Top 29 Process Engineering Manager Interview Questions and Answers [Updated 2025]
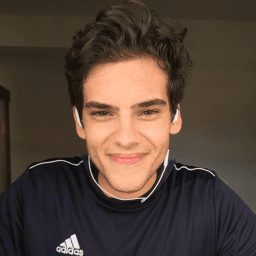
Andre Mendes
•
March 30, 2025
Navigating the interview landscape for a Process Engineering Manager role can be challenging, but our latest blog post is here to guide you. Discover the most common interview questions you might face, along with example answers and strategic tips to help you respond effectively. Whether you're a seasoned professional or new to the field, this post will equip you with the insights needed to impress potential employers and secure your desired position.
Download Process Engineering Manager Interview Questions in PDF
To make your preparation even more convenient, we've compiled all these top Process Engineering Managerinterview questions and answers into a handy PDF.
Click the button below to download the PDF and have easy access to these essential questions anytime, anywhere:
List of Process Engineering Manager Interview Questions
Situational Interview Questions
If there was an unexpected shutdown in the production line, what immediate steps would you take?
How to Answer
- 1
Assess the situation to understand the cause of the shutdown.
- 2
Communicate with team members to gather information on the issue.
- 3
Activate the emergency response plan if necessary.
- 4
Prioritize safety and ensure all personnel are safe.
- 5
Begin troubleshooting to identify the root cause and potential solutions.
Example Answers
First, I would assess the situation to determine what caused the shutdown. I would then communicate with my team to gather insights on the issue, ensuring everyone's safety is prioritized. If needed, I'd activate our emergency response plan and start troubleshooting to find a solution as quickly as possible.
A critical piece of equipment has malfunctioned, potentially delaying production. How would you handle this situation?
How to Answer
- 1
Assess the extent of the malfunction and its impact on production immediately.
- 2
Communicate with the team to gather insights and discuss potential solutions.
- 3
Implement a temporary workaround if possible to minimize downtime.
- 4
Coordinate with maintenance for urgent repairs and ensure rapid action.
- 5
Keep stakeholders updated on the situation and expected recovery timeline.
Example Answers
First, I would quickly assess the malfunction's impact on our current production schedule. I would gather the team to brainstorm immediate solutions, such as optimizing other processes to maintain output. Then, I would contact our maintenance team to expedite repairs while keeping management informed on our progress.
Don't Just Read Process Engineering Manager Questions - Practice Answering Them!
Reading helps, but actual practice is what gets you hired. Our AI feedback system helps you improve your Process Engineering Manager interview answers in real-time.
Personalized feedback
Unlimited practice
Used by hundreds of successful candidates
You are assigned to manage a project with tight deadlines and limited resources. How would you ensure its success?
How to Answer
- 1
Prioritize tasks by impact and urgency to focus on what matters most
- 2
Communicate clearly with your team about expectations and limitations
- 3
Identify and utilize key team strengths to maximize productivity
- 4
Regularly monitor progress and be flexible to adjust as needed
- 5
Engage stakeholders early to manage expectations and gather support
Example Answers
I would start by prioritizing the key deliverables based on their impact on the project. Then, I would hold a kickoff meeting to align the team on tasks and set clear responsibilities. By identifying team strengths, I would delegate effectively and ensure that we monitor our progress weekly, adapting our plan as necessary.
Your manager asks you to improve an already efficient process. How would you go about this?
How to Answer
- 1
Gather data on current process performance metrics
- 2
Identify areas with potential for minor improvements
- 3
Engage team members for their input and insights
- 4
Test small changes in a controlled environment
- 5
Monitor the results and adjust based on feedback
Example Answers
I would start by analyzing the current metrics to identify any non-obvious inefficiencies. Then, I would consult with my team for their insights, as they often know where small adjustments can yield larger benefits. After selecting a few promising changes, I'd implement them on a trial basis and monitor the results closely.
How would you communicate a complex technical issue to a non-technical manager?
How to Answer
- 1
Use simple language, avoiding jargon and technical terms.
