Top 31 Reliability Technician Interview Questions and Answers [Updated 2025]
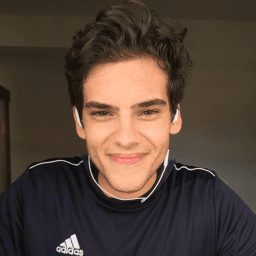
Andre Mendes
•
March 30, 2025
Preparing for a Reliability Technician interview can be daunting, but we're here to help you succeed. In this post, you'll find a collection of the most common interview questions for this critical role, complete with example answers and tips on how to respond effectively. Whether you're a seasoned professional or new to the field, this guide will equip you with the insights you need to impress potential employers.
Download Reliability Technician Interview Questions in PDF
To make your preparation even more convenient, we've compiled all these top Reliability Technicianinterview questions and answers into a handy PDF.
Click the button below to download the PDF and have easy access to these essential questions anytime, anywhere:
List of Reliability Technician Interview Questions
Technical Interview Questions
What is your experience with conducting reliability audits and what do you look for?
How to Answer
- 1
Summarize your previous experience with reliability audits clearly.
- 2
Mention specific methodologies you have used, such as FMEA or RCA.
- 3
Identify key areas to look for during audits, like system performance and failure rates.
- 4
Discuss how you report findings and implement changes based on audit results.
- 5
Emphasize your attention to detail and problem-solving skills.
Example Answers
In my previous role, I conducted quarterly reliability audits using FMEA. I focused on failure rates and root causes, ensuring each system's performance metrics were evaluated. After identifying issues, I worked with the engineering team to implement corrective actions.
What are the key steps you take when performing preventive maintenance on machinery?
How to Answer
- 1
Identify and understand the maintenance schedule for the machinery.
- 2
Gather the necessary tools and replacement parts before starting inspections.
- 3
Perform a thorough inspection of the machinery to identify wear and tear.
- 4
Clean all components and lubricate moving parts as recommended in the manual.
- 5
Document any findings and maintenance performed for future reference.
Example Answers
I follow a maintenance schedule, checking the machinery regularly. First, I gather tools and parts, then inspect the equipment for any signs of damage. After cleaning and lubricating as needed, I document everything I've done before finishing up.
Don't Just Read Reliability Technician Questions - Practice Answering Them!
Reading helps, but actual practice is what gets you hired. Our AI feedback system helps you improve your Reliability Technician interview answers in real-time.
Personalized feedback
Unlimited practice
Used by hundreds of successful candidates
Explain how you have used data analysis to improve system reliability in the past.
How to Answer
- 1
Identify a specific project where you used data analysis.
- 2
Quantify the impact of your analysis on system reliability.
- 3
Discuss the tools and methods you used for data analysis.
- 4
Explain how your findings led to actionable improvements.
- 5
Reflect on the results or metrics post-implementation.
Example Answers
In my previous role, I analyzed downtime data from our equipment over six months using Excel. I identified that 30% of failures were from a specific part. After implementing a change in our maintenance schedule for that part, reliability improved by 25%.
What reliability testing methods are you familiar with, and how do you choose which to apply?
How to Answer
- 1
List specific reliability testing methods you know, like MTBF, FMEA, and accelerated life testing.
- 2
Explain the context or goals of each method briefly.
- 3
Discuss how you assess the needs of the project or product when selecting a method.
- 4
Mention any relevant standards or guidelines that inform your choice.
- 5
Provide an example of a past experience where you applied a method effectively.
Example Answers
I am familiar with methods like MTBF, FMEA, and accelerated life testing. I choose based on project requirements; for example, if I'm assessing product durability, I prefer accelerated life testing to expose potential weaknesses early.
Which tools or software do you use for reliability analysis and why do you prefer them?
How to Answer
- 1
Mention specific tools you are proficient in.
- 2
Explain the purpose of each tool in reliability analysis.
- 3
Share your experiences or outcomes with these tools.
- 4
Highlight any unique features of the tools that you appreciate.
- 5
Align your tool preferences with the job requirements.
Example Answers
I primarily use Weibull++ for reliability analysis because it allows for detailed failure data analysis and provides excellent visualizations for reliability functions. In my experience, it helped reduce our product failure rates by 15%.
