Top 34 Sleever Interview Questions and Answers [Updated 2025]
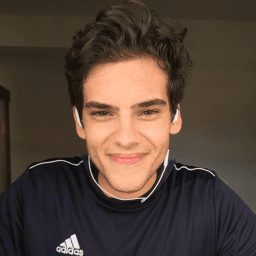
Andre Mendes
•
March 30, 2025
Preparing for a Sleever job interview? Dive into our comprehensive guide featuring the most common interview questions for the Sleever role, complete with example answers and expert tips. This post is designed to equip you with the insights needed to craft compelling responses and make a lasting impression. Get ready to boost your confidence and ace your interview with ease!
Download Sleever Interview Questions in PDF
To make your preparation even more convenient, we've compiled all these top Sleeverinterview questions and answers into a handy PDF.
Click the button below to download the PDF and have easy access to these essential questions anytime, anywhere:
List of Sleever Interview Questions
Situational Interview Questions
What would you do if you noticed unsafe practices in the sleeving area?
How to Answer
- 1
Identify the unsafe practice clearly and calmly.
- 2
Ensure immediate safety by alerting nearby colleagues.
- 3
Report the unsafe practice to a supervisor or safety officer.
- 4
Suggest improvements or corrective actions based on your knowledge.
- 5
Follow up to ensure that the issues have been addressed.
Example Answers
If I noticed unsafe practices such as workers not wearing PPE, I would first alert my colleagues to ensure everyone's immediate safety. Then, I would report the situation to my supervisor so they can investigate further and implement necessary changes.
If you are nearing a deadline and the sleeving equipment fails, what steps would you take?
How to Answer
- 1
Assess the situation quickly and identify the nature of the failure
- 2
Notify team members and supervisors about the issue immediately
- 3
Implement a temporary workaround if possible to maintain production
- 4
Contact maintenance for assistance to fix the equipment
- 5
Monitor the progress closely and adjust plans as necessary to meet the deadline
Example Answers
I would first assess the failure to understand what went wrong. Then I would notify my supervisor and the maintenance team. If feasible, I would look for a temporary workaround to keep production going until the equipment is fixed.
Don't Just Read Sleever Questions - Practice Answering Them!
Reading helps, but actual practice is what gets you hired. Our AI feedback system helps you improve your Sleever interview answers in real-time.
Personalized feedback
Unlimited practice
Used by hundreds of successful candidates
How would you handle a disagreement with a team member over the best approach to a sleeving task?
How to Answer
- 1
Listen actively to the team member's perspective
- 2
Share your reasoning clearly and respectfully
- 3
Seek common ground and shared goals
- 4
Suggest collaborating on a trial of both approaches
- 5
Remain open to feedback and willing to adjust your view
Example Answers
I would first listen to my team member's thoughts to understand their viewpoint. Then, I would share my approach and explain why I believe it's effective. Together, we could find common goals and maybe even test both methods to see which works best.
You have been given limited resources to complete an urgent sleeving order; how would you prioritize your tasks?
How to Answer
- 1
Assess the urgency and importance of the sleeving order.
- 2
Break down the tasks necessary to complete the order.
- 3
Identify available resources and any constraints.
- 4
Prioritize tasks that have the highest impact on meeting the deadline.
- 5
Communicate with your team to delegate tasks effectively.
Example Answers
First, I would assess the specific requirements of the urgent sleeving order. Then, I would list out all the tasks needed to complete it and identify which of those can be done simultaneously. I'd prioritize the most critical tasks that directly affect the completion time, delegate any that can be handled by team members, and keep everyone in the loop to ensure we all move efficiently towards meeting the deadline.
A new employee is struggling with the sleeving machine; how would you assist them?
How to Answer
- 1
Observe the employee to identify specific issues they are facing.
- 2
Ask the employee questions to understand their challenges better.
- 3
Provide a step-by-step demonstration of the machine's operation.
- 4
Encourage the employee to try operating the machine with your support.
- 5
Follow up after the training to ensure they are comfortable and improve.
Example Answers
I would first observe the new employee working on the machine to see where they are having trouble. Then, I'd ask them specific questions to better understand their challenges. After that, I would demonstrate how to use the machine step by step and let them practice while I supervise, giving them tips along the way.
How would you handle a situation where a client is dissatisfied with the quality of the sleeving?
