Top 29 Log Peeler Interview Questions and Answers [Updated 2025]
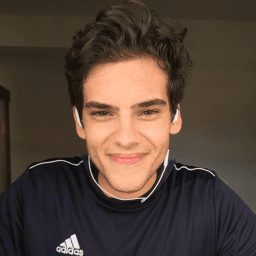
Andre Mendes
•
March 30, 2025
Navigating the interview process for a Log Peeler role can be daunting, but we're here to help. In this blog post, you'll find a curated list of the most common interview questions for this specialized position. Alongside each question, we've provided example answers and insightful tips to help you respond confidently and effectively. Get ready to enhance your interview skills and stand out in the hiring process.
Download Log Peeler Interview Questions in PDF
To make your preparation even more convenient, we've compiled all these top Log Peelerinterview questions and answers into a handy PDF.
Click the button below to download the PDF and have easy access to these essential questions anytime, anywhere:
List of Log Peeler Interview Questions
Behavioral Interview Questions
Describe a time when you had to coordinate with a team to meet production targets. How did you ensure everyone was aligned?
How to Answer
- 1
Identify a specific project where teamwork was essential.
- 2
Explain your communication methods to share goals.
- 3
Discuss how you monitored progress towards the targets.
- 4
Mention any challenges faced and how you resolved them.
- 5
Conclude with the results achieved and lessons learned.
Example Answers
In my previous job, we had a tight deadline for peeling logs for a big order. I called a team meeting to discuss our production targets and assigned specific roles based on everyone's strengths. I checked in daily to monitor progress and adjusted our plans as needed when issues arose. In the end, we met the target ahead of schedule, which boosted team morale.
Give an example of how you have contributed to workplace safety in previous roles.
How to Answer
- 1
Identify specific safety measures you implemented or promoted.
- 2
Use the STAR method: Situation, Task, Action, Result.
- 3
Quantify outcomes whenever possible (e.g., reduced incidents by X%).
- 4
Mention collaboration with colleagues or training efforts.
- 5
Relate your example to the log peeling process if possible.
Example Answers
In my previous job as a saw operator, I noticed that the area around the machines was often slippery. I suggested implementing a regular cleaning schedule, and after we did this, we reduced slips and falls by 30% within three months.
Don't Just Read Log Peeler Questions - Practice Answering Them!
Reading helps, but actual practice is what gets you hired. Our AI feedback system helps you improve your Log Peeler interview answers in real-time.
Personalized feedback
Unlimited practice
Used by hundreds of successful candidates
Can you tell me about a difficult situation you encountered on the job and how you resolved it?
How to Answer
- 1
Choose a specific situation that demonstrates your problem-solving skills.
- 2
Use the STAR method: Situation, Task, Action, Result.
- 3
Focus on your direct contributions and avoid blaming others.
- 4
Highlight what you learned from the experience.
- 5
Keep it relevant to the Log Peeler position.
Example Answers
In my last job, we faced a machinery breakdown that delayed our operations. I quickly assessed the situation, communicated with my team to ensure safety, and coordinated with our maintenance crew for repairs. I kept everyone informed on progress, which helped maintain morale. As a result, we minimized downtime and completed our orders on schedule.
Tell us about a time when you had to learn a new skill or adapt to a change in your job.
How to Answer
- 1
Think of a specific situation where you had to learn something new.
- 2
Explain why the new skill was important for your job.
- 3
Describe how you approached the learning process.
- 4
Mention any challenges you faced and how you overcame them.
- 5
Conclude with the positive outcome or what you gained from the experience.
Example Answers
In my previous job, we switched to a new project management software. I dedicated time after work to learn the new features. Initially, I struggled with the interface, but I attended a couple of training sessions and practiced daily. Eventually, I became the go-to person for my team, helping others adapt, which improved our workflow significantly.
Technical Interview Questions
What types of log peeling equipment are you familiar with, and what is your experience with each?
How to Answer
- 1
List specific types of log peeling machines you have used.
