Top 31 Hub Cutter Interview Questions and Answers [Updated 2025]
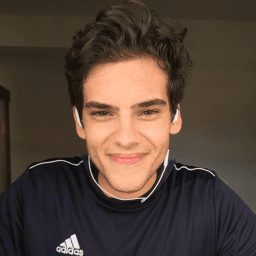
Andre Mendes
•
March 30, 2025
Preparing for a Hub Cutter interview? This blog post is your ultimate guide to acing it! We’ve compiled the most common interview questions for the Hub Cutter role, complete with example answers and effective answering tips. Whether you're a seasoned professional or new to the field, these insights will help you confidently navigate your interview and make a great impression. Dive in and start preparing today!
Download Hub Cutter Interview Questions in PDF
To make your preparation even more convenient, we've compiled all these top Hub Cutterinterview questions and answers into a handy PDF.
Click the button below to download the PDF and have easy access to these essential questions anytime, anywhere:
List of Hub Cutter Interview Questions
Behavioral Interview Questions
Can you describe a time when you had to work closely with a team to meet a deadline in a cutting operation?
How to Answer
- 1
Choose a specific example from your past experience.
- 2
Highlight your role and contributions to the team effort.
- 3
Describe the challenge or tight deadline you faced.
- 4
Explain the teamwork involved and how you communicated.
- 5
Conclude with the positive outcome and what you learned.
Example Answers
In my previous job, our team had to complete a large cutting order within a very tight timeframe. I coordinated with the machine operators to ensure everyone was aligned on priorities. We held brief daily meetings to track our progress, and I adjusted workflows as needed. As a result, we met the deadline successfully and improved our process for future orders.
Tell me about a challenging cutting task that you faced, and how you resolved it.
How to Answer
- 1
Choose a specific cutting task that was particularly difficult.
- 2
Explain the reasons it was challenging, including any technical or environmental factors.
- 3
Describe your thought process in identifying a solution.
- 4
Mention the steps you took to resolve the issue and any tools or methods you used.
- 5
Highlight the positive outcome or what you learned from the experience.
Example Answers
In a recent project, I faced a challenging cutting task where I had to cut a very thick material with uneven surfaces. The main issue was ensuring precision while maintaining safety. I evaluated the tools at my disposal and decided to use a specialized saw with adjustable settings. By measuring carefully and making multiple passes, I was able to achieve a clean cut without damaging the material. This taught me the importance of adapting my tools to the task.
Don't Just Read Hub Cutter Questions - Practice Answering Them!
Reading helps, but actual practice is what gets you hired. Our AI feedback system helps you improve your Hub Cutter interview answers in real-time.
Personalized feedback
Unlimited practice
Used by hundreds of successful candidates
Give an example of how you communicated an issue to your supervisor when performing cutting tasks.
How to Answer
- 1
Identify a specific cutting task where you encountered an issue.
- 2
Explain the problem clearly and concisely.
- 3
Describe how you approached your supervisor about the issue.
- 4
Mention any relevant details that supported your case.
- 5
Share the outcome or resolution after communicating.
Example Answers
During a large cutting job, I noticed the machine was consistently misaligning the cuts. I documented the issue and approached my supervisor to explain the misalignment and showed examples from the cutting sheets. After discussing it, we decided to recalibrate the machine, which solved the problem.
Describe a situation where you had to lead a team of cutters. What approach did you take?
How to Answer
- 1
Select a specific situation where you led a team of cutters
- 2
Explain the goal you aimed to achieve with the team
- 3
Describe your leadership style and how you motivated the team
- 4
Highlight any challenges faced and how you overcame them
- 5
Conclude with the results and what you learned from the experience
Example Answers
In my previous role, I led a team of five cutters to meet a tight deadline for a large project. My goal was to optimize our workflow and improve efficiency. I held a briefing to assign tasks according to each cutter's strengths and encouraged them to communicate openly about any issues. We faced equipment failures, but I ensured we had a quick response plan. We successfully completed the project ahead of schedule, and I learned the importance of adaptability and clear communication.
Discuss a time when you had to adapt to new cutting equipment or technology on the job.
How to Answer
- 1
Identify a specific instance where you faced new cutting equipment.
- 2
Describe the steps you took to learn the equipment quickly.
- 3
Include details about any challenges you faced and how you overcame them.
- 4
Highlight the positive outcome of adapting to the new technology.
- 5
Keep your answer focused and concise, illustrating your ability to adapt.
