Top 30 Nut Grinder Interview Questions and Answers [Updated 2025]
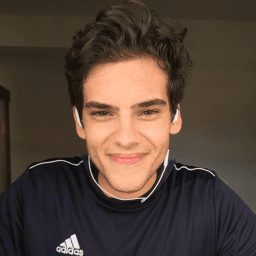
Andre Mendes
•
March 30, 2025
Preparing for a Nut Grinder role interview? Our comprehensive guide offers the most common questions you might face, along with example answers and expert tips to help you respond effectively. Whether you're a seasoned professional or a newcomer, this post is designed to boost your confidence and enhance your interview performance, setting the stage for success in this specialized field.
Download Nut Grinder Interview Questions in PDF
To make your preparation even more convenient, we've compiled all these top Nut Grinderinterview questions and answers into a handy PDF.
Click the button below to download the PDF and have easy access to these essential questions anytime, anywhere:
List of Nut Grinder Interview Questions
Behavioral Interview Questions
Can you describe a time when you had to troubleshoot a malfunctioning nut grinder?
How to Answer
- 1
Identify the issue you faced with the nut grinder.
- 2
Describe the steps you took to diagnose the problem.
- 3
Explain how you resolved the issue effectively.
- 4
Mention any tools or techniques you used during troubleshooting.
- 5
Share the outcome and any lessons learned.
Example Answers
In my previous role, the nut grinder frequently jammed. I inspected the feed chute and discovered an accumulation of leftover nuts. I cleared the chute, then adjusted the grinder's settings to ensure proper flow. The grinder worked efficiently after that, and production resumed without delay.
Have you ever worked in a team to optimize grinding processes? What was your role?
How to Answer
- 1
Start with a brief description of the team project and its goals
- 2
Clearly define your specific role and contributions
- 3
Mention any tools or methods used for process optimization
- 4
Include measurable outcomes or improvements achieved
- 5
Express what you learned from the teamwork experience
Example Answers
In my last position, I worked on a team that aimed to reduce material waste in the grinding process. I was responsible for analyzing data and suggesting adjustments to the grinding speed. We implemented these changes and reduced waste by 15%, which also improved overall efficiency.
Don't Just Read Nut Grinder Questions - Practice Answering Them!
Reading helps, but actual practice is what gets you hired. Our AI feedback system helps you improve your Nut Grinder interview answers in real-time.
Personalized feedback
Unlimited practice
Used by hundreds of successful candidates
Tell us about a time when you prioritized safety while operating heavy machinery.
How to Answer
- 1
Choose a specific example from your experience.
- 2
Describe the situation and the type of machinery involved.
- 3
Explain the safety measures you implemented.
- 4
Highlight the outcome and any lessons learned.
- 5
Keep your response concise and focused.
Example Answers
During my time at the warehouse, I operated a forklift. I noticed a colleague not wearing their safety gear. I stopped the machine and reminded them of the importance of safety. As a result, we all became more diligent about wearing our gear, ensuring a safer work environment.
Describe a situation where you had to ensure the quality of ground nuts. What steps did you take?
How to Answer
- 1
Start with a specific example from your past experience.
- 2
Mention the quality standards or specifications you had to meet.
- 3
Explain the steps you took to check and maintain quality.
- 4
Highlight any tools or techniques you used during the process.
- 5
Conclude with the outcome and how it benefited the company.
Example Answers
In my previous role at a nut processing facility, I was responsible for overseeing the grinding process of almonds. I ensured quality by first specifying the grind size required for our almond butter product. I regularly checked the nuts for humidity levels and used calibrated machines for consistent results. Additionally, I implemented a random sampling method to taste-test the product during processing. This led to a 15% decrease in returns due to quality issues.
How have you adapted to changes in production demands in your previous roles?
How to Answer
- 1
Identify specific changes you faced in production demands.
- 2
Describe the actions you took to adapt to those changes.
- 3
Highlight any tools or methods you used to improve efficiency.
- 4
Emphasize collaboration with your team to meet new demands.
