Top 31 Field Service Mechanic Interview Questions and Answers [Updated 2025]
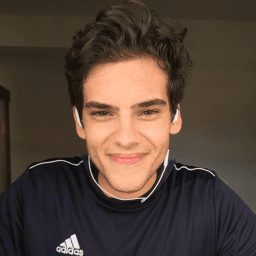
Andre Mendes
•
March 30, 2025
Navigating the interview process for a Field Service Mechanic role can be daunting, but this comprehensive guide is here to help. We've compiled the most common interview questions you might encounter, complete with example answers and tips to help you respond confidently and effectively. Whether you're a seasoned mechanic or a newcomer, this post will equip you with the insights needed to make a great impression.
Download Field Service Mechanic Interview Questions in PDF
To make your preparation even more convenient, we've compiled all these top Field Service Mechanicinterview questions and answers into a handy PDF.
Click the button below to download the PDF and have easy access to these essential questions anytime, anywhere:
List of Field Service Mechanic Interview Questions
Behavioral Interview Questions
Describe a time when you faced a mechanical failure in the field. How did you diagnose the issue?
How to Answer
- 1
Start by briefly describing the situation and the equipment involved
- 2
Explain the steps you took to diagnose the issue clearly
- 3
Include any tools or resources you used to assist in the diagnosis
- 4
Mention how your actions led to a successful resolution of the problem
- 5
Conclude with the learning outcome or how it improved your skills
Example Answers
During a field service visit to maintain an industrial generator, it failed to start. I tested the battery and discovered it was low on charge. I used a multimeter to check the connections, ensuring they were clean and secure. After recharging the battery, the generator started. This experience taught me to always check power sources first in troubleshooting.
Can you provide an example of a successful team project you worked on as a field service mechanic?
How to Answer
- 1
Choose a project where teamwork was essential.
- 2
Focus on your specific role and contributions to the project.
- 3
Include the outcomes or benefits of the project.
- 4
Mention any challenges you faced and how you overcame them.
- 5
Highlight how this experience improved team dynamics or efficiency.
Example Answers
On a project for a large construction site, our team had to repair multiple heavy machinery on a tight schedule. I took the lead in coordinating our work and communicating between the mechanics and the site manager. We completed the repairs ahead of time, minimizing downtime, and our team received commendations for our efficiency.
Don't Just Read Field Service Mechanic Questions - Practice Answering Them!
Reading helps, but actual practice is what gets you hired. Our AI feedback system helps you improve your Field Service Mechanic interview answers in real-time.
Personalized feedback
Unlimited practice
Used by hundreds of successful candidates
Tell me about a time when you had to deal with a difficult customer. How did you handle the situation?
How to Answer
- 1
Choose a specific example where you faced an upset customer.
- 2
Describe the customer's concern clearly and calmly.
- 3
Explain the steps you took to resolve the issue.
- 4
Highlight the positive outcome and what you learned.
- 5
Mention any follow-up actions you took to ensure customer satisfaction.
Example Answers
Once, a customer was frustrated because their machinery was down. I listened to their concerns, assured them I would help, and quickly diagnosed the problem. I managed to fix it within an hour, and the customer was relieved and thankful. They later praised our service, and I learned the importance of staying calm under pressure.
Give an example of a situation where you had to adapt quickly to a change while working in the field.
How to Answer
- 1
Choose a specific example from your experience.
- 2
Describe the initial situation and the unexpected change.
- 3
Explain the actions you took to adapt.
- 4
Highlight the positive outcome or what you learned.
- 5
Keep your answer focused and to the point.
Example Answers
While repairing a truck on-site, I discovered a critical part was missing. I quickly contacted the supplier for an emergency delivery and changed my plan to perform a different repair in the meantime. This kept the project on schedule.
Describe an experience where you had to ensure safety protocols were followed during a repair.
How to Answer
- 1
Think of a specific repair situation where safety was critical.
- 2
Explain the safety protocols you followed step by step.
- 3
Mention any tools or equipment used to maintain safety.
- 4
Highlight the outcome and how it ensured safety for everyone.
- 5
Conclude with what you learned about safety from that experience.
Example Answers
During a maintenance job on a heavy excavator, I ensured that safety protocols were followed by first verifying that all machines were powered down. I wore the necessary personal protective equipment like gloves and safety goggles. I used lockout/tagout procedures to prevent any accidental restarts, which ensured that I could work safely. The repair was successful, and I learned the importance of systematic safety checks.
