Top 31 Instrument Repair Technician Interview Questions and Answers [Updated 2025]
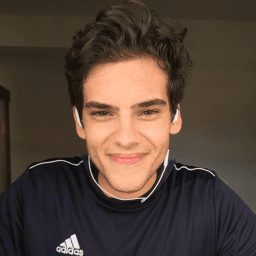
Andre Mendes
•
March 30, 2025
Are you preparing for an Instrument Repair Technician interview and want to stand out? Our updated guide provides the most common interview questions tailored for this role, complete with example answers and actionable tips to help you respond with confidence. Whether you're a seasoned pro or just starting out, this post will equip you with the insights needed to impress your potential employers.
Download Instrument Repair Technician Interview Questions in PDF
To make your preparation even more convenient, we've compiled all these top Instrument Repair Technicianinterview questions and answers into a handy PDF.
Click the button below to download the PDF and have easy access to these essential questions anytime, anywhere:
List of Instrument Repair Technician Interview Questions
Behavioral Interview Questions
How do you keep records of repairs and ensure documentation is accurate?
How to Answer
- 1
Use a standardized form or software for recording repairs
- 2
Document each repair detail immediately after completion
- 3
Verify information with the customer for accuracy
- 4
Regularly back up records to prevent data loss
- 5
Review records periodically to ensure all information is complete
Example Answers
I use a digital logging system to record each repair in real time. After each job, I detail the issue, parts replaced, and customer feedback. I also back up these records weekly.
Can you describe a time when you diagnosed a complex issue with an instrument? What steps did you take to resolve it?
How to Answer
- 1
Start by briefly stating the instrument and the issue you faced.
- 2
Outline specific symptoms that helped you identify the problem.
- 3
Describe the diagnostic steps you took, including any tools used.
- 4
Explain how you resolved the issue step by step.
- 5
Conclude with the result and any feedback received.
Example Answers
I worked on a digital multimeter that was displaying erratic readings. I noticed it was fine on some functions but failed on others. I used a multimeter to measure the internal voltage levels, which guided me to a faulty capacitor on the main board. After replacing the capacitor, the multimeter functioned perfectly, and the customer was very satisfied.
Don't Just Read Instrument Repair Technician Questions - Practice Answering Them!
Reading helps, but actual practice is what gets you hired. Our AI feedback system helps you improve your Instrument Repair Technician interview answers in real-time.
Personalized feedback
Unlimited practice
Used by hundreds of successful candidates
Tell me about a situation where you had to work closely with a team to repair a malfunctioning instrument. How did you ensure effective collaboration?
How to Answer
- 1
Identify a specific team project that involved instrument repair
- 2
Describe your role and responsibilities within the team
- 3
Mention communication methods used to share information
- 4
Explain how teamwork contributed to solving the problem
- 5
Highlight any tools or strategies that facilitated collaboration
Example Answers
In my previous job, our team faced an issue with a malfunctioning oscilloscope. I took the initiative to organize a meeting where each technician could share their input. We used a shared digital tool to document our findings, which streamlined our collaboration. My role was to lead the troubleshooting process, and by maintaining open communication, we quickly identified the faulty component and made the necessary repairs.
Describe a time when you had to adapt to new repair techniques or technologies. How did you handle the learning curve?
How to Answer
- 1
Choose a specific example demonstrating adaptability.
- 2
Explain what the new technique or technology was.
- 3
Discuss the steps you took to learn it, like training or practice.
- 4
Mention any challenges you faced and how you overcame them.
- 5
Conclude with the positive outcome or what you learned.
Example Answers
At my previous job, I encountered a new digital tuning system for wind instruments. I researched the system through online tutorials, shadowed a senior technician, and practiced on demo instruments. Initially, I struggled with the software, but by dedicating extra hours to learn it, I became proficient. This enhanced my repair efficiency and client satisfaction.
Can you provide an example of how you handled a challenging customer situation involving an instrument repair?
How to Answer
- 1
Describe the situation clearly and state why it was challenging.
- 2
Explain your approach to communicating with the customer.
- 3
Outline the steps you took to resolve the issue.
- 4
Highlight the outcome and what the customer reaction was.
- 5
Mention any lessons learned or changes you made to improve service.
Example Answers
I once had a customer who was upset because their instrument was not repaired on time. I listened to their concerns, apologized for the delay, and explained the reasons for it. I offered a discount on their next service, and they appreciated my transparency, which led to a positive resolution.
