Top 32 Station Mechanic Interview Questions and Answers [Updated 2025]
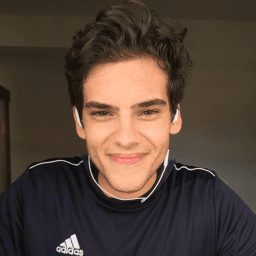
Andre Mendes
•
March 30, 2025
Preparing for a Station Mechanic interview can be daunting, but we're here to help streamline your preparation. In this blog post, we cover the most common interview questions for this role, complete with example answers and valuable tips on how to respond effectively. Whether you're a seasoned professional or new to the field, our guide will equip you with the insights needed to confidently tackle your interview.
Download Station Mechanic Interview Questions in PDF
To make your preparation even more convenient, we've compiled all these top Station Mechanicinterview questions and answers into a handy PDF.
Click the button below to download the PDF and have easy access to these essential questions anytime, anywhere:
List of Station Mechanic Interview Questions
Situational Interview Questions
If you are given a limited budget for parts, how would you prioritize repairs?
How to Answer
- 1
Assess the criticality of each repair based on safety and operational impact
- 2
Consider the age and condition of the components needing repair
- 3
Evaluate the potential downtime each repair may cause
- 4
Prioritize repairs that prevent further damage or costly future repairs
- 5
Communicate with team members to understand their insights on priorities
Example Answers
I would first identify repairs that affect safety and ensure those are prioritized. Then, I would look at repairs that if delayed could lead to more significant issues down the line.
What would you do if you discovered a safety hazard while performing maintenance?
How to Answer
- 1
Identify and assess the safety hazard immediately.
- 2
If it's safe, take steps to mitigate the hazard temporarily.
- 3
Report the hazard to the appropriate supervisor or safety officer.
- 4
Document the hazard and the actions taken.
- 5
Follow up to ensure corrective actions are implemented.
Example Answers
Upon discovering a safety hazard, I would first assess the situation to understand the risks. Then, I would take immediate steps to mitigate the hazard if possible, such as securing the area. Next, I would report it to my supervisor and document everything for further actions.
Don't Just Read Station Mechanic Questions - Practice Answering Them!
Reading helps, but actual practice is what gets you hired. Our AI feedback system helps you improve your Station Mechanic interview answers in real-time.
Personalized feedback
Unlimited practice
Used by hundreds of successful candidates
How would you respond if a critical piece of equipment failed just before a busy service period?
How to Answer
- 1
Stay calm and assess the situation quickly
- 2
Communicate the issue to your team immediately
- 3
Prioritize safety and minimize disruption
- 4
Implement a temporary solution if possible
- 5
Follow up with a plan for permanent repairs later
Example Answers
I would remain calm and evaluate the situation to understand the failure. Then, I would inform my team about the issue and work with them to ensure everyone's safety, putting a temporary fix in place if feasible to reduce downtime.
Imagine you are faced with an unfamiliar type of machinery to repair. What steps would you take?
How to Answer
- 1
Start by consulting the machinery's manual or technical documentation.
- 2
Identify and assess the most critical issues affecting its operation.
- 3
Gather any necessary tools and safety equipment for the task.
- 4
Take notes on the existing problems and potential solutions.
- 5
If needed, seek advice from colleagues or experts familiar with similar equipment.
Example Answers
First, I would locate and review the machinery's manual to understand its functions and components. Then, I would identify the specific issue at hand and gather the appropriate tools. I would document my findings and consider reaching out to a colleague for additional insights if necessary.
How would you handle a situation where a colleague is not communicating important information related to a repair task?
How to Answer
- 1
Address the issue directly with the colleague in a private and respectful manner
- 2
Ask open-ended questions to understand their perspective
- 3
Clarify the importance of the information for the team's success
- 4
Suggest ways to improve communication going forward
- 5
Follow up with the colleague to ensure understanding and agreement
Example Answers
I would have a private chat with my colleague to express my concerns about the missing information. I would ask if there’s anything causing the communication gap and emphasize how vital clear information is for our repair tasks.
What would you do if your team disagrees on the best approach to repair equipment?
