Top 30 Line Mechanic Interview Questions and Answers [Updated 2025]
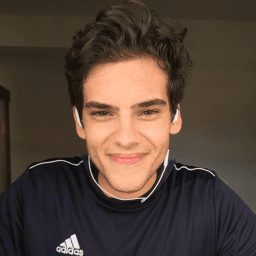
Andre Mendes
•
March 30, 2025
Preparing for a Line Mechanic interview can be daunting, but with the right resources, you can approach it with confidence. In this post, we’ve compiled the most common interview questions specific to the Line Mechanic role, complete with example answers and effective response strategies. Whether you're a seasoned professional or a newcomer to the field, these insights will help you make a strong impression and land the job.
Download Line Mechanic Interview Questions in PDF
To make your preparation even more convenient, we've compiled all these top Line Mechanicinterview questions and answers into a handy PDF.
Click the button below to download the PDF and have easy access to these essential questions anytime, anywhere:
List of Line Mechanic Interview Questions
Behavioral Interview Questions
Can you describe a time when you encountered a significant mechanical failure? How did you troubleshoot and resolve the issue?
How to Answer
- 1
Start with a brief description of the mechanical failure and its impact.
- 2
Explain the steps you took to diagnose the problem.
- 3
Discuss the tools or methods you used for troubleshooting.
- 4
Describe how you implemented the solution effectively.
- 5
Conclude with the outcome and what you learned from the experience.
Example Answers
During a routine inspection, I discovered a hydraulic leak in a system that shut down operations. I quickly isolated the system and checked for leaks using dye penetrant. I found a damaged seal, replaced it, and tested the system for functionality. This resolved the issue and allowed us to resume work without further delays.
Describe a situation where you worked as part of a team to accomplish a maintenance task. What was your role, and how did the team perform?
How to Answer
- 1
Think of a specific maintenance project you worked on with a team
- 2
Briefly describe the task and your specific role in it
- 3
Explain how the team collaborated and communicated effectively
- 4
Mention any obstacles faced and how the team overcame them
- 5
Conclude with the outcome of the task and what you learned
Example Answers
In my last job, we had a major maintenance task to overhaul the electrical systems in our facility. I was responsible for coordinating the wiring team. We held daily briefings to discuss progress and any issues. We faced challenges with outdated schematics, but by pooling our resources and expertise, we found solutions and completed the task ahead of schedule, improving our downtime rates significantly.
Don't Just Read Line Mechanic Questions - Practice Answering Them!
Reading helps, but actual practice is what gets you hired. Our AI feedback system helps you improve your Line Mechanic interview answers in real-time.
Personalized feedback
Unlimited practice
Used by hundreds of successful candidates
Tell me about a time when you had to adapt to a sudden change in work plans or priorities. How did you handle it?
How to Answer
- 1
Describe the situation clearly and succinctly.
- 2
Explain the sudden change and its impact on your work.
- 3
Detail the steps you took to adapt to the new situation.
- 4
Highlight any positive outcomes from your adaptability.
- 5
Keep the focus on your skills and how you remained effective.
Example Answers
At my previous job, a supplier suddenly delayed a shipment we were relying on. I quickly reassessed our material needs, communicated with my team about the change, and sourced alternative local suppliers. We managed to keep the project on schedule, and my adaptability helped maintain client satisfaction.
Have you ever taken the lead on a repair project? What challenges did you face and how did you motivate others?
How to Answer
- 1
Provide a specific example of a repair project you led.
- 2
Describe the challenges clearly and how they impacted the project.
- 3
Explain the methods you used to keep the team motivated.
- 4
Highlight any successful outcomes from your leadership.
- 5
Be concise and focus on your personal contributions.
Example Answers
In my last job, I led a team to repair a malfunctioning power transformer. We faced time constraints and a lack of spare parts. I motivated the team by organizing daily check-ins and breaking down tasks into manageable parts. We completed the project on time and restored operations ahead of schedule.
Describe a time when your attention to detail helped prevent a significant issue in your work.
How to Answer
- 1
Think of a specific incident where your detail-oriented approach made a difference.
