Top 29 Tool Design Engineer Interview Questions and Answers [Updated 2025]
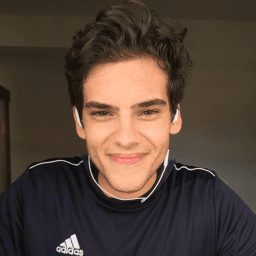
Andre Mendes
•
March 30, 2025
Navigating the competitive field of tool design engineering requires not only technical expertise but also the ability to articulate your skills and experiences effectively during interviews. In this blog post, we present a curated collection of the most common interview questions for aspiring tool design engineers, complete with example answers and insightful tips to help you respond confidently and stand out from the competition. Dive in to enhance your interview readiness and secure your next role.
Download Tool Design Engineer Interview Questions in PDF
To make your preparation even more convenient, we've compiled all these top Tool Design Engineerinterview questions and answers into a handy PDF.
Click the button below to download the PDF and have easy access to these essential questions anytime, anywhere:
List of Tool Design Engineer Interview Questions
Behavioral Interview Questions
Can you describe a time when you had to design a tool under tight constraints? How did you prioritize and manage your work?
How to Answer
- 1
Identify specific constraints like time, budget, or material limitations.
- 2
Focus on your initial assessment of the situation and how you set priorities.
- 3
Describe the steps you took to address the constraints effectively.
- 4
Mention any tools or methodologies you used to streamline the design process.
- 5
Conclude with the outcome and what you learned from the experience.
Example Answers
In my previous role, I had to design a fastening tool within a 2-week deadline and a limited budget. I started by listing essential requirements and prioritized functionality over aesthetics. Using CAD software, I created a basic prototype and tested it quickly, allowing me to iterate on design until it met specifications. The project was completed on time and under budget, leading to increased efficiency in our production line.
Tell me about a project where you worked closely with a manufacturing team. How did you handle communication and collaboration?
How to Answer
- 1
Select a specific project that illustrates your role and responsibilities.
- 2
Highlight how you established clear communication channels with the manufacturing team.
- 3
Discuss any tools or techniques you used to facilitate collaboration.
- 4
Mention challenges faced and how you addressed them through teamwork.
- 5
Conclude with the positive outcome and lessons learned from the project.
Example Answers
In a recent project for designing a mold for a plastic component, I worked closely with the manufacturing team. We held weekly meetings where everyone could share updates. I used project management software for task tracking, which helped us stay aligned. When a design issue arose, we quickly collaborated to propose a new approach that met the timeline. As a result, we successfully completed the project on schedule, improving the prototype's quality.
Don't Just Read Tool Design Engineer Questions - Practice Answering Them!
Reading helps, but actual practice is what gets you hired. Our AI feedback system helps you improve your Tool Design Engineer interview answers in real-time.
Personalized feedback
Unlimited practice
Used by hundreds of successful candidates
Describe a situation where you came up with an innovative tool design that significantly impacted a project. What was the outcome?
How to Answer
- 1
Choose a specific project where you made a significant impact.
- 2
Clearly explain the problem that required an innovative tool.
- 3
Describe your design process and any challenges you faced.
- 4
Share measurable outcomes or benefits due to your design.
- 5
Focus on your contribution and the skills you utilized.
Example Answers
In a recent project, we needed to reduce the assembly time of a complex component. I designed a custom tool that allowed the team to align parts more accurately and quickly. As a result, we cut assembly time by 30%, which saved the company costs and improved our delivery schedule.
Can you provide an example of a disagreement you had with a colleague about a design choice and how you resolved it?
How to Answer
- 1
Choose a specific disagreement that highlights your problem-solving skills.
- 2
Explain the design choice in question clearly.
- 3
Describe the approach you took to resolve the disagreement.
- 4
Emphasize teamwork and communication in your resolution process.
- 5
Mention the outcome and what you learned from the experience.
Example Answers
I disagreed with a colleague about the material choice for a tool design. I preferred aluminum for its strength, while they suggested plastic for weight savings. We discussed our concerns and conducted a stress analysis together. Ultimately, we decided to prototype both options and evaluate their performance. This collaboration led to a successful design that combined the best of both worlds.
Describe a time when a project requirement changed unexpectedly. How did you adapt your tool design to fit the new requirements?
How to Answer
- 1
Use the STAR method: Situation, Task, Action, Result.