How to Answer
- 1
Encourage open discussion to hear all perspectives
- 2
Evaluate the pros and cons of each suggested approach
- 3
Consider consulting technical manuals or guidelines
- 4
Propose a trial of the different methods for a small repair
- 5
Seek input from a supervisor if disagreement persists
Example Answers
I would bring the team together to discuss each method. I'd encourage everyone to share their reasoning and then weigh the pros and cons of each approach to find the best solution.
If you are running behind on a repair task but have another task waiting, how would you prioritize?
How to Answer
- 1
Assess the urgency and impact of both tasks
- 2
Communicate with your supervisor or team about the delay
- 3
Determine if the waiting task can be started in parallel
- 4
Focus on completing the current task to a safe stopping point
- 5
Plan for catch-up time after addressing priority tasks
Example Answers
I would first evaluate which repair is more urgent and communicates that to my supervisor. If the waiting task can begin without impacting safety or quality, I would start on that while finishing key parts of my current task.
If you notice one of your team members is struggling with a task, what would you do?
How to Answer
- 1
Assess the situation quickly to understand the issue
- 2
Approach the team member kindly and ask if they need help
- 3
Listen carefully to their concerns and difficulties
- 4
Offer specific assistance or suggest solutions
- 5
Encourage teamwork to solve the problem together
Example Answers
I would first check in with the team member to see what specific challenges they are facing. Then, I would offer to help them directly with the task, providing guidance or sharing resources that may assist them.
Imagine a customer is unhappy about a delay. How would you handle that situation?
How to Answer
- 1
Acknowledge the customer's feelings and listen actively
- 2
Provide a clear explanation of the delay without making excuses
- 3
Offer a solution or compensation if possible
- 4
Keep your tone calm and professional throughout the interaction
- 5
Follow up with the customer after the issue is resolved
Example Answers
I would start by acknowledging the customer's frustration and listen to their concerns. Then, I would explain the reason for the delay clearly. I would also offer to provide a discount on their next service as a goodwill gesture.
Behavioral Interview Questions
Can you give an example of a time when you worked as part of a team to complete a project?
How to Answer
- 1
Select a specific project or task with a team involvement
- 2
Describe your role and contributions to the team
- 3
Highlight any challenges the team faced and how you overcame them
- 4
Emphasize the outcome and what you learned from the experience
- 5
Keep it concise and focused on teamwork dynamics
Example Answers
In my last job, I was part of a team tasked with overhauling maintenance procedures. My role was to coordinate between different departments and ensure everyone was on the same page. We faced a delay due to equipment availability, but I organized a flexible schedule to maximize our time. The project was completed ahead of the deadline, and I learned the importance of communication in a team setting.
Describe a conflict you faced with a colleague and how you resolved it.
How to Answer
- 1
Focus on a specific situation rather than a general overview
- 2
Describe the conflict clearly and the emotions involved
- 3
Explain the steps you took to address the conflict
- 4
Highlight the resolution and any lessons learned
- 5
Keep it professional and stick to work-related issues
Example Answers
In one instance, I disagreed with a colleague about the best approach to a maintenance procedure. I scheduled a meeting with them to discuss our viewpoints. We both presented our arguments, and I listened to their perspective. We agreed to consult our supervisor for an additional opinion, which led to a collaborative decision that improved the process.
Don't Just Read Station Mechanic Questions - Practice Answering Them!
Reading helps, but actual practice is what gets you hired. Our AI feedback system helps you improve your Station Mechanic interview answers in real-time.
Personalized feedback
Unlimited practice
Used by hundreds of successful candidates
Tell me about a time you faced a significant challenge while working on equipment. How did you handle it?
How to Answer
- 1
Choose a specific challenge related to equipment maintenance or repair.
- 2
Explain the steps you took to diagnose the issue.
- 3
Highlight your problem-solving skills and any teamwork involved.
- 4
Describe the outcome and what you learned from the experience.
- 5
Keep it brief and focus on your contributions to resolving the challenge.
Example Answers
While working on a locomotive, I faced a significant challenge when the engine failed to start. I methodically checked the battery and wiring and discovered a short circuit. I collaborated with a colleague to isolate the issue, and we replaced the damaged wiring. The engine started successfully, and I learned the importance of systematic troubleshooting.
