Top 30 Guitar Maker Interview Questions and Answers [Updated 2025]
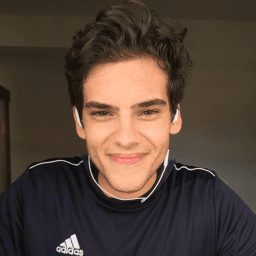
Andre Mendes
•
March 30, 2025
Embarking on a journey to become a guitar maker? Our latest blog post offers insight into the most common interview questions for this unique role. Discover example answers and valuable tips to help you craft responses that resonate with potential employers. Whether you're a seasoned artisan or a passionate newcomer, this guide will prepare you to hit all the right notes in your next interview.
Download Guitar Maker Interview Questions in PDF
To make your preparation even more convenient, we've compiled all these top Guitar Makerinterview questions and answers into a handy PDF.
Click the button below to download the PDF and have easy access to these essential questions anytime, anywhere:
List of Guitar Maker Interview Questions
Situational Interview Questions
What would you do if you were running behind schedule on a custom guitar order with a firm deadline?
How to Answer
- 1
Identify the specific reasons for the delay.
- 2
Communicate promptly and transparently with the customer.
- 3
Prioritize tasks that will help meet the deadline.
- 4
Consider working extra hours or adjusting your workflow.
- 5
Deliver what you can on time, and propose a solution for any remaining work.
Example Answers
If I found myself behind schedule, I would first determine the root causes of the delay and then reach out to the customer to inform them of the situation. I’d outline my plan to expedite the process by focusing on critical tasks and, if necessary, working overtime to meet the deadline.
If a customer complains that the guitar you made has a buzzing sound, how would you approach diagnosing and fixing the issue?
How to Answer
- 1
Ask the customer specific questions about when and where the buzzing occurs.
- 2
Check the guitar setup, including string height and neck relief.
- 3
Inspect the frets for any unevenness or wear.
- 4
Look for issues with hardware, like loose tuning machines or bridge components.
- 5
Test the guitar yourself to replicate the buzzing before making adjustments.
Example Answers
I would begin by talking to the customer to find out more about the buzzing – when it happens, what type of music they're playing, and so on. After that, I would check the guitar's setup for string height and neck relief before inspecting the frets for any signs of unevenness.
Don't Just Read Guitar Maker Questions - Practice Answering Them!
Reading helps, but actual practice is what gets you hired. Our AI feedback system helps you improve your Guitar Maker interview answers in real-time.
Personalized feedback
Unlimited practice
Used by hundreds of successful candidates
A client requests a custom modification to a guitar that is technically challenging. How would you handle this request?
How to Answer
- 1
Clarify the client's vision and specific requirements
- 2
Assess the technical challenges and feasibility of the request
- 3
Communicate any limitations or concerns openly with the client
- 4
Propose alternative solutions or compromises if necessary
- 5
Document all agreements and provide a timeline for completion
Example Answers
I would start by discussing with the client to understand exactly what modifications they want and why. After assessing the technical aspects, I would explain any challenges I foresee and suggest alternative options that could still meet their needs.
You've been asked to design a new model of guitar that incorporates sustainable materials without compromising quality. How would you tackle this project?
How to Answer
- 1
Research sustainable materials that have been successfully used in guitar making.
- 2
Consider the acoustic properties required for guitar quality and how to achieve them with these materials.
- 3
Engage with suppliers who provide sustainable options and get samples for testing.
- 4
Prototype the design focusing on playability and sound quality while using sustainable materials.
- 5
Gather feedback from musicians on the prototype to refine the design.
Example Answers
I would start by researching eco-friendly woods like bamboo or reclaimed timber, which have good sound quality. Then, I'd prototype a guitar using these materials to ensure the acoustic properties are up to standard, followed by testing it with musicians for their feedback.
A client comes to you wanting to upgrade an old guitar to improve its playability and sound. How would you assess and proceed with this task?
How to Answer
- 1
Start by inspecting the guitar thoroughly for structural issues.
- 2
Evaluate the tonewoods and their condition to assess sound quality.
- 3
Check the hardware, such as tuning machines and bridge, for functionality.
- 4
Discuss with the client their specific playability concerns and preferred sound.
- 5
Suggest upgrades like new pickups, fretwork, or a new setup based on your assessment.
Example Answers
I would first check the guitar for any structural problems like cracks or warping, then assess the tonewoods for quality. Next, I would look at the tuning hardware to ensure it's functioning correctly. After that, I would talk to the client about their playability issues, and suggest upgrades like new pickups or a fret level to enhance the sound and playability.