- 2
Be specific about the requirement change and its impact.
- 3
Discuss the steps you took to adapt your design.
- 4
Highlight any collaboration with the team to address the change.
- 5
Emphasize the positive outcome or learning from the experience.
Example Answers
In a recent project, the client changed the specifications for a tool design halfway through development. I quickly gathered the team to assess the impact of the new requirements. We brainstormed potential modifications and I revised the design within a week, which increased efficiency by 20%. The client was pleased with the timely adaptation.
Have you ever led a team in a tool design project? How did you ensure success through your leadership?
How to Answer
- 1
Briefly describe the project and your role as a leader
- 2
Highlight specific leadership actions you took to guide the team
- 3
Mention any tools or methods used to facilitate communication and collaboration
- 4
Include measurable outcomes or successes from the project
- 5
Reflect on what you learned as a leader during the project
Example Answers
I led a team developing a high-precision fixture for a CNC machine. I scheduled regular check-in meetings to track progress and address issues. We used CAD software for sharing designs, which improved our collaboration. The project was completed two weeks early, resulting in a significant cost savings.
Technical Interview Questions
What CAD software are you most skilled in, and how have you used it in designing tools?
How to Answer
- 1
Identify the CAD software you are most proficient in.
- 2
Describe a specific project where you used that software.
- 3
Highlight key features of the software that enhanced your design process.
- 4
Mention any collaboration or feedback you received while using the software.
- 5
Conclude with the impact of your design on the final tool.
Example Answers
I am most skilled in SolidWorks. In my last project, I designed a custom tool holder for a CNC machine. I utilized the simulation feature to test my design under stress, which led to a more durable product. Working with my team through the design review process allowed us to refine the final specifications.
How do you select appropriate materials for tool design? Can you give an example where material choice played a critical role in the design?
How to Answer
- 1
Consider material properties like strength, durability, and thermal resistance that suit the application
- 2
Think about the manufacturing process and how materials behave during shaping
- 3
Evaluate cost and availability of the materials for the project
- 4
Provide real-world examples where material choice impacted performance or results
- 5
Discuss collaboration with suppliers or using simulation tools to aid material selection
Example Answers
In selecting materials, I focus on strength and wear resistance for high-pressure die casting tools. For instance, I once chose tool steel for a die that handled aluminum. This choice significantly reduced wear and increased tool life.
Don't Just Read Tool Design Engineer Questions - Practice Answering Them!
Reading helps, but actual practice is what gets you hired. Our AI feedback system helps you improve your Tool Design Engineer interview answers in real-time.
Personalized feedback
Unlimited practice
Used by hundreds of successful candidates
Explain the importance of tolerancing in tool design and provide an example from a past project.
How to Answer
- 1
Define tolerancing and its role in tool design clearly.
- 2
Emphasize how precise tolerances ensure interoperability and function.
- 3
Include a specific example of a past project where tolerances impacted success.
- 4
Discuss the consequences of ignoring tolerances in your example.
- 5
Keep your answer structured: definition, importance, example, and outcome.
Example Answers
Tolerancing is vital in tool design as it specifies how much variation is allowed in manufacturing. Accurate tolerances ensure that parts fit together correctly and function as intended. For instance, in a project designing a precision injection mold, we set tight tolerances on the core and cavity dimensions. This precision prevented misalignment and ensured high-quality parts. Ignoring these tolerances would have led to defective products and increased costs.
How do you ensure that a tool design is manufacturable? What steps do you take to evaluate this?
How to Answer
- 1
Conduct a Design for Manufacturability (DFM) analysis during the design phase.
- 2
Collaborate closely with manufacturing engineers to understand their capabilities.
- 3
Use CAD software to simulate the manufacturing process and identify potential issues.
- 4
Analyze tolerance and fit to minimize assembly problems.
- 5
Create prototypes and gather feedback from the production team.
Example Answers
To ensure manufacturability, I start with a Design for Manufacturability analysis, focusing on the feasibility of each design feature. I also consult with manufacturing engineers early on to align the design with available production capabilities.
Have you used any simulation tools in your designs? How do they assist in the tool design process?
How to Answer
- 1
Identify specific simulation tools you have used, such as ANSYS or SolidWorks.
- 2
Explain how you utilized these tools in your design process.
- 3
Highlight the benefits these tools provided, like reducing development time or improving accuracy.