Example Answers
In my previous job, we switched to a CNC cutting machine. I took the initiative to attend training sessions and studied the user manual extensively. I faced a challenge with the software integration but collaborated with a colleague who had experience. As a result, I became the go-to person for the machine, improving our team's efficiency by 20%.
Can you provide an example of when you went above and beyond in your role as a cutter?
How to Answer
- 1
Choose a specific project where your effort made a significant difference.
- 2
Highlight any challenges you faced and how you overcame them.
- 3
Emphasize teamwork and communication if applicable.
- 4
Include measurable results or positive feedback received.
- 5
Keep the story concise and focused on your actions.
Example Answers
During a major project, we were short on time to meet a tight deadline. I volunteered to work extra hours and coordinated with the team to ensure we completed the cuts accurately and on time. This led to a successful project delivery and praise from management for our efforts.
Describe a time when you had to manage multiple cutting tasks at once. How did you handle it?
How to Answer
- 1
Use the STAR method: Situation, Task, Action, Result.
- 2
Clearly outline the tasks you were managing and their importance.
- 3
Emphasize your prioritization and time management skills.
- 4
Highlight any collaboration with team members or use of tools.
- 5
Conclude with the positive outcome and what you learned.
Example Answers
In my previous job, I was tasked to manage three cutting projects simultaneously for an exhibition. I prioritized the tasks based on deadlines and materials availability. I communicated with my team to delegate some aspects, ensuring efficiency. As a result, all projects were completed on time, and the exhibits received great feedback.
Discuss a situation where you set a goal for your cutting productivity and achieved it.
How to Answer
- 1
Choose a specific timeframe and clear metric for productivity.
- 2
Explain the steps you took to achieve the goal.
- 3
Highlight any challenges you faced and how you overcame them.
- 4
Mention the outcome and how it benefited the team or process.
- 5
Reflect on what you learned from this experience.
Example Answers
In my previous role, I aimed to increase my cutting efficiency by 20% within a month. I tracked my daily output and adjusted my techniques by practicing precision cuts during downtime. I encountered some material supply issues but worked closely with the supply team to resolve them. By the end of the month, I improved my output by 25%, enhancing the overall production speed and meeting tight deadlines.
Tell me about a time when you had to manage your energy and focus during a long cutting shift.
How to Answer
- 1
Choose a specific shift example that highlights your experience.
- 2
Explain the challenge you faced in maintaining energy and focus.
- 3
Describe the strategies you used to overcome fatigue.
- 4
Highlight any support or tools you utilized to help manage your focus.
- 5
Conclude with the positive outcome of your efforts.
Example Answers
During a 12-hour cutting shift, I struggled with fatigue around the 8-hour mark. To manage my energy, I took scheduled breaks to stretch and hydrate, and I also kept a small snack of nuts handy for quick energy boosts. This approach helped me stay focused and maintain my cutting precision until the end of my shift.
Don't Just Read Hub Cutter Questions - Practice Answering Them!
Reading helps, but actual practice is what gets you hired. Our AI feedback system helps you improve your Hub Cutter interview answers in real-time.
Personalized feedback
Unlimited practice
Used by hundreds of successful candidates
Describe an instance where you implemented a new technique that improved cutting times.
How to Answer
- 1
Identify a specific technique you used.
- 2
Explain how you discovered or developed this technique.
- 3
Include measurable results or improvements in cutting times.
- 4
Highlight any challenges you faced and how you overcame them.
- 5
Conclude with how this technique was received by your team or affected overall operations.
Example Answers
In my last role, I introduced a new cutting technique using a more efficient blade that I researched. This method reduced our cutting time by 20%. Initially, some team members were hesitant, but after a training session, they embraced it, resulting in increased productivity.
Technical Interview Questions
What safety measures do you implement while cutting materials?
How to Answer
- 1
Always wear personal protective equipment such as gloves and safety glasses.
- 2
Ensure the cutting area is clean and free from obstructions.
- 3
Use the proper cutting tools and ensure they are well-maintained.
- 4
Establish a safe distance from others while cutting materials.
- 5
Follow the manufacturer's instructions for the equipment being used.
Example Answers
I always wear safety glasses and gloves to protect myself while cutting materials. I also make sure to keep the workspace clean to avoid any accidents.
Can you explain the steps involved in setting up a cutting machine?
How to Answer
- 1
Gather necessary tools and safety equipment.
- 2
Check the machine's specifications and settings.
- 3
Load the material securely into the machine.
- 4
Adjust the cutting parameters as needed.
- 5
Perform a test cut to ensure accuracy.