How would you handle building a high-quality guitar on a limited budget without sacrificing essential features?
How to Answer
- 1
Focus on selecting cost-effective materials that still meet quality standards.
- 2
Prioritize essential features that impact sound and playability over aesthetic elements.
- 3
Leverage efficient manufacturing techniques to reduce waste and save costs.
- 4
Consider sourcing locally to minimize shipping costs and support community businesses.
- 5
Use simple designs that are easier and cheaper to produce while maintaining quality.
Example Answers
To build a high-quality guitar on a budget, I would carefully select lower-cost woods that still provide excellent tonal qualities. By focusing on essential features like the neck profile and fret material, I can ensure the guitar plays well without adding unnecessary costs.
A client requests a guitar with very specific, unusual specifications. How would you approach the design and build process?
How to Answer
- 1
Listen carefully to the client's specifications and clarify any uncertainties.
- 2
Conduct research to understand the implications of the unusual specifications.
- 3
Create a detailed design plan that incorporates the client's vision.
- 4
Communicate with the client throughout the process for feedback and adjustments.
- 5
Document any challenges and solutions during the build for future reference.
Example Answers
I would start by having an in-depth conversation with the client to fully understand their unusual specifications. After that, I would research how these specifications might affect the sound and playability of the guitar. Then, I would draft a design plan and share it with the client for their input before proceeding with the build, keeping them updated along the way.
A guitar you've made is returned for a repair due to a crack. What steps would you take to repair it and prevent future issues?
How to Answer
- 1
Inspect the crack thoroughly to determine its cause and extent.
- 2
Use appropriate wood glue for the repair and clamp it securely.
- 3
Sand the area gently to ensure a smooth finish after the glue has cured.
- 4
Apply finish that matches the original to protect the repair.
- 5
Consider the wood's moisture levels and environmental conditions to prevent future cracks.
Example Answers
First, I would inspect the crack to understand its size and whether it was caused by environmental factors. Then, I would carefully apply wood glue and clamp the crack to ensure a strong bond. Once the glue dries, I'd sand the area to match the guitar's finish and apply a matching finish to protect the repair. Lastly, I would recommend maintaining proper humidity levels to prevent future issues.
If there's a sudden shortage of a specific wood you use, how would you adapt to ensure continued production?
How to Answer
- 1
Consider alternative materials that can achieve similar tonal qualities.
- 2
Research and source new suppliers who offer the wood you need.
- 3
Adjust your designs to accommodate available woods without compromising quality.
- 4
Engage with other luthiers to share solutions and resources.
- 5
Stay informed on industry trends to anticipate future shortages.
Example Answers
I would start by researching alternative woods that have similar acoustic properties, such as using mahogany instead of mahogany if it’s unavailable. Simultaneously, I would reach out to my network of suppliers to find other sources.
Behavioral Interview Questions
Can you describe a time when you were particularly proud of a guitar you built? What made it special?
How to Answer
- 1
Choose a specific guitar project you are proud of.
- 2
Explain the challenges you faced during the build.
- 3
Highlight the unique features that made the guitar stand out.
- 4
Connect the experience to your growth as a guitar maker.
- 5
Convey your passion and attention to detail in the build process.
Example Answers
I built a custom acoustic guitar last year that I am very proud of. The challenge was achieving the perfect tonal balance. I used a unique combination of spruce and mahogany, which resulted in a warm sound. It stands out because it has intricate inlay work that reflects my design philosophy. This project taught me a lot about wood selection and craftsmanship.
Tell me about a difficult problem you encountered during the guitar-making process and how you solved it.
How to Answer
- 1
Think of a specific challenge you faced while making a guitar.
- 2
Explain the steps you took to address the problem clearly.
- 3
Highlight any skills or techniques you used to solve the issue.
- 4
Discuss the outcome and what you learned from the experience.
- 5
Keep your answer focused and relevant to guitar-making.
Example Answers
While building my first acoustic guitar, I struggled with the alignment of the neck joint. To solve it, I researched techniques online and practiced the setup with a test piece to ensure accuracy. In the end, the guitar turned out well, and I learned the importance of precise measurements.
Don't Just Read Guitar Maker Questions - Practice Answering Them!
Reading helps, but actual practice is what gets you hired. Our AI feedback system helps you improve your Guitar Maker interview answers in real-time.
Personalized feedback
Unlimited practice
Used by hundreds of successful candidates
Have you ever collaborated with other artisans on a large project? What role did you play and how did you ensure effective teamwork?
