Top 29 Pump Installer Interview Questions and Answers [Updated 2025]
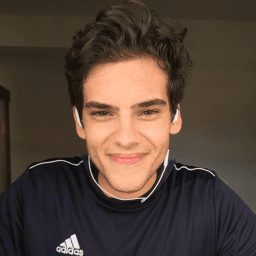
Andre Mendes
•
March 30, 2025
Preparing for a Pump Installer interview? This blog post has you covered with the most common questions you can expect, complete with example answers and effective answering tips. Whether you're a seasoned professional or new to the field, these insights will help you confidently navigate your interview and showcase your expertise. Read on to equip yourself with the knowledge and strategies to succeed.
Download Pump Installer Interview Questions in PDF
To make your preparation even more convenient, we've compiled all these top Pump Installerinterview questions and answers into a handy PDF.
Click the button below to download the PDF and have easy access to these essential questions anytime, anywhere:
List of Pump Installer Interview Questions
Behavioral Interview Questions
Can you describe a time when you worked as part of a team to install a complex pump system?
How to Answer
- 1
Choose a specific project that highlights teamwork.
- 2
Explain each team member's role briefly.
- 3
Describe the challenges faced and how the team overcame them.
- 4
Highlight your specific contributions to the project.
- 5
Conclude with the successful outcome of the installation.
Example Answers
In a recent project, I collaborated with a team of four to install an industrial pump system at a manufacturing plant. My role was to handle the electrical connections. We faced a tight deadline, but by scheduling daily check-ins, we managed to stay on track and completed the installation ahead of schedule, ensuring the system was not only operational but also met safety standards.
Tell me about a challenging installation problem you encountered and how you resolved it.
How to Answer
- 1
Choose a specific example that highlights your problem-solving skills.
- 2
Explain the context of the installation and what made it challenging.
- 3
Describe the steps you took to address the issue clearly.
- 4
Mention any tools or techniques used in your solution.
- 5
Wrap up with the outcome and what you learned from the experience.
Example Answers
During a commercial pump installation, I encountered an issue with incorrect pipe fittings. Realizing the dimensions were off, I quickly assessed the situation and sourced the correct fittings from the nearby hardware store. By collaborating with my team, we adapted the setup and successfully completed the installation ahead of schedule. This taught me the importance of double-checking measurements before starting.
Don't Just Read Pump Installer Questions - Practice Answering Them!
Reading helps, but actual practice is what gets you hired. Our AI feedback system helps you improve your Pump Installer interview answers in real-time.
Personalized feedback
Unlimited practice
Used by hundreds of successful candidates
Describe an experience where you had to ensure safety during a pump installation.
How to Answer
- 1
Identify a specific installation project where safety was a concern
- 2
Explain the safety measures you implemented step by step
- 3
Mention any relevant safety guidelines or regulations you followed
- 4
Highlight the outcomes of your safety measures on the project
- 5
Reflect on what you learned about safety from the experience
Example Answers
During a recent installation of a submersible pump, we faced potential electrical hazards. I ensured all power sources were switched off before starting. I also used lockout/tagout procedures to prevent accidental reactivation. This adherence to safety protocols not only protected our team but also ensured the installation was completed without any incidents.
How have you communicated technical information to a non-technical client or colleague?
How to Answer
- 1
Understand the audience's background and knowledge level
- 2
Use simple language and avoid jargon
- 3
Use analogies or visuals to explain complex concepts
- 4
Check for understanding by asking questions
- 5
Be patient and open to follow-up questions
Example Answers
I once explained a pump's operation to a client by comparing it to a water hose, highlighting how pressure changes affect water flow. I checked in with them throughout to ensure they grasped the concepts.
Can you give an example of a time when you had to adapt to changing conditions during an installation?
How to Answer
- 1
Identify a specific installation project you worked on.
- 2
Describe the unexpected change that occurred during the installation.
- 3
Explain how you assessed the situation and made quick decisions.
- 4
Share the positive outcome and what you learned from the experience.
- 5
Keep it concise and focus on your problem-solving skills.
Example Answers
During a residential pump installation, we encountered heavy rain that flooded the site. I quickly assessed the situation, moved equipment to higher ground, and adjusted our timeline to wait for the rain to subside. The installation was completed successfully with minimal delay.
