Top 32 Label Remover Interview Questions and Answers [Updated 2025]
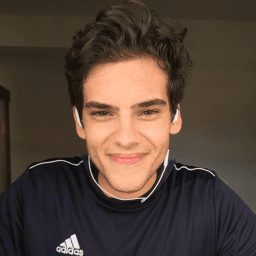
Andre Mendes
•
March 30, 2025
Preparing for a label remover interview? This blog post is your ultimate guide, offering a curated selection of the most common interview questions for this role. Dive in to discover insightful example answers and practical tips on how to respond effectively, ensuring you leave a lasting impression. Equip yourself with the knowledge to confidently tackle any question that comes your way.
Download Label Remover Interview Questions in PDF
To make your preparation even more convenient, we've compiled all these top Label Removerinterview questions and answers into a handy PDF.
Click the button below to download the PDF and have easy access to these essential questions anytime, anywhere:
List of Label Remover Interview Questions
Behavioral Interview Questions
Can you describe a time when you had to quickly adjust to a change in a labeling process?
How to Answer
- 1
Think of a specific instance where a process changed unexpectedly.
- 2
Explain how you assessed the situation quickly.
- 3
Describe the steps you took to adapt.
- 4
Highlight any skills you used, such as problem-solving or communication.
- 5
Conclude with the positive outcome of your adjustment.
Example Answers
In my previous role, we switched to a new software for labeling mid-project. I quickly learned the new system by accessing the tutorials provided and sought clarification from a colleague who was familiar with it. I then organized a brief team meeting to share my insights and help others adapt, which resulted in us meeting our deadlines smoothly.
Tell me about a time you had to collaborate with a team to complete a labeling project successfully.
How to Answer
- 1
Choose a specific project where teamwork was key.
- 2
Highlight your role and contributions in the project.
- 3
Emphasize communication and how challenges were addressed.
- 4
Mention the positive outcome and any metrics if possible.
- 5
Keep the example concise and relevant to labeling.
Example Answers
In my previous job, we had a tight deadline to label images for a new product catalog. I organized a meeting to divide tasks among the team and ensured everyone knew their responsibilities. We faced issues with inconsistent labeling standards, so I created a shared document outlining the guidelines. In the end, we completed the project two days early, and the catalog received positive feedback for its accuracy.
Don't Just Read Label Remover Questions - Practice Answering Them!
Reading helps, but actual practice is what gets you hired. Our AI feedback system helps you improve your Label Remover interview answers in real-time.
Personalized feedback
Unlimited practice
Used by hundreds of successful candidates
Describe a situation where you faced a challenge while removing a label that required innovative thinking.
How to Answer
- 1
Identify a specific challenge you faced while label removing.
- 2
Highlight the innovative approach you took to overcome it.
- 3
Explain the results of your actions and what you learned.
- 4
Use the STAR method: Situation, Task, Action, Result.
- 5
Keep your response concise and focused on the problem-solving aspect.
Example Answers
In my previous job, I needed to remove a stubborn price label from a glass surface. The challenge was that the typical adhesive removers left a residue. I innovatively used a mixture of vinegar and baking soda, which effectively dissolved the adhesive without damaging the glass. The result was a clean surface that impressed my manager, and I shared this method with the team.
How have you managed your time effectively when faced with tight deadlines in a labeling task?
How to Answer
- 1
Prioritize tasks based on deadlines and complexity
- 2
Break the labeling task into smaller, manageable chunks
- 3
Set specific time limits for each chunk to maintain focus
- 4
Use tools or software to automate repetitive tasks
- 5
Communicate with team members to distribute workload effectively
Example Answers
I prioritize my tasks by sorting the labels needed by urgency, and then I break the work into smaller sections. For example, I set 30 minutes for the most critical part and then assess my progress before moving on to the next set.
Can you give an example of a time you had a disagreement with a colleague about labeling standards, and how you resolved it?
How to Answer
- 1
Select a specific incident that highlights your communication skills.
- 2
Show how you listened to the other person's perspective.
- 3
Explain the steps you took to find common ground.
- 4
Discuss the end result and any improvements made.
- 5
Keep the focus on collaboration rather than conflict.
Example Answers
In my previous role, I disagreed with a colleague about the placement of safety labels on equipment. I listened to their rationale and shared my concerns. We decided to test both placements and gather feedback. Ultimately, we found a hybrid solution that satisfied both our standards and improved visibility for users.
