Top 31 Hose Wrapper Interview Questions and Answers [Updated 2025]
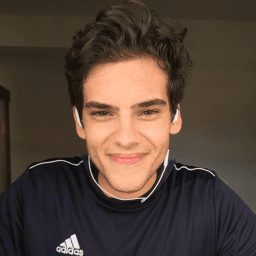
Andre Mendes
•
March 30, 2025
Preparing for a Hose Wrapper interview and unsure of what to expect? Look no further! Our latest blog post compiles the most common interview questions for this specialized role, complete with example answers and insightful tips to help you respond with confidence. Whether you're new to the field or seeking to refine your skills, this guide is designed to set you up for success. Dive in and start preparing effectively!
Download Hose Wrapper Interview Questions in PDF
To make your preparation even more convenient, we've compiled all these top Hose Wrapperinterview questions and answers into a handy PDF.
Click the button below to download the PDF and have easy access to these essential questions anytime, anywhere:
List of Hose Wrapper Interview Questions
Technical Interview Questions
How do you ensure that hoses are wrapped to the correct length and specifications?
How to Answer
- 1
Measure hoses accurately before wrapping to avoid length issues.
- 2
Follow standard specifications provided for hose wrapping.
- 3
Use a consistent wrapping technique to maintain uniformity.
- 4
Check the wrapped hose against a template if available.
- 5
Communicate any discrepancies to the team before finalizing.
Example Answers
I always start by measuring the hose to ensure I know its exact length. Then, I follow the specified wrapping guidelines carefully. I use a consistent motion while wrapping to keep it uniform and check it against a template when I can.
What techniques do you use to wrap hoses securely and efficiently?
How to Answer
- 1
Use a figure-eight pattern to prevent tangling.
- 2
Keep the hose straight while wrapping to ensure a tight coil.
- 3
Secure the hose with ties or straps after wrapping for stability.
- 4
Avoid kinks by maintaining even tension while wrapping.
- 5
Store hoses in a designated area to prevent damage and promote easy access.
Example Answers
I use a figure-eight pattern when wrapping hoses to avoid tangles, and I ensure the hose remains straight to create a nice tight coil. After wrapping, I secure it with straps to keep it in place.
Don't Just Read Hose Wrapper Questions - Practice Answering Them!
Reading helps, but actual practice is what gets you hired. Our AI feedback system helps you improve your Hose Wrapper interview answers in real-time.
Personalized feedback
Unlimited practice
Used by hundreds of successful candidates
What types of materials do you commonly work with when wrapping hoses, and why do they matter?
How to Answer
- 1
Identify common materials like rubber, plastic, and cloth.
- 2
Explain the purpose of each material: durability, flexibility, or protection.
- 3
Discuss how material choice affects performance and longevity.
- 4
Mention any industry standards or regulations regarding materials.
- 5
Be prepared to give examples of specific hoses you've wrapped.
Example Answers
I commonly work with rubber, PVC, and nylon. Rubber provides excellent durability for heavy-duty hoses, while PVC is used for lighter applications due to its flexibility. Using the right material ensures that the hose can withstand environmental conditions and maintain its integrity over time.
What tools or equipment do you consider essential for the hose wrapping process?
How to Answer
- 1
Identify key tools like hose wrapping machines or hand tools.
- 2
Mention safety equipment important for the wrapping process.
- 3
Discuss materials used in the hose wrapping, like protection wraps.
- 4
Explain the importance of quality control tools for product consistency.
- 5
Consider mentioning any relevant software for tracking or efficiency.
Example Answers
I believe that a hose wrapping machine is essential for efficiency, along with hand tools like scissors for trimming. Safety gloves for handling materials are also important, and using quality wraps ensures durability.
What industry standards or best practices do you follow when wrapping hoses?
How to Answer
- 1
Understand the types of hoses and their specifications.
- 2
Follow manufacturer guidelines for wrapping and storage.
- 3
Ensure hoses are clean and dry before wrapping.
- 4
Use proper techniques to prevent kinking and damage.
- 5
Regularly inspect hoses for wear and tear during wrapping.
Example Answers
I follow best practices by first identifying the type of hose I'm dealing with and adhering to the manufacturer's guidelines for wrapping. This ensures the hose remains functional and lasts longer.
How do you maintain the tools and equipment used for hose wrapping to ensure optimal performance?
