Top 30 Grain Elevator Operator Interview Questions and Answers [Updated 2025]
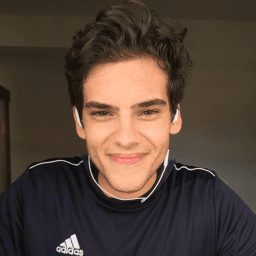
Andre Mendes
•
March 30, 2025
Preparing for a Grain Elevator Operator interview? This blog post is your ultimate guide, featuring the most common questions asked in interviews for this crucial role. We provide example answers and insightful tips to help you respond effectively and confidently. Whether you're a seasoned professional or new to the field, this resource is designed to enhance your interview preparation and boost your chances of success.
Download Grain Elevator Operator Interview Questions in PDF
To make your preparation even more convenient, we've compiled all these top Grain Elevator Operatorinterview questions and answers into a handy PDF.
Click the button below to download the PDF and have easy access to these essential questions anytime, anywhere:
List of Grain Elevator Operator Interview Questions
Technical Interview Questions
What safety measures are crucial when operating a grain elevator?
How to Answer
- 1
Mention personal protective equipment such as gloves and helmets
- 2
Discuss the importance of regular maintenance and inspections
- 3
Highlight the need for proper training and adherence to safety protocols
- 4
Emphasize monitoring for potential dust explosions and fire hazards
- 5
Note the significance of having clear emergency procedures in place
Example Answers
Personal protective equipment like gloves and helmets is essential for operator safety. Regular maintenance checks help prevent equipment failures. Training ensures everyone knows safety protocols, and we must always monitor for dust and fire hazards.
What are some key maintenance tasks for grain elevator equipment that you are familiar with?
How to Answer
- 1
Identify specific equipment types like conveyors, silos, and dryers
- 2
Mention inspection routines for wear and tear
- 3
Discuss lubrication schedules to prevent friction
- 4
Include cleaning protocols to avoid clogs and contamination
- 5
Talk about safety checks for electrical systems and emergency stops
Example Answers
I am familiar with regular inspections of conveyors and silos to check for wear and tear, as well as adhering to lubrication schedules to ensure smooth operation.
Don't Just Read Grain Elevator Operator Questions - Practice Answering Them!
Reading helps, but actual practice is what gets you hired. Our AI feedback system helps you improve your Grain Elevator Operator interview answers in real-time.
Personalized feedback
Unlimited practice
Used by hundreds of successful candidates
Explain how the condition and quality of grains are maintained during storage and handling.
How to Answer
- 1
Ensure proper moisture levels to prevent spoilage.
- 2
Implement regular inspections for pests and spoilage.
- 3
Use temperature controls to maintain optimal storage conditions.
- 4
Rotate inventory to use older stock first.
- 5
Train staff on best handling practices to reduce damage.
Example Answers
To maintain grain quality, we monitor moisture levels closely to avoid mold. Regular pest inspections are crucial and we control the temperature in storage to keep grains healthy. Rotating inventory helps us use older stock before newer batches.
Describe your experience with diagnosing and troubleshooting mechanical issues in a work environment.
How to Answer
- 1
Begin with specific types of machinery or equipment you have worked with.
- 2
Mention any relevant training or certifications in mechanical maintenance.
- 3
Provide an example of a specific mechanical issue you diagnosed and how you approached it.
- 4
Highlight the tools and techniques you used for troubleshooting.
- 5
Conclude with the outcome of your intervention and any lessons learned.
Example Answers
In my last role at the grain facility, I regularly maintained the grain augers. When one of the augers jammed, I quickly identified the electrical issue by using voltage testing. After replacing a faulty relay, the problem was resolved, and operations resumed without delays.
What steps do you take to ensure grain quality meets industry standards?
How to Answer
- 1
Regularly conduct visual and physical inspections of grain.
- 2
Ensure proper storage conditions to prevent spoilage and contamination.
- 3
Maintain and calibrate equipment for accurate quality control testing.
- 4
Follow established procedures for sample collection and testing.
- 5
Stay updated with industry standards and best practices.
Example Answers
I conduct regular inspections of the grain to check for signs of spoilage or contamination and ensure that storage facilities maintain optimal conditions for grain quality.
