Top 30 Line Puller Interview Questions and Answers [Updated 2025]
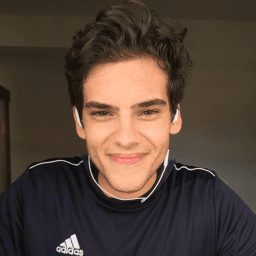
Andre Mendes
•
March 30, 2025
Navigating the competitive job market for a Line Puller position requires preparation and confidence. This blog post compiles the most common interview questions for this role, offering not only example answers but also insightful tips on how to tackle these questions effectively. Whether you're a seasoned professional or new to the field, equip yourself with the knowledge and strategies to ace your next interview.
Download Line Puller Interview Questions in PDF
To make your preparation even more convenient, we've compiled all these top Line Pullerinterview questions and answers into a handy PDF.
Click the button below to download the PDF and have easy access to these essential questions anytime, anywhere:
List of Line Puller Interview Questions
Technical Interview Questions
How do you calculate the required force and tension for pulling a specific type of line?
How to Answer
- 1
Identify the type of line and its materials.
- 2
Understand the load being pulled and its weight.
- 3
Consider friction factors and angles involved in the pull.
- 4
Use formulas: Tension = Load + Friction.
- 5
Always ensure safety margins in calculations.
Example Answers
To calculate the required force for pulling a line, I first identify the type of line and material, then assess the total weight of the load. For example, if I'm pulling a 1000 lb load on a nylon line, I consider friction, perhaps using Tension = Load + Friction to find the tension needed.
What experience do you have with line detection systems and how do they assist in line pulling?
How to Answer
- 1
Identify specific line detection systems you have used.
- 2
Explain your role and responsibilities in using these systems.
- 3
Describe how these systems improve accuracy and efficiency in line pulling.
- 4
Include any relevant technical skills associated with these systems.
- 5
Mention any training or certifications you have related to line detection.
Example Answers
I have worked with the XLR line detection system for over two years, where I was responsible for monitoring and calibrating the equipment. This system helps us accurately locate underground lines, reducing errors during pulling. My training in this system allowed me to quickly identify line locations and ensure safety during operations.
Don't Just Read Line Puller Questions - Practice Answering Them!
Reading helps, but actual practice is what gets you hired. Our AI feedback system helps you improve your Line Puller interview answers in real-time.
Personalized feedback
Unlimited practice
Used by hundreds of successful candidates
What types of line pulling equipment are you familiar with, and what maintenance do they require?
How to Answer
- 1
List specific types of line pulling equipment you have used
- 2
Mention key maintenance tasks for each equipment type
- 3
Highlight any safety inspections you perform
- 4
Discuss how to keep the equipment in good working condition
- 5
Share any relevant training or certifications related to the equipment
Example Answers
I am familiar with hydraulic winches and come-alongs. For hydraulic winches, I regularly check fluid levels and inspect hoses for wear. For come-alongs, I ensure that the cables are free of kinks and lubricate the moving parts regularly.
Can you explain the different techniques used for pulling lines and the situations in which each is preferable?
How to Answer
- 1
Identify common line pulling techniques like straight pull, differential pull, and mechanical advantage.
- 2
Explain the scenarios where each technique is best suited, such as weight of the load or environmental conditions.
- 3
Use specific terminology relevant to line pulling to show your expertise.
- 4
Mention safety considerations for each technique, such as load limits and securing lines.
- 5
Provide real-world examples or experiences that highlight your knowledge and skills.
Example Answers
One technique is the straight pull, which is ideal for light loads on level ground. For heavier loads or uneven surfaces, I recommend a differential pull as it distributes the weight more evenly. Mechanical advantage can be used in scenarios where space allows for it, such as using pulleys to pull a heavy line, which minimizes the effort needed.
What safety protocols do you follow when working with high-tension lines?
How to Answer
- 1
Always assess the environment before starting work.
- 2
Wear appropriate personal protective equipment like gloves and hard hats.
- 3
Use insulated tools to prevent electrical accidents.
