Top 30 Sign Fabricator Interview Questions and Answers [Updated 2025]
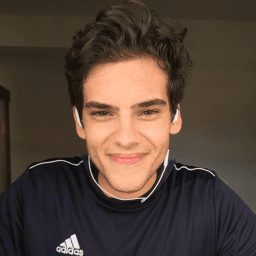
Andre Mendes
•
March 30, 2025
Preparing for a sign fabricator interview can be daunting, but our comprehensive guide is here to help. Dive into the most common interview questions for this unique role, complete with example answers and insightful tips to craft your own responses effectively. Whether you're a seasoned professional or a newcomer to the field, this post will equip you with the knowledge and confidence to impress your potential employers.
Download Sign Fabricator Interview Questions in PDF
To make your preparation even more convenient, we've compiled all these top Sign Fabricatorinterview questions and answers into a handy PDF.
Click the button below to download the PDF and have easy access to these essential questions anytime, anywhere:
List of Sign Fabricator Interview Questions
Behavioral Interview Questions
Can you describe a time when your attention to detail saved a project from potential failure?
How to Answer
- 1
Choose a specific project where detail was crucial.
- 2
Describe the specific detail you noticed and acted on.
- 3
Explain the potential consequences if you hadn't caught that detail.
- 4
Highlight the positive outcome due to your attention to detail.
- 5
Keep your answer concise and focused on your role.
Example Answers
In a recent project for a large sign installation, I noticed that the layout measurements were incorrect. I double-checked the dimensions and identified a mistake in the design file. If I hadn't caught it, the signs would not have fit the allocated space, causing delays and extra costs. After correcting it, we finished on time and received great feedback from the client.
Give an example of a time you introduced a new technique or idea in sign fabrication that improved efficiency or quality.
How to Answer
- 1
Focus on a specific technique you introduced.
- 2
Quantify the improvement in efficiency or quality if possible.
- 3
Describe the challenge you faced before the technique was introduced.
- 4
Mention the reaction of your team or management.
- 5
Conclude with the long-term benefits observed.
Example Answers
At my previous job, I introduced a laser cutting technique for intricate designs. This method reduced our cutting time by 30% and improved the accuracy of the cuts. My team was initially skeptical, but after a demonstration, they quickly adopted it. As a result, we completed projects faster and our quality issues decreased significantly.
Don't Just Read Sign Fabricator Questions - Practice Answering Them!
Reading helps, but actual practice is what gets you hired. Our AI feedback system helps you improve your Sign Fabricator interview answers in real-time.
Personalized feedback
Unlimited practice
Used by hundreds of successful candidates
How do you prioritize tasks when working on multiple sign fabrication projects simultaneously?
How to Answer
- 1
List all projects and their deadlines to get an overview.
- 2
Assess the complexity and time required for each task.
- 3
Communicate with your team about project priorities.
- 4
Use a scheduling tool to organize tasks by priority level.
- 5
Be flexible and ready to adjust priorities based on project needs.
Example Answers
I start by listing all my current projects and their deadlines. Then, I evaluate how much time and resources each task will take. I keep my team updated about our project priorities to ensure everyone is on the same page.
How do you stay updated with the latest trends and technologies in sign fabrication?
How to Answer
- 1
Follow industry-specific blogs and websites related to sign making.
- 2
Join professional organizations for sign manufacturers to network and share insights.
- 3
Attend trade shows and conventions focused on signage and graphics.
- 4
Participate in online forums and social media groups dedicated to sign fabrication.
- 5
Take online courses or webinars on new sign-making technologies and techniques.
Example Answers
I regularly read blogs like SignWeb and follow industry leaders on social media to keep current with trends.
Describe a time when you disagreed with a colleague about the best approach to a project. How did you resolve the disagreement?
How to Answer
- 1
Choose a relevant project experience from your past.
- 2
Explain the specific disagreement you had regarding the project.
- 3
Detail the steps you took to communicate and resolve the issue.
- 4
Highlight any compromises or solutions you reached.
- 5
Reflect on what you learned from the experience for future collaboration.
Example Answers
In a recent project, my colleague wanted to use a certain material for a sign that I felt was not durable enough. I explained my concerns and suggested a different material based on our previous successes. We decided to test both materials on a smaller scale, and the results showed my choice was the better option. This taught us the value of experimentation in decision-making.
Have you ever led a team or coordinated a project in sign fabrication? How did you ensure the project stayed on track?
How to Answer
- 1
Start with a specific project example where you led a team.
- 2
Describe your role and responsibilities clearly.
