Top 30 Stower Interview Questions and Answers [Updated 2025]
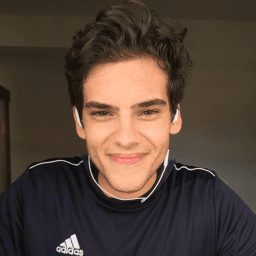
Andre Mendes
•
March 30, 2025
Preparing for a Stower job interview can be daunting, but we're here to help you shine. In this post, we've compiled a list of the most common interview questions for the Stower role, complete with example answers and practical tips to help you respond confidently and effectively. Whether you're a seasoned professional or new to the field, this guide will equip you with the insights needed to impress your interviewer and secure the job.
Download Stower Interview Questions in PDF
To make your preparation even more convenient, we've compiled all these top Stowerinterview questions and answers into a handy PDF.
Click the button below to download the PDF and have easy access to these essential questions anytime, anywhere:
List of Stower Interview Questions
Behavioral Interview Questions
Can you describe a time when you worked as part of a team? What was your role, and what was the outcome?
How to Answer
- 1
Choose a specific project or task.
- 2
Clearly define your role and responsibilities.
- 3
Highlight collaboration with team members.
- 4
Mention the challenges faced and how they were overcome.
- 5
Conclude with the positive outcome and what you learned.
Example Answers
In my last job at a warehouse, I was part of a team responsible for organizing inventory. My role involved sorting items and labeling shelves. We faced a tight deadline, but by communicating and dividing tasks effectively, we completed the project two days early. This taught me the importance of teamwork and clear communication.
Tell me about a time you faced a challenge with maintaining accuracy in your work. How did you handle it?
How to Answer
- 1
Identify a specific challenge you faced related to accuracy.
- 2
Explain the impact of the accuracy issue on your work.
- 3
Describe the steps you took to resolve the issue.
- 4
Highlight any tools or methods you used to improve accuracy.
- 5
Conclude with the positive outcome and any lessons learned.
Example Answers
In my previous role as a warehouse assistant, I miscounted inventory items during a stock check. I realized the error when discrepancies showed in our reports. I double-checked the counts, used a checklist to ensure all items were accounted for, and confirmed with my team members. This led to accurate inventory records and smoother operations. I learned the importance of cross-verifying important tasks.
Don't Just Read Stower Questions - Practice Answering Them!
Reading helps, but actual practice is what gets you hired. Our AI feedback system helps you improve your Stower interview answers in real-time.
Personalized feedback
Unlimited practice
Used by hundreds of successful candidates
Describe a situation where you encountered a significant problem while stowing items. How did you resolve it?
How to Answer
- 1
Identify a specific problem you faced while stowing.
- 2
Explain the impact of the problem on your work or team.
- 3
Detail the steps you took to resolve the issue.
- 4
Mention any tools or methods you used to solve the problem.
- 5
Conclude with the positive outcome and what you learned.
Example Answers
During a busy shift, I discovered that several items were incorrectly labeled for stowing. This caused delays for my team. I quickly double-checked the inventory, corrected the labels, and reorganized the items. This streamlined the stowing process and made sure everyone had accurate information. My approach reduced our stowing time by 15%.
Provide an example of how you prioritized your tasks during a particularly busy shift.
How to Answer
- 1
Identify the key tasks that needed immediate attention.
- 2
Explain how you assessed task importance and urgency.
- 3
Discuss any tools or methods used to organize tasks.
- 4
Mention how communication with teammates helped.
- 5
Conclude with the outcome of your prioritization.
Example Answers
During a busy shift, I noticed the incoming orders were piling up. I assessed that fulfilling the next three highest priority orders would keep our delivery times on track. I used a checklist to organize my tasks and communicated with my team to delegate some prep work. As a result, we reduced wait times and kept customer satisfaction high.
Have you ever had to adapt to a change in process or technology? How did you manage that change?
How to Answer
- 1
Describe the specific change you faced.
- 2
Explain how you reacted to the change initially.
- 3
Mention any steps you took to learn the new process or technology.
- 4
Highlight the outcome or improvement after adapting.
- 5
Emphasize your willingness to embrace change in the future.
Example Answers
In my last job, we switched to a new inventory management system. At first, I was unsure and struggled to navigate it. I then took the initiative to attend training sessions and practiced using the system daily. As a result, I became proficient and was able to help my team adapt as well.
What keeps you motivated during repetitive tasks like stowing inventory?
