Top 29 Tap Builder Interview Questions and Answers [Updated 2025]
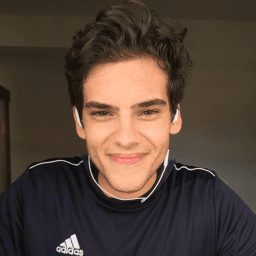
Andre Mendes
•
March 30, 2025
Are you preparing for a Tap Builder interview and unsure what to expect? Dive into our comprehensive guide, where we've compiled the most common interview questions for this specialized role. Not only will you find example answers, but also invaluable tips on how to tackle each question with confidence. Equip yourself with the insights you need to excel and land your dream job in the Tap Builder field.
Download Tap Builder Interview Questions in PDF
To make your preparation even more convenient, we've compiled all these top Tap Builderinterview questions and answers into a handy PDF.
Click the button below to download the PDF and have easy access to these essential questions anytime, anywhere:
List of Tap Builder Interview Questions
Behavioral Interview Questions
How do you ensure the quality and durability of the taps you build in your past projects?
How to Answer
- 1
Use high-quality materials specific to tap construction
- 2
Implement strict testing protocols for every batch of taps
- 3
Follow best practices in design for optimal durability
- 4
Stay updated with industry standards and innovations
- 5
Seek feedback and perform regular maintenance on taps in use
Example Answers
I ensure quality by using premium materials, like brass, and I implement rigorous testing to check for leaks and durability. Each tap undergoes a series of tests before it leaves the workshop.
Don't Just Read Tap Builder Questions - Practice Answering Them!
Reading helps, but actual practice is what gets you hired. Our AI feedback system helps you improve your Tap Builder interview answers in real-time.
Personalized feedback
Unlimited practice
Used by hundreds of successful candidates
Describe a time when you had to collaborate with others on a tap design project. What was your role, and how did you ensure the project’s success?
How to Answer
- 1
Think of a specific project that involved teamwork.
- 2
Clearly define your role in the project.
- 3
Highlight your contributions to the collaboration process.
- 4
Explain how you overcame challenges with your team.
- 5
Mention the outcome and any learnings from the project.
Example Answers
In a recent tap design project, I was the lead designer. I collaborated closely with engineers and marketing teams. My role involved creating initial designs and gathering feedback through regular meetings. We faced challenges with functionality vs. aesthetics, but through group discussions, we adapted our designs. The final product was well-received, and we learned the importance of cross-departmental communication.
Tell me about a time you disagreed with a colleague about a design decision. How did you handle the situation?
How to Answer
- 1
Choose a specific example that shows your collaboration skills.
- 2
Clearly state the disagreement and your perspective on the design.
- 3
Describe how you approached the discussion with your colleague respectfully.
- 4
Emphasize the outcome and any compromise or solution you found.
- 5
Reflect on what you learned from the experience.
Example Answers
In a recent project, my colleague wanted to implement a complex design that I felt would confuse users. I scheduled a meeting to discuss our ideas and listened to their reasoning. I shared user feedback we had received, and together we brainstormed a simpler solution that satisfied both our concerns. The final design was well-received and easier for users.
Give an example of how you manage tight deadlines when building taps. What strategies do you use?
How to Answer
- 1
Prioritize tasks by urgency and importance to focus on critical features first
- 2
Break down the project into smaller, manageable parts to track progress easily
- 3
Communicate regularly with the team to identify challenges early on
- 4
Use time management techniques like the Pomodoro technique for increased focus
- 5
Be flexible to adjust plans as necessary while keeping the end goal in sight
Example Answers
In a previous project, I had to build a tap for a major release in two weeks. I prioritized the core functionality first and divided the project into daily milestones. This way, I could track my progress and adjust tasks as needed. I communicated with my team daily to address any roadblocks swiftly.
Describe a time when your technical skills were tested on a tap building project. How did you handle it?
How to Answer
- 1
Select a specific project where you faced a technical challenge.