Describe the process you follow to conduct root cause analysis for equipment failures.
How to Answer
- 1
Begin with defining the problem clearly to understand the failure context.
- 2
Gather data on the failure, including timestamps, symptoms, and maintenance history.
- 3
Use systematic tools like the 5 Whys or Fishbone diagram to identify potential root causes.
- 4
Validate root causes by testing hypotheses or analyzing further data.
- 5
Develop and implement corrective actions to prevent future failures.
Example Answers
I start by clearly defining the equipment failure to establish what went wrong. Then I collect data such as operational logs and maintenance records. I often use the 5 Whys technique to drill down to the root cause, validating my findings before proposing corrective actions.
What is your experience with calibration of instruments used in reliability testing?
How to Answer
- 1
Describe specific instruments you have calibrated
- 2
Mention any relevant procedures or standards you followed
- 3
Include any software tools you used for calibration
- 4
Highlight the importance of calibration in reliability testing
- 5
Share any results or outcomes from your calibration work
Example Answers
I have calibrated various instruments such as oscilloscopes and multimeters following ISO 9001 standards. I used calibration software to ensure accuracy and record keeping, which improved our testing reliability.
What are common failure modes you have encountered in your work, and how have you addressed them?
How to Answer
- 1
Identify specific failure modes you have experienced.
- 2
Use examples from your work history or projects.
- 3
Explain the impact of each failure mode on operations.
- 4
Describe the methods you used to resolve each issue.
- 5
Highlight any preventive measures you implemented afterward.
Example Answers
In my previous role, a common failure mode was capacitor failures in circuit boards. We addressed this by replacing the capacitors with higher-rated ones and improving the thermal management of the area. This reduced failures by over 30%.
What performance metrics do you track to assess the reliability of systems?
How to Answer
- 1
Identify key reliability metrics like MTBF and MTTR.
- 2
Discuss the importance of tracking failure rates.
- 3
Mention the role of preventive maintenance metrics.
- 4
Include the analysis of downtime and its impact.
- 5
Emphasize the use of trending data for reliability improvement.
Example Answers
I track metrics such as Mean Time Between Failures (MTBF) and Mean Time To Repair (MTTR) to gauge the reliability of systems. These metrics help identify problem areas and improve our maintenance schedules.
Don't Just Read Reliability Technician Questions - Practice Answering Them!
Reading helps, but actual practice is what gets you hired. Our AI feedback system helps you improve your Reliability Technician interview answers in real-time.
Personalized feedback
Unlimited practice
Used by hundreds of successful candidates
What considerations do you take into account when designing a system for reliability?
How to Answer
- 1
Identify critical components and their failure modes
- 2
Understand environmental factors affecting performance
- 3
Incorporate redundancy where necessary
- 4
Plan for regular maintenance and testing
- 5
Use data analytics for predictive reliability enhancements
Example Answers
When designing a system for reliability, I first focus on identifying critical components and their potential failure modes to prioritize reliability efforts. Then, I ensure that environmental factors such as temperature and humidity are accounted for in the design. Incorporating redundancy for key components is also essential to minimize downtime.
What statistical methods do you use in reliability engineering, and can you provide an example?
How to Answer
- 1
Identify common statistical methods used in reliability such as Weibull analysis, reliability block diagrams, or failure rates.
- 2
Mention specific tools or software you use for these analyses, like Minitab or R.
- 3
Provide a concrete example from your experience where you successfully applied a statistical method.
- 4
Discuss the outcome of your analysis and its impact on the project's reliability.
- 5
Keep your explanation clear and avoid jargon unless necessary.
Example Answers
In reliability engineering, I often use Weibull analysis to assess the reliability of products. For instance, in a previous project, I analyzed the failure data of a series of components using Weibull statistics to determine their lifespan. This analysis led to design improvements that reduced the failure rate by 20%.
Situational Interview Questions
If a piece of critical equipment fails, and the team has disagreements on the repair approach, how would you resolve this?
How to Answer
- 1
Stay calm and collected to foster a positive environment.
- 2
Listen to all team members' opinions and concerns.
