Top 30 Saw Repairer Interview Questions and Answers [Updated 2025]
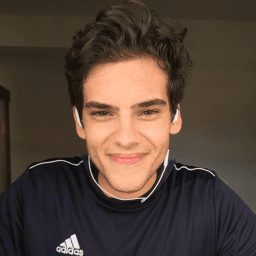
Andre Mendes
•
March 30, 2025
Are you preparing for a saw repairer job interview and feeling unsure about what to expect? This blog post is your go-to resource, offering a comprehensive collection of the most common interview questions for the saw repairer role. Dive in to discover example answers and insightful tips that will help you respond with confidence and make a lasting impression on your potential employer.
Download Saw Repairer Interview Questions in PDF
To make your preparation even more convenient, we've compiled all these top Saw Repairerinterview questions and answers into a handy PDF.
Click the button below to download the PDF and have easy access to these essential questions anytime, anywhere:
List of Saw Repairer Interview Questions
Behavioral Interview Questions
Describe how you ensure safety measures are followed while repairing saws.
How to Answer
- 1
Always wear personal protective equipment like gloves and goggles.
- 2
Inspect tools and machinery for defects before starting repairs.
- 3
Follow the manufacturer's guidelines for safety and operation.
- 4
Work in a clean and organized space to prevent accidents.
- 5
Keep safety equipment, such as fire extinguishers, accessible.
Example Answers
I ensure safety measures by always wearing my gloves and goggles during repairs, and I inspect the saw for any defects before I start. I strictly follow the manufacturer's guidelines and maintain a clean workspace to avoid any hazards.
Can you describe a time when you faced a challenging repair on a saw and how you resolved it?
How to Answer
- 1
Start with a specific example of a saw repair.
- 2
Explain why it was challenging and what made it difficult.
- 3
Detail the steps you took to diagnose the issue.
- 4
Describe the solution you implemented and how it resolved the problem.
- 5
Conclude with what you learned from the experience.
Example Answers
I once worked on a table saw that would not start. The challenge was diagnosing whether it was an electrical issue or a safety switch malfunction. I checked the wiring and found a loose connection. I repaired it and the saw worked perfectly afterward. I learned to double-check connections first in future repairs.
Don't Just Read Saw Repairer Questions - Practice Answering Them!
Reading helps, but actual practice is what gets you hired. Our AI feedback system helps you improve your Saw Repairer interview answers in real-time.
Personalized feedback
Unlimited practice
Used by hundreds of successful candidates
Tell me about a situation where you had to collaborate with a colleague to repair a saw.
How to Answer
- 1
Choose a specific incident where teamwork was key.
- 2
Describe your colleague's role and your role in the repair.
- 3
Explain the challenge faced and how you worked together to overcome it.
- 4
Highlight the outcome of the repair and the importance of collaboration.
- 5
Keep it concise and focused on your contributions.
Example Answers
In my previous job, I worked with a colleague to repair a band saw that was consistently jamming. I focused on adjusting the blade tension while my colleague inspected the alignment. We communicated constantly to ensure both adjustments were in sync. As a result, we successfully fixed the saw, reducing downtime by 30%.
Give an example of when you missed a minor issue during a repair that led to a bigger problem.
How to Answer
- 1
Choose a specific instance from your experience.
- 2
Explain the minor issue you overlooked clearly.
- 3
Describe how this issue escalated into a larger problem.
- 4
Focus on what you learned from this experience.
- 5
Emphasize steps you take now to avoid similar issues.
Example Answers
During a routine blade sharpening, I missed a small chip on the edge of the saw. This led to uneven cutting during use and caused additional wear on the equipment. I learned to always double-check the blade for any imperfections before completing the job.
How do you prioritize multiple saw repairs when you have tight deadlines?
How to Answer
- 1
Assess the urgency of each repair based on deadlines and customer needs
- 2
Identify which repairs are quickest to complete for immediate impact
- 3
Group similar repairs to maximize efficiency and reduce setup time
- 4
Communicate with your team about priorities to ensure everyone is aligned
- 5
Keep customers informed about progress and estimated completion times
Example Answers
I start by listing all the repairs and assessing their urgency based on set deadlines. Then, I tackle the quicker repairs first to clear the backlog and create a flow. Lastly, I communicate with my team to ensure we're all focused on the most critical tasks.
How have you handled a situation where a customer was dissatisfied with a saw repair?
