Top 32 Tool Worker Interview Questions and Answers [Updated 2025]
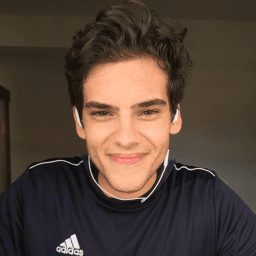
Andre Mendes
•
March 30, 2025
Are you preparing for a Tool Worker interview and eager to make a lasting impression? This blog post is your go-to resource, featuring the most common interview questions for the Tool Worker role. Dive in to find example answers and insightful tips on how to respond effectively, ensuring you stand out as a top candidate. Read on to boost your confidence and ace your interview!
Download Tool Worker Interview Questions in PDF
To make your preparation even more convenient, we've compiled all these top Tool Workerinterview questions and answers into a handy PDF.
Click the button below to download the PDF and have easy access to these essential questions anytime, anywhere:
List of Tool Worker Interview Questions
Technical Interview Questions
What safety procedures do you follow when operating cutting tools?
How to Answer
- 1
Always wear appropriate personal protective equipment such as gloves, goggles, and ear protection.
- 2
Ensure the cutting tool is in good working condition before use, checking for any damage.
- 3
Maintain a clean and organized workspace to prevent accidents.
- 4
Follow the manufacturer's instructions for operating the tool safely.
- 5
Keep hands and other body parts away from the cutting area to prevent injury.
Example Answers
I always wear gloves and goggles when using cutting tools, and I make sure the workspace is clean to avoid any hazards.
What types of tools have you worked with, and can you explain the maintenance procedures for one of them?
How to Answer
- 1
List specific tools you've used in your previous roles.
- 2
Choose one tool and explain its maintenance in simple steps.
- 3
Mention any safety procedures you follow while maintaining tools.
- 4
Highlight any relevant experience related to the tools you mention.
- 5
Be concise and ensure your explanation is clear and logical.
Example Answers
I have experience with power tools such as drills and saws, as well as hand tools like wrenches and screwdrivers. For instance, with drills, I perform maintenance by checking the battery life, cleaning the drill bits regularly, and lubricating moving parts to ensure they function smoothly.
Don't Just Read Tool Worker Questions - Practice Answering Them!
Reading helps, but actual practice is what gets you hired. Our AI feedback system helps you improve your Tool Worker interview answers in real-time.
Personalized feedback
Unlimited practice
Used by hundreds of successful candidates
How do you ensure the safe operation of heavy machinery?
How to Answer
- 1
Conduct thorough pre-operational inspections of the equipment
- 2
Always wear appropriate personal protective equipment (PPE)
- 3
Follow manufacturer guidelines and safety regulations
- 4
Maintain clear communication with team members
- 5
Stay focused and avoid distractions while operating machinery
Example Answers
I ensure the safe operation of heavy machinery by conducting a detailed inspection before each use, wearing my PPE, and following all manufacturer instructions.
Explain the steps you would take to troubleshoot a malfunctioning tool.
How to Answer
- 1
Start by identifying the tool and its specific malfunction.
- 2
Inspect the tool for any visible damage or wear.
- 3
Check the power source and connections if applicable.
- 4
Test the tool's functionality step by step to isolate the issue.
- 5
Consult the tool's manual or manufacturer guidelines if needed.
Example Answers
If a tool is malfunctioning, I would first identify which tool it is and what the symptoms of the issue are. Then, I'd inspect it for any visible damage or missing parts. Next, I would check the power source to ensure it’s connected properly. After that, I’d test various functions to see if I can pinpoint the problem. If necessary, I would refer to the tool's manual for troubleshooting tips.
What techniques do you use to ensure accurate measurements in your work?
How to Answer
- 1
Always use calibrated measuring tools to ensure precision.
- 2
Double-check measurements by measuring from different reference points.
- 3
Document measurements to track accuracy and identify discrepancies.
- 4
Stay organized by keeping tools and workspaces clean and unobstructed.
- 5
Use appropriate measuring techniques based on the material and task at hand.
Example Answers
I always start by using calibrated tools to ensure accuracy. I double-check each measurement and document them carefully to track any discrepancies.
Can you describe the properties of different materials you typically work with and how they affect tool choice?
How to Answer
- 1
Identify common materials you work with such as metals, plastics, and composites.