How to Answer
- 1
Focus on the bigger picture of teamwork and efficiency
- 2
Set personal goals to track progress and stay engaged
- 3
Break tasks into smaller segments for a sense of accomplishment
- 4
Use music or podcasts to make the work environment enjoyable
- 5
Remember the positive impact on customers and operations
Example Answers
I stay motivated by thinking about how my work contributes to the overall efficiency of the team. Setting small goals helps me track my progress and keeps me engaged.
Can you provide an example of a time you took the initiative to improve a work process?
How to Answer
- 1
Think of a specific situation where you saw a problem.
- 2
Describe the action you took to address the issue.
- 3
Explain the outcome of your action, focusing on its impact.
- 4
Use quantifiable results where possible to highlight success.
- 5
Keep it concise and relevant to the Stower position.
Example Answers
At my last job, I noticed that inventory checks were taking too long. I suggested using a new scanning system that reduced the time from 3 hours to 1 hour per inventory session, helping the team stay on schedule.
Have you ever received constructive criticism about your stowing techniques? How did you react?
How to Answer
- 1
Acknowledge the feedback and show appreciation for it
- 2
Explain the specific criticism you received
- 3
Describe the actions you took to improve your techniques
- 4
Mention the positive outcomes from implementing the changes
- 5
Emphasize your openness to ongoing feedback and learning
Example Answers
Yes, I received feedback about my stowing techniques being inefficient. I appreciated the input and took time to analyze the suggestions given. I adjusted my approach by organizing items according to size and shape, which improved my speed. As a result, my stowing times decreased significantly, and I felt more confident in my work.
Describe a time when you led a group to achieve a common goal in your workplace.
How to Answer
- 1
Choose a specific project or task you led.
- 2
Highlight your role and responsibilities clearly.
- 3
Explain the goal and the outcome achieved together.
- 4
Mention any challenges faced and how you overcame them.
- 5
Include what you learned and how it helped the team.
Example Answers
In my previous role, I led a team to improve our inventory management process. Our goal was to reduce stock discrepancies by 20% within three months. I organized weekly meetings, delegated tasks based on strengths, and implemented a new tracking system. We faced resistance to change initially but overcame that with clear communication and training, ultimately achieving a 25% reduction in discrepancies. This experience taught me the value of teamwork and adaptability.
Don't Just Read Stower Questions - Practice Answering Them!
Reading helps, but actual practice is what gets you hired. Our AI feedback system helps you improve your Stower interview answers in real-time.
Personalized feedback
Unlimited practice
Used by hundreds of successful candidates
Technical Interview Questions
What inventory management systems or tools are you familiar with, and how have you used them in your previous roles?
How to Answer
- 1
Identify specific inventory systems you have used, like WMS or ERP software.
- 2
Highlight how you used these systems to improve efficiency or accuracy.
- 3
Mention any relevant metrics or outcomes from your experience.
- 4
Be prepared to describe a challenge you faced and how the system helped address it.
- 5
Connect your experience with the job requirements if possible.
Example Answers
I have experience with SAP and Oracle Inventory Management. In my last role, I used SAP to track inventory levels, which helped reduce stock discrepancies by 20%.
Can you explain the proper use of the equipment necessary for stowing items efficiently?
How to Answer
- 1
Understand the layout of the stowing area to maximize space usage
- 2
Use equipment like hand carts or pallet jacks for heavy items
- 3
Ensure items are scanned and labeled correctly before stowing
- 4
Prioritize storing frequently accessed items in easily reachable locations
- 5
Regularly maintain equipment to ensure it works effectively
Example Answers
In stowing efficiently, I ensure to know the area layout and use hand carts for larger items. I always scan and label items before storage to keep track and prioritize high-demand items for easy access.
Don't Just Read Stower Questions - Practice Answering Them!
Reading helps, but actual practice is what gets you hired. Our AI feedback system helps you improve your Stower interview answers in real-time.
Personalized feedback
Unlimited practice
Used by hundreds of successful candidates
What safety protocols do you follow while operating machinery and handling inventory?
How to Answer
- 1
Always wear the required personal protective equipment such as gloves and safety glasses
- 2
Conduct a pre-operation check to ensure that all machinery is functioning properly
- 3
Maintain a clear workspace and ensure aisles are free of obstacles
- 4
Follow the manufacturer's operating guidelines and safety instructions
- 5
Report any unsafe conditions or incidents immediately to a supervisor
Example Answers
I always wear gloves and safety glasses while operating machinery and check everything before use to make sure it's safe to operate.
How do you ensure that items are correctly categorized and stored for easy retrieval?
How to Answer
- 1
Follow a consistent labeling system for all items
- 2
Utilize bins and shelves that are clearly marked
- 3
Regularly review and reorganize inventory as needed
- 4
Use a digital tracking system to log item locations
- 5
Implement a standard operating procedure for new items
Example Answers
I ensure items are categorized by consistently labeling each bin and shelf, making it easy to find what I need quickly.