What are some regulations or standards you must adhere to when operating a grain elevator?
How to Answer
- 1
Know the local and federal safety regulations for grain handling.
- 2
Be familiar with OSHA standards related to workplace safety.
- 3
Understand the environmental regulations that apply to grain storage and handling.
- 4
Maintain compliance with grain quality and inspection standards.
- 5
Stay updated on industry best practices and policies.
Example Answers
I adhere to OSHA regulations for safety, ensuring that all equipment is safe to operate. I also follow the local health department's standards for grain storage and ensure environmental regulations are met to prevent contamination.
What kind of records do you maintain when working in a grain elevator, and why are they important?
How to Answer
- 1
Identify key records such as inventory logs, quality reports, and safety checks.
- 2
Explain the purpose of each record in ensuring smooth operations.
- 3
Mention compliance with regulations and tracking grain quality.
- 4
Highlight the importance of accuracy to prevent issues.
- 5
Discuss how records aid in communication among staff and stakeholders.
Example Answers
I maintain inventory logs to track the amount of grain stored, which helps manage supply and demand effectively.
How do different weather conditions affect the operations of a grain elevator?
How to Answer
- 1
Discuss the impact of moisture levels on grain quality and storage.
- 2
Explain how rain can lead to delays in unloading and loading grain.
- 3
Mention temperature extremes and their effect on machinery and grain handling.
- 4
Talk about how snow can affect access to the elevator facilities.
- 5
Highlight the need for monitoring weather patterns to ensure operational efficiency.
Example Answers
Moisture levels are crucial as high humidity can reduce grain quality and lead to spoilage during storage. Rain may also delay loading operations since we need dry conditions to handle grain efficiently.
Can you name different types of grains you have handled and any specific considerations for each?
How to Answer
- 1
List specific types of grains you have experience with.
- 2
Mention specific handling practices for each grain.
- 3
Discuss storage, moisture content, or pest control for each grain.
- 4
Share any relevant safety considerations or equipment used.
- 5
Explain how your experience has prepared you for this role.
Example Answers
I have handled wheat, corn, and soybeans. For wheat, I ensure low moisture content to prevent spoilage. With corn, I focus on checking for pests and using proper aeration. Soybeans require careful temperature control during storage to maintain quality.
What is your experience with automated systems in grain handling?
How to Answer
- 1
Mention specific automated systems you have experience with
- 2
Explain how you used these systems effectively in grain operations
- 3
Highlight any troubleshooting or issues you managed with automation
- 4
Discuss your familiarity with monitoring and adjusting these systems
- 5
Emphasize your training or certifications related to automation in grain handling
Example Answers
I have worked with automated grain handling systems such as the Agri-Systems grain storage management software. I used it to monitor inventory levels and ensure timely grain transfers, which improved efficiency significantly.
Don't Just Read Grain Elevator Operator Questions - Practice Answering Them!
Reading helps, but actual practice is what gets you hired. Our AI feedback system helps you improve your Grain Elevator Operator interview answers in real-time.
Personalized feedback
Unlimited practice
Used by hundreds of successful candidates
Behavioral Interview Questions
Can you describe a time when you had to pay great attention to detail in your work? How did it affect the outcome?
How to Answer
- 1
Choose a specific situation from past experience
- 2
Highlight the importance of detail in that context
- 3
Explain the steps you took to ensure accuracy
- 4
Discuss the positive outcome and any metrics if possible
- 5
Relate it back to skills relevant to a Grain Elevator Operator
Example Answers
In my previous job at a grain processing plant, I noticed discrepancies in weight measurements during loading. I carefully recalibrated the scales and conducted multiple checks. This attention to detail ensured that our shipments were accurate, leading to a 100% satisfaction rating from our clients that month.
Tell us about a situation where you worked closely with a team in a stressful environment. How did you contribute to maintaining team spirit?
How to Answer
- 1
Recall a specific stressful situation at work.
- 2
Describe your role and responsibilities in that situation.
- 3
Highlight actions you took to support and motivate the team.
- 4
Emphasize the outcome and how team spirit was enhanced.
- 5
Be positive and focus on teamwork and communication.
