Top 31 Plant Superintendent Interview Questions and Answers [Updated 2025]
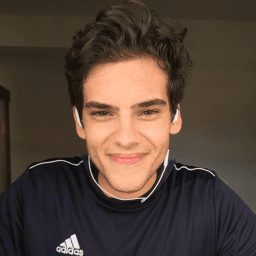
Andre Mendes
•
March 30, 2025
Navigating the interview process for a Plant Superintendent role can be daunting, but we’ve got you covered with our expertly curated list of the most common interview questions. In this blog post, you'll find insightful example answers and practical tips to help you respond confidently and effectively. Whether you're a seasoned professional or new to the field, these insights will prepare you for success in your next interview.
Download Plant Superintendent Interview Questions in PDF
To make your preparation even more convenient, we've compiled all these top Plant Superintendentinterview questions and answers into a handy PDF.
Click the button below to download the PDF and have easy access to these essential questions anytime, anywhere:
List of Plant Superintendent Interview Questions
Behavioral Interview Questions
Can you describe a time when you successfully led a team through a major plant upgrade?
How to Answer
- 1
Start with a clear context of the upgrade.
- 2
Highlight your role and responsibilities.
- 3
Discuss the challenges faced and solutions implemented.
- 4
Emphasize team collaboration and communication.
- 5
Conclude with the positive outcomes achieved.
Example Answers
During a major upgrade to our production line, I led a team of 15 technicians. We faced equipment delays and budget constraints. I organized daily briefings to address issues and kept communication open. The upgrade was completed on time and increased production efficiency by 25%.
Don't Just Read Plant Superintendent Questions - Practice Answering Them!
Reading helps, but actual practice is what gets you hired. Our AI feedback system helps you improve your Plant Superintendent interview answers in real-time.
Personalized feedback
Unlimited practice
Used by hundreds of successful candidates
Tell me about a conflict you had with a team member and how you resolved it.
How to Answer
- 1
Choose a specific conflict that had a positive outcome.
- 2
Focus on how you listened to the other person's perspective.
- 3
Explain the steps you took to address the issue together.
- 4
Highlight the lessons learned and how it improved team dynamics.
- 5
Keep it professional and avoid personal attacks.
Example Answers
I had a disagreement with a colleague over the best approach to a project. I listened to his ideas and shared my concerns. Together, we organized a meeting to discuss both perspectives and came up with a compromise that merged our approaches, which ultimately improved the project's success.
Describe a challenging operational issue you've encountered and how you tackled it.
How to Answer
- 1
Identify a specific operational issue you faced in your previous role.
- 2
Explain the steps you took to analyze the situation and gather information.
- 3
Discuss how you collaborated with your team or other departments to address the issue.
- 4
Highlight the solution you implemented and the impact it had on operations.
- 5
Mention any lessons learned and how they can be applied in future situations.
Example Answers
In my previous position, we faced a significant delay in production due to equipment breakdown. I analyzed the issue by reviewing maintenance logs and consulting with the maintenance team. We developed a rapid response plan and reallocated resources to minimize the downtime. This resulted in a 25% reduction in our average downtime and improved overall team coordination. I learned the importance of proactive maintenance scheduling.
Can you give an example of how you fostered collaboration among your team members during a challenging project?
How to Answer
- 1
Identify a specific project with clear challenges
- 2
Describe the team dynamics and individual strengths
- 3
Explain the strategies used to encourage collaboration
- 4
Share the positive outcome or impact on the project
- 5
Include any feedback received from team members
Example Answers
During a recent equipment upgrade project, I noticed the engineers and operators were not communicating effectively. I organized weekly cross-functional meetings where team members could share insights and concerns. This led to improved understanding of specific needs and resulted in completing the project ahead of schedule.
Discuss a time when you had to deliver difficult news to your team. How did you approach it?
How to Answer
- 1
Be honest and direct about the situation.
- 2
Acknowledge the team's emotions and concerns.
- 3
Provide clear context and reasons for the news.
- 4
Offer solutions or next steps to move forward.
- 5
Encourage open dialogue and address questions.
