Top 29 Robotic Weld Technician Interview Questions and Answers [Updated 2025]
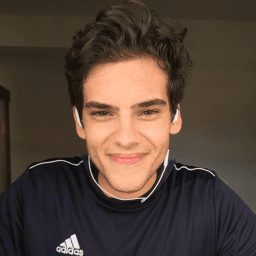
Andre Mendes
•
March 30, 2025
Preparing for an interview as a Robotic Weld Technician can be daunting, but our latest blog post is here to help. We've gathered the most common interview questions for this role, complete with example answers and expert tips to help you respond confidently and effectively. Dive in to enhance your preparation and ace that interview with ease.
Download Robotic Weld Technician Interview Questions in PDF
To make your preparation even more convenient, we've compiled all these top Robotic Weld Technicianinterview questions and answers into a handy PDF.
Click the button below to download the PDF and have easy access to these essential questions anytime, anywhere:
List of Robotic Weld Technician Interview Questions
Behavioral Interview Questions
Can you describe a time when you had to troubleshoot a robotic welding system that was not performing correctly? What steps did you take, and what was the outcome?
How to Answer
- 1
Start with a brief context of the issue encountered with the robotic welding system.
- 2
Describe the specific steps you took to diagnose the problem.
- 3
Include any tools or techniques you used during the troubleshooting process.
- 4
Emphasize the outcome, highlighting any improvements achieved after your intervention.
- 5
Conclude with a lesson learned or how this experience prepared you for future challenges.
Example Answers
In my previous role, our robotic welder started experiencing inconsistent welds. I reviewed the weld parameters and discovered the settings had been altered. I recalibrated the machine and performed test welds. The outcome was improved consistency in weld quality, and production efficiency increased by 15%. This experience taught me the importance of strict adherence to settings and regular system checks.
Tell me about a time you worked with a team to improve a welding process. What was your role, and what was the result?
How to Answer
- 1
Describe the situation clearly and concisely.
- 2
Focus on your specific role and contributions.
- 3
Mention the strategies your team used to improve the process.
- 4
Highlight the measurable results or improvements achieved.
- 5
Include what you learned from the experience.
Example Answers
In my previous job, our team noticed inconsistencies in weld quality. I led a brainstorming session to identify root causes, then we implemented a new welding technique. As a result, our defect rate decreased by 20%, and production efficiency improved significantly. I learned the value of teamwork in overcoming challenges.
Don't Just Read Robotic Weld Technician Questions - Practice Answering Them!
Reading helps, but actual practice is what gets you hired. Our AI feedback system helps you improve your Robotic Weld Technician interview answers in real-time.
Personalized feedback
Unlimited practice
Used by hundreds of successful candidates
Describe an instance where you led a project involving robotic welding. How did you ensure the project was successful?
How to Answer
- 1
Start with a clear project overview, including goals and timeline
- 2
Explain your leadership role and responsibilities in the project
- 3
Highlight specific challenges faced and solutions implemented
- 4
Discuss collaboration with team members or departments
- 5
Conclude with measurable outcomes or lessons learned
Example Answers
In my last position, I led a project to optimize our robotic welding process for automotive parts. I set clear goals for reducing cycle time by 20% and completed it within three months. I coordinated a team of 5 technicians, and we tackled issues like misalignment by adjusting the fixtures. Regular team meetings ensured everyone was aligned. As a result, we reduced our welding time significantly, leading to a 25% increase in production capacity.
How have you adapted to changes in technology or processes in your previous role as a welding technician?
How to Answer
- 1
Start with a specific example of a technology change you faced.
- 2
Explain the steps you took to learn or adapt to the new technology.
- 3
Highlight a positive outcome from your adaptation efforts.
- 4
Mention any training or resources you utilized.
- 5
Emphasize your willingness to learn and improve continuously.
Example Answers
At my last job, we switched to robotic welding systems. I attended a workshop to learn how to program and operate the robots, which helped improve our productivity by 20%.
Give an example of how you have promoted safety in your role. Have you ever suggested changes to improve safety standards?
How to Answer
- 1
Use specific examples from your experience
- 2
Focus on actions you took to promote safety
- 3
Mention any measurable outcomes or results
- 4
Include a suggestion you made to improve safety
- 5
Demonstrate your commitment to a safe work environment
Example Answers
In my previous role, I noticed that our welding area lacked proper signage for safety equipment locations. I suggested we install clear, visible signs which resulted in a 30% decrease in tool-related accidents.
