Top 30 Manufacturer Interview Questions and Answers [Updated 2025]
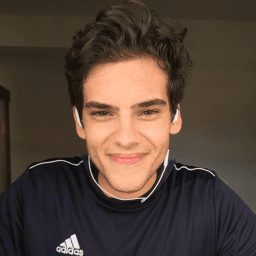
Andre Mendes
•
March 30, 2025
Navigating the competitive job market in the manufacturing industry can be challenging, but preparation is key to standing out. In this post, we explore the most common interview questions for the Manufacturer role, offering insightful example answers and strategic tips to help you respond with confidence and clarity. Prepare to impress potential employers and secure your next opportunity by mastering these essential interview questions.
Download Manufacturer Interview Questions in PDF
To make your preparation even more convenient, we've compiled all these top Manufacturerinterview questions and answers into a handy PDF.
Click the button below to download the PDF and have easy access to these essential questions anytime, anywhere:
List of Manufacturer Interview Questions
Technical Interview Questions
What experience do you have with CAD software in the context of manufacturing, and can you provide an example of how you've used it?
How to Answer
- 1
Identify specific CAD software you have used.
- 2
Describe the projects where you applied CAD skills.
- 3
Highlight how CAD contributed to improving manufacturing processes.
- 4
Mention any collaboration with engineers or designers.
- 5
Use a measurable outcome to demonstrate success.
Example Answers
I have extensive experience with SolidWorks for creating 3D models of components in our production line. For instance, I designed a custom fixture that increased assembly efficiency by 20%.
Can you explain the principles of lean manufacturing and how you have applied them in your previous roles?
How to Answer
- 1
Define lean manufacturing clearly and mention its goals: waste reduction and efficiency.
- 2
Discuss specific principles such as value stream mapping, 5S, or Kaizen.
- 3
Provide a concrete example of how you implemented lean practices in a past job.
- 4
Quantify the impact of your actions if possible, using metrics like reduced cycle time or cost savings.
- 5
Conclude with what you learned from the experience and how it shapes your approach today.
Example Answers
Lean manufacturing is about maximizing value by minimizing waste. In my previous role, I used value stream mapping to identify bottlenecks in our production line. By reorganizing workflow and implementing 5S practices, we reduced cycle time by 20% and improved team efficiency significantly.
Don't Just Read Manufacturer Questions - Practice Answering Them!
Reading helps, but actual practice is what gets you hired. Our AI feedback system helps you improve your Manufacturer interview answers in real-time.
Personalized feedback
Unlimited practice
Used by hundreds of successful candidates
What quality control processes are you familiar with and how do you ensure they are effectively implemented?
How to Answer
- 1
Identify specific quality control processes you have experience with
- 2
Explain how you monitor compliance with quality standards
- 3
Discuss the importance of documentation in quality control
- 4
Mention tools or software you use for quality management
- 5
Share a brief example of resolving a quality issue
Example Answers
I am familiar with ISO 9001 quality management systems. I ensure compliance by conducting regular audits and training staff. Documentation is key, so I maintain detailed records of inspections and corrective actions, using software like Qualityze for tracking.
How do you identify opportunities for process improvements on the production line?
How to Answer
- 1
Observe the production line regularly to identify bottlenecks or delays.
- 2
Engage with team members for their input on inefficiencies.
- 3
Analyze production data to determine patterns and areas of waste.
- 4
Pilot small changes to evaluate impact before wider implementation.
- 5
Keep updated on industry best practices and new technologies.
Example Answers
I regularly walk through the production line to spot any bottlenecks. Last month, I noticed that a specific machine was slowing down the whole line, so I suggested maintenance that improved its efficiency by 15%.
What experience do you have with ISO standards in manufacturing, and how have you ensured compliance?
How to Answer
- 1
Identify specific ISO standards you have worked with, like ISO 9001.
- 2
Describe your role in implementing or maintaining compliance with these standards.
- 3
Give examples of processes or audits you have led or participated in.
- 4
Mention any training or tools you used to ensure compliance.
- 5
Explain the results of your efforts in terms of quality improvement or operational efficiency.
Example Answers
I have extensive experience with ISO 9001 standards. In my previous role, I led a team to develop quality management processes aligned with these standards, which included thorough documentation and regular audits. We achieved compliance certification within six months, resulting in a 15% reduction in defects.
What is your experience with automation technologies in manufacturing, and how have they impacted the processes you managed?
How to Answer
- 1
Identify specific automation technologies you've used, like robotics or PLCs.