- 5
Conclude with the positive outcomes from your adaptations.
Example Answers
In my previous role, we experienced a sudden increase in demand for a specific product. I quickly analyzed our workflow and proposed adjustments, reallocating resources and prioritizing tasks. I also organized team meetings to boost morale and ensure everyone was aligned. As a result, we met the new demands without sacrificing quality.
Tell me about a time when you had to manage multiple tasks in a high-pressure environment.
How to Answer
- 1
Choose a specific situation that highlights your multitasking skills.
- 2
Explain the tasks you had to manage and the pressure involved.
- 3
Show how you prioritized the tasks effectively.
- 4
Discuss the outcome and what you learned from the experience.
- 5
Keep your answer concise and focused on your role in the situation.
Example Answers
In my previous job at a coffee shop, I had to handle multiple orders during a weekend rush. I prioritized the orders based on complexity and communicated with my team to delegate tasks. I managed to serve all customers on time, which improved our reviews that week.
Have you ever suggested a new process or technique in your past job? What was the outcome?
How to Answer
- 1
Identify a specific instance where you suggested a process change
- 2
Explain the context and the reason for your suggestion
- 3
Describe the implementation process and how it was received
- 4
Share the positive outcomes or improvements that resulted
- 5
Mention any feedback or recognition you received for your suggestion
Example Answers
In my last job at the bakery, I suggested we switch to a different grinding technique that maximized efficiency. I noticed our current method was taking too long and causing delays. After discussing with my manager, we implemented the change, which reduced grinding time by 20%, and improved our production speed substantially. The team appreciated the change and I was recognized in our monthly meeting for the contribution.
What motivates you to work efficiently and safely in a production environment?
How to Answer
- 1
Emphasize personal responsibility for safety and efficiency.
- 2
Connect your motivation to the importance of teamwork.
- 3
Mention how meeting production goals encourages you.
- 4
Discuss past experiences that shaped your work ethic.
- 5
Highlight your commitment to quality and workplace safety.
Example Answers
I am motivated by the responsibility of ensuring both my safety and the safety of my colleagues. I believe that working efficiently helps us all meet our goals and fosters a positive team environment.
Don't Just Read Nut Grinder Questions - Practice Answering Them!
Reading helps, but actual practice is what gets you hired. Our AI feedback system helps you improve your Nut Grinder interview answers in real-time.
Personalized feedback
Unlimited practice
Used by hundreds of successful candidates
Describe an experience where collaboration was key to resolving a nut grinding issue.
How to Answer
- 1
Think of a specific situation where teamwork helped solve a problem.
- 2
Highlight the roles of different team members and how they contributed.
- 3
Describe the outcome and how collaboration improved the final result.
- 4
Use clear examples to illustrate your points.
- 5
Keep the answer focused on your personal contributions.
Example Answers
In my previous job at a nut processing facility, we faced an issue where the grinder would jam frequently. I collaborated with the maintenance team and the production staff. Together, we discovered that the problem was due to inconsistent nut size. By implementing a pre-sorting process, we reduced jams by 30% and improved grinding efficiency.
Situational Interview Questions
If the grinder suddenly stopped working during a peak production hour, what steps would you take?
How to Answer
- 1
Quickly assess the situation and determine the cause of the stoppage
- 2
Notify your supervisor or team lead immediately
- 3
Isolate the grinder if necessary to ensure safety
- 4
Check the manual or troubleshooting guide for common issues
- 5
If simple fixes do not work, escalate to maintenance promptly
Example Answers
First, I would check the grinder for any visible issues, such as blockages or faults. Then, I would inform my supervisor about the situation. If it’s safe, I might attempt basic troubleshooting, but I would escalate to maintenance if I can't resolve it quickly.
If you notice a discrepancy in the consistency of ground nuts, how would you handle it?
How to Answer
- 1
Identify the source of the inconsistency by checking equipment settings and ingredient quality.
- 2
Communicate the issue to your supervisor or team immediately.
- 3
Test a small batch to assess the extent of the problem.