Describe a situation where you had to communicate technical information about welding defects to non-technical staff. How did you ensure they understood?
How to Answer
- 1
Use simple language avoiding technical jargon
- 2
Provide clear examples of defects and their implications
- 3
Use visuals like charts or diagrams to illustrate points
- 4
Ask questions to check for understanding
- 5
Summarize key points at the end of your explanation
Example Answers
In a recent project, I held a meeting with the assembly team to discuss issues with weld defects. I explained the types of defects, such as porosity and cracks, using diagrams to show what they looked like. I asked if they had questions and explained the impact of these defects on the final product's strength. At the end, I summarized the key defects we needed to watch for.
Tell me about a time when you had a conflict with a coworker about a welding procedure. How did you resolve it?
How to Answer
- 1
Start with a clear example of the conflict.
- 2
Describe the perspectives of both you and your coworker.
- 3
Explain the steps you took to address the conflict.
- 4
Highlight what you learned from the experience.
- 5
Conclude with how the resolution improved the work environment or process.
Example Answers
At my previous job, I disagreed with a coworker about the best welding technique for a specific metal. He preferred TIG while I thought MIG was better for that project. We sat down to discuss our reasons and consulted the welding procedure specifications. Ultimately, we agreed to test both methods on a small section and evaluate the results. This approach allowed us to make an informed decision based on data instead of opinion.
Technical Interview Questions
What programming languages or software have you used to program robotic welders? Can you describe your experience with them?
How to Answer
- 1
List the specific programming languages or software you have used.
- 2
Briefly explain how you used each tool in your work.
- 3
Mention any relevant projects or situations where you applied your skills.
- 4
If possible, highlight any certifications or training you have related to these tools.
- 5
Keep your answer concise and focused on your practical experience.
Example Answers
I have used KUKA KRL and FANUC TPP to program robotic welders. In my last role, I programmed KUKA robots for automated welding on automotive components. I led a project that increased production efficiency by 20% through optimizing the welding paths.
Can you explain the differences between MIG, TIG, and spot welding? In what scenarios would you use each method with a robot?
How to Answer
- 1
Define each welding method clearly and concisely.
- 2
Highlight the key characteristics of MIG, TIG, and spot welding.
- 3
Mention specific applications or materials suited for each method.
- 4
Discuss robot capabilities for each welding type.
- 5
Conclude with examples of scenarios for robotic welding.
Example Answers
MIG welding uses a continuous wire feed and is great for thicker materials like steel. It's fast and suitable for robotic applications in automotive manufacturing. TIG welding involves a tungsten electrode and is precise, perfect for aluminum and thin materials, often used in aerospace. Spot welding is used for joining overlaps in sheet metal, commonly found in car body manufacturing with high speed and efficiency.
Don't Just Read Robotic Weld Technician Questions - Practice Answering Them!
Reading helps, but actual practice is what gets you hired. Our AI feedback system helps you improve your Robotic Weld Technician interview answers in real-time.
Personalized feedback
Unlimited practice
Used by hundreds of successful candidates
How do you calibrate a robotic welding system to ensure accuracy and precision in welds?
How to Answer
- 1
Understand the welding parameters including voltage, amperage, and travel speed
- 2
Use calibration tools to check the robot's position accuracy
- 3
Regularly inspect the tooling and fixtures for alignment and wear
- 4
Adjust the welding robot's programming as necessary based on test welds
- 5
Document the calibration process for quality assurance and repeatability
Example Answers
I calibrate the robotic welding system by first ensuring that the welding parameters like voltage and amperage are set to the manufacturer's specifications. Next, I use tools like laser measurement devices to confirm the robot's positioning accuracy. After that, I perform test welds and adjust the programming to refine the weld quality before documenting all settings.
What common issues have you encountered with robotic welding systems, and how do you typically address them?
How to Answer
- 1
Identify specific common issues like misalignment or inconsistent weld quality.
- 2
Explain how you diagnose the issue using tools or software.
- 3
Discuss your approach to fixing the issues, such as recalibration or changing settings.
- 4
Mention any preventative measures you take to avoid future problems.
- 5
Be concise but detailed enough to show your expertise.