Example Answers
During a harvest season at the grain elevator, we faced delays due to equipment failure. I took the initiative to organize a quick team meeting, where we brainstormed solutions. I also motivated my teammates by reminding them of how far we had come and shared jokes to lighten the mood. This boosted everyone's morale, and we managed to fix the issue quickly and finish the job on time.
Don't Just Read Grain Elevator Operator Questions - Practice Answering Them!
Reading helps, but actual practice is what gets you hired. Our AI feedback system helps you improve your Grain Elevator Operator interview answers in real-time.
Personalized feedback
Unlimited practice
Used by hundreds of successful candidates
Describe an instance where you had to follow strict safety protocols. How did you ensure compliance and what was the result?
How to Answer
- 1
Choose a specific example from your experience.
- 2
Focus on the safety protocols that were relevant to your role.
- 3
Explain your actions to ensure compliance with those protocols.
- 4
Describe the outcome or impact of following these safety measures.
- 5
Highlight any feedback or lessons learned from the experience.
Example Answers
In my previous role at a grain facility, we had strict protocols for lockout/tagout procedures during maintenance. I ensured compliance by verifying that all equipment was shut down and locked before anyone began work. The result was a safe working environment without any incidents during maintenance.
Can you give an example of a problem you faced while working with machinery and how you resolved it?
How to Answer
- 1
Choose a specific machinery issue you encountered.
- 2
Explain the steps you took to identify the problem.
- 3
Detail the solution you implemented and any tools used.
- 4
Mention the outcome and what you learned from the experience.
- 5
Keep your example relevant to grain elevator operations.
Example Answers
While operating the grain conveyor, I noticed it started making unusual noises. I stopped the machinery and checked the bearings. I discovered they were worn out, so I replaced them with new ones. This fixed the issue, and the conveyor ran smoothly afterward. I learned the importance of regular maintenance checks.
Situational Interview Questions
How would you respond if you noticed a malfunction in the grain elevator that could lead to a safety hazard?
How to Answer
- 1
Immediately report the malfunction to your supervisor or safety officer
- 2
Secure the area to prevent others from entering until the hazard is resolved
- 3
Document the malfunction and any steps taken for future reference
- 4
Follow safety protocols and guidelines as trained
- 5
Remain calm and focused, ensuring clear communication with your team
Example Answers
If I noticed a malfunction in the grain elevator, I would quickly report it to my supervisor and ensure the area is secured to prevent any accidents. I would document what I observed and the actions I took, following the safety protocols we have in place.
Imagine a disagreement arises between coworkers about the process for loading grain. How would you handle it?
How to Answer
- 1
Stay calm and listen to both sides of the disagreement
- 2
Encourage open communication to understand each person's perspective
- 3
Suggest a meeting to discuss the issue as a team
- 4
Focus on finding a solution that benefits the operation
- 5
Remind everyone of the shared goal of safety and efficiency
Example Answers
I would listen to both coworkers to understand their viewpoints and then facilitate a meeting where we can discuss our concerns and find a common solution that works well for everyone.
Don't Just Read Grain Elevator Operator Questions - Practice Answering Them!
Reading helps, but actual practice is what gets you hired. Our AI feedback system helps you improve your Grain Elevator Operator interview answers in real-time.
Personalized feedback
Unlimited practice
Used by hundreds of successful candidates
If you are running behind schedule on grain loading due to unexpected delays, how would you prioritize your tasks?
How to Answer
- 1
Assess the reason for the delay and identify critical tasks.
- 2
Communicate promptly with the team and stakeholders about the situation.
- 3
Focus on tasks that minimize further delays to loading operations.
- 4
Consider safety and operational efficiency when rescheduling tasks.
- 5
Adjust priorities dynamically based on real-time developments.
Example Answers
I would first assess what caused the delay and identify which tasks are most critical to get back on schedule. Then, I would communicate with my team about the situation and prioritize tasks that will help us load the grain as quickly and safely as possible while considering any safety protocols.
If you discover a shortage of resources needed for grain handling operations, how would you address the issue?
How to Answer
- 1
Assess the specific shortage and its impact on operations.
- 2
Communicate the issue to your supervisor and relevant team members immediately.
- 3
Identify potential alternative resources or solutions.
- 4
Implement short-term fixes while sourcing long-term solutions.