Describe a time when you took the initiative to improve the labeling or removal process.
How to Answer
- 1
Think of a specific situation where you identified an issue.
- 2
Explain the steps you took to address that issue.
- 3
Mention any tools or methods you used.
- 4
Highlight the results of your actions.
- 5
Focus on how your initiative benefited the team or process.
Example Answers
In my previous role, I noticed that our labeling process was slow and prone to errors due to manual entries. I proposed introducing a barcode system to automate the labeling. After researching and presenting my findings, we implemented the system, which reduced errors by 40% and sped up the process by 30%.
How do you keep updated with new labeling technologies or methods?
How to Answer
- 1
Follow industry blogs and websites related to labeling technology.
- 2
Attend relevant workshops and seminars to learn about new methods.
- 3
Engage in online forums and communities focused on labeling innovations.
- 4
Subscribe to newsletters from packaging and labeling associations.
- 5
Participate in online courses related to labeling advancements.
Example Answers
I follow several industry blogs that discuss the latest in labeling technologies, and I regularly attend workshops to stay hands-on with new methods.
Can you provide an example of how you've managed a customer's expectations regarding label removal?
How to Answer
- 1
Understand the customer's needs and concerns before the discussion.
- 2
Set a clear timeline for the label removal process.
- 3
Communicate the limitations or challenges that may arise during the process.
- 4
Provide regular updates as the label removal progresses.
- 5
Ensure to confirm customer satisfaction after the label removal is completed.
Example Answers
In my previous role, a customer wanted a label removed quickly. I first asked about their timeline and explained the typical 2-day process. I kept them updated during the removal, and they were pleased with the results.
Tell me about a time you received constructive feedback on your work related to label removal and how you responded.
How to Answer
- 1
Choose a specific example where you received feedback on label removal.
- 2
Explain the context of the feedback and what you learned from it.
- 3
Describe the actions you took to address the feedback.
- 4
Highlight the positive outcome that resulted from your changes.
- 5
Keep the focus on your growth and willingness to improve.
Example Answers
In my previous role, I was tasked with removing labels from products efficiently. I received feedback that my technique was leaving residue on some items. I took this seriously, researched better methods, and practiced until I improved my technique. My new approach reduced residue significantly, which pleased my team and improved our quality ratings.
Don't Just Read Label Remover Questions - Practice Answering Them!
Reading helps, but actual practice is what gets you hired. Our AI feedback system helps you improve your Label Remover interview answers in real-time.
Personalized feedback
Unlimited practice
Used by hundreds of successful candidates
Can you describe a time when you went above and beyond in your role as a label remover?
How to Answer
- 1
Think of a specific situation where you exceeded expectations.
- 2
Focus on the impact of your actions on the team or the process.
- 3
Use the STAR method: Situation, Task, Action, Result.
- 4
Highlight any skills or qualities you demonstrated.
- 5
Keep it concise and relevant to the label remover position.
Example Answers
In my last job, we had a large shipment with labels that needed removal quickly. The team was behind schedule, so I volunteered to stay late and help everyone finish ahead of deadline. As a result, we improved our efficiency and avoided penalties for late deliveries.
Technical Interview Questions
What tools and technologies do you typically use for label removal, and how proficient are you with them?
How to Answer
- 1
Identify the main tools you use for label removal like chemical solvents or heat guns
- 2
Mention any software used for digital label removal or design
- 3
Discuss your proficiency level with each tool: beginner, intermediate, or expert
- 4
Include any relevant experiences or projects where you used these tools
- 5
Be prepared to explain your choice of tools and their effectiveness
Example Answers
I typically use chemical solvents like acetone and heat guns for physical label removal, and I consider myself at an intermediate proficiency with these tools. In my last job, I successfully removed labels from various surfaces, ensuring no residue was left behind.
Explain the steps you follow when preparing an item for label removal.
How to Answer
- 1
Identify the type of label and material to determine the best removal method.
- 2
Carefully assess the item surface to avoid damage during label removal.
- 3
Use appropriate tools such as a heat gun or adhesive remover for effective label removal.
- 4
Apply the chosen method gradually, ensuring not to rush the process.
- 5
Clean the surface thoroughly after label removal to remove any residue.
Example Answers
First, I identify the type of label and material. Then, I assess the item's surface to plan the safest removal method. I usually use a heat gun to loosen the adhesive, carefully peeling the label away to prevent damage. Finally, I clean any residue left on the surface.