What methods do you employ to maximize efficiency while stowing products?
How to Answer
- 1
Identify the most efficient storage locations for items based on size and weight
- 2
Use clear labeling to quickly locate items and reduce search time
- 3
Employ a methodical approach to stowing, such as grouping similar items together
- 4
Maintain a consistent flow by organizing your work area and minimizing distractions
- 5
Regularly review and adjust stowing processes based on efficiency metrics
Example Answers
I maximize efficiency by categorizing items by size and placing them in the optimal storage locations. This reduces the time spent searching for products.
What time-tracking methods do you use to ensure completion of your stowing tasks?
How to Answer
- 1
Use a personal checklist to monitor your daily stowing tasks.
- 2
Set specific time limits for each stowing operation to maintain pace.
- 3
Utilize timers or stopwatches to track the duration of your tasks.
- 4
Regularly review your efficiency and adjust methods as needed.
- 5
Prioritize tasks based on urgency and importance to streamline your workflow.
Example Answers
I create a checklist for my stowing tasks and set a timer for each one to keep a steady pace.
What are the quality control measures you would implement while stowing items?
How to Answer
- 1
Ensure each item is scanned and matches its description before stowing.
- 2
Organize items by category and size for easier retrieval and inventory management.
- 3
Regularly check for damage or discrepancies in stock and report immediately.
- 4
Follow a designated stowing procedure to maintain consistency and accuracy.
- 5
Perform periodic audits to ensure items are correctly stowed and accounted for.
Example Answers
I would scan each item to verify it matches its description before placing it in the stow area, ensuring that we avoid errors.
What types of inventory have you previously worked with, and how did that impact your stowing process?
How to Answer
- 1
Identify specific types of inventory you have handled, like large items or fragile goods.
- 2
Explain how each type required different stowing techniques or organization.
- 3
Mention any tools or systems used for stowing that were influenced by the inventory type.
- 4
Highlight the importance of efficiency and safety in stowing different inventories.
- 5
Connect your experience to potential benefits for their operations.
Example Answers
I have worked with both large home appliances and fragile electronics. For large items, I ensured I utilized available vertical space and created clear paths for easy access. For fragile goods, I used extra padding and careful placement to avoid damage.
Situational Interview Questions
If you were to receive multiple urgent stowing requests simultaneously, how would you decide which to tackle first?
How to Answer
- 1
Prioritize based on deadline urgency and item importance
- 2
Assess the impact of each request on operations or customer experience
- 3
Communicate with the team about workload and status
- 4
Stay organized by listing requests and sorting them clearly
- 5
Remain flexible to adjust priorities as new information arises
Example Answers
I would quickly list the requests and assess their urgency and importance. Then, I would communicate with my team to ensure we are all aligned on priorities before starting on the most critical tasks.
How would you handle a disagreement with a coworker about the correct storage location for an item?
How to Answer
- 1
Stay calm and approach the coworker with an open mind
- 2
Listen to their perspective and ask questions for clarity
- 3
Share your reason for your storage suggestion based on policy or efficiency
- 4
Suggest checking company guidelines or asking a supervisor if needed
- 5
Aim for a collaborative solution that respects both viewpoints
Example Answers
I would first talk to my coworker calmly and ask them to explain their reasoning. After listening, I would share my perspective based on our storage policy. If we're still unsure, I would suggest we check with a supervisor for clarification.
Don't Just Read Stower Questions - Practice Answering Them!
Reading helps, but actual practice is what gets you hired. Our AI feedback system helps you improve your Stower interview answers in real-time.
Personalized feedback
Unlimited practice
Used by hundreds of successful candidates
If you realized that you stowed an item incorrectly, what steps would you take to correct the mistake?
How to Answer
- 1
Quickly assess the item and its correct location
- 2
Notify a supervisor if necessary, especially for heavy or hazardous items
- 3
Carefully remove the item, ensuring it doesn't disrupt other stowed items
- 4
Place the item in the correct location following safety protocols
- 5
Double-check the surrounding area to ensure no new mistakes were made
Example Answers
If I found I stowed an item incorrectly, I would first verify its correct location. Then, I'd notify my supervisor if the item was heavy. After that, I would safely remove the item and place it in the right spot, checking nearby items to ensure everything is organized properly.
How would you respond if a team member asked you to assist them with a stowing situation they are struggling with?
How to Answer
- 1
Stay calm and listen to the team member's issue carefully.
- 2
Ask clarifying questions to fully understand their challenge.
- 3
Offer to demonstrate a stowing technique or process.