Tell me about a time when you had multiple instrument repairs to complete within a tight deadline. How did you prioritize your tasks?
How to Answer
- 1
Identify the specific situation and repairs involved.
- 2
Explain how you assessed the urgency of each repair.
- 3
Discuss the criteria you used for prioritization.
- 4
Include how you communicated with stakeholders to manage expectations.
- 5
Share the outcome of your prioritization efforts.
Example Answers
In my previous role, I had three sensitive instruments to repair in a single day. I first evaluated which instruments were critical for upcoming projects and prioritized those. I communicated with my supervisor to ensure everyone was on the same page about deadlines. I managed to complete the most urgent repairs by focusing my time on those instruments first, which were successfully delivered on time.
Have you ever led a project to improve repair processes or systems? What was your approach and what were the results?
How to Answer
- 1
Identify a specific project where you improved a repair process.
- 2
Explain your role and the steps you took to lead the project.
- 3
Highlight the methodologies or tools you used for improvement.
- 4
Discuss the positive outcomes or metrics that resulted from your work.
- 5
Make sure to relate it to the skills relevant to the Instrument Repair Technician role.
Example Answers
At my previous job, I led a project to streamline the instrument calibration process. I gathered input from the team, created a standardized checklist, and implemented a tracking system. This reduced our calibration time by 30% and improved our accuracy rates, leading to better quality control.
Describe a time when you implemented a new technique or tool in your repair process. What inspired this change?
How to Answer
- 1
Choose a specific example related to your repair work.
- 2
Explain the old technique or tool you were using.
- 3
Describe the new technique or tool you implemented.
- 4
Share the results of this change on efficiency or quality.
- 5
Mention what inspired you to make this change, like a problem you faced.
Example Answers
In my previous job, we used a traditional soldering method that was time-consuming. I learned about a new soldering iron with precise temperature control that reduced rework. After implementing it, our repair speed improved by 30%, and the quality of the repairs was much better. I was inspired to make this change after seeing how much time we lost due to overheating components with the old tool.
How do you handle receiving constructive criticism about your repair work?
How to Answer
- 1
Listen carefully to the criticism without interrupting.
- 2
Acknowledge the feedback and thank the person for it.
- 3
Reflect on the criticism and consider its validity.
- 4
Implement the suggestions in future work to improve.
- 5
View constructive criticism as an opportunity for growth.
Example Answers
I always listen to constructive criticism with an open mind and thank the person for their feedback. It helps me see my work from a different perspective. I take the time to reflect on the advice given and apply it to similar repairs in the future. This way, I can continuously improve my skills.
Don't Just Read Instrument Repair Technician Questions - Practice Answering Them!
Reading helps, but actual practice is what gets you hired. Our AI feedback system helps you improve your Instrument Repair Technician interview answers in real-time.
Personalized feedback
Unlimited practice
Used by hundreds of successful candidates
What sparked your interest in becoming an instrument repair technician, and how do you maintain your enthusiasm for the job?
How to Answer
- 1
Share a specific moment or experience that inspired you to pursue this career.
- 2
Explain what aspects of instrument repair you find most enjoyable.
- 3
Discuss how you keep your skills up-to-date and stay motivated.
- 4
Mention any challenges you’ve overcome that deepened your passion.
- 5
Express your commitment to quality and service in this field.
Example Answers
I became interested in instrument repair when I fixed my grandfather's old watch as a child. The satisfaction I felt from making it work again sparked my curiosity. I maintain my enthusiasm by continually learning about new technologies and attending workshops.
Technical Interview Questions
What software or applications do you use in your repair work, and what functions do they serve?
How to Answer
- 1
Identify specific software you use regularly in your repairs.
- 2
Explain the purpose of each software clearly.
- 3
Mention how these applications help improve your efficiency.
- 4
Discuss any software you use for troubleshooting or diagnostics.
- 5
Be prepared to give examples of how you've used these tools.
Example Answers
I often use Service Now for tracking repair requests as it helps me manage workflow efficiently. I also use multimeter calibration software to ensure accurate measurements and troubleshooting applications for diagnosing instrument issues.
What routine maintenance techniques do you apply to prolong the life of instruments?