How to Answer
- 1
Regularly inspect tools for wear and tear before and after use
- 2
Clean equipment thoroughly after each wrapping job to prevent residue build-up
- 3
Lubricate moving parts periodically to ensure smooth operation
- 4
Store tools in a dry, clean, and organized area to prevent damage
- 5
Keep a maintenance log to track issues and repairs for each tool
Example Answers
I regularly inspect each tool for any signs of wear or damage before starting my work. After each job, I clean them thoroughly to remove any residue and lubricate moving parts to ensure they perform well. I also keep a log to track maintenance activities for each tool.
What methods do you use to test the wrapped hoses for durability and performance?
How to Answer
- 1
Describe specific tests you perform, like pressure tests or abrasion resistance tests
- 2
Mention tools or equipment used in your testing methods
- 3
Explain how you ensure consistency in your testing processes
- 4
Share examples of performance metrics you monitor during testing
- 5
Discuss any relevant standards or protocols you follow
Example Answers
I perform pressure tests on the wrapped hoses to check for leaks and ensure they can withstand the required pressure levels. I also use abrasion resistance tests to evaluate the durability against wear. I monitor metrics like burst pressure and hose life cycle to ensure performance aligns with industry standards.
What safety regulations do you believe are important when wrapping hoses?
How to Answer
- 1
Understand the proper handling techniques to avoid strain injuries.
- 2
Ensure hoses are stored in a way that prevents kinks and tangles, reducing hazards.
- 3
Identify and follow any industry-specific safety standards or guidelines for hose use.
- 4
Use appropriate personal protective equipment (PPE) when handling hoses.
- 5
Regularly inspect hoses for damage or wear to prevent accidents.
Example Answers
I believe proper handling techniques are crucial to avoid strain injuries, and ensuring hoses are stored properly can prevent accidents like tripping.
How would you troubleshoot a problem with a hose that was improperly wrapped?
How to Answer
- 1
Identify the symptoms of the improper wrapping
- 2
Check for twists or kinks in the hose
- 3
Unwrap the hose carefully to avoid damage
- 4
Assess the wrapping technique used previously
- 5
Practice proper wrapping techniques to prevent recurrences
Example Answers
I would first inspect the hose for visible twists or kinks causing the issue. Then, I'd carefully unwrap it to avoid further damage, evaluate how it was wrapped before, and apply proper wrapping techniques afterward to ensure it is stored correctly.
What innovative techniques have you implemented in your hose wrapping tasks?
How to Answer
- 1
Think about any new tools or materials you introduced for hose wrapping
- 2
Consider processes you streamlined to improve efficiency or safety
- 3
Mention any specific techniques that enhanced the quality of wrapping
- 4
Highlight how your innovations have benefited the team or operations
- 5
Provide quantitative results if possible to showcase impact
Example Answers
I introduced a heat shrink wrap that improved durability and reduced wear on hoses compared to traditional methods, resulting in a 20% decrease in hose replacements.
Don't Just Read Hose Wrapper Questions - Practice Answering Them!
Reading helps, but actual practice is what gets you hired. Our AI feedback system helps you improve your Hose Wrapper interview answers in real-time.
Personalized feedback
Unlimited practice
Used by hundreds of successful candidates
Behavioral Interview Questions
Can you describe a time when you had to wrap hoses efficiently under a tight deadline?
How to Answer
- 1
Choose a specific example that highlights your efficiency.
- 2
Explain the context clearly, including the deadline you faced.
- 3
Describe the actions you took to meet the deadline.
- 4
Mention any tools or techniques you used to improve efficiency.
- 5
Conclude with the outcome to show the success of your actions.
Example Answers
In my previous job, I was responsible for wrapping hoses for a large event happening the next day. The team was short-staffed, and we had a deadline of four hours. I quickly organized the hoses by size and type, used a hose reel for the larger ones, and delegated tasks to my colleagues. We completed the wrapping in two hours, which was half the expected time, allowing us to prepare for the event smoothly.
Tell me about a situation where you worked as part of a team to complete a complex hose wrapping task.
How to Answer
- 1
Describe the team composition and roles clearly.
- 2
Explain the complexity of the task and why it was challenging.
- 3
Highlight your specific contributions to the team efforts.
- 4
Mention any tools or techniques used during the task.
- 5
Conclude with the outcome and what you learned from the experience.
