Top 29 Printing Plate Maker Interview Questions and Answers [Updated 2025]
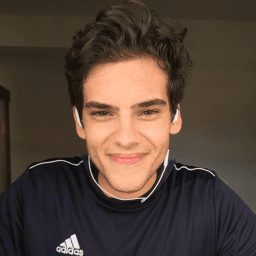
Andre Mendes
•
March 30, 2025
In the competitive world of printing, nailing an interview for the role of Printing Plate Maker requires more than just technical skills. This blog post equips you with the most common interview questions you'll face, offering insightful examples and effective tips to craft standout answers. Prepare to impress your potential employers with confidence and clarity, as you navigate through these essential questions and ace your interview.
Download Printing Plate Maker Interview Questions in PDF
To make your preparation even more convenient, we've compiled all these top Printing Plate Makerinterview questions and answers into a handy PDF.
Click the button below to download the PDF and have easy access to these essential questions anytime, anywhere:
List of Printing Plate Maker Interview Questions
Behavioral Interview Questions
Can you give an example of how customer feedback influenced your work in plate making?
How to Answer
- 1
Reflect on specific feedback you received from customers.
- 2
Explain how you analyzed the feedback to identify actionable insights.
- 3
Describe the changes you made to your plate making process based on this feedback.
- 4
Highlight any improvements in customer satisfaction or product quality.
- 5
Use a clear example that shows your responsiveness to customer needs.
Example Answers
In my previous role, we received feedback that some prints had color variations. I analyzed the customer comments and adjusted our ink mixing process to ensure consistency. As a result, we saw a 20% reduction in complaints and improved customer trust.
Can you describe a time when you worked as part of a team to solve a problem in the printing process?
How to Answer
- 1
Identify a specific printing problem you faced as a team.
- 2
Explain your role in the team and the actions you took.
- 3
Describe how the team collaborated to find a solution.
- 4
Highlight the outcome and any lessons learned.
- 5
Keep it concise and focused on teamwork and results.
Example Answers
In my previous position, our team noticed a recurring issue with color misalignment during the printing run. I took the initiative to gather everyone for a quick meeting to discuss potential causes. We determined that the problem was related to our outdated calibration equipment. Working together, we set up a new calibration schedule and monitored the results closely. As a result, our print quality improved significantly and we reduced reprints by 20%.
Don't Just Read Printing Plate Maker Questions - Practice Answering Them!
Reading helps, but actual practice is what gets you hired. Our AI feedback system helps you improve your Printing Plate Maker interview answers in real-time.
Personalized feedback
Unlimited practice
Used by hundreds of successful candidates
Tell me about a situation where your attention to detail caught a significant error in your work.
How to Answer
- 1
Focus on a specific example from your past work experience
- 2
Describe the situation clearly and concisely
- 3
Explain the error and how you discovered it
- 4
Highlight the impact of your attention to detail on the outcome
- 5
Conclude with what you learned from the experience
Example Answers
In my last job, I was responsible for preparing printing layouts. I noticed that one of the files had incorrect color codes just before the printing process started. I double-checked the files and found that the ink would have been the wrong shade, leading to a major production issue. I corrected it before the press started, saving the company time and resources. This experience taught me the importance of verifying details thoroughly.
Describe a time when you had to adapt quickly to changes in a project or production schedule.
How to Answer
- 1
Think of a specific example that illustrates your flexibility.
- 2
Explain the situation clearly, including the challenge faced.
- 3
Describe the actions you took to adapt to the changes.
- 4
Highlight the positive outcome of your actions.
- 5
Keep your answer focused and relevant to the printing industry.
Example Answers
In my previous role as a production assistant, we received an urgent request for a special print job with a tight deadline due to a client's last-minute marketing campaign. I quickly assessed our resources, coordinated with the team to prioritize this job, and adjusted our workflow. We managed to complete the job ahead of schedule, and the client was thrilled with the quality and speed, which strengthened our relationship.
How have you managed tight deadlines in your previous roles as a printing plate maker?