How to Answer
- 1
Inspect instruments regularly for signs of wear or damage
- 2
Clean instruments thoroughly after each use to remove debris and contaminants
- 3
Lubricate moving parts periodically to prevent rust and wear
- 4
Store instruments in proper conditions to avoid environmental damage
- 5
Follow manufacturer maintenance guidelines and schedules
Example Answers
I regularly inspect instruments for any signs of wear and make repairs as needed. After each use, I clean them thoroughly to prevent buildup.
Don't Just Read Instrument Repair Technician Questions - Practice Answering Them!
Reading helps, but actual practice is what gets you hired. Our AI feedback system helps you improve your Instrument Repair Technician interview answers in real-time.
Personalized feedback
Unlimited practice
Used by hundreds of successful candidates
What is your process for troubleshooting electrical issues in instruments?
How to Answer
- 1
Start by reviewing the instrument's documentation and schematics.
- 2
Perform a visual inspection for obvious signs of damage or loose connections.
- 3
Use a multimeter to test for continuity, voltage, and resistance as needed.
- 4
Isolate the problem by checking each component systematically.
- 5
Document your findings and the steps taken for future reference.
Example Answers
I review the instrument's manuals to understand the circuitry, then inspect for physical damage. After that, I use a multimeter to check continuity and voltages before narrowing down to faulty components.
Explain how you would approach repairing a mechanical failure in an instrument.
How to Answer
- 1
Identify the symptoms of the mechanical failure clearly.
- 2
Conduct a preliminary inspection to diagnose the issue.
- 3
Gather necessary tools and replacement parts for the repair.
- 4
Follow manufacturer's guidelines for repair procedures.
- 5
Test the instrument thoroughly after the repair to ensure functionality.
Example Answers
First, I would observe the instrument to identify the symptoms of the mechanical failure. Then, I would perform a thorough inspection to pinpoint the exact issue. After diagnosing the problem, I would gather the required tools and any replacement parts. Following the manufacturer's repair guidelines, I would carry out the repair and conduct tests to confirm that the instrument is working correctly.
How do you perform calibration on various types of instruments? Can you describe the steps involved?
How to Answer
- 1
Identify the type of instrument and its calibration requirements
- 2
Gather the necessary calibration standards and tools
- 3
Follow the manufacturer's instructions meticulously
- 4
Document the calibration results thoroughly
- 5
Conduct a post-calibration check to ensure accuracy
Example Answers
For electronic instruments, I start by identifying the calibration standards required. I then gather the necessary equipment and follow the manufacturer's detailed instructions. After performing the calibration, I document the results and conduct a final check to ensure the instrument is functioning accurately.
What safety protocols do you follow when repairing sensitive instruments?
How to Answer
- 1
Always wear appropriate personal protective equipment such as gloves and safety goggles.
- 2
Ensure all tools and equipment are calibrated and in good condition before use.
- 3
Follow specific manufacturer instructions for handling and repairing instruments.
- 4
Maintain a clean and organized workspace to prevent accidents and damage.
- 5
Be aware of electrical safety protocols, especially when dealing with sensitive electronic components.
Example Answers
I always use gloves and safety goggles when handling sensitive instruments to protect myself from any harmful chemicals or debris.
What diagnostic tools and equipment do you commonly use in your repairs, and how do you utilize them?
How to Answer
- 1
List specific diagnostic tools you are familiar with.
- 2
Explain how each tool helps in diagnosing issues.
- 3
Mention any experience with software or digital tools.
- 4
Include safety practices while using diagnostic equipment.
- 5
Share an example of a successful repair using these tools.
Example Answers
I commonly use a multimeter for checking electrical connections and circuit continuity. It's crucial for identifying issues with power supply in instruments. Additionally, I use an oscilloscope to analyze signal waveforms during repairs, ensuring that all components are functioning properly.
What types of instruments are you most experienced in repairing?
How to Answer
- 1
Identify specific instruments you have worked with.
- 2
Mention any special techniques or tools you use.
- 3
Highlight your experience level with each type of instrument.
- 4
Provide examples of repairs you have successfully completed.
- 5
Connect your experience to the job requirements.
Example Answers
I have over five years of experience repairing brass instruments, particularly trumpets and trombones. I use specialized tools for dent removal and valve alignment, which has helped me restore over 100 instruments to excellent condition.
What testing procedures do you use to verify that an instrument is functioning correctly after a repair?