Example Answers
In my last role, I had to inform my team about significant budget cuts. I gathered everyone and explained the reasons, acknowledging their potential impact. I encouraged them to share their thoughts and we brainstormed ways to adapt, ensuring they felt involved in the solution.
Describe how you have handled underperforming employees in your past roles.
How to Answer
- 1
Identify specific performance issues clearly and factually
- 2
Engage in a one-on-one conversation to understand their challenges
- 3
Set clear, achievable goals for improvement with deadlines
- 4
Provide ongoing support and training resources
- 5
Regularly review progress and adjust the plan as needed
Example Answers
In my last position, I noticed a team member struggling to meet deadlines. I scheduled a meeting to discuss their workload and discovered they needed help with time management. Together, we set specific daily goals and I provided additional resources. After a few weeks, their performance improved significantly.
Tell me about a situation where you had to adapt to significant changes in your plant's operations.
How to Answer
- 1
Identify a specific change that occurred in plant operations.
- 2
Explain the reasons behind the change to set context.
- 3
Describe your role in managing the transition.
- 4
Highlight the outcome and any improvements achieved.
- 5
Mention any lessons learned or future adjustments made.
Example Answers
During a shift to automated machinery due to labor shortages, I collaborated with our engineering team to ensure smooth integration. I organized training sessions for staff on the new systems, resulting in a 20% increase in productivity and reduced downtime.
Give an example of a time when you introduced an innovative solution in the plant.
How to Answer
- 1
Identify a specific problem that needed solving.
- 2
Describe the innovative solution you implemented.
- 3
Explain the steps you took to implement this solution.
- 4
Highlight the impact of this solution on the plant's operations.
- 5
Use metrics or outcomes to demonstrate success.
Example Answers
At my previous plant, we faced frequent downtime due to machine breakdowns. I introduced a predictive maintenance system using IoT sensors, which allowed us to monitor equipment health in real-time. After implementing this, we reduced downtime by 30% within six months.
Don't Just Read Plant Superintendent Questions - Practice Answering Them!
Reading helps, but actual practice is what gets you hired. Our AI feedback system helps you improve your Plant Superintendent interview answers in real-time.
Personalized feedback
Unlimited practice
Used by hundreds of successful candidates
Technical Interview Questions
What methods do you use to monitor and improve plant production efficiency?
How to Answer
- 1
Discuss specific metrics you track for production efficiency
- 2
Mention tools or software you use for data analysis
- 3
Share examples of process improvements you implemented
- 4
Explain how you engage your team in efficiency initiatives
- 5
Highlight any continuous improvement methodologies you use
Example Answers
I monitor production efficiency by tracking key metrics like OEE and cycle times using advanced analytics software. Implementing improvements based on this data, such as adjusting equipment settings, helped reduce downtime by 15%.
Can you explain the maintenance strategies you implement to ensure equipment reliability?
How to Answer
- 1
Focus on preventive maintenance to reduce breakdowns.
- 2
Incorporate regular inspections and audits of equipment.
- 3
Utilize data analysis to track performance and predict failures.
- 4
Establish a clear maintenance schedule for all critical machinery.
- 5
Train staff on best practices for equipment care and operation.
Example Answers
I implement a preventive maintenance program that includes regular inspections and scheduled servicing of all critical equipment. This helps to identify issues before they lead to failures.
Don't Just Read Plant Superintendent Questions - Practice Answering Them!
Reading helps, but actual practice is what gets you hired. Our AI feedback system helps you improve your Plant Superintendent interview answers in real-time.
Personalized feedback
Unlimited practice
Used by hundreds of successful candidates
What regulations do you consider most important in plant operations, and how do you ensure compliance?
How to Answer
- 1
Identify key regulations specific to the industry, such as environmental, safety, and quality standards.
- 2
Explain how you stay updated on regulatory changes through training and resources.
- 3
Discuss your methods for training staff on compliance and instilling a culture of safety.
- 4
Highlight specific compliance monitoring practices, such as audits and inspections.