How to Answer
- 1
Acknowledge the client's concerns promptly and empathetically
- 2
Ask for specific details about the quality issues they experienced
- 3
Offer a solution, such as redoing the sleeving or providing a refund
- 4
Communicate your commitment to quality and client satisfaction
- 5
Follow up with the client after resolving the issue to ensure their satisfaction
Example Answers
I would first listen to the client's concerns and acknowledge their dissatisfaction. I would ask them to detail the specific issues they noticed with the sleeving, then offer to redo the work at no cost to them or provide a refund if they prefer. I'd assure them that quality is my priority and follow up with them afterward to make sure they are happy with the resolution.
You are managing multiple sleeving projects at once; how do you organize your workflow?
How to Answer
- 1
Prioritize projects based on deadlines and impact
- 2
Use project management tools to track progress
- 3
Set clear milestones for each project
- 4
Communicate regularly with team members and stakeholders
- 5
Review and adjust your workflow weekly to stay on track
Example Answers
I prioritize my sleeving projects by their deadlines and overall impact. I use project management tools like Trello to visualize progress and ensure all tasks are on schedule. I set clear milestones and check in with my team every week to discuss any obstacles.
If you notice an error in the sleeving process after it has started, what would you do?
How to Answer
- 1
Stay calm and assess the situation quickly
- 2
Identify the type and impact of the error on the product
- 3
Communicate the issue to your supervisor or team lead immediately
- 4
Take corrective action if you are authorized to do so
- 5
Document the error and the steps taken to resolve it
Example Answers
If I notice an error, I would first remain calm and assess how serious the situation is. Then, I would inform my supervisor right away and discuss the necessary steps to correct it. If I have the authority, I would make the correction myself and document everything.
Imagine you are asked to innovate a new sleeving process. What ideas would you consider?
How to Answer
- 1
Identify current challenges in sleaving processes.
- 2
Research recent technological advancements in materials.
- 3
Consider automation to improve efficiency.
- 4
Explore sustainability in sleeving materials.
- 5
Think about user experience and ease of application.
Example Answers
I would focus on developing a biodegradable sleeving material to reduce environmental impact while also investigating automated application systems that can streamline the process.
If instructed to implement a new sleeving technique but are already busy with other projects, how would you proceed?
How to Answer
- 1
Evaluate the urgency and importance of the new sleeving technique.
- 2
Communicate with your manager to prioritize tasks.
- 3
Identify resources or team members who can assist.
- 4
Break down the implementation into manageable steps.
- 5
Schedule time to focus specifically on the new technique.
Example Answers
I would first assess how critical the new technique is compared to my current workload. Then, I would discuss with my manager about prioritizing tasks and possibly delegating some responsibilities to teammates.
Don't Just Read Sleever Questions - Practice Answering Them!
Reading helps, but actual practice is what gets you hired. Our AI feedback system helps you improve your Sleever interview answers in real-time.
Personalized feedback
Unlimited practice
Used by hundreds of successful candidates
If you were the team leader during a sleeving project and faced resistance from team members, how would you address it?
How to Answer
- 1
Listen to the concerns of team members to understand the root of resistance
- 2
Communicate the vision and goals of the project clearly to the team
- 3
Encourage open dialogue and provide a platform for feedback
- 4
Offer solutions to address specific concerns raised by team members
- 5
Foster collaboration by involving team members in decision-making
Example Answers
I would start by listening to the team members' concerns to understand their resistance. After identifying the issues, I would communicate the overall vision of the sleeving project and how each person's contribution is valuable. I would create a safe space for open dialogue and work collaboratively to address specific challenges they may have.
Behavioral Interview Questions
Can you describe a time when you had to work closely with a team to complete a sleeving project?
How to Answer
- 1
Identify a specific sleeving project you worked on with a team
- 2
Highlight your role and contributions in the team
- 3
Discuss any challenges faced and how you worked together to overcome them
- 4
Emphasize the outcome and what you learned from the collaboration
- 5
Keep your answer focused and concise, using the STAR method (Situation, Task, Action, Result)
Example Answers
In my previous role, we had a project to sleeve a batch of products for a major client. I collaborated with three colleagues, each handling different aspects. I coordinated the design process, ensuring it met client specifications. We faced tight deadlines, but through daily check-ins, we streamlined our workflow and completed it on time, exceeding client expectations. This taught me the importance of communication in teamwork.
Tell me about a time when you had to adapt to a last-minute change in a production schedule.
How to Answer
- 1
Choose a specific situation where a change occurred.
- 2
Explain your immediate reaction and decision-making process.
- 3
Highlight the steps you took to adapt effectively.
