Top 31 Mixer Operator Interview Questions and Answers [Updated 2025]
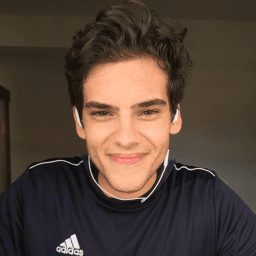
Andre Mendes
•
March 30, 2025
Preparing for a Mixer Operator interview? This blog post is your ultimate guide, featuring the most common questions asked during interviews for this role. Discover example answers and expert tips on how to respond effectively, ensuring you stand out to potential employers. Dive in to enhance your interview skills and boost your confidence as you prepare to land your next job.
Download Mixer Operator Interview Questions in PDF
To make your preparation even more convenient, we've compiled all these top Mixer Operatorinterview questions and answers into a handy PDF.
Click the button below to download the PDF and have easy access to these essential questions anytime, anywhere:
List of Mixer Operator Interview Questions
Behavioral Interview Questions
Can you describe a time when you had to work closely with a team to complete a mixing task?
How to Answer
- 1
Select a specific project or task involving mixing.
- 2
Highlight your role in the team and how you contributed.
- 3
Explain how the team collaborated effectively.
- 4
Mention any challenges faced and how they were overcome.
- 5
Conclude with the outcome of the project and its impact.
Example Answers
In my previous role, we had a project to create a new blend for a client. I coordinated with the ingredients team to select the right materials and led the mixing process. We faced a challenge with the consistency of the blend, but through teamwork and open communication, we adjusted the ratios and succeeded in finishing the project ahead of schedule, which impressed the client.
Tell me about a difficult mixing challenge you faced and how you resolved it.
How to Answer
- 1
Identify a specific mixing challenge you encountered.
- 2
Briefly describe the context of the challenge.
- 3
Explain the steps you took to address the challenge.
- 4
Discuss the outcome and what you learned.
- 5
Highlight any teamwork or support involved.
Example Answers
In my last position, we faced a challenge with a new ingredient that clumped during mixing. I analyzed the mixing process and adjusted the speed and duration, which resolved the issue and improved the consistency of the mixture.
Don't Just Read Mixer Operator Questions - Practice Answering Them!
Reading helps, but actual practice is what gets you hired. Our AI feedback system helps you improve your Mixer Operator interview answers in real-time.
Personalized feedback
Unlimited practice
Used by hundreds of successful candidates
Describe an instance where you identified a safety hazard in the mixing process. What did you do about it?
How to Answer
- 1
Think of a specific incident that highlights your attention to safety.
- 2
Explain how you recognized the hazard - was it a routine check or an observed issue?
- 3
Describe the steps you took to address the hazard - did you report it, fix it, or implement a new procedure?
- 4
Mention any collaboration with colleagues or management to improve safety protocols.
- 5
Conclude with the outcome of your actions and how it enhanced safety.
Example Answers
During a routine check of the mixing area, I noticed that the safety guard on the mixer was missing. I immediately stopped the machine, reported the issue to my supervisor, and ensured that a replacement guard was installed before the machine was used again. This action not only prevented potential injuries but also led to a review of our equipment maintenance procedures.
Have you ever had to adapt quickly to a change in the mixing formula or recipe? How did you handle it?
How to Answer
- 1
Share a specific example from your past experience
- 2
Describe the change in the recipe clearly
- 3
Explain your thought process in adapting to the change
- 4
Highlight any teamwork or communication involved
- 5
Mention the outcome and what you learned from the situation
Example Answers
At my previous job, we had a sudden change in the client's specifications for a product. I quickly reviewed the recipe adjustments, recalibrated the mixer settings, and communicated with my team to ensure everyone was aligned. We successfully met the client's needs without delays, and it taught me the importance of flexibility and teamwork.
Give an example of a time when your attention to detail made a difference in the mixing process.
How to Answer
- 1
Think of a specific incident where you spotted an error.
- 2
Explain how your attention to detail directly impacted the results.
- 3
Include quantitative results if possible, like improved quality or reduced waste.
- 4
Keep your example focused on the mixing process.
- 5
Show how this experience reinforced your attention to detail.
Example Answers
During a production run, I noticed that the weight of one ingredient was slightly off from specifications. I double-checked the measurements and corrected it before adding the ingredient. This attention to detail ensured that the final product met quality standards, reducing rework by 15%.