How to Answer
- 1
Identify a specific project where teamwork was essential
- 2
Clearly describe your role and contributions
- 3
Highlight communication strategies you used
- 4
Mention any conflict resolution or problem-solving methods
- 5
Show the positive outcome of the collaboration
Example Answers
In a recent project, I collaborated with a woodworker and a painter to create a custom guitar. I took the role of lead guitar builder, coordinating our efforts. We held regular meetings to discuss progress and I used shared digital documents to track tasks. This helped us stay in sync and ensured the project was completed on time, resulting in a beautiful instrument that delighted the client.
Describe a situation where you had to learn a new technique or tool quickly. How did you approach it?
How to Answer
- 1
Identify the specific technique or tool you learned
- 2
Explain the context and why it was necessary to learn quickly
- 3
Describe your learning method or resources used
- 4
Mention any challenges faced and how you overcame them
- 5
Conclude with the outcome and what you learned from the experience
Example Answers
When I started working at a guitar shop, I had to quickly learn how to use a new CNC machine for guitar body shaping. I watched instructional videos and read the manual to understand its functions. I practiced on scrap wood to build confidence. Although I struggled at first, I asked for help from a more experienced colleague, which helped me master the machine in a week. As a result, I was able to produce high-quality guitar bodies efficiently.
How have you used customer feedback to improve your guitar-making process?
How to Answer
- 1
Identify specific feedback sources like surveys or direct communication.
- 2
Detail how you analyzed and prioritized feedback for action.
- 3
Provide an example of a change you made based on feedback.
- 4
Discuss the outcome of the change and any positive customer responses.
- 5
Express openness to ongoing feedback for continuous improvement.
Example Answers
I collected feedback from customers through post-purchase surveys and found that many wanted a lighter guitar. I prioritized this by experimenting with different materials and adjusting the design. The new models received positive reviews for their playability, and sales increased by 20%.
Give an example of how your attention to detail has impacted the final quality of a guitar.
How to Answer
- 1
Think of a specific project where your attention to detail made a difference.
- 2
Describe the exact detail you focused on and how you ensured it was perfect.
- 3
Explain the outcome and how it improved the guitar's quality.
- 4
Use terms associated with guitar making, like intonation, finishing, or wood selection.
- 5
Keep the example concise but clear, highlighting the significance of your detail-oriented approach.
Example Answers
In building a custom electric guitar, I meticulously measured the intonation after each string was attached, ensuring that each note was in perfect pitch up the neck. This resulted in a guitar that had superb playability in all positions.
Can you provide an example of how you improved your craft over the years?
How to Answer
- 1
Identify a specific skill or technique you focused on improving.
- 2
Mention resources you used, such as books, workshops, or online courses.
- 3
Include a tangible result that shows your improvement.
- 4
Discuss the process of receiving feedback from peers or mentors.
- 5
Reflect on how this improvement has impacted your work as a guitar maker.
Example Answers
I focused on refining my fretting technique by attending a workshop led by a renowned luthier. After practicing the skills learned there, my fretwork became more precise and cleaner, which improved intonation on my guitars.
Tell me about a time when you introduced a new idea or method in your work as a guitar maker.
How to Answer
- 1
Identify a specific instance where you innovated.
- 2
Explain the method and its benefits clearly.
- 3
Share the impact it had on your work or the final product.
- 4
Mention any feedback received from peers or customers.
- 5
Conclude with what you learned from the experience.
Example Answers
In my previous position, I introduced a new fret leveling technique using a laser level. This ensured a more precise alignment, resulting in better playability. My colleagues noticed the difference in setup times, and feedback from customers was overwhelmingly positive. I learned the importance of precision in the setup process.
Describe how you plan and manage your time when working on multiple guitar builds simultaneously.
How to Answer
- 1
Prioritize tasks based on deadlines and complexity.
- 2
Create a detailed timeline for each build with key milestones.
- 3
Allocate specific time blocks for different aspects of each build.
- 4
Use checklists to track progress on individual builds.
- 5
Regularly review your schedule and adjust as necessary.
Example Answers
I prioritize my builds by setting deadlines and identifying which guitars require more intricate work. I create a timeline for each project and block time on my calendar to focus on different tasks such as sanding, finishing, or assembly.
How do you maintain consistency in quality across different guitars that you make?