- 4
Emphasize any positive outcomes or lessons learned.
- 5
Keep it concise and relevant to the role of a Sleever.
Example Answers
In my previous job, we had a sudden change in a production order that required us to switch the product line last minute. I quickly assessed the situation, coordinated with the team to prioritize tasks, and we managed to streamline the process by reallocating resources. As a result, we met the new deadline without sacrificing quality.
Don't Just Read Sleever Questions - Practice Answering Them!
Reading helps, but actual practice is what gets you hired. Our AI feedback system helps you improve your Sleever interview answers in real-time.
Personalized feedback
Unlimited practice
Used by hundreds of successful candidates
Describe a challenging problem you faced during the sleeving process and how you resolved it.
How to Answer
- 1
Identify a specific problem you encountered.
- 2
Explain the impact of the problem on the sleeving process.
- 3
Describe the steps you took to solve the problem.
- 4
Highlight the outcome of your actions.
- 5
Connect the experience to your skills or lessons learned.
Example Answers
During a sleeving project, we faced a quality issue where the sleeves were not properly adhering to the products. This caused delays in production. I investigated the adhesive used and discovered it wasn't suitable for the materials. I coordinated with suppliers to obtain a better adhesive and retrained the team on the correct application. As a result, we improved adherence and met our deadlines.
Give an example of how you communicated effectively with colleagues during a complex project.
How to Answer
- 1
Choose a specific project and highlight the complexity.
- 2
Describe the communication methods you used, such as meetings or emails.
- 3
Mention how you ensured clarity and understanding among team members.
- 4
Emphasize any feedback mechanisms you implemented.
- 5
Conclude with the positive outcome of your effective communication.
Example Answers
During a product launch project, our team faced multiple challenges regarding timelines. I organized weekly update meetings to discuss progress and gather feedback from all departments. By summarizing key points and action items clearly in follow-up emails, we ensured everyone was on the same page. This led to the project being completed one week ahead of schedule.
Have you ever taken the lead on a sleeving project? What was the outcome?
How to Answer
- 1
Start by briefly describing the project you led.
- 2
Highlight your specific role and responsibilities in the project.
- 3
Explain the challenges you faced and how you overcame them.
- 4
Discuss the outcome and any measurable improvements achieved.
- 5
Conclude with a reflection on what you learned from the experience.
Example Answers
I led a sleeving project to streamline our packaging process. My role was to coordinate between the design and production teams. We faced delays due to material shortages, but I negotiated with suppliers to ensure timely delivery. The project resulted in a 20% reduction in packaging time and increased customer satisfaction. I learned the importance of clear communication in cross-departmental projects.
What has motivated you to work in the sleeving industry?
How to Answer
- 1
Identify personal experiences that sparked your interest in the sleeving industry.
- 2
Discuss specific skills or strengths that align with sleeving work.
- 3
Mention the importance of quality and efficiency in production.
- 4
Express enthusiasm for innovation and advancements in sleeving technology.
- 5
Connect your motivation to your career goals and how they align with the company's mission.
Example Answers
I became interested in the sleeving industry while working on a project that involved packaging solutions. I realized how crucial sleeving is for both functionality and aesthetics, and it motivated me to learn more and contribute to this field.
Describe a time when you received constructive feedback on your work and how you applied it.
How to Answer
- 1
Select a specific example where feedback was given.
- 2
Describe the feedback clearly and honestly.
- 3
Explain the actions you took to implement the feedback.
- 4
Share the positive outcome or improvement that resulted.
- 5
Keep your response focused and concise.
Example Answers
In my last project, my manager pointed out that my presentation lacked clarity. I took this feedback seriously and revamped my slides, focusing on key points and visuals. This led to a more engaging presentation, and I received higher praise from my team.
Can you provide an example of when you took the initiative to improve a sleeving process?
How to Answer
- 1
Identify a specific problem in the sleeving process you observed.
- 2
Explain the initiative you took to address this problem.
- 3
Describe the steps you implemented and how you executed your plan.
- 4
Share the results of your initiative and how it improved the process.
- 5
Mention any feedback received or measurable outcomes from your improvements.
Example Answers
In my previous role, I noticed that the sleeving machine often jammed due to insufficient operator training. I took the initiative to create a training manual and held a workshop for the team. This resulted in a 30% reduction in machine downtime.
How do you prioritize your tasks when working on a tight project deadline?
How to Answer
- 1
Identify all tasks required for the project.
- 2
Use a priority matrix to categorize tasks by urgency and importance.
