Top 29 Supplier Quality Engineer Interview Questions and Answers [Updated 2025]
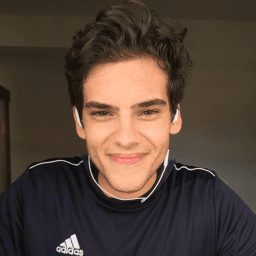
Andre Mendes
•
March 30, 2025
Are you preparing for a Supplier Quality Engineer interview and want to make a lasting impression? Look no further! This blog post covers the most common interview questions for the Supplier Quality Engineer role, complete with example answers and expert tips to help you respond effectively. Dive in to boost your confidence and equip yourself with the insights needed to ace your interview.
Download Supplier Quality Engineer Interview Questions in PDF
To make your preparation even more convenient, we've compiled all these top Supplier Quality Engineerinterview questions and answers into a handy PDF.
Click the button below to download the PDF and have easy access to these essential questions anytime, anywhere:
List of Supplier Quality Engineer Interview Questions
Behavioral Interview Questions
Can you describe a time when you found a defect in a supplier's product and how you handled it?
How to Answer
- 1
Identify the specific defect and its impact on your project or product.
- 2
Explain the steps you took to investigate and confirm the defect.
- 3
Discuss how you communicated the issue to the supplier and what response you received.
- 4
Mention any corrective actions taken and how you ensured follow-up.
- 5
Reflect on the outcome and what you learned from the experience.
Example Answers
In my last role, I discovered that a batch of circuit boards from a supplier failed our stress tests. I collected data and analysis results to confirm the defect. I immediately contacted the supplier, shared our findings, and we arranged for a joint investigation. The supplier acknowledged the issue, and we implemented a stricter quality inspection process for future deliveries. This not only resolved the immediate issue but improved overall product reliability.
Tell me about a situation where you had to collaborate with a supplier to improve quality. What was your role?
How to Answer
- 1
Select a specific project or incident where you collaborated with a supplier.
- 2
Describe your role clearly – were you leading the effort or supporting it?
- 3
Focus on the outcome – how did your collaboration improve quality?
- 4
Mention any metrics or data that highlight the improvement.
- 5
Discuss lessons learned that you can apply in future collaborations.
Example Answers
In a project to reduce defects in our components, I led a cross-functional team working with a key supplier. We analyzed failure data together and identified process adjustments that decreased defects by 30% within three months.
Don't Just Read Supplier Quality Engineer Questions - Practice Answering Them!
Reading helps, but actual practice is what gets you hired. Our AI feedback system helps you improve your Supplier Quality Engineer interview answers in real-time.
Personalized feedback
Unlimited practice
Used by hundreds of successful candidates
Describe a difficult conversation you had with a supplier regarding quality issues. How did you approach it?
How to Answer
- 1
Start by describing the situation and the specific quality issue.
- 2
Explain your preparation before the conversation to gather facts.
- 3
Focus on maintaining a professional and collaborative tone.
- 4
Discuss the solution-oriented approach you took during the dialogue.
- 5
Highlight the outcome and any follow-up actions taken.
Example Answers
I faced a situation where a supplier's parts had consistent defects. Before addressing it, I collected data on the defect rates and arranged a meeting. I approached the conversation calmly, sharing the data and expressing my concern. Together, we identified the root cause and created an action plan for improvement, which resulted in a 30% reduction in defects.
Explain a time when you had to lead an initiative to enhance supplier quality processes. What challenges did you face?
How to Answer
- 1
Start with a brief overview of the initiative and its goal.
- 2
Mention specific metrics or standards you aimed to improve.
- 3
Describe the challenges you encountered and how you addressed them.
- 4
Highlight the outcomes and any improvements in supplier quality.
- 5
Conclude with lessons learned or next steps for sustaining quality.
Example Answers
I led an initiative to reduce defects in a critical supplier's production line. Our goal was to decrease defect rates by 20%. We faced resistance from the supplier’s management, as they were unsure about the changes. I held workshops to clarify benefits, which helped ease concerns. As a result, we improved defect rates by 25% within six months, enhancing overall quality.
Have you ever had to adapt your approach to quality management due to unforeseen circumstances? What did you do?
How to Answer
- 1
Identify a specific situation where you faced unexpected challenges.