Example Answers
I've encountered misalignment of the welding arm that led to inconsistent welds. I typically diagnose it using the system's software to check calibration settings, and if necessary, I recalibrate the robot based on the manufacturer's guidelines. Additionally, I regularly inspect the fixtures to prevent future misalignments.
How do you perform quality checks on welds made by robotic systems? What tools or procedures do you use?
How to Answer
- 1
Discuss the importance of setting quality standards before production
- 2
Mention specific tools like ultrasonic testing and visual inspection cameras
- 3
Explain procedures such as reviewing welding parameters and conducting regular audits
- 4
Highlight the role of software in monitoring welding quality
- 5
Emphasize continuous training for personnel in quality inspection procedures
Example Answers
I perform quality checks by using ultrasonic testing to detect any internal flaws in the welds. I also conduct visual inspections using high-definition cameras to ensure surface quality meets our standards.
What routine maintenance tasks are necessary for robotic welding systems to ensure they operate efficiently?
How to Answer
- 1
Discuss the importance of regular inspections for wear and tear.
- 2
Mention the need for cleaning the welding nozzle and work area frequently.
- 3
Explain the value of checking and calibrating sensors and safety devices.
- 4
Highlight the necessity of updating software and firmware regularly.
- 5
Include the significance of lubricating mechanical parts to prevent rust and ensure smooth operation.
Example Answers
Routine maintenance includes inspecting cables and connections for wear, cleaning the welding nozzle weekly, checking and calibrating sensors, updating software regularly, and lubricating all moving parts every month.
How do you read and interpret welding blueprints and specifications to set up a robotic welder?
How to Answer
- 1
Identify key components such as weld symbols, joint types, and specifications.
- 2
Understand the dimensions and tolerances provided in the blueprint.
- 3
Check for material types and thicknesses to set appropriate welding parameters.
- 4
Refer to any notes or legends that explain unique specifications or requirements.
- 5
Practice using real examples of blueprints to improve interpretation skills.
Example Answers
I start by examining the weld symbols on the blueprint, which tell me the type of weld needed and joint configurations. I then pay careful attention to dimensions and tolerances to ensure correct setups.
How do you decide which robotic welding equipment to use for different materials and thicknesses?
How to Answer
- 1
Assess the material type and its specific welding requirements
- 2
Consider the thickness of the materials for selecting power and speed settings
- 3
Choose a welding process suitable for the material and thickness, such as MIG or TIG
- 4
Evaluate the availability of equipment and its production capabilities
- 5
Ensure to follow industry standards and best practices for safety and quality
Example Answers
I first identify the type of material, such as steel or aluminum, and assess its thickness to determine the most suitable welding process. For instance, I would typically use MIG welding for heavier steel materials, ensuring the power and wire feed speed are adjusted for the thickness.
Situational Interview Questions
Imagine a robot welder starts malfunctioning during a production run, causing defects in the product. How would you handle this situation?
How to Answer
- 1
Identify and confirm the malfunctioning issue quickly.
- 2
Pause production to prevent further defects and assess the situation.
- 3
Follow safety protocols to ensure a safe working environment.
- 4
Troubleshoot the robot using diagnostic tools or refer to manuals.
- 5
Document the incident and the steps taken for future reference.
Example Answers
First, I would quickly check the robot's indicators to identify the issue. Then, I would pause production to prevent further defects. Following safety protocols, I would safely troubleshoot using the diagnostic tools available, and finally document the incident for future improvement.
You've been tasked with improving the efficiency of a robotic welding line. What steps would you take to identify areas for improvement?
How to Answer
- 1
Analyze production data to identify bottlenecks
- 2
Observe and assess the current welding processes
- 3
Review cycle times and downtime records
- 4
Gather feedback from operators and technicians
- 5
Explore opportunities for automation enhancements
Example Answers
I would start by analyzing production data to pinpoint where delays occur. Then, I would observe the welding line in action to see if there are any inefficiencies in the process. By checking cycle times and downtime, I can identify the main bottlenecks, and I would also talk to operators for their insights on potential improvements.
Don't Just Read Robotic Weld Technician Questions - Practice Answering Them!
Reading helps, but actual practice is what gets you hired. Our AI feedback system helps you improve your Robotic Weld Technician interview answers in real-time.
Personalized feedback
Unlimited practice
Used by hundreds of successful candidates
A new robotic welding technology is being introduced. How would you approach integrating this into existing systems?
