Top 30 Quality Control Coordinator Interview Questions and Answers [Updated 2025]
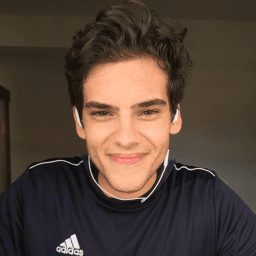
Andre Mendes
•
March 30, 2025
Preparing for a Quality Control Coordinator interview? This blog post is your go-to resource for the most common interview questions you might face in this crucial role. Dive in to discover insightful example answers and practical tips on how to respond effectively, ensuring you present yourself as a top candidate. Get ready to navigate your interview with confidence and showcase your skills and experience.
Download Quality Control Coordinator Interview Questions in PDF
To make your preparation even more convenient, we've compiled all these top Quality Control Coordinatorinterview questions and answers into a handy PDF.
Click the button below to download the PDF and have easy access to these essential questions anytime, anywhere:
List of Quality Control Coordinator Interview Questions
Situational Interview Questions
Suppose you find that a vendor is consistently not meeting quality standards. How would you handle the situation?
How to Answer
- 1
Document the specific quality issues in detail.
- 2
Communicate with the vendor to discuss the problems.
- 3
Work with the vendor to develop an action plan for improvement.
- 4
Set clear deadlines for when improvements need to be made.
- 5
Monitor the situation closely and follow up regularly.
Example Answers
I would first document the quality issues in detail, then reach out to the vendor for a discussion. We would identify root causes together, create an action plan with specific deadlines, and I would follow up regularly to ensure improvements are being made.
Imagine you discover a significant defect in a batch of products shortly before shipment. What steps would you take to address the situation?
How to Answer
- 1
Immediately halt the shipment process to avoid sending defective products.
- 2
Assess the extent of the defect and identify affected products.
- 3
Communicate with the relevant stakeholders, including your team and management.
- 4
Investigate the root cause of the defect to prevent future occurrences.
- 5
Implement corrective actions and re-evaluate the batch before any reshipment.
Example Answers
First, I would stop the shipment right away to prevent any defective products from leaving. Then, I would check the entire batch to find out how many products are affected. It's crucial to notify my supervisor and the shipping department about the issue. I would investigate what caused the defect and work on finding a solution to fix it. Finally, I would ensure that all necessary corrections are made before we consider reshipping any products.
Don't Just Read Quality Control Coordinator Questions - Practice Answering Them!
Reading helps, but actual practice is what gets you hired. Our AI feedback system helps you improve your Quality Control Coordinator interview answers in real-time.
Personalized feedback
Unlimited practice
Used by hundreds of successful candidates
A critical process in production is underperforming. How would you approach analyzing and improving it?
How to Answer
- 1
Identify key performance indicators (KPIs) related to the process
- 2
Gather quantitative data on the current performance
- 3
Engage with team members to understand ground-level issues
- 4
Analyze the data to find bottlenecks or trends
- 5
Propose targeted improvements and set a timeline for re-evaluation
Example Answers
I would start by reviewing the KPIs to find where performance is lagging. Then, I'd collect data on production times and defects. Conversations with team members would help uncover potential issues. After analyzing the data, I'd identify a specific bottleneck to address and suggest improvements, followed by a timeline to check progress.
A customer has reported a problem with a product that passed quality control. How would you investigate and resolve this issue?
How to Answer
- 1
Begin by gathering all relevant information from the customer about the problem.
- 2
Review the quality control records for the specific product batch.
- 3
Conduct a root cause analysis to identify any lapses in the QC process.
- 4
Communicate findings and potential solutions to the customer promptly.
- 5
Implement corrective actions and follow up to ensure customer satisfaction.
Example Answers
First, I would ask the customer for detailed information on the issue they experienced. Then, I would review the QC records for that product to check if it met all specifications. If there were any deviations, I would conduct a root cause analysis to understand why it passed QC. After identifying the issue, I would inform the customer of our findings and suggest corrective actions, ensuring they feel valued through regular updates.
You receive an urgent alert about a potential quality issue that could halt production. How do you prioritize and address this?
How to Answer
- 1
Immediately gather initial data on the quality alert
- 2
Assess the potential impact on production and safety
- 3
Communicate with key stakeholders to inform them of the issue
- 4
Prioritize actions based on urgency and severity
- 5
Document steps taken and results to ensure tracking
Example Answers
First, I would quickly collect information about the quality alert to understand its nature and scope. Then, I would evaluate how this issue could affect production timelines and safety. After assessing the impact, I would inform relevant stakeholders such as the production manager and quality team to discuss immediate actions. We would prioritize a response to minimize downtime, and I would make sure to document everything for future reference.
