Top 29 Refrigeration Mechanic Interview Questions and Answers [Updated 2025]
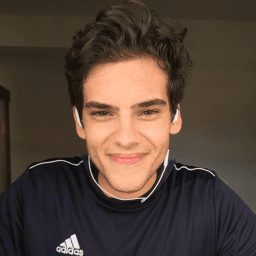
Andre Mendes
•
March 30, 2025
Preparing for a refrigeration mechanic interview can be daunting, but having the right guidance can make all the difference. In this post, we cover the most common interview questions for the refrigeration mechanic role, providing example answers and effective tips to help you stand out. Whether you're a seasoned professional or just starting, this guide will boost your confidence and enhance your interview skills.
Download Refrigeration Mechanic Interview Questions in PDF
To make your preparation even more convenient, we've compiled all these top Refrigeration Mechanicinterview questions and answers into a handy PDF.
Click the button below to download the PDF and have easy access to these essential questions anytime, anywhere:
List of Refrigeration Mechanic Interview Questions
Technical Interview Questions
What are the main components of a refrigeration system and their functions?
How to Answer
- 1
Identify major components like compressor, condenser, evaporator, and expansion valve.
- 2
Briefly describe the function of each component in the refrigeration cycle.
- 3
Use simple terms to explain technical concepts.
- 4
Structure your response logically, starting from compression to expansion.
- 5
Keep it concise, aim for clarity over detail.
Example Answers
A refrigeration system mainly consists of a compressor, condenser, evaporator, and expansion valve. The compressor circulates refrigerant, the condenser dissipates heat, the evaporator absorbs heat from the environment, and the expansion valve controls the refrigerant flow.
How would you troubleshoot a refrigeration system that is not cooling effectively?
How to Answer
- 1
Check the refrigerant level for leaks or low charge
- 2
Inspect the compressor for proper operation and any unusual noises
- 3
Examine the condenser coils for cleanliness and airflow issues
- 4
Test the thermostat settings and verify the proper temperature control
- 5
Look for any obstructions in the evaporator and air ducts
Example Answers
First, I would check the refrigerant level to see if it's low or leaking. A refrigerant leak can cause cooling problems. Next, I’d inspect the compressor to ensure it's functioning properly and listen for any strange noises. Finally, I would clean the condenser coils to improve heat exchange.
Don't Just Read Refrigeration Mechanic Questions - Practice Answering Them!
Reading helps, but actual practice is what gets you hired. Our AI feedback system helps you improve your Refrigeration Mechanic interview answers in real-time.
Personalized feedback
Unlimited practice
Used by hundreds of successful candidates
What is the purpose of a drier in a refrigeration system?
How to Answer
- 1
Explain that a drier removes moisture from refrigerant.
- 2
Mention that moisture can cause corrosion and damage to the system.
- 3
State that a drier helps maintain efficiency and prolongs equipment life.
- 4
Discuss the different types of driers, like filter driers and liquid line driers.
- 5
Emphasize the importance of regular maintenance and checking the drier's condition.
Example Answers
A drier in a refrigeration system removes moisture from the refrigerant to prevent corrosion and damage. Keeping moisture out helps maintain the system's efficiency and prolongs its life.
Can you explain the environmental impact of common refrigerants and any alternatives?
How to Answer
- 1
Identify common refrigerants like CFCs, HCFCs, and HFCs.
- 2
Discuss their effects on ozone depletion and global warming potential.
- 3
Mention current regulations on refrigerants like the Montreal Protocol.
- 4
Introduce alternatives such as natural refrigerants (e.g., ammonia, CO2) and low-GWP options.
- 5
Emphasize the importance of transitioning to eco-friendly refrigerants.
Example Answers
Common refrigerants like R-22 and R-410A have high global warming potential and contribute significantly to climate change. CFCs are harmful to the ozone layer. Alternatives such as CO2 and ammonia are more environmentally friendly and have lower global warming potential. The industry is moving towards these sustainable options due to regulations like the Montreal Protocol.
What refrigerant handling regulations are you familiar with and how do you comply with them?