Can you talk about a time when you had to communicate important information to your team during a mixing operation?
How to Answer
- 1
Identify a specific situation where communication was crucial.
- 2
Explain what information needed to be conveyed and why it was important.
- 3
Describe how you communicated the information effectively to the team.
- 4
Include the outcome of the communication and its impact on the operation.
- 5
Keep the example relevant to mixing operations and teamwork.
Example Answers
During a recent batch mix, we discovered a discrepancy in ingredient weights. I immediately called a team huddle to clarify the situation, ensuring everyone understood the correct weights needed. This communication helped us avoid an error in the final product and we completed the mix on schedule.
Describe your experience in training new operators on mixing techniques and safety practices.
How to Answer
- 1
Highlight your role in the training process clearly.
- 2
Discuss specific techniques or methods you taught.
- 3
Mention safety practices and the importance of compliance.
- 4
Include any metrics or feedback that show the effectiveness of your training.
- 5
Share a personal success story or challenge from training.
Example Answers
In my previous role, I trained new operators by demonstrating key mixing techniques like proper ingredient measurement and blending speeds. I emphasized safety practices such as wearing PPE and following the SOPs. After my training sessions, we saw a 20% reduction in mixing errors, and I received positive feedback from my trainees on clarity and hands-on support.
Can you give an example of how you handled receiving constructive criticism about your mixing techniques?
How to Answer
- 1
Acknowledge the feedback positively and thank the person for it.
- 2
Explain the specific criticism you received and its context.
- 3
Describe the steps you took to improve based on the feedback.
- 4
Highlight the results of implementing the changes you made.
- 5
Reflect on what you learned from the experience.
Example Answers
During a review, my supervisor mentioned that my mixing consistency could be improved. I thanked them for the feedback and then spent extra time studying the mixing ratios. After adjusting my technique, I was able to achieve a more uniform product, which increased our quality ratings.
Have you ever taken the initiative to improve a process related to mixing? What was it?
How to Answer
- 1
Think of a specific instance where you noticed inefficiencies.
- 2
Describe the steps you took to analyze the process.
- 3
Explain the solution you proposed and how you implemented it.
- 4
Highlight any positive outcomes such as time saved or quality improved.
- 5
Be ready to discuss any challenges you faced and how you overcame them.
Example Answers
In my previous job, I noticed that our mixing process was slow due to frequent equipment cleaning. I proposed a schedule to clean equipment during non-production hours, which reduced downtime by 20% and increased our output significantly.
Technical Interview Questions
What types of mixing equipment are you experienced with, and what are their key functions?
How to Answer
- 1
Identify specific types of mixing equipment you have used
- 2
Describe each type's primary function and its application
- 3
Mention any relevant experiences or settings where you used the equipment
- 4
Highlight any safety or maintenance protocols you follow
- 5
Be concise and focused on your technical expertise
Example Answers
I have experience with ribbon blenders, which are excellent for mixing dry powders. They ensure even distribution and are great for making bulk mixtures in a production line setting.
Explain the steps you take to prepare a mixer before starting production.
How to Answer
- 1
Ensure the mixer is clean from any previous batch.
- 2
Check the operational status of all mixer components.
- 3
Calibrate the mixer settings according to production specifications.
- 4
Prepare and measure all ingredients before loading them into the mixer.
- 5
Conduct a test run without ingredients to confirm proper functionality.
Example Answers
First, I clean the mixer thoroughly to remove any leftover materials. Then, I inspect the mixer components to ensure everything is functioning correctly. I calibrate the mixer settings according to the recipe, prepare the ingredients, and finally, I run a quick test to make sure the mixer operates smoothly.
Don't Just Read Mixer Operator Questions - Practice Answering Them!
Reading helps, but actual practice is what gets you hired. Our AI feedback system helps you improve your Mixer Operator interview answers in real-time.
Personalized feedback
Unlimited practice
Used by hundreds of successful candidates
How do you ensure quality control in the mixing process? What tests do you perform?
How to Answer
- 1
Start with describing your standard operating procedures for mixing.
- 2
Mention specific tests like viscosity testing, temperature checks, or sample tasting depending on the mix.
- 3
Talk about the importance of monitoring ingredient ratios and consistency.
- 4
Explain how you document results and any corrective actions taken.
- 5
Highlight your experience with quality control systems or certifications if applicable.