A new product is about to be launched, and you're responsible for its quality control. What steps do you take to ensure quality?
How to Answer
- 1
Define quality standards based on product specifications and industry regulations
- 2
Develop a quality control plan outlining testing and inspection methods
- 3
Conduct pre-launch testing to identify and fix defects early
- 4
Engage with cross-functional teams to ensure alignment on quality expectations
- 5
Implement a feedback loop for continuous improvement after the launch
Example Answers
First, I would establish clear quality standards that align with both the product specifications and industry regulations. Then, I would create a detailed quality control plan that includes all testing and inspection methods. Pre-launch testing would be essential to catch any defects, and I'd collaborate closely with teams from production, marketing, and sales to ensure everyone understands quality expectations. Finally, I would set up a system to gather feedback from customers after the launch for ongoing improvements.
How would you handle a situation where cross-departmental cooperation is required to resolve a quality issue?
How to Answer
- 1
Identify the departments involved and their roles in the issue
- 2
Initiate a meeting to discuss the quality issue collaboratively
- 3
Encourage open communication and provide a platform for feedback
- 4
Suggest practical solutions and a clear action plan
- 5
Follow up to ensure the resolution is implemented and effective
Example Answers
I would first identify the key departments affected by the quality issue, such as production and logistics. Then, I would set up a collaborative meeting to discuss the problem, encouraging all parties to share their insights. Together, we would brainstorm solutions and create a step-by-step action plan, followed by regular check-ins to assess progress.
If you identified recurring quality issues with a supplier’s materials, how would you address this?
How to Answer
- 1
Investigate and gather data on the quality issues
- 2
Communicate directly with the supplier about the concerns
- 3
Collaborate to identify root causes and solutions
- 4
Implement a corrective action plan and monitor results
- 5
Consider alternate suppliers if issues persist
Example Answers
I would first collect data and analyze the recurring issues to understand their impact. Then, I would schedule a meeting with the supplier to discuss my findings and seek their input on root causes. Together, we can develop a corrective action plan to resolve these issues, and I would closely monitor the results to ensure improvement.
Behavioral Interview Questions
Can you describe a time when you identified a quality issue in a product and how you resolved it?
How to Answer
- 1
Choose a specific example that clearly illustrates the quality issue.
- 2
Explain the steps you took to investigate and analyze the problem.
- 3
Describe the actions you implemented to resolve the issue.
- 4
Highlight the outcome and any improvements made to prevent recurrence.
- 5
Keep the focus on your role and contributions in resolving the issue.
Example Answers
In my previous role, I noticed a recurring defect in one of our electronic products that caused failures in the field. I examined the production process and discovered that a specific assembly step was being performed incorrectly. I collaborated with the assembly team to retrain them on proper techniques and introduced a checklist to ensure compliance. As a result, the defect rate dropped by 30%, greatly improving customer satisfaction.
Tell me about a time when you worked with a team to improve a manufacturing process. What was your role and the outcome?
How to Answer
- 1
Choose a clear example from your experience.
- 2
Explain your specific role in the team effort.
- 3
Describe the process improvement and its impact.
- 4
Use metrics or data to highlight success.
- 5
Conclude with what you learned from the experience.
Example Answers
In my previous job, our team noticed high rejection rates in our production line. I led a cross-functional group to analyze the process, and we identified a bottleneck. My role was to implement a new inspection system that reduced errors. As a result, we lowered rejection rates by 30%, which saved the company significant costs.
Don't Just Read Quality Control Coordinator Questions - Practice Answering Them!
Reading helps, but actual practice is what gets you hired. Our AI feedback system helps you improve your Quality Control Coordinator interview answers in real-time.
Personalized feedback
Unlimited practice
Used by hundreds of successful candidates
Give an example of a situation where your attention to detail prevented a major issue in production.
How to Answer
- 1
Think of a specific incident from your experience.
- 2
Describe the context and your role in detail.
- 3
Explain the potential issue that could have occurred without your attention.
- 4
Highlight the specific actions you took to prevent the issue.
- 5
Conclude with the positive outcome resulting from your actions.