- 2
Break down the issue into key components or steps.
- 3
Use analogies or examples that relate to the manager's experience.
- 4
Focus on the impact and benefits rather than the technical details.
- 5
Encourage questions to ensure understanding.
Example Answers
I would explain the issue by comparing it to something familiar. For example, if we're dealing with a bottleneck in production, I'd compare it to traffic congestion and explain how clearing the bottleneck improves overall flow and efficiency.
If given a fixed budget and increasing demand, how would you prioritize and allocate resources?
How to Answer
- 1
Assess demand versus capacity to identify critical areas
- 2
Use data analysis to prioritize projects based on ROI
- 3
Engage with stakeholders to align on resource needs
- 4
Implement a phased approach to allocation of resources
- 5
Monitor and adjust priorities based on results and feedback
Example Answers
I would start by analyzing demand data to identify the most critical areas that align with our strategic goals. Then, I'd prioritize projects based on their return on investment, ensuring that we're focusing our limited budget on the highest impact initiatives. Communication with stakeholders would be key to ensure everyone is on board with the prioritization and to adjust as necessary based on ongoing performance metrics.
A major supplier is unable to fulfill an order on time. How would you address this?
How to Answer
- 1
Assess the impact on production and deadlines
- 2
Contact the supplier to understand the cause of the delay
- 3
Explore alternative suppliers or solutions if necessary
- 4
Communicate with internal teams about potential delays
- 5
Develop a contingency plan to mitigate risks in the future
Example Answers
I would first evaluate how the delay affects our production schedule and inform relevant team members. Then, I would reach out to the supplier to understand the issue and explore if they can expedite the process. If not, I would look for alternative suppliers while keeping the team updated on the situation.
You are tasked with introducing a new technology that has been resisted by the team. How would you approach this challenge?
How to Answer
- 1
Understand the team's concerns by having open conversations.
- 2
Clearly communicate the benefits of the new technology to the team.
- 3
Involve the team in the implementation process to gain their buy-in.
- 4
Provide training and support to ease the transition.
- 5
Encourage feedback and make adjustments based on team input.
Example Answers
I would first hold a meeting to listen to the team's concerns about the new technology. Then, I would clearly outline how the technology can benefit our processes and make their work easier. By involving them in the rollout and offering training, I hope to gain their support.
A key stakeholder disagrees with the current direction of a project. How would you handle this situation?
How to Answer
- 1
Listen actively to the stakeholder's concerns first
- 2
Ask clarifying questions to understand their perspective
- 3
Present data and rationale for your project direction
- 4
Explore compromises that address the stakeholder's concerns
- 5
Follow up to ensure the stakeholder feels their input was valued
Example Answers
I would start by listening to the stakeholder's concerns thoroughly and ask questions to understand their point of view. Then, I would share the data and research that support our current direction, looking for common ground or potential compromises.
Behavioral Interview Questions
Can you describe a time when you led a team through a significant process improvement initiative? What was the outcome?
How to Answer
- 1
Use the STAR method: Situation, Task, Action, Result.
- 2
Focus on a specific initiative you led, detailing your role clearly.
- 3
Highlight measurable outcomes, such as reduced costs or improved efficiency.
- 4
Discuss team dynamics and how you motivated your team.
- 5
Emphasize skills used, such as problem-solving or communication.
Example Answers
In my previous role, we faced long lead times in our manufacturing process. I led a cross-functional team to analyze the workflow. We identified bottlenecks in the supply chain and implemented a new inventory management system. As a result, we reduced lead time by 30%, which increased customer satisfaction.
Tell me about a time when you had to resolve a conflict within your team. How did you handle it?
How to Answer
- 1
Provide a specific example from your experience.
- 2
Explain the conflict briefly and its impact on the team.
- 3
Describe the steps you took to resolve the conflict.
- 4
Highlight the outcome and what you learned from it.
- 5
Emphasize team collaboration and communication in your resolution.