Example Answers
First, I gather all tools and ensure I'm wearing safety gear. Then, I check the machine's specs. After that, I securely load the material and adjust the cutting parameters. Lastly, I perform a test cut to confirm the setup is correct.
Don't Just Read Hub Cutter Questions - Practice Answering Them!
Reading helps, but actual practice is what gets you hired. Our AI feedback system helps you improve your Hub Cutter interview answers in real-time.
Personalized feedback
Unlimited practice
Used by hundreds of successful candidates
What types of materials have you worked with in cutting processes, and what are the unique challenges of each?
How to Answer
- 1
Identify specific materials you have experience with such as metals, composites, plastics, etc.
- 2
Discuss the cutting methods used for each material, like laser cutting or waterjet cutting.
- 3
Explain unique challenges faced with each material, such as hardness, thickness, or heat sensitivity.
- 4
Mention any specific tools or machinery you have used and their relevance to the materials.
- 5
Reflect on how you addressed these challenges or improved the cutting process.
Example Answers
I have worked with aluminum, steel, and composite materials. For aluminum, I used laser cutting, which is efficient, but requires careful speed settings to prevent melting. Steel posed challenges due to its hardness, requiring high-speed machining. Composites, on the other hand, needed precision cutting to avoid delamination, which I managed by optimizing the feed rate.
How do you ensure that the cuts you make conform to specification and quality standards?
How to Answer
- 1
Review and understand the specifications for each job before starting.
- 2
Use precise measuring tools to double-check dimensions before cutting.
- 3
Perform regular maintenance on cutting equipment to ensure accuracy.
- 4
Implement a checklist to track quality control steps during the cutting process.
- 5
Incorporate feedback from quality control inspections to improve future cuts.
Example Answers
I always start by thoroughly reviewing the specifications provided for each project. Then, I use precise measuring tools like calipers to verify dimensions before making any cuts. Regularly maintaining my cutting equipment also plays a crucial role in ensuring accuracy.
What is your experience with maintaining cutting equipment? Can you provide an example?
How to Answer
- 1
Mention specific types of cutting equipment you have worked with
- 2
Discuss routine maintenance practices you followed
- 3
Include any troubleshooting experiences
- 4
Emphasize the importance of safety during maintenance
- 5
Provide measurable outcomes from your maintenance efforts
Example Answers
I have worked with various types of cutting equipment such as band saws and CNC machines. In my previous role, I performed routine maintenance every month which included lubricating parts and checking for wear, ensuring everything ran smoothly and safely.
What different cutting techniques are you familiar with, and how do you decide which to use?
How to Answer
- 1
List the cutting techniques you know such as straight cutting, bevel cutting, and contour cutting.
- 2
Explain the pros and cons of each technique briefly.
- 3
Discuss how the material type influences your choice of technique.
- 4
Mention specific projects where you applied these techniques effectively.
- 5
Conclude with a decision-making process based on the project requirements.
Example Answers
I'm familiar with straight cutting, bevel cutting, and contour cutting. Straight cutting is great for clean edges in wood, while bevel cutting is useful for creating angled joints. For complex shapes, contour cutting is ideal. I choose based on the material's properties; for instance, I would use straight cutting for plywood, but if I need to create a decorative edge, I'd switch to bevel cutting.
How do you calibrate a cutting machine to ensure precision?
How to Answer
- 1
Start with inspecting the machine and its components for wear and damage.
- 2
Use calibration tools such as gauges and laser levels to measure settings.
- 3
Adjust the cutting parameters according to manufacturer's specifications.
- 4
Run test cuts on scrap material to verify accuracy.
- 5
Document the calibration process and any adjustments made.
Example Answers
I first inspect the machine for any signs of wear. Then I use gauges to measure the blade alignment and adjust it as specified by the manufacturer's guide. I make test cuts on scrap material to ensure precision before finalizing the settings.
What is your understanding of tolerances in cutting, and how do you ensure you meet them?
How to Answer
- 1
Discuss the definition of tolerances and their importance in cutting operations
- 2
Mention common tolerance standards like ISO or ANSI
- 3
Explain the measurement methods used to verify tolerances
- 4
Highlight your experience with adjusting processes to meet tolerance requirements
- 5
Include examples of tools or techniques you use to ensure precision
Example Answers
Tolerances are the allowable limits of variation in a part's dimensions. I follow ISO standards to ensure each cut meets these specifications. I use calipers and micrometers to measure parts accurately and adjust machining parameters as needed to achieve the desired tolerance.