Example Answers
In my previous job at the hose manufacturing plant, I was part of a five-member team responsible for wrapping a new type of high-pressure hose. The challenge was that the material required precise handling to avoid damage. I coordinated with the team to ensure everyone understood their role, and I operated the wrapping machine while others prepared the materials. We used special adhesives and wrapping techniques to secure the hoses. The project was completed on time, and we increased production efficiency by 15%. This experience taught me the value of teamwork in completing complex tasks.
Don't Just Read Hose Wrapper Questions - Practice Answering Them!
Reading helps, but actual practice is what gets you hired. Our AI feedback system helps you improve your Hose Wrapper interview answers in real-time.
Personalized feedback
Unlimited practice
Used by hundreds of successful candidates
Describe an experience when you identified a safety issue while wrapping hoses. What did you do about it?
How to Answer
- 1
Identify a specific incident where you saw a safety issue.
- 2
Explain how you recognized the issue and its potential consequences.
- 3
Detail the actions you took to address the problem.
- 4
Mention any communication with team members or supervisors.
- 5
Highlight any positive outcomes from your actions.
Example Answers
While wrapping hoses, I noticed that one was frayed and posed a risk of leaks. I immediately stopped, informed my supervisor, and replaced the hose with a new one. This prevented any potential safety hazards.
Have you ever been involved in ensuring the quality of the hoses you wrapped? What steps did you take?
How to Answer
- 1
Discuss specific quality control methods you used.
- 2
Mention any standards or guidelines you followed.
- 3
Describe regular inspections or tests you conducted.
- 4
Share how you handled any quality issues that arose.
- 5
Highlight teamwork or communication involved in quality assurance.
Example Answers
Yes, I was responsible for quality checks during the hose wrapping process. I followed specific industry standards and conducted visual inspections after each batch.
Give an example of a time when you had to adapt your hose wrapping technique to meet a unique requirement.
How to Answer
- 1
Identify a specific situation where you faced a unique wrapping requirement.
- 2
Describe the original technique you used and what changed.
- 3
Explain the new technique you implemented to adapt.
- 4
Highlight the result of your adaptation and how it succeeded.
- 5
Mention any feedback you received that reflects the effectiveness of your adaptation.
Example Answers
In my last job, I was wrapping hoses for a client who needed more compact storage solutions. Instead of my usual spiral wrap, I used a figure-eight method which allowed the hoses to be more tightly packed. The client was thrilled with the new arrangement, and it even saved them space in their storage area.
Can you discuss a lesson you learned from a mistake you made while wrapping hoses?
How to Answer
- 1
Identify a specific mistake related to hose wrapping.
- 2
Explain the impact that mistake had on the task or project.
- 3
Describe how you corrected the mistake.
- 4
Discuss the lesson you learned from the experience.
- 5
Relate how you apply that lesson in your current work.
Example Answers
Once, I wrapped a hose too tightly and it kinked, causing a blockage during use. I recognized that a gradual wrap would prevent this. Now, I always ensure to wrap hoses loosely enough to maintain flexibility, which has improved efficiency.
Describe a time when you took initiative to improve the hose wrapping process. What was the outcome?
How to Answer
- 1
Think of a specific situation where you noticed an inefficiency.
- 2
Explain the steps you took to implement a change.
- 3
Highlight the impact of your actions on the team or process.
- 4
Use metrics or specific results if possible.
- 5
Keep your answer structured: Situation, Action, Result.
Example Answers
In my previous job, I noticed that the hose wrapping process was taking too long. I introduced a new technique using a pipe system to hold the hoses in place, which streamlined the wrapping. As a result, we reduced time spent on wrapping by 30%, allowing us to handle more orders each day.
How have you demonstrated reliability in your past hose wrapping roles?
How to Answer
- 1
Provide specific examples of meeting deadlines consistently.
- 2
Mention how you followed safety protocols reliably.
- 3
Share instances when you maintained quality standards.
- 4
Talk about being dependable in team settings.
- 5
Describe situations where you took ownership of your tasks.
Example Answers
In my last job, I consistently met deadline for wrapping hoses, ensuring every order was completed on time. I communicated effectively with my team to balance our workloads.
Tell me about a time when you received constructive criticism regarding your wrapping technique.
How to Answer
- 1
Choose a specific instance that highlights your ability to learn.