How to Answer
- 1
Identify key refrigerant regulations such as EPA 608 and local codes
- 2
Discuss your certification status and any training completed
- 3
Explain your procedures for safe refrigerant handling and recovery
- 4
Mention record-keeping practices for refrigerant use and disposal
- 5
Emphasize importance of staying updated on regulations and best practices
Example Answers
I am familiar with EPA 608 regulations, and I hold an EPA certification. I follow protocols for safe refrigerant handling and recovery, ensuring that I capture any refrigerants during repairs. I keep detailed records of all refrigerant transactions to comply with regulatory requirements.
What tools and equipment do you use to measure refrigerant levels and diagnose issues?
How to Answer
- 1
Mention specific tools like manifold gauges and digital refrigerant scales.
- 2
Explain how you use each tool in practice.
- 3
Include any diagnostic equipment you regularly employ.
- 4
Emphasize your experience or certifications related to these tools.
- 5
Show your understanding of safety protocols when handling refrigerants.
Example Answers
I regularly use manifold gauges to check refrigerant pressures and temperatures. In addition, I utilize a digital refrigerant scale for precise measurements when charging systems. My experience also includes leak detectors to diagnose any issues, and I always follow safety protocols when handling refrigerants.
Can you walk us through your process for replacing a compressor?
How to Answer
- 1
Start by ensuring the system is off and safely drained of refrigerant according to EPA regulations.
- 2
Remove any necessary access panels and disconnect electrical wiring from the old compressor.
- 3
Detach the compressor from the mounting brackets and the refrigerant lines using appropriate tools.
- 4
Install the new compressor by reversing the removal steps, ensuring all connections are tight and leak-free.
- 5
Test the system thoroughly after installation to ensure proper function and check for leaks.
Example Answers
First, I ensure the system is powered down and safely recover any refrigerant. Next, I remove access panels and disconnect the wiring from the compressor. I then detach the compressor from its mount and refrigerant lines. I install the new compressor by securing it in place and reconnecting the lines and wiring, ensuring everything is tight. Finally, I test the system to confirm it's functioning correctly and check for any leaks.
What considerations do you take into account when designing a new refrigeration system?
How to Answer
- 1
Assess the application requirements, such as temperature range and load capacity.
- 2
Select appropriate refrigerants based on environmental regulations and efficiency.
- 3
Evaluate the energy efficiency of the system to reduce operational costs.
- 4
Consider the installation space and accessibility for maintenance.
- 5
Plan for scalability or future upgrades based on potential needs.
Example Answers
When designing a new refrigeration system, I first assess the temperature range and load requirements to ensure the system will perform adequately. I choose refrigerants that are efficient and compliant with regulations. Energy efficiency is a top priority to lower operational costs, and I also plan for easy access for maintenance.
What steps do you take to assess the functionality of an expansion valve?
How to Answer
- 1
Check for visible signs of leakage or damage.
- 2
Measure the inlet and outlet pressures to ensure they meet specifications.
- 3
Observe the temperature difference across the valve to assess its performance.
- 4
Listen for unusual noises that may indicate a malfunction.
- 5
Consult manufacturer specifications to compare actual performance against recommended values.
Example Answers
I start by inspecting the expansion valve for any visible leaks or physical damage. Next, I measure the inlet and outlet pressures to ensure they are within the recommended range. Then, I check the temperature difference across the valve to confirm it is properly regulating the refrigerant flow.
What is the ideal temperature range for commercial refrigeration, and why?
How to Answer
- 1
State the temperature range typically used for commercial refrigeration, generally between 32°F and 40°F (0°C to 4°C).
- 2
Explain the importance of maintaining this range for food safety and product quality.
- 3
Mention how different products may require slight adjustments within this range.
- 4
Highlight the role of refrigeration in preventing spoilage and bacterial growth.
- 5
Include any relevant regulations or standards related to commercial refrigeration.
Example Answers
The ideal temperature range for commercial refrigeration is between 32°F and 40°F. This range is crucial for food safety as it slows bacterial growth, ensuring that perishable items remain fresh and safe for consumption.
Don't Just Read Refrigeration Mechanic Questions - Practice Answering Them!
Reading helps, but actual practice is what gets you hired. Our AI feedback system helps you improve your Refrigeration Mechanic interview answers in real-time.
Personalized feedback
Unlimited practice
Used by hundreds of successful candidates
How often do you recommend servicing a refrigeration system, and what does a typical service include?