Example Answers
In my previous role as a Quality Control Technician, I noticed a batch of components had incorrect measurements on the specification sheet. I double-checked the components and discovered they were off by several millimeters. I alerted the production team immediately, preventing faulty assembly and saving the company significant rework costs.
Describe a situation where you led a project to enhance quality control measures. What were the challenges and outcomes?
How to Answer
- 1
Choose a specific project that had clear quality improvements.
- 2
Highlight your role and the steps you took to lead the project.
- 3
Mention specific challenges you faced and how you overcame them.
- 4
Discuss measurable outcomes or improvements resulting from your actions.
- 5
Use the STAR method: Situation, Task, Action, Result.
Example Answers
In my previous role, I led a project to improve our product inspection process. We faced challenges with inconsistent inspection results. I implemented a standardized checklist and trained the team. The outcome was a 30% reduction in product defects over three months.
Tell us about a time when you had to communicate a quality concern to a non-technical team member. How did you ensure they understood the issue?
How to Answer
- 1
Use a specific example from your experience.
- 2
Explain the quality issue in simple terms.
- 3
Relate the impact of the issue on their work or the project.
- 4
Use visual aids or analogies if applicable.
- 5
Follow up to ensure they understood the problem.
Example Answers
In my previous role, I noticed that a batch of products did not meet our quality standards. I scheduled a meeting with the marketing team to explain that the defect could affect customer satisfaction. I used clear visuals to show the differences and how it could impact their campaigns. After the meeting, I asked for their feedback to confirm their understanding.
Describe a conflict you encountered while enforcing quality standards and how you resolved it.
How to Answer
- 1
Identify a specific conflict related to quality standards.
- 2
Explain the root cause of the conflict clearly and concisely.
- 3
Describe the actions you took to address the conflict.
- 4
Highlight the outcome of your resolution efforts.
- 5
Reflect on what you learned from the experience.
Example Answers
In my previous role, a production team resisted a new quality protocol that I introduced. I found that the team felt it increased their workload without clear benefits. I organized a meeting to explain the importance of the standards for product safety. By involving them in the implementation process, we achieved compliance and improved product quality, and I learned the value of collaboration.
Describe a time when you had to adapt quickly to a change in quality control procedures.
How to Answer
- 1
Use the STAR method to structure your response
- 2
Focus on a specific example from your past experience
- 3
Highlight the challenge of the change in procedures
- 4
Emphasize your role in adapting and leading the change
- 5
Conclude with the positive outcome of your actions
Example Answers
In my previous job, the company suddenly changed the inspection procedure for packaging. I quickly organized a training session for the quality control team to ensure everyone understood the new protocol. This adaptation helped us maintain our quality standards, and we passed the next audit with zero issues.
Tell us about a time when you trained team members on quality procedures. How did you ensure successful learning outcomes?
How to Answer
- 1
Select a specific training experience with measurable results
- 2
Outline the key quality procedures you focused on
- 3
Describe your training methods and materials used
- 4
Discuss how you assessed the learning outcomes
- 5
Mention any follow-up actions taken to reinforce training
Example Answers
In my previous role, I trained a team of 10 on our new quality control software. I developed a hands-on workshop where team members could practice using the software in real scenarios. After the training, I assessed their understanding through quizzes and practical tests, leading to a 90% pass rate.
Can you describe an initiative you took to proactively improve quality in a past role?
How to Answer
- 1
Identify a specific quality issue you noticed in your work.
- 2
Explain the steps you took to address the issue.
- 3
Highlight any team collaboration or support you received.
- 4
Share the measurable impact of your initiative on quality outcomes.
- 5
Reflect on what you learned from the experience.
Example Answers
In my previous role, I noticed that our product defect rate was higher than the industry standard. I initiated a weekly quality review meeting with the production team to analyze defects. We implemented a new checklist for quality checks during production. This led to a 25% reduction in defects over three months, improving our customer satisfaction scores.
Describe a situation where you managed quality control tasks under tight deadlines. How did you handle it?
How to Answer
- 1
Identify a specific project with a deadline.
- 2
Explain the quality control tasks you were responsible for.
- 3
Discuss the challenges faced due to the tight timeline.
- 4
Highlight the strategies you used to meet the deadlines.
- 5
Conclude with the successful outcome of your actions.
Example Answers
In my previous role, I was tasked with ensuring quality for a product launch that had a very tight deadline. I created a prioritized checklist for the critical quality checks and divided the tasks among the team. We held daily stand-up meetings to track progress and address any issues quickly. In the end, we completed the quality assessments on time, leading to a successful product launch with zero defects reported in the first month.