Example Answers
In a previous role, two engineers disagreed on the design approach for a project, causing delays. I organized a meeting for them to share their viewpoints. By facilitating the discussion, they each proposed alternatives and ultimately collaborated on a hybrid solution that combined their ideas. This not only resolved the conflict but also improved the overall design and team dynamics.
Don't Just Read Process Engineering Manager Questions - Practice Answering Them!
Reading helps, but actual practice is what gets you hired. Our AI feedback system helps you improve your Process Engineering Manager interview answers in real-time.
Personalized feedback
Unlimited practice
Used by hundreds of successful candidates
Describe a time when you introduced a new technology or process improvement in your previous role.
How to Answer
- 1
Choose a specific instance that had a measurable impact.
- 2
Explain the problem you were addressing with the new technology or process improvement.
- 3
Describe your thought process and the steps you took to implement the change.
- 4
Highlight the results or benefits of the improvement, using data if possible.
- 5
Conclude with any learnings or how you might approach it differently next time.
Example Answers
In my last role as a process engineer, I implemented a new automation system for our quality checks. The previous manual process was slow, leading to bottlenecks. I researched and proposed a new automated system that reduced check times by 40%. After three months, we saw a 30% improvement in overall production efficiency.
Give an example of how you effectively delegated tasks within your team.
How to Answer
- 1
Identify a specific project where delegation was key to success
- 2
Explain how you assessed team members' strengths and weaknesses
- 3
Describe the delegation process and how you communicated expectations
- 4
Share the outcomes of the delegation and any lessons learned
- 5
Emphasize the importance of trust and support in delegation
Example Answers
In my last project, we had to redesign a process under tight deadlines. I assessed my team's skills and delegated tasks based on their strengths. John, who excels in data analysis, handled metrics, while Sarah, a strong communicator, coordinated stakeholder updates. This clear delegation ensured that tasks were completed on time, and the project succeeded.
Describe an instance when you worked with cross-functional teams to achieve an engineering goal.
How to Answer
- 1
Identify the engineering goal and the teams involved.
- 2
Explain your role and responsibilities in the collaboration.
- 3
Highlight the challenges faced during the project.
- 4
Discuss how communication and teamwork played a role in success.
- 5
Conclude with the outcome and what you learned from the experience.
Example Answers
In my last role, I led a project to improve product quality by collaborating with the manufacturing and quality assurance teams. I was responsible for designing a new testing protocol. We faced challenges in aligning our schedules, but I set up weekly meetings to keep everyone updated. This teamwork led to a 20% reduction in defects, and I learned the value of clear communication.
How have you handled performance issues within your engineering team?
How to Answer
- 1
Identify the specific performance issue succinctly
- 2
Discuss the assessment process you used to analyze the situation
- 3
Explain the steps taken to address the issue with the team member
- 4
Highlight any follow-up actions or improvements made post-intervention
- 5
Share a success story or positive outcome resulting from your approach
Example Answers
In my previous role, I noticed a team member consistently missed deadlines. I set up a one-on-one to openly discuss their challenges. We created a performance improvement plan with clear milestones, and after three months, their delivery improved drastically, leading to them taking the lead on a critical project.
Explain a time when you identified potential risks in a project and how you mitigated them.
How to Answer
- 1
Select a specific project where risks were apparent
- 2
Describe the risk identification process clearly
- 3
Explain the mitigation strategies you employed
- 4
Quantify the impact of your actions if possible
- 5
Highlight teamwork or collaboration if applicable
Example Answers
In a recent project to optimize a production line, I noticed a risk of equipment failure due to lack of maintenance. I organized a maintenance schedule and trained the team, reducing downtime by 30%.
Have you ever mentored a junior engineer? How did you go about it and what was the outcome?
How to Answer
- 1
Describe a specific instance where you mentored a junior engineer.
- 2
Explain your mentorship style and methods used during the process.
- 3
Highlight the skills or knowledge you helped them develop.
- 4
Share a successful outcome from the mentorship, including any measurable results.
- 5
Mention any feedback you received from the mentee.