Can you describe an instance where you helped reduce costs without compromising quality during a project?
How to Answer
- 1
Identify a specific project where cost reduction was a goal.
- 2
Explain the methods used to analyze costs and quality.
- 3
Provide a clear example of a change implemented.
- 4
Quantify the results in terms of cost savings and quality maintained.
- 5
Highlight teamwork or collaboration if applicable.
Example Answers
During a water pump installation project, I noticed that we could reduce material costs by 15% by sourcing pumps from a local supplier. I ensured that the pumps met the same quality standards by working closely with the supplier on specifications. As a result, we saved $3,000 while maintaining project quality.
Describe a time when you took the lead on a pump installation project. What was the outcome?
How to Answer
- 1
Choose a specific project where you were the lead.
- 2
Explain your role and responsibilities clearly.
- 3
Highlight the challenges you faced and how you overcame them.
- 4
Discuss the successful outcome and any measurable results.
- 5
Reflect on what you learned and how it improved your skills.
Example Answers
During a recent project at a manufacturing plant, I led the installation of a new pump system. My responsibility included coordinating the schedule and managing the team. We faced challenges with alignment, but I organized additional training and worked directly with the technicians to ensure precision. The installation was completed ahead of schedule and improved the plant's efficiency by 20%. I learned the importance of hands-on leadership during technical challenges.
Have you ever proposed a new method or technology to improve pump installation? What was the result?
How to Answer
- 1
Think of a specific instance where you identified a problem in pump installation.
- 2
Explain the method or technology you proposed clearly and concisely.
- 3
Share the reasoning behind your suggestion, focusing on benefits like efficiency or safety.
- 4
Discuss the outcome, including any metrics or feedback received.
- 5
Be honest if your proposal was not adopted, but emphasize what you learned.
Example Answers
In my last job, I proposed using a digital monitoring system for real-time pressure readings during pump installation. This allowed us to detect issues early. As a result, we reduced installation time by 20% and improved overall safety.
Tell me about a time when you utilized innovative thinking in a pump installation scenario.
How to Answer
- 1
Focus on a specific challenge you faced during installation.
- 2
Describe the innovative solution you implemented.
- 3
Explain the impact of your solution on the project outcome.
- 4
Use clear examples to demonstrate your problem-solving skills.
- 5
Keep it concise and relevant to pump installations.
Example Answers
In a recent installation, we encountered a problem with pump alignment. I suggested using a laser level to ensure precise positioning, which reduced setup time and prevented future maintenance issues. This innovation not only saved us time but also improved the pump's efficiency.
Technical Interview Questions
What are the differences between centrifugal and positive displacement pumps?
How to Answer
- 1
Start by defining both types of pumps clearly.
- 2
Highlight the principle of operation for each pump type.
- 3
Discuss key applications and when to use each type.
- 4
Mention efficiency and the effect of fluid viscosity.
- 5
Include any relevant examples to illustrate your points.
Example Answers
Centrifugal pumps operate by converting rotational energy into fluid motion through impellers, making them efficient for low-viscosity fluids. Positive displacement pumps, on the other hand, move fluid by trapping a fixed amount and forcing it through the outlet, making them ideal for high-viscosity fluids.
What steps do you take when preparing for a pump installation?
How to Answer
- 1
Review project specifications and site requirements
- 2
Gather all necessary tools and equipment
- 3
Check pump specifications and compatibility
- 4
Coordinate with team members for roles
- 5
Conduct a pre-installation site assessment
Example Answers
I start by reviewing the project specs and ensuring I understand the site requirements. Then, I gather all the tools and equipment I'll need for the installation.
Don't Just Read Pump Installer Questions - Practice Answering Them!
Reading helps, but actual practice is what gets you hired. Our AI feedback system helps you improve your Pump Installer interview answers in real-time.
Personalized feedback
Unlimited practice
Used by hundreds of successful candidates
What tools and equipment do you believe are essential for installing pumps?
How to Answer
- 1
List specific tools like wrenches, pipe cutters, and screwdrivers.
- 2
Mention safety equipment such as gloves and goggles.
- 3
Include any measuring devices needed for precise installation.