- 2
Discuss a project where you implemented automation and the results achieved.
- 3
Highlight improvements in efficiency, quality, or safety due to automation.
- 4
Use quantifiable metrics to demonstrate impact, such as reduced downtime or increased output.
- 5
Mention any challenges faced during automation implementation and how you overcame them.
Example Answers
In my previous role, I managed a team where we used robotics for assembly line automation. This implementation reduced our production time by 30% and improved product consistency.
What knowledge do you have of material science and how does it apply to your manufacturing work?
How to Answer
- 1
Identify key materials you have worked with in manufacturing.
- 2
Explain the relationship between material properties and manufacturing processes.
- 3
Highlight any specific projects where material science knowledge contributed to success.
- 4
Discuss how understanding material science improves product quality or efficiency.
- 5
Mention any relevant certifications or training in material science.
Example Answers
I have extensive experience with polymers and metals, particularly how their properties affect machining processes. In a project where we used high-strength alloys, I applied my knowledge of tensile strength to optimize machining parameters, leading to improved product quality.
What supply chain management systems are you experienced with, and how have they improved manufacturing efficiency?
How to Answer
- 1
Identify specific supply chain management systems you have used.
- 2
Explain your role and how you utilized these systems.
- 3
Provide examples of measurable improvements in efficiency.
- 4
Link the improvements to specific manufacturing processes.
- 5
Use industry terminology appropriately to demonstrate your expertise.
Example Answers
I have experience with SAP SCM, where I implemented demand planning modules. This improved our inventory turnover by 20%, reducing excess stock and streamlining the production schedule.
Explain how you have used statistical process control in your work and the results you've achieved.
How to Answer
- 1
Identify specific processes where you applied SPC.
- 2
Discuss the tools or techniques you used in SPC.
- 3
Highlight measurable results or improvements from your SPC efforts.
- 4
Use data or KPIs to support your achievements.
- 5
Mention any collaboration with team members to implement SPC.
Example Answers
In my previous role, I applied SPC using control charts to monitor our assembly line. By tracking defect rates weekly, we reduced defects by 25%, resulting in significant cost savings.
Can you discuss your experience with Six Sigma methodologies in manufacturing?
How to Answer
- 1
Start with your specific role and responsibilities using Six Sigma
- 2
Mention any relevant projects and the outcomes you achieved
- 3
Highlight your knowledge of key Six Sigma tools like DMAIC or Kaizen
- 4
Discuss how you contributed to reducing waste or improving quality
- 5
Conclude with the impact of your work on the overall manufacturing process
Example Answers
In my previous role as a manufacturing engineer, I led a Six Sigma project focusing on reducing defects in our production line. By employing the DMAIC framework, we identified root causes and implemented solutions, which resulted in a 15% reduction in defects over six months.
Don't Just Read Manufacturer Questions - Practice Answering Them!
Reading helps, but actual practice is what gets you hired. Our AI feedback system helps you improve your Manufacturer interview answers in real-time.
Personalized feedback
Unlimited practice
Used by hundreds of successful candidates
Behavioral Interview Questions
Tell me about a time when you had to work closely with a team in a manufacturing environment. What was your role and what did you accomplish together?
How to Answer
- 1
Identify a specific project or period where teamwork was essential.
- 2
Clarify your specific role and responsibilities within the team.
- 3
Highlight a challenge that you overcame together as a team.
- 4
Emphasize the results or successes achieved through collaboration.
- 5
Reflect on what you learned from the experience and how it impacted your work.
Example Answers
In my previous job, we had to launch a new assembly line. As the team lead, I coordinated with engineers and operators to optimize the workflow. We faced delays in equipment delivery, but by adjusting our schedule and cross-training team members, we reduced downtime and met our launch date. The new line increased output by 30%, demonstrating the power of teamwork.
Describe a time when you brought a new idea to improve a manufacturing process. What was the idea and what impact did it have?
How to Answer
- 1
Select a specific example where you identified a problem.
- 2
Clearly explain the new idea you proposed for improvement.
- 3
Describe the steps you took to implement the idea.
- 4
Share the outcomes and measurable impacts of your idea.
- 5
Use the STAR method to structure your response.
Example Answers
In my previous job, I noticed that our assembly line was facing delays due to manual inventory checks. I proposed an automated inventory management system using RFID technology. I led a small team to implement it, which reduced the check time by 50%. As a result, our production rate increased significantly, leading to higher customer satisfaction.
Don't Just Read Manufacturer Questions - Practice Answering Them!