- 4
Establish a safety perimeter and warn others about the operation.
- 5
Follow lockout/tagout procedures to ensure lines are de-energized.
Example Answers
I always ensure the area is safe and clear before beginning work on high-tension lines. I wear gloves and a hard hat for protection and use insulated tools to avoid any risk of shock.
What types of materials are suitable for line pulling and what are their strengths and weaknesses?
How to Answer
- 1
Identify common materials used in line pulling, such as steel cable, synthetic rope, and chain.
- 2
Discuss the tensile strength and flexibility of each material.
- 3
Mention environmental factors that may affect material suitability, like moisture and temperature.
- 4
Highlight safety considerations related to each material type.
- 5
Be concise and focus on practical applications or scenarios where each material excels.
Example Answers
Steel cable is strong and durable, making it great for heavy loads, but it can rust in wet conditions. Synthetic rope is lightweight and flexible, suitable for tight spaces, but it can be damaged by UV exposure.
What regulations and industry standards do you follow in line pulling operations?
How to Answer
- 1
Familiarize yourself with OSHA regulations related to line pulling and safety.
- 2
Mention specific industry standards like ASTM or IEEE that apply to your work.
- 3
Discuss the importance of following manufacturer guidelines for equipment used.
- 4
Emphasize the significance of safety protocols and risk assessments in operations.
- 5
Share experiences where adhering to standards ensured safety and efficiency.
Example Answers
In line pulling operations, I always adhere to OSHA regulations to ensure worker safety. I also follow ASTM standards for the materials we use, which helps maintain quality and reliability.
How do you test the integrity and strength of lines before pulling?
How to Answer
- 1
Inspect the line visually for any signs of wear or damage
- 2
Perform a tension test by applying a load gradually to check the line's response
- 3
Use a calibrated gauge to measure the line's tensile strength
- 4
Check for any knots, twists or tangles that could affect performance
- 5
Ensure proper connections and hardware are used to maintain system integrity
Example Answers
I start by visually inspecting the line for frays or wear before pulling. Then, I perform a gradual tension test to ensure it holds well under load. Finally, I use a gauge to confirm the tensile strength meets our requirements.
How do you assess the weight and load characteristics of different types of lines?
How to Answer
- 1
Understand the specifications of each line type including material and thickness
- 2
Use tools such as a load cell or scale for accurate weight measurement
- 3
Consider the application and environment where the line will be used
- 4
Check manufacturer guidelines for load limits and safe working loads
- 5
Perform a visual inspection for signs of wear or damage before use
Example Answers
I assess the weight and load characteristics by first understanding the material and thickness of the line. I then use a load cell to measure the weight and compare it with the manufacturer's specifications for safe working loads.
What are the best practices for maintaining and storing pulling ropes?
How to Answer
- 1
Inspect ropes regularly for wear and damage.
- 2
Clean pulling ropes with mild soap and water after use.
- 3
Store ropes in a cool, dry place away from sunlight.
- 4
Use proper knots and avoid overloading the rope to extend its life.
- 5
Coil ropes neatly to prevent kinks and tangles.
Example Answers
It is important to inspect pulling ropes regularly for any signs of wear or damage. Cleaning them after use and storing them in a dry place also helps prolong their lifespan.
Don't Just Read Line Puller Questions - Practice Answering Them!
Reading helps, but actual practice is what gets you hired. Our AI feedback system helps you improve your Line Puller interview answers in real-time.
Personalized feedback
Unlimited practice
Used by hundreds of successful candidates
What is your understanding of emergency response procedures when working on line pulling?
How to Answer
- 1
Know the emergency response plan specific to line pulling operations.
- 2
Identify locations of safety equipment like first aid kits and fire extinguishers.
- 3
Be aware of communication protocols during an emergency, including who to notify.
- 4
Understand the risks specific to line pulling and appropriate evacuation routes.
- 5
Practice situational awareness to quickly assess emergencies and react accordingly.
Example Answers
In line pulling, I understand that the emergency response plan includes immediate notification of a supervisor if an incident occurs, locating safety equipment, and ensuring everyone knows the evacuation routes to follow.