- 4
Explain the importance of using the right types of pumps for specific applications.
- 5
Consider mentioning personal protective equipment (PPE) relevant to the installation environment.
Example Answers
I believe essential tools for installing pumps include adjustable wrenches, pipe cutters, and screwdrivers. Safety gear such as gloves and goggles is also crucial. Additionally, a measuring tape ensures that everything is properly aligned and fitted.
What common troubleshooting techniques do you employ when a pump is not functioning properly?
How to Answer
- 1
Start with a visual inspection of the pump and surrounding area.
- 2
Check for any abnormal noises or vibrations during operation.
- 3
Verify the power supply and ensure all electrical connections are secure.
- 4
Examine the intake and discharge lines for blockages or leaks.
- 5
Consult the manufacturer's manual for specific troubleshooting steps.
Example Answers
I begin by visually inspecting the pump for any obvious issues, such as leaks or misalignments. Then, I listen for abnormal noises, which can indicate mechanical problems. Next, I ensure the power supply is stable and all connections are tight.
What safety regulations or guidelines must be followed during pump installation?
How to Answer
- 1
Know and mention local and national safety regulations relevant to pump installation.
- 2
Highlight the importance of personal protective equipment (PPE) such as gloves, goggles, and helmets.
- 3
Discuss the need for electrical safety when working with pumps.
- 4
Emphasize securing the work area to prevent accidents and unauthorized access.
- 5
Mention the importance of training and following manufacturer guidelines for installation procedures.
Example Answers
During pump installation, it's crucial to follow OSHA regulations, wear PPE like gloves and goggles, and ensure electrical safety by disconnecting power before starting work.
What routine maintenance do you suggest to clients after a pump installation?
How to Answer
- 1
Advise clients to regularly check the pump's oil levels and ensure they are at recommended levels.
- 2
Recommend inspecting filters and screens monthly to prevent clogging and ensure optimal performance.
- 3
Suggest scheduling annual professional maintenance checks to assess performance and make necessary adjustments.
- 4
Encourage clients to monitor the pump for unusual noises or vibrations that could indicate issues.
- 5
Teach clients to keep the pump and its surrounding area clean and clear of debris.
Example Answers
I recommend that clients regularly check the oil levels in the pump, inspect filters and screens monthly, and schedule an annual maintenance check to ensure everything is functioning correctly.
How would you determine the capacity and size of the pump needed for a specific application?
How to Answer
- 1
Assess the fluid properties like viscosity and density.
- 2
Determine the desired flow rate required by the application.
- 3
Calculate the total dynamic head (TDH) including elevation and friction losses.
- 4
Consider peak demand and potential future growth when sizing.
- 5
Select a pump type that suits the application criteria.
Example Answers
To determine the pump size, first, I assess the fluid properties, including its viscosity and density. Then I establish the flow rate required for the specific application. Next, I calculate the total dynamic head by taking into account the elevation difference and pressure loss from friction. Finally, I pick a pump type that meets these criteria, considering future needs.
Can you explain the basic principles of hydraulics as they relate to pump operation?
How to Answer
- 1
Start by defining hydraulics and its significance in pumps.
- 2
Mention Pascal's principle and how it applies to pressure in fluids.
- 3
Explain the function of pumps in moving fluids and creating pressure.
- 4
Discuss flow rate and how it is affected by the pump design.
- 5
Provide real-world examples of hydraulic systems using pumps.
Example Answers
Hydraulics refers to the study of liquids in motion. Pumps operate based on Pascal's principle, which states that pressure applied to a confined fluid is transmitted equally in all directions. This is essential for moving fluids efficiently. A pump creates pressure that allows fluids to flow through pipelines, and the flow rate depends on the pump's design and capacity. For instance, in irrigation systems, pumps move water from a source to fields using these hydraulic principles.
What do you know about electrical wiring and controls related to pump systems?
How to Answer
- 1
Explain basic wiring components like switches, relays, and circuit breakers.
- 2
Mention control systems such as PLCs or variable frequency drives (VFDs).
- 3
Discuss the importance of following electrical codes and safety standards.
- 4
Include examples of troubleshooting common electrical issues in pump systems.
- 5
Emphasize the role of proper grounding and circuit protection.