- 2
Discuss specific properties like hardness, flexibility, and thermal resistance.
- 3
Explain how each property influences your tool selection, such as choosing drill bits or saw blades.
- 4
Mention any specific tools you prefer for certain materials and why.
- 5
Highlight your experience with tools and how it helps in material selection.
Example Answers
In my work, I often use steel and aluminum. Steel is hard and durable, so I choose high-speed steel drill bits for it. Aluminum is softer, so I prefer using carbide bits to prevent damage. I also work with plastics, which require less aggressive tools to avoid melting.
How would you approach repairing a damaged tool while minimizing downtime?
How to Answer
- 1
Assess the type and extent of the damage quickly
- 2
Gather the necessary repair tools and parts before starting
- 3
Prioritize tasks that can minimize the overall downtime
- 4
Communicate with the team about expected timelines
- 5
Keep a checklist for future preventive maintenance
Example Answers
First, I would quickly assess the tool to identify the damage. Then I'd gather all necessary tools and parts needed for the repair. I would prioritize fixing the most critical issues and communicate with my team about how long I expect the repair to take.
How do you determine which tool is appropriate for a specific task?
How to Answer
- 1
Analyze the requirements of the task carefully.
- 2
Consider the materials you are working with.
- 3
Evaluate the precision and finish needed for the task.
- 4
Review safety considerations and tool availability.
- 5
Consult manufacturer guidelines or standards when in doubt.
Example Answers
I start by reviewing the task requirements, then assess the materials involved. For example, if I'm cutting wood, I'd choose a saw suited for that material and required finish.
What is your experience with calibrating tools to ensure they function correctly?
How to Answer
- 1
Start by defining what calibration means in a tool context
- 2
Mention specific tools you have calibrated
- 3
Explain the steps you take during the calibration process
- 4
Include any relevant measurements or standards you follow
- 5
Conclude with a result or benefit from your calibration experience
Example Answers
In my previous role, I calibrated various hand tools like calipers and micrometers by first checking their accuracy against standard gauges. I ensured the readings matched the specifications, making adjustments as necessary. This process improved measurement precision, which ultimately enhanced product quality.
What role does documentation play in your work with tools, and how do you manage it?
How to Answer
- 1
Explain how documentation ensures safety and compliance.
- 2
Discuss how it helps in tracking tool usage and maintenance.
- 3
Mention the importance of keeping records for accountability.
- 4
Describe methods you use to organize and store documentation.
- 5
Share an example of how documentation helped resolve an issue.
Example Answers
Documentation is crucial as it maintains safety protocols and ensures tools are compliant with regulations. I track all tool usage and maintenance in a shared online document, which helps our team stay accountable and organized. For instance, we once discovered a malfunctioning tool during an inspection, but our documentation allowed us to trace its last maintenance date and act quickly.
Don't Just Read Tool Worker Questions - Practice Answering Them!
Reading helps, but actual practice is what gets you hired. Our AI feedback system helps you improve your Tool Worker interview answers in real-time.
Personalized feedback
Unlimited practice
Used by hundreds of successful candidates
How frequently do you perform routine maintenance on your tools, and what does it involve?
How to Answer
- 1
Mention a regular schedule for maintenance, like weekly or monthly.
- 2
Explain specific actions you take, such as cleaning, sharpening, or lubricating tools.
- 3
Highlight the importance of maintenance for tool longevity and safety.
- 4
Use examples from your experience to describe your maintenance routine.
- 5
Conclude with a positive note on how your routine has benefited your work.
Example Answers
I perform routine maintenance on my tools every month. This involves cleaning them, sharpening blades, and lubricating moving parts. Doing this regularly helps keep my tools in top shape and ensures safety while using them.
What personal protective equipment do you consider essential for tool work?
How to Answer
- 1
Identify the specific tools you will use and potential hazards.
- 2
Mention essential PPE like safety glasses, gloves, and hearing protection.
- 3
Emphasize the importance of safety shoes and hard hats in certain environments.
- 4
Explain how PPE protects against injuries related to the specific job tasks.
- 5
Conclude with a commitment to safety and following company policies on PPE.
Example Answers
For tool work, I consider safety glasses essential to protect my eyes from flying debris, along with gloves to prevent cuts. Hearing protection is important when using loud machinery. Depending on the site, I also ensure to wear safety shoes and a hard hat for protection.