Don't Just Read Label Remover Questions - Practice Answering Them!
Reading helps, but actual practice is what gets you hired. Our AI feedback system helps you improve your Label Remover interview answers in real-time.
Personalized feedback
Unlimited practice
Used by hundreds of successful candidates
What safety precautions do you take when removing labels from products?
How to Answer
- 1
Always wear protective gloves to avoid skin irritation.
- 2
Use appropriate tools, like label removers or scrapers, to prevent injury.
- 3
Ensure proper ventilation if using solvents or adhesives.
- 4
Keep your workspace organized to avoid accidents.
- 5
Follow company safety protocols for handling products.
Example Answers
I always wear gloves to protect my skin while removing labels. I use a specialized label remover tool to avoid any cuts or injuries.
How do you determine the best method for removing labels from different types of surfaces or materials?
How to Answer
- 1
Identify the surface material: (plastic, glass, wood, etc.)
- 2
Assess label type: (paper, vinyl, adhesive strength)
- 3
Choose a suitable removal method: (heat, solvents, scraping)
- 4
Test on a small area first to avoid damage
- 5
Follow up with cleaning to remove any residue
Example Answers
First, I check the surface material, whether it's plastic or glass. Then, I determine the label type and its adhesive strength. For stubborn labels, I might use heat or a solvent like rubbing alcohol. I always test in a small area to avoid damage, and finish by cleaning the surface.
What quality control measures do you implement to ensure labels are removed satisfactorily?
How to Answer
- 1
Clearly define the steps in your label removal process.
- 2
Explain how you check for residue or damage after removal.
- 3
Mention any tools or techniques you use for verifying successful label removal.
- 4
Describe how you train staff or ensure consistency in the process.
- 5
Highlight the importance of feedback and continuous improvement.
Example Answers
I follow a structured process where I first remove the label, then inspect the surface for any residue. I use a solvent for stubborn labels and a scraper for any excess. After removal, I inspect the area under bright light to ensure it’s clean before proceeding.
How do you keep track of labeling operations and the items you work on?
How to Answer
- 1
Use a structured system like spreadsheets or project management tools to log each operation.
- 2
Update the record in real-time as you label items to avoid confusion.
- 3
Include details such as item ID, timestamp, and any notes on the labeling process.
- 4
Regularly review and audit your records to ensure accuracy and completeness.
- 5
Communicate with your team about any updates or changes in labeling operations.
Example Answers
I maintain a detailed spreadsheet where I log each labeling operation with the item ID and the date. I update it as soon as I finish an item to keep everything current.
What common issues do you encounter with label adhesives, and how do you resolve them?
How to Answer
- 1
Identify specific adhesive problems such as poor adhesion or residue left on surfaces.
- 2
Discuss the impact of environmental factors like temperature and humidity on adhesive performance.
- 3
Explain techniques for removing labels without damaging products.
- 4
Mention the importance of testing adhesives on different surfaces before full implementation.
- 5
Highlight any tools or products you use for resolving adhesive issues.
Example Answers
One common issue is adhesive residue left after label removal. I resolve this by using a solvent designed for adhesive removal, which cleans the surface without damaging it. I also ensure to test the solvent on a small area first.
How do you measure the efficiency of your label removal processes?
How to Answer
- 1
Define key performance indicators for the removal process, such as time taken and accuracy.
- 2
Collect data on the number of successful vs unsuccessful removals.
- 3
Evaluate the time efficiency by timing each removal and comparing against benchmarks.
- 4
Implement feedback loops to gather input on the effectiveness of label removal.
- 5
Regularly review and adjust the process based on collected data.
Example Answers
I measure efficiency by tracking the average time it takes to remove labels and the success rate of removals. I compare these metrics against set benchmarks to identify areas for improvement.
What steps do you take to ensure that an item is clean and undamaged after label removal?
How to Answer
- 1
Inspect the item carefully before starting the label removal.
- 2
Use the right tools for label removal to avoid damage.
- 3
Remove labels slowly and steadily to reduce residue and damage risk.
- 4
Clean the area where the label was placed with appropriate cleaners.
- 5
Conduct a final check to ensure the item is clean and free from damage.
Example Answers
I always start by inspecting the item for any existing damage. Then, I use a heat gun or a plastic scraper to carefully remove the label, ensuring I go slowly. After that, I clean the surface with a suitable cleaner to remove any residue, and finally, I inspect the item again to confirm it's in perfect condition.