- 4
Encourage them to try it themselves with your guidance.
- 5
Follow up later to ensure they feel confident with the process.
Example Answers
I would first listen to my teammate's specific issue to understand the details. Then, I would demonstrate the proper technique and encourage them to try it while I offer support.
Imagine you notice a consistent inefficiency in the stowing process. How would you approach suggesting changes?
How to Answer
- 1
Identify specific inefficiencies with clear examples
- 2
Gather data to support your observations
- 3
Consult with team members for their insights
- 4
Propose a clear, actionable solution
- 5
Suggest a trial period to evaluate the changes
Example Answers
I noticed that items often get misplaced leading to longer search times. I collected data showing a 20% increase in stow time. I talked to my colleagues who shared their struggles. I suggest introducing color-coded bins for easier identification. We could try this for a month and see if it reduces our time.
If you were falling behind on your stow quotas, what strategies would you implement to catch up?
How to Answer
- 1
Prioritize your tasks by focusing on high-volume items first
- 2
Minimize distractions by creating a quiet workspace or using headphones
- 3
Utilize efficient stowing techniques like stacking or grouping items
- 4
Take short breaks to maintain energy and avoid burnout
- 5
Seek help from teammates if you’re struggling with specific categories
Example Answers
I would start by prioritizing the high-volume items that need to be stowed first, then try to work in a distraction-free area, making sure to take short breaks for energy.
If a team member was not contributing to the stowing process effectively, how would you address the situation?
How to Answer
- 1
Observe the team member's workflow and identify specific issues
- 2
Approach them privately and express your observations without blame
- 3
Ask if they need help or resources to improve their performance
- 4
Encourage open communication and offer your support
- 5
Suggest follow-up meetings to monitor progress and provide feedback
Example Answers
I would first observe the individual's workflow to identify any specific issues. Then, I'd approach them privately and share my observations in a constructive manner. I would ask if they needed any help or resources, emphasizing that I am here to support them.
What would you do if you witnessed a safety violation during the stowing process?
How to Answer
- 1
Stay calm and assess the situation for immediate danger.
- 2
Follow company policies for reporting safety issues.
- 3
Address the person involved if it's safe and appropriate.
- 4
Document the violation accurately with details.
- 5
Notify a supervisor or safety officer as soon as possible.
Example Answers
If I saw a safety violation, I would first ensure that there was no immediate danger. Then I would follow company protocol by reporting it to my supervisor and providing them with all the necessary details.
If you need to stow a large shipment quickly, what steps would you take to organize the workload?
How to Answer
- 1
Assess the size and type of items to be stowed
- 2
Prioritize items based on weight and size for efficient stowing
- 3
Divide the workload among team members if possible
- 4
Create a clear plan for storage locations to maximize space
- 5
Communicate effectively with the team to ensure everyone understands their tasks
Example Answers
First, I would assess the shipment to understand the size and types of items. Then, I would prioritize stowing heavier items first to ensure balance. If I have a team, I would divide the workload based on each person's strengths and monitor the plan for optimized storage. Finally, I would keep communication open to make quick adjustments as needed.
How would you handle using a new stowing technology that you're not familiar with?
How to Answer
- 1
Research the new technology beforehand to understand its basic functions
- 2
Ask for training or guidance from a supervisor or experienced coworker
- 3
Practice using the technology in a safe environment before full implementation
- 4
Stay calm and patient, recognizing that learning takes time
- 5
Document any challenges or questions to address later
Example Answers
I would start by researching the new technology to grasp its main features and benefits. Then, I would reach out to a supervisor or a knowledgeable colleague for training. Before using it in my regular stowing tasks, I would practice with the system to build my confidence and skills.
Don't Just Read Stower Questions - Practice Answering Them!
Reading helps, but actual practice is what gets you hired. Our AI feedback system helps you improve your Stower interview answers in real-time.
Personalized feedback
Unlimited practice
Used by hundreds of successful candidates
If your supervisor observed that your stowing speed was below expectations, how would you respond?
How to Answer
- 1
Acknowledge the feedback positively.
- 2
Ask for specific areas of improvement.
- 3
Share any challenges you faced impacting your speed.
- 4
Express your commitment to improve.
- 5
Suggest ways to enhance your efficiency.
Example Answers
I appreciate the feedback and understand the importance of stowing speed. Could you share which specific areas I should focus on? I faced some challenges with the new layout, but I'm committed to improving and will track my progress.
Ace Your Next Interview!
Practice with AI feedback & get hired faster
Personalized feedback
Used by hundreds of successful candidates
Ace Your Next Interview!
Practice with AI feedback & get hired faster
Personalized feedback
Used by hundreds of successful candidates