Reading helps, but actual practice is what gets you hired. Our AI feedback system helps you improve your Manufacturer interview answers in real-time.
Personalized feedback
Unlimited practice
Used by hundreds of successful candidates
Can you provide an example of a situation where you had to lead a manufacturing team through a challenging project or period?
How to Answer
- 1
Choose a specific project that was difficult but rewarding.
- 2
Describe the challenges the team faced and your role in addressing them.
- 3
Highlight your leadership actions and the strategies you implemented.
- 4
Emphasize the outcome and what you and your team learned.
- 5
Mention any metrics or results that demonstrate the success of the project.
Example Answers
In my previous role, we faced a major delay in production due to a supplier issue. I organized daily meetings to track progress and brainstorm solutions. By prioritizing tasks and reallocating resources, we managed to get back on schedule, reducing delays by 30%. The team learned the importance of cross-functional communication.
Describe an instance where you had to resolve a conflict between two team members on the manufacturing floor. What was the outcome?
How to Answer
- 1
Identify the specific conflict and the parties involved
- 2
Describe your role in facilitating the resolution
- 3
Explain the steps you took to mediate the situation
- 4
Highlight the outcome and how it benefited the team
- 5
Reflect on any lessons learned from the experience
Example Answers
In a recent project, two team members disagreed on the best method to assemble a component. I organized a meeting where both could present their viewpoints. After discussing their perspectives, we combined their ideas into a new approach. This not only resolved the conflict but also improved the assembly process, and both members felt valued.
Can you discuss a time when you had to adapt to significant changes in a manufacturing process or technology?
How to Answer
- 1
Select a specific project where changes were implemented.
- 2
Describe the nature of the change, focusing on the technology or process.
- 3
Explain your role and actions taken to adapt.
- 4
Highlight the outcome and what you learned from the experience.
- 5
Keep your answer structured with a clear beginning, middle, and end.
Example Answers
In a previous position, our team switched from manual to automated assembly lines. I led the training program for operators on the new machinery, ensuring that everyone was comfortable using it. As a result, our production rate increased by 30%. This taught me the importance of proactive communication during transitions.
Give an example of how you've contributed to continuous improvement initiatives in your previous manufacturing roles.
How to Answer
- 1
Identify a specific improvement project you were involved in
- 2
Describe your role and contributions clearly
- 3
Use metrics to quantify the results of the improvement
- 4
Highlight collaboration with team members or other departments
- 5
Focus on the impact on efficiency, quality, or cost savings
Example Answers
In my last role, I led a project to streamline the assembly process by implementing a new layout. This reduced assembly time by 20% and improved worker safety. My efforts included organizing team workshops to gather input and adjustments.
Describe how you have managed competing priorities and tight deadlines during a busy production cycle.
How to Answer
- 1
Identify specific competing priorities you faced.
- 2
Explain how you prioritized tasks based on urgency and importance.
- 3
Discuss tools or methods you used for tracking progress and deadlines.
- 4
Highlight any collaboration with team members to meet goals.
- 5
Share an outcome or result that demonstrates your success in managing the situation.
Example Answers
In my last role, we had multiple orders due at the same time. I prioritized tasks by assessing which orders were most urgent and communicated this with my team. We used a shared progress tracker to stay on top of deadlines, and I delegated tasks effectively. As a result, we completed all orders on time and received positive feedback from our clients.
Discuss a situation where you implemented a successful quality improvement project.
How to Answer
- 1
Identify a specific project you led or were significantly involved in.
- 2
Explain the quality issue you addressed and why it was important.
- 3
Describe the steps you took to implement improvements and gather data.
- 4
Share the outcomes and how you measured success.
- 5
Reflect on any lessons learned or how it impacted the team or company.
Example Answers
In my previous role, we faced high defect rates in our assembly line. I initiated a project to standardize assembly procedures. I gathered data on defects, implemented new training for staff, and established a checklist for quality checks. As a result, defect rates dropped by 30% in three months, improving overall production efficiency.
Can you describe a time when you significantly improved the efficiency of a manufacturing process?
How to Answer
- 1
Choose a specific example from your experience.
- 2
Mention the original process and its inefficiencies.
- 3
Explain the changes you implemented clearly.
- 4
Quantify the results of your improvement with metrics.
- 5
Highlight how it impacted the team or company overall.
Example Answers
At my previous job, the assembly line had a bottleneck at the packing stage. I implemented a new packing system that reduced the packing time from 10 minutes per unit to 5 minutes. This change increased our overall production rate by 20%, which helped us meet customer demand more efficiently.