Have you ever suggested a new approach or tool at your workplace? What was it and what was the outcome?
How to Answer
- 1
Choose a specific example relevant to your mechanical skills.
- 2
Explain the problem you identified that needed addressing.
- 3
Describe the new approach or tool you suggested clearly.
- 4
Share the outcome and any positive results from your suggestion.
- 5
Mention any feedback received from colleagues or management.
Example Answers
In my previous role, I noticed that our maintenance schedule was often delayed because we lacked a digital tracking system. I proposed implementing a software tool to monitor and schedule maintenance tasks. After we adopted the new tool, our efficiency improved by 30% and we were able to complete tasks on time more consistently.
Describe a time when you had to train a new team member. How did you approach it?
How to Answer
- 1
Start with a clear, specific example from your experience.
- 2
Explain your training plan and materials used.
- 3
Highlight your communication style and how you engaged the new member.
- 4
Mention any feedback or adjustments made during the training.
- 5
Conclude with the outcome and how the new team member performed.
Example Answers
I trained a new mechanic last summer. I created a step-by-step plan for his first week, focusing on safety protocols and basic repairs. I used hands-on demonstrations and encouraged questions. After a few days, I asked for feedback to adjust the pace. By the end of the month, he was confidently handling his tasks.
Can you tell me about a project that required a lot of effort and time? What motivated you to see it through?
How to Answer
- 1
Select a specific project relevant to mechanics or field service.
- 2
Highlight challenges faced and how you overcame them.
- 3
Emphasize your problem-solving skills and determination.
- 4
Explain the motivations that drove you, such as personal growth or project success.
- 5
Relate the project outcome to your passion for mechanics or customer satisfaction.
Example Answers
In my last role, I worked on overhauling an old generator for a client. It took several weeks and required sourcing rare parts. I was motivated by the challenge it presented and the satisfaction of restoring reliable service for the customer. Seeing their gratitude made all the effort worth it.
Describe a time when you had to respond to an emergency repair situation. What was your approach?
How to Answer
- 1
Identify a specific emergency repair incident you handled
- 2
Explain the urgency and impact of the situation
- 3
Detail the steps you took to assess and solve the problem
- 4
Highlight any teamwork or communication involved
- 5
Conclude with the outcome and what you learned
Example Answers
There was a time when I was called out to a site where a critical piece of machinery had broken down during peak hours. I quickly assessed the situation, identified it was a hydraulic failure, and communicated with the team about the urgency. I prioritized the repairs by gathering the necessary tools and replacement parts, working on it with a colleague. We completed the repair within an hour, minimizing downtime and ensuring the production resumed.
How do you manage stress during high-pressure service calls?
How to Answer
- 1
Stay calm and take deep breaths to clear your mind
- 2
Prioritize tasks based on urgency and importance
- 3
Communicate clearly with the customer to set expectations
- 4
Use your experience to troubleshoot efficiently and confidently
- 5
Take short breaks when possible to regain focus
Example Answers
I manage stress during high-pressure calls by staying calm and taking deep breaths to focus my mind. I prioritize the tasks at hand, addressing the most urgent issues first. Communication is key, so I always make sure to explain the process to the customer clearly, which helps reduce their stress as well.
Don't Just Read Field Service Mechanic Questions - Practice Answering Them!
Reading helps, but actual practice is what gets you hired. Our AI feedback system helps you improve your Field Service Mechanic interview answers in real-time.
Personalized feedback
Unlimited practice
Used by hundreds of successful candidates
Technical Interview Questions
What are some common hazards you look for when working on a job site?
How to Answer
- 1
Identify potential hazards specific to field service work.
- 2
Mention equipment-related hazards such as moving parts and electrical risks.
- 3
Discuss environmental hazards like weather conditions.
- 4
Highlight the importance of personal protective equipment.
- 5
Emphasize the need for proper training and safety protocols.
Example Answers
I look for equipment hazards such as moving parts on machinery and electrical risks. I also assess the job site for environmental factors like wet surfaces and extreme weather. Ensuring everyone is wearing the appropriate personal protective gear is essential.
What tools do you typically use for diagnosing mechanical problems in equipment?