- 2
Explain the nature of the challenge and why it was difficult.
- 3
Outline the steps you took to resolve the issue.
- 4
Highlight any tools or techniques you used.
- 5
Conclude with the positive outcome and lessons learned.
Example Answers
On a tap building project for a large client, I encountered a significant API integration issue that caused the data retrieval to fail. I immediately analyzed the logs and identified the error in the API response format. I reached out to the API provider for clarification, and then I adjusted our request structure accordingly. After implementing the fix, the integration worked smoothly and the client was satisfied, reinforcing the importance of thorough testing.
Describe a situation where you had to adapt to a significant change during a tap building project.
How to Answer
- 1
Think of a specific project where changes were unexpected.
- 2
Describe the nature of the change clearly and concisely.
- 3
Explain how you responded to the change and what steps you took.
- 4
Highlight the positive outcome or lessons learned from the experience.
- 5
Use the STAR method to structure your answer: Situation, Task, Action, Result.
Example Answers
In a recent tap building project, we were informed last minute that the materials were delayed due to supply chain issues. I quickly sourced alternative materials that met our design requirements while ensuring we stayed on schedule. This adaptability allowed us to complete the project on time, and our client was very satisfied with the final outcome.
Technical Interview Questions
What CAD software do you prefer for tap design, and what features do you find most useful?
How to Answer
- 1
Choose a specific CAD software you are skilled in.
- 2
Mention key features that aid in tap design such as parametric modeling or simulation.
- 3
Explain why these features are beneficial for the design process.
- 4
Provide an example of how you used the software in a project.
- 5
Be confident and articulate about your preferences.
Example Answers
I prefer using SolidWorks for tap design. Its parametric modeling allows for quick adjustments and iterations, which is crucial when finalizing tap specifications. I once redesigned a tap system, utilizing the simulation feature to ensure proper flow and durability before physical prototyping.
How do you conduct performance testing for taps to ensure they meet industry standards?
How to Answer
- 1
Identify key performance metrics such as flow rate, pressure, and temperature stability.
- 2
Develop a test plan that includes various scenarios like peak usage and low flow conditions.
- 3
Use monitoring tools to record data during testing periods for accurate analysis.
- 4
Compare results against industry standards and benchmarks.
- 5
Iterate on design based on test findings to optimize performance.
Example Answers
I start by identifying the key metrics like flow rate and pressure. Then, I create a test plan to simulate different usage scenarios, monitoring everything with precise tools. After testing, I analyze the data to ensure compliance with industry standards.
Don't Just Read Tap Builder Questions - Practice Answering Them!
Reading helps, but actual practice is what gets you hired. Our AI feedback system helps you improve your Tap Builder interview answers in real-time.
Personalized feedback
Unlimited practice
Used by hundreds of successful candidates
Explain how understanding hydrodynamics is crucial in tap design and function.
How to Answer
- 1
Define hydrodynamics and its relevance to fluid flow.
- 2
Explain how hydrodynamic principles affect water pressure in taps.
- 3
Discuss the influence of design on flow rate and user experience.
- 4
Mention examples of designs influenced by hydrodynamics.
- 5
Highlight benefits of optimizing tap design using hydrodynamic analysis.
Example Answers
Hydrodynamics helps us understand fluid flow and pressure. In tap design, it ensures that water flows smoothly without splashing. By optimizing the shape and size of the tap, we can enhance the user experience and conserve water.
How do you ensure compatibility of taps with various plumbing systems?
How to Answer
- 1
Research the specifications of the plumbing system before installation.
- 2
Check the tap's compatibility with existing pipe sizes and materials.
- 3
Consider the pressure ratings of both the tap and the plumbing system.
- 4
Use adapters or fittings if necessary to ensure proper connections.
- 5
Stay informed about industry standards and regulations for plumbing compatibility.
Example Answers
I ensure compatibility by researching the specifications of the plumbing system beforehand and checking if the tap matches the pipe sizes and materials used.