How do you troubleshoot issues that arise during the cutting process?
How to Answer
- 1
Identify the specific issue with the cut, such as blade sharpness or material misalignment.
- 2
Check machine settings and confirm they are configured correctly for the material being cut.
- 3
Conduct a visual inspection of the cutting apparatus and the workpiece for any visible defects.
- 4
Refer to troubleshooting manuals for standard solutions based on the issue identified.
- 5
Test adjustments on scrap material before applying them to the actual product.
Example Answers
When troubleshooting issues during the cutting process, I first identify the specific problem, like blade dullness or misalignment of the material. Then I verify the machine settings to ensure they match the specifications for the material. If everything seems fine, I visually inspect the cutting tool and the workpiece for defects. If the problem persists, I consult the troubleshooting manual for solutions and test any adjustments on scrap material first.
How do the characteristics of different materials affect your cutting approach?
How to Answer
- 1
Identify key material characteristics like hardness, ductility, and thermal conductivity
- 2
Explain how each characteristic influences cutting speed or tool choice
- 3
Discuss the importance of adjusting feed rate and cutting depth based on materials
- 4
Mention any specific tools or techniques suited for different materials
- 5
Provide real-world examples to illustrate your points
Example Answers
Different materials require different cutting techniques. For example, harder materials like steel need slower cutting speeds and sharper tools, while softer materials like aluminum can be cut faster and with less pressure. I always adjust my feed rate based on the material to avoid tool wear.
Don't Just Read Hub Cutter Questions - Practice Answering Them!
Reading helps, but actual practice is what gets you hired. Our AI feedback system helps you improve your Hub Cutter interview answers in real-time.
Personalized feedback
Unlimited practice
Used by hundreds of successful candidates
Situational Interview Questions
If you discover a defect in the material while cutting, what steps would you take to address the issue?
How to Answer
- 1
Stop cutting immediately to prevent further waste.
- 2
Assess the extent of the defect to determine if it is salvageable.
- 3
Notify your supervisor or team leader about the defect.
- 4
Document the defect with photos or notes for future reference.
- 5
Follow the company's protocol for handling defective materials.
Example Answers
I would stop cutting right away and inspect the defect to see how severe it is. Then, I would inform my supervisor to decide the next steps and follow the protocol for defective materials.
Imagine you are under pressure to increase production. How would you prioritize your tasks as a Hub Cutter?
How to Answer
- 1
Assess current workflow and identify bottlenecks
- 2
Focus on high-impact tasks that directly boost output
- 3
Delegate less critical tasks to team members
- 4
Monitor production metrics to make data-driven decisions
- 5
Stay adaptable to change priorities as new challenges arise
Example Answers
First, I would analyze the existing workflow and see where delays are happening. Then, I'd focus on the tasks that can immediately improve production. If specific jobs are time-consuming, I'd delegate those to teammates to concentrate on the crucial cutting operations. Finally, I'd keep an eye on our output metrics to ensure we're meeting our targets.
Don't Just Read Hub Cutter Questions - Practice Answering Them!
Reading helps, but actual practice is what gets you hired. Our AI feedback system helps you improve your Hub Cutter interview answers in real-time.
Personalized feedback
Unlimited practice
Used by hundreds of successful candidates
How would you handle a disagreement with a co-worker about the cutting process?
How to Answer
- 1
Listen carefully to the co-worker's perspective before responding
- 2
Stay calm and respectful to maintain a positive working relationship
- 3
Use examples and data to support your point of view on cutting techniques
- 4
Propose a trial or test to evaluate both methods fairly
- 5
Be open to compromise if it leads to a better outcome for the project
Example Answers
I would first listen to my co-worker's point of view to understand their reasoning. Then, I would calmly share my perspective using data from previous projects. If we still disagreed, I might suggest running a small test of both methods to see which yields better results.
What would you do if a cutting machine malfunctions during a critical production period?
How to Answer
- 1
Stay calm and assess the situation quickly
- 2
Notify your supervisor and the maintenance team immediately
- 3
Check the machine for any obvious issues or error messages
- 4
Prepare alternative solutions, such as switching to another machine
- 5
Communicate with the team to adjust schedules and minimize impact
Example Answers
I would first remain calm and quickly assess the malfunction. Then, I would notify my supervisor and maintenance for immediate assistance while looking for any visible issues or error codes. If the problem cannot be resolved quickly, I would coordinate with the team to use another machine and adjust our production plan accordingly.