- 5
Provide examples of how your compliance efforts have positively impacted plant operations.
Example Answers
I consider OSHA regulations and EPA standards critical for ensuring a safe and environmentally compliant operation. I stay updated via professional seminars and update my team regularly through workshops, fostering a strong safety culture. We conduct quarterly audits to ensure compliance and quickly address any identified issues.
How do you apply Lean and Six Sigma principles in your plant management?
How to Answer
- 1
Identify specific Lean tools you've implemented, like 5S or Kaizen events
- 2
Explain how you've used Six Sigma methodologies to reduce defects, such as DMAIC
- 3
Share concrete examples of improvements in efficiency or quality outcomes
- 4
Discuss team training and involvement in Lean and Six Sigma initiatives
- 5
Highlight the impact on costs or production rates from your efforts
Example Answers
In my previous role, I implemented 5S to enhance workplace organization, leading to a 20% reduction in search time for tools and materials.
Describe your experience with budgeting and cost control in a manufacturing environment.
How to Answer
- 1
Highlight specific budgeting methods you have used.
- 2
Discuss any tools or software that helped in tracking costs.
- 3
Provide examples of how you reduced costs without compromising quality.
- 4
Mention collaboration with other departments for effective budgeting.
- 5
Frame your experience with measurable results or outcomes.
Example Answers
In my previous role, I utilized zero-based budgeting to align expenses with production goals. By implementing an inventory management system, I tracked costs effectively and reduced waste by 15%.
What techniques do you use for effective production scheduling?
How to Answer
- 1
Prioritize clear communication with team members and departments.
- 2
Utilize software tools for real-time data tracking and analysis.
- 3
Implement a buffer system to manage unexpected delays.
- 4
Regularly review and adjust schedules based on production performance.
- 5
Involve operators in scheduling discussions to leverage their insights.
Example Answers
I prioritize communication, ensuring my team is aligned on production goals and schedules. I use scheduling software like Trello to track tasks in real-time, allowing for quick adjustments as needed.
How do you assess and ensure product quality during the manufacturing process?
How to Answer
- 1
Implement regular quality checks at key stages of production
- 2
Use statistical process control to monitor variations
- 3
Train staff on quality standards and procedures
- 4
Incorporate customer feedback into quality assessments
- 5
Conduct root cause analysis for any defects or issues
Example Answers
I assess product quality by establishing key inspection points during production. I implement regular quality checks and involve the team in training them on standards.
How do you stay updated with the latest technologies relevant to plant management?
How to Answer
- 1
Subscribe to industry newsletters and publications
- 2
Attend webinars and workshops on emerging technologies
- 3
Participate in professional organizations and local chapters
- 4
Follow leading experts and companies on social media
- 5
Engage in online forums to discuss best practices and innovations
Example Answers
I regularly subscribe to industry newsletters like Plant Engineering to receive updates on technology trends. Additionally, I attend webinars and workshops to learn from experts and share insights with my team.
Situational Interview Questions
If a critical piece of equipment fails unexpectedly, how would you react to minimize production downtime?
How to Answer
- 1
Immediately assess the situation and identify the failure's impact on production.
- 2
Communicate the issue to the team and relevant stakeholders promptly.
- 3
Implement emergency procedures to safely manage the failure.
- 4
Coordinate with maintenance personnel to initiate repairs or replacements.
- 5
Explore alternative production methods or equipment to keep operations running.
Example Answers
In the event of equipment failure, I would first assess the impact on our production line. Then, I would quickly inform my team and relevant leaders to ensure everyone is aware. We would follow our emergency procedures while I coordinate with maintenance to expedite repairs. If possible, I would also look at alternative equipment to minimize downtime further.
Imagine a situation where you have limited resources but multiple production objectives. How would you prioritize?
How to Answer
- 1
Assess the impact of each objective on overall production goals.
- 2
Identify critical deadlines and compliance requirements.
- 3
Evaluate resource availability and constraints.
- 4
Engage the team for input on urgent needs and potential solutions.
- 5
Create a clear prioritization matrix to visualize objectives.