How to Answer
- 1
Mention a servicing frequency, typically every 6 months or annually.
- 2
Include key components to check like evaporator coils, condenser coils, and refrigerant levels.
- 3
Highlight the importance of cleaning and maintenance to ensure efficiency.
- 4
Discuss safety checks, such as electrical components and leak detection.
- 5
Emphasize the potential cost savings from regular maintenance.
Example Answers
I recommend servicing a refrigeration system every six months. A typical service includes checking the refrigerant levels, cleaning the evaporator and condenser coils, inspecting electrical connections, and testing safety features. Regular maintenance helps prevent costly breakdowns.
Behavioral Interview Questions
Can you describe a time when you identified a major issue in a refrigeration system? What steps did you take to resolve it?
How to Answer
- 1
Briefly describe the situation and the refrigeration system involved.
- 2
Explain how you diagnosed the major issue clearly and concisely.
- 3
Outline the steps you took to resolve the issue, highlighting any tools or techniques used.
- 4
Mention any collaboration with team members or communication with clients.
- 5
Conclude with the result of your actions and any lessons learned.
Example Answers
In a commercial kitchen, I noticed that the walk-in freezer wasn't maintaining the correct temperature. I inspected the evaporator coils and identified a refrigerant leak. I used leak detection tools to confirm the location, repaired the leak, and recharged the system with the appropriate refrigerant. The freezer returned to optimal operation, and I implemented a regular maintenance check to prevent future issues.
Tell me about a time when you had to work closely with others to complete a refrigeration installation. What was your role?
How to Answer
- 1
Identify a specific project where teamwork was essential.
- 2
Describe your role clearly and how you contributed to the team effort.
- 3
Explain the outcome of the installation and any challenges faced.
- 4
Emphasize communication and collaboration skills.
- 5
Highlight any technical skills you applied during the process.
Example Answers
During a large commercial refrigeration installation last year, I worked with a team of four to set up a new HVAC system. My role was to oversee the piping installation, ensuring proper connections and refrigerant flow. We faced some tight deadlines, and I coordinated with electricians to manage our schedule. The installation was completed on time, significantly improving the client's energy efficiency.
Don't Just Read Refrigeration Mechanic Questions - Practice Answering Them!
Reading helps, but actual practice is what gets you hired. Our AI feedback system helps you improve your Refrigeration Mechanic interview answers in real-time.
Personalized feedback
Unlimited practice
Used by hundreds of successful candidates
Describe a situation where you had to adjust your approach on the job due to unforeseen circumstances.
How to Answer
- 1
Think of a specific incident that required you to adapt.
- 2
Focus on the problem you faced and the immediate solution you implemented.
- 3
Emphasize the skills or knowledge that helped you adjust.
- 4
Highlight the positive outcome of your adjustment.
- 5
Keep your explanation clear and to the point.
Example Answers
During a routine maintenance check, I discovered that a refrigerant leak was much worse than anticipated. I quickly shifted my focus to containment and prioritized fixing that issue before continuing with the maintenance tasks. This adjustment prevented further equipment damage and allowed us to resolve the problem swiftly.
Have you ever had to train or mentor a less experienced mechanic? How did you ensure they learned effectively?
How to Answer
- 1
Share a specific example of a time you mentored a colleague.
- 2
Explain the methods you used to teach them, such as hands-on practice or shadowing.
- 3
Discuss how you assessed their understanding and provided feedback.
- 4
Mention any resources or materials you used to aid their learning.
- 5
Highlight the positive outcome of your mentorship.
Example Answers
Yes, I mentored a new mechanic last summer. I had them shadow me during installations and guided them through each step. We had regular check-ins to discuss their progress and I provided them with manuals and cheat sheets. By the end of the season, they were able to handle installations independently.
Talk about a time when you went above and beyond your job responsibilities in a refrigeration project.
How to Answer
- 1
Choose a specific project where you added value.
- 2
Emphasize your initiative and proactive actions.
- 3
Highlight the positive outcome or impact of your efforts.
- 4
Explain how it benefited the team or customer.
- 5
Keep the story concise and focused on your contributions.
Example Answers
During a commercial refrigeration upgrade, I noticed the existing system had inefficiencies. I researched and proposed a more eco-friendly refrigerant that reduced energy costs. The customer was thrilled with the savings, and our team received recognition for sustainability.