- 2
Explain the key changes you made to your quality management approach.
- 3
Highlight the positive outcomes of your adaptations.
- 4
Use metrics or results if possible to showcase effectiveness.
- 5
Keep the focus on your role and contributions in the situation.
Example Answers
In a previous project, a supplier faced an unexpected shutdown that impacted our timelines. I quickly switched to a dual sourcing strategy, assessing alternative suppliers. This not only mitigated delays but also improved our contingency plans for future disruptions.
Describe how you measured the impact of a quality improvement initiative you implemented with a supplier.
How to Answer
- 1
Identify the key metrics you used to measure quality improvement.
- 2
Explain the baseline data before the initiative and the results after implementation.
- 3
Discuss the tools or methodologies employed to analyze the data.
- 4
Include how the findings influenced future supplier relationships.
- 5
Highlight any cross-functional collaboration that supported the initiative.
Example Answers
We established a baseline by tracking defect rates at our supplier before the initiative. After implementing a quality training program, we measured a 30% reduction in defects over three months, confirming the initiative's effectiveness.
Can you provide an example of how you have aligned supplier quality objectives with customer expectations?
How to Answer
- 1
Identify a specific customer requirement and corresponding supplier quality goal.
- 2
Explain the communication process with the supplier about these expectations.
- 3
Describe how you monitored supplier performance against those objectives.
- 4
Share an example of an improvement made based on feedback from either the customer or the supplier.
- 5
Highlight the positive impact of this alignment on customer satisfaction.
Example Answers
In my previous role, we had a customer that required a specific defect rate of less than 1%. I discussed this goal directly with the supplier and implemented monthly performance reviews to ensure alignment. We identified areas for improvement, and by making adjustments to their processes, we achieved consistent compliance, which led to increased customer satisfaction scores.
Have you ever had to train a supplier on quality expectations? What approach did you take?
How to Answer
- 1
Identify the specific quality expectations that were needed.
- 2
Explain how you assessed the supplier's current capabilities.
- 3
Detail the training methods you used, such as workshops or one-on-one sessions.
- 4
Discuss any materials or resources you provided during the training.
- 5
Mention how you followed up to ensure compliance and understanding.
Example Answers
Yes, I trained a supplier on our quality expectations by first assessing their current processes. I conducted a workshop where I outlined our standards and provided examples of acceptable work. I also shared training materials for their reference and followed up a month later to address any questions.
Tell me about a time when your analysis of supplier data led to a significant decision or change.
How to Answer
- 1
Choose a specific example that showcases your analytical skills.
- 2
Highlight the data analysis tools or methods you used.
- 3
Explain the impact of your findings on the supplier or organization.
- 4
Discuss any follow-up actions taken due to your analysis.
- 5
Keep it concise and focused on your role.
Example Answers
At my previous job, I noticed a trend in supplier defect rates using statistical process control. By presenting this data in a clear report, we switched to a new quality assurance approach that reduced defects by 25%.
Can you describe a situation where you had to balance ethical considerations with quality requirements?
How to Answer
- 1
Identify a specific situation that highlights ethical dilemmas in quality control.
- 2
Explain the quality standards you were required to meet.
- 3
Discuss the ethical considerations involved in your decision-making.
- 4
Describe the actions you took to resolve the issue.
- 5
Highlight the outcome and any lessons learned.
Example Answers
In a previous role, I discovered a supplier used substandard materials to cut costs. I had to decide whether to overlook it for immediate production needs or report it. I chose to report it, ensuring we adhered to quality standards, which ultimately led to a more reliable product and a stronger relationship with the supplier who improved their practices.
Don't Just Read Supplier Quality Engineer Questions - Practice Answering Them!
Reading helps, but actual practice is what gets you hired. Our AI feedback system helps you improve your Supplier Quality Engineer interview answers in real-time.
Personalized feedback
Unlimited practice
Used by hundreds of successful candidates
Technical Interview Questions
What quality standards and methodologies are you familiar with, such as ISO 9001 or Six Sigma?
How to Answer
- 1
Identify and list key quality standards relevant to Supplier Quality Engineering.
- 2
Explain your experience with each standard or methodology briefly.
- 3
Highlight any certifications or training you've completed.
- 4
Include examples of how you've applied these standards to enhance quality.