Don't Just Read Quality Control Coordinator Questions - Practice Answering Them!
Reading helps, but actual practice is what gets you hired. Our AI feedback system helps you improve your Quality Control Coordinator interview answers in real-time.
Personalized feedback
Unlimited practice
Used by hundreds of successful candidates
Can you give an example of how you've contributed to continuous improvement in a quality control role?
How to Answer
- 1
Identify a specific improvement project you led or participated in.
- 2
Highlight the methods used for analysis, such as root cause analysis or data tracking.
- 3
Discuss measurable outcomes or benefits achieved from your contributions.
- 4
Emphasize collaboration with team members or other departments.
- 5
Keep your answer focused on your direct actions and results.
Example Answers
In my last role, I led a project to reduce defects by implementing a new inspection process. We analyzed previous data and discovered key areas of concern. By adjusting our procedures, we decreased defects by 20% within three months.
Technical Interview Questions
What are some of the key quality control standards you are familiar with, and how have you implemented them in the past?
How to Answer
- 1
Identify specific standards like ISO 9001 or Six Sigma that are relevant to the role.
- 2
Mention your experience in applying these standards in previous roles.
- 3
Provide concrete examples of processes you improved or issues you resolved using these standards.
- 4
Highlight any tools or software you used for quality control compliance.
- 5
Discuss the impact your implementation had on overall quality or efficiency.
Example Answers
In my previous role, I implemented ISO 9001 standards by creating a detailed documentation process for our production line, which reduced errors by 20%.
What inspection techniques have you used in previous quality control roles, and which do you find most effective?
How to Answer
- 1
Identify specific inspection techniques you have experience with
- 2
Explain the context in which you used each technique
- 3
Discuss the effectiveness of these techniques based on measurable outcomes
- 4
Mention why you prefer one technique over others
- 5
Connect your experience to the needs of the position you are applying for
Example Answers
In my previous role, I used visual inspection and automated testing. Visual inspection was crucial for identifying surface defects, while automated testing helped in checking functionality. I found automated testing most effective due to its speed and accuracy, allowing us to catch errors early in the production process.
Don't Just Read Quality Control Coordinator Questions - Practice Answering Them!
Reading helps, but actual practice is what gets you hired. Our AI feedback system helps you improve your Quality Control Coordinator interview answers in real-time.
Personalized feedback
Unlimited practice
Used by hundreds of successful candidates
How do you apply statistical process control (SPC) in your quality control processes?
How to Answer
- 1
Explain the key SPC tools you use, such as control charts.
- 2
Discuss how you monitor process performance over time with SPC.
- 3
Provide an example of how SPC helped in a previous job.
- 4
Mention how you train your team on SPC methods and their importance.
- 5
Emphasize continuous improvement based on SPC data analysis.
Example Answers
I use control charts for monitoring production processes. For instance, in my last role, we tracked defect rates and identified trends which allowed us to take corrective actions before quality issues escalated.
Can you explain your approach to conducting a root cause analysis when a quality issue arises?
How to Answer
- 1
Define the problem clearly and gather relevant data.
- 2
Use techniques like the 5 Whys or Fishbone Diagram to identify root causes.
- 3
Involve team members who are familiar with the issue for broader insights.
- 4
Develop and implement corrective actions based on the identified root causes.
- 5
Follow up to ensure that the solutions effectively resolve the issue.
Example Answers
When a quality issue arises, I first define the problem and collect all necessary data, then I use the 5 Whys method to drill down to the root cause. I involve my team to get different perspectives, after which I create corrective actions and monitor their effectiveness through follow-up assessments.
What is your experience with quality control documentation and how do you ensure accuracy and compliance?
How to Answer
- 1
Highlight specific types of documentation you've worked with, such as SOPs or quality manuals
- 2
Mention tools or systems you use to track and manage the documentation
- 3
Discuss your process for reviewing and updating documents for compliance
- 4
Provide examples of how you handled discrepancies or errors in documentation
- 5
Emphasize the importance of training and communication in maintaining quality standards
Example Answers
In my previous role, I managed quality control documentation that included SOPs, inspection reports, and compliance checklists. I used a document management system to ensure easy access and tracking of revisions. I regularly conducted audits to review documentation accuracy and provided training sessions to staff on compliance, ensuring everyone understood the quality standards.
How familiar are you with ISO 9001 standards, and how have you applied them in your previous roles?