How to Answer
- 1
Prioritize tasks by urgency and importance
- 2
Communicate clearly with your team and clients about timelines
- 3
Utilize time management tools to keep track of deadlines
- 4
Anticipate potential delays and have contingency plans
- 5
Document processes to improve efficiency in future projects
Example Answers
In my last role, I prioritized urgent tasks by creating a daily checklist. I communicated with my team to ensure we met our tight deadlines, and I also scheduled regular check-ins to track our progress.
Have you ever implemented a new method or technology in your plate-making process? What was the outcome?
How to Answer
- 1
Identify a specific technology or method you used.
- 2
Explain why you chose to implement it.
- 3
Discuss the steps you took to integrate it into your workflow.
- 4
Share measurable outcomes or benefits from the implementation.
- 5
Reflect on any challenges faced and how you addressed them.
Example Answers
I introduced a digital plate-making system to enhance precision. I chose this method to reduce errors and improve efficiency. After integration, we saw a 30% decrease in production time and fewer reprints, which saved costs.
What steps do you take to stay updated on technological advancements in printing plate making?
How to Answer
- 1
Subscribe to industry journals and online publications focused on printing technologies.
- 2
Join professional organizations related to printing and attend their events or webinars.
- 3
Participate in online forums and discussion groups to share knowledge and insights.
- 4
Attend trade shows and expos to see new technologies and equipment firsthand.
- 5
Engage with manufacturers and suppliers for updates on their latest products and innovations.
Example Answers
I subscribe to printing technology magazines and regularly read articles about innovations in plate making. I also attend industry webinars to hear from experts.
Describe a time when you received constructive criticism. How did you respond?
How to Answer
- 1
Choose a specific example where criticism improved your work.
- 2
Explain the feedback clearly and how you felt initially.
- 3
Highlight the actions you took to implement the feedback.
- 4
Discuss the positive outcome from making those changes.
- 5
Keep it concise and focus on your growth from the experience.
Example Answers
In my previous job, my manager pointed out that my attention to detail in plate alignment could be improved. I felt a bit defensive initially, but I listened carefully. I started double-checking my work and even began using a checklist. As a result, my error rate decreased significantly, and I received praise for my improved accuracy.
Can you provide an example of when you took the initiative to improve a procedure in your previous job?
How to Answer
- 1
Identify a specific procedure you improved.
- 2
Explain the problem with the existing process.
- 3
Describe the action you took to improve it.
- 4
Highlight the positive outcomes of your initiative.
- 5
Keep your example relevant to printing or production.
Example Answers
In my last role, the ink mixing process was causing inconsistent print quality. I noticed that the measuring tools were not calibrated regularly, leading to errors. I took the initiative to implement a weekly calibration schedule for the equipment. As a result, our print quality improved significantly, and we reduced waste by 20%.
Don't Just Read Printing Plate Maker Questions - Practice Answering Them!
Reading helps, but actual practice is what gets you hired. Our AI feedback system helps you improve your Printing Plate Maker interview answers in real-time.
Personalized feedback
Unlimited practice
Used by hundreds of successful candidates
Technical Interview Questions
What common issues might arise during the plate-making process and how would you address them?
How to Answer
- 1
Identify specific issues such as incorrect exposure times.
- 2
Discuss quality control measures during the process.
- 3
Mention the importance of maintaining equipment regularly.
- 4
Explain how to troubleshoot and make adjustments quickly.
- 5
Highlight the need for good communication with the design team.
Example Answers
A common issue is incorrect exposure times which can lead to poor image quality. I would check the exposure settings and adjust them based on the material used. Regular calibration of equipment also helps prevent this.
What types of materials are commonly used in the production of printing plates?
How to Answer
- 1
Mention the main types of printing plates like offset, flexo, and digital.
- 2
Identify specific materials such as aluminum, polyester, and rubber.
- 3
Explain the purpose of each material in the printing process.
- 4
Keep explanations concise and relevant to the printing industry.
- 5
Demonstrate knowledge of recent advancements in plate materials.
Example Answers
Common materials for printing plates include aluminum for offset plates, polyester for low run jobs, and rubber for flexographic printing. Each material serves to create a strong and durable surface for ink transfer.