- 2
Use the STAR method: Situation, Task, Action, Result.
- 3
Quantify the result if possible to show impact.
- 4
Focus on what you did to ensure everything was correct.
- 5
Relate it back to skills relevant to a Line Mechanic position.
Example Answers
In a previous role, I was responsible for inspecting electrical systems. During one inspection, I noticed a minor frayed wire that others had missed. I immediately flagged it for replacement, preventing a potential short circuit that could have caused a blackout. My attention to detail ensured the safety of the entire system.
Give an example of how you manage stress when working under tight deadlines.
How to Answer
- 1
Identify specific techniques you use to handle stress.
- 2
Provide a relevant example from your experience.
- 3
Explain how these techniques improve your work effectiveness.
- 4
Emphasize staying organized and prioritizing tasks.
- 5
Mention any tools or methods that help you manage your time.
Example Answers
When facing tight deadlines, I prioritize my tasks using a checklist. For instance, during a recent project, sorting tasks by urgency helped me focus on what needed immediate attention. This kept me organized and reduced my stress.
Tell me about a time you had to communicate technical information to a non-technical team member.
How to Answer
- 1
Identify a specific instance when you communicated technical details.
- 2
Explain the technical information in simple terms.
- 3
Focus on the outcome and the understanding achieved by the non-technical member.
- 4
Highlight the importance of communication skills in that scenario.
- 5
Reflect on what you learned from the experience.
Example Answers
In a project, I explained our wiring setup to a project manager by using analogies related to everyday items. This helped her understand how power flows and its impact on the schedule. As a result, we improved coordination in timeline adjustments.
Describe a time when you took the initiative to fix a problem before it escalated.
How to Answer
- 1
Think of a specific situation where you noticed a problem early.
- 2
Explain what actions you took to address the issue immediately.
- 3
Highlight the impact of your intervention and the results achieved.
- 4
Use the STAR method: Situation, Task, Action, Result.
- 5
Keep it relevant to line mechanic work, like equipment or safety issues.
Example Answers
In my last job, I noticed that a conveyor belt was making unusual noises, which indicated potential wear. I took the initiative to inspect the belt and found that a bearing was about to fail. I replaced the bearing before it could cause a full shutdown. As a result, we avoided costly downtime and kept production on schedule.
Don't Just Read Line Mechanic Questions - Practice Answering Them!
Reading helps, but actual practice is what gets you hired. Our AI feedback system helps you improve your Line Mechanic interview answers in real-time.
Personalized feedback
Unlimited practice
Used by hundreds of successful candidates
Technical Interview Questions
What types of mechanical systems are you most familiar with, and can you explain how they operate?
How to Answer
- 1
Identify mechanical systems relevant to the job.
- 2
Explain each system's basic components and function.
- 3
Use specific examples from your experience.
- 4
Relate the systems to the job requirements.
- 5
Be clear and concise in your explanations.
Example Answers
I am most familiar with hydraulic and pneumatic systems. A hydraulic system uses fluid to transmit power, and it's commonly used in equipment like forklifts. Pneumatic systems, on the other hand, use compressed air to operate tools and machinery, like air brakes in transportation.
Can you walk us through your process for routine maintenance on machinery?
How to Answer
- 1
Start by outlining the importance of safety protocols before beginning maintenance.
- 2
Describe specific tasks such as inspecting and cleaning machinery components.
- 3
Mention checking fluid levels and replacing filters as part of routine tasks.
- 4
Include how you document maintenance activities for future reference.
- 5
Conclude with how you ensure the machinery is tested and functioning properly post-maintenance.
Example Answers
I start each maintenance session by ensuring all safety protocols are in place. Then, I inspect and clean key components like belts and bearings, check fluid levels, replace filters, and document all activities. Finally, I run tests to confirm the machinery operates efficiently before finishing up.
Don't Just Read Line Mechanic Questions - Practice Answering Them!
Reading helps, but actual practice is what gets you hired. Our AI feedback system helps you improve your Line Mechanic interview answers in real-time.