- 2
Include details about your practical experience with these machines.
- 3
Mention any maintenance or safety procedures you are familiar with.
- 4
Highlight your ability to troubleshoot common issues with the equipment.
- 5
Provide examples of projects where you successfully operated this equipment.
Example Answers
I have experience with rotary log peelers, specifically the XYS-300 model. I operated this machine for two years at XYZ Sawmill, handling logs up to 22 inches in diameter. I also performed regular maintenance, such as replacing knives and checking alignment.
How do you approach routine maintenance and troubleshooting of log peeling machines?
How to Answer
- 1
Inspect machines daily for unusual sounds or vibrations.
- 2
Follow the manufacturer's maintenance schedule closely.
- 3
Keep a log of maintenance performed and issues encountered.
- 4
Immediately address any mechanical issues to prevent downtime.
- 5
Use appropriate safety gear and procedures during maintenance.
Example Answers
I start by conducting daily inspections of the log peeling machines, checking for any unusual sounds or signs of wear. I adhere strictly to the manufacturer's maintenance schedule to ensure the equipment runs smoothly. I also maintain a detailed log of all maintenance activities and any issues that arise, which helps in troubleshooting efficiently.
Don't Just Read Log Peeler Questions - Practice Answering Them!
Reading helps, but actual practice is what gets you hired. Our AI feedback system helps you improve your Log Peeler interview answers in real-time.
Personalized feedback
Unlimited practice
Used by hundreds of successful candidates
What techniques do you use to ensure the quality of the peeled logs meets the required standards?
How to Answer
- 1
Inspect logs visually for defects before peeling.
- 2
Calibrate and maintain peeling machinery regularly.
- 3
Use a consistent technique to peel logs uniformly.
- 4
Perform quality checks during and after the peeling process.
- 5
Document and address any recurring issues to improve quality.
Example Answers
I start by inspecting each log for any visible defects before peeling. This helps ensure that only high-quality logs are processed. I also make sure that my peeling machine is calibrated and maintained to guarantee consistent results.
What safety precautions must be taken when operating log peeling machinery?
How to Answer
- 1
Ensure all operators are trained and certified for the machinery
- 2
Wear appropriate personal protective equipment, including gloves and safety goggles
- 3
Conduct regular maintenance checks on the machinery to ensure it is in good working condition
- 4
Keep the work area clear of obstructions and materials that could cause accidents
- 5
Understand and follow the manufacturer's safety guidelines for the specific equipment being used
Example Answers
When operating log peeling machinery, it is crucial to ensure that all operators are trained and certified. Additionally, wearing safety goggles and gloves is necessary to protect against debris. Regular maintenance checks also help prevent malfunctions.
How do you ensure the precision of the log peeling to match specification requirements?
How to Answer
- 1
Always calibrate the peeling machine before starting production.
- 2
Regularly check the thickness of the peel using calipers or gauges.
- 3
Monitor the logs for consistent diameter throughout the peeling process.
- 4
Document any adjustments made to the peeling settings.
- 5
Conduct periodic quality control checks during the shift.
Example Answers
I ensure precision by calibrating the machine at the beginning of each shift and checking the peel thickness with calipers regularly.
Can you describe the characteristics of different wood types and how they affect the log peeling process?
How to Answer
- 1
Identify key wood types, such as pine, oak, and birch.
- 2
Mention characteristics like hardness, grain pattern, and moisture content.
- 3
Explain how these characteristics affect peeling speed and quality.
- 4
Discuss the importance of matching the peeling method to wood type.
- 5
Keep your answer focused on practical applications in the peeling process.
Example Answers
Pine is softer and has a straight grain, which allows for faster peeling and a smoother finish. In contrast, oak is harder and more fibrous, requiring slower peeling to avoid tearing the wood. Birch has a fine grain and peels well but needs to be treated for moisture content to avoid warping.
What are common issues you might encounter with a log peeler, and how would you address them?