- 4
Adjust the grinder settings or process as necessary to correct the consistency.
- 5
Document the incident and any adjustments made for future reference.
Example Answers
I would first check the grinder settings and inspect the quality of the nuts used. If I find a problem, I would inform my supervisor right away and run a small test batch to see if the issue persists. Then, I would make the needed adjustments before continuing production.
Don't Just Read Nut Grinder Questions - Practice Answering Them!
Reading helps, but actual practice is what gets you hired. Our AI feedback system helps you improve your Nut Grinder interview answers in real-time.
Personalized feedback
Unlimited practice
Used by hundreds of successful candidates
How would you adjust your grinding process if you were given a higher volume production target?
How to Answer
- 1
Assess current grinding capacity and identify bottlenecks
- 2
Consider increasing machine speed or using a larger grinder
- 3
Implement workflow changes to enhance efficiency
- 4
Evaluate the quality of grind at higher volume to ensure standards
- 5
Collaborate with the team to distribute workload effectively
Example Answers
I would first analyze our current grinder's capacity to pinpoint any bottlenecks. If feasible, I'd increase the grinder speed while monitoring the quality, or switch to one with a larger capacity to meet demand. Additionally, I'd optimize our workflow to streamline the process.
If a new employee joins your team, how would you train them on operating the nut grinder safely and effectively?
How to Answer
- 1
Begin with an overview of the nut grinder's parts and functions.
- 2
Demonstrate safety protocols, including proper locking mechanisms.
- 3
Walk them through the grinding process step-by-step.
- 4
Supervise their first few uses, providing feedback and corrections.
- 5
Encourage questions and ensure they understand the safety guidelines.
Example Answers
I would start by explaining the nut grinder's components before demonstrating its operation and safety features. Then, I'd guide the new employee through a step-by-step process while supervising their first attempts and addressing any questions they have.
How would you handle a situation where a batch of ground nuts failed quality control tests?
How to Answer
- 1
Acknowledge the seriousness of the quality control issue
- 2
Investigate the cause of the failure promptly and thoroughly
- 3
Communicate transparently with the team and supervisors
- 4
Implement corrective actions to prevent future issues
- 5
Document the process and outcomes for future reference
Example Answers
I would first assess the quality control report to understand the specific reasons for the failure. Then, I would collaborate with my team to identify the root cause, whether it was a processing mistake or equipment malfunction. After that, I would inform management and propose immediate solutions to rectify the issue and improve our processes.
How would you respond to customer complaints regarding the taste of your ground nuts?
How to Answer
- 1
Listen carefully to the customer's feedback and acknowledge their taste concerns.
- 2
Ask specific questions to understand their taste preferences better.
- 3
Provide reassurance that you take their feedback seriously and will look into the matter.
- 4
Offer a replacement or refund if appropriate, to demonstrate commitment to customer satisfaction.
- 5
Encourage the customer to try a different product or batch, expressing confidence in quality.
Example Answers
I would listen to the customer's feedback and acknowledge their concerns about the taste of our ground nuts. Then, I would ask specific questions to learn more about their preferences. I would assure them that their feedback is valuable and we will investigate the issue. If needed, I would offer a replacement or suggest a different product that might better meet their taste.
If you were part of a production team under tight deadlines, how would you contribute to maintaining efficiency?
How to Answer
- 1
Prioritize tasks by urgency and importance to focus on critical activities.
- 2
Communicate openly with team members to ensure everyone is aligned and aware of deadlines.
- 3
Stay organized by using checklists or production schedules to track progress.
- 4
Identify potential bottlenecks early and propose solutions proactively.
- 5
Be flexible and ready to adapt to changing circumstances or unexpected challenges.
Example Answers
I would prioritize the most urgent tasks and keep the team informed about any potential delays, ensuring we all stay on the same page.
If you notice an unsafe practice among colleagues while using the grinder, how would you address it?