Example Answers
I follow strict SOPs during the mixing process to ensure consistency. I perform viscosity tests and temperature checks to confirm the mix is within specifications. I document all results and make adjustments if something is off.
What common issues might arise during operation of a mixer, and how would you troubleshoot them?
How to Answer
- 1
Identify common mechanical and operational problems with mixers.
- 2
Describe specific symptoms for each problem to look out for.
- 3
Outline basic troubleshooting steps to diagnose the issues.
- 4
Mention any safety precautions to take while troubleshooting.
- 5
Share examples from past experiences if possible.
Example Answers
Common issues include uneven mixing and excessive noise. For uneven mixing, check the paddle alignment and adjust if necessary. For noise, inspect for loose parts and ensure components are lubricated properly.
How do you approach recipe formulation when mixing different substances?
How to Answer
- 1
Understand the properties of each substance involved
- 2
Determine the desired outcome for the mix
- 3
Use precise measurements for accuracy
- 4
Adjust based on trial and feedback
- 5
Document the formulation for future reference
Example Answers
I analyze each substance's properties to understand how they interact. For example, when mixing a binder and a filler, I ensure that the binder can effectively hold the filler. Then, I measure accurately and make slight adjustments until I achieve the desired consistency.
What is your process for cleaning the mixing equipment after a batch is completed?
How to Answer
- 1
Begin by ensuring the equipment is turned off and locked out for safety.
- 2
Remove any remaining material by scraping or using a vacuum.
- 3
Use appropriate cleaning solutions as per manufacturer guidelines.
- 4
Thoroughly rinse all parts with clean water to remove residue.
- 5
Inspect the equipment for damage or wear before reassembly.
Example Answers
After finishing a batch, I first shut down and lock out the equipment. Then, I scrape and vacuum any leftover material, followed by cleaning with a diluted solution as recommended. I rinse everything thoroughly with clean water and check for any issues before putting the equipment back together.
How do you determine the proportion of raw materials needed for a specific mixing job?
How to Answer
- 1
Review the recipe or formula for the mix carefully
- 2
Calculate the total weight or volume required for the batch
- 3
Use precise scales or measuring tools to achieve accuracy
- 4
Adjust proportions based on any batch size changes
- 5
Keep records of proportion adjustments for consistency in future mixes.
Example Answers
I start by reviewing the recipe for the mix and determining the batch size needed. For example, if I need 100 kg of the mix and the recipe calls for a 40-30-30 ratio of ingredients A, B, and C, I calculate 40 kg of A, 30 kg of B, and 30 kg of C. I always double-check my measurements to ensure accuracy.
What mixing theories or principles are you familiar with, and how do they apply to your work?
How to Answer
- 1
Identify key mixing theories you have studied or applied, such as fluid dynamics or particle size distribution.
- 2
Explain how these theories improve mixing efficiency and product quality in your role.
- 3
Use specific examples from your previous experience to illustrate your knowledge.
- 4
Be ready to discuss the impact of factors like viscosity and shear rate on mixing outcomes.
- 5
Show enthusiasm for mixing science and your eagerness to apply these principles.
Example Answers
I am familiar with fluid dynamics and the principles of laminar versus turbulent flow. In my previous job, I utilized these concepts to optimize a mixing process, ensuring uniformity in our final product.
What metrics do you use to assess the efficiency of the mixing process?
How to Answer
- 1
Identify key performance indicators like mixing time and homogeneity.
- 2
Discuss the importance of batch consistency and quality testing results.
- 3
Mention the role of equipment utilization rates in assessing efficiency.
- 4
Include how waste reduction and cost saving metrics are relevant.
- 5
Highlight the significance of operator feedback in continuous improvement.
Example Answers
I evaluate mixing efficiency by examining metrics such as mixing time and the homogeneity of the mix. For instance, I aim for a mixing time that meets the target specifications while ensuring that the end product consistently passes quality tests.
What experience do you have with automated mixing systems, and how do you operate them?
How to Answer
- 1
Highlight your specific experience with automated systems.
- 2
Mention any relevant training or certifications.
- 3
Describe the types of materials or products you mixed.
- 4
Explain your familiarity with operating controls and monitoring systems.
- 5
Share an example of a successful mixing process you managed.
Example Answers
I have three years of experience working with automated mixing systems, primarily in a food processing facility. I operated and calibrated the mixing controls and maintained quality by monitoring the output.