- 3
Highlight the tools or methods you used to track progress.
- 4
Mention how you communicated with your team and stakeholders.
- 5
Discuss any challenges faced and how you overcame them.
Example Answers
In my previous role, I led a team to fabricate a series of outdoor signs for a mall. I set up weekly meetings to monitor progress and used project tracking software to ensure we stayed on budget and on schedule. I communicated any delays promptly to stakeholders and adjusted our workload accordingly, ultimately completing the project ahead of schedule.
Tell me about a time when you had to adapt to a new technology or process in sign fabrication. How did you manage the transition?
How to Answer
- 1
Identify a specific technology or process change you faced.
- 2
Describe the impact of the change on your work.
- 3
Explain the steps you took to learn the new technology.
- 4
Highlight any support you received from colleagues or supervisors.
- 5
Conclude with the positive results of your adaptation.
Example Answers
In my previous job, we switched to a new CNC router. I first spent time reading the manual and watching training videos. I also asked a senior fabricator for tips, which helped. After a week, I was comfortable and even improved our production efficiency by 20%.
Describe a situation where you had to collaborate with a graphic designer to complete a sign project. How did you ensure the project was successful?
How to Answer
- 1
Choose a specific project that involved a graphic designer.
- 2
Describe your role and contributions to the project.
- 3
Explain how you communicated with the designer to align on ideas.
- 4
Mention any challenges faced and how you overcame them together.
- 5
Highlight the final outcome and feedback received.
Example Answers
In a recent project, I collaborated with a graphic designer to create a large outdoor sign. I communicated closely with them to understand their vision and provided input on what materials would work best. We faced a challenge with color matching, but we resolved it by testing samples together. The sign turned out great, and the client was very pleased with its visibility.
Tell me about a time when you faced a significant challenge during a sign fabrication project. How did you overcome it?
How to Answer
- 1
Identify a specific challenge related to sign fabrication.
- 2
Explain the impact of the challenge on the project.
- 3
Describe the steps you took to address the challenge.
- 4
Highlight any tools or techniques you used to solve the problem.
- 5
Conclude with the outcome and what you learned from the experience.
Example Answers
During a project for a local restaurant, we received the wrong materials which delayed the fabrication. I quickly contacted the suppliers to expedite the correct materials and coordinated with the production team to rearrange the schedule. We managed to complete the project on time, and the restaurant owner was very satisfied.
Describe a situation where you went above and beyond to meet a client's expectations for a sign fabrication project.
How to Answer
- 1
Choose a specific project where you faced challenges.
- 2
Highlight the actions you took to exceed expectations.
- 3
Focus on the impact of your efforts on the client.
- 4
Use quantifiable results if possible.
- 5
Emphasize any feedback or appreciation received from the client.
Example Answers
I worked on a large outdoor sign for a local restaurant that needed to be installed in less than a week. I personally stayed late to ensure the design met the client's vision, and I sourced special materials to elevate the sign's look. As a result, the restaurant opened on schedule and they received rave reviews.
Don't Just Read Sign Fabricator Questions - Practice Answering Them!
Reading helps, but actual practice is what gets you hired. Our AI feedback system helps you improve your Sign Fabricator interview answers in real-time.
Personalized feedback
Unlimited practice
Used by hundreds of successful candidates
Technical Interview Questions
What materials do you typically work with when fabricating signs, and how do you choose the appropriate material for a project?
How to Answer
- 1
Discuss common materials like metal, wood, acrylic, and vinyl.
- 2
Explain how the project use (indoor/outdoor) influences material choice.
- 3
Mention the importance of durability and weather resistance for outdoor signs.
- 4
Highlight aesthetic considerations and branding requirements.
- 5
Consider the budget and cost-effectiveness of materials for the project.
Example Answers
I typically work with materials such as acrylic for indoor signs, vinyl for short-term projects, and aluminum for outdoor displays. For each project, I assess whether it will be indoors or outdoors and choose materials that will withstand environmental factors. For example, if the sign will be placed outside, I always opt for durable materials like aluminum or treated wood.
What is your experience with incorporating electrical components into signs, such as LEDs or neon lighting?
How to Answer
- 1
Mention specific types of electrical components you have worked with
- 2
Discuss the processes you followed for installation and wiring
- 3
Include any troubleshooting or maintenance experiences
- 4
Highlight any safety protocols you adhered to during the work
- 5
Share results or feedback from previous projects involving electrical components
Example Answers
I have experience installing LED lighting in channel letters. I carefully followed wiring schematics, ensuring that each LED module was properly connected. I also conducted a final test for brightness and uniformity before installation.