How to Answer
- 1
Identify mechanical failures like blade dullness or misalignment
- 2
Discuss the importance of regular maintenance checks
- 3
Mention potential safety hazards and how to mitigate them
- 4
Emphasize the significance of training operators properly
- 5
Highlight the need for consistent quality control of the output
Example Answers
One common issue is blade dullness, which can lead to inefficient peeling. I would regularly check and sharpen the blades to maintain performance.
How do you optimize the peeling process to maximize efficiency and minimize waste?
How to Answer
- 1
Assess the current peeling method to identify inefficiencies
- 2
Utilize sharp and well-maintained tools for better peeling results
- 3
Train team members on best practices and proper techniques
- 4
Implement a feedback loop to continuously improve the process
- 5
Regularly review and analyze waste levels to find areas for reduction
Example Answers
I assess the current peeling method by observing workers and collecting data on peeling times and waste. I replace dull tools and ensure all equipment is well-maintained. I also hold regular training sessions to teach best practices to the team, ensuring consistency and efficiency.
Are you experienced with any specific software or automation systems used in log peeling processes?
How to Answer
- 1
Identify the specific software you have used in log peeling.
- 2
Mention any automation systems you are familiar with.
- 3
Highlight any relevant training or certifications in these systems.
- 4
Discuss how you effectively used these systems in previous roles.
- 5
Emphasize your ability to learn new software quickly if needed.
Example Answers
I have experience with the LogPro software, which I used extensively during my previous position. I also have worked with automated peeling machines that utilized advanced CNC software.
Explain the typical steps involved in the log peeling process.
How to Answer
- 1
Start with preparing the logs by debarking them.
- 2
Load the logs onto the peeling machine securely.
- 3
Adjust the machine settings for the specific log type.
- 4
Initiate the peeling process while ensuring a consistent speed.
- 5
Remove the finished veneer sheets for drying or further processing.
Example Answers
The log peeling process begins by debarking the logs, then they are securely loaded onto the peeling machine. The machine settings are adjusted according to the log type, and we start peeling at a consistent speed before finally collecting the finished veneer.
Don't Just Read Log Peeler Questions - Practice Answering Them!
Reading helps, but actual practice is what gets you hired. Our AI feedback system helps you improve your Log Peeler interview answers in real-time.
Personalized feedback
Unlimited practice
Used by hundreds of successful candidates
Situational Interview Questions
If you notice that a batch of logs is not meeting quality standards, how would you handle the situation?
How to Answer
- 1
Identify specific quality issues with the logs.
- 2
Communicate the concerns to your supervisor immediately.
- 3
Document the observations for accountability.
- 4
Assess potential causes and suggest solutions.
- 5
Work collaboratively with the team to rectify the issues.
Example Answers
I would first identify the specific quality issues, such as defects or irregularities. Then, I'd report these concerns to my supervisor right away. I would document everything I noticed to ensure accountability and look into possible causes, suggesting adjustments in processing to improve quality.
Imagine a scenario where there is a disagreement within your team about process priorities. How would you resolve it?
How to Answer
- 1
Listen to all team members to understand their perspectives
- 2
Encourage open communication to facilitate discussion
- 3
Identify common goals to align the team
- 4
Propose a compromise or a trial period for conflicting ideas
- 5
Follow up to assess the effectiveness of the resolution
Example Answers
I would first listen to each team member's reasoning about their priorities. Then, I would facilitate a discussion to find common goals and suggest a trial period for the different processes to see which works best.
Don't Just Read Log Peeler Questions - Practice Answering Them!
Reading helps, but actual practice is what gets you hired. Our AI feedback system helps you improve your Log Peeler interview answers in real-time.
Personalized feedback
Unlimited practice
Used by hundreds of successful candidates
Suppose you are facing a tight deadline and are asked to rush the process. How would you balance speed and quality?
How to Answer
- 1
Prioritize critical tasks that directly impact project outcomes.
- 2
Communicate with your team to ensure everyone is aligned on what is essential.