Describe a time when you had a disagreement with a coworker about a technical issue. How did you resolve it?
How to Answer
- 1
Choose a specific disagreement related to refrigeration or HVAC work.
- 2
Describe the differing perspectives clearly and objectively.
- 3
Explain the steps you took to resolve the issue, focusing on communication and collaboration.
- 4
Highlight any technical resolution or compromise that was reached.
- 5
Emphasize what you learned from the experience and how it improved teamwork.
Example Answers
In my previous job, my coworker and I disagreed on the best method to charge a refrigeration system. I believed using a superheat method was best, while he favored a liquid charge method. We decided to consult our team lead for a second opinion, who suggested a hybrid approach. By discussing and combining our methods, we achieved better efficiency, and I learned the value of collaboration in problem-solving.
Reflecting on your previous roles, what do you consider your greatest strength as a refrigeration mechanic?
How to Answer
- 1
Identify a specific technical skill relevant to refrigeration.
- 2
Mention a tangible result that demonstrates this strength.
- 3
Link your strength to a benefit for the employer or client.
- 4
Keep your answer focused and concise.
- 5
Practice delivering your answer confidently.
Example Answers
My greatest strength is my attention to detail in diagnosing system issues. For example, by meticulously checking coolant levels and pressure, I was able to prevent a major system failure, saving the company significant repair costs.
Can you describe a time when you had to be particularly patient with a complex mechanical problem?
How to Answer
- 1
Choose a specific example that shows your patience.
- 2
Explain the complexity of the problem clearly.
- 3
Describe the steps you took to diagnose and resolve the issue.
- 4
Highlight the outcome and what you learned from the experience.
- 5
Mention how this patience benefited the team or the project.
Example Answers
During a commercial refrigeration installation, I faced a persistent leak in the system. I carefully traced the problem through multiple layers of piping, systematically checking each joint and connection over several hours. Eventually, I found a tiny puncture in a hard-to-reach spot. My patience led to a successful fix and ensured the system operated efficiently.
Situational Interview Questions
If you find a significant leak in a refrigeration system during a routine check, what would you do?
How to Answer
- 1
Safety first: turn off the system to prevent further damage.
- 2
Identify the source of the leak carefully.
- 3
Evaluate the system and determine the necessary repair actions.
- 4
Document the leak and repairs for future reference.
- 5
Notify the supervisor or team about the incident.
Example Answers
I would first turn off the refrigeration system to avoid any complications. Then I'd locate the source of the leak and assess what repairs are needed. After documenting my findings, I would inform my supervisor about the situation.
You receive a call about a refrigeration system down at a critical facility. How would you prioritize your actions?
How to Answer
- 1
Assess the urgency of the situation based on the facility's critical function.
- 2
Gather all relevant information about the system and the issue from the caller.
- 3
Determine if immediate action is required or if you need to gather resources first.
- 4
Communicate your plan and estimated arrival time to the caller.
- 5
Prepare necessary tools and equipment while en route to the site.
Example Answers
I would first assess how critical the refrigeration system is to the facility's operations. Then, I would gather necessary details from the caller about the issue, such as the symptoms and any previous maintenance. Based on this, I would prioritize my actions to address the emergency effectively, ensuring I communicate my estimated time of arrival.
Don't Just Read Refrigeration Mechanic Questions - Practice Answering Them!
Reading helps, but actual practice is what gets you hired. Our AI feedback system helps you improve your Refrigeration Mechanic interview answers in real-time.
Personalized feedback
Unlimited practice
Used by hundreds of successful candidates
Imagine you're on-site and a customer is unhappy due to a delay in repairs. How would you handle the situation?
How to Answer
- 1
Listen actively to the customer's concerns without interrupting.
- 2
Acknowledge their frustration and express empathy for their situation.
- 3
Provide a clear explanation of the delay and what you are doing to resolve it.
- 4
Offer reassurance by outlining next steps and an estimated timeline.
- 5
Follow up with the customer after the repairs to ensure satisfaction.
Example Answers
I would first listen to the customer to understand their concerns clearly. I would acknowledge their frustration and apologize for the inconvenience caused by the delay. Then, I would explain the reason for the delay and inform them of the steps I am taking to expedite the repairs. I would give them a timeframe for when they can expect the repair to be completed and assure them that I will keep them updated.