- 5
Demonstrate understanding of how these standards affect supplier selection and management.
Example Answers
I am familiar with ISO 9001 and have applied its principles in my previous role by implementing a quality management system that improved supplier performance metrics by 30%.
How do you approach statistical process control when evaluating supplier performance?
How to Answer
- 1
Define key performance indicators specific to the supplier's processes
- 2
Collect data on product quality and process variability regularly
- 3
Utilize control charts to visualize data trends over time
- 4
Conduct capability analysis to assess the supplier's process consistency
- 5
Communicate findings with suppliers to drive continuous improvement
Example Answers
I start by identifying the key performance indicators that align with our business goals. Next, I gather quality data and use control charts to track process variations. This helps to identify trends that may indicate potential issues.
Don't Just Read Supplier Quality Engineer Questions - Practice Answering Them!
Reading helps, but actual practice is what gets you hired. Our AI feedback system helps you improve your Supplier Quality Engineer interview answers in real-time.
Personalized feedback
Unlimited practice
Used by hundreds of successful candidates
What tools and software are you experienced with for quality assurance and supplier evaluations?
How to Answer
- 1
List specific tools you have used, like Minitab or APQP.
- 2
Highlight your experience with any ERP systems, such as SAP or Oracle.
- 3
Mention any software for reporting and documentation, like Microsoft Excel or Quality Management Systems (QMS).
- 4
Include any experience with statistical process control (SPC) tools.
- 5
Be ready to explain how these tools helped you improve supplier quality.
Example Answers
I have experience with Minitab for data analysis and SAP for managing supplier information. I also use Excel for documentation and reporting.
Explain your process for conducting root cause analysis when quality issues arise with a supplier.
How to Answer
- 1
Define the problem clearly with specific data.
- 2
Use a structured method like 5 Whys or Fishbone diagram.
- 3
Involve cross-functional teams for diverse perspectives.
- 4
Implement corrective actions based on the findings.
- 5
Monitor the outcomes and adjust the process as needed.
Example Answers
When quality issues arise, I first gather specific data to define the problem accurately. Then, I employ techniques like the 5 Whys to dig deep into the root cause, involving colleagues from different departments for a well-rounded view. Once identified, I develop corrective actions and closely monitor the results to ensure effectiveness.
Can you walk us through the steps you take when conducting a supplier quality audit?
How to Answer
- 1
Start by preparing an audit checklist based on supplier requirements and industry standards.
- 2
Schedule the audit and communicate expectations with the supplier's management team.
- 3
Conduct the audit using the checklist to evaluate processes, documentation, and compliance.
- 4
Document findings, noting any non-conformities or areas for improvement.
- 5
Hold a closing meeting with the supplier to discuss findings and agree on corrective actions.
Example Answers
I prepare an audit checklist aligned with the supplier's quality management system before scheduling the audit. During the audit, I evaluate their processes against this checklist. After the audit, I document my findings and hold a meeting with the supplier to discuss necessary corrections.
How do you ensure that suppliers comply with industry regulations regarding product quality?
How to Answer
- 1
Conduct regular audits of suppliers' quality processes and documentation
- 2
Establish clear quality requirements and communicate them to suppliers
- 3
Implement a robust supplier performance monitoring system with metrics
- 4
Provide training and support to suppliers to help them meet standards
- 5
Maintain open communication for continuous improvement and feedback
Example Answers
I ensure supplier compliance by conducting regular audits and reviewing their quality management systems. This helps identify any gaps early on. I also set clear quality requirements upfront and maintain ongoing communication to support their improvement efforts.
What types of materials and processes do you have experience with in terms of quality assurance?
How to Answer
- 1
Identify key materials relevant to the position and mention specific types.
- 2
Discuss specific quality assurance processes you have utilized.
- 3
Relate your experience to industry standards and regulations.
- 4
Include examples of metrics or tools you used to ensure quality.
- 5
Emphasize any experience with cross-functional teams or problem-solving.
Example Answers
I have experience working with metals and plastics, specifically conducting quality inspections using ISO 9001 standards. I regularly utilized statistical process control tools to assess manufacturing processes.
What types of measurement systems have you used to assess supplier quality?
How to Answer
- 1
Identify specific measurement tools or systems you have used.
- 2
Highlight key metrics like defect rates, compliance levels, or audit scores.