- 5
Document the situation to improve future resource management.
Example Answers
First, I would evaluate the extent of the resource shortage and how it affects current operations. Then, I'd inform my supervisor and the team about the issue so we can brainstorm solutions. If possible, I would look for alternative suppliers or backup resources to keep operations running smoothly until we resolve the shortage.
You discover that an order was mishandled, leading to a delay in delivery. How would you communicate this with the client?
How to Answer
- 1
Acknowledge the mistake honestly and upfront
- 2
Provide a clear explanation of what went wrong without making excuses
- 3
Communicate what steps are being taken to resolve the issue
- 4
Offer a new timeline for delivery or compensation if applicable
- 5
Maintain a professional tone and reassure the client of your commitment
Example Answers
I would start by informing the client about the mishandling of their order honestly. I would explain the reason for the delay and that we are taking immediate action to correct it. I would also provide them with a new delivery timeline and assure them that we are committed to preventing this in the future.
A critical piece of equipment breaks down during peak operation times. What steps would you take to minimize disruptions?
How to Answer
- 1
Prioritize safety and ensure all team members are informed of the situation.
- 2
Assess the severity and impact of the breakdown on operations.
- 3
Communicate with maintenance to start repairs immediately.
- 4
Implement a contingency plan to redistribute tasks or equipment.
- 5
Document the incident for future reference and process improvement.
Example Answers
First, I would ensure everyone's safety by stopping operations and informing the team. Then, I'd assess how the breakdown impacts our current workload. I would immediately contact maintenance for urgent repairs and initiate our contingency plan to balance the workload among other equipment. After resolving the issue, I'd document the incident to identify ways we can improve our response in the future.
If you witness a coworker not following safety protocols, how would you address it?
How to Answer
- 1
Stay calm and approach the situation respectfully
- 2
Privately speak to the coworker about the safety concern
- 3
Use specific examples to explain why the behavior is risky
- 4
Encourage them to follow the safety protocols for everyone's benefit
- 5
Report the incident to a supervisor if the issue persists
Example Answers
I would first talk to my coworker privately and let them know I noticed they weren't following the safety protocols. I would explain why it's important for everyone’s safety and suggest that we all stick to the guidelines.
How would you handle a situation where there is a discrepancy in the grain inventory records?
How to Answer
- 1
Investigate the root cause by checking records and conducting a physical inventory.
- 2
Communicate with relevant team members to gather insights and confirm discrepancies.
- 3
Document all findings and actions taken during the investigation.
- 4
Suggest solutions to prevent future discrepancies, such as improved tracking processes.
- 5
Follow up on the resolution and ensure accuracy in the updated records.
Example Answers
I would start by conducting a physical count of the grain inventory to identify the discrepancy. Then, I would review the records and discuss with the team to see if anyone noticed any issues. After documenting everything, I would suggest ways to improve our inventory tracking to avoid this in the future.
If you notice inefficiencies in the grain handling process, how would you propose and implement improvements?
How to Answer
- 1
Identify specific inefficiencies through observation or data analysis.
- 2
Engage with team members for their insights and suggestions.
- 3
Propose practical solutions that are cost-effective and easy to implement.
- 4
Create a step-by-step plan for testing changes, including metrics to measure success.
- 5
Communicate clearly with management and your team about changes and expected outcomes.
Example Answers
I would first observe the grain handling process and gather data on wait times and throughput. After identifying slow spots, I would discuss with my team to gather their input. A practical solution might be to reorganize the workflow to minimize downtime. I would then test this new workflow for a week and track the results to see if efficiency improved.
How would you manage your workload if an unexpected large shipment arrives?
How to Answer
- 1
Assess the current workload and prioritize tasks based on urgency
- 2
Communicate with team members to delegate responsibilities effectively
- 3
Coordinate with receiving and loading teams to prepare for the shipment
- 4
Utilize any available technology to streamline processes
- 5
Maintain a flexible mindset to adapt to changing circumstances
Example Answers
I would first evaluate my current responsibilities and identify what can be postponed. Then, I would inform my team and delegate tasks so we can efficiently handle the large shipment together. I would also make sure to coordinate with the loading crew to prepare for the arrival and ensure we meet the deadlines.