- 2
Explain the feedback you received clearly and honestly.
- 3
Describe the steps you took to improve your wrapping technique.
- 4
Show how this experience has made you a better wrapper.
- 5
Conclude with any positive results from your improvement.
Example Answers
During my last job, a supervisor pointed out that my wrapping was too loose, which could lead to damage. I took this feedback seriously and practiced my technique by using tighter wraps while still ensuring the items were secure. This helped me improve efficiency and maintain quality, and my wrapping accuracy improved significantly.
Don't Just Read Hose Wrapper Questions - Practice Answering Them!
Reading helps, but actual practice is what gets you hired. Our AI feedback system helps you improve your Hose Wrapper interview answers in real-time.
Personalized feedback
Unlimited practice
Used by hundreds of successful candidates
What motivates you to perform well as a hose wrapper?
How to Answer
- 1
Focus on personal pride in craftsmanship and quality of work
- 2
Mention the importance of teamwork and supporting colleagues
- 3
Highlight meeting production goals and deadlines as a motivator
- 4
Emphasize the satisfaction from learning and improving skills
- 5
Share how contributing to overall safety and efficiency inspires you
Example Answers
I take pride in my work and enjoy ensuring every hose is wrapped neatly and securely, as it reflects my commitment to quality.
Situational Interview Questions
If you were assigned multiple hose wrapping assignments of varying priority, how would you determine which to tackle first?
How to Answer
- 1
Assess the deadlines for each assignment
- 2
Evaluate the impact of each task on operations
- 3
Consider the complexity and resources required for each task
- 4
Communicate with your supervisor for prioritization
- 5
Organize tasks based on urgency and importance
Example Answers
I would first check the deadlines for each assignment to see which ones are due soonest. Then, I would assess which tasks have the biggest impact on our operations to prioritize those. If needed, I would consult with my supervisor for their input on prioritizing the assignments. Lastly, I'd tackle the simpler tasks first if they are urgent to free up time for the more complex ones.
How would you handle a situation where a colleague is not following the proper hose wrapping procedure?
How to Answer
- 1
Observe the colleague and confirm they are not following procedures.
- 2
Approach them calmly and ask if they need assistance or clarification.
- 3
Explain the importance of the procedure for safety and efficiency.
- 4
Suggest practicing the correct method together for better understanding.
- 5
If the issue persists, inform a supervisor to address it properly.
Example Answers
I would first observe the colleague to ensure they're not following the correct hose wrapping procedure. Then, I would approach them in a friendly manner, asking if they need help or if there's a reason for the deviation. I'd explain that following the correct procedure is crucial for safety. If they still struggle, I would offer to practice with them to reinforce the correct method. If it continues, I would involve a supervisor.
Don't Just Read Hose Wrapper Questions - Practice Answering Them!
Reading helps, but actual practice is what gets you hired. Our AI feedback system helps you improve your Hose Wrapper interview answers in real-time.
Personalized feedback
Unlimited practice
Used by hundreds of successful candidates
Imagine you notice that your current hose wrapping method is taking longer than expected. What steps would you take to improve efficiency?
How to Answer
- 1
Analyze the current wrapping process to identify bottlenecks.
- 2
Consider using different tools or equipment to speed up the wrapping.
- 3
Train team members on best practices to improve their efficiency.
- 4
Experiment with techniques to find a faster wrapping method.
- 5
Gather feedback from colleagues on potential improvements.
Example Answers
I would first observe where the delays are happening in the wrapping process and then test using a different type of wrapping tool that could be faster.
If a customer expressed dissatisfaction with the wrapped hose product, how would you address their concerns?
How to Answer
- 1
Listen actively to the customer's complaints.
- 2
Empathize with the customer's feelings and situation.
- 3
Ask clarifying questions to understand the issue fully.
- 4
Provide a solution or compensation if appropriate.
- 5
Follow up to ensure customer satisfaction after resolution.
Example Answers
I would first listen to the customer to understand their issue fully. Then, I would empathize with their frustration, ask clarifying questions, and offer a replacement or refund if applicable.
If two team members disagreed on how to wrap a particular hose, how would you facilitate a resolution?
How to Answer
- 1
Listen to both team members' perspectives without bias.
- 2
Encourage a collaborative discussion to explore both wrapping methods.
- 3
Focus on the advantages of each method and common goals.