Behavioral Interview Questions
Can you describe a time when you had to work as part of a team to complete a line pulling project?
How to Answer
- 1
Start with a specific project context
- 2
Explain your role and responsibilities
- 3
Highlight teamwork and collaboration aspects
- 4
Mention challenges faced and how you overcame them
- 5
Conclude with the outcome and what you learned
Example Answers
In a recent project to install power lines, I worked with a team of five. My role was to coordinate with the team on the placement of the lines. We faced a challenge when one section was obstructed by trees, but together we devised a plan to reroute the line and communicated effectively to adjust our approach. The project was completed on time, and I learned the importance of clear communication in teamwork.
Tell me about a situation where you identified a safety risk while performing your duties. What did you do?
How to Answer
- 1
Start by briefly describing the situation and the specific safety risk you identified.
- 2
Explain the actions you took to address the risk and ensure safety.
- 3
Discuss the outcome and any long-term changes that resulted from your actions.
- 4
Use clear, direct language and avoid jargon if possible.
- 5
Focus on your proactive attitude and commitment to safety.
Example Answers
While working as a line puller, I noticed that some cables were frayed and posed a risk of breaking. I immediately reported it to my supervisor and recommended that the cables be replaced before proceeding with any lifting operations. The team replaced the cables, which prevented a potential accident and reinforced our safety protocols.
Don't Just Read Line Puller Questions - Practice Answering Them!
Reading helps, but actual practice is what gets you hired. Our AI feedback system helps you improve your Line Puller interview answers in real-time.
Personalized feedback
Unlimited practice
Used by hundreds of successful candidates
Describe a challenging problem you faced while pulling lines and what steps you took to overcome it.
How to Answer
- 1
Think of a specific incident related to line pulling
- 2
Explain the problem clearly and detail its impact
- 3
Outline the steps you took to solve the issue
- 4
Highlight any teamwork or communication involved
- 5
Conclude with what you learned from the experience
Example Answers
Once, while pulling a heavy line, we encountered a snag caused by debris. To overcome this, I communicated with my team to identify the exact location of the snag. We worked together to carefully remove the obstruction and realign the line, which allowed us to continue. This experience taught me the importance of quick teamwork under pressure.
Can you give an example of how you communicated effectively with your team during a line pulling operation?
How to Answer
- 1
Use specific terminology related to line pulling to show familiarity
- 2
Describe a situation where clear instructions were crucial
- 3
Include how you ensured everyone understood their role
- 4
Mention any tools or methods you used for communication
- 5
Highlight the outcome of your effective communication
Example Answers
During a line pulling operation, I clearly explained the steps we needed to follow and assigned specific tasks to each team member. I used hand signals to complement verbal instructions, ensuring we stayed in sync even in noisy conditions. This led to a successful and timely completion of the task without any safety issues.
Tell me about a time when you had to adapt to unexpected changes during a line pulling task.
How to Answer
- 1
Describe the specific situation clearly.
- 2
Highlight the unexpected change that occurred.
- 3
Explain how you assessed the impact of the change.
- 4
Detail the actions you took to adapt.
- 5
Conclude with the result or what you learned from the experience.
Example Answers
During a line pulling task, we experienced a sudden weather change that made the area unsafe. I quickly halted the operation and gathered my team to discuss alternative locations and made sure to communicate the reasons clearly. We adjusted our plan and moved the operation to a sheltered area. As a result, we completed the task safely and within the deadline.
Describe a time when you received constructive feedback on your work. How did it affect your performance?
How to Answer
- 1
Choose a specific instance when feedback was given.
- 2
Explain what the feedback was and who provided it.
- 3
Describe how you implemented the feedback.
- 4
Discuss the positive impact on your work or performance.
- 5
Keep it concise and focused on learning and improvement.
Example Answers
In my previous role, my supervisor pointed out that I needed to improve my time management skills. I took her advice seriously and started using a planner to prioritize my tasks. As a result, I was able to meet all my deadlines and even assist my team with their workload.