How to Answer
- 1
Establish a standardized process for each type of guitar you make
- 2
Use high-quality materials sourced from reliable suppliers
- 3
Implement regular quality checks at different stages of production
- 4
Document your techniques and measurements to ensure repeatability
- 5
Continuously seek feedback and make adjustments for improvement
Example Answers
I maintain consistency by having a detailed process for each guitar, using the same materials for every build, and conducting quality checks at each stage to catch any issues early.
Don't Just Read Guitar Maker Questions - Practice Answering Them!
Reading helps, but actual practice is what gets you hired. Our AI feedback system helps you improve your Guitar Maker interview answers in real-time.
Personalized feedback
Unlimited practice
Used by hundreds of successful candidates
Technical Interview Questions
What are the different types of wood you prefer for the body of a guitar, and why?
How to Answer
- 1
Identify specific woods you prefer like mahogany, alder, or maple.
- 2
Explain the tonal qualities of each wood and how it affects the sound.
- 3
Mention any personal experiences with these woods in your guitar making.
- 4
Discuss how aesthetics and durability factor into your choices.
- 5
Be prepared to relate your preferences to the type of music or playing style.
Example Answers
I prefer mahogany for its warm sound and great sustain, particularly suited for blues and rock music. I've used it in several builds and appreciate its visual appeal and durability.
How do you ensure the best possible acoustic quality in the guitars you make?
How to Answer
- 1
Select high-quality tonewoods suited for the desired sound.
- 2
Pay attention to the thickness and shape of the guitar's top and back.
- 3
Use proper bracing patterns to enhance resonance and sustain.
- 4
Test and adjust the guitar during the building process for tonal quality.
- 5
Incorporate feedback from musicians to refine acoustic performance.
Example Answers
I ensure the best acoustic quality by carefully selecting tonewoods like spruce and mahogany, which are known for their resonant qualities. I also focus on optimal bracing patterns to maximize the sound output.
Don't Just Read Guitar Maker Questions - Practice Answering Them!
Reading helps, but actual practice is what gets you hired. Our AI feedback system helps you improve your Guitar Maker interview answers in real-time.
Personalized feedback
Unlimited practice
Used by hundreds of successful candidates
What techniques do you use to apply a finish to a guitar, and how do you decide which finish to use?
How to Answer
- 1
Identify common finishes like nitrocellulose, poly, or oil, and understand their properties.
- 2
Explain the application techniques such as spraying, brushing, or wiping, and when to use each.
- 3
Discuss the importance of surface preparation and the steps to sand and clean before finishing.
- 4
Mention how you consider the type of guitar and desired sound when choosing a finish.
- 5
Share experiences of finishing guitars and any learning moments from the process.
Example Answers
I typically use nitrocellulose lacquer for electric guitars as it enhances the sound. I spray it on after thorough sanding to ensure a smooth finish. For acoustic guitars, I prefer an oil finish because it allows for better resonance and warmth in sound. Each finish is chosen based on the guitar's design and the tonal qualities desired.
What experience do you have with installing and configuring electronic components in electric guitars?
How to Answer
- 1
Explain specific electronic components you have worked with.
- 2
Mention any relevant projects, including the types of guitars you modified or built.
- 3
Discuss your understanding of wiring diagrams and electronic schematics.
- 4
Highlight any tools or techniques you commonly use.
- 5
Share how you troubleshoot issues with electronic components.
Example Answers
I have experience installing humbuckers and single-coil pickups in various guitar models. For example, I rewired a Fender Stratocaster to include a push-pull pot for coil splitting, which enhanced its tonal versatility.
What are the key considerations when building the neck of a guitar?
How to Answer
- 1
Select the right wood for strength and resonance
- 2
Ensure proper fret placement for accurate intonation
- 3
Design a comfortable neck profile that suits the player
- 4
Choose appropriate scale length to optimize playability
- 5
Consider incorporating a truss rod for neck adjustment
Example Answers
When building the neck of a guitar, I consider using hardwood like mahogany for durability and good tone. Accurate fret placement is critical for excellent intonation, and I always ensure the neck profile is comfortable for players’ hands.
How do you ensure the correct positioning of a guitar bridge to achieve optimal playability and intonation?
How to Answer
- 1
Understand the scale length for the guitar type being worked on
- 2
Use precise measurements for string length from nut to bridge
- 3
Adjust the bridge position based on intonation checks at the 12th fret
- 4
Consider the type of bridge and its design for better adjustment
- 5
Perform thorough play testing after adjustments to confirm results
Example Answers
To ensure the correct bridge positioning, I first measure the scale length and then place the bridge accordingly. After securing it, I check the intonation by fretting the 12th fret to see if it's in tune. If adjustments are needed, I reposition the bridge slightly and check again.