Example Answers
Yes, I mentored a junior engineer last year by setting up regular one-on-one sessions. I focused on helping them understand process optimization techniques. As a result, they improved their project delivery time by 20% and received positive feedback from our manager.
Don't Just Read Process Engineering Manager Questions - Practice Answering Them!
Reading helps, but actual practice is what gets you hired. Our AI feedback system helps you improve your Process Engineering Manager interview answers in real-time.
Personalized feedback
Unlimited practice
Used by hundreds of successful candidates
Technical Interview Questions
Explain how you would implement Lean principles in a new production line.
How to Answer
- 1
Identify value from the customer's perspective.
- 2
Map the current process to identify waste.
- 3
Implement continuous flow to reduce cycle times.
- 4
Use 5S practices to organize the workspace effectively.
- 5
Train staff on Lean principles for sustainable implementation.
Example Answers
To implement Lean principles in a new production line, I would start by mapping the entire process to identify areas of waste. Next, I would define value from the customer's perspective to ensure we focus on what matters most. Implementing continuous flow would help us minimize cycle times, and adopting 5S practices would keep our workspace organized and efficient. Finally, I would provide Lean training to the team to ensure everyone understands and embraces these principles for long-term success.
How do you perform a root cause analysis when faced with a recurring production issue?
How to Answer
- 1
Identify the problem clearly and gather data on the last occurrences.
- 2
Use a structured method like the 5 Whys or Fishbone Diagram.
- 3
Involve team members in brainstorming potential causes.
- 4
Validate causes with evidence and prioritize based on impact.
- 5
Develop action items to address the root causes and monitor results.
Example Answers
First, I define the problem by analyzing production data to find patterns. Then, I apply the 5 Whys method to drill down to the root cause. Involving my team helps gather diverse insights, and once we identify the cause, I create a list of corrective actions and ensure we monitor the outcomes.
Don't Just Read Process Engineering Manager Questions - Practice Answering Them!
Reading helps, but actual practice is what gets you hired. Our AI feedback system helps you improve your Process Engineering Manager interview answers in real-time.
Personalized feedback
Unlimited practice
Used by hundreds of successful candidates
What statistical tools do you use for quality control and how do you apply them?
How to Answer
- 1
Identify key statistical tools relevant to quality control like control charts, histograms, and process capability analysis.
- 2
Explain how you have used these tools in past projects with specific examples.
- 3
Discuss the results achieved using these tools, such as improved quality and reduced defects.
- 4
Mention any software or systems you utilize for these statistical analyses.
- 5
Emphasize your understanding of how these tools contribute to overall process improvement.
Example Answers
I regularly use control charts to monitor process stability. In my last role, I implemented a control chart for a manufacturing line, which helped us identify variations and reduce defects by 15%.
How would you go about implementing automation to improve process efficiency?
How to Answer
- 1
Identify key processes that are time-consuming or error-prone
- 2
Evaluate suitable automation technology that aligns with company goals
- 3
Create a pilot project to test automation scalability
- 4
Involve team members in the implementation process to gain insights
- 5
Measure results and iterate to optimize the automation solution
Example Answers
To improve process efficiency, I would first identify the top processes that are causing delays. For instance, if data entry is a bottleneck, I would evaluate robotic process automation tools that can help. Then, I would run a small pilot program to test these tools and gather feedback from the team before full implementation. Finally, I would analyze the impact on efficiency and make adjustments as necessary.
What considerations do you keep in mind when designing a new manufacturing process?
How to Answer
- 1
Identify the key requirements such as product specifications and quality standards.
- 2
Consider the available technology and equipment that will be utilized.
- 3
Evaluate the impact of the process on cost efficiency and downtime.
- 4
Plan for scalability and flexibility to adapt to future changes.
- 5
Ensure compliance with safety and environmental regulations.
Example Answers
When designing a new manufacturing process, I focus on meeting product specifications while utilizing the latest technology to enhance efficiency. I also assess cost implications and prioritize safety regulations.