Personalized feedback
Unlimited practice
Used by hundreds of successful candidates
What types of tools do you prefer when performing mechanical repairs, and why?
How to Answer
- 1
Mention specific tools you are familiar with and their uses.
- 2
Explain why you prefer these tools based on experience or efficiency.
- 3
Include any brand preferences if relevant and why.
- 4
Discuss how these tools improve safety and quality of work.
- 5
Convey adaptability to use various tools depending on the job.
Example Answers
I prefer using impact wrenches for fastener removal and installation because they save time and reduce physical strain. I also like using torque wrenches to ensure proper tightness for safety.
How do you approach diagnosing a mechanical fault? Can you give a specific example?
How to Answer
- 1
Start by gathering information about the issue from the user or system logs.
- 2
Inspect the affected machinery for obvious signs of damage or wear.
- 3
Isolate the fault by testing individual components or systems.
- 4
Use diagnostic tools to measure parameters like voltage, pressure, or operational speeds.
- 5
Document your findings and the steps taken for future reference.
Example Answers
I start by asking the operator specific questions about the fault they've encountered. For instance, if a conveyor belt is not running, I’ll check for power supply issues, then inspect for any blockages or worn components. Last month, I found that a faulty relay was preventing the belt from starting, and replacing it resolved the issue.
Explain the basic principles of hydraulic systems and how you have worked with them in the past.
How to Answer
- 1
Start by defining hydraulic systems as systems that use fluid to transmit power.
- 2
Explain Pascal's principle and how it relates to the operation of hydraulic systems.
- 3
Discuss components like pumps, actuators, and fluid reservoirs.
- 4
Share a personal experience where you operated or repaired hydraulic systems.
- 5
Highlight any specific tasks or troubleshooting methods you employed.
Example Answers
Hydraulic systems use incompressible fluid to transmit force. Pascal's principle states that pressure applied to an enclosed fluid is transmitted undiminished. I have worked with hydraulic pumps and cylinders when maintaining forklifts, ensuring proper fluid levels and troubleshooting leaks.
What experience do you have with troubleshooting electrical systems in production equipment?
How to Answer
- 1
Describe specific equipment you have worked on.
- 2
Mention methods you use for troubleshooting.
- 3
Highlight any relevant certifications or training.
- 4
Give examples of successful troubleshooting experiences.
- 5
Discuss teamwork and communication in resolving issues.
Example Answers
In my previous role, I worked on conveyor systems where I identified and fixed electrical faults using multimeters and visual inspections. I completed a course on industrial electrical systems, which helped me understand the wiring and components better.
How do you prioritize and manage maintenance schedules for multiple pieces of equipment?
How to Answer
- 1
Assess the criticality of each equipment to operations
- 2
Consider manufacturer recommendations for maintenance intervals
- 3
Use a software tool or system to organize and track maintenance tasks
- 4
Communicate with team members to understand equipment usage patterns
- 5
Review and adjust priorities regularly based on performance data
Example Answers
I prioritize equipment based on its impact on production. For instance, if a machine is essential for daily operations, I schedule its maintenance first while ensuring I comply with the manufacturer's recommendations.
What steps do you follow to install new machinery, and what challenges have you faced during installations?
How to Answer
- 1
Start by outlining the basic steps you take for installations.
- 2
Mention any preparation or planning you do before starting.
- 3
Discuss specific challenges you encountered during past installations.
- 4
Highlight how you resolved any issues faced during the installation.
- 5
Conclude with what you learned from the experience.
Example Answers
First, I review the machinery's installation manual and plan out the workspace. I ensure all tools are ready and the area is safe. During a previous installation, I faced a challenge with a misalignment of parts, which I resolved by consulting the manual and using shims to adjust the positioning.
What methods do you use to ensure that your work meets quality standards?
How to Answer
- 1
Mention specific quality control methods you use regularly
- 2
Highlight the importance of following safety and regulatory standards
- 3
Discuss how you document your work for accountability
- 4
Explain how you perform and respond to regular inspections and feedback
- 5
Provide an example of a successful quality assurance strategy you've implemented
Example Answers
I use a checklist for every job to ensure all tasks meet quality standards. I also follow safety guidelines strictly and keep detailed records of my work for future reference.