Don't Just Read Grain Elevator Operator Questions - Practice Answering Them!
Reading helps, but actual practice is what gets you hired. Our AI feedback system helps you improve your Grain Elevator Operator interview answers in real-time.
Personalized feedback
Unlimited practice
Used by hundreds of successful candidates
If you find that some grain is at risk of spoilage, what actions would you take to mitigate the issue?
How to Answer
- 1
Assess the level of spoilage and determine the source of moisture or heat.
- 2
Improve ventilation in the storage area to reduce humidity.
- 3
Consider transferring the grain to a drier or cooler location.
- 4
Implement or increase aeration to cool down the grain quickly.
- 5
Monitor the grain regularly to catch spoilage early.
Example Answers
First, I would assess the storage area to identify the source of moisture. Then, I would increase ventilation and aeration to cool and dry the grain. If necessary, I'd transfer the grain to a drier location to prevent further spoilage.
You are asked to train a new employee on operating procedures. How would you ensure they understand and follow all guidelines?
How to Answer
- 1
Start with a clear overview of the operating procedures and their importance.
- 2
Use hands-on demonstrations to show specific tasks and safety protocols.
- 3
Allow the trainee to perform tasks under supervision while you guide them.
- 4
Encourage questions and provide clear answers to reinforce learning.
- 5
Follow up with regular check-ins to assess understanding and address any concerns.
Example Answers
I would begin by giving a brief overview of the operating procedures, emphasizing their importance for safety. Then, I'd demonstrate key tasks and let the new employee practice them under my supervision. I encourage questions to clarify their understanding and follow up weekly to ensure they are comfortable with the procedures.
Describe how you would adjust your approach if a new type of grain with different handling requirements is introduced.
How to Answer
- 1
Research the specific handling requirements of the new grain type.
- 2
Communicate with senior staff or supervisors about changes needed.
- 3
Update equipment or processes to accommodate the new grain.
- 4
Train the team on any new procedures or safety protocols.
- 5
Monitor the handling of the grain and gather feedback for continuous improvement.
Example Answers
I would first research the handling requirements for the new grain to understand what adjustments are necessary. Then, I would consult with my supervisor to discuss any potential changes to our current processes and equipment. Additionally, I would ensure that the team is trained on the new procedures and closely monitor how the grain is handled to spot any issues early.
How would you handle a situation where you need to reduce operational costs without compromising service quality?
How to Answer
- 1
Identify key areas where costs can be reduced without affecting service.
- 2
Implement efficient inventory management to minimize waste.
- 3
Engage with the team for their insights on cost-saving measures.
- 4
Explore technology upgrades that improve efficiency.
- 5
Monitor key performance indicators to ensure service quality remains high.
Example Answers
I would start by analyzing our current operational costs and identifying areas where we can cut expenses, such as reducing waste in materials. Additionally, I would optimize our inventory management systems to ensure we don't overstock and waste resources, while still meeting service demands.
A new software system is being introduced to manage operations. How would you approach learning and integrating this new technology?
How to Answer
- 1
Take a hands-on approach by practicing on the system as soon as possible
- 2
Utilize training resources such as tutorials or manuals provided by the company
- 3
Collaborate with colleagues who are more familiar with the software to gain insights
- 4
Set specific goals to learn features of the software over time
- 5
Ask for feedback and help from supervisors during the learning process
Example Answers
I would start by exploring the software myself to familiarize myself with its interface. Then, I would use any training materials the company provides and set aside time each week to practice. I would also reach out to colleagues for tips and best practices to enhance my learning.
Grain Elevator Operator Position Details
Salary Information
Recommended Job Boards
These job boards are ranked by relevance for this position.
Related Positions
- Grain Merchandiser
- Grain Broker
- Grain Buyer
- Farm Contractor
- Livestock Dealer
- Cotton Broker
- Cattle Broker
- Cow Buyer
- Food Broker
- Cattle Trader
Similar positions you might be interested in.
Ace Your Next Interview!
Practice with AI feedback & get hired faster
Personalized feedback
Used by hundreds of successful candidates
Ace Your Next Interview!
Practice with AI feedback & get hired faster
Personalized feedback
Used by hundreds of successful candidates