- 3
Use existing tools and methods to speed up the process without compromising quality.
- 4
Set clear expectations with stakeholders regarding what can be realistically achieved.
- 5
Plan for minimal revisions by focusing on planning and reviewing early.
Example Answers
In a tight deadline, I prioritize tasks by identifying what is crucial for project success. I would communicate clearly with my team to ensure we all focus on these key elements, using our established tools to maintain our quality standards.
How would you go about training a new team member on the log peeling process?
How to Answer
- 1
Start with an overview of the log peeling process and its importance.
- 2
Demonstrate the peeling technique step-by-step using actual logs.
- 3
Provide hands-on practice opportunities for the new team member.
- 4
Encourage questions throughout the training to clarify doubts.
- 5
Offer feedback on their technique and progress after practice sessions.
Example Answers
I would first explain the log peeling process and its significance to our operation. Then, I would demonstrate the peeling technique with a log, allowing the new member to see the proper method. Next, I'd let them practice while I observe and offer guidance, encouraging them to ask questions as they learn.
You notice an opportunity to improve the peeling process. How would you propose and implement this change?
How to Answer
- 1
Identify the specific inefficiency in the peeling process you observed.
- 2
Suggest a clear change or tool that would enhance the peeling.
- 3
Outline steps to communicate your idea to your supervisor.
- 4
Describe how you would test the proposed change before full implementation.
- 5
Mention how you would gather feedback from the team after changes are made.
Example Answers
I noticed that we often waste time peeling logs due to inconsistent knife sharpening. I would propose implementing a regular sharpening schedule. I'd present my idea to my supervisor and suggest a trial period where we sharpen knives every shift. After implementing this, I would collect feedback from the team to assess the improvement in efficiency.
What would you do if you observed a safety hazard on the production floor?
How to Answer
- 1
Immediately report the hazard to a supervisor or safety officer
- 2
Ensure the area is marked or cordoned off to prevent others from accessing it
- 3
Take note of the specific details of the hazard to assist in resolving it
- 4
Follow up to confirm that the issue has been addressed properly
- 5
Maintain a proactive approach to safety by staying vigilant and encouraging others to do the same
Example Answers
If I saw a safety hazard, I would report it to my supervisor right away and make sure the area is marked to keep everyone safe. I would also check in to ensure the problem gets fixed.
If you were given limited resources and high demand, how would you prioritize tasks?
How to Answer
- 1
Identify the most critical tasks that directly impact production.
- 2
Evaluate tasks based on urgency and importance.
- 3
Communicate with the team to understand their workload and capacity.
- 4
Streamline processes to maximize efficiency.
- 5
Be flexible and ready to adjust priorities as new information arises.
Example Answers
I would first assess which tasks are crucial for meeting production deadlines. Then, I would prioritize the high-impact tasks and delegate if necessary, ensuring the team is aligned and informed.
How would you handle a situation where a customer complains about the quality of a log batch?
How to Answer
- 1
Listen carefully to the customer's complaint without interrupting.
- 2
Acknowledge the issue and empathize with the customer's feelings.
- 3
Ask for specific details about the complaint to understand the problem better.
- 4
Offer a solution or a way to rectify the situation, like replacing the logs.
- 5
Follow up with the customer after the resolution to ensure satisfaction.
Example Answers
I would first listen to the customer and let them express their concerns completely. Then I would acknowledge their complaint and apologize for the inconvenience. I would ask for specifics about the quality issue, and depending on the information, I might offer to replace the batch or give a discount. Lastly, I would check back in after the resolution to ensure they are satisfied.
If the facility was upgrading to a new log peeling technology, how would you prepare yourself and your team for the transition?
How to Answer
- 1
Research the new technology and its benefits thoroughly.
- 2
Gather feedback from team members to address concerns and suggestions.
- 3
Create a training schedule to familiarize the team with the new equipment.
- 4
Set clear goals and metrics to evaluate the transition's success.
- 5
Maintain open communication throughout the transition process.