Provide an example of a technical issue you solved on the manufacturing floor. What was the problem and how did you resolve it?
How to Answer
- 1
Identify a specific problem you faced on the manufacturing floor.
- 2
Explain the impact of the problem on production and outcomes.
- 3
Outline the steps you took to analyze and resolve the issue.
- 4
Highlight any teamwork or cross-departmental collaboration involved.
- 5
Conclude with the positive results or improvements achieved.
Example Answers
In my previous role, we had a recurring issue with a CNC machine malfunctioning, causing delays. I gathered a team to analyze the data logs and found that the coolant levels were too low. We implemented a monitoring system for coolant levels and adjusted our maintenance schedule, which reduced machine downtimes by 30%.
Don't Just Read Manufacturer Questions - Practice Answering Them!
Reading helps, but actual practice is what gets you hired. Our AI feedback system helps you improve your Manufacturer interview answers in real-time.
Personalized feedback
Unlimited practice
Used by hundreds of successful candidates
Situational Interview Questions
Imagine there is a sudden increase in defect rates on the production line. How would you approach identifying and addressing the root cause?
How to Answer
- 1
Gather data on defect rates to understand the extent and patterns of the issue
- 2
Engage team members to obtain insights and observations from the production line
- 3
Review recent changes in processes, materials, or machinery that may correlate with the defects
- 4
Conduct root cause analysis, such as 5 Whys or Fishbone Diagram, to pinpoint underlying causes
- 5
Implement corrective actions based on findings and monitor for improvement
Example Answers
I would first collect data on the defect rates and identify any patterns that correlate with shifts or changes in the production process. Then, I would speak with the team to gather their input on what they have noticed. After that, I would analyze any recent changes made to materials or machinery and use a root cause analysis method to identify the main factors causing the increase. Finally, I would work on implementing targeted solutions and track the impact on defect rates.
A safety incident has occurred on the shop floor. What steps would you take to handle the immediate situation and prevent future incidents?
How to Answer
- 1
Assess the situation to ensure everyone is safe and there are no ongoing hazards.
- 2
Provide first aid or call for medical assistance if needed.
- 3
Notify management and report the incident following company protocols.
- 4
Investigate the root cause of the incident promptly and gather evidence.
- 5
Implement preventive measures and train staff to avoid future incidents.
Example Answers
First, I would ensure everyone's safety by assessing the situation and moving any personnel away from immediate danger. Then I would call for medical help if anyone is injured. After that, I would inform management and adhere to our incident reporting procedures. I would investigate the causes of the incident as soon as possible to prevent it from happening again and implement any necessary safety training.
Don't Just Read Manufacturer Questions - Practice Answering Them!
Reading helps, but actual practice is what gets you hired. Our AI feedback system helps you improve your Manufacturer interview answers in real-time.
Personalized feedback
Unlimited practice
Used by hundreds of successful candidates
If you encounter a disruption in the supply chain that affects production schedules, how would you address the issue?
How to Answer
- 1
Identify the specific cause of the disruption quickly.
- 2
Communicate promptly with relevant stakeholders about the issue.
- 3
Explore alternative suppliers or materials to minimize delay.
- 4
Adjust production schedules as needed, prioritizing critical orders.
- 5
Implement strategies to prevent future disruptions based on lessons learned.
Example Answers
I would first assess the root cause of the disruption to determine its impact. Then, I would inform my team and suppliers, while looking for alternative sources to maintain production. Adjustments to our schedule would follow, focusing on urgent orders.
How would you handle a situation where key machinery breaks down unexpectedly and affects production deadlines?
How to Answer
- 1
Assess the situation quickly to understand the extent of the breakdown
- 2
Communicate with the team and management about the issue and potential impacts
- 3
Identify alternatives such as shifting production to other machines or processes
- 4
Prioritize repairs and ensure that the maintenance team is ready to act
- 5
Document the incident to identify any patterns and improve future responses
Example Answers
If a key machine breaks down, I would first assess the situation to determine how serious it is. I would then inform my team and management about the breakdown and its impact on our deadlines. Next, I would explore alternative machines to keep production moving and make sure the maintenance team is on the job immediately to fix the issue. Finally, I would document the incident to review later and improve our response for the future.
If tasked with reducing manufacturing costs without compromising quality, what strategies would you employ?
