Top 30 Equipment Manager Interview Questions and Answers [Updated 2025]
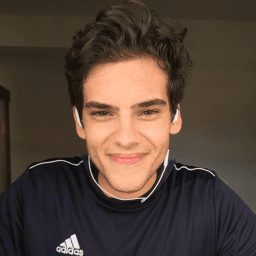
Andre Mendes
•
March 30, 2025
Preparing for an Equipment Manager interview can be daunting, but we've got you covered with the most common questions and expert tips to help you shine. In this post, you'll find example answers and strategies for responding effectively, ensuring you're ready to tackle any challenge. Dive in to boost your confidence and make a lasting impression in your next interview!
Download Equipment Manager Interview Questions in PDF
To make your preparation even more convenient, we've compiled all these top Equipment Managerinterview questions and answers into a handy PDF.
Click the button below to download the PDF and have easy access to these essential questions anytime, anywhere:
List of Equipment Manager Interview Questions
Behavioral Interview Questions
Can you describe a time when you had to work closely with a team to manage equipment efficiently?
How to Answer
- 1
Choose a specific project or situation for your example.
- 2
Highlight your role and contributions within the team.
- 3
Emphasize communication and coordination with team members.
- 4
Discuss the outcome and how it improved efficiency or performance.
- 5
Use the STAR method to structure your answer: Situation, Task, Action, Result.
Example Answers
In my previous role, our team was tasked with organizing an equipment upgrade for a major project. I coordinated with the maintenance team to assess current equipment needs and ensured proper scheduling for minimal downtime. This communication led to a smoother upgrade process and reduced our equipment handling time by 20%.
Tell me about a challenging situation you faced with equipment maintenance and how you resolved it.
How to Answer
- 1
Select a specific situation that highlights your problem-solving skills.
- 2
Explain the challenge clearly, focusing on what made it difficult.
- 3
Detail the steps you took to resolve the situation.
- 4
Mention any positive outcomes or lessons learned.
- 5
Keep your explanation concise and focused on your actions.
Example Answers
In my previous role, we faced a critical breakdown of our main compactor just before a major project deadline. I quickly assessed the issue, coordinated with our maintenance team to source replacement parts, and implemented temporary workarounds to keep operations running. We completed the project on time, and I learned the importance of proactive maintenance schedules.
Don't Just Read Equipment Manager Questions - Practice Answering Them!
Reading helps, but actual practice is what gets you hired. Our AI feedback system helps you improve your Equipment Manager interview answers in real-time.
Personalized feedback
Unlimited practice
Used by hundreds of successful candidates
Describe your experience in leading a team of technicians or operators in managing and maintaining equipment.
How to Answer
- 1
Highlight your leadership role and responsibilities
- 2
Mention specific equipment types you managed
- 3
Discuss strategies you implemented for team efficiency
- 4
Share a success story that illustrates your impact
- 5
Include any relevant metrics or achievements
Example Answers
In my previous role as an Equipment Manager, I led a team of six technicians in maintaining our fleet of construction equipment. We improved our maintenance response time by 30% by implementing a scheduled maintenance program that allowed us to address issues proactively.
Give an example of how you effectively communicated equipment needs to other departments.
How to Answer
- 1
Identify a specific situation where communication was essential.
- 2
Explain the method used to communicate, such as meetings or reports.
- 3
Highlight the importance of clear and concise messaging.
- 4
Discuss any feedback you received from other departments.
- 5
Share the positive outcomes that resulted from your communication.
Example Answers
In my previous role, I noticed our maintenance team needed more tools for repairs. I organized a meeting with the maintenance and purchasing departments to discuss the specific tools required, using a list I had compiled. This ensured everyone understood the urgency and the tools were ordered promptly, reducing downtime by 20%.
Describe a time when you had to adapt to a significant change in equipment management practices.
How to Answer
- 1
Think of a specific change, like new technology or procedures.
- 2
Describe your initial reaction to the change and any challenges faced.
- 3
Explain how you adapted, including training or collaboration efforts.
- 4
Highlight the positive outcomes of the adaptation for your team or organization.
- 5
Keep the focus on your role and contributions during the change.