Behavioral Interview Questions
Can you describe a time when you had to work closely with a team to accomplish a project?
How to Answer
- 1
Choose a specific project that highlights teamwork.
- 2
Mention your role and how you contributed to the team.
- 3
Include any challenges the team faced and how you overcame them.
- 4
Discuss the outcome of the project and what you learned.
- 5
Emphasize cooperation and communication within the team.
Example Answers
In my last job, our team worked on a new tool implementation project. I was responsible for coordinating between the design and engineering teams. We faced issues with design mismatches, but by facilitating daily meetings and encouraging open communication, we resolved our problems quickly. The project was completed on time and improved our production efficiency by 20%.
Tell me about a challenging problem you faced while working with tools and how you resolved it.
How to Answer
- 1
Select a specific problem you've encountered with tools.
- 2
Describe the context and what made it challenging.
- 3
Explain the steps you took to resolve the issue.
- 4
Share the outcome and any lessons learned.
- 5
Keep it concise and relevant to the position.
Example Answers
I once faced a problem when the drill I was using stopped functioning during a critical project. I identified that the battery was dead, so I quickly switched to a spare battery, finished my task on time, and learned to always have backups ready.
Don't Just Read Tool Worker Questions - Practice Answering Them!
Reading helps, but actual practice is what gets you hired. Our AI feedback system helps you improve your Tool Worker interview answers in real-time.
Personalized feedback
Unlimited practice
Used by hundreds of successful candidates
Describe a situation where you had to meet a tight deadline. How did you prioritize your tasks?
How to Answer
- 1
Think of a specific deadline scenario you faced.
- 2
Outline the main tasks you needed to complete.
- 3
Explain how you evaluated the tasks' importance.
- 4
Describe the tools or methods you used to manage time.
- 5
Conclude with the outcome and any lessons learned.
Example Answers
In my previous role, we had a week to prepare for a major tool inspection. I listed all tasks, focusing on compliance checks first because they were crucial. I used a priority matrix and dedicated the first two days solely to ensure everything was in order. We successfully passed the inspection, and I learned the value of structured task management.
Have you ever taken a leadership role in a project? What did you do to ensure the project's success?
How to Answer
- 1
Select a specific project where you led a team or initiative
- 2
Highlight your leadership methods, such as communication and delegation
- 3
Discuss any challenges you faced and how you overcame them
- 4
Mention measurable outcomes or successes from the project
- 5
Reflect on what you learned from the experience
Example Answers
In my previous job, I led a team to implement a new inventory system. I organized weekly check-ins to communicate progress and address issues. Despite a tight deadline, we completed the project two weeks early, reducing errors by 30%
Can you provide an example of a time when you had to quickly adapt to a change in work conditions or tools?
How to Answer
- 1
Choose a specific example from your experience
- 2
Explain the situation and the change clearly
- 3
Describe your actions to adapt to the change
- 4
Highlight the outcome of your actions
- 5
Emphasize any skills or lessons learned
Example Answers
In my last job, we unexpectedly ran out of our usual tools. I quickly identified alternative tools in our inventory and adjusted the workflow to use them. As a result, we completed the project on time without compromising quality.
Describe a time when effective communication helped you resolve an issue at work.
How to Answer
- 1
Think of a specific situation where communication was key.
- 2
Explain the issue clearly and concisely.
- 3
Detail how you communicated with others to solve the issue.
- 4
Highlight the positive outcome that resulted from your communication.
- 5
Use the STAR method: Situation, Task, Action, Result.
Example Answers
In my last job, we had a problem with a delayed tool shipment. I called a team meeting (Situation) to discuss our backup plan (Task). I clearly communicated the impact of the delay and listened to team suggestions (Action). As a result, we implemented a successful workaround that kept our project on schedule.
Can you provide an example of a time when you went above and beyond your job duties?
How to Answer
- 1
Think of a specific situation where you took extra initiative.
- 2
Describe the challenge you faced and how you addressed it.
- 3
Emphasize the positive impact your actions had on the team or project.
- 4
Use the STAR method: Situation, Task, Action, Result.
- 5
Keep your answer concise and focused on your role and contributions.