Have you ever had to lead a project or a group? What was your approach?
How to Answer
- 1
Describe a specific project you led.
- 2
Explain your role and responsibilities clearly.
- 3
Mention how you organized the team and delegated tasks.
- 4
Highlight any challenges you faced and how you overcame them.
- 5
Conclude with the results of the project and what you learned.
Example Answers
I led a project to overhaul the maintenance schedule for our department. I organized a team meeting to gather input, assigned tasks based on each member's strengths, and set clear deadlines. We faced challenges with resource availability, but I negotiated additional support with management. The project resulted in a 20% reduction in downtime and improved team efficiency.
Describe a situation where you had to quickly adapt to a change in work procedures or technologies.
How to Answer
- 1
Identify a specific change you faced in your work environment
- 2
Explain the steps you took to adapt to the new procedures or technology
- 3
Mention any challenges you encountered and how you overcame them
- 4
Highlight the positive outcome of your adaptability
- 5
Connect this experience to your role as a Station Mechanic
Example Answers
At my previous job, we switched to a new software for tracking maintenance schedules. I took the initiative to attend training sessions and also practiced using the software after hours. Initially, I found it challenging to locate specific reports quickly but I created a guide for my team. This not only improved my own efficiency but helped the entire team adapt faster, resulting in a smoother transition and fewer delays in maintenance work.
Give an example of a time when your attention to detail made a difference in your work outcomes.
How to Answer
- 1
Choose a specific instance where detail was crucial to success.
- 2
Explain what the task was and the potential risks of overlooking details.
- 3
Describe the steps you took to ensure accuracy.
- 4
Highlight the positive outcome that resulted from your attention to detail.
- 5
Relate the experience to how it applies to the Station Mechanic role.
Example Answers
In my previous job as a mechanic, I noticed a small leak in a hydraulic line during a routine inspection. I double-checked the entire system to ensure there were no other issues. This attention to detail prevented a major failure during testing, saving the company time and money. It reinforced my commitment to thorough inspections.
Have you ever trained someone in mechanical operations? What method did you find most effective?
How to Answer
- 1
Share a specific instance when you trained someone.
- 2
Describe the method you used for training clearly.
- 3
Explain why that method was effective.
- 4
Include any measurable results or feedback received.
- 5
Highlight your adaptability in training styles if needed.
Example Answers
I trained a new technician using a hands-on approach, guiding them through real tasks while explaining each step. This method was effective as they learned by doing and reported feeling confident after our sessions.
Have you ever had to explain repairs or delays to a customer? How did you handle it?
How to Answer
- 1
Stay calm and professional during the interaction.
- 2
Clearly explain the situation without using technical jargon.
- 3
Offer an honest timeline for repairs and any alternatives available.
- 4
Acknowledge the customer's inconvenience and express empathy.
- 5
Follow up to ensure customer satisfaction after the explanation.
Example Answers
Yes, I once had to explain a delay in a repair for a customer's vehicle. I calmly explained the issue, using simple terms to ensure they understood. I provided a timeline for when the repairs would be completed and offered a loaner vehicle in the meantime. The customer appreciated my honesty and my willingness to help.
Describe a time when you went above and beyond your job requirements. What motivated you?
How to Answer
- 1
Think of a specific instance where you exceeded expectations.
- 2
Explain the context and what prompted you to take extra initiative.
- 3
Focus on the impact of your actions on the team or project.
- 4
Mention any skills or qualities you utilized to achieve this.
- 5
Conclude with how this experience shaped your approach to work.
Example Answers
In my last role, we had a critical deadline for maintenance completion. I coordinated with our suppliers to expedite parts delivery, which allowed us to finish the job two days ahead of schedule. I was motivated by the team's reliance on timely repairs and the desire to exceed our client's expectations.
Describe a time when you took the initiative to improve a work process.
How to Answer
- 1
Identify a specific work process you improved.
- 2
Outline the problem you noticed in that process.
- 3
Explain the steps you took to implement the change.
- 4
Share the outcome or benefits of your initiative.
- 5
Keep your example relevant to mechanical tasks or teamwork.