What types of labels have you worked with, and how do their removal processes differ?
How to Answer
- 1
Identify specific types of labels you have used, like adhesive, fabric, or price tags.
- 2
Explain different removal techniques for each label type, focusing on effectiveness and safety.
- 3
Mention any tools or chemicals that assist in label removal.
- 4
Share any personal experiences that highlight your expertise in this area.
- 5
Keep your answer structured to demonstrate your knowledge clearly.
Example Answers
I have worked with adhesive labels, such as those on packaging, which I typically remove using a heat gun to soften the glue. For fabric labels, I prefer to use a seam ripper to avoid damaging the material.
Don't Just Read Label Remover Questions - Practice Answering Them!
Reading helps, but actual practice is what gets you hired. Our AI feedback system helps you improve your Label Remover interview answers in real-time.
Personalized feedback
Unlimited practice
Used by hundreds of successful candidates
How do you document the label removal process for quality assurance purposes?
How to Answer
- 1
Outline each step of the label removal process clearly.
- 2
Include details such as materials used and safety precautions.
- 3
Record observations about the label's condition and adhesive residue.
- 4
Use photos or diagrams to illustrate before and after states.
- 5
Create a checklist to ensure consistency and completeness.
Example Answers
I document the label removal process by creating a step-by-step outline that includes the tools used, safety measures taken, and any issues encountered. I also take photos before and after the removal to provide a visual record.
Situational Interview Questions
If you encounter a product with multiple labels of differing removal difficulties, how would you prioritize which to remove first?
How to Answer
- 1
Assess the removal difficulty of each label immediately.
- 2
Remove labels that obscure important information first.
- 3
Consider the type of adhesive and potential damage to the product.
- 4
Plan to remove labels in a systematic way to avoid confusion.
- 5
Ensure the product remains visually appealing after label removal.
Example Answers
I would first remove the label that covers essential product information as it is crucial for clarity. Then, I would tackle the easiest label to remove, ensuring I minimize damage to the product.
Imagine you have a high volume of items to process with a strict deadline. How would you plan your workflow?
How to Answer
- 1
Prioritize tasks based on urgency and importance.
- 2
Break down the work into manageable chunks.
- 3
Set specific time limits for each chunk to maintain pace.
- 4
Utilize any available tools or technology to increase efficiency.
- 5
Regularly check progress and adjust the plan if necessary.
Example Answers
I would start by listing all items to be processed and categorize them by urgency. Then, I would break them into batches, setting timed milestones for each. I'll use our processing tools to streamline the workflow and frequently check my progress to ensure I meet the deadline.
Don't Just Read Label Remover Questions - Practice Answering Them!
Reading helps, but actual practice is what gets you hired. Our AI feedback system helps you improve your Label Remover interview answers in real-time.
Personalized feedback
Unlimited practice
Used by hundreds of successful candidates
If you find that a label is glued so securely that it may damage the product upon removal, what steps would you take?
How to Answer
- 1
Assess the situation to determine the risk of damage to the product.
- 2
Try a gentle approach using heat or steam to loosen the adhesive.
- 3
Consider using adhesive removers that are safe for the product material.
- 4
If damage is likely, consult with a supervisor for guidance on handling.
- 5
Document the situation in case of needed follow-up or quality control.
Example Answers
First, I would assess the glue's strength and the product's material to prevent any damage. If safe, I'd apply heat to loosen the label. If it still won't budge, I'd look for a suitable adhesive remover. If I believe removal could harm the product, I'd reach out to my supervisor for advice.
If a customer complains about an item that was improperly labeled or had remnants of a label, how would you handle the situation?
How to Answer
- 1
Listen to the customer's concern attentively
- 2
Apologize sincerely for the inconvenience caused
- 3
Investigate the issue promptly and determine the cause
- 4
Offer a solution such as a replacement or refund
- 5
Follow up with the customer to ensure satisfaction
Example Answers
I would first listen carefully to the customer's complaint and apologize for any inconvenience. Then, I would verify the issue and see if it is a recurring problem before offering them a replacement item or a full refund. Finally, I would check back with them to confirm they are satisfied with the resolution.
You believe a certain label removal method is more effective than what your supervisor suggests. How would you communicate your viewpoint?
How to Answer
- 1
Be respectful and acknowledge your supervisor's experience.
- 2
Present clear evidence or data supporting your method.