Don't Just Read Sign Fabricator Questions - Practice Answering Them!
Reading helps, but actual practice is what gets you hired. Our AI feedback system helps you improve your Sign Fabricator interview answers in real-time.
Personalized feedback
Unlimited practice
Used by hundreds of successful candidates
How do you apply color theory in your fabrication work to ensure effective sign visibility and aesthetics?
How to Answer
- 1
Understand the basics of color theory, including primary, secondary, and complementary colors.
- 2
Consider contrast to ensure the sign is readable from a distance; use high contrast for text and background.
- 3
Utilize color psychology to evoke appropriate feelings or associations related to the brand or message.
- 4
Test color combinations with different materials under various lighting conditions to check visibility.
- 5
Stay updated on industry trends in color to keep designs modern and appealing.
Example Answers
I apply color theory by using high contrast colors, like dark blue text on a light yellow background, to ensure visibility from a distance. I also consider the psychological impact, using red to grab attention for sale signs.
What cutting techniques do you use, and how do you ensure accuracy in your work?
How to Answer
- 1
Mention specific tools like CNC machines or band saws you prefer.
- 2
Explain your process for measuring and marking materials before cutting.
- 3
Discuss any techniques you use for double-checking measurements.
- 4
Highlight the importance of maintaining tools for precise cuts.
- 5
Share an example of a situation where your technique ensured a successful outcome.
Example Answers
I primarily use CNC machines for precise cuts, and I always measure twice before cutting. I mark my materials clearly and use a square to ensure everything is aligned. I regularly inspect my tools to maintain accuracy.
What finishing processes do you utilize to enhance the durability and appearance of the signs you fabricate?
How to Answer
- 1
Discuss common finishing techniques such as sealing, painting, or laminating
- 2
Mention specific materials or coatings used for durability
- 3
Include any quality control measures taken after finishing processes
- 4
Highlight any eco-friendly or innovative approaches if applicable
- 5
Be confident and concise about your practical experiences and results
Example Answers
I typically use a UV-resistant clear coat to seal the signs, enhancing both durability and gloss. Additionally, I apply a weatherproof laminate for outdoor signs, ensuring they withstand harsh conditions.
What types of machinery and tools are you proficient with in sign fabrication?
How to Answer
- 1
List specific machines you have experience with, like CNC routers or vinyl cutters.
- 2
Mention any software tools you use alongside the machinery, like Adobe Illustrator.
- 3
Highlight any safety training or certifications you have related to the tools.
- 4
Emphasize the types of materials you've worked with, such as wood or metal.
- 5
Share examples of projects where you successfully used these tools.
Example Answers
I am proficient with CNC routers and vinyl cutters. I often use Adobe Illustrator for design and have worked with materials like acrylic and wood. Recently, I fabricated a large outdoor sign using these tools, which improved my skills.
How proficient are you with CAD software, and how do you use it in your sign fabrication process?
How to Answer
- 1
Mention specific CAD software you are familiar with.
- 2
Describe your experience level with the software.
- 3
Explain how you use CAD for design and planning.
- 4
Provide an example of a project where CAD was crucial.
- 5
Highlight any certifications or training in CAD, if applicable.
Example Answers
I am proficient in AutoCAD and have been using it for over 5 years. I use it primarily to create detailed sign designs and layouts, ensuring accuracy in measurements. For example, I designed a large billboard project where CAD helped me visualize dimensions and placement effectively.
What types of welding techniques do you use in sign fabrication, and when do you apply them?
How to Answer
- 1
Identify the main welding techniques you have experience with
- 2
Mention specific applications for each technique in sign fabrication
- 3
Explain the advantages of each technique in terms of durability and aesthetics
- 4
Be prepared to discuss any safety measures you follow while welding
- 5
Keep your answers concise and focused on relevance to sign making
Example Answers
I primarily use MIG and TIG welding for sign fabrication. I apply MIG for larger metal structures because it provides a strong bond quickly, while I use TIG for detailed work on smaller components due to its precision and cleaner finish.
What printing techniques are you familiar with in sign production, and how do you decide which to use?
How to Answer
- 1
List specific printing techniques you have experience with.
- 2
Explain the advantages of each technique in relation to the project.
- 3
Discuss factors that influence your choice, such as materials and design requirements.
- 4
Mention how you consider durability and environmental conditions for the intended sign use.
- 5
Provide a brief example of a project where your decision on printing technique was crucial.