Don't Just Read Mixer Operator Questions - Practice Answering Them!
Reading helps, but actual practice is what gets you hired. Our AI feedback system helps you improve your Mixer Operator interview answers in real-time.
Personalized feedback
Unlimited practice
Used by hundreds of successful candidates
How do you determine the appropriate mixing time for different materials?
How to Answer
- 1
Analyze the properties of each material including viscosity and texture.
- 2
Consult manufacturer specifications or guidelines for mixing times.
- 3
Perform small scale tests to observe the mixing behavior.
- 4
Adjust the mixing time based on the desired consistency and homogeneity.
- 5
Keep records of optimal times for future reference and consistency.
Example Answers
I start by examining the viscosity and physical properties of the materials. I then refer to any manufacturer guidelines and run small tests to judge how well they mix. Based on these observations, I adjust the time to ensure a consistent blend.
Situational Interview Questions
If the mixed product does not meet specifications, what immediate steps would you take?
How to Answer
- 1
Stop the mixing process to prevent further defective product.
- 2
Identify the deviation from the specifications and document it.
- 3
Communicate with team members and supervisors about the issue.
- 4
Evaluate the cause of the problem by checking equipment and ingredient quality.
- 5
Implement corrective actions based on the findings and retest the product.
Example Answers
I would immediately stop the mixer to prevent any more off-spec product. Then, I'd assess what went wrong by checking our ingredients and the equipment. I would document my findings and communicate with my supervisor before taking corrective actions.
If you notice that a colleague is not following safety protocols while operating the mixer, how would you handle the situation?
How to Answer
- 1
Stay calm and approach your colleague respectfully.
- 2
Ask them if they are aware of the safety protocols.
- 3
Suggest the proper procedures in a non-confrontational way.
- 4
If necessary, report the behavior to a supervisor for safety.
- 5
Emphasize the importance of safety for everyone.
Example Answers
I would calmly approach my colleague and ask if they're aware of the safety protocols. I would then kindly remind them of the correct procedures and why they are important for our safety and the quality of our work.
Don't Just Read Mixer Operator Questions - Practice Answering Them!
Reading helps, but actual practice is what gets you hired. Our AI feedback system helps you improve your Mixer Operator interview answers in real-time.
Personalized feedback
Unlimited practice
Used by hundreds of successful candidates
Imagine you have multiple orders to fulfill and limited time. What strategy would you use to prioritize your tasks?
How to Answer
- 1
Assess the urgency of each order based on deadlines.
- 2
Consider the complexity and time required for each task.
- 3
Prioritize orders that contribute the most to production goals.
- 4
Communicate with team members about workload and expectations.
- 5
Adjust priorities as needed based on real-time developments.
Example Answers
I would first assess each order's deadline and prioritize the ones due soon. Then, I'd allocate time based on how complicated each order is, focusing on the ones that require the least time first to clear out some tasks quickly. Finally, I would keep my supervisor updated on my progress.
If you are part of a team and there is a disagreement on how to adjust the mixing parameters, how would you proceed?
How to Answer
- 1
Listen to all team members' perspectives on the issue.
- 2
Identify the reasons behind differing viewpoints to understand the concerns.
- 3
Suggest a trial period to test different parameters and gather data.
- 4
Aim for a collaborative decision by weighing the pros and cons of each suggestion.
- 5
Keep an open mind and be willing to adjust your own opinion based on evidence.
Example Answers
I would first listen to everyone's opinions on the mixing parameters to understand each viewpoint. Then, I would suggest a trial run where we test the proposed adjustments and gather data to see which approach yields the best results.
How would you handle a situation where you are under pressure to maintain production while facing equipment failure?
How to Answer
- 1
Stay calm and assess the situation quickly
- 2
Communicate immediately with your team about the issue
- 3
Identify the cause of the failure and possible quick fixes
- 4
Prioritize tasks to minimize downtime
- 5
If needed, escalate to management for additional support
Example Answers
In the event of equipment failure, I would first keep a cool head and quickly assess the issue. I would inform my team right away and discuss potential quick fixes. We could prioritize tasks for ongoing operations while I troubleshoot the problem. If we can't fix it promptly, I would escalate the situation to ensure leadership is aware.
If you were leading a team of mixer operators and faced a production halt, what actions would you take?