How to Answer
- 1
List specific diagnostic tools you are familiar with and have used.
- 2
Explain the purpose of each tool in the diagnosis process.
- 3
Mention any software or digital tools if applicable.
- 4
Share a situation where a specific tool helped solve a problem.
- 5
Keep your answer concise and relevant to the position.
Example Answers
I typically use multimeters for electrical diagnostics, pressure gauges for hydraulic systems, and diagnostic software for electronic control systems. For example, I once used a multimeter to trace an electrical fault that was preventing a machine from starting.
Don't Just Read Field Service Mechanic Questions - Practice Answering Them!
Reading helps, but actual practice is what gets you hired. Our AI feedback system helps you improve your Field Service Mechanic interview answers in real-time.
Personalized feedback
Unlimited practice
Used by hundreds of successful candidates
Explain the difference between hydraulic and pneumatic systems.
How to Answer
- 1
Define both systems briefly to set context.
- 2
Mention the primary fluid used in each system.
- 3
Highlight the typical applications of hydraulic and pneumatic systems.
- 4
Discuss the advantages and disadvantages of each technology.
- 5
Keep the explanation clear and avoid technical jargon when possible.
Example Answers
Hydraulic systems use liquids like oil to transmit power, while pneumatic systems use compressible gases like air. Hydraulics are often used in heavy machinery like excavators, while pneumatics are common in factory automation.
How do you troubleshoot electrical systems to identify issues in machinery?
How to Answer
- 1
Start with safety and ensure power is off before investigation
- 2
Check for obvious signs of damage, such as burnt wires or loose connections
- 3
Use a multimeter to test for continuity and voltage in circuits
- 4
Consult schematics to understand the wiring and components involved
- 5
Isolate the problem by testing individual components and connections
Example Answers
I always begin by ensuring that the power is turned off to avoid any accidents. Then I visually inspect the wiring for any signs of wear or damage. If nothing is obvious, I use a multimeter to check for continuity in critical circuits, following the schematics until I pinpoint the fault.
What is your process for conducting preventative maintenance on machinery?
How to Answer
- 1
Start with understanding the equipment and manufacturer's recommendations
- 2
List and schedule regular maintenance tasks based on usage hours
- 3
Document and track maintenance history for pattern recognition
- 4
Use checklists to ensure no steps are missed during maintenance
- 5
Involve team members in the process for comprehensive coverage
Example Answers
I begin by reviewing the manufacturer's maintenance guidelines and then I create a schedule for preventive checks based on the operating hours of each machine. I always document what was done to keep track of any patterns in machinery wear.
What types of machinery are you most experienced in servicing?
How to Answer
- 1
Identify the specific types of machinery you've worked with
- 2
Highlight any relevant certifications or training
- 3
Mention the variety of maintenance tasks you've performed
- 4
Share examples of problem-solving experiences with machinery
- 5
Connect your experience to the requirements of the job you're applying for
Example Answers
I have extensive experience servicing hydraulic excavators and bulldozers, having worked on them for over 5 years. I am also certified in diesel engine repair, which enhances my ability to troubleshoot specific issues.
Describe the process you follow for repairing a faulty engine.
How to Answer
- 1
Start with a thorough diagnostic to identify the problem.
- 2
Gather all necessary tools and parts before starting the repair.
- 3
Carefully disassemble the engine components to access the fault.
- 4
Replace or repair damaged parts, ensuring everything is clean.
- 5
Reassemble the engine and run tests to confirm the repair was successful.
Example Answers
I begin by running a diagnostic to pinpoint the engine issue, then gather all necessary tools. After disassembling the parts carefully, I replace any damaged components. Finally, I reassemble everything and perform tests to ensure it runs correctly.
How do you document your service and repairs completed in the field?
How to Answer
- 1
Use a standardized form or digital tool for consistency.
- 2
Include key details like date, time, location, and customer information.
- 3
Describe the issue, steps taken, and parts used in detail.
- 4
Take before and after photos to support your documentation.
- 5
Review and communicate any follow-up services needed with the customer.
Example Answers
I use a digital service management app to log each repair. I write down the date, the nature of the service, any parts replaced, and take photos of the equipment before and after repairs.
What safety equipment do you usually carry with you in the field?
How to Answer
- 1
List specific safety equipment you carry regularly.