Example Answers
I would start by researching the new technology to understand its advantages. Then, I would discuss with my team to gather their insights and concerns. I'd organize training sessions to ensure everyone is comfortable with the transition and set specific goals to measure our progress.
If multiple urgent tasks arise, how would you decide which tasks to delegate and to whom?
How to Answer
- 1
Assess the urgency and importance of each task
- 2
Identify team members' skills and current workloads
- 3
Delegate tasks that match team members' strengths
- 4
Communicate deadlines clearly while delegating
- 5
Follow up and offer support as needed
Example Answers
I would first list the tasks and prioritize them based on urgency. Then, I would consider my team's strengths and current workload to delegate the tasks accordingly, ensuring that each person has the capacity to take on their new responsibilities.
Don't Just Read Log Peeler Questions - Practice Answering Them!
Reading helps, but actual practice is what gets you hired. Our AI feedback system helps you improve your Log Peeler interview answers in real-time.
Personalized feedback
Unlimited practice
Used by hundreds of successful candidates
A colleague is underperforming. How would you approach this situation?
How to Answer
- 1
Assess the colleague's work habits objectively
- 2
Have a private and respectful conversation about their performance
- 3
Offer support and resources to help them improve
- 4
Set clear expectations and goals together
- 5
Follow up regularly to monitor their progress
Example Answers
I would first evaluate how my colleague is working and identify the specific areas where they are struggling. Then, I would arrange a private chat to discuss my observations and ask if they are facing any challenges. I'd offer my help and suggest resources they could use, like training or mentoring. Together, we would set achievable goals, and I’d check in on their progress regularly.
What steps would you take if there was an unexpected delay in the supply of logs?
How to Answer
- 1
Assess the impact of the delay on production schedules.
- 2
Communicate with suppliers to understand the reason for the delay.
- 3
Explore alternative sources or suppliers of logs.
- 4
Implement a contingency plan to manage production with reduced materials.
- 5
Keep the team informed about changes and adjustments to plans.
Example Answers
I would first evaluate how the delay affects our current production timelines. Then, I would reach out to our suppliers for updates and to understand the issue. If necessary, I would look for alternative suppliers to ensure we can maintain output. Meanwhile, I'd prepare a plan to adjust our operations during this period. Finally, I would communicate any changes transparently with the team.
Describe how you would manage the team during an evacuation due to a fire drill.
How to Answer
- 1
Stay calm and collected to set an example for the team.
- 2
Communicate clear instructions on the evacuation route.
- 3
Assign specific roles to team members to ensure efficiency.
- 4
Ensure everyone is accounted for before leaving the building.
- 5
Conduct a debriefing after the drill to discuss improvements.
Example Answers
During the evacuation, I would stay calm and guide the team by clearly instructing them on the designated exit route. I would assign roles to ensure someone is responsible for assisting others and someone is in charge of headcount before we leave.
If a piece of machinery suddenly breaks down during a shift, what steps would you take?
How to Answer
- 1
Assess the situation quickly and safely.
- 2
Notify your supervisor immediately.
- 3
Follow the company's protocol for equipment failure.
- 4
Attempt to identify the cause of the breakdown if safe to do so.
- 5
Document the incident and any steps taken for future reference.
Example Answers
I would quickly assess if it was safe to approach the machine and check for any obvious issues. Then, I would notify my supervisor about the breakdown right away and follow our protocol to ensure everyone is safe.
Log Peeler Position Details
Related Positions
- Bark Peeler
- Peeler
- Log Cutter
- Lumber Cutter
- Log Skidder
- Wood Chopper
- Wood Cutter
- Log Roller
- Pole Cutter
- Timber Cutter
Similar positions you might be interested in.
Ace Your Next Interview!
Practice with AI feedback & get hired faster
Personalized feedback
Used by hundreds of successful candidates
Ace Your Next Interview!
Practice with AI feedback & get hired faster
Personalized feedback
Used by hundreds of successful candidates