How to Answer
- 1
Assess the situation to identify the cause of the production halt.
- 2
Communicate clearly with the team members to keep everyone informed.
- 3
Prioritize immediate actions to resolve the issue, like troubleshooting equipment.
- 4
Assign specific tasks to team members to address the problem efficiently.
- 5
Document the issue and the resolution steps for future reference.
Example Answers
First, I would assess the reason for the production halt by checking the equipment and getting input from the team. Then, I would communicate clearly about the issue at hand, assign tasks based on each operator’s strengths, and ensure we work together to resolve the problem quickly.
If you notice minor wear on the mixing blades, what steps would you take before continuing operation?
How to Answer
- 1
Stop the operation immediately to ensure safety.
- 2
Inspect the wear carefully to assess severity.
- 3
Consult the manufacturer's guidelines for maintenance.
- 4
Determine if replacement or repair is necessary.
- 5
Document the findings and inform a supervisor.
Example Answers
I would stop the mixer immediately to prevent further damage, inspect the blades for severity of wear, consult the manual for recommended actions, and document everything before seeking approval for repairs.
If a batch you're mixing is running out of time and is not yet ready, how would you manage the situation?
How to Answer
- 1
Assess the current state of the mixture to identify issues.
- 2
Communicate with your supervisor about the situation.
- 3
Adjust mixing time if possible and necessary.
- 4
Prioritize safety and quality over rushing the batch.
- 5
Document the situation for future reference and improvement.
Example Answers
I would first check the mixture to see what is causing the delay. Then, I'd inform my supervisor about the situation to get guidance. If allowed, I would extend the mixing time to ensure quality.
If you need to handle a batch of hazardous materials, what procedures do you follow to ensure safety?
How to Answer
- 1
Always wear the appropriate personal protective equipment (PPE).
- 2
Review the safety data sheets (SDS) for the materials before starting.
- 3
Ensure proper ventilation in the mixing area.
- 4
Have emergency procedures in place and know where the safety equipment is located.
- 5
Conduct regular training and drills for handling hazardous materials.
Example Answers
I always make sure to wear the appropriate PPE like gloves and goggles. Before handling any hazardous materials, I read the safety data sheet to understand the risks. I also ensure the area is well-ventilated and that I know the emergency procedures.
How would you ensure that customer specifications are met while mixing?
How to Answer
- 1
Review customer specifications thoroughly before starting the mixing process
- 2
Use precise measurement tools to ensure accurate ingredient proportions
- 3
Regularly check and adjust the mixing process according to customer needs
- 4
Communicate with team members to confirm understanding of specifications
- 5
Document the mixing process to track adherence to specifications
Example Answers
I make sure to carefully review all customer specifications and use accurate measuring tools to mix the ingredients to the exact requirements. Additionally, I check progress regularly and communicate with my team to ensure everyone is on the same page.
Don't Just Read Mixer Operator Questions - Practice Answering Them!
Reading helps, but actual practice is what gets you hired. Our AI feedback system helps you improve your Mixer Operator interview answers in real-time.
Personalized feedback
Unlimited practice
Used by hundreds of successful candidates
If you have limited resources for mixing production, how do you handle the workload?
How to Answer
- 1
Prioritize tasks based on urgency and impact
- 2
Communicate with your team about resource limitations
- 3
Look for ways to optimize the mixing process
- 4
Consider reallocating resources to critical tasks
- 5
Stay flexible and adapt to changes quickly
Example Answers
In a situation with limited resources, I would first prioritize tasks to focus on the most critical mixes that impact our deadlines. I would communicate clearly with the team to ensure everyone understands the limits and possibly work together to optimize our mixing processes.
Mixer Operator Position Details
Salary Information
Recommended Job Boards
ZipRecruiter
www.ziprecruiter.com/Jobs/Mixer-OperatorThese job boards are ranked by relevance for this position.
Related Positions
- Audio Operator
- Transmission Operator
- Engineering Operator
- Television Operator
- Control Operator
- Studio Engineer
- Videotape Operator
- Board Operator
- Audio Engineer
- Studio Technician
Similar positions you might be interested in.
Ace Your Next Interview!
Practice with AI feedback & get hired faster
Personalized feedback
Used by hundreds of successful candidates
Ace Your Next Interview!
Practice with AI feedback & get hired faster
Personalized feedback
Used by hundreds of successful candidates