Don't Just Read Printing Plate Maker Questions - Practice Answering Them!
Reading helps, but actual practice is what gets you hired. Our AI feedback system helps you improve your Printing Plate Maker interview answers in real-time.
Personalized feedback
Unlimited practice
Used by hundreds of successful candidates
Can you explain how a photogravure printing plate is created?
How to Answer
- 1
Start by defining photogravure and its uses.
- 2
Explain the process of coating the plate with a light-sensitive emulsion.
- 3
Describe how the image is exposed using a photo negative.
- 4
Discuss the development process to reveal the image on the plate.
- 5
Mention the etching process to create depth before inking the plate.
Example Answers
Photogravure is a printing process that uses photographic images transferred to a metal plate. First, the plate is coated with a light-sensitive emulsion. Then, a photo negative is used to expose the emulsion. After that, the plate is developed to reveal the image, and finally, it undergoes an etching process to create texture for inking.
What software have you used for designing and preparing printing plates?
How to Answer
- 1
List specific software you've worked with, such as Adobe Illustrator or Photoshop.
- 2
Mention any specialized printing plate software you are familiar with.
- 3
Explain how you used each software in the context of printing plate preparation.
- 4
Highlight any relevant training or certifications in these software programs.
- 5
Show enthusiasm for learning new software if needed.
Example Answers
I have extensive experience using Adobe Illustrator for creating and preparing designs for printing plates. I've also used a program called FlexiSign specifically for preparing vinyl graphics.
Describe the step-by-step process of making a flexographic printing plate.
How to Answer
- 1
Start with image preparation and converting it to a digital format.
- 2
Use a laser engraving process to carve the image into a photopolymer plate.
- 3
Expose the plate to UV light through a film positive to harden specific areas.
- 4
Wash out unexposed areas to reveal the raised image.
- 5
Cure the plate using additional UV light to ensure durability.
Example Answers
The process starts with preparing the image and converting it to a digital format. Then, a laser engraver carves the image into a photopolymer plate. After that, the plate is exposed to UV light through a film positive to harden the desired areas. We wash out the unexposed areas to leave the raised image. Finally, we cure the plate with more UV light for durability.
What are the differences between analog and digital plate making systems?
How to Answer
- 1
Define both analog and digital plate making systems clearly
- 2
Highlight key differences such as process, accuracy, and cost
- 3
Mention a few specific advantages and disadvantages of each system
- 4
Use examples to illustrate your points
- 5
Keep your answer concise and focused on relevant industry terms
Example Answers
Analog plate making uses physical film to create plates, while digital plate making involves direct imaging from digital files. Analog often has lower setup costs but longer turnaround times due to film processing. Digital is generally faster and offers higher precision, making it ideal for short runs or varied jobs.
How do you perform routine maintenance on plate-making equipment?
How to Answer
- 1
Familiarize yourself with the equipment's manual for specific maintenance tasks.
- 2
Regularly clean all components to prevent buildup of dust and ink.
- 3
Check and replace worn or damaged parts to ensure equipment efficiency.
- 4
Lubricate moving parts as recommended to minimize wear and tear.
- 5
Perform routine checks on settings and calibrations to maintain quality.
Example Answers
I follow the equipment manual to perform routine maintenance, which includes cleaning the components daily, checking for any worn parts weekly, and lubricating them regularly.
Can you explain the role of chemistry in the plate-making process?
How to Answer
- 1
Discuss the chemical processes involved in preparing the plate.
- 2
Mention how chemistry affects the imaging and developing of plates.
- 3
Explain the role of different chemical solutions used during plate making.
- 4
Highlight the importance of chemical reactions in achieving image fidelity.
- 5
Refer to any environmental considerations related to the chemicals used.
Example Answers
In plate-making, chemistry plays a crucial role as it involves preparing photo-sensitive coatings that react to light. These coatings undergo a chemical change when exposed to a light source, forming the image on the plate. Additionally, developing solutions are used to remove unexposed areas, ensuring sharp images.
What regulatory standards do you need to comply with in printing plate making?