How to Answer
- 1
Assess the situation and ensure you understand the unsafe practice clearly
- 2
Prioritize your safety and the safety of others before intervening
- 3
Calmly approach the colleague and express your concerns about the practice
- 4
Suggest safer alternatives or refer to safety protocols
- 5
Report the issue to a supervisor if the unsafe practice continues
Example Answers
I would first ensure the situation is safe before addressing it. Then, I would approach my colleague and politely explain my concern about what I saw, recommending a safer method based on our safety guidelines.
How would you manage stress during a critical production outage?
How to Answer
- 1
Stay calm and assess the situation quickly
- 2
Prioritize tasks to address the most critical issues first
- 3
Communicate clearly with the team to coordinate efforts
- 4
Use stress-reduction techniques like deep breathing if needed
- 5
Document the situation for future reference and learning
Example Answers
In a critical production outage, I would first take a moment to stay calm and quickly assess what the key issues are. Then, I would prioritize which problems need to be addressed immediately and communicate with my team to ensure we are all aligned on our next steps. Throughout the process, I would use deep breathing techniques to manage my stress and keep a clear head.
Technical Interview Questions
What types of nuts have you worked with, and how does the grinding process differ for each type?
How to Answer
- 1
List specific nuts you have experience with like almonds, walnuts, and cashews.
- 2
Explain the texture and fat content differences among these nuts.
- 3
Describe how these factors influence the grinding time and technique.
- 4
Mention any specific grinding equipment or methods used.
- 5
Highlight any challenges faced and how you overcame them.
Example Answers
I have worked primarily with almonds, walnuts, and peanuts. Almonds have a lower fat content, so they tend to grind into a finer flour more quickly, while walnuts are oilier and can turn into butter faster. For almonds, I prefer using a food processor, while for walnuts, a heavy-duty grinder is more effective to handle the oil.
What safety checks do you perform before operating a nut grinder?
How to Answer
- 1
Inspect the nut grinder for any visible damage or wear.
- 2
Ensure all guards and safety covers are in place and functioning.
- 3
Check that the power cord is in good condition and properly plugged in.
- 4
Verify that the machine is clean and free of debris before use.
- 5
Familiarize yourself with the emergency shut-off mechanism.
Example Answers
Before operating the nut grinder, I check for any signs of damage on the machine, ensure safety guards are correctly installed, and confirm the power cord is safe to use.
Don't Just Read Nut Grinder Questions - Practice Answering Them!
Reading helps, but actual practice is what gets you hired. Our AI feedback system helps you improve your Nut Grinder interview answers in real-time.
Personalized feedback
Unlimited practice
Used by hundreds of successful candidates
How do you maintain the nut grinder to ensure it operates efficiently?
How to Answer
- 1
Regularly clean the grinder after each use to prevent residue buildup
- 2
Check and tighten any loose screws or components frequently
- 3
Lubricate moving parts according to the manufacturer's recommendations
- 4
Inspect blades for sharpness and replace or sharpen as needed
- 5
Keep the grinder in a dry environment to prevent rust and corrosion
Example Answers
I maintain the nut grinder by cleaning it thoroughly after every use, ensuring no nuts or oils remain inside. I also check the screws and tightness of any components daily, lubricate moving parts as suggested, and make sure the blades are sharp for efficient grinding.
Explain the different grinding techniques and how they affect the final product.
How to Answer
- 1
Start by defining key grinding techniques like dry grinding, wet grinding, and cold grinding.
- 2
Explain how the particle size can vary with each technique and its impact on texture and flavor.
- 3
Discuss the type of materials suited for each method and their applications in nut grinding.
- 4
Mention the importance of heat generation during grinding and how it can affect oils in nuts.
- 5
Conclude with a summary of how these techniques can influence the quality of the final nut product.
Example Answers
There are several grinding techniques including dry grinding, which produces a coarse texture, and wet grinding, which results in a creamier product. Dry grinding works well for harder nuts like almonds, while wet grinding is better for softer nuts like cashews. Heat generation can cause oils to separate, so using a cold grinding method preserves flavor.
What are common issues you might encounter with nut grinders, and how would you address them?