What is your approach for troubleshooting mechanical issues, and what resources do you utilize?
How to Answer
- 1
Start with a clear understanding of the problem through observation.
- 2
Use a systematic approach, such as defining the symptoms and isolating the issue.
- 3
Consult technical manuals or schematics for the equipment.
- 4
Utilize diagnostic tools to gather data on performance.
- 5
Collaborate with team members for additional insights and troubleshooting ideas.
Example Answers
I begin by carefully observing the mechanical issue, noting any unusual sounds or performance. Then, I refer to the equipment manual to check for common problems and specific troubleshooting steps.
Don't Just Read Line Mechanic Questions - Practice Answering Them!
Reading helps, but actual practice is what gets you hired. Our AI feedback system helps you improve your Line Mechanic interview answers in real-time.
Personalized feedback
Unlimited practice
Used by hundreds of successful candidates
What is your understanding of preventive maintenance, and how do you implement it in your work?
How to Answer
- 1
Define preventive maintenance clearly.
- 2
Mention specific tasks you perform regularly.
- 3
Discuss how you track and schedule maintenance.
- 4
Provide an example of a successful preventive maintenance case.
- 5
Emphasize teamwork and communication in your maintenance processes.
Example Answers
Preventive maintenance involves regular inspections and servicing to prevent equipment failure. In my work, I check and lubricate machinery weekly, ensure we replace worn parts before they fail, and maintain records of all maintenance tasks to schedule future work efficiently.
Situational Interview Questions
Imagine a key piece of machinery has broken down during a critical production period. What steps would you take to address the issue?
How to Answer
- 1
Assess the situation and identify specific failure points of the machinery.
- 2
Inform your supervisor and relevant team members about the breakdown immediately.
- 3
Gather necessary tools and parts required for repairs.
- 4
Prioritize safety and follow lockout/tagout procedures.
- 5
Document the issue and the steps taken to resolve it for future reference.
Example Answers
First, I would assess the issue to understand what part of the machinery has failed. Then, I would inform my supervisor and the team to make sure everyone is aware. After that, I would get the necessary tools and replacement parts to start repairs. Safety is my top priority, so I'd ensure the machinery is properly shut down following lockout procedures. Finally, I would document everything I did to fix the problem for future troubleshooting.
If you're in the middle of a repair and discover a secondary issue that could delay the project, how would you handle it?
How to Answer
- 1
Assess the severity of the secondary issue quickly.
- 2
Communicate the new issue to your supervisor or team immediately.
- 3
Re-evaluate the timeline and inform all stakeholders about potential delays.
- 4
Prioritize tasks to address the secondary issue effectively.
- 5
Document the issue and the steps taken to resolve it for future reference.
Example Answers
I would quickly assess how serious the secondary issue is, then inform my supervisor right away. After that, I'd discuss how it may affect the timeline and work with the team to prioritize resolving it to minimize delays.
Don't Just Read Line Mechanic Questions - Practice Answering Them!
Reading helps, but actual practice is what gets you hired. Our AI feedback system helps you improve your Line Mechanic interview answers in real-time.
Personalized feedback
Unlimited practice
Used by hundreds of successful candidates
You’re working on a team and there is a disagreement about how to approach a repair task. How would you resolve this?
How to Answer
- 1
Listen to each team member's perspective on the repair.
- 2
Keep the focus on the task and avoid personal conflicts.
- 3
Encourage collaboration to find a compromise or a mix of ideas.
- 4
Suggest discussing the pros and cons of each approach.
- 5
If needed, involve a supervisor or refer to established protocols.
Example Answers
I would start by listening to everyone's viewpoints to understand their reasoning. Then, I would suggest we discuss the merits of each approach and look for a solution that incorporates the best ideas from everyone.
You notice that a safety protocol is not being followed by a colleague. How do you approach the situation?
How to Answer
- 1
Speak to the colleague privately to avoid embarrassment.