How do you incorporate sustainable practices in your tap designs?
How to Answer
- 1
Research and use eco-friendly materials in your designs
- 2
Implement water-saving features like aerators or flow restrictors
- 3
Design for longevity to reduce waste and encourage durability
- 4
Consider the lifecycle of the product, including end-of-life disposal
- 5
Collaborate with suppliers who share a commitment to sustainability
Example Answers
I prioritize eco-friendly materials such as recycled metals and avoid harmful coatings to minimize environmental impact. Additionally, I design taps with aerators to conserve water while maintaining performance.
What are the key design principles to consider when designing a functional and aesthetic tap?
How to Answer
- 1
Focus on usability and ergonomics to ensure ease of use.
- 2
Consider materials that are durable and easy to clean.
- 3
Incorporate water-saving features without sacrificing performance.
- 4
Ensure the design complements contemporary kitchen and bathroom aesthetics.
- 5
Evaluate the installation process for simplicity and accessibility.
Example Answers
When designing a tap, I prioritize usability by creating a lever that is easy to operate for all users, while choosing stainless steel for durability and aesthetic appeal.
What materials do you consider best for durability and aesthetics in tap manufacturing, and why?
How to Answer
- 1
Identify key materials used in tap manufacturing, like brass, stainless steel, and plastic.
- 2
Discuss the durability of each material and its resistance to corrosion and wear.
- 3
Highlight the aesthetic qualities of these materials, such as finish and color variety.
- 4
Emphasize how customer preference influences material choice.
- 5
Mention any certifications or standards relevant to material selection.
Example Answers
I consider brass and stainless steel to be the best materials for tap manufacturing due to their excellent durability and resistance to corrosion. Brass offers a classic aesthetic with a warm finish, while stainless steel has a modern look that appeals to many consumers.
Can you explain the different types of tap mechanisms and their applications?
How to Answer
- 1
Start by briefly defining what a tap mechanism is.
- 2
Identify the main types of tap mechanisms like compression, ball, cartridge, and disc.
- 3
Explain the application of each type in various settings like kitchens, bathrooms, or commercial use.
- 4
Use examples to highlight the advantages of each type.
- 5
Be ready to discuss any personal experience you have with these tap types.
Example Answers
A tap mechanism controls the flow of water and comes in several types. The most common are compression, ball, cartridge, and disc. Compression taps are often found in older kitchens, while ball taps, known for their durability, are widely used in kitchen sinks. Cartridge taps provide smooth operation and are popular in modern bathrooms, while disc taps offer precise control and are great for high-end designs.
Which tools and equipment are essential for a tap builder, and how do you use them?
How to Answer
- 1
Identify the main tools like tap drills, taps, and dies.
- 2
Explain the purpose of each tool in the tapping process.
- 3
Mention safety equipment like gloves and goggles.
- 4
Discuss any calibration or setup needed before use.
- 5
Provide an example of a project where you effectively used these tools.
Example Answers
An essential tool for a tap builder is a tap set, which includes taps and dies for creating internal threads. I use tap drills to make precise holes followed by the taps to thread the metal. I also always wear safety goggles and gloves to protect myself during the process.
Situational Interview Questions
A batch of taps was reported to have a quality defect. How would you investigate and resolve this issue?
How to Answer
- 1
Identify the specifics of the defect reported.
- 2
Gather data on the production process and materials used.
- 3
Inspect samples from the batch for visible defects.
- 4
Consult with team members who worked on the batch.
- 5
Develop a corrective action plan to address the defect.
Example Answers
First, I would gather information on the specific quality defect reported and which taps are affected. Then, I would review the production records and inspect samples from the batch to identify any patterns or issues.
If a client asks for a highly innovative and custom tap design, how would you approach the project?
How to Answer
- 1
Understand the client's vision by asking detailed questions.
- 2
Research current trends and innovations in tap design.