How to Answer
- 1
Evaluate the current welding systems and identify integration points.
- 2
Train staff on the new technology to ensure smooth operation.
- 3
Conduct pilot tests to assess compatibility and performance.
- 4
Develop a phased rollout plan to minimize downtime.
- 5
Gather feedback and optimize the integration process continuously.
Example Answers
I would start by analyzing our existing welding systems to see where the new technology can fit in. Next, I would organize training sessions for the staff to familiarize them with the new equipment. After that, I'd initiate a pilot test to see how well it integrates and performs. Following that, I would implement a phased rollout to limit disruptions and gather feedback to make any necessary adjustments.
You need to train a new technician on operating the robotic welders. What is your approach to ensure they are proficient?
How to Answer
- 1
Start with a structured training plan that covers basic concepts and safety protocols.
- 2
Demonstrate hands-on training by operating the robotic welder for them.
- 3
Encourage questions during training to clarify any doubts immediately.
- 4
Provide supervised practice sessions where the trainee operates the welder while you observe and assist.
- 5
Evaluate their performance with practical tests and provide constructive feedback.
Example Answers
I would develop a detailed training plan that includes both theory and hands-on practice. I'll demonstrate the welder's operations and then let the technician practice under my supervision, encouraging them to ask questions at any time.
A robotic welder is producing inconsistent welds. Describe your process for diagnosing and resolving the issue.
How to Answer
- 1
Check the robot's programming for errors or misalignments.
- 2
Inspect the welding equipment for wear or malfunction.
- 3
Analyze the materials being used for compatibility and quality.
- 4
Review the environmental conditions affecting the weld process.
- 5
Test and calibrate the robotic settings to optimize performance.
Example Answers
First, I would check the robot's programming to ensure there are no errors in the weld path. Next, I would inspect the equipment, looking for any worn components that might affect the weld consistency. Finally, I would analyze the materials to confirm they are compatible and of high quality.
You're given a limited budget to upgrade the welding department. How would you prioritize spending to maximize efficiency?
How to Answer
- 1
Evaluate current equipment and identify the most outdated or inefficient.
- 2
Consider investing in training for staff to improve skills and productivity.
- 3
Implement technology upgrades that provide the best return on investment.
- 4
Focus on safety enhancements to reduce workplace accidents and downtime.
- 5
Gather feedback from operators on tools and processes that can be improved.
Example Answers
I would first assess the current equipment in the welding department to identify the oldest and least efficient machines that are costing us time. Then I would allocate funds to purchase a high-efficiency welding robot that can handle repetitive tasks faster. Additionally, I would set aside some budget for training our technicians on this robot, ensuring they can operate it effectively.
A client has increased an order requiring a quicker turnaround. How would you adjust the robotic welding schedule to meet the new deadline?
How to Answer
- 1
Assess current production capacity and identify bottlenecks
- 2
Prioritize the new order in the schedule
- 3
Consider adding shifts or overtime to increase output
- 4
Optimize robotic settings for speed without compromising quality
- 5
Communicate changes to the team for seamless execution
Example Answers
I would first check our current output rate and identify any bottlenecks in our process. Then, I would prioritize the new order by reallocating resources and perhaps adjust the programming of the robot for faster cycle times. If necessary, I would suggest adding overtime shifts to ensure we meet the deadline.
You need to collaborate with the design department to resolve a welding issue. How would you approach this situation?
How to Answer
- 1
Start with identifying the specific welding issue and its impact on production.
- 2
Schedule a meeting with relevant design team members to discuss the issue.
- 3
Prepare data or examples to clearly communicate the welding problem.
- 4
Be open to feedback and suggestions from the design team.
- 5
Aim for a collaborative solution that addresses both welding and design requirements.
Example Answers
To resolve the welding issue, I would first gather details about the problem and its production effect. Then, I would set up a meeting with the design team, bringing relevant data to discuss our findings. I'm open to their insights, aiming for a solution that works for everyone.
Due to a power outage, the robotic welders were down. What actions would you take to quickly resume operations once power is restored?
How to Answer
- 1
Check for any error messages on the robotic welders after power is restored.
- 2
Conduct a safety inspection to ensure all systems are operational and safe to restart.
- 3
Restart the welding program or software once systems are checked.