- 3
Encourage a collaborative discussion to explore options.
- 4
Focus on data and the technical merits of each approach.
- 5
Reach a consensus or utilize a decision-making framework if needed.
Example Answers
I would first listen to everyone's opinions and ensure all voices are heard. Then, I would facilitate a discussion focusing on the technical aspects and data supporting each repair approach, helping the team to reach a consensus based on the best solution.
Imagine you have multiple reliability issues to address at the same time. How would you prioritize them?
How to Answer
- 1
Assess the impact of each issue on operations and safety.
- 2
Consider the time and resources required to address each problem.
- 3
Evaluate the frequency and severity of the failures associated with each issue.
- 4
Consult with stakeholders to understand their priorities and concerns.
- 5
Identify quick wins that can be resolved immediately to build momentum.
Example Answers
I would first evaluate each issue by its potential impact on safety and production. Issues affecting critical operations would take priority. Next, I would look at the resources required and ongoing failures to help rank them effectively.
Don't Just Read Reliability Technician Questions - Practice Answering Them!
Reading helps, but actual practice is what gets you hired. Our AI feedback system helps you improve your Reliability Technician interview answers in real-time.
Personalized feedback
Unlimited practice
Used by hundreds of successful candidates
You discover a potential reliability risk that has not yet caused a failure. What steps would you take to address it?
How to Answer
- 1
Identify the root cause of the risk as quickly as possible
- 2
Assess the potential impact of the risk on operations
- 3
Communicate the risk to relevant stakeholders
- 4
Develop an action plan to mitigate the risk
- 5
Monitor the situation continuously until resolved
Example Answers
First, I would analyze the data to identify the root cause of the reliability risk. Then, I would evaluate how this risk could impact our operations and immediately inform my supervisor and the engineering team. Next, I'd collaborate on a mitigation plan, which may include preventive maintenance schedules or design changes, and ensure that we monitor the area closely until the issue is fully addressed.
You're assigned a new reliability improvement project with a tight deadline. What steps will you take to ensure success?
How to Answer
- 1
Define clear goals and outcomes for the project
- 2
Assess current reliability data to identify key areas for improvement
- 3
Develop a detailed project plan with specific milestones
- 4
Allocate resources and assign responsibilities early on
- 5
Establish regular check-ins to track progress and adjust plans if necessary
Example Answers
First, I would define the specific goals of the reliability improvement project, ensuring they are measurable and aligned with company objectives. Next, I would analyze existing reliability data to pinpoint critical failure points. Then, I'd create a detailed project plan outlining milestones and assign tasks to team members. Regular communication through check-ins would help us stay on track and adjust our approach if needed.
Suppose a team member is consistently underperforming. How would you approach this situation?
How to Answer
- 1
Identify the performance issues clearly and objectively
- 2
Schedule a private conversation to discuss concerns
- 3
Focus on understanding the root causes of the underperformance
- 4
Set specific goals and provide support for improvement
- 5
Follow up regularly to monitor progress and provide feedback
Example Answers
I would first identify specific areas where the team member is underperforming. Then, I would have a one-on-one conversation to discuss my observations and listen to any challenges they might be facing. Together, we would set clear, achievable goals and check in regularly to track their progress.
If you need additional resources to complete a project, how would you approach your manager?
How to Answer
- 1
Clearly define the resources needed and why they are important.
- 2
Prepare to explain how the additional resources will impact project outcomes positively.
- 3
Schedule a one-on-one meeting for a focused discussion.
- 4
Use data or examples to support your request for additional resources.
- 5
Be open to feedback and alternative suggestions from your manager.
Example Answers
I would first gather specific details on the resources I need, such as personnel or equipment. Then I would request a meeting with my manager to discuss the project's goals, showing how these additional resources would lead to a faster and more effective completion.
How would you integrate reliability practices into an ongoing project that lacks them?
How to Answer
- 1
Assess the current project status and identify failure points.
- 2
Engage team members to discuss reliability improvement opportunities.
- 3
Introduce basic reliability metrics and track them over time.
- 4
Implement a reliability testing phase in the project timeline.
- 5
Promote a culture of continuous improvement related to reliability.