How would you address complaints from the quality assurance team regarding the accuracy of your cuts?
How to Answer
- 1
Acknowledge the concern and thank the QA team for their feedback
- 2
Ask for specific examples of the inaccuracies they noticed
- 3
Review your cutting process to identify potential errors
- 4
Implement any necessary adjustments or training based on the feedback
- 5
Follow up with the QA team to confirm improvements
Example Answers
I would start by thanking the QA team for bringing the issues to my attention. I'd ask for specific instances where cuts were inaccurate to understand better. Then I would evaluate my processes, make any adjustments needed, and perhaps receive further training if necessary. Finally, I would check in with the QA team to see if my changes have resolved their concerns.
If you could redesign any aspect of the cutting process to be more efficient, what would you change?
How to Answer
- 1
Identify a specific part of the cutting process.
- 2
Consider technology that could improve efficiency.
- 3
Think about reducing waste or time.
- 4
Make sure your idea is practical and implementable.
- 5
Explain the benefits of your proposed change clearly.
Example Answers
I would implement a digital cutting guide system that uses sensors to optimize blade angles and reduce material waste.
How would you motivate a team that is feeling overwhelmed with their cutting workload?
How to Answer
- 1
Acknowledge the team's feelings and validate their hard work
- 2
Break down the workload into smaller, manageable tasks
- 3
Encourage open communication about challenges and support each other
- 4
Set clear goals and celebrate small victories to boost morale
- 5
Provide resources or adjust deadlines if necessary
Example Answers
I would first acknowledge the team's feelings and reassure them that it's okay to feel overwhelmed. Then, I'd help break down their tasks into smaller, actionable items, allowing everyone to focus on one thing at a time. Open communication would be encouraged, so everyone feels supported. I'd also set short-term goals and celebrate when we meet them to keep morale high.
If a safety incident occurs on the cutting floor, what is your immediate course of action?
How to Answer
- 1
Assess the situation to determine the severity of the incident.
- 2
Ensure that all workers are safe and accounted for.
- 3
Administer first aid if needed and call for medical assistance.
- 4
Report the incident to a supervisor immediately.
- 5
Document the incident details for further investigation.
Example Answers
First, I would quickly assess the situation to see if anyone is injured and ensure their safety. Next, I would provide first aid if necessary and call for medical help. Then, I would inform my supervisor about the incident and document everything that happened.
How would you train a new employee on the cutting team to ensure they understand the processes?
How to Answer
- 1
Start with a comprehensive overview of cutting processes and safety protocols.
- 2
Use hands-on demonstrations to showcase techniques and equipment usage.
- 3
Create a step-by-step training guide or checklist for reference.
- 4
Encourage questions throughout the training for clarification.
- 5
Schedule regular follow-up sessions to assess understanding and provide feedback.
Example Answers
I would first provide the new employee with a detailed overview of our cutting processes, emphasizing safety. Then, I would demonstrate each cutting technique, allowing them to practice hands-on. I’d create a checklist they can refer to, and I would encourage them to ask questions whenever something is unclear. Lastly, I’d set up weekly feedback sessions to monitor their progress and address any issues.
What actions would you take if you realized your cutting process was causing unnecessary waste?
How to Answer
- 1
Identify the source of waste in the cutting process
- 2
Analyze current cutting patterns and materials
- 3
Implement adjustments to cutting techniques or machine settings
- 4
Consult with team members for input and suggestions
- 5
Monitor the changes and measure waste reduction
Example Answers
I would first identify where the most waste is occurring in the cutting process by reviewing the cutting patterns. Then, I would adjust the settings of the machines to optimize the cuts and minimize scrap materials. I would also involve the team to brainstorm improvements and keep track of the changes made to see if waste decreases.
Don't Just Read Hub Cutter Questions - Practice Answering Them!
Reading helps, but actual practice is what gets you hired. Our AI feedback system helps you improve your Hub Cutter interview answers in real-time.
Personalized feedback
Unlimited practice
Used by hundreds of successful candidates
Hub Cutter Position Details
Related Positions
- Die Cutter
- Cam Maker
- Die Maker
- Jig Maker
- Panel Cutter
- Key Cutter
- Pattern Cutter
- Cutter
- Brush Cutter
- Road Cutter
Similar positions you might be interested in.
Ace Your Next Interview!
Practice with AI feedback & get hired faster
Personalized feedback
Used by hundreds of successful candidates
Ace Your Next Interview!
Practice with AI feedback & get hired faster
Personalized feedback
Used by hundreds of successful candidates