Example Answers
I know that electrical wiring in pump systems includes essential components like circuit breakers and relays, which help control the flow of electricity. I also understand that PLCs can automate pump operations effectively and ensure safe running conditions.
What performance metrics do you monitor after installing a pump?
How to Answer
- 1
Identify key metrics specific to pump performance, such as flow rate and pressure.
- 2
Discuss the importance of monitoring energy consumption and efficiency.
- 3
Consider the need for tracking maintenance indicators like vibration and temperature.
- 4
Mention customer feedback or system reliability as a performance metric.
- 5
Explain how you would collect data and analyze it regularly for optimal performance.
Example Answers
After installing a pump, I monitor flow rate, discharge pressure, and energy consumption to ensure efficiency. I also check for any abnormal vibrations and temperature to catch potential issues early.
Don't Just Read Pump Installer Questions - Practice Answering Them!
Reading helps, but actual practice is what gets you hired. Our AI feedback system helps you improve your Pump Installer interview answers in real-time.
Personalized feedback
Unlimited practice
Used by hundreds of successful candidates
Situational Interview Questions
If a pump installation site becomes unsafe due to weather, what steps would you take to secure the area?
How to Answer
- 1
Assess the immediate dangers and conditions of the site
- 2
Evacuate all personnel from the area
- 3
Secure tools and equipment to prevent damage or hazards
- 4
Mark the area with clear signage indicating it is unsafe
- 5
Monitor weather updates and only return when safe
Example Answers
Firstly, I would assess the site for any immediate dangers like flooding or high winds. Then, I would evacuate all personnel to a safe location. After ensuring everyone is clear, I would secure equipment and tools to prevent them from becoming hazards. I would then mark the area clearly, so no one enters until it's safe. Lastly, I would keep an eye on weather reports before deciding to return.
How would you handle a situation where the pump installation needs to be completed ahead of schedule?
How to Answer
- 1
Assess current progress and identify critical tasks.
- 2
Communicate with the team about the new deadline.
- 3
Prioritize tasks and allocate additional resources if necessary.
- 4
Stay organized and maintain quality while working fast.
- 5
Keep the client updated on progress and potential changes.
Example Answers
I would first assess what has been completed and what still needs to be done. I would then have a quick meeting with the team to align on priorities and reallocate efforts to critical tasks to meet the deadline.
Don't Just Read Pump Installer Questions - Practice Answering Them!
Reading helps, but actual practice is what gets you hired. Our AI feedback system helps you improve your Pump Installer interview answers in real-time.
Personalized feedback
Unlimited practice
Used by hundreds of successful candidates
How would you manage a situation where a client is unhappy with the installation work done?
How to Answer
- 1
Listen carefully to the client's concerns and validate their feelings
- 2
Apologize for any inconveniences caused, even if you believe you did the work correctly
- 3
Assess the situation to understand what specifically the client is unhappy about
- 4
Provide a clear plan to resolve the issue, including timelines
- 5
Follow up after the resolution to ensure the client is satisfied
Example Answers
I would start by listening to the client's concerns without interrupting. I would acknowledge their feelings and apologize for the dissatisfaction. Then, I would review the work together to understand their specific issues and propose a solution, ensuring I keep them informed throughout the process.
If you discover that a pump is defective right before installation, what would your course of action be?
How to Answer
- 1
Immediately assess the extent of the defect and identify the issue.
- 2
Communicate the problem to your supervisor or team without delay.
- 3
Document the defect to maintain clear records.
- 4
Look for a replacement or backup pump in inventory.
- 5
Follow up on the installation schedule to minimize delays.
Example Answers
Upon discovering a defect, I would quickly assess the issue, inform my supervisor, and document the problem. Then, I would check our inventory for a replacement pump to ensure we stay on schedule.
How would you address a conflict between team members on a pump installation project?
How to Answer
- 1
Identify the underlying issue causing the conflict.
- 2
Speak to each team member privately to understand their perspective.
- 3
Encourage open communication in a group setting to address concerns.
- 4
Focus on finding a solution that works for everyone involved.
- 5
Follow up after resolving the conflict to ensure it doesn't happen again.