How to Answer
- 1
Review the key principles of ISO 9001: customer focus, leadership, engagement of people, process approach, improvement, evidence-based decision making, relationship management.
- 2
Share specific examples of how you implemented ISO 9001 in past roles, such as developing documentation or conducting audits.
- 3
Mention any training or certifications you have related to ISO 9001.
- 4
Discuss the outcomes or improvements achieved from applying these standards in your work.
- 5
Be honest about your level of familiarity but emphasize your willingness to learn.
Example Answers
I have a solid understanding of ISO 9001 standards, and I became familiar with them while working as a Quality Analyst. I led a team to document our quality management processes, which improved our compliance and resulted in a 20% reduction in errors reported.
How do you ensure that testing and measurement equipment is properly calibrated?
How to Answer
- 1
Use a standard operating procedure for calibration.
- 2
Keep a schedule for regular calibration and maintenance checks.
- 3
Document all calibration results and any adjustments made.
- 4
Train staff on the importance of calibration and how to perform it.
- 5
Ensure equipment is calibrated according to manufacturer specifications.
Example Answers
I ensure proper calibration by following a strict standard operating procedure that outlines the necessary steps and frequency of calibration. I keep detailed records of all calibrations performed.
What is your understanding of Lean Six Sigma, and how have you applied its principles in quality control?
How to Answer
- 1
Define Lean Six Sigma and its goals of reducing waste and improving quality.
- 2
Mention relevant tools like DMAIC (Define, Measure, Analyze, Improve, Control).
- 3
Give a specific example of a project where you used these principles.
- 4
Highlight measurable outcomes from your application of Lean Six Sigma.
- 5
Emphasize teamwork and continuous improvement as key aspects.
Example Answers
Lean Six Sigma is a methodology that aims to improve processes by eliminating waste and reducing variation. In my previous role, I led a project using DMAIC to streamline our quality control processes, which resulted in a 20% reduction in defect rates.
What experience do you have with non-destructive testing methods in quality control?
How to Answer
- 1
Identify specific non-destructive testing methods you have used.
- 2
Explain your role and responsibilities regarding these methods.
- 3
Mention any certifications or training related to non-destructive testing.
- 4
Provide examples of projects where you applied these testing methods.
- 5
Highlight the impact of your testing on product quality and safety.
Example Answers
In my previous role as a quality control inspector, I used ultrasonic testing to detect flaws in welds. I was responsible for conducting these tests and reporting findings, which helped us improve our welding techniques and reduce defects by 20%.
What has been your role in conducting quality audits, and what are the key elements you focus on during an audit?
How to Answer
- 1
Describe specific audits you have led or participated in.
- 2
Mention the standards or guidelines you follow during audits.
- 3
Highlight key areas like compliance, process effectiveness, and documentation.
- 4
Emphasize teamwork and communication with other departments.
- 5
Provide examples of findings and how you addressed them.
Example Answers
In my previous role, I led quarterly quality audits where I focused on compliance with ISO standards and effective documentation practices. I collaborated with various teams to ensure all processes were aligned, and addressed any non-conformances promptly. One key finding was a documentation gap that we resolved by implementing a new tracking system.
Don't Just Read Quality Control Coordinator Questions - Practice Answering Them!
Reading helps, but actual practice is what gets you hired. Our AI feedback system helps you improve your Quality Control Coordinator interview answers in real-time.
Personalized feedback
Unlimited practice
Used by hundreds of successful candidates
How do you develop and implement corrective actions when quality issues are found?
How to Answer
- 1
Identify the root cause of the quality issue
- 2
Collaborate with relevant stakeholders to brainstorm solutions
- 3
Develop a clear and actionable corrective action plan
- 4
Implement the corrective actions with proper training if needed
- 5
Monitor the effectiveness of the actions and adjust as necessary
Example Answers
When a quality issue is found, I first conduct a root cause analysis to pinpoint the underlying problem. Then, I work with the production team to develop a corrective action plan, which outlines the steps to fix the issue. After implementation, I make sure to monitor the results to ensure the problem is resolved and prevent recurrences.
Quality Control Coordinator Position Details
Recommended Job Boards
These job boards are ranked by relevance for this position.
Related Positions
Ace Your Next Interview!
Practice with AI feedback & get hired faster
Personalized feedback
Used by hundreds of successful candidates
Ace Your Next Interview!
Practice with AI feedback & get hired faster
Personalized feedback
Used by hundreds of successful candidates