How to Answer
- 1
Research specific industry standards such as ISO 12647 for color management
- 2
Mention any environmental regulations relevant to waste and chemical disposal
- 3
Include safety regulations related to equipment operation and handling materials
- 4
Consider local laws regarding employee safety and health standards
- 5
Be prepared to discuss quality control measures you implement to meet these standards.
Example Answers
In my previous role, I ensured compliance with ISO 12647 which focuses on color accuracy in printing. Additionally, I adhered to local regulations concerning chemical safety and waste disposal to minimize environmental impact.
What methods do you use to ensure accurate color matching in your printing plates?
How to Answer
- 1
Use standardized color references like Pantone or CMYK color guides.
- 2
Perform regular calibration of printing equipment to maintain color accuracy.
- 3
Utilize spectrophotometers for precise color measurement.
- 4
Conduct tests and samples before final production to check for color integrity.
- 5
Document color matching processes and results for consistency.
Example Answers
I utilize standardized color references such as Pantone guides for color matching. I also calibrate the printing equipment regularly to ensure accuracy, and I use a spectrophotometer to measure colors precisely.
Don't Just Read Printing Plate Maker Questions - Practice Answering Them!
Reading helps, but actual practice is what gets you hired. Our AI feedback system helps you improve your Printing Plate Maker interview answers in real-time.
Personalized feedback
Unlimited practice
Used by hundreds of successful candidates
Situational Interview Questions
If you noticed that the color output on a printed product was off, what steps would you take to investigate and resolve the issue?
How to Answer
- 1
Check the calibration settings of the printer to ensure they are correct.
- 2
Review the color profiles used for the print job to identify any discrepancies.
- 3
Inspect the inks and materials to ensure they are not expired or faulty.
- 4
Conduct a test print and compare it to the expected output for any differences.
- 5
Document the findings and adjustments made for future reference.
Example Answers
First, I would check the printer's calibration settings to ensure they are accurate. Then, I would review the color profiles used for that specific print job. I would also examine the inks to make sure they're not expired. After that, I would run a test print to see if the issue persists.
Imagine you have a suggestion to improve the plate-making process. How would you present your ideas to the management?
How to Answer
- 1
Identify the specific area of the plate-making process to improve.
- 2
Gather data or examples to support your suggestion.
- 3
Prepare a clear and concise presentation of your idea.
- 4
Consider the benefits and potential challenges of your suggestion.
- 5
Be open to feedback and willing to discuss improvements.
Example Answers
I would focus on the ink drying process. I've noticed that optimizing the temperature can reduce drying time. I would present data comparing current drying times to potential improvements and outline the benefits in terms of efficiency and cost savings.
Don't Just Read Printing Plate Maker Questions - Practice Answering Them!
Reading helps, but actual practice is what gets you hired. Our AI feedback system helps you improve your Printing Plate Maker interview answers in real-time.
Personalized feedback
Unlimited practice
Used by hundreds of successful candidates
How would you handle a disagreement with a press operator about the quality of the printing plates you made?
How to Answer
- 1
Listen to the press operator's concerns without interrupting
- 2
Ask for specific examples of the quality issues they are seeing
- 3
Provide objective data or past examples to support your view
- 4
Propose a collaborative solution to test and validate the quality
- 5
Follow up after resolving the issue to ensure satisfaction on both sides
Example Answers
I would first listen carefully to the press operator's concerns and ask for examples of what they perceive as quality issues. Then, I would share any relevant data or specifications that support my work, and we could work together to create a test print to review.
You realize that a colleague is not following safety protocols while operating machinery. What would you do?
How to Answer
- 1
Assess the situation to confirm safety protocols are being ignored.
- 2
Approach the colleague privately and express your concern respectfully.
- 3
Suggest they follow the safety protocols and offer to help if needed.
- 4
If the behavior continues, report it to your supervisor to ensure safety in the workplace.
- 5
Always prioritize the safety of yourself and others above all.
Example Answers
I would first observe to confirm that the colleague is indeed not following safety protocols. Then, I would speak to them privately and suggest they adhere to the protocols, explaining that it's important for everyone's safety. If they don't change their behavior, I would report it to our supervisor.