How to Answer
- 1
Listen carefully to the customer's concerns and acknowledge their feelings
- 2
Apologize for any inconvenience caused, regardless of fault
- 3
Assess the situation and clarify the issue with the saw repair
- 4
Offer a solution, such as re-evaluation, additional repairs, or a refund
- 5
Follow up after resolving the issue to ensure customer satisfaction
Example Answers
I listened to the customer's concerns about the saw performance and acknowledged their frustration. I apologized for any inconvenience and carefully assessed the issue. I found a misalignment and fixed it at no extra charge. The customer was happy with the resolution.
Have you ever introduced a new method or tool that improved the efficiency of saw repairs?
How to Answer
- 1
Identify a specific method or tool you proposed or implemented.
- 2
Explain the reason for the change and what problem it addressed.
- 3
Share measurable results or improvements that came from the change.
- 4
Mention any feedback from team members or customers that highlights the success.
- 5
Keep your answer focused on your role and contribution.
Example Answers
In my previous job, I introduced a new type of diamond sharpening wheel that cut down the time required for saw blade sharpening by 30%. This was because it provided a finer edge much faster than our old tools.
Describe a time when you had to train someone on how to repair saws. What challenges did you face?
How to Answer
- 1
Focus on a specific training experience you had.
- 2
Mention the training methods you used and why.
- 3
Discuss specific challenges like skill level or equipment issues.
- 4
Explain how you overcame those challenges.
- 5
Highlight the positive outcome of your training.
Example Answers
I trained a new employee on saw repair using hands-on demonstration and step-by-step guidance. The challenge was their lack of experience with tools, so I simplified the process and provided additional practice time. In the end, they became proficient in basic repairs, which improved our team's efficiency.
Tell me about a time when you had to adapt to new technology or techniques in saw repair.
How to Answer
- 1
Identify a specific instance where you faced new technology in saw repair.
- 2
Explain the new technology or technique clearly.
- 3
Describe your initial challenges and how you overcame them.
- 4
Highlight any training or resources you used to adapt.
- 5
Conclude with the positive outcome of your adaptation.
Example Answers
In my previous job, we were introduced to a CNC saw sharpening machine. At first, I struggled with the software interface, but I took a weekend course to learn it. I practiced on the machine during my breaks and soon became one of the top users, increasing our shop's efficiency by 30%.
Can you describe a time you received constructive feedback on your repair work and how you implemented it?
How to Answer
- 1
Think of a specific instance when you received feedback while repairing a saw.
- 2
Explain what the feedback was and who provided it.
- 3
Describe how you adjusted your methods or techniques based on the feedback.
- 4
Mention any positive outcomes or improvements that resulted from implementing the feedback.
- 5
Keep your response focused on the learning experience and how it made you a better repairer.
Example Answers
In my previous role, I worked on a chainsaw and my supervisor pointed out that my alignment wasn't precise. I took their advice to slow down and double-check the blade alignment before securing it. This change improved my repair time and the precision of my work significantly.
Don't Just Read Saw Repairer Questions - Practice Answering Them!
Reading helps, but actual practice is what gets you hired. Our AI feedback system helps you improve your Saw Repairer interview answers in real-time.
Personalized feedback
Unlimited practice
Used by hundreds of successful candidates
Technical Interview Questions
What are the main differences between reconditioning and repairing various types of saws?
How to Answer
- 1
Define reconditioning and repairing to show understanding.
- 2
Discuss when each method is appropriate based on the saw's condition.
- 3
Mention specific types of saws and how the methods apply to them.
- 4
Highlight the impact of reconditioning on performance versus simple repairs.
- 5
Provide examples of what might be done in each process.
Example Answers
Reconditioning involves overhauling the saw, replacing worn-out parts for improved performance, while repairing is fixing specific issues like blade sharpening. For instance, reconditioning a circular saw might include changing the motor, whereas a repair could just be blade replacement.
Which tools are essential for the repair of different types of saws and why?
How to Answer
- 1
List specific tools for each type of saw.
- 2
Explain the purpose of each tool in the repair process.
- 3
Use examples of saw types to illustrate your points.
- 4
Highlight any advanced tools if applicable.
- 5
Keep the answer organized and concise.
Example Answers
For circular saws, essential tools include a wrench for blade removal, a screwdriver for adjusting screws, and a multimeter for testing electrical components. Each tool plays a crucial role in ensuring the saw functions properly after repairs.