Example Answers
In my previous role as a tool worker, we had a major project with a tight deadline. I noticed that our tool inventory was low, affecting our efficiency. I took the initiative to organize a tool audit and reached out to suppliers to expedite orders. As a result, we completed the project two days early, and my manager commended my proactive approach.
Tell me about a time when you encountered a setback. How did you overcome it?
How to Answer
- 1
Choose a specific setback related to your work or projects.
- 2
Explain the context and what led to the setback.
- 3
Describe the actions you took to address the setback.
- 4
Share the outcome and what you learned from the experience.
- 5
Focus on positive results and personal growth.
Example Answers
In a previous job, I was responsible for a tool project that fell behind schedule due to unexpected equipment failures. I organized a team meeting to identify solutions, delegated tasks effectively, and we worked overtime to catch up. As a result, we completed the project just in time, and I learned the importance of proactive communication and planning for contingencies.
Describe a situation where you had to learn a new tool or technique. How did you approach it?
How to Answer
- 1
Identify a specific tool or technique you learned.
- 2
Explain the context and why it was necessary to learn it.
- 3
Describe your learning process, including any resources used.
- 4
Mention challenges faced and how you overcame them.
- 5
Conclude with the outcome and any skills gained.
Example Answers
In my previous job, I needed to learn a new CAD software to complete a project. I enrolled in an online course and practiced with tutorials. Initially, I struggled with some features, but I reached out to colleagues for help. Ultimately, I became proficient and completed the project ahead of schedule.
Don't Just Read Tool Worker Questions - Practice Answering Them!
Reading helps, but actual practice is what gets you hired. Our AI feedback system helps you improve your Tool Worker interview answers in real-time.
Personalized feedback
Unlimited practice
Used by hundreds of successful candidates
What motivates you to excel in your role as a Tool Worker?
How to Answer
- 1
Focus on your passion for craftsmanship and quality work
- 2
Highlight the importance of teamwork and collaboration
- 3
Mention the satisfaction of problem-solving and efficiency
- 4
Discuss your commitment to safety and compliance standards
- 5
Emphasize continuous learning and skill development
Example Answers
I am motivated by my love for craftsmanship; creating high-quality tools and seeing my work directly impact our products drives me to excel.
Situational Interview Questions
If you noticed a colleague using a tool improperly, what steps would you take to address the situation?
How to Answer
- 1
Assess the situation quickly but thoroughly to ensure safety.
- 2
Approach the colleague discreetly to avoid embarrassment.
- 3
Politely explain the correct use of the tool and potential risks.
- 4
Offer assistance or resources, such as manuals or training.
- 5
Follow up to ensure the proper use is being adhered to.
Example Answers
I would first ensure that no one is in immediate danger. Then, I would approach my colleague privately and say something like, 'I noticed you were using the tool this way; it's important to use it like this instead for safety.' I would make sure to offer help if they need it.
How would you handle a situation where there is a disagreement within the team regarding tool usage?
How to Answer
- 1
Listen to both sides of the disagreement calmly to understand their perspectives
- 2
Encourage open communication among team members to discuss tool usage
- 3
Suggest finding common ground that addresses the concerns of both parties
- 4
Propose a trial period for the different approaches to see what works best
- 5
Ensure that the final decision is based on safety and efficiency in tool usage
Example Answers
In a situation of disagreement, I would first listen to both sides to understand their reasons. After that, I would facilitate a discussion to find common ground, ensuring everyone feels heard. If necessary, I would suggest a trial period to test the different approaches and see which one is more effective.
Don't Just Read Tool Worker Questions - Practice Answering Them!
Reading helps, but actual practice is what gets you hired. Our AI feedback system helps you improve your Tool Worker interview answers in real-time.
Personalized feedback
Unlimited practice
Used by hundreds of successful candidates
Suppose you're given multiple tasks with conflicting deadlines. How would you prioritize and approach each task?
How to Answer
- 1
List all tasks and their deadlines to visualize your workload
- 2
Assess the importance and urgency of each task using the Eisenhower Matrix
- 3
Communicate with stakeholders to clarify priorities if needed
- 4
Break down tasks into smaller steps and set mini-deadlines
- 5
Stay flexible and be prepared to adjust your plan based on changes
Example Answers
I would start by listing out all the tasks and their respective deadlines. Then, I would evaluate each task's importance and urgency to prioritize effectively. If I find conflicting tasks, I would communicate with my manager to understand which tasks are the highest priority. After determining priorities, I would break each task into smaller steps and set mini-deadlines for each step to stay on track.