- 4
Mention any specific project examples where simulation was crucial.
- 5
Keep your explanation concise and focused on outcomes.
Example Answers
Yes, I have used SolidWorks for simulation in my designs. It helped me analyze stress distribution in a tool design, allowing me to optimize the thickness of components, which ultimately reduced material costs and increased durability.
Describe your approach to estimating the cost of a tool design project.
How to Answer
- 1
Break down the project into major components such as materials, labor, and overhead.
- 2
Research historical costs for similar projects to inform your estimates.
- 3
Include a contingency budget for unexpected expenses.
- 4
Consult with suppliers for up-to-date pricing on materials and components.
- 5
Document all assumptions and justifications for your estimates.
Example Answers
I start by breaking the project into key components like materials, labor, and overhead. Then, I refer to historical data on similar projects to guide my estimates. I also factor in a contingency for unexpected costs and check with suppliers for the latest material prices.
What are your experiences with prototyping in tool design? How do you use prototypes to refine your designs?
How to Answer
- 1
Share specific examples of tools you designed and the prototyping methods used.
- 2
Explain how prototypes helped identify flaws and improve functionality.
- 3
Discuss collaboration with team members during the prototyping phase.
- 4
Mention tools or software used in the prototyping process.
- 5
Highlight any feedback cycles and iterations involved in refining your designs.
Example Answers
In my last project, I designed a mold for a plastic parts manufacturer. I created several prototypes using 3D printing, which allowed the team to test fit and function. From these tests, we identified design flaws in the initial concept. After collecting feedback, I refined the design to improve part durability, and the final prototype was significantly more efficient.
How do you integrate quality control measures into your tool designs?
How to Answer
- 1
Incorporate design reviews at each stage of development
- 2
Utilize simulations to predict performance and identify potential failures
- 3
Select appropriate materials and manufacturing processes that comply with quality standards
- 4
Implement tolerance analysis to ensure parts fit and function correctly
- 5
Establish feedback loops with testing to refine designs based on real data
Example Answers
I integrate quality control by conducting design reviews at each stage and using simulations to predict issues. I also select materials that meet industry standards and perform tolerance analysis to ensure proper fit.
Why is ergonomics important in tool design, and how do you address it in your projects?
How to Answer
- 1
Explain how ergonomics improves user comfort and efficiency.
- 2
Discuss the impact of poor ergonomics on injury and productivity.
- 3
Provide examples of ergonomic considerations you've included in designs.
- 4
Mention any user feedback or testing processes you employ.
- 5
Highlight your awareness of industry standards related to ergonomics.
Example Answers
Ergonomics is vital in tool design because it enhances user comfort and reduces the risk of injury. In my projects, I conduct user studies to identify pain points and adjust tool dimensions accordingly. For instance, I've redesigned a handle to fit a wider range of hand sizes, which increased user satisfaction and decreased strain.
What software tools do you use for finite element analysis in tool design?
How to Answer
- 1
List specific software tools you are proficient in.
- 2
Mention your experience with each tool and its application in FEA.
- 3
Highlight any certifications or training relevant to the software.
- 4
Provide examples of projects where you used these tools for analysis.
- 5
Be prepared to discuss the advantages of the software you prefer.
Example Answers
I primarily use Autodesk Inventor and ANSYS for finite element analysis in tool design. I've applied ANSYS in several projects to simulate stress distributions in molds, which helped optimize their design for manufacturing.
Don't Just Read Tool Design Engineer Questions - Practice Answering Them!
Reading helps, but actual practice is what gets you hired. Our AI feedback system helps you improve your Tool Design Engineer interview answers in real-time.
Personalized feedback
Unlimited practice
Used by hundreds of successful candidates
What are the key principles you follow in designing tools that are both effective and durable?
How to Answer
- 1
Focus on user needs and functionality
- 2
Select high-quality materials for longevity
- 3
Incorporate ergonomic design for user comfort
- 4
Ensure ease of maintenance and repair
- 5
Test prototypes rigorously before full production
Example Answers
I prioritize understanding the user's needs, ensuring the tool serves its purpose effectively. I also select materials that resist wear and tear, such as high-grade steel, to enhance durability.
Can you discuss a complex 3D model you created for a tool design and the challenges you faced?
How to Answer
- 1
Choose a specific project that highlights your skills.