Don't Just Read Saw Repairer Questions - Practice Answering Them!
Reading helps, but actual practice is what gets you hired. Our AI feedback system helps you improve your Saw Repairer interview answers in real-time.
Personalized feedback
Unlimited practice
Used by hundreds of successful candidates
Explain the routine maintenance procedures you perform on saws before repairs.
How to Answer
- 1
Start with safety precautions, like wearing gloves and goggles.
- 2
Inspect the blade for wear, damage, or dullness.
- 3
Check all safety features and ensure they are functioning correctly.
- 4
Clean the saw thoroughly to remove dust and debris.
- 5
Lubricate moving parts as per the manufacturer's recommendations.
Example Answers
First, I always put on safety gloves and goggles. Then, I inspect the saw blade for any signs of damage or dullness. I also check that all safety features, like guards and triggers, are working. After that, I clean the saw to remove any dust, and finally, I lubricate the moving parts to keep them in good condition.
How do you diagnose issues in a saw that is not functioning properly?
How to Answer
- 1
Start by inspecting the saw for any visible damage or loose parts.
- 2
Check the power source or battery to ensure it is properly charged.
- 3
Listen for unusual sounds that may indicate motor issues or binding.
- 4
Test the blade for sharpness and secure attachment to the saw.
- 5
Run through the manufacturer's troubleshooting guide if available.
Example Answers
I begin my diagnosis by visually inspecting the saw for any obvious damage. Then, I check the power source to ensure it's functioning. If the saw makes odd noises, I investigate the motor and any binding issues. Finally, I look at the blade to see if it’s dull or not attached correctly.
What specific techniques do you use to sharpen saw blades?
How to Answer
- 1
Mention the type of saw blades you're experienced with
- 2
Describe the sharpening tools you use, like files or grinders
- 3
Explain the process you follow step-by-step
- 4
Highlight any maintenance tips for prolonging blade life
- 5
Share any specific adjustments you make for different types of cuts
Example Answers
I specialize in sharpening both hand saws and power saw blades. I typically use a combination of triangular files for hand saws and bench grinders for circular blades. My process starts with cleaning the blade, followed by filing each tooth to restore its angle, ensuring consistent sharpness throughout. I also recommend oiling the blade after sharpening to prevent rust.
How do you identify the correct replacement parts needed for different saw models?
How to Answer
- 1
Refer to the manufacturer's manual for each saw model to find part numbers.
- 2
Use online databases or parts lookup tools specific to saw brands.
- 3
Check the existing part for its label or number for direct replacement.
- 4
Consult with colleagues or specialists who have experience with various saws.
- 5
Stay updated with industry trends and common part issues for different models.
Example Answers
I begin by checking the manufacturer's manual for the specific saw model, which lists all compatible parts. If I can't find it there, I use online tools that match parts to models to ensure accuracy.
What safety standards must be considered while repairing saws?
How to Answer
- 1
Discuss the importance of personal protective equipment such as gloves, goggles, and ear protection.
- 2
Mention the need for machine lockout/tagout procedures to prevent accidental start-up.
- 3
Highlight the importance of checking for electrical safety when working with power saws.
- 4
Explain the need to ensure a clean work area to prevent accidents and provide proper ventilation if needed.
- 5
Address the necessity of following manufacturer guidelines and safety standards to maintain compliance.
Example Answers
When repairing saws, I always ensure to wear appropriate personal protective equipment like gloves and goggles. I also follow lockout/tagout procedures to make sure the machine is powered down before I begin any repairs.
What testing processes do you follow to ensure a saw is fully operational after repair?
How to Answer
- 1
Begin by explaining initial visual inspections for obvious damage.
- 2
Describe testing for mechanical functionality, such as blade movement.
- 3
Mention electrical checks if applicable, like power and safety features.
- 4
Talk about performance tests like cutting through materials.
- 5
Conclude with the importance of safety checks before final approval.
Example Answers
I start with a visual inspection to check for any physical damage. Next, I test the blade movement to ensure it's operating smoothly. If it's an electric saw, I check the power and ensure all safety features are functional. I then perform a cutting test to verify it cuts properly through material. Finally, I conduct a thorough safety check before approving it for use.
What specific challenges do you face when repairing electrical saws compared to manual saws?
How to Answer
- 1
Identify the complexities of electrical systems in saws.