Example Answers
I am familiar with techniques such as digital printing, screen printing, and vinyl cutting. I choose based on the materials and the sign's intended use. For instance, digital printing is great for detailed graphics, while screen printing works well for bold colors and larger runs. In one project, I used vinyl cutting for a window graphic, considering the outdoor exposure and the need for high durability.
Which design software tools are you comfortable using, and how do they assist in your sign fabrication projects?
How to Answer
- 1
List specific design software you know, like Adobe Illustrator or CorelDRAW.
- 2
Explain how each tool is used in your sign fabrication process.
- 3
Highlight any experience you have with vector graphics or 3D modeling software.
- 4
Mention any specific projects where these tools played a key role.
- 5
Be honest about your skill level with each software.
Example Answers
I am proficient in Adobe Illustrator, which I use to create vector graphics for signs. It helps me ensure crisp edges and accurate scaling when fabricating pieces.
Don't Just Read Sign Fabricator Questions - Practice Answering Them!
Reading helps, but actual practice is what gets you hired. Our AI feedback system helps you improve your Sign Fabricator interview answers in real-time.
Personalized feedback
Unlimited practice
Used by hundreds of successful candidates
Situational Interview Questions
If a customer approaches you with a design that is not feasible for the intended purpose, how would you handle the situation?
How to Answer
- 1
Listen carefully to the customer's ideas and concerns
- 2
Explain the specific reasons why the design is not feasible
- 3
Offer alternative solutions or modifications that could work
- 4
Make sure to keep the conversation positive and collaborative
- 5
Ensure the customer feels valued and understood throughout the discussion
Example Answers
I would first listen to the customer's design to understand their vision. Then, I would explain why the design isn’t feasible, such as material limitations. I would suggest a modified version that meets both their needs and safety standards.
If a design needs to be altered due to last-minute changes, how would you go about implementing these changes without compromising quality?
How to Answer
- 1
Assess the specific changes needed and their impact on the existing design.
- 2
Consult with the design team to clarify requirements and expectations.
- 3
Prioritize quality by ensuring materials and techniques align with industry standards.
- 4
Communicate clearly with the fabrication team about any changes and expectations.
- 5
Plan the production workflow to accommodate changes while minimizing downtime.
Example Answers
I would first evaluate the changes required and their implications on the current design. Then, I'd speak to the design team for clarity. Ensuring we use high-quality materials is next, so I would confirm that we have what we need before proceeding. Clear communication with the fabrication team is crucial, followed by adjusting our workflow to integrate these changes efficiently.
Don't Just Read Sign Fabricator Questions - Practice Answering Them!
Reading helps, but actual practice is what gets you hired. Our AI feedback system helps you improve your Sign Fabricator interview answers in real-time.
Personalized feedback
Unlimited practice
Used by hundreds of successful candidates
You discover a minor defect in a sign that is ready for delivery. What steps would you take to address this before the sign leaves your shop?
How to Answer
- 1
Assess the defect to determine its impact on aesthetics and functionality
- 2
Consult with a team member or supervisor if unsure how to proceed
- 3
Decide on the best corrective action, such as repair or replacement
- 4
Document the defect and the steps taken for quality control records
- 5
Communicate with the customer about any changes or delays if significant
Example Answers
First, I would carefully examine the defect to see if it affects the overall look or function of the sign. If it’s significant, I’d consult my supervisor for advice. Then, I would either repair the defect or create a new piece if necessary. Finally, I’d document the issue and correction for our records.
If you notice a coworker not following safety protocols, what would you do to handle the situation?
How to Answer
- 1
Observe the situation discreetly to ensure you understand the context.
- 2
Approach the coworker calmly and privately to discuss the issue.
- 3
Express your concerns directly, focusing on safety and well-being.
- 4
Encourage them to follow the protocols and suggest resources if needed.
- 5
If necessary, report the behavior to a supervisor for further action.
Example Answers
I would first observe the situation to confirm what I saw. Then, I'd approach my coworker privately and say something like, 'Hey, I noticed you weren't wearing your safety goggles. Safety is really important for our team's well-being. Can we make sure we follow the protocol?' If they didn’t respond well, I would inform a supervisor.
Suppose you have a limited supply of materials and an increase in production demand. How would you manage your resources?
How to Answer
- 1
Assess and prioritize production orders based on urgency and importance
- 2
Optimize existing materials through efficient cutting and assembly techniques
- 3
Communicate with team members to align strategies for material use
- 4
Consider outsourcing some components if internal resources are too limited
- 5
Monitor usage closely to avoid overstocking on lesser priority items
Example Answers
I would first evaluate all production orders and prioritize them based on deadlines. Then, I would optimize the use of materials, ensuring cuts are efficient and minimizing waste. Additionally, I would keep the team informed about our material constraints and involve them in finding creative solutions.