Example Answers
In my previous role, I noticed that our routine equipment checks were taking too long. I proposed a new checklist format that allowed us to identify issues faster. After implementing it, we reduced check times by 30%.
Don't Just Read Station Mechanic Questions - Practice Answering Them!
Reading helps, but actual practice is what gets you hired. Our AI feedback system helps you improve your Station Mechanic interview answers in real-time.
Personalized feedback
Unlimited practice
Used by hundreds of successful candidates
Technical Interview Questions
What are the key maintenance practices you follow for ensuring the longevity of machinery in a station?
How to Answer
- 1
Emphasize the importance of preventive maintenance schedules.
- 2
Mention the use of regular inspections to detect issues early.
- 3
Include your experience with lubrication and cleaning to reduce wear.
- 4
Discuss documentation of maintenance activities for accountability.
- 5
Share any experience with training staff on proper machine use.
Example Answers
I follow a strict preventive maintenance schedule, performing regular inspections and servicing machinery to catch potential issues early. I also ensure that lubrication and cleaning are done consistently to minimize wear and tear.
Can you explain how you would conduct a troubleshooting process for a malfunctioning piece of equipment?
How to Answer
- 1
Identify the symptoms of the malfunction clearly.
- 2
Gather relevant background information about the equipment.
- 3
Use systematic steps to isolate potential causes.
- 4
Test one hypothesis at a time to determine the issue.
- 5
Document your findings and the steps you took.
Example Answers
First, I would identify and note the symptoms of the malfunction. Then, I would gather any manuals or past maintenance records. Next, I would systematically test each potential cause, like checking electrical connections or fluid levels, isolating one issue at a time until I find the culprit. Finally, I would document everything to assist in future troubleshooting.
Don't Just Read Station Mechanic Questions - Practice Answering Them!
Reading helps, but actual practice is what gets you hired. Our AI feedback system helps you improve your Station Mechanic interview answers in real-time.
Personalized feedback
Unlimited practice
Used by hundreds of successful candidates
What safety protocols do you follow while working on heavy machinery?
How to Answer
- 1
Always wear personal protective equipment including gloves and safety glasses.
- 2
Conduct a thorough inspection of the machinery before starting work.
- 3
Follow lockout/tagout procedures to ensure equipment is safely shut down.
- 4
Keep the work area clean and free of hazards to prevent accidents.
- 5
Stay informed about the specific safety regulations and protocols for the equipment you are operating.
Example Answers
I always wear gloves and safety glasses when working. I begin by inspecting the machinery for any issues, then I follow proper lockout procedures, and make sure the area is clean to prevent any hazards.
What tools and techniques do you use for diagnosing engine problems?
How to Answer
- 1
Mention specific diagnostic tools you are familiar with, like OBD-II scanners
- 2
Explain how you interpret diagnostic trouble codes
- 3
Discuss visual inspections for signs of wear or damage
- 4
Include any techniques for testing engine performance, like compression testing
- 5
Highlight your experience with specific engine systems, such as fuel or ignition
Example Answers
I typically use an OBD-II scanner to read diagnostic codes, and then I interpret those codes to pinpoint issues. I also perform visual inspections to check for leaks and damaged components.
Can you walk me through your process for performing a major repair on station equipment?
How to Answer
- 1
Start with initial assessment of the equipment to identify issues.
- 2
Develop a clear repair plan outlining necessary tools and parts.
- 3
Communicate with the team about the repair timeline and safety protocols.
- 4
Execute the repair systematically, following the plan step-by-step.
- 5
Test the equipment after repair to ensure it meets operational standards.
Example Answers
First, I assess the equipment to pinpoint the problem. Then, I create a repair plan, noting what tools and parts I need. I inform my team about the repair process and any safety measures. I methodically carry out the repair, following the steps in my plan, and finally, I test the equipment to confirm it operates correctly.
What different types of engines and systems are you familiar with, and how have you worked with them?
How to Answer
- 1
List specific engine types you have experience with such as diesel, turbo, or electric.
- 2
Mention relevant systems like fuel management, hydraulic systems, or electrical systems.
- 3
Include practical examples of your hands-on experience with these engines and systems.
- 4
Discuss any certifications or training related to engine maintenance or repair.