Example Answers
In my previous role, our company switched from manual equipment tracking to an automated system. Initially, I was frustrated as I had to learn a new software. I dedicated time to understand the system through online tutorials and collaborated with the IT department. As a result, I became the point of contact for my team, ensuring a smooth transition and increasing our tracking efficiency by 30%.
Provide an example of a time when your attention to detail helped prevent a costly equipment issue.
How to Answer
- 1
Think of a specific incident where your detail-oriented approach made a difference.
- 2
Use the STAR method: Situation, Task, Action, Result to structure your example.
- 3
Focus on the equipment involved and the potential cost of the issue.
- 4
Highlight your proactive measures and the outcome of your actions.
- 5
Be prepared to explain what you learned from the experience.
Example Answers
In my previous job, I noticed that a maintenance schedule for our heavy machinery was not being followed correctly. I reviewed the records and discovered that a critical inspection was overdue. I alerted my supervisor, and we were able to perform the inspection just in time, which prevented a major breakdown and saved the company thousands in repairs.
Describe your approach to building and maintaining relationships with equipment suppliers.
How to Answer
- 1
Establish clear communication channels from the start.
- 2
Regularly check in and provide feedback on equipment performance.
- 3
Attend industry events to network with suppliers.
- 4
Develop trust by being transparent and meeting commitments.
- 5
Negotiate win-win scenarios to foster long-term partnerships.
Example Answers
I prioritize clear communication by setting up regular check-ins with suppliers to discuss equipment performance and any issues that arise. This helps us maintain a strong working relationship.
Describe a strategic plan you've created for equipment lifecycle management.
How to Answer
- 1
Identify the key stages of the equipment lifecycle: acquisition, operation, maintenance, and disposal.
- 2
Discuss specific metrics you used to evaluate equipment performance over its lifecycle.
- 3
Explain how you incorporated feedback loops for continuous improvement.
- 4
Mention collaboration with cross-functional teams for better resource allocation.
- 5
Highlight any cost-saving measures or efficiency improvements achieved.
Example Answers
In my previous role, I developed a lifecycle management plan that focused on monitoring equipment usage and scheduling maintenance based on runtime hours. This included a detailed analysis of repair costs versus replacement costs, enabling us to maintain optimal equipment availability while reducing overhead costs.
Don't Just Read Equipment Manager Questions - Practice Answering Them!
Reading helps, but actual practice is what gets you hired. Our AI feedback system helps you improve your Equipment Manager interview answers in real-time.
Personalized feedback
Unlimited practice
Used by hundreds of successful candidates
Technical Interview Questions
What methods do you use to assess the condition and efficiency of equipment?
How to Answer
- 1
Use regular inspections to check physical condition and functionality
- 2
Implement a maintenance log to track performance over time
- 3
Utilize software tools for real-time monitoring of equipment metrics
- 4
Analyze downtime records to identify patterns in equipment failure
- 5
Gather feedback from operators to assess usability and performance issues
Example Answers
I conduct regular inspections to assess physical wear and check for any operational issues. I also maintain a detailed log of maintenance activities to track performance trends over time.
How do you manage equipment inventory and ensure that tools and machines are available when needed?
How to Answer
- 1
Implement a systematic inventory tracking software.
- 2
Conduct regular physical audits of equipment.
- 3
Establish clear protocols for checking out and returning equipment.
- 4
Maintain relationships with suppliers for timely replenishment.
- 5
Train staff on proper equipment usage and reporting needs.
Example Answers
I utilize inventory tracking software that updates in real-time. Regular audits help me ensure that all tools are in the right place, and I have set up a check-out system to monitor equipment usage.
Don't Just Read Equipment Manager Questions - Practice Answering Them!
Reading helps, but actual practice is what gets you hired. Our AI feedback system helps you improve your Equipment Manager interview answers in real-time.
Personalized feedback
Unlimited practice
Used by hundreds of successful candidates
What preventive maintenance strategies do you implement to minimize equipment failures?
How to Answer
- 1
Identify key equipment and their critical failure points.
- 2
Establish a regular maintenance schedule based on manufacturer recommendations.
- 3
Implement tracking software to monitor maintenance activities and equipment performance.