How to Answer
- 1
Analyze current production processes for inefficiencies
- 2
Implement lean manufacturing principles to reduce waste
- 3
Negotiate better terms with suppliers for raw materials
- 4
Invest in training staff to improve skills and productivity
- 5
Utilize technology for automation where it offers a clear return on investment
Example Answers
I would start by analyzing our current processes to identify inefficiencies. For example, streamlining workflows and reducing bottlenecks can save time and costs. Implementing lean manufacturing techniques also helps us minimize waste while maintaining quality standards.
How would you approach training new employees to ensure they meet production and safety standards?
How to Answer
- 1
Start with a comprehensive orientation that covers company policies and safety protocols
- 2
Implement hands-on training with experienced employees as mentors
- 3
Utilize checklists for critical tasks to ensure consistency and adherence to standards
- 4
Regularly assess new employees' understanding through quizzes and practical demonstrations
- 5
Solicit feedback from new employees to improve the training process continuously
Example Answers
I would begin with an orientation that thoroughly explains our safety protocols. Then, I would pair new hires with experienced mentors for hands-on training. Checklists would be provided for key tasks to ensure consistency, and I'd schedule regular assessments to ensure they understand procedures.
What actions would you take if you noticed an increase in material waste during production?
How to Answer
- 1
Analyze production data to identify waste patterns.
- 2
Discuss findings with the production team for insights.
- 3
Implement process changes to reduce identified waste.
- 4
Monitor the effects of changes on waste levels.
- 5
Train staff on best practices for material usage.
Example Answers
I would first analyze the production data to see where the waste is occurring. Then, I would meet with the team to gather their input and identify possible causes. Based on this, I would implement targeted changes in the production process and monitor waste levels closely.
If tasked with integrating a new technology into existing processes, how would you ensure a smooth transition?
How to Answer
- 1
Assess current processes to identify integration points.
- 2
Involve key stakeholders early to gather input and support.
- 3
Develop a clear implementation plan with timelines and milestones.
- 4
Provide training and resources to teams affected by the change.
- 5
Monitor progress and gather feedback for continuous improvement.
Example Answers
I would start by analyzing our existing processes to pinpoint where the new technology fits best, then engage with team leaders to understand their concerns and needs. Following that, I would create a detailed plan with clear timelines and involve the team in training to ensure everyone is comfortable with the transition. Lastly, I'd monitor the implementation closely and adjust based on feedback.
What would be your immediate steps if a natural disaster impacted the manufacturing facility?
How to Answer
- 1
Assess the safety of all personnel first.
- 2
Communicate with emergency services and follow their directives.
- 3
Evaluate the extent of damage to equipment and facilities.
- 4
Initiate a business continuity plan to resume operations.
- 5
Document everything for insurance and recovery purposes.
Example Answers
First, I would ensure that all employees are safe and accounted for. Then, I would contact emergency services if needed and start assessing the damage to our equipment and facilities. After that, I'd activate our business continuity plan to minimize disruption to operations.
If asked to improve energy efficiency within the plant, what initiatives would you consider?
How to Answer
- 1
Identify current energy consumption patterns and sources of waste.
- 2
Consider implementing energy-efficient equipment or technologies.
- 3
Engage employees in energy-saving practices and awareness campaigns.
- 4
Evaluate and improve insulation and climate control systems.
- 5
Explore renewable energy options or partnerships for the plant.
Example Answers
To improve energy efficiency, I would start by analyzing our current energy usage to pinpoint areas of waste. Then, I would look into upgrading to energy-efficient machinery and equipment. Additionally, I would implement training for staff to promote energy-saving practices.
Don't Just Read Manufacturer Questions - Practice Answering Them!
Reading helps, but actual practice is what gets you hired. Our AI feedback system helps you improve your Manufacturer interview answers in real-time.
Personalized feedback
Unlimited practice
Used by hundreds of successful candidates
Manufacturer Position Details
Recommended Job Boards
iHireManufacturing
www.ihiremanufacturing.com/jobs/searchCareerBuilder
www.careerbuilder.com/jobs/manufacturerZipRecruiter
www.ziprecruiter.com/Jobs/ManufacturerThese job boards are ranked by relevance for this position.
Related Positions
- Utilities Manager
- Software Publisher
- Billing Manager
- Music Publisher
- Project Administrator
- Team Leader
- Project Leader
- Watermaster
- Registration Officer
- Pool Manager
Similar positions you might be interested in.
Ace Your Next Interview!
Practice with AI feedback & get hired faster
Personalized feedback
Used by hundreds of successful candidates
Ace Your Next Interview!
Practice with AI feedback & get hired faster
Personalized feedback
Used by hundreds of successful candidates