- 2
Describe the 3D modeling software you used and why.
- 3
Explain the complexity of the design and any specific requirements.
- 4
Discuss the challenges you faced and how you overcame them.
- 5
Mention any collaborative aspects or feedback from peers.
Example Answers
In my previous role, I designed a complex injection mold using SolidWorks. The model needed to accommodate multiple gating systems for efficient material flow. One challenge was fitting the cooling lines without interfering with the mold features. I collaborated closely with the manufacturing team to iterate on the design based on their insights, which ultimately improved the mold's performance.
Situational Interview Questions
Imagine you are asked to design a tool for a new, unfamiliar material. How would you approach this task?
How to Answer
- 1
Research the properties of the new material thoroughly.
- 2
Identify the specific requirements for the tooling process.
- 3
Consider existing tools and their limitations with similar materials.
- 4
Conduct trials or simulations to refine the tool design.
- 5
Collaborate with material experts for insights and recommendations.
Example Answers
I would start by researching the properties of the new material, like its hardness and thermal stability. Then I would define the requirements for the tool based on the machining process. I would also look at how similar materials have been approached in tool design to gather insights. After that, I’d run some simulations to ensure the design is functional. Lastly, I’d involve material specialists to optimize the tool parameters.
You are given a very tight deadline for a tool design project. What strategies would you employ to ensure timely delivery?
How to Answer
- 1
Prioritize tasks based on their impact on the project's success
- 2
Break the project into smaller, manageable phases
- 3
Communicate clearly with team members and stakeholders about deadlines
- 4
Utilize efficient design software and tools for rapid prototyping
- 5
Set regular check-ins to monitor progress and adjust plans as needed
Example Answers
To meet the tight deadline, I would prioritize critical tasks that affect the overall design. I would break the project into phases and assign team members specific roles. Regular communication is key, so I'd ensure everyone is updated on deadlines. I'd also leverage design software for quicker iterations.
Don't Just Read Tool Design Engineer Questions - Practice Answering Them!
Reading helps, but actual practice is what gets you hired. Our AI feedback system helps you improve your Tool Design Engineer interview answers in real-time.
Personalized feedback
Unlimited practice
Used by hundreds of successful candidates
A client wants a quick redesign of an existing tool to meet new requirements. How would you handle this request?
How to Answer
- 1
Clarify the new requirements with the client to ensure understanding.
- 2
Review the existing tool's design and performance to identify improvement areas.
- 3
Propose a timeline and present initial concepts for the redesign.
- 4
Communicate potential challenges and solutions during the redesign.
- 5
Keep the client updated throughout the process to manage expectations.
Example Answers
I would start by sitting down with the client to clearly define the new requirements. Then, I’d analyze the existing tool to understand its strengths and weaknesses before drafting an initial redesign proposal with a timeline.
If a tool you designed fails during testing, what steps would you take to diagnose and fix the issue?
How to Answer
- 1
Review the design specifications and compare them with the test results
- 2
Identify specific failure modes and potential causes of the failure
- 3
Conduct a failure analysis using appropriate tools and techniques
- 4
Develop and implement design modifications to address the identified issues
- 5
Retest the modified tool to ensure the changes resolved the failure
Example Answers
First, I would review the design specifications to see if the tool met the intended design parameters. Next, I would identify how the tool failed and what specific failure modes were apparent. After that, I would perform a thorough failure analysis to determine the root cause. Finally, I would modify the design as needed and retest the tool to confirm that the issue is resolved.
How would you approach a situation where your current tool design needs to be innovated to reduce production costs?
How to Answer
- 1
Analyze current designs for material cost and manufacturing efficiency
- 2
Collaborate with production teams for insights on bottlenecks and waste
- 3
Research alternative materials or processes that are cost-effective
- 4
Prototype quick solutions and conduct cost-benefit analyses
- 5
Implement changes incrementally, monitoring production outcomes closely
Example Answers
I would begin by analyzing the current designs to identify the most expensive materials and processes. Then, I would collaborate with our production team to understand waste areas and find more efficient methods. Researching cheaper materials that maintain quality would also be vital, alongside creating prototypes to evaluate effectiveness before full implementation.
If there is a conflict between the tool design team and the production team, how would you mediate the situation for a successful outcome?