- 4
Conduct routine inspections and training to ensure staff follow maintenance protocols.
- 5
Gather and analyze data on equipment failures to continuously improve maintenance strategies.
Example Answers
I focus on key equipment by identifying critical failure points and developing a regular preventive maintenance schedule based on manufacturer guidelines. I also use tracking software to log maintenance activities and proactively address any issues.
What safety standards must be adhered to when managing heavy machinery?
How to Answer
- 1
Familiarize yourself with OSHA regulations regarding heavy equipment.
- 2
Ensure daily inspections and maintenance checks are conducted.
- 3
Train operators on safety protocols and emergency procedures.
- 4
Use proper personal protective equipment (PPE) at all times.
- 5
Implement a system for reporting and addressing safety hazards promptly.
Example Answers
In managing heavy machinery, I strictly follow OSHA regulations, conduct daily inspections, and ensure all operators are trained on safety and emergency procedures.
Which equipment management software tools are you familiar with and how have you used them?
How to Answer
- 1
List the specific software tools you are familiar with.
- 2
Mention your experience with each tool and how you used them in previous roles.
- 3
Highlight any features of the software that you found particularly useful.
- 4
Emphasize the impact your use of these tools had on efficiency or cost savings.
- 5
Be prepared to discuss your learning process for new tools.
Example Answers
I have experience with CMMS software like UpKeep and Hippo. In my previous job, I used UpKeep to schedule maintenance and track equipment history, which helped reduce downtime by 20%.
What types of equipment have you managed in the past, and what unique challenges did each present?
How to Answer
- 1
Identify key types of equipment you have managed.
- 2
Highlight specific challenges for each type of equipment.
- 3
Discuss your strategies for overcoming these challenges.
- 4
Keep answers concise but informative.
- 5
Tailor your examples to the job description where applicable.
Example Answers
I managed construction machinery, including excavators and bulldozers. A challenge was maintaining equipment during peak seasons. I implemented a preventive maintenance schedule that reduced downtime.
What regulations and compliance issues do you need to consider in your equipment management role?
How to Answer
- 1
Identify key regulatory frameworks relevant to your industry such as OSHA or EPA.
- 2
Discuss the importance of safety standards and equipment certifications.
- 3
Mention the need for proper documentation and record-keeping for audits.
- 4
Highlight the role of environmental regulations in equipment disposal and maintenance.
- 5
Consider how compliance training for staff is essential in equipment management.
Example Answers
In my role as Equipment Manager, I ensure compliance with OSHA regulations to guarantee a safe work environment. I also keep detailed records for equipment inspections and certifications to avoid any legal issues.
What experience do you have with diagnosing equipment malfunctions and overseeing repair procedures?
How to Answer
- 1
Highlight specific equipment types you have worked with
- 2
Mention your diagnostic techniques or tools used
- 3
Explain how you prioritize repair tasks
- 4
Include any collaboration with technicians or engineers
- 5
Share a success story of a complex repair situation
Example Answers
In my previous role as a maintenance technician, I worked extensively with hydraulic systems and was responsible for diagnosing issues using both visual inspections and diagnostic software. I prioritized repairs based on the impact on operations, often collaborating with engineers to ensure efficiency in the repair process.
What emergency procedures should be in place for equipment failures?
How to Answer
- 1
Identify critical equipment and prioritize their failure responses
- 2
Establish clear communication channels for reporting issues
- 3
Develop a maintenance and inspection schedule to minimize failures
- 4
Train staff on emergency shutdown procedures and safety protocols
- 5
Create a contingency plan for replacing or fixing equipment quickly
Example Answers
We should have a priority response system for our most critical equipment, with protocols to immediately report failures through designated channels. Regular maintenance can prevent many issues.
How do you stay current with new technology and innovations in equipment management?
How to Answer
- 1
Attend industry conferences and expos focused on equipment management.
- 2
Subscribe to industry-specific journals and newsletters to receive updates.
- 3
Participate in online forums and professional groups related to equipment management.
- 4
Set aside time each week to research new technologies and trends online.
- 5
Network with peers and attend workshops to exchange knowledge and best practices.