- 2
Mention the purpose of each item briefly.
- 3
Highlight any equipment unique to your projects or work environment.
- 4
Emphasize your commitment to safety and regulations.
- 5
Be prepared to discuss how you use this equipment in practice.
Example Answers
I always carry a hard hat to protect my head, gloves for hand safety, safety glasses to shield my eyes, and steel toe boots to prevent foot injuries.
Are you familiar with any software tools for scheduling or logging service calls? Which ones?
How to Answer
- 1
Mention specific software tools you have used.
- 2
Describe your experience with those tools briefly.
- 3
Highlight how the tools helped improve efficiency in service calls.
- 4
Be honest if you haven't used specific tools and express willingness to learn.
- 5
Relate your past experience directly to the job requirements.
Example Answers
Yes, I have used ServiceTitan extensively for scheduling and logging service calls. It helped our team track jobs efficiently and ensured we met our appointments on time.
Don't Just Read Field Service Mechanic Questions - Practice Answering Them!
Reading helps, but actual practice is what gets you hired. Our AI feedback system helps you improve your Field Service Mechanic interview answers in real-time.
Personalized feedback
Unlimited practice
Used by hundreds of successful candidates
What is your approach for troubleshooting a mechanical system that doesn’t start?
How to Answer
- 1
Start with basic checks like power supply and connections
- 2
Listen for any unusual noises that may indicate issues
- 3
Check for any error codes or indicators on the system
- 4
Inspect mechanical parts for damage or wear
- 5
Test individual components if necessary, such as starters or relays
Example Answers
I begin by ensuring the machine is receiving power and that all connections are secure. Then, I listen for any abnormal sounds that might hint at mechanical failure. If everything seems fine, I check the error codes displayed, if applicable. Finally, I inspect moving parts for signs of wear and test critical components like the starter.
Situational Interview Questions
You receive multiple service calls at once. How do you prioritize which one to address first?
How to Answer
- 1
Assess the urgency of each call based on the customer's needs.
- 2
Consider the impact of each issue on operations or safety.
- 3
Evaluate your proximity and resources for each job.
- 4
Communicate with customers to set expectations.
- 5
Document your priorities to keep track of calls.
Example Answers
I prioritize service calls by first assessing their urgency. If one call involves a safety issue, I address that first. Next, I look at my location and available tools to determine which calls I can handle most efficiently.
If a technician begins to argue with a client over service provided, how would you step in?
How to Answer
- 1
Stay calm and assess the situation before acting
- 2
Acknowledge the client's feelings to show empathy
- 3
Ask the technician to take a step back and breathe
- 4
Facilitate a constructive dialogue between the technician and the client
- 5
Offer a solution or compromise that addresses both parties' concerns
Example Answers
I would first approach the situation calmly, acknowledging the client's frustration. Then I would ask the technician to take a moment to step back and refocus. Facilitating a constructive dialogue is key, and I would suggest a solution that addresses the client's concerns, like offering another appointment for re-evaluation.
Don't Just Read Field Service Mechanic Questions - Practice Answering Them!
Reading helps, but actual practice is what gets you hired. Our AI feedback system helps you improve your Field Service Mechanic interview answers in real-time.
Personalized feedback
Unlimited practice
Used by hundreds of successful candidates
Imagine you arrive on site and find that the machinery is different from what was described. What would you do?
How to Answer
- 1
Assess the new machinery quickly to understand its specifications
- 2
Check the job documentation to confirm the expected equipment
- 3
Communicate immediately with dispatch or the client about the discrepancy
- 4
Determine if you have the necessary tools and knowledge to proceed
- 5
Document the situation for future reference and clarity
Example Answers
I would first take a moment to assess the machinery and see how it differs from what was described. Next, I would check the job order and notes to confirm what was expected. If there's a significant difference, I'd contact dispatch to discuss how to proceed, ensuring I have the tools needed and documenting everything for clarity.
You have to complete a job in a limited time window. How would you ensure efficiency?
How to Answer
- 1
Plan the job step-by-step before starting.
- 2
Prioritize tasks based on importance and urgency.
- 3
Gather all tools and materials needed in advance.
- 4
Communicate with team members to delegate parts of the job.
- 5
Stay focused and avoid distractions while working.