Imagine you are close to a deadline and a crucial part of your sign fabrication machinery breaks down. What would you do to ensure the project is completed on time?
How to Answer
- 1
Stay calm and assess the situation quickly
- 2
Identify critical tasks that can be completed without the broken machinery
- 3
Contact maintenance or the supplier for immediate repairs or replacements
- 4
Communicate with your team and stakeholders about the issue
- 5
Consider alternative solutions or temporary fixes to keep the project moving
Example Answers
I would stay calm and assess which part of the machinery is broken. Then, I would focus on completing tasks that can be done without that machine. I would also reach out to our maintenance team for a quick fix or look for a local supplier who could provide a replacement part. Keeping my team informed would be a priority so we can all adapt our workflow.
A client is not satisfied with the initial sign you fabricated. How would you handle their feedback and resolve the issue?
How to Answer
- 1
Listen carefully to the client's concerns and understand their perspective.
- 2
Acknowledge their feedback and express understanding of their dissatisfaction.
- 3
Ask specific questions to clarify what they would like changed or improved.
- 4
Propose a solution or revision and provide a timeline for when it can be accomplished.
- 5
Follow up to ensure they are satisfied with the final product.
Example Answers
I would listen to the client's feedback closely to fully understand their concerns. Then, I would acknowledge their dissatisfaction and ask specific questions to clarify what aspects they want to be changed. After that, I would propose a solution and let them know when they can expect the revised sign.
If a fire breaks out in your workshop due to an electrical fault, what would be your immediate course of action?
How to Answer
- 1
Stay calm and assess the situation quickly
- 2
Activate the fire alarm and alert all personnel immediately
- 3
Use the nearest fire extinguisher if the fire is manageable
- 4
Evacuate the workshop and direct everyone to a safe location
- 5
Do not try to extinguish a large fire or put yourself in danger
Example Answers
I would first stay calm and assess the fire's severity. Then, I would activate the fire alarm to alert everyone in the workshop. If the fire is small and manageable, I would attempt to use the nearest fire extinguisher while ensuring that everyone else is evacuating. Finally, I would make sure everyone is safely outside before calling for emergency help.
A client requests a high-quality sign but has a limited budget. How would you approach this to ensure client satisfaction while staying within budget?
How to Answer
- 1
Discuss the client's priorities and the essential features of the sign.
- 2
Suggest cost-effective materials that maintain quality.
- 3
Offer options for simpler designs that can achieve a similar look.
- 4
Propose a phased approach, starting with the most critical elements.
- 5
Communicate openly about budget constraints and potential compromises.
Example Answers
I would first talk with the client to understand what aspects of the sign are most important to them. Then, I would suggest cost-effective materials that still ensure durability and aesthetics. Offering a simplified design could also help keep costs down while still delivering a quality sign.
If asked to replicate a competitor's patented design, how would you respond to ensure ethical practices?
How to Answer
- 1
Acknowledge the importance of intellectual property laws
- 2
Explain the need to respect patents and designs
- 3
Suggest alternatives to creative replication
- 4
Discuss the importance of innovation in your work
- 5
Highlight the need for ethical discussions with your team or supervisor
Example Answers
I would first respect the competitor's patent by not replicating their design. Instead, I would brainstorm original ideas that meet our client's needs and maybe even improve on existing concepts.
Don't Just Read Sign Fabricator Questions - Practice Answering Them!
Reading helps, but actual practice is what gets you hired. Our AI feedback system helps you improve your Sign Fabricator interview answers in real-time.
Personalized feedback
Unlimited practice
Used by hundreds of successful candidates
Sign Fabricator Position Details
Salary Information
Recommended Job Boards
CareerBuilder
www.careerbuilder.com/jobs-sign-fabricatorZipRecruiter
www.ziprecruiter.com/Jobs/Sign-FabricatorThese job boards are ranked by relevance for this position.
Related Positions
- Sign Maker
- Fly Maker
- Frame Builder
- Plastic Fabricator
- Frame Maker
- Body Maker
- Pad Maker
- Camera Maker
- End Maker
- Button Maker
Similar positions you might be interested in.
Ace Your Next Interview!
Practice with AI feedback & get hired faster
Personalized feedback
Used by hundreds of successful candidates
Ace Your Next Interview!
Practice with AI feedback & get hired faster
Personalized feedback
Used by hundreds of successful candidates