Example Answers
I attend industry conferences regularly, where I can see firsthand the latest equipment innovations. I also subscribe to key industry journals to get insights on emerging trends and technologies.
Don't Just Read Equipment Manager Questions - Practice Answering Them!
Reading helps, but actual practice is what gets you hired. Our AI feedback system helps you improve your Equipment Manager interview answers in real-time.
Personalized feedback
Unlimited practice
Used by hundreds of successful candidates
Situational Interview Questions
Imagine a critical piece of equipment fails unexpectedly on a busy workday. What steps would you take to handle the situation?
How to Answer
- 1
Stay calm and assess the situation immediately
- 2
Identify the specific equipment that has failed
- 3
Notify relevant team members and stakeholders
- 4
Determine if a temporary fix or backup equipment is available
- 5
Plan for repair or replacement as soon as possible
Example Answers
First, I would assess the situation and confirm the equipment failure. Then, I would inform my team leaders and relevant staff members so they are aware. If we have backup equipment readily available, I'd arrange to use that while the faulty equipment is being repaired. Lastly, I would coordinate with our maintenance team to prioritize the repair process.
You have a limited budget for new equipment purchases. How would you prioritize your needs?
How to Answer
- 1
Assess the current inventory and identify any critical equipment failures.
- 2
Consider the impact on operations and prioritize equipment that increases efficiency.
- 3
Gather input from team members to understand their needs and any equipment gaps.
- 4
Evaluate any potential return on investment for new equipment purchases.
- 5
Make a phased plan for equipment acquisition based on urgency and budget.
Example Answers
I would first review our current equipment to identify any that are non-functional or outdated. Then, I would prioritize replacements that will have the greatest impact on our daily operations, such as equipment that if replaced would significantly reduce downtime.
Don't Just Read Equipment Manager Questions - Practice Answering Them!
Reading helps, but actual practice is what gets you hired. Our AI feedback system helps you improve your Equipment Manager interview answers in real-time.
Personalized feedback
Unlimited practice
Used by hundreds of successful candidates
If you encounter an unsatisfactory vendor, how would you approach renegotiating terms or seeking alternatives?
How to Answer
- 1
Assess the specific issues with the vendor's performance.
- 2
Prepare for the negotiation by gathering data on pricing and service standards.
- 3
Communicate clearly and professionally with the vendor about your concerns.
- 4
Explore alternative vendors while maintaining the relationship with the current vendor.
- 5
Define what terms are non-negotiable and what you are willing to compromise on.
Example Answers
I would first identify the exact issues with the vendor's service, such as delayed deliveries. Then, I'd prepare by researching comparable vendors and their pricing. During our meeting, I would address my concerns directly, suggest possible adjustments, and express my willingness to discuss solutions. If necessary, I would also investigate alternative vendors to ensure I have options.
If two team members disagreed on the best method for equipment maintenance, how would you mediate the situation?
How to Answer
- 1
Listen to both team members to understand their perspectives
- 2
Encourage open communication and respectful dialogue
- 3
Facilitate a discussion to evaluate the pros and cons of each method
- 4
Suggest a trial period for both methods to assess effectiveness
- 5
Aim for a compromise that incorporates the best elements of both approaches.
Example Answers
I would first listen to both team members without interruption to understand their viewpoints clearly. Then, I would facilitate a discussion to compare their methods, weighing the benefits and drawbacks. If needed, we could try both methods for a short period to determine which one works best in practice.
You receive data that shows declining equipment performance. How would you investigate and address this issue?
How to Answer
- 1
Review historical performance data to identify specific trends.
- 2
Conduct interviews or surveys with operators and maintenance staff for insights.
- 3
Examine maintenance logs for patterns that correlate with performance issues.
- 4
Assess equipment and ensure it meets operating standards and specifications.
- 5
Implement a plan to address identified issues with timeline and resources.
Example Answers
First, I would analyze the performance data over time to pinpoint when the decline started and look for patterns. Then, I would talk to operators to gather their experiences and feedback. After understanding their insights, I would review the maintenance logs for any related issues. Based on this information, I would ensure the equipment is operating correctly and develop a targeted plan to resolve any identified problems.