- 3
Mention any software or databases utilized for tracking quality data.
- 4
Discuss how you analyzed and reported on supplier performance.
- 5
Provide examples of how these measurements improved supplier quality.
Example Answers
I have used statistical process control charts to monitor defect rates and identify trends. This allowed me to track supplier performance effectively and address issues proactively.
What do you understand by fault tolerance in the context of supply chain quality?
How to Answer
- 1
Define fault tolerance in terms of supply chain processes.
- 2
Discuss how it impacts supplier selection and evaluation.
- 3
Explain the importance of redundancy and risk management.
- 4
Provide examples of fault tolerance in quality control measures.
- 5
Highlight its role in maintaining product integrity and customer satisfaction.
Example Answers
Fault tolerance in supply chain quality means having systems that can continue to function despite potential failures. This involves selecting suppliers with robust quality management systems and implementing redundant processes to catch defects. For example, if one supplier fails to meet quality standards, having an alternative supplier ready ensures product quality is not compromised.
What is your experience with process mapping in relation to supplier quality management?
How to Answer
- 1
Describe specific tools you used for process mapping, like flowcharts or swimlane diagrams
- 2
Explain how you identified critical quality checkpoints in the mapping process
- 3
Discuss any improvements made to supplier processes as a result of your mapping
- 4
Mention collaboration with suppliers to ensure buy-in on process changes
- 5
Highlight outcomes, such as reduced defects or improved efficiency
Example Answers
In my previous role, I utilized flowcharts to map supplier processes, identifying quality checkpoints that led to a 20% reduction in defects over six months.
Don't Just Read Supplier Quality Engineer Questions - Practice Answering Them!
Reading helps, but actual practice is what gets you hired. Our AI feedback system helps you improve your Supplier Quality Engineer interview answers in real-time.
Personalized feedback
Unlimited practice
Used by hundreds of successful candidates
Situational Interview Questions
If a supplier consistently fails to meet quality standards, how would you address the situation to ensure improvement?
How to Answer
- 1
Gather data on the specific quality issues outlined by the supplier.
- 2
Initiate a meeting with the supplier to discuss the quality concerns transparently.
- 3
Develop a corrective action plan together with clear timelines and responsibilities.
- 4
Implement regular follow-ups to monitor progress and provide support.
- 5
Evaluate if additional training or resources are needed for the supplier.
Example Answers
I would first collect data on the specific issues and then arrange a meeting with the supplier to openly discuss the problems. Together, we would create a corrective action plan with set deadlines to ensure accountability.
Imagine a scenario where you have conflicting quality reports from two suppliers. How would you determine which report to trust?
How to Answer
- 1
Review both reports for methodology consistency and data quality.
- 2
Consult with technical teams or quality experts for insights.
- 3
Look for historical data and past performance of the suppliers.
- 4
Conduct a root cause analysis to identify discrepancies.
- 5
Consider on-site evaluations or audits of both suppliers.
Example Answers
I would first examine the methodologies used in both reports to ensure consistency. Next, I'd consult with our quality team to gain insights. After that, I'd analyze past performance data from both suppliers to see if there’s a trend. If necessary, I'd perform a root cause analysis on the discrepancies before making a decision.
Don't Just Read Supplier Quality Engineer Questions - Practice Answering Them!
Reading helps, but actual practice is what gets you hired. Our AI feedback system helps you improve your Supplier Quality Engineer interview answers in real-time.
Personalized feedback
Unlimited practice
Used by hundreds of successful candidates
If you have multiple suppliers with quality issues, how would you prioritize which ones to address first?
How to Answer
- 1
Assess the criticality of the supplied components to production.
- 2
Evaluate the frequency of quality issues reported for each supplier.
- 3
Consider the financial impact of quality issues on product cost or customer satisfaction.
- 4
Check for any regulatory or compliance implications tied to specific suppliers.
- 5
Review the suppliers' past performance and responsiveness to quality concerns.
Example Answers
I would start by identifying which suppliers provide critical components and have frequent issues. Then, I would analyze the financial impact of these issues on our overall production costs and customer satisfaction. Finally, I would prioritize suppliers based on the urgency of compliance or regulatory concerns.
Suppose you notice a new trend in defects from a supplier. How would you initiate a corrective action plan?