- 2
Discuss safety concerns related to working with electrical components.
- 3
Mention the need for specialized tools and equipment for electrical saws.
- 4
Highlight the importance of understanding electronics and wiring diagrams.
- 5
Explain how the repair process differs in terms of time and troubleshooting.
Example Answers
Repairing electrical saws presents challenges like understanding their complex electrical systems, which require specialized knowledge of electronics and wiring diagrams.
Why is lubrication important in saw maintenance, and what types of lubricants do you use?
How to Answer
- 1
Explain the role of lubrication in reducing friction and wear.
- 2
Mention how lubrication helps in prolonging the life of the saw.
- 3
Discuss the types of lubricants appropriate for saw maintenance.
- 4
Provide examples of specific lubricants you have used.
- 5
Highlight safety and efficiency improvements with proper lubrication.
Example Answers
Lubrication is crucial because it minimizes friction and wear, which helps extend the life of the saw. I typically use oil-based lubricants for the moving parts, and I occasionally apply silicone spray on blades to enhance performance.
Don't Just Read Saw Repairer Questions - Practice Answering Them!
Reading helps, but actual practice is what gets you hired. Our AI feedback system helps you improve your Saw Repairer interview answers in real-time.
Personalized feedback
Unlimited practice
Used by hundreds of successful candidates
How do you determine the best blade type for different materials when repairing saws?
How to Answer
- 1
Identify the type of material you are cutting, such as wood, metal, or plastic.
- 2
Understand the hardness and density of the material to choose the right blade tooth geometry.
- 3
Check the recommended blade specifications for the saw model and material compatibility.
- 4
Consider the cutting speed and application, whether it's for fine cuts or rough cuts.
- 5
Consult manufacturer guidelines or industry standards for specific materials.
Example Answers
To determine the best blade type, I first identify the material. For example, hardwood requires a finer tooth blade for clean cuts, while softwood may work with a more aggressive tooth pattern.
Situational Interview Questions
If a customer brings in a saw with an intermittent problem, how would you approach diagnosing the issue?
How to Answer
- 1
Ask the customer detailed questions about the problem occurrence.
- 2
Inspect the saw for obvious signs of damage or wear.
- 3
Test the saw under different conditions to replicate the issue.
- 4
Check the electrical components and connections for faults.
- 5
Use systematic troubleshooting to isolate the fault.
Example Answers
I would start by asking the customer when the problem occurs and under what conditions it happens. Then, I'd visually inspect the saw for any physical damage and test it while simulating those conditions.
Imagine you receive a request for an urgent repair on a saw that is critical for a customer's operations. How would you handle it?
How to Answer
- 1
Acknowledge the urgency and show you understand its importance.
- 2
Assess the situation and gather necessary details from the customer.
- 3
Prioritize the repair by scheduling it as soon as possible.
- 4
Communicate clearly with the customer about what to expect.
- 5
Follow up after the repair to ensure the customer's satisfaction.
Example Answers
I would first reassure the customer that I understand the urgency of the repair. I would ask specific questions to gather details about the problem and then prioritize the repair in my schedule, aiming to fix it at the earliest possible time. Following the repair, I’d check back to ensure everything is working well.
Don't Just Read Saw Repairer Questions - Practice Answering Them!
Reading helps, but actual practice is what gets you hired. Our AI feedback system helps you improve your Saw Repairer interview answers in real-time.
Personalized feedback
Unlimited practice
Used by hundreds of successful candidates
You disagree with a colleague on the best approach to repair a saw. How would you resolve this situation?
How to Answer
- 1
Listen carefully to your colleague's viewpoint to understand their reasoning.
- 2
Present your own perspective clearly and back it up with relevant experience or data.
- 3
Seek common ground and explore a compromise that incorporates both ideas.
- 4
Propose a trial approach or test case to evaluate both methods practically.
- 5
Remain respectful and professional to maintain a positive working relationship.
Example Answers
I would first listen to my colleague's reasoning to fully understand their approach. Then, I would share my own method, citing any relevant experiences I've had. If there's room, I would suggest we combine our ideas or even run a test to see which method yields better results.
You have multiple saws requiring repairs at the same time with limited staff. How do you manage the workload?
How to Answer
- 1
Prioritize repairs based on severity and impact on operations.
- 2
Assign specific tasks to each staff member based on their skills.