Example Answers
First, I would assess the current project to identify any frequent failure points. Then, I would hold a meeting with the team to gather their input on where they see reliability issues. From there, I'd introduce some simple reliability metrics to monitor performance and set targets for improvement. Additionally, I'd allocate time for reliability testing throughout the project phases to catch issues early.
If you were tasked with evaluating a proposed new technology for reliability, what factors would you consider?
How to Answer
- 1
Assess the technology's historical performance data and reliability metrics.
- 2
Evaluate the potential failure modes and their impacts.
- 3
Consider the manufacturability and ease of use of the technology.
- 4
Analyze the compatibility with existing systems and processes.
- 5
Review any testing and validation plans proposed for the technology.
Example Answers
I would start by reviewing the technology's historical performance data to check its reliability metrics. Then, I would identify potential failure modes using FMEA, and assess the impacts of those failures. Additionally, I would ensure the technology integrates well with our existing systems.
You are behind schedule on a reliability project due to unforeseen issues. How do you address this?
How to Answer
- 1
Assess the impact of the delays on project goals
- 2
Communicate with all stakeholders about the challenges
- 3
Identify possible solutions or workarounds
- 4
Prioritize tasks to focus efforts on critical areas
- 5
Adjust the timeline and expectations if necessary
Example Answers
I would first analyze the specific issues causing the delay and assess how they affect the project outcomes. Then, I'd inform my team and management about these challenges and propose a clear plan to address them by focusing on the most critical tasks.
Behavioral Interview Questions
Can you describe a time when you identified a reliability issue in a system and how you resolved it?
How to Answer
- 1
Identify a specific reliability issue you encountered.
- 2
Explain the steps you took to analyze the problem.
- 3
Discuss the solution you implemented and its impact.
- 4
Use metrics or data to quantify the improvement if possible.
- 5
Keep the explanation concise and focused on your role.
Example Answers
In my previous role, I noticed that a specific piece of equipment was failing more frequently than expected. I used historical failure data to trace the issue back to a faulty sensor. I replaced the sensor and implemented a regular inspection schedule, which reduced failures by 30%.
Tell me about a time when you collaborated with engineers or other technicians to improve equipment performance.
How to Answer
- 1
Choose a specific project where collaboration was key.
- 2
Describe the challenge you faced with the equipment.
- 3
Explain your role and contribution to the solution.
- 4
Highlight the outcome and benefits of the collaboration.
- 5
Mention any skills or tools you used during the process.
Example Answers
In my previous role, we had issues with a conveyor system that was repeatedly failing. I collaborated with engineers to analyze performance data and pinpoint root causes. I contributed by suggesting adjustments to the timing sensors, which improved the reliability by 30%. This also reduced downtime significantly, saving the company both time and money.
Don't Just Read Reliability Technician Questions - Practice Answering Them!
Reading helps, but actual practice is what gets you hired. Our AI feedback system helps you improve your Reliability Technician interview answers in real-time.
Personalized feedback
Unlimited practice
Used by hundreds of successful candidates
Describe a situation where you had to make a critical decision under pressure. What was the outcome?
How to Answer
- 1
Choose a relevant and specific example from your experience
- 2
Highlight the factors that contributed to the pressure
- 3
Explain the decision-making process clearly
- 4
Discuss the outcome and what you learned from the situation
- 5
Keep your answer focused and concise
Example Answers
During a system failure last summer, I quickly analyzed several malfunction reports and determined that a specific component was likely at fault. I prioritized repairs over routine checks and coordinated with the team to resolve the issue in under two hours. This minimized downtime and the team learned better prioritization under pressure.
Have you ever taken the lead on a reliability project? What challenges did you face and how did you address them?
How to Answer
- 1
Identify a specific project where you led the reliability efforts
- 2
Describe the challenges you encountered in detail
- 3
Explain the specific actions you took to overcome those challenges
- 4
Highlight the positive outcomes or results from your leadership
- 5
Connect your experience to how it makes you a strong candidate for this role
Example Answers
In my previous role at XYZ Corp, I led a project to improve the reliability of our assembly line equipment. We faced issues with frequent breakdowns, which led to downtime. I conducted a root cause analysis and implemented a predictive maintenance schedule. As a result, equipment downtime was reduced by 30%, and I received recognition from management for my efforts.