Can you describe a time when you performed under pressure while pulling lines? What was the outcome?
How to Answer
- 1
Think of a specific situation where you faced pressure.
- 2
Describe the challenge you encountered during line pulling.
- 3
Explain the actions you took to address the pressure.
- 4
Mention the results of your actions and what you learned.
- 5
Keep your answer focused and concise.
Example Answers
During a storm, I had to pull lines quickly to secure equipment. The wind was strong and visibility was low. I focused on teamwork, communicated clearly, and we succeeded in securing everything without damage.
Have you ever led a team during a line pulling project? What was your approach to leadership?
How to Answer
- 1
Describe a specific line pulling project where you were a team leader
- 2
Highlight your communication style with the team
- 3
Discuss how you ensured safety and efficiency during the project
- 4
Mention any tools or methods you used to keep the team motivated
- 5
Share the outcome of the project and what you learned
Example Answers
In my last project, I led a team of 5 during a cable installation. I held daily briefings to clearly communicate our goals and safety protocols. I encouraged open feedback, which helped us adapt quickly to challenges. We completed the project ahead of schedule, ensuring a safe work environment.
What motivates you to perform well in your role as a line puller, especially during challenging tasks?
How to Answer
- 1
Identify personal and professional goals that drive you.
- 2
Reflect on the importance of teamwork and collaboration in your role.
- 3
Consider the satisfaction of completing difficult tasks successfully.
- 4
Think about how safety and efficiency motivate your work.
- 5
Discuss how you handle stress and stay focused under pressure.
Example Answers
I am motivated by my desire to meet my personal goals and contribute to the team's success, especially when we face tough challenges together.
Don't Just Read Line Puller Questions - Practice Answering Them!
Reading helps, but actual practice is what gets you hired. Our AI feedback system helps you improve your Line Puller interview answers in real-time.
Personalized feedback
Unlimited practice
Used by hundreds of successful candidates
Situational Interview Questions
If you witnessed a colleague neglecting safety procedures during a line pulling task, what would you do?
How to Answer
- 1
Assess the situation quickly to ensure immediate safety.
- 2
Speak to the colleague privately to address the issue calmly.
- 3
Refer to your supervisor if the behavior continues after your conversation.
- 4
Document the incident if needed for future reference.
- 5
Always prioritize safety and encourage a culture of accountability.
Example Answers
I would first ensure that no one is in immediate danger. Then, I would talk to my colleague privately, expressing my concerns about their safety practices. If they don’t change their behavior, I would escalate the issue to our supervisor.
Imagine you are in the middle of a job and the pulling equipment fails. How would you handle the situation?
How to Answer
- 1
Stay calm and assess the situation quickly.
- 2
Check for any immediate safety issues before proceeding.
- 3
Communicate the issue to your team and supervisor.
- 4
Follow the protocol for equipment failure and report it.
- 5
Prepare to switch to backup equipment if available.
Example Answers
If the pulling equipment fails, I would first calm myself and quickly assess if there are any safety concerns. Then, I would communicate with my team, inform them of the situation, and follow our established safety protocols for equipment failure. If we have backup equipment on-site, I would prepare to switch to that while ensuring the area is secured.
Don't Just Read Line Puller Questions - Practice Answering Them!
Reading helps, but actual practice is what gets you hired. Our AI feedback system helps you improve your Line Puller interview answers in real-time.
Personalized feedback
Unlimited practice
Used by hundreds of successful candidates
How would you approach a conflict with a team member over the best way to pull a line?
How to Answer
- 1
Listen to the other person's viewpoint first.
- 2
Share your perspective calmly and clearly.
- 3
Look for common ground between both approaches.
- 4
Discuss the pros and cons of each method together.
- 5
Aim for a collaborative solution that works for both.
Example Answers
I would start by listening to my team member’s approach to pulling the line. Then, I would explain my technique and we could compare our methods for effectiveness, looking for a solution that combines the best aspects of both.
If you were tasked with planning a line pulling project, what steps would you take to ensure its success?