- 3
Implement a time management plan to maximize efficiency.
- 4
Communicate regularly with the team to ensure everyone is aligned.
- 5
Take notes on any ongoing issues for future reference and faster diagnosis.
Example Answers
I would start by assessing the condition of each saw and prioritize the repairs that affect operations the most. I would then assign specific tasks to each technician based on their expertise. We would check in regularly to manage progress and ensure tasks are completed efficiently.
If a newly repaired saw breaks shortly after repair, what steps do you take to address the issue?
How to Answer
- 1
Identify the failure point by inspecting the saw thoroughly.
- 2
Contact the customer immediately to inform them of the situation.
- 3
Determine if the issue was due to a repair error or a user-related problem.
- 4
Offer a remedy, such as a follow-up repair or replacement if necessary.
- 5
Document the incident for quality control and future reference.
Example Answers
First, I would inspect the saw to identify where it failed. Then, I would contact the customer to let them know about the issue and discuss next steps. Depending on the cause, I would either fix it at no charge or offer a replacement if it was a significant fault.
If a customer asks for a low-cost repair for a heavily worn saw, how would you respond?
How to Answer
- 1
Acknowledge the customer's request for a low-cost option
- 2
Explain the risks of repairing a heavily worn saw cheaply
- 3
Offer a transparent explanation of repair costs versus quality
- 4
Suggest alternative solutions, such as maintenance or upgrades
- 5
Emphasize the importance of safety and reliability in repairs
Example Answers
I appreciate your request for a low-cost repair. However, a heavily worn saw may require more extensive work to ensure safety and performance. I'd recommend investing in a proper repair to avoid future issues, but I can provide you with a detailed estimate so you can see the costs involved.
You find that a common issue with saws is more complex than anticipated during repairs. What do you do?
How to Answer
- 1
Remain calm and assess the situation step by step.
- 2
Use diagnostic tools to identify the root cause of the problem.
- 3
Consult technical manuals and repair guides for complex issues.
- 4
Collaborate with colleagues or seek advice from more experienced repairers.
- 5
Document the process and results, including any learning points for future reference.
Example Answers
When I encounter a complex issue, I first take a breath and calmly assess the situation. I then use diagnostic tools to try and pinpoint the root cause and consult the technical manual for further guidance. If needed, I discuss the issue with a colleague who might have experience with similar problems.
If you notice a pattern of defects in repairs, what steps would you take to improve quality?
How to Answer
- 1
Identify and document the specific defects observed.
- 2
Analyze the root cause of the defects through inspection of processes and materials.
- 3
Consult with team members to gather insights and suggestions.
- 4
Implement necessary adjustments to repair techniques or equipment calibration.
- 5
Monitor the results of changes and continue to adjust as needed.
Example Answers
First, I would document the defects I've noticed in detail to understand the scope. Then, I would analyze our current repair processes to find potential causes. Afterward, I would discuss my findings with the team to get their input. Once we agree on needed changes, I would implement them and monitor for improvements.
You have limited parts available for a common repair. How would you manage customer expectations?
How to Answer
- 1
Communicate promptly with the customer about the situation.
- 2
Explain the specific parts that are unavailable and potential impact on the repair.
- 3
Provide alternatives or possible solutions to the customer.
- 4
Set a realistic timeline for when the repair can be completed.
- 5
Follow up with the customer regularly to keep them informed.
Example Answers
I would first inform the customer about the parts that are currently unavailable and explain how it affects the repair timeline. I would then offer to order the necessary parts and give them an estimated time for delivery and repair completion, ensuring to keep them updated throughout the process.
Saw Repairer Position Details
Recommended Job Boards
CareerBuilder
www.careerbuilder.com/jobs-saw-repairerZipRecruiter
www.ziprecruiter.com/Jobs/Saw-RepairerThese job boards are ranked by relevance for this position.
Related Positions
- Electric Motor Repairer
- Lathe Mechanic
- Motor Mechanic
- Transformer Mechanic
- Tool Technician
- Generator Repairer
- Electric Motor Mechanic
- Battery Mechanic
- Battery Repairer
- Motor Rebuilder
Similar positions you might be interested in.
Ace Your Next Interview!
Practice with AI feedback & get hired faster
Personalized feedback
Used by hundreds of successful candidates
Ace Your Next Interview!
Practice with AI feedback & get hired faster
Personalized feedback
Used by hundreds of successful candidates