- 3
Sketch initial ideas and concepts based on client discussions.
- 4
Present a few design options to the client for feedback.
- 5
Incorporate client feedback into the final design before production.
Example Answers
I would start by asking the client specific questions to understand their vision and requirements. Afterward, I would research the latest trends in tap design and sketch some initial ideas. These would be presented to the client for feedback, allowing us to refine the concepts together.
Don't Just Read Tap Builder Questions - Practice Answering Them!
Reading helps, but actual practice is what gets you hired. Our AI feedback system helps you improve your Tap Builder interview answers in real-time.
Personalized feedback
Unlimited practice
Used by hundreds of successful candidates
A project is falling behind schedule. What steps would you take to ensure timely completion without compromising quality?
How to Answer
- 1
Assess the current status and identify key bottlenecks.
- 2
Prioritize tasks and resources that will have the most impact on the schedule.
- 3
Communicate with the team to gather insights and suggestions.
- 4
Consider adjusting timelines or reallocating resources to critical tasks.
- 5
Implement regular check-ins to monitor progress and adjust plans as needed.
Example Answers
First, I would assess where the delays are occurring and identify any bottlenecks. Then, I would prioritize the critical tasks and allocate more resources to them. I would also communicate with the team to get their input on possible solutions and ensure we're all aligned on the next steps, allowing us to adjust our plans where necessary.
How would you handle receiving critical feedback from a client about a tap design you created?
How to Answer
- 1
Listen actively to the client's feedback without interrupting
- 2
Acknowledge their concerns and express appreciation for their input
- 3
Ask clarifying questions to fully understand their perspective
- 4
Discuss potential revisions or adjustments based on their feedback
- 5
Follow up after implementing changes to ensure client satisfaction
Example Answers
I would listen carefully to the client's feedback, ensuring I understand their concerns fully. Then, I would acknowledge their perspective and express gratitude for their insights. If possible, I'd ask questions to clarify specifics and discuss how I can adjust the design to meet their vision. Finally, I would follow up to confirm they are satisfied with the changes made.
Midway through a project, the client decides to change the tap design significantly. How do you respond?
How to Answer
- 1
Acknowledge the client's change as important and valid.
- 2
Ask clarifying questions to understand the new vision and requirements.
- 3
Evaluate the implications of the changes on the timeline and budget.
- 4
Propose a plan to integrate the changes effectively.
- 5
Communicate openly about any potential challenges and next steps.
Example Answers
I appreciate the client's new vision and would start by understanding their specific concerns. I would ask for details on the new design and review how it affects our current timeline and budget before proposing adjustments.
During a tap building project, two team members are in conflict over the design approach. How would you address this?
How to Answer
- 1
Listen to both team members' perspectives carefully.
- 2
Encourage open communication in a neutral setting.
- 3
Identify the underlying reasons for their disagreement.
- 4
Facilitate a brainstorming session to explore solutions.
- 5
Aim for a compromise that satisfies both parties and the project goals.
Example Answers
I would first set up a meeting where both team members can express their viewpoints. After understanding their concerns, I would facilitate a discussion to explore common ground and alternative solutions that could work for the project.
Your tap building project is experiencing cost overruns. How would you manage this scenario?
How to Answer
- 1
Analyze the reasons for cost overruns to identify key issues
- 2
Review the project budget and look for areas to cut costs
- 3
Communicate with your team and stakeholders about the situation
- 4
Implement corrective actions and track expenses closely going forward
- 5
Consider revising the project timeline if necessary to manage costs
Example Answers
First, I would analyze the cost overruns to understand where the money is being lost. After identifying the main issues, I would review the budget and look for non-essential expenses that can be reduced. I would involve my team and discuss these findings with stakeholders to ensure everyone is informed. Then, I would implement a tighter expense tracking process to prevent future overruns.
What would you do if a key supplier for your tap components suddenly can't fulfill an order?