Example Answers
I would start by outlining the job into clear steps, prioritizing tasks based on what needs to be done first. I would also gather all necessary tools and parts beforehand to avoid wasting time during the job.
If a client is uncertain about the repairs needed, how would you explain your recommendations?
How to Answer
- 1
Ask questions to understand their concerns and uncertainties.
- 2
Use simple, non-technical language to explain the issue.
- 3
Provide a clear reason for each recommended repair.
- 4
Discuss the potential consequences of not making the repairs.
- 5
Offer to show the client the problem, if possible.
Example Answers
I would first listen to the client's concerns and ask what they are unsure about. Then, I would explain the repairs needed in simple terms, emphasizing why each repair is important and what might happen if it's not done. I would also suggest showing them the issue on the equipment.
If you discover that a critical part needed for a repair is unavailable, what steps would you take?
How to Answer
- 1
Assess the urgency of the repair and the impact of the delay.
- 2
Communicate immediately with your supervisor or team about the issue.
- 3
Check inventory for alternative parts or solutions that can be used.
- 4
Contact suppliers to confirm part availability and expected delivery times.
- 5
Document the issue and your steps taken for future reference.
Example Answers
I would first assess how critical the repair is and communicate with my supervisor about the unavailability. Then, I would search our inventory for alternatives and contact suppliers to estimated delivery if needed.
You’re in a remote location with limited resources. How do you manage the repair?
How to Answer
- 1
Assess the situation and identify the problem clearly.
- 2
Use available tools and materials creatively for temporary fixes.
- 3
Prioritize safety for yourself and the equipment.
- 4
Document the issue for follow-up or detailed repair later.
- 5
Communicate with team members or support for assistance if possible.
Example Answers
I would first assess the problem to understand what's wrong. Then, I'd use any available tools and parts, perhaps improvising with what I have to make a temporary fix. Safety would be my priority, ensuring that I don’t make the situation worse, and I would document everything for later evaluation when more resources are available.
How would you handle a situation where your repair project falls behind schedule?
How to Answer
- 1
Assess the reasons for the delay quickly.
- 2
Communicate with your team and stakeholders immediately.
- 3
Prioritize tasks to focus on what can be done to recover time.
- 4
Consider alternative solutions or resources, such as additional manpower.
- 5
Document your actions and learnings to prevent future delays.
Example Answers
If I find the project behind schedule, I first analyze the cause of the delay. I then communicate the issue with my team and supervisors to keep everyone informed. Next, I prioritize the most critical tasks and may adjust my approach by bringing in an extra team member to help speed things up. I ensure that I document what went wrong for future reference.
If you find that another department's work is interfering with your repairs, how would you address it?
How to Answer
- 1
Communicate clearly and respectfully with the other department
- 2
Identify the specific issues causing the interference
- 3
Propose a collaborative solution that benefits both teams
- 4
Document the issues and your proposed solutions
- 5
Follow up to ensure the changes are implemented
Example Answers
I would first talk to the other department to understand what is causing the interference. Then I would identify a schedule that works for both departments, ensuring we can complete our tasks without disruption.
After completing a job, how do you seek and incorporate client feedback?
How to Answer
- 1
Ask open-ended questions to clients about their satisfaction.
- 2
Use specific examples from the job to prompt their feedback.
- 3
Listen actively and take notes on their comments.
- 4
Thank clients for their feedback and clarify any points.
- 5
Implement changes based on feedback in future jobs.
Example Answers
After finishing a job, I ask the client how they felt about the service provided. I use specific situations from the job to guide the conversation. I take notes on their feedback, clarify any points, and express my appreciation for their insights. I then use this feedback to improve my future work.
Don't Just Read Field Service Mechanic Questions - Practice Answering Them!
Reading helps, but actual practice is what gets you hired. Our AI feedback system helps you improve your Field Service Mechanic interview answers in real-time.
Personalized feedback
Unlimited practice
Used by hundreds of successful candidates
Field Service Mechanic Position Details
Recommended Job Boards
CareerBuilder
www.careerbuilder.com/jobs/field-service-mechanicThese job boards are ranked by relevance for this position.
Related Positions
Ace Your Next Interview!
Practice with AI feedback & get hired faster
Personalized feedback
Used by hundreds of successful candidates
Ace Your Next Interview!
Practice with AI feedback & get hired faster
Personalized feedback
Used by hundreds of successful candidates