How does string tension affect the construction decisions of a guitar?
How to Answer
- 1
Explain the basics of string tension and its impact on sound.
- 2
Discuss how different tensions affect neck curvature and fretting.
- 3
Mention materials and construction techniques used to handle tension.
- 4
Talk about how string tension influences tone and playability.
- 5
Relate tension choices to different musical styles and player preferences.
Example Answers
String tension directly affects the sound quality of a guitar. Higher tension can produce a brighter tone but also requires careful neck adjustments to prevent bowing. For instance, a flat-fingerboard construction helps manage this tension effectively.
What are the steps involved in ensuring that the fretwork on a guitar is precise and smooth?
How to Answer
- 1
Start with accurate fret placement and secure each fret tightly.
- 2
Use a quality fret leveling file to achieve a flat surface on all frets.
- 3
Polish the frets with progressively finer sandpaper or polishing wheels.
- 4
Check the fret edges for sharpness and ease them with a file.
- 5
Perform a playability test to ensure smooth action and intonation.
Example Answers
To ensure precise fretwork, I begin by carefully aligning and securing each fret. Then, I level the frets with a fret file to guarantee a flat surface, followed by polishing them with finer sandpaper for a smooth finish. Lastly, I check for sharp edges and conduct a playability test for overall smoothness.
What characteristics are you looking for in a soundboard, and how do they affect the guitar's tone?
How to Answer
- 1
Discuss wood species and their properties such as stiffness and density
- 2
Mention the importance of grain orientation in soundboard construction
- 3
Explain how thickness affects resonance and overall tone projection
- 4
Consider how the finish impacts the soundboard's vibrational characteristics
- 5
Relate your choices to the desired tonal qualities for different styles of music
Example Answers
When selecting a soundboard, I look for a spruce or cedar wood due to their superior stiffness-to-weight ratio. This affects tone by providing clarity and responsiveness. I also pay close attention to the grain orientation to ensure it promotes even vibrations, enhancing projection.
Can you explain the role of bracing patterns in acoustic guitars and how they affect sound?
How to Answer
- 1
Start with a brief definition of bracing and its purpose in the guitar structure.
- 2
Mention different bracing patterns, such as X-bracing and ladder bracing, and their common uses.
- 3
Explain how bracing affects the strength of the guitar body and its ability to project sound.
- 4
Discuss how bracing influences the tonal qualities, such as volume and sustain.
- 5
Wrap up with an example of how a specific pattern might be chosen based on the desired outcome.
Example Answers
Bracing refers to the internal wood supports that help shape the guitar's body and influence its sound. X-bracing is common in many acoustic guitars due to its balance of strength and sound projection. It allows for a broader sound and good sustain, while ladder bracing offers a different tonal character, often providing a tighter sound with less overtones. Choosing the right bracing pattern can impact everything from volume to tonal richness.
Don't Just Read Guitar Maker Questions - Practice Answering Them!
Reading helps, but actual practice is what gets you hired. Our AI feedback system helps you improve your Guitar Maker interview answers in real-time.
Personalized feedback
Unlimited practice
Used by hundreds of successful candidates
What specific tools are essential for building a high-quality guitar from scratch?
How to Answer
- 1
Start by listing the main categories of tools needed.
- 2
Mention both hand tools and power tools.
- 3
Explain the purpose of each tool briefly.
- 4
Focus on tools that directly impact sound quality and craftsmanship.
- 5
Consider mentioning specialized tools for guitar making.
Example Answers
Essential tools for building a high-quality guitar include a bandsaw for cutting wood, chisels for shaping, a router for edge work, and a fret saw for precise cuts. Each tool contributes to the sound and playability of the final instrument.
Guitar Maker Position Details
Recommended Job Boards
ZipRecruiter
www.ziprecruiter.com/Jobs/Guitar-MakerThese job boards are ranked by relevance for this position.
Related Positions
- Luthier
- Instrument Designer
- Furniture Maker
- Toy Maker
- Furniture Artist
- Wood Crafter
- Crafter
- Craftsman
- Artisan
- Guitar Builder
Similar positions you might be interested in.
Ace Your Next Interview!
Practice with AI feedback & get hired faster
Personalized feedback
Used by hundreds of successful candidates
Ace Your Next Interview!
Practice with AI feedback & get hired faster
Personalized feedback
Used by hundreds of successful candidates