- 4
Suggest a trial run of both methods to evaluate effectiveness.
- 5
Make a final decision based on team input and practical results.
Example Answers
I would listen to both individuals to understand their viewpoints. Then, I would facilitate a discussion to highlight the benefits of each wrapping method. If necessary, we could test both methods during a practice session and decide based on the outcomes.
What would you do if a supervisor provided you with critical feedback on your hose wrapping method?
How to Answer
- 1
Listen carefully to the feedback and understand the specific points raised.
- 2
Ask clarifying questions if needed to ensure you comprehend the feedback.
- 3
Reflect on the feedback and evaluate how it can improve your technique.
- 4
Demonstrate openness by thanking the supervisor for their guidance.
- 5
Incorporate the feedback into your practice and follow up with the supervisor about your progress.
Example Answers
I would listen to my supervisor's feedback attentively and ask questions if I needed clarification. Then, I would reflect on how I could improve my hose wrapping method and would implement those changes right away. Finally, I’d follow up to show my progress and keep the lines of communication open.
If you had to wrap a large number of hoses in a limited timeframe, what strategies would you implement?
How to Answer
- 1
Assess the size and length of hoses to determine wrapping efficiency
- 2
Use a team approach to divide the work and increase throughput
- 3
Employ tools or jigs to facilitate quicker wrapping
- 4
Establish a clear workflow to minimize movement and downtime
- 5
Practice efficient wrapping techniques to speed up the process
Example Answers
To wrap a large number of hoses quickly, I would first divide the hoses by size to streamline the process. Then, I would gather a team to work in parallel, wrapping different hoses simultaneously. We could also use a hose wrapping tool to speed things up, and I would ensure we have a clear system set up to manage the workflow effectively.
If you were short on supplies, how would you ensure you still met your hose wrapping goals?
How to Answer
- 1
Assess current inventory and prioritize essential supplies
- 2
Look for alternative materials that can be used temporarily
- 3
Communicate with your team about the supply shortage and seek input
- 4
Adjust goals and timelines based on the availability of supplies
- 5
Implement creative solutions to maximize efficiency with limited resources
Example Answers
I would first check our current inventory to see what we have left and prioritize the most critical supplies needed for wrapping. Then, I might suggest using some alternative wrapping materials we have in stock while discussing with the team how to proceed effectively.
How would you approach improving a hose wrapping process that has become outdated?
How to Answer
- 1
Analyze the current wrapping process to identify bottlenecks.
- 2
Research modern wrapping technologies and techniques.
- 3
Gather feedback from team members who use the process.
- 4
Implement a pilot program with new methods to measure improvements.
- 5
Document changes and train team members on the updated process.
Example Answers
I would start by observing the current hose wrapping process to pinpoint inefficiencies. Then, I'd research newer wrapping techniques and engage the team for feedback. After selecting potential improvements, I would run a trial to see how they impact our workflow.
If a hose you wrapped was found to be defective shortly after delivery, how would you respond?
How to Answer
- 1
Acknowledge the issue and take responsibility.
- 2
Investigate the cause of the defect promptly.
- 3
Communicate transparently with the customer about the situation.
- 4
Offer solutions, such as a replacement or refund.
- 5
Implement measures to prevent similar issues in the future.
Example Answers
I would first acknowledge the defect to the customer and apologize for any inconvenience caused. Then I would assess what went wrong and discuss the issue openly with the team to find out how it happened. I would offer the customer a replacement hose or a refund and ensure that we address any quality controls to avoid this in the future.
Don't Just Read Hose Wrapper Questions - Practice Answering Them!
Reading helps, but actual practice is what gets you hired. Our AI feedback system helps you improve your Hose Wrapper interview answers in real-time.
Personalized feedback
Unlimited practice
Used by hundreds of successful candidates
Hose Wrapper Position Details
Related Positions
- Roll Wrapper
- Coil Wrapper
- Bottle Carrier
- Hook Puller
- Hanker
- Hand Blocker
- Body Hanger
- Heading Maker
- Wire Insulator
- Respooler
Similar positions you might be interested in.
Ace Your Next Interview!
Practice with AI feedback & get hired faster
Personalized feedback
Used by hundreds of successful candidates
Ace Your Next Interview!
Practice with AI feedback & get hired faster
Personalized feedback
Used by hundreds of successful candidates