How to Answer
- 1
Define the project scope and objectives clearly
- 2
Identify the resources needed including team and equipment
- 3
Develop a detailed project timeline with milestones
- 4
Assess potential risks and create a mitigation plan
- 5
Communicate regularly with all stakeholders for updates
Example Answers
I would start by defining the project goals and scope to make sure everyone understands the desired outcome. Then, I'd identify all resources needed, including team members and tools. Next, I'd create a timeline with important milestones to track progress. I'd also evaluate possible risks and have a plan to address them. Finally, I'd maintain regular communication with all stakeholders to keep them informed.
If adverse weather conditions arise while you are working, how would you adjust your approach to line pulling?
How to Answer
- 1
Assess the severity of the weather conditions to ensure safety.
- 2
Communicate with your team to discuss adjustments in procedure.
- 3
Implement additional safety measures, such as securing the line more thoroughly.
- 4
Follow any company protocols for inclement weather operations.
- 5
Be prepared to stop work if conditions become too dangerous.
Example Answers
In severe weather, I would first assess the conditions and communicate with my team. If it's unsafe to proceed, I would stop and secure everything until conditions improve.
How would you manage a situation where team members are not communicating effectively during a line pulling operation?
How to Answer
- 1
Identify the communication breakdown by observing team dynamics
- 2
Encourage open dialogue among team members to express concerns
- 3
Introduce regular check-ins to ensure everyone is on the same page
- 4
Use visual aids or hand signals to enhance understanding
- 5
Provide feedback and conduct a brief team meeting to address issues
Example Answers
I would start by identifying where the communication breakdown is happening. Then, I'd facilitate a discussion among team members to share their concerns and ensure everyone feels heard. After that, I would implement regular check-ins to monitor progress and address any misunderstandings early.
What would you do if you discovered that the line you were pulling was compromised?
How to Answer
- 1
Assess the situation quickly and identify the nature of the compromise
- 2
Stop pulling the line immediately to prevent further damage or risk
- 3
Communicate the issue to your supervisor and team promptly
- 4
Follow safety protocols to ensure the area is secure
- 5
Document the incident and any actions taken for review
Example Answers
If I discovered the line was compromised, I would stop pulling immediately to avoid further issues. Next, I would inform my supervisor right away so we could assess the situation together. I would also ensure that the area is safe and take notes on what happened for future reference.
How would you prioritize tasks if resources were limited during a line pulling project?
How to Answer
- 1
Identify critical tasks essential for project progress.
- 2
Assess the impact of each task on safety and efficiency.
- 3
Communicate with the team to understand their needs and constraints.
- 4
Be flexible and ready to adapt priorities based on real-time challenges.
- 5
Document decisions and reasons for task prioritization for future reference.
Example Answers
I would first identify the critical tasks that directly impact the safety and progression of the line pulling project. For example, ensuring that safety checks are done early on is essential. Then, I'd consult with the team to gauge their input on what tasks they believe should be prioritized, ensuring we’re addressing the most pressing issues efficiently.
If you noticed that a particular technique was slowing down your team’s efficiency in line pulling, how would you approach it?
How to Answer
- 1
Assess the current technique and identify specific inefficiencies.
- 2
Collect feedback from team members about the technique.
- 3
Research alternative methods that may improve efficiency.
- 4
Propose a trial of a new technique and measure its impact.
- 5
Communicate openly with the team about changes and involve them in the process.
Example Answers
I would first evaluate the technique to pinpoint what is slowing us down. Then, I'd discuss this with the team to gather their insights. If we find a better method, I would suggest trying it out on a small scale and track our progress before fully implementing it.
Line Puller Position Details
Related Positions
- Insulator Helper
- Trench Digger
- Sounder
- Construction Helper
- Note Keeper
- Taper
- Machine Puller
- Puller
- Pin Puller
- Hook Puller
Similar positions you might be interested in.
Ace Your Next Interview!
Practice with AI feedback & get hired faster
Personalized feedback
Used by hundreds of successful candidates
Ace Your Next Interview!
Practice with AI feedback & get hired faster
Personalized feedback
Used by hundreds of successful candidates