Give an example of how you communicated technical information to non-technical team members.
How to Answer
- 1
Identify a specific situation where communication was needed.
- 2
Use simple language and avoid jargon when explaining.
- 3
Include how you adjusted your explanation based on the audience's understanding.
- 4
Mention any visual aids or tools you used to enhance understanding.
- 5
Describe the outcome of your communication and any feedback received.
Example Answers
In a team meeting, I explained the results of a reliability test to our marketing team. I used simple terms and avoided technical jargon. By providing a simple side-by-side comparison chart, I illustrated the difference in failure rates, which helped them understand the importance of our findings.
Tell me about a time when you had to adapt to a significant change in a project or work environment. How did you handle it?
How to Answer
- 1
Focus on a specific change you faced in a project or environment.
- 2
Describe your initial reaction to the change honestly.
- 3
Explain the steps you took to adapt and what strategies you used.
- 4
Mention any tools or methods that helped you manage the transition.
- 5
Conclude with the positive outcome and what you learned from the experience.
Example Answers
In my previous role, we shifted to a new maintenance tracking software mid-project. At first, I was frustrated, but I quickly took it upon myself to learn the new system. I attended extra training sessions and helped my team transition by sharing tips and best practices. This not only improved our tracking efficiency but also helped us catch issues sooner, leading to a 20% reduction in downtime over the following months.
Can you describe an instance where you learned a new skill or technology that improved your work performance?
How to Answer
- 1
Choose a specific skill or technology relevant to reliability engineering.
- 2
Explain the situation where you identified the need to learn this skill.
- 3
Describe the steps you took to learn it, including resources used.
- 4
Share measurable outcomes or improvements in your performance after applying the skill.
- 5
Be concise and focus on your personal contribution and achievements.
Example Answers
At my previous job, I realized our team struggled with data analysis for reliability testing. I took an online course in statistical software and applied those skills to analyze test results, which reduced downtime by 15%.
Have you ever suggested an innovative solution to a reliability problem? What was it and what was the outcome?
How to Answer
- 1
Think of a specific example where you identified a reliability issue.
- 2
Describe your innovative solution clearly and concisely.
- 3
Explain the outcome and how it positively impacted the situation.
- 4
Highlight any collaborative efforts or teamwork involved.
- 5
Mention any metrics or data that showcase the success of your solution.
Example Answers
In my previous role, we faced frequent failures in a conveyor system. I suggested implementing a predictive maintenance program using vibration analysis. As a result, we reduced downtime by 30% and extended equipment life by 20%. My team and I worked closely to gather data and analyze trends, which reinforced the success of the program.
Describe a time you received constructive feedback. How did you incorporate it into your work?
How to Answer
- 1
Choose a specific instance where feedback was given.
- 2
Explain the feedback clearly and why it was important.
- 3
Describe how you applied the feedback in your work.
- 4
Mention any positive results that came from this change.
- 5
Keep it focused on your personal growth and learning.
Example Answers
In my previous role, my supervisor pointed out that I needed to improve the accuracy of my reporting. I took this feedback seriously and enrolled in a data analysis workshop. After applying the new techniques I learned, I significantly reduced errors in my reports, which improved our team's project outcomes.
Don't Just Read Reliability Technician Questions - Practice Answering Them!
Reading helps, but actual practice is what gets you hired. Our AI feedback system helps you improve your Reliability Technician interview answers in real-time.
Personalized feedback
Unlimited practice
Used by hundreds of successful candidates
Reliability Technician Position Details
Salary Information
Recommended Job Boards
These job boards are ranked by relevance for this position.
Related Positions
- Radio Technician
- TV Technician
- Television Technician
- Control Engineer
- Broadcast Technician
- Radio Engineer
- Studio Technician
- Station Engineer
- Color Technician
- Television Engineer
Similar positions you might be interested in.
Ace Your Next Interview!
Practice with AI feedback & get hired faster
Personalized feedback
Used by hundreds of successful candidates
Ace Your Next Interview!
Practice with AI feedback & get hired faster
Personalized feedback
Used by hundreds of successful candidates