How to Answer
- 1
Describe specific testing tools you use like multimeters or oscilloscopes
- 2
Explain the step-by-step process of your testing procedure
- 3
Mention any calibration standards you follow after repairs
- 4
Include any visual or functional tests you perform
- 5
Talk about documentation practices for tracking test results
Example Answers
After a repair, I use a multimeter to check for proper voltage levels and continuity, followed by a calibration check against industry standards. I also perform functional tests to ensure the instrument behaves as expected.
What do you know about warranty policies for the instruments you repair, and how do they influence your work?
How to Answer
- 1
Understand the specific warranty policies of the brands you work with.
- 2
Consider how warranty terms affect the repairs you accept and perform.
- 3
Be aware of documentation required for warranty claims.
- 4
Know the process for troubleshooting and claims under warranty.
- 5
Discuss any experience you have with warranty-related repairs.
Example Answers
I understand that each brand has specific warranty coverage, which specifies what is included and for how long. This influences my repairs, as I ensure to document all work thoroughly and inform customers of any labor or parts covered under their warranty.
Don't Just Read Instrument Repair Technician Questions - Practice Answering Them!
Reading helps, but actual practice is what gets you hired. Our AI feedback system helps you improve your Instrument Repair Technician interview answers in real-time.
Personalized feedback
Unlimited practice
Used by hundreds of successful candidates
Situational Interview Questions
If you found that a co-worker was making mistakes in instrument repairs, how would you address the situation?
How to Answer
- 1
Approach the co-worker privately to discuss your observations.
- 2
Be specific about the mistakes you noticed without being confrontational.
- 3
Offer to help or collaborate on the repairs if needed.
- 4
Encourage an open dialogue for them to explain their perspective.
- 5
Suggest a follow-up meeting to check on progress or improvements.
Example Answers
I would speak to my co-worker in private and share the specific mistakes I observed, ensuring to do this gently. I would offer my assistance in their next repair to help them improve.
Imagine you are faced with an urgent repair request on a critical instrument just before a major project deadline. How would you handle it?
How to Answer
- 1
Assess the urgency and impact of the repair on the project
- 2
Prioritize the repair task to ensure it's done efficiently
- 3
Communicate clearly with your team about the repair status
- 4
Use your skills to implement a quick yet effective solution
- 5
Document the repair process for future reference
Example Answers
I would first analyze how critical the instrument is to the project and prioritize its repair. I'd quickly communicate my plan to my team, ensuring everyone is aware of the situation. Then, using my expertise, I'd focus on a rapid but reliable fix before the deadline.
Don't Just Read Instrument Repair Technician Questions - Practice Answering Them!
Reading helps, but actual practice is what gets you hired. Our AI feedback system helps you improve your Instrument Repair Technician interview answers in real-time.
Personalized feedback
Unlimited practice
Used by hundreds of successful candidates
Suppose you are unable to ascertain the cause of a malfunctioning instrument. What steps would you take to troubleshoot the issue?
How to Answer
- 1
Start with a visual inspection for obvious signs of damage.
- 2
Check all connections and cables for secure and correct placement.
- 3
Review any available manuals or documentation for troubleshooting tips.
- 4
Isolate components to test them individually if possible.
- 5
Consult with colleagues or seek advice from online forums or resources.
Example Answers
First, I would conduct a visual inspection of the instrument to look for any physical damage or loose components. Then, I would check all connections to ensure they are secure. If the problem persists, I would refer to the manuals for specific troubleshooting advice and isolate the components to test them individually.
If a client is dissatisfied with a repair you performed, how would you manage that conversation?
How to Answer
- 1
Listen carefully to the client's concerns without interrupting.
- 2
Acknowledge their feelings and validate their dissatisfaction.
- 3
Apologize for the inconvenience caused by the repair.
- 4
Propose a solution or offer to re-evaluate the repair.
- 5
Follow up after resolving the issue to ensure satisfaction.
Example Answers
I would first listen to the client and understand their concerns fully. I would acknowledge their feelings and apologize for any inconvenience. Then, I would offer to re-evaluate the repair and discuss a solution to ensure they're satisfied.
You need to select components for repairing an instrument with specific requirements. How would you decide which materials to use?
How to Answer
- 1
Analyze the instrument's specifications and requirements carefully.
- 2
Consider the environment where the instrument will be used.
- 3
Evaluate the durability and compatibility of different materials.
- 4
Prioritize cost-effectiveness while ensuring quality.
- 5
Consult manufacturer guidelines or previous repair experiences.