- 3
Break down large tasks into smaller, manageable steps.
- 4
Set clear deadlines for each task to maintain focus.
- 5
Communicate with your team about priorities and progress.
Example Answers
I start by listing all the tasks needed for the project and then use a priority matrix to differentiate what is urgent and important. This helps me focus on high-priority tasks first and break them down into smaller steps to manage them effectively.
Describe a time when you went above and beyond in your role as a sleever.
How to Answer
- 1
Choose a specific instance that highlights your commitment.
- 2
Focus on actions you took that exceeded the normal expectations.
- 3
Quantify results if possible to show impact.
- 4
Reflect on the skills or values that drove your actions.
- 5
Prepare to explain what you learned from the experience.
Example Answers
In my last job as a sleever, we had an unexpected surge in orders due to a promotion. I volunteered to stay late to ensure we met the increased demand, which helped boost our on-time delivery to 98%. I learned the importance of teamwork and flexibility under pressure.
Don't Just Read Sleever Questions - Practice Answering Them!
Reading helps, but actual practice is what gets you hired. Our AI feedback system helps you improve your Sleever interview answers in real-time.
Personalized feedback
Unlimited practice
Used by hundreds of successful candidates
How do you stay updated on the latest trends and technologies in the sleeving industry?
How to Answer
- 1
Subscribe to industry newsletters and blogs focused on sleeving technology.
- 2
Attend trade shows and industry conferences relevant to sleeving.
- 3
Join professional associations for networking and sharing knowledge.
- 4
Participate in online forums and social media groups about sleeving advancements.
- 5
Engage with suppliers and manufacturers to learn about new products and technologies.
Example Answers
I subscribe to several industry newsletters and blogs, such as Sleeving Today, and I also attend major trade shows like Pack Expo to see the latest innovations.
Technical Interview Questions
What types of sleeving machinery are you familiar with and what are their key functions?
How to Answer
- 1
List specific types of sleeving machines you have worked with
- 2
Describe the main function of each machine
- 3
Mention any relevant experience or projects involving these machines
- 4
Keep the answer concise, focusing on key points
- 5
Be prepared to discuss any recent technological advancements
Example Answers
I am familiar with heat shrink sleeving machines, which apply heat to shrink a sleeve around products. I have also used pressure-sensitive label applicators that apply sleeves using adhesive. In my last job, I operated a fully automated sleeving line that improved production efficiency by 30%.
Can you explain the different methods of applying sleeves to products?
How to Answer
- 1
Start by listing common sleeve application methods.
- 2
Explain each method briefly with key characteristics.
- 3
Mention any specific tools or machines used for each method.
- 4
Provide examples of products that typically use these methods.
- 5
Conclude with a reflection on the importance of choosing the right method.
Example Answers
There are several methods for applying sleeves, including shrink sleeve application, stretch sleeve application, and label applicators. Shrink sleeves use heat to conform to the product's shape, while stretch sleeves rely on elasticity. Equipment like sleeve applicators and heat tunnels are common in these processes. Products like bottles and cans frequently use these sleeve methods. Choosing the appropriate method impacts product display and brand messaging.
Don't Just Read Sleever Questions - Practice Answering Them!
Reading helps, but actual practice is what gets you hired. Our AI feedback system helps you improve your Sleever interview answers in real-time.
Personalized feedback
Unlimited practice
Used by hundreds of successful candidates
What factors do you consider when selecting materials for sleeving?
How to Answer
- 1
Consider the environment where the sleeve will be used, such as temperature and exposure to chemicals.
- 2
Evaluate the mechanical properties required, like abrasion resistance and flexibility.
- 3
Think about the electrical properties needed, if applicable, such as dielectric strength or conductivity.
- 4
Assess the compatibility with existing materials for adhesion and bonding.
- 5
Factor in the cost and availability of materials to ensure budget adherence.
Example Answers
I consider the operating environment first, specifically temperature and chemical exposure, then evaluate the mechanical properties needed, such as flexibility and abrasion resistance. Lastly, I look at compatibility with other materials to ensure a secure bond.
How do you ensure quality control during the sleeving process?
How to Answer
- 1
Implement regular machine calibration checks to maintain precision.
- 2
Establish a checklist for each batch to monitor key quality metrics.
- 3
Conduct visual inspections of finished products for defects.
- 4
Use quality control sampling to test sleeves at different stages.
- 5
Train team members on quality expectations and proper procedures.