A sudden increase in orders requires you to expedite the plate-making process. How would you approach this situation?
How to Answer
- 1
Evaluate current workload and prioritize urgent orders
- 2
Identify bottlenecks in the plate-making process
- 3
Consider reallocating resources or overtime for critical tasks
- 4
Communicate with the team to ensure everyone is aligned
- 5
Monitor progress and adjust plans as necessary
Example Answers
I would first assess the current workload and prioritize the most urgent orders to tackle first. Next, I would look for any bottlenecks in the production process and address them, possibly by reallocating resources or providing overtime where needed. After aligning with the team on our goals, I would keep track of our progress and make adjustments as required to meet the new demands.
If you are falling behind on multiple projects, how would you prioritize your tasks?
How to Answer
- 1
Assess the deadlines of each project and identify the most urgent ones
- 2
Determine the impact of each project on the overall workflow or team goals
- 3
Break down larger tasks into smaller, manageable tasks to clarify your focus
- 4
Communicate with your team or supervisor about your workload and priorities
- 5
Adjust your schedule to allocate time blocks for the highest priority tasks
Example Answers
I would start by reviewing all my projects and noting their deadlines. Then, I would prioritize those that are most urgent and will have the highest impact on our team’s goals. I would break those tasks down into smaller steps to make them manageable and communicate regularly with my supervisor about my progress.
You are under pressure to finish a large order. What strategies would you use to ensure quality is maintained?
How to Answer
- 1
Prioritize essential quality checks throughout the production process
- 2
Delegate tasks effectively to team members based on their strengths
- 3
Implement a workflow that incorporates regular feedback loops
- 4
Use batch testing to identify quality issues early
- 5
Stay organized and keep communication clear among team members
Example Answers
I would set up a series of quality checkpoints so we can catch any issues early. Additionally, I would assign specific aspects of the printing process to team members who excel in those areas, which helps maintain our standards even under pressure.
You’re part of a team that must complete a project involving several departments. How would you ensure effective collaboration?
How to Answer
- 1
Establish clear roles and responsibilities for each team member.
- 2
Set up regular communication channels like meetings or updates.
- 3
Encourage open dialogue and active listening to understand each department's needs.
- 4
Use collaborative tools to track progress and share resources.
- 5
Foster a positive team culture that values teamwork and respect.
Example Answers
I would first define roles within the team to ensure everyone knows their responsibilities. Then, I would schedule weekly check-ins to keep everyone aligned and address any challenges. Additionally, I would promote open communication to facilitate feedback between departments.
How would you handle a client who is unhappy with the quality of the plates you produced?
How to Answer
- 1
Listen carefully to the client's concerns without interrupting
- 2
Acknowledge their feelings and show empathy for their situation
- 3
Ask specific questions to understand the nature of the quality issues
- 4
Explain the steps you can take to address the problem and improve
- 5
Follow up with the client after corrections to ensure satisfaction
Example Answers
I would first ensure I understand the client's concerns by listening attentively. I would acknowledge their feelings and let them know I take their feedback seriously. Then, I would ask specific questions about the quality issues they experienced. After understanding the problem, I would explain how we can rectify the situation and enhance the process in the future. Finally, I would check in with them after the resolution to make sure they are satisfied.
Printing Plate Maker Position Details
Recommended Job Boards
CareerBuilder
www.careerbuilder.com/jobs/printing-plate-makerZipRecruiter
www.ziprecruiter.com/Jobs/Printing-Plate-MakerThese job boards are ranked by relevance for this position.
Related Positions
- Plate Maker
- Platemaker
- Printing Technician
- Plate Mounter
- Prepress Operator
- Phototypesetter
- Electrotyper
- Plate Straightener
- Photoengraver
- Job Lithographer
Similar positions you might be interested in.
Ace Your Next Interview!
Practice with AI feedback & get hired faster
Personalized feedback
Used by hundreds of successful candidates
Ace Your Next Interview!
Practice with AI feedback & get hired faster
Personalized feedback
Used by hundreds of successful candidates