How to Answer
- 1
Identify mechanical issues like overheating or clogging
- 2
Discuss electrical problems such as power failures
- 3
Mention product quality concerns with grain fineness
- 4
Talk about maintenance practices to prevent issues
- 5
Provide examples of troubleshooting steps
Example Answers
Common issues with nut grinders include overheating and clogging. I would monitor the temperature during use and ensure that the grinder is cleaned regularly to prevent nut buildup.
What parameters do you consider critical when setting up the nut grinder?
How to Answer
- 1
Identify the type of nuts being ground and their specific requirements.
- 2
Set the correct grind size according to the recipe or end use.
- 3
Ensure the grinder settings are calibrated for optimal efficiency.
- 4
Check for proper maintenance and cleanliness of the machine.
- 5
Adjust the feed rate to maintain consistent grinding without clogging.
Example Answers
I focus on the type of nuts to ensure the grind size fits their purpose, like using a finer grind for nut butter. I also check the machine's calibration and maintenance before starting.
What health and safety regulations must you consider when operating a nut grinder?
How to Answer
- 1
Identify key regulations such as PPE requirements like gloves and goggles.
- 2
Discuss cleanliness and hygiene standards to prevent contamination.
- 3
Mention the importance of machine guarding to prevent accidents.
- 4
Explain the need for proper training and understanding of emergency procedures.
- 5
Highlight regular maintenance checks to ensure equipment safety.
Example Answers
When operating a nut grinder, I always prioritize wearing personal protective equipment like gloves and goggles to ensure my safety. I also maintain cleanliness to avoid any potential contamination of the nuts.
What emerging trends in nut processing have you observed, and how do they impact your work?
How to Answer
- 1
Identify specific trends relevant to nut processing, such as automation or sustainability.
- 2
Discuss how these trends affect efficiency, cost, or product quality.
- 3
Mention any technologies or methods that are gaining popularity.
- 4
Connect the trends to your previous or current work experience.
- 5
Be prepared to explain how you adapt to or leverage these trends.
Example Answers
One emerging trend I've observed is the increased use of automation in nut processing. This has significantly improved efficiency, reducing labor costs while ensuring consistent product quality. In my previous role, I implemented automated sorting machines, which led to a 20% increase in production capacity.
How do you incorporate feedback from quality control into your grinding process?
How to Answer
- 1
Listen carefully to the feedback from quality control.
- 2
Identify specific areas where improvements are needed.
- 3
Make adjustments to grinding settings based on the feedback.
- 4
Test the new process and gather results to ensure quality standards are met.
- 5
Communicate with the quality control team to ensure ongoing improvements.
Example Answers
I prioritize feedback by reviewing the quality control reports thoroughly. If they highlight uneven consistency in the grind, I adjust the grinder settings for finer adjustments, then retest the product to confirm the changes meet standards.
What steps would you take to optimize the grinding time while maintaining quality?
How to Answer
- 1
Assess the type of nuts being ground and their specifications
- 2
Adjust the grinder settings for optimal speed and consistency
- 3
Monitor the temperature during grinding to prevent overheating
- 4
Implement a regular maintenance schedule for grinding equipment
- 5
Conduct tests to determine the ideal grind time for each nut type
Example Answers
To optimize grinding time, I would first assess the specific nuts being used for grinding and fine-tune the grinder settings to maximize efficiency. I would ensure the equipment is regularly maintained to minimize downtimes.
Don't Just Read Nut Grinder Questions - Practice Answering Them!
Reading helps, but actual practice is what gets you hired. Our AI feedback system helps you improve your Nut Grinder interview answers in real-time.
Personalized feedback
Unlimited practice
Used by hundreds of successful candidates
Nut Grinder Position Details
Related Positions
Similar positions you might be interested in.
Ace Your Next Interview!
Practice with AI feedback & get hired faster
Personalized feedback
Used by hundreds of successful candidates
Ace Your Next Interview!
Practice with AI feedback & get hired faster
Personalized feedback
Used by hundreds of successful candidates