How to Answer
- 1
Listen actively to both teams to understand their perspectives
- 2
Identify the root cause of the conflict rather than just the symptoms
- 3
Facilitate a meeting where both teams can express their concerns
- 4
Encourage collaboration by finding common goals
- 5
Propose solutions that take into account the needs of both teams
Example Answers
I would start by listening to both the tool design team and the production team to fully understand their viewpoints and concerns. After that, I would identify the root cause of the conflict and facilitate a meeting where each team can present their issues openly. I believe in finding a common goal that aligns both teams and proposing a solution that satisfies both parties.
What would you do if you identified a potential risk in a tool design during the final stages before release?
How to Answer
- 1
Assess the severity of the risk immediately.
- 2
Communicate the risk to your team and stakeholders promptly.
- 3
Propose a potential solution or mitigation strategy.
- 4
Document the risk and your actions taken for accountability.
- 5
Be prepared to adjust the timeline if necessary to ensure quality.
Example Answers
If I identified a potential risk in a tool design just before release, I would first evaluate how serious the risk is. Then, I would inform my team and relevant stakeholders about the issue. Next, I would suggest possible solutions or ways to mitigate the risk. It’s also important to document everything for future reference. If fixing the risk takes more time, I would advocate for adjustments to the timeline to ensure we release a safe and effective tool.
How would you contribute to a team initiative aimed at improving the tool design process based on past feedback?
How to Answer
- 1
Analyze previous feedback to identify common issues in the design process.
- 2
Propose specific changes or processes that can address the identified issues.
- 3
Collaborate with team members to gather insights and suggestions for improvement.
- 4
Utilize prototyping or simulation tools to test proposed changes quickly.
- 5
Establish metrics to evaluate the impact of changes on tool performance.
Example Answers
I would start by reviewing past feedback from team members and identifying key themes. For instance, if several comments highlighted difficulties with tool assembly, I would suggest modifications to the design for easier assembly and validate those through prototypes.
After receiving negative feedback from a customer about a tool's performance, what steps would you take to address the issues raised?
How to Answer
- 1
Acknowledge the customer's feedback and express gratitude for sharing their concerns
- 2
Conduct a thorough investigation to understand the specific issues reported
- 3
Collaborate with your team to analyze performance data and identify root causes
- 4
Develop a plan to rectify the issues, including potential design adjustments
- 5
Communicate the resolution and follow up with the customer to ensure satisfaction
Example Answers
I would first thank the customer for their feedback. Then, I would investigate the reports to pinpoint performance issues. Collaborating with my team, we would analyze the data and identify the root causes. Next, I would create a plan for necessary adjustments to the tool and ensure we communicate this to the customer, following up to verify their satisfaction.
A new technology becomes available that could be integrated into your tool designs. How would you assess its feasibility and benefit?
How to Answer
- 1
Identify the core features of the new technology
- 2
Evaluate how it aligns with current design specifications
- 3
Consider cost implications and return on investment
- 4
Assess potential risks and limitations
- 5
Gather feedback from team members and stakeholders
Example Answers
I would first analyze the core features of the new technology to see how they integrate with our tool designs. Then, I’d evaluate if it meets our specifications and enhances performance. Cost analysis would follow to ensure it’s a sound investment, and I’d consult with the team to gather varied insights on feasibility.
Don't Just Read Tool Design Engineer Questions - Practice Answering Them!
Reading helps, but actual practice is what gets you hired. Our AI feedback system helps you improve your Tool Design Engineer interview answers in real-time.
Personalized feedback
Unlimited practice
Used by hundreds of successful candidates
Tool Design Engineer Position Details
Recommended Job Boards
CareerBuilder
www.careerbuilder.com/jobs-tool-design-engineerZipRecruiter
www.ziprecruiter.com/Jobs/Tool-Design-EngineerThese job boards are ranked by relevance for this position.
Related Positions
- Machine Design Engineer
- Tool Engineer
- Tooling Engineer
- Tool Designer
- Product Development Engineer
- Application Engineer
- Engine Designer
- Sheet Metal Engineer
- Mechanical Engineer
- Tool Maker
Similar positions you might be interested in.
Ace Your Next Interview!
Practice with AI feedback & get hired faster
Personalized feedback
Used by hundreds of successful candidates
Ace Your Next Interview!
Practice with AI feedback & get hired faster
Personalized feedback
Used by hundreds of successful candidates