Example Answers
I would start by reviewing the instrument's specifications to understand the required performance and tolerances. Next, I'd assess the operating environment to choose materials that resist wear and corrosion. I’d compare options based on durability and cost to ensure a reliable yet affordable repair.
If you encounter a new type of instrument that you have not worked on before, how would you approach learning about its repair?
How to Answer
- 1
Research the make and model online to find manufacturer documentation or repair guides
- 2
Join online forums or communities of technicians who specialize in that type of instrument
- 3
Check for instructional videos available on platforms like YouTube specifically related to the instrument
- 4
Contact the manufacturer for technical support or training materials
- 5
Practice on similar models if available, to gain hands-on experience with related mechanisms
Example Answers
I would start by researching the instrument's make and model online to find any repair manuals or documentation provided by the manufacturer. I would also look for online communities where I can connect with experienced technicians who might share their insights on that instrument.
If a customer called with unusual behavior from their instrument, how would you guide them over the phone while they are troubleshooting?
How to Answer
- 1
Ask the customer to describe the unusual behavior in detail.
- 2
Instruct them to check power sources and connections first.
- 3
Guide them through resetting the instrument or checking any error codes.
- 4
Encourage them to perform basic diagnostics, like self-tests if available.
- 5
Take notes on their findings and suggest next steps based on the symptoms.
Example Answers
I would start by asking the customer to describe the unusual behavior in detail. I would then advise them to check the power source and make sure all connections are secure. If it has any error codes, I would walk them through how to interpret those and recommend a reset if necessary.
If faced with limited resources while repairing an instrument, how would you maximize what you have to ensure a successful repair?
How to Answer
- 1
Assess all available tools and materials before starting.
- 2
Prioritize repairs that will restore functionality with minimal resources.
- 3
Use creative problem solving to adapt existing tools for new purposes.
- 4
Document the repair process to ensure consistency if further repairs are needed.
- 5
Communicate with colleagues to share knowledge and solutions.
Example Answers
In a situation with limited resources, I would first evaluate what tools and parts I have on hand, then focus on the most critical repairs that will bring the instrument back to working order. For example, if I needed a part that I don't have, I would try to use similar materials to fabricate a temporary solution until I can get the correct part.
Consider a scenario where the workshop is busy and you have an instrument that requires immediate attention. What would you do?
How to Answer
- 1
Assess the urgency of the instrument's issue compared to other tasks.
- 2
Communicate with your supervisor or team about the situation.
- 3
Prioritize the immediate repair if it's critical for a performance or event.
- 4
Use available resources efficiently to minimize wait times.
- 5
Keep detailed notes of your actions for follow-up work if needed.
Example Answers
I would quickly evaluate the issue's urgency and determine if it can be postponed or if it needs immediate action. I would then inform my supervisor and prioritize the repair accordingly, ensuring any other tasks are delegated if necessary.
You have several instruments needing repairs but limited time. How would you determine which to address first?
How to Answer
- 1
Assess the urgency of each repair based on instrument usage.
- 2
Prioritize repairs that affect critical functions or clients directly.
- 3
Consider the complexity of repairs and estimate time needed for each.
- 4
Evaluate which instruments can be quickly fixed and returned to service.
- 5
Communicate with stakeholders to understand any pressing needs.
Example Answers
I would first check which instruments are most urgently needed, focusing on those used for upcoming performances. Then I would prioritize simpler fixes that can quickly get those instruments back in use.
Don't Just Read Instrument Repair Technician Questions - Practice Answering Them!
Reading helps, but actual practice is what gets you hired. Our AI feedback system helps you improve your Instrument Repair Technician interview answers in real-time.
Personalized feedback
Unlimited practice
Used by hundreds of successful candidates
Instrument Repair Technician Position Details
Recommended Job Boards
These job boards are ranked by relevance for this position.
Related Positions
- Stringed Instrument Repairer
- Violin Repairer
- Guitar Repairer
- Piano Technician
- Guitar Technician
- Violin Mechanic
- Piano Mechanic
- Piano Tuner
- Piano Regulator
- Accordion Tuner
Similar positions you might be interested in.
Ace Your Next Interview!
Practice with AI feedback & get hired faster
Personalized feedback
Used by hundreds of successful candidates
Ace Your Next Interview!
Practice with AI feedback & get hired faster
Personalized feedback
Used by hundreds of successful candidates