Example Answers
I would start by assessing the impact of each objective on our production goals and then focus on the ones that significantly affect our output quality and customer satisfaction. I would also consult with my team to gather insights on urgent needs.
Don't Just Read Plant Superintendent Questions - Practice Answering Them!
Reading helps, but actual practice is what gets you hired. Our AI feedback system helps you improve your Plant Superintendent interview answers in real-time.
Personalized feedback
Unlimited practice
Used by hundreds of successful candidates
If you notice a drop in team morale, what steps would you take to address this issue?
How to Answer
- 1
Identify the root causes by conducting one-on-one conversations with team members.
- 2
Encourage open communication to create a safe space for sharing concerns.
- 3
Implement team-building activities to strengthen relationships.
- 4
Recognize and celebrate individual and team achievements regularly.
- 5
Provide opportunities for professional development to show investment in team growth.
Example Answers
First, I would hold one-on-one meetings to understand the specific concerns impacting morale. Then, I would facilitate a team meeting to foster open dialogue. To boost morale, I'd organize a team-building event and ensure we celebrate our successes regularly.
How would you handle a situation where your department needs support from another department that is not responsive?
How to Answer
- 1
Identify the key stakeholders in the other department and approach them directly.
- 2
Communicate the urgency and importance of your request clearly.
- 3
Propose a specific meeting or call to discuss the needs and potential solutions.
- 4
Follow up with a polite reminder if they do not respond within a reasonable time.
- 5
Consider escalating the issue to higher management if necessary.
Example Answers
I would first reach out to the key people in the other department to explain our situation and the urgent need for their support. If they are unresponsive, I'd schedule a meeting to discuss how we can collaborate effectively.
What would you do if you discovered a compliance issue during an internal audit?
How to Answer
- 1
Assess the severity of the compliance issue immediately
- 2
Document the findings with clear evidence and details
- 3
Notify the relevant stakeholders and management promptly
- 4
Develop a plan for corrective action and prevention
- 5
Follow up to ensure compliance and effectiveness of the actions taken
Example Answers
Upon discovering a compliance issue, I would first evaluate its urgency and impact. Then, I would document the issue thoroughly, gathering all relevant data. I would inform management and affected teams immediately, and propose a corrective action plan. Lastly, I would set up a follow-up to ensure the issue is resolved and similar issues do not occur in the future.
If you had to implement a new technology in the plant while maintaining production, how would you go about it?
How to Answer
- 1
Assess the current production capabilities and identify the best integration points for the new technology
- 2
Develop a detailed plan that includes timelines, training, and resource allocation
- 3
Engage stakeholders to gain support and address concerns upfront
- 4
Pilot the new technology on a small scale to evaluate performance without disrupting overall production
- 5
Gather feedback and make adjustments before full-scale implementation
Example Answers
First, I would evaluate our current processes to see where the new technology fits best. Then, I'd create a rollout plan outlining timelines and training for the staff. I would involve key stakeholders in discussions to ensure their concerns are addressed. After that, I'd run a pilot program on a small section of the plant to assess impact before a wider launch.
How would you approach training new hires to ensure they are safe and effective in their roles?
How to Answer
- 1
Start with a comprehensive orientation on safety protocols and equipment use
- 2
Pair new hires with experienced mentors for hands-on learning
- 3
Utilize checklists and step-by-step guides for complex tasks
- 4
Conduct regular safety drills and assessments to reinforce knowledge
- 5
Gather feedback from new hires to continuously improve the training program
Example Answers
I would begin by providing a detailed orientation focused on our safety protocols. Then, I would pair new hires with seasoned employees for practical training, ensuring they have guidance as they learn. Regular safety drills would help reinforce their training and identify areas for improvement.
If you needed to reduce operational costs by 10%, what areas would you focus on?
How to Answer
- 1
Analyze energy consumption for potential savings.
- 2
Evaluate labor efficiency and assess workforce productivity.
- 3
Review supplier contracts for better pricing or alternatives.
- 4
Implement regular maintenance to prevent costly breakdowns.
- 5
Optimize inventory levels to reduce excess stock.