How to Answer
- 1
Gather relevant data on defect trends from the supplier.
- 2
Conduct a root cause analysis to identify underlying issues.
- 3
Collaborate with the supplier to discuss findings and potential solutions.
- 4
Develop a corrective action plan outlining steps and responsibilities.
- 5
Monitor the effectiveness of the corrective actions taken.
Example Answers
I would start by collecting data on the defects to understand the trends better. Then, I’d perform a root cause analysis and work with the supplier to discuss the identified issues. Together we would create a corrective action plan, and I’d ensure we monitor its effectiveness over time.
You are facing tight deadlines on multiple supplier assessments. How would you manage your time to ensure thorough evaluations?
How to Answer
- 1
Prioritize assessments based on risk and impact to the project.
- 2
Break down evaluations into manageable tasks and set specific time limits for each.
- 3
Use templates and checklists to streamline the evaluation process.
- 4
Communicate with suppliers to gather necessary data quickly.
- 5
Schedule regular check-ins to monitor progress and adjust priorities as needed.
Example Answers
I would prioritize the assessments by focusing on suppliers that have the highest impact on our project. Then, I'd break the evaluations into smaller tasks and allocate specific time slots for each task to stay on track.
If a supplier disagrees with your quality assessment, how would you handle this disagreement?
How to Answer
- 1
Listen carefully to the supplier's concerns and perspective
- 2
Clarify the facts of the quality assessment with data and evidence
- 3
Engage in a constructive dialogue to understand the root cause
- 4
Explore common ground and seek a solution collaboratively
- 5
Document the conversation and agreed actions for future reference
Example Answers
I would first listen to the supplier's viewpoint to fully understand their concerns. Then, I would present the data and evidence backing my assessment and work with them to clarify any misunderstandings.
How would you implement a continuous improvement program for supplier quality management?
How to Answer
- 1
Assess current supplier performance metrics and quality issues
- 2
Establish clear quality objectives and KPIs for suppliers
- 3
Develop a collaborative relationship with suppliers for feedback
- 4
Implement a training program for suppliers to enhance their quality capabilities
- 5
Regularly review and analyze quality data to identify improvement opportunities
Example Answers
I would start by assessing current performance metrics and identifying key quality issues. Then, I'd set clear quality objectives and KPIs for our suppliers to align their goals with ours. Collaborating with suppliers to gather their feedback is crucial, and I would implement training programs to enhance their quality capabilities. Lastly, I would regularly analyze quality data to spot areas for improvement.
If you discovered that a supplier's material failed a critical quality test, what steps would you take immediately after?
How to Answer
- 1
Immediately notify the supplier about the failure
- 2
Collect all relevant data and documentation regarding the test results
- 3
Initiate an internal review to assess potential impact on production
- 4
Work with the supplier to investigate the root cause of the failure
- 5
Develop a corrective action plan in collaboration with the supplier
Example Answers
First, I would promptly inform the supplier about the quality test failure to address the issue. Then, I would gather all data related to the test results to understand the scope. Next, I'd conduct an internal review to evaluate how this might affect our production line.
If you were tasked with innovating quality control processes with suppliers, what steps would you take?
How to Answer
- 1
Assess current quality control processes to identify gaps and inefficiencies
- 2
Engage suppliers in collaborative workshops to brainstorm innovative solutions
- 3
Research and implement advanced technologies, like AI or automation, to enhance quality checks
- 4
Establish clear communication channels for ongoing feedback and improvement
- 5
Set measurable quality metrics to evaluate the effectiveness of new processes
Example Answers
I would start by analyzing the existing quality control processes to pinpoint areas needing improvement. Then, I would hold brainstorming sessions with suppliers to generate innovative ideas collaboratively. Next, I would explore incorporating AI technologies that can help automate inspections and provide real-time feedback.
Supplier Quality Engineer Position Details
Salary Information
Recommended Job Boards
CareerBuilder
www.careerbuilder.com/jobs/supplier-quality-engineerThese job boards are ranked by relevance for this position.
Related Positions
Ace Your Next Interview!
Practice with AI feedback & get hired faster
Personalized feedback
Used by hundreds of successful candidates
Ace Your Next Interview!
Practice with AI feedback & get hired faster
Personalized feedback
Used by hundreds of successful candidates