Outline the main steps you would take to set up a quality assurance program for a new product line.
How to Answer
- 1
Define quality standards based on industry benchmarks and customer expectations
- 2
Develop a comprehensive quality plan detailing processes, responsibilities, and timelines
- 3
Implement training programs for staff on quality assurance procedures
- 4
Utilize data analytics to monitor quality metrics and identify areas for improvement
- 5
Establish regular review and feedback mechanisms to adapt the program as necessary
Example Answers
To set up a quality assurance program, I would first define clear quality standards based on both industry benchmarks and customer expectations. Next, I would develop a detailed quality plan that includes processes, assigned responsibilities, and a timeline for implementation. I would also conduct training sessions for all relevant staff to ensure they understand the quality procedures. Data analytics would help us monitor quality metrics effectively, and I would establish regular review meetings to continuously improve the program.
How do you ensure compliance with safety regulations in process engineering?
How to Answer
- 1
Familiarize yourself with relevant safety regulations and standards
- 2
Conduct regular training sessions for the team on safety protocols
- 3
Implement a safety management system to monitor compliance
- 4
Perform routine audits and inspections of processes and equipment
- 5
Engage with safety officers and regulatory bodies for updates and feedback
Example Answers
I ensure compliance by regularly reviewing OSHA regulations and integrating them into our processes. I conduct team training sessions quarterly and maintain a detailed safety management system to track our compliance metrics.
How do you utilize data analytics in improving engineering processes?
How to Answer
- 1
Identify key performance indicators relevant to your processes
- 2
Use data visualization tools to analyze trends and outliers
- 3
Regularly review data to make informed decisions on process changes
- 4
Implement root cause analysis using data to address inefficiencies
- 5
Share insights from data analysis with your team to foster a culture of continuous improvement
Example Answers
I focus on key performance indicators like cycle time and defect rates. By analyzing these metrics with tools like Tableau, I identify trends that help us streamline operations.
What steps do you take to enhance energy efficiency in production processes?
How to Answer
- 1
Conduct an energy audit to identify current energy usage patterns
- 2
Implement energy monitoring systems for real-time data
- 3
Evaluate and upgrade equipment to more energy-efficient models
- 4
Train staff on best practices for energy conservation
- 5
Encourage a culture of continuous improvement and energy awareness
Example Answers
I start with an energy audit to pinpoint high consumption areas and then I install monitoring systems for ongoing analysis. This helps us make informed decisions about upgrades and staff training.
What methodologies do you use to identify bottlenecks in a manufacturing process?
How to Answer
- 1
Focus on specific methodologies like Lean, Six Sigma, or Value Stream Mapping.
- 2
Explain how you collect data and analyze process flow.
- 3
Discuss the importance of involving team members for insights.
- 4
Mention tools or software you use for process analysis.
- 5
Emphasize continuous improvement efforts.
Example Answers
I use Lean methodologies to streamline processes, employing tools like Value Stream Mapping to visualize the workflow and identify bottlenecks. I also leverage team feedback and data analysis to pinpoint inefficiencies.
Don't Just Read Process Engineering Manager Questions - Practice Answering Them!
Reading helps, but actual practice is what gets you hired. Our AI feedback system helps you improve your Process Engineering Manager interview answers in real-time.
Personalized feedback
Unlimited practice
Used by hundreds of successful candidates
Process Engineering Manager Position Details
Salary Information
Recommended Job Boards
These job boards are ranked by relevance for this position.
Related Positions
- Environmental Engineering Manager
- Project Engineering Manager
- Data Engineering Manager
- Engineering Project Manager
- Engineering Design Manager
- Engineering Program Manager
- Mechanical Engineering Manager
- Engineering Supervisor
- Civil Engineering Manager
- Engineering Director
Similar positions you might be interested in.
Ace Your Next Interview!
Practice with AI feedback & get hired faster
Personalized feedback
Used by hundreds of successful candidates
Ace Your Next Interview!
Practice with AI feedback & get hired faster
Personalized feedback
Used by hundreds of successful candidates