Example Answers
I would first identify what triggered the conflict by speaking to each team member to understand their viewpoints. Then, I would bring them together to discuss the issue openly and encourage collaboration on a solution that satisfies both parties.
What would you do if you found that the pump installed did not meet the specified quality standards?
How to Answer
- 1
Stay calm and assess the situation clearly.
- 2
Identify the specific quality standards that were not met.
- 3
Communicate the issue to your supervisor or project manager promptly.
- 4
Propose a solution or corrective action based on your expertise.
- 5
Document the findings and corrective measures taken for future reference.
Example Answers
If I found that the pump did not meet the specified quality standards, I would first identify how it fell short. I would then inform my supervisor about the issue immediately and suggest potential corrective actions, such as re-installation or repairs. Lastly, I would document everything to ensure accountability and future learning.
How would you prioritize tasks when multiple installations are scheduled at the same time?
How to Answer
- 1
Assess urgency and impact of each installation.
- 2
Consider the proximity of locations for efficiency.
- 3
Evaluate the resources available for each task.
- 4
Communicate with the team about workload and priorities.
- 5
Document the plan to keep track of progress.
Example Answers
I would first determine which installation is the most urgent based on client needs and deadlines. Then, I would optimize my schedule by grouping installations that are geographically close to minimize travel time. I would also make sure that I have the necessary tools and parts ready for each task before heading out.
How would you educate a client about the operational features of the pump they just installed?
How to Answer
- 1
Start with a brief overview of the pump's main functions.
- 2
Explain key components and their roles in operation.
- 3
Demonstrate how to operate the pump with a practical demonstration.
- 4
Discuss maintenance tips and frequency for optimal performance.
- 5
Encourage questions to ensure the client understands and feels confident.
Example Answers
I would first explain that the pump is designed to move water efficiently. Then, I'd describe its main components like the motor and impeller, explaining their functions. I would offer to show the client how to start and stop the pump in real-time. Next, I’d advise them on how often to check the filters and perform regular maintenance. Finally, I’d ask if they have any questions to clarify their understanding.
What steps would you take if a supplier delayed the delivery of critical components for a pump installation?
How to Answer
- 1
Communicate with the supplier to understand the cause of the delay.
- 2
Assess the impact of the delay on the installation timeline.
- 3
Explore alternative suppliers for the components if possible.
- 4
Inform the project manager and team about the situation and expectations.
- 5
Adjust the project plan to mitigate delays and keep the project on track.
Example Answers
I would first contact the supplier to get detailed information on the delay and when I can expect the delivery. Then I would evaluate the impact on our timeline and discuss potential alternatives with my team.
After receiving complaints about a pump's performance, how would you investigate the issue?
How to Answer
- 1
Gather detailed information about the complaints from the users
- 2
Conduct a visual inspection of the pump to identify any apparent issues
- 3
Check the pump's operational parameters against the manufacturer's specifications
- 4
Review maintenance records for any previous issues or repairs
- 5
Test the pump's performance in different conditions to isolate the problem
Example Answers
I would first ask the users to provide specific details about the performance complaints they experienced. Then, I would inspect the pump visually to look for any obvious damage or leaks. After that, I would check its operational parameters against the specifications to see if any values are out of range.
Don't Just Read Pump Installer Questions - Practice Answering Them!
Reading helps, but actual practice is what gets you hired. Our AI feedback system helps you improve your Pump Installer interview answers in real-time.
Personalized feedback
Unlimited practice
Used by hundreds of successful candidates
Pump Installer Position Details
Recommended Job Boards
CareerBuilder
www.careerbuilder.com/jobs/pump-installerZipRecruiter
www.ziprecruiter.com/Jobs/Pump-InstallerThese job boards are ranked by relevance for this position.
Related Positions
- Fire Extinguisher Installer
- Furniture Installer
- Gun Fitter
- Swimming Pool Maintenance
- Toy Mechanic
- Water Pump Installer
- Pump Mechanic
- Water Pumper
- Pump Oiler
- Heat Pump Installer
Similar positions you might be interested in.
Ace Your Next Interview!
Practice with AI feedback & get hired faster
Personalized feedback
Used by hundreds of successful candidates
Ace Your Next Interview!
Practice with AI feedback & get hired faster
Personalized feedback
Used by hundreds of successful candidates