Example Answers
I would start by analyzing our energy consumption to identify areas where we can implement more efficient practices. Additionally, I would evaluate our labor efficiency to ensure we're maximizing productivity. Reviewing supplier contracts could yield better pricing or allow us to switch to more cost-effective sources.
What initiatives would you launch to improve safety culture within the plant?
How to Answer
- 1
Implement regular safety training sessions for all employees.
- 2
Establish a system for reporting near misses without fear of repercussions.
- 3
Encourage employee participation in safety committees to share insights.
- 4
Conduct monthly safety audits and share the results openly.
- 5
Recognize and reward safe behaviors to promote engagement.
Example Answers
I would launch regular safety training sessions to ensure everyone is updated on best practices, combined with a near-miss reporting system that empowers employees to speak up without fear.
Suppose a plant project is falling behind schedule. How would you communicate this to stakeholders?
How to Answer
- 1
Assess the situation and gather relevant data on delays
- 2
Be transparent and clear about the reasons for the delay
- 3
Outline the potential impact on project goals and timelines
- 4
Suggest corrective actions and highlight any support needed
- 5
Plan a follow-up to keep stakeholders informed of progress
Example Answers
I would first gather all relevant data to understand the reasons for the delay. Then, I would communicate transparently with stakeholders, explaining the causes and potential impacts on timelines, while also suggesting actionable steps we can take moving forward.
Don't Just Read Plant Superintendent Questions - Practice Answering Them!
Reading helps, but actual practice is what gets you hired. Our AI feedback system helps you improve your Plant Superintendent interview answers in real-time.
Personalized feedback
Unlimited practice
Used by hundreds of successful candidates
How would you introduce sustainability practices in plant operations while balancing production needs?
How to Answer
- 1
Assess current operations for sustainability gaps
- 2
Engage staff in sustainability training and ideas
- 3
Implement energy-efficient technologies gradually
- 4
Set measurable sustainability goals aligned with production
- 5
Monitor progress and adjust practices based on feedback
Example Answers
First, I would assess our current processes to identify areas where we can reduce waste and improve energy use. Next, I'd create a training program to engage and empower staff to contribute ideas. Introducing energy-efficient technologies over time will help us minimize disruptions, and I'd ensure our sustainability goals align with our production targets.
If a new policy is implemented that your team disagrees with, how would you manage the response?
How to Answer
- 1
Acknowledge team concerns openly and create a safe space for discussion
- 2
Gather feedback to understand specific issues and suggestions from the team
- 3
Communicate the reasons behind the policy clearly and transparently
- 4
Engage in collaborative problem-solving to find a compromise or alternative
- 5
Follow up with the team regularly to address ongoing concerns and make adjustments
Example Answers
I would start by holding a team meeting to discuss the new policy and listen to their specific concerns. Understanding their perspective is crucial. Then, I would explain the rationale behind the policy and how it fits into our overall objectives. Together, we can brainstorm solutions or adjustments to make the policy more acceptable.
If production data shows a consistent decline, how would you analyze the issue and determine a course of action?
How to Answer
- 1
Review historical production data to identify trends.
- 2
Conduct root cause analysis to identify contributing factors.
- 3
Engage with team members to gather insights and observations.
- 4
Benchmark against similar operations to find best practices.
- 5
Develop an action plan with targeted interventions and timelines.
Example Answers
I would start by reviewing historical production metrics to pinpoint when the decline began. Then, I'd perform a root cause analysis, collaborating with my team to gather their insights. Finally, I'd develop an action plan that includes process improvements and set clear timelines for implementation.
Plant Superintendent Position Details
Salary Information
Recommended Job Boards
ZipRecruiter
www.ziprecruiter.com/Jobs/Plant-SuperintendentThese job boards are ranked by relevance for this position.
Related Positions
Ace Your Next Interview!
Practice with AI feedback & get hired faster
Personalized feedback
Used by hundreds of successful candidates
Ace Your Next Interview!
Practice with AI feedback & get hired faster
Personalized feedback
Used by hundreds of successful candidates