You are tasked with evaluating an old refrigeration unit for potential repair versus replacement. What factors would you consider?
How to Answer
- 1
Assess the age and condition of the refrigeration unit
- 2
Consider the cost of necessary repairs versus replacement costs
- 3
Evaluate the energy efficiency of the unit compared to new models
- 4
Review the availability of replacement parts and service
- 5
Analyze the impact on operations and downtime during repairs or replacement
Example Answers
I would first check the age and overall condition of the unit, as older units typically have more issues. Then, I’d calculate the repair costs and compare them to the quote for a new unit. Energy efficiency is also crucial, as new models often save a significant amount on energy bills. I’d consider how often parts need replacing and the potential downtime for repairs versus a new installation.
If you encounter a safety hazard while working on a unit, how would you handle it?
How to Answer
- 1
Identify the hazard clearly and assess its risk.
- 2
Stop work immediately to ensure personal and team safety.
- 3
Report the hazard to a supervisor or safety officer.
- 4
Follow company procedures for hazard handling and reporting.
- 5
Ensure the area is safe before resuming work.
Example Answers
If I find a safety hazard, I would stop working immediately, assess the risk, and inform my supervisor about the issue. Then, I would follow our safety protocols to ensure that everyone is safe before any work continues.
You are assigned to a project that requires collaboration with electrical engineers. How would you approach this?
How to Answer
- 1
Establish clear communication with the engineers from the start
- 2
Understand their needs and concerns related to refrigeration systems
- 3
Share your expertise and knowledge of refrigeration mechanics
- 4
Set regular meetings to discuss progress and address issues
- 5
Document your conversations and decisions for future reference
Example Answers
I would start by setting up a meeting with the electrical engineers to understand their requirements for the project. Communication is key, so I would ensure we have regular check-ins to address any concerns they might have about the integration of our systems.
How would you manage your time when tasked with multiple refrigeration repairs in a single day?
How to Answer
- 1
Prioritize jobs based on urgency and impact.
- 2
Allocate specific time slots for each repair based on complexity.
- 3
Communicate with clients about estimated arrival and completion times.
- 4
Prepare tools and parts before starting to minimize downtime.
- 5
Keep a detailed log of repairs and time spent for future reference.
Example Answers
I would start by prioritizing the repairs based on their urgency. For instance, if one unit is down in a commercial setting, I would address that first. Then, I'd allocate time slots for each job and prepare my tools in advance to ensure efficiency.
If you were to design a new energy-efficient refrigeration system, what features would you prioritize?
How to Answer
- 1
Focus on energy efficiency through advanced refrigerants
- 2
Incorporate smart technology for monitoring and control
- 3
Emphasize insulation and heat exchange efficiency
- 4
Consider renewable energy integration
- 5
Plan for easy maintenance and repair to reduce downtime
Example Answers
I would prioritize using low-GWP refrigerants and a variable speed compressor to enhance efficiency. Additionally, smart sensors could optimize cooling based on demand.
You lack a specific tool for a repair. How do you improvise to complete the job effectively?
How to Answer
- 1
Assess the job requirements to understand what the tool would accomplish.
- 2
Consider available tools or materials on hand that can serve a similar purpose.
- 3
Think creatively about how to use your knowledge and skills to substitute the missing tool.
- 4
Communicate with your team or supervisor about the situation and seek input if necessary.
- 5
Ensure the improvised solution meets safety standards and doesn't compromise the repair quality.
Example Answers
If I find myself without a specific wrench, I would first assess how critical that wrench is for the job. Then, I might use a pair of pliers or a vice grip that I have in my toolbox, adjusting my technique accordingly to ensure a clean fit. I'd check in with the team to see if anyone has the correct tool, and ensure my improvised method is safe to use.
Refrigeration Mechanic Position Details
Recommended Job Boards
CareerBuilder
www.careerbuilder.com/jobs-refrigeration-mechanicThese job boards are ranked by relevance for this position.
Related Positions
Ace Your Next Interview!
Practice with AI feedback & get hired faster
Personalized feedback
Used by hundreds of successful candidates
Ace Your Next Interview!
Practice with AI feedback & get hired faster
Personalized feedback
Used by hundreds of successful candidates