Example Answers
I ensure quality control during the sleeving process by implementing regular calibration checks on the machines and using a quality checklist for each batch.
What common issues have you encountered with sleeving and how do you troubleshoot them?
How to Answer
- 1
Identify key sleeving issues like inconsistent tension or wrinkles.
- 2
Explain your systematic approach to diagnosing problems.
- 3
Mention specific tools or techniques you've used to resolve issues.
- 4
Share an example of a successful troubleshooting experience.
- 5
Highlight the importance of teamwork in problem-solving.
Example Answers
I often encountered inconsistent tension while sleeving. I troubleshoot this by adjusting the roller pressure and checking the material feed. Once, during a production run, I noticed the sleeves wrinkling and resolved it by recalibrating the equipment, which improved quality immediately.
Are you experienced in using design software for creating sleeve designs? Please elaborate.
How to Answer
- 1
Mention specific design software you are profcient in.
- 2
Describe a project where you used the software for sleeve design.
- 3
Highlight any unique techniques or styles you employed.
- 4
Discuss the outcome of your design work and any feedback received.
- 5
Be confident and concise in your response.
Example Answers
I am proficient in Adobe Illustrator and CorelDRAW. Recently, I created a series of sleeve designs for a local clothing brand, using Illustrator to incorporate unique color gradients and patterns. The designs were well received and increased the brand's visibility on social media.
What industry standards do you follow when performing sleeving operations?
How to Answer
- 1
Mention specific industry standards like ISO, ASTM, or others related to sleeving.
- 2
Highlight the importance of safety standards during operations.
- 3
Discuss any relevant quality control measures you implement.
- 4
Explain how you keep up-to-date with industry regulations and practices.
- 5
Provide examples of situations where you applied these standards.
Example Answers
I always follow ISO 9001 for quality management in my sleeving operations and ensure compliance with ASTM standards for material specifications.
What are the different types of sleeves you have worked with and their specific applications?
How to Answer
- 1
Identify the types of sleeves you've encountered in your work.
- 2
Explain their specific applications and contexts in which you've used them.
- 3
Highlight any relevant projects where you utilized these sleeves.
- 4
Mention any unique properties or benefits of the sleeves you worked with.
- 5
Be concise and focus on examples relevant to the Sleever position.
Example Answers
I have worked with elastic sleeves for lightweight fabrics, often used in casual wear to allow for stretch. I've also used structured sleeves in tailored garments, which require a more formal silhouette. For instance, in my last project, I designed a dress shirt that featured both types depending on the sleeve style needed.
How do you perform testing to ensure the sleeves meet specific requirements?
How to Answer
- 1
Identify the specific requirements of the sleeves
- 2
Choose appropriate testing methods like tensile testing or wear testing
- 3
Conduct tests according to industry standards
- 4
Document the results and compare against requirements
- 5
Iterate on design if testing reveals deficiencies
Example Answers
To ensure sleeves meet requirements, I first clarify the specifications needed for the material. Then I conduct tensile testing to measure strength and flexibility, ensuring they pass established industry standards. I document everything and make modifications based on test results if needed.
Don't Just Read Sleever Questions - Practice Answering Them!
Reading helps, but actual practice is what gets you hired. Our AI feedback system helps you improve your Sleever interview answers in real-time.
Personalized feedback
Unlimited practice
Used by hundreds of successful candidates
Can you explain the packaging process following the sleeving stage?
How to Answer
- 1
Start by briefly defining what sleeving is in packaging.
- 2
Outline the immediate steps after sleeving such as quality checks.
- 3
Discuss the secondary packaging methods used post-sleeving.
- 4
Mention how products are labeled and finalized for shipping.
- 5
Conclude with the importance of efficiency and accuracy in the process.
Example Answers
After the sleeving stage, we first conduct a quality check to ensure the sleeve is properly placed and the product's integrity is maintained. Then, we move on to the secondary packaging phase, where sleeved products are placed in boxes or containers. Each package is labeled correctly before being finalized for shipping. Ensuring accuracy and efficiency is crucial to meet delivery deadlines.
Sleever Position Details
Recommended Job Boards
ZipRecruiter
www.ziprecruiter.com/Jobs/SleeverThese job boards are ranked by relevance for this position.
Related Positions
Similar positions you might be interested in.
Ace Your Next Interview!
Practice with AI feedback & get hired faster
Personalized feedback
Used by hundreds of successful candidates
Ace Your Next Interview!
Practice with AI feedback & get hired faster
Personalized feedback
Used by hundreds of successful candidates