- 3
Suggest a trial or comparison of both methods to demonstrate effectiveness.
- 4
Ask for your supervisor's feedback and opinions on your approach.
- 5
Keep the conversation focused on improving results for the team.
Example Answers
I appreciate your method and the experience behind it. However, I believe my approach has some advantages, particularly in efficiency. I have data from previous projects showing a 20% faster removal time. Would you be open to a side-by-side test to compare the two methods?
A teammate is struggling with label removal techniques and impacting the team's productivity. What action would you take?
How to Answer
- 1
Assess the specific difficulties the teammate is facing with label removal techniques.
- 2
Offer to provide a one-on-one training session to go over the techniques step-by-step.
- 3
Encourage open communication and create a safe space for them to ask questions.
- 4
Share resources such as videos or documentation that clarify the techniques.
- 5
Suggest a pair-working approach where you can assist them directly in practice.
Example Answers
I would first talk to my teammate to understand exactly what issues they are facing with the label removal techniques. Then, I would offer to train them on those techniques in a one-on-one session, ensuring they feel comfortable asking questions.
If you notice that safety procedures are not being followed by a coworker during label removal, what do you do?
How to Answer
- 1
Assess the situation quickly and ensure your own safety first.
- 2
Approach the coworker calmly and explain the importance of following safety procedures.
- 3
Suggest alternative methods or remind them of the correct process.
- 4
If the behavior continues, report the incident to a supervisor or safety officer.
- 5
Document the interaction if necessary for future reference.
Example Answers
I would first ensure that I'm safe and then approach my coworker calmly to discuss the safety procedures they are overlooking. I'd suggest the correct methods and emphasize the importance of safety for all of us.
If you're given limited materials to remove labels, how would you allocate these resources effectively?
How to Answer
- 1
Identify the most critical labels to remove first based on impact.
- 2
Evaluate the efficiency of each material for label removal tasks.
- 3
Consider the time constraints and prioritize tasks accordingly.
- 4
Utilize a methodical approach to maximize output with limited resources.
- 5
Collaborate with the team to share insights on resource usage.
Example Answers
I would first assess which labels, when removed, would have the highest impact on operations. After that, I would choose the most effective removal method for each label type based on the materials at hand. Time management is key, so I would prioritize the tasks that can be completed with minimal resources in the shortest time.
If you were tasked with redesigning the label removal workflow, what aspects would you focus on improving?
How to Answer
- 1
Identify bottlenecks in the current workflow and address them.
- 2
Consider the technology and tools that could enhance efficiency.
- 3
Engage with team members for their input on pain points.
- 4
Streamline communication between departments involved.
- 5
Implement a tracking system for continuous improvement.
Example Answers
I would first analyze the current workflow to pinpoint bottlenecks, such as delays in label removal due to manual processes. Then, I would explore automation tools that could speed up these tasks. Additionally, I think involving team feedback would help identify frequent issues and improve overall efficiency.
If you were asked to train a new hire on label removal techniques, what key points would you emphasize?
How to Answer
- 1
Explain the importance of using the right tools for different surfaces.
- 2
Demonstrate proper techniques to avoid damaging products.
- 3
Emphasize safety protocols when handling solvents or tools.
- 4
Teach how to assess adhesive types and their removal methods.
- 5
Encourage practice and feedback for skill improvement.
Example Answers
I would start by showing them the necessary tools like scrapers and solvents, then demonstrate how to use them properly to avoid product damage. Safety is crucial, so I'd highlight the importance of wearing gloves when handling chemicals. Assessing the adhesive type is also vital; different adhesives require different techniques.
Don't Just Read Label Remover Questions - Practice Answering Them!
Reading helps, but actual practice is what gets you hired. Our AI feedback system helps you improve your Label Remover interview answers in real-time.
Personalized feedback
Unlimited practice
Used by hundreds of successful candidates
Label Remover Position Details
Related Positions
- Resin Remover
- Gum Remover
- Varnish Remover
- Paper Stripper
- Screw Remover
- Leather Whitener
- Log Washer
- Deblocker
- Furniture Cleaner
- Hand Stripper
Similar positions you might be interested in.
Ace Your Next Interview!
Practice with AI feedback & get hired faster
Personalized feedback
Used by hundreds of successful candidates
Ace Your Next Interview!
Practice with AI feedback & get hired faster
Personalized feedback
Used by hundreds of successful candidates