How would you train a new employee on the use of specific equipment?
How to Answer
- 1
Assess the employee's current knowledge level
- 2
Demonstrate equipment operation clearly and step-by-step
- 3
Encourage hands-on practice under supervision
- 4
Provide easy-to-understand manuals or guides
- 5
Schedule follow-up sessions to address questions and reinforce training
Example Answers
I would first understand what the new employee already knows about the equipment, then I would demonstrate its operation while explaining each step. After that, I would let them try using the equipment themselves while I supervise and offer guidance. Finally, I would provide them with written instructions for reference and check in with them later to see how they're doing.
How would you determine the most effective allocation of equipment across multiple projects?
How to Answer
- 1
Assess the equipment needs for each project based on their scope and timeline.
- 2
Evaluate the current availability and condition of equipment.
- 3
Prioritize projects based on their urgency and impact on the business.
- 4
Consider using a tracking system for real-time visibility of equipment utilization.
- 5
Communicate with project managers to understand their needs and adjust allocations.
Example Answers
I would start by listing the equipment requirements for each project, then assess what is currently available. I could rank projects based on their deadlines and importance, ensuring that critical projects receive the necessary equipment first. Regular communication with project managers would help align equipment allocation with ongoing needs.
If you noticed that equipment was underperforming, what steps would you take to improve its efficiency?
How to Answer
- 1
Conduct an initial assessment to identify specific performance issues.
- 2
Analyze data to pinpoint causes of underperformance.
- 3
Consult with team members for insights and suggestions.
- 4
Implement targeted maintenance or repair schedules.
- 5
Monitor equipment post-improvement to ensure efficiency gains.
Example Answers
I would start by assessing which equipment is underperforming and gather performance data to understand the issues. Then, I would involve my team to get their insights and suggestions. Based on this information, I would implement a targeted maintenance plan and closely monitor the equipment to ensure efficiency improves.
How would you approach optimizing equipment usage to increase productivity?
How to Answer
- 1
Assess current equipment usage to identify underutilized assets.
- 2
Implement regular maintenance schedules to reduce downtime.
- 3
Train staff on best practices for equipment handling.
- 4
Analyze equipment performance data to pinpoint inefficiencies.
- 5
Encourage feedback from operators to discover operational challenges.
Example Answers
I would start by analyzing the utilization rates of all equipment. By identifying which machines are underused, I can allocate resources more effectively and create a schedule that maximizes their use.
What would you do if equipment maintenance caused a delay in project timelines?
How to Answer
- 1
Acknowledge the impact of equipment maintenance on the project schedule
- 2
Communicate the issue promptly with all stakeholders
- 3
Explore immediate solutions such as alternative equipment or temporary workarounds
- 4
Review maintenance schedules to prevent future delays
- 5
Document the incident and outcomes for future reference
Example Answers
I would first assess the situation and communicate with my team and stakeholders about the delay. Then, I would look for any available alternative equipment or see if we could implement a temporary solution while the maintenance is completed. Finally, I would review our maintenance processes to ensure we can avoid similar delays in the future.
Don't Just Read Equipment Manager Questions - Practice Answering Them!
Reading helps, but actual practice is what gets you hired. Our AI feedback system helps you improve your Equipment Manager interview answers in real-time.
Personalized feedback
Unlimited practice
Used by hundreds of successful candidates
Equipment Manager Position Details
Salary Information
Recommended Job Boards
CareerBuilder
www.careerbuilder.com/jobs/equipment-managerZipRecruiter
www.ziprecruiter.com/Jobs/Equipment-ManagerThese job boards are ranked by relevance for this position.
Related Positions
- Jet Worker
- Fire Control Technician
- Weapons Mechanic
- Toy Mechanic
- Fire Extinguisher Installer
- Repairer
- Umbrella Repairer
- Display Mechanic
- Groundsman
- Pool Table Mechanic
Similar positions you might be interested in.
Ace Your Next Interview!
Practice with AI feedback & get hired faster
Personalized feedback
Used by hundreds of successful candidates
Ace Your Next Interview!
Practice with AI feedback & get hired faster
Personalized feedback
Used by hundreds of successful candidates