- 2
Express concern for their safety and the team's safety.
- 3
Use specific examples of the protocol being ignored.
- 4
Suggest alternatives or solutions to follow the protocol.
- 5
If the issue persists, report it to a supervisor.
Example Answers
I would pull my colleague aside and mention that I noticed the safety protocol wasn't being followed. I'd explain that it’s important for everyone's safety and suggest we review the protocol together.
If you do not have all the necessary parts to complete a job, how would you manage the situation?
How to Answer
- 1
Assess what parts are missing and their impact on the job.
- 2
Prioritize tasks that can still be completed without the parts.
- 3
Communicate clearly with your supervisor or team about the situation.
- 4
Explore alternatives, such as borrowing parts from another job or sourcing them quickly.
- 5
Document the issue and the steps taken to resolve it for future reference.
Example Answers
I would first identify which parts are missing and if it's critical to the job. Then, I would see if any tasks can be progressed without the missing parts. After that, I would inform my supervisor about the situation and discuss potential solutions, like borrowing parts or ordering them quickly.
If machinery starts showing signs of wear, how would you determine whether to repair it or replace it?
How to Answer
- 1
Assess the severity and type of wear observed.
- 2
Evaluate the cost of repairs versus the cost of replacement.
- 3
Consider the age and reliability of the machine.
- 4
Analyze the impact on productivity during downtime.
- 5
Consult maintenance records and previous repair history.
Example Answers
I would first inspect the machine to understand the extent of the wear. If the repair costs are less than half the replacement cost, and the machine is not too old, I would choose to repair it.
You are asked to train a new apprentice. What key skills and knowledge would you focus on?
How to Answer
- 1
Highlight technical skills like safety protocols and equipment handling
- 2
Emphasize soft skills such as communication and teamwork
- 3
Discuss the importance of troubleshooting and problem-solving
- 4
Mention the need for knowledge of electrical systems and diagrams
- 5
Stress hands-on training and real-world experience
Example Answers
I would focus on safety protocols and proper equipment handling to ensure the apprentice understands the risks and safety measures. Additionally, I would emphasize communication skills for effective teamwork and the importance of troubleshooting techniques to solve issues.
How would you react if there was an equipment failure that posed a safety risk to the workers?
How to Answer
- 1
Assess the situation quickly and determine the extent of the risk
- 2
Immediately inform all affected personnel to evacuate the area
- 3
Use emergency protocols to shut down equipment safely if possible
- 4
Communicate clearly with supervisors and maintenance for further action
- 5
Document the incident and the steps taken for future reference
Example Answers
I would quickly assess the equipment and evaluate the risk level. Then, I would inform all workers to evacuate the area until it's safe. I would follow emergency protocols to shut down the equipment if possible, and notify my supervisor and maintenance team.
If you were collaborating with engineers on a machine upgrade, how would you ensure the repair team’s needs are met?
How to Answer
- 1
Communicate openly with the engineering team to understand the upgrade details.
- 2
Gather input from the repair team about their specific requirements and concerns.
- 3
Set up regular check-ins to keep everyone updated on progress and modifications.
- 4
Document all feedback and decisions to avoid misunderstandings.
- 5
Prioritize the repair team's feedback in the upgrade process to ensure functionality.
Example Answers
I would first arrange a meeting with the engineers to discuss the upgrade and gather details. After that, I would collect feedback from the repair team about any specific needs or concerns they have regarding the upgrade. Regular updates would ensure everyone is on the same page.
Line Mechanic Position Details
Recommended Job Boards
Lineman Central
jobs.linemancentral.comCareerBuilder
www.careerbuilder.com/jobs/line-mechanicZipRecruiter
www.ziprecruiter.com/Jobs/Line-MechanicThese job boards are ranked by relevance for this position.
Related Positions
Ace Your Next Interview!
Practice with AI feedback & get hired faster
Personalized feedback
Used by hundreds of successful candidates
Ace Your Next Interview!
Practice with AI feedback & get hired faster
Personalized feedback
Used by hundreds of successful candidates