- 4
Perform a test weld to ensure everything is functioning correctly.
- 5
Notify the team about the status and any adjustments needed in the production schedule.
Example Answers
First, I would check the robotic welders for any error messages after the power is restored. Then, I would carry out a safety inspection to ensure everything is safe to operate. Once confirmed, I would restart the welding program and run a test weld before resuming normal production.
Management wants to reduce costs in the robotic welding operation. What suggestions would you make without sacrificing quality?
How to Answer
- 1
Analyze the current welding cycle times for efficiency improvements.
- 2
Implement preventive maintenance schedules to avoid costly breakdowns.
- 3
Seek out bulk material purchasing options to reduce raw material costs.
- 4
Train staff on best practices to minimize waste and rework.
- 5
Review and optimize the programming of robotic weld paths to enhance performance.
Example Answers
I would first analyze the welding cycle times to identify areas where we can reduce them without affecting quality. This could improve throughput and lower operational costs.
Don't Just Read Robotic Weld Technician Questions - Practice Answering Them!
Reading helps, but actual practice is what gets you hired. Our AI feedback system helps you improve your Robotic Weld Technician interview answers in real-time.
Personalized feedback
Unlimited practice
Used by hundreds of successful candidates
You've noticed a decline in weld quality. What steps would you take to investigate and rectify this issue?
How to Answer
- 1
Conduct a thorough inspection of the welds to identify specific defects.
- 2
Review the welding parameters and settings to ensure they are within the correct ranges.
- 3
Check the condition and calibration of welding equipment and sensors.
- 4
Analyze recent changes in materials or consumables used for welding.
- 5
Engage with the welders to gather feedback on any difficulties they might be experiencing.
Example Answers
First, I would inspect the welds to pinpoint the exact issues, such as porosity or warping. Then, I would review the welding parameters like voltage and amperage to ensure they meet specifications. Next, I would check if the welding equipment is properly calibrated and functioning. I would also consider any recent material changes, and finally, I would talk to the welders to understand their challenges.
How would you redesign the workflow of a robotic welding line to increase throughput without compromising quality?
How to Answer
- 1
Analyze current workflow bottlenecks to identify inefficiencies
- 2
Implement parallel processing where feasible to reduce cycle time
- 3
Ensure that the robotic cells are properly synchronized to avoid delays
- 4
Utilize data analytics to monitor performance and make informed adjustments
- 5
Train staff on best practices to maintain quality while increasing speed
Example Answers
I would first map the entire workflow and identify bottlenecks, then introduce parallel processing in non-critical areas. This would allow multiple welds to occur simultaneously, increasing throughput without losing focus on quality checks between each process.
A new regulation impacts the materials you can use in your welding process. How do you ensure your operations remain compliant?
How to Answer
- 1
Stay updated on welding regulations through industry newsletters and government websites
- 2
Implement a material review process to evaluate compliance with new regulations
- 3
Conduct regular training sessions for the team on compliance standards
- 4
Establish relationships with suppliers to ensure they provide compliant materials
- 5
Document compliance efforts and review them periodically for effectiveness
Example Answers
I keep track of new regulations by subscribing to industry updates and newsletters. I also have a material review process in place that lets me check the compliance of all materials we use.
Suggest a new technique or technology that could be implemented to improve the robotic welding process. How would you justify its adoption?
How to Answer
- 1
Research recent trends in welding technology for current techniques.
- 2
Consider the impacts on efficiency, cost, and quality improvements.
- 3
Think about automation and data analysis for monitoring and feedback.
- 4
Be prepared to discuss implementation steps and training requirements.
- 5
Address potential challenges to adopting the new technology.
Example Answers
One technique that could improve robotic welding is the use of machine learning algorithms for real-time quality monitoring. This technology would help identify defects as they occur, ensuring higher quality welds and reducing rework costs. Implementation would involve integrating sensors and training staff on the new system.
Robotic Weld Technician Position Details
Recommended Job Boards
CareerBuilder
www.careerbuilder.com/jobs/robotic-weld-technicianThese job boards are ranked by relevance for this position.
Related Positions
Ace Your Next Interview!
Practice with AI feedback & get hired faster
Personalized feedback
Used by hundreds of successful candidates
Ace Your Next Interview!
Practice with AI feedback & get hired faster
Personalized feedback
Used by hundreds of successful candidates