You are running behind schedule on a tool assembly project. How do you communicate this to your supervisor?
How to Answer
- 1
Be honest and straightforward about the delay
- 2
Provide specific reasons for the delay
- 3
Suggest potential solutions or ways to catch up
- 4
Reassure about the project's overall quality and timelines
- 5
Request feedback or additional support if necessary
Example Answers
I would approach my supervisor and say, 'I've encountered some challenges that have set us back on the tool assembly project. Specifically, I experienced delays in receiving parts. However, I have a plan to address this and can expedite the assembly process by adjusting the schedule. I wanted to keep you informed.'
If you found a defect in a tool you produced, how would you proceed to fix it?
How to Answer
- 1
Identify the defect clearly and document it.
- 2
Analyze the root cause of the defect.
- 3
Communicate the issue to your supervisor or team.
- 4
Implement a fix or adjustment to address the defect.
- 5
Test the tool after the repair to ensure it meets quality standards.
Example Answers
I would first identify and document the defect to understand its nature. Then, I would analyze the root cause to prevent future occurrences. After that, I'd inform my supervisor about the issue and propose a solution. Once I fix the tool, I would conduct thorough testing to ensure it functions correctly.
If you are assigned to train a new worker on tool handling, what key points would you focus on?
How to Answer
- 1
Start with safety protocols and proper personal protective equipment usage.
- 2
Demonstrate the correct way to handle each tool, explaining its purpose.
- 3
Highlight the importance of tool maintenance and inspection.
- 4
Encourage consistent practice with supervision until proficiency is achieved.
- 5
Foster a culture of asking questions and communicating any uncertainties.
Example Answers
I would begin by emphasizing safety, ensuring they always wear appropriate PPE. Then, I'd demonstrate how to use each tool, explaining why each step is important. I would also discuss how to inspect tools for wear and tear before use.
If you were asked to use a faulty tool to complete a task, how would you respond?
How to Answer
- 1
Assess the tool to identify the specific faults
- 2
Communicate the issue clearly to your supervisor or team
- 3
Suggest alternative tools or solutions if available
- 4
Prioritize safety and effectiveness in your approach
- 5
Document the issue for future reference
Example Answers
I would quickly evaluate the tool to determine what was wrong. Then, I would inform my supervisor about the issue and suggest using a different, functional tool to complete the task safely.
If you were tasked with improving a tool's design, what factors would you consider?
How to Answer
- 1
Identify the tool's primary purpose and usage context
- 2
Consider user feedback and ergonomics for comfort
- 3
Evaluate materials for durability and weight
- 4
Assess manufacturing processes for cost-effectiveness
- 5
Look into safety features to reduce risks
Example Answers
I would first think about what the tool is primarily used for and how users interact with it. Then, user feedback would guide improvements, focusing on ergonomics for ease of use. I'd also consider using lighter but stronger materials and ensuring that the design is cost-effective to produce.
If your tool broke down during an important task, what would be your next steps?
How to Answer
- 1
Assess the situation to understand the cause of the breakdown
- 2
Communicate with your team or supervisor about the issue
- 3
Implement immediate safety measures if necessary
- 4
Determine if a backup tool is available for use
- 5
Document the incident and gather details for future reference
Example Answers
I would first stop working to assess what caused the tool to break down. Then, I would inform my supervisor about the issue and check if we have a backup tool available to continue the task safely.
Tool Worker Position Details
Recommended Job Boards
CareerBuilder
www.careerbuilder.com/jobs-tool-workerZipRecruiter
www.ziprecruiter.com/Jobs/Tool-WorkerThese job boards are ranked by relevance for this position.
Related Positions
- Shop Worker
- Track Worker
- Mill Worker
- Wheel Worker
- Table Worker
- Sand Worker
- Piece Worker
- Factory Worker
- Ship Worker
- Wireworker
Similar positions you might be interested in.
Ace Your Next Interview!
Practice with AI feedback & get hired faster
Personalized feedback
Used by hundreds of successful candidates
Ace Your Next Interview!
Practice with AI feedback & get hired faster
Personalized feedback
Used by hundreds of successful candidates