How to Answer
- 1
Evaluate the urgency of the order and the impact on production.
- 2
Reach out to the supplier for more details on the issue.
- 3
Explore alternative suppliers who can provide the components.
- 4
Communicate transparently with your team and stakeholders about the situation.
- 5
Consider adjusting the production schedule if needed.
Example Answers
I would first assess how critical the order is for our timeline. Then, I would contact the supplier to understand the problem and see if there's a possibility for a partial shipment or alternative solutions. If not, I would quickly source alternative suppliers to fulfill our needs and inform my team about the changes.
If you encounter unforeseen challenges during a project, how do you ensure it still meets the deadline?
How to Answer
- 1
Assess the challenge quickly and determine its impact.
- 2
Prioritize tasks and focus on critical elements of the project.
- 3
Communicate clearly with stakeholders about the issue and your plan.
- 4
Adjust timelines or resources if possible, while keeping the team aligned.
- 5
Implement a contingency plan if necessary to stay on track.
Example Answers
When an unforeseen challenge arises, I first assess its impact on the project timeline. I then prioritize the remaining tasks and focus on the critical ones to ensure we meet our deadline. I communicate transparently with my team and stakeholders about the situation and our adjusted plan. If necessary, I add extra resources to critical tasks to help mitigate delays.
How would you evaluate and decide whether to implement a new technology in your tap building process?
How to Answer
- 1
Identify the specific problem the technology addresses.
- 2
Research the technology's reliability and user feedback.
- 3
Consider the cost versus the expected benefits.
- 4
Evaluate how it integrates with existing processes.
- 5
Pilot the technology on a small scale before full implementation.
Example Answers
I would start by assessing the specific challenges in our current tap building process. Then, I'd research the new technology to see how it addresses these issues and check reviews from others who have used it. I'd weigh the costs against the potential efficiency gains, and consider how easily it fits into our existing workflow. Finally, I'd suggest a pilot program to evaluate its effectiveness before making a full commitment.
Don't Just Read Tap Builder Questions - Practice Answering Them!
Reading helps, but actual practice is what gets you hired. Our AI feedback system helps you improve your Tap Builder interview answers in real-time.
Personalized feedback
Unlimited practice
Used by hundreds of successful candidates
You need to collaborate with the electrical team to incorporate sensors into taps. How would you manage this collaboration?
How to Answer
- 1
Establish clear communication channels with the electrical team.
- 2
Schedule regular meetings to discuss progress and challenges.
- 3
Define roles and responsibilities for both teams early on.
- 4
Create a shared document or project management tool for tracking integration.
- 5
Encourage open feedback to resolve issues quickly.
Example Answers
I would set up a weekly meeting with the electrical team to ensure we are aligned on the sensor specifications and integration timeline. I would also create a shared document where both teams can update their progress and highlight any challenges.
How would you adjust your designs if you notice a new market trend in tap preferences?
How to Answer
- 1
Research the new trend to understand customer preferences.
- 2
Analyze how existing designs can be adapted to fit the trend.
- 3
Consult with the sales and marketing teams for insights.
- 4
Prototype new designs quickly to test market response.
- 5
Gather feedback from users and iterate on the design.
Example Answers
I would start by researching the trend to see what specific customer preferences are emerging. Then, I would analyze which features of our current designs align with those preferences and which ones might need modification. Collaborating with sales could provide further insights, followed by prototyping new adjustments and gathering user feedback for improvement.
Tap Builder Position Details
Related Positions
- Tap Puller
- Table Maker
- Pot Builder
- Frame Builder
- Pad Maker
- Button Maker
- Car Builder
- Organ Builder
- Body Maker
- Tube Pusher
Similar positions you might be interested in.
Ace Your Next Interview!
Practice with AI feedback & get hired faster
Personalized feedback
Used by hundreds of successful candidates
Ace Your Next Interview!
Practice with AI feedback & get hired faster
Personalized feedback
Used by hundreds of successful candidates