explaining the situation and proposing a new installation date. Following that, I would work with my team to ensure we have the right resources available for the new schedule.
If a contractor doesn't follow the installation guidelines you've given them, how would you address this?
How to Answer
- 1
Stay calm and professional when addressing the issue
- 2
Ask open-ended questions to understand their reasoning
- 3
Reiterate the importance of following the guidelines
- 4
Offer support and clarification on the installation process
- 5
Document the conversation and any agreed-upon next steps
Example Answers
I would first discuss the situation with the contractor to understand why they deviated from the guidelines. After that, I would remind them how critical it is to follow the instructions for safety and efficiency. I would offer my help to clarify any misunderstandings.
How would you approach an installation that involves unusually complex components or configurations?
How to Answer
- 1
Break down the installation into smaller, manageable steps.
- 2
Review the manufacturer's instructions thoroughly before beginning.
- 3
Consult with team members or supervisors for their insights and experiences.
- 4
Use diagrams or models to visualize the configuration.
- 5
Test components individually before final installation to ensure compatibility.
Example Answers
I would start by breaking down the installation into smaller steps and review the manufacturer's instructions carefully. Collaborating with my team to discuss our insights would be crucial, and I would utilize diagrams to visualize the setup accordingly.
Equipment Installer Position Details
Salary Information
Recommended Job Boards
CareerBuilder
www.careerbuilder.com/jobs/equipment-installerZipRecruiter
www.ziprecruiter.com/Jobs/Equipment-InstallerThese job boards are ranked by relevance for this position.
Related Positions
Ace Your Next Interview!
Practice with AI feedback & get hired faster
Personalized feedback
Used by hundreds of successful candidates
Ace Your Next Interview!
Practice with AI feedback & get hired faster
Personalized feedback
Used by hundreds of successful candidates