- 5
Highlight problem-solving experiences you’ve had with engines or systems.
Example Answers
I have worked with diesel engines and hydraulic systems for over 5 years in my previous role at a transit authority. I performed routine maintenance, troubleshooting, and repairs to keep the fleet operational.
How do you analyze the root cause of a recurring issue in machinery?
How to Answer
- 1
Gather data on the occurrences of the issue over time.
- 2
Use the 5 Whys technique to drill down to the root cause.
- 3
Test potential causes one at a time to identify the true issue.
- 4
Consult with colleagues for different perspectives and insights.
- 5
Document findings and solutions for future reference.
Example Answers
I start by collecting data on when the issue occurs, using the 5 Whys method to trace back the symptoms to their source. Then, I test each potential cause systematically. Collaboration with the team helps to ensure nothing is overlooked.
What regulations do you consider when maintaining equipment in a station?
How to Answer
- 1
Identify key industry regulations relevant to station maintenance.
- 2
Discuss safety standards like OSHA or EPA guidelines.
- 3
Mention any specific equipment regulations, such as manufacturer recommendations.
- 4
Highlight the importance of keeping logs and documentation for compliance.
- 5
Emphasize the need for ongoing training and awareness of regulatory updates.
Example Answers
I consider OSHA regulations for workplace safety and ensure that all equipment is maintained according to manufacturer specifications. I also keep detailed logs of maintenance activities for compliance.
What experience do you have with upgrading older equipment or systems?
How to Answer
- 1
Identify specific projects you worked on involving upgrades.
- 2
Highlight the skills and tools you used during the upgrade.
- 3
Mention any challenges you faced and how you overcame them.
- 4
Emphasize the impact of the upgrades on performance or efficiency.
- 5
Show your understanding of safety and compliance during upgrades.
Example Answers
In my previous position, I led a project to upgrade an outdated conveyor system. I used CAD software to design new layouts and coordinated with the team to implement the changes while maintaining safety protocols.
What methods do you use for preventive maintenance planning?
How to Answer
- 1
Identify key equipment and their maintenance needs
- 2
Use a maintenance management system for scheduling
- 3
Incorporate manufacturer recommendations and industry standards
- 4
Review maintenance history for trends and recurring issues
- 5
Plan maintenance during off-peak hours to reduce downtime
Example Answers
I prioritize equipment based on their criticality, then schedule regular maintenance using our CMMS to ensure tasks are completed on time, following manufacturer guidelines.
Don't Just Read Station Mechanic Questions - Practice Answering Them!
Reading helps, but actual practice is what gets you hired. Our AI feedback system helps you improve your Station Mechanic interview answers in real-time.
Personalized feedback
Unlimited practice
Used by hundreds of successful candidates
What special certifications do you hold that are relevant to this position?
How to Answer
- 1
Identify all relevant certifications specific to mechanic roles.
- 2
Mention any industry-recognized licenses or certificates.
- 3
Highlight safety training certifications, as safety is crucial.
- 4
If you have recent training, emphasize the relevance to current technologies.
- 5
Be prepared to explain how your certifications enhance your skills.
Example Answers
I hold an FAA Airframe and Powerplant certification, which directly relates to this position. Additionally, I am certified in OSHA safety standards, ensuring compliance with safety regulations.
How do you utilize technical manuals and schematics in your work?
How to Answer
- 1
Reference manuals for equipment specifications and troubleshooting procedures
- 2
Study schematics to understand system layouts and connections
- 3
Use diagrams to identify components and their functions during repairs
- 4
Keep manuals accessible for quick reference during maintenance tasks
- 5
Stay updated with revisions to ensure you have the latest information
Example Answers
I regularly refer to technical manuals to troubleshoot issues with machinery. For instance, when diagnosing a hydraulic system problem, I consult the manual for the specifications and common faults. I also study the schematics to visualize how components interact, ensuring I address the right parts promptly.
Station Mechanic Position Details
Related Positions
Ace Your Next Interview!
Practice with AI feedback & get hired faster
Personalized feedback
Used by hundreds of successful candidates
Ace Your Next Interview!
Practice with AI feedback & get hired faster
Personalized feedback
Used by hundreds of successful candidates