Top 30 Wooden Box Maker Interview Questions and Answers [Updated 2025]
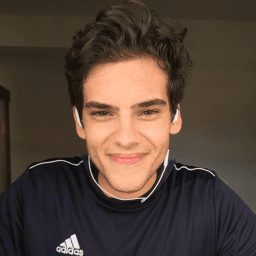
Andre Mendes
•
March 30, 2025
Are you preparing for a Wooden Box Maker job interview and want to stand out from the competition? Our updated guide for 2025 provides a comprehensive list of the most common interview questions for this unique role. Dive into expertly crafted example answers and practical tips to help you respond with confidence and precision, ensuring you make a lasting impression on potential employers.
Download Wooden Box Maker Interview Questions in PDF
To make your preparation even more convenient, we've compiled all these top Wooden Box Makerinterview questions and answers into a handy PDF.
Click the button below to download the PDF and have easy access to these essential questions anytime, anywhere:
List of Wooden Box Maker Interview Questions
Technical Interview Questions
What hand tools and power tools are essential for making wooden boxes and why?
How to Answer
- 1
Start by listing the basic hand tools and explain their uses.
- 2
Include important power tools and discuss their benefits.
- 3
Mention how each tool contributes to the quality of the wooden box.
- 4
Keep the answer concise and focused on woodworking.
- 5
Show enthusiasm for the craft and its tools.
Example Answers
For making wooden boxes, essential hand tools include a chisel for fine detailing and a hand saw for accurate cuts. Power tools like a table saw are crucial for straight cuts and speed. Each tool helps achieve precision and quality in the final product.
Describe the different types of wood joints you have experience with and their applications.
How to Answer
- 1
Mention at least three types of joints you know.
- 2
Explain the purpose of each joint briefly.
- 3
Include examples of projects where you used these joints.
- 4
Highlight any techniques or tools associated with making these joints.
- 5
Show your understanding of why certain joints are better for specific applications.
Example Answers
I have experience with mortise and tenon joints, which are strong and typically used in furniture making like tables. I also use dovetail joints for drawers due to their aesthetic appeal and strength. Lastly, I often use butt joints for simple projects, where ease of construction is important.
Don't Just Read Wooden Box Maker Questions - Practice Answering Them!
Reading helps, but actual practice is what gets you hired. Our AI feedback system helps you improve your Wooden Box Maker interview answers in real-time.
Personalized feedback
Unlimited practice
Used by hundreds of successful candidates
Explain the process you follow to finish a wooden box. What techniques do you use?
How to Answer
- 1
Start with sanding the box to create a smooth surface.
- 2
Use wood filler for any visible imperfections.
- 3
Choose the right stain or paint for the desired finish.
- 4
Apply a protective coat, like polyurethane or wax.
- 5
Always allow adequate drying time between each step.
Example Answers
First, I sand the box with multiple grits, starting coarse and finishing fine to ensure a smooth finish. Then, I fill any imperfections with wood filler. After that, I choose a suitable stain to enhance the wood's natural color before applying a couple of coats of polyurethane for protection.
How do you ensure the dimensions of the boxes are precise and accurate?
How to Answer
- 1
Use calibrated measuring tools like tape measures and calipers.
- 2
Double-check measurements before cutting materials.
- 3
Follow specifications closely for each type of box.
- 4
Maintain a clean and organized workspace to avoid errors.
- 5
Perform regular maintenance on your tools to ensure they are accurate.
Example Answers
I use calibrated measuring tools and always double-check my measurements before making cuts to ensure precision. Each box's specifications guide my process.
Can you read and interpret blueprints or plans for box designs? How do you approach this task?
How to Answer
- 1
Familiarize yourself with common symbols and notations used in blueprints
- 2
Practice interpreting different box designs from sample blueprints
- 3
Explain your step-by-step process for analyzing blueprints
- 4
Mention any tools or software you use for better accuracy
- 5
Highlight a specific example of a project where you successfully used blueprints
Example Answers
Yes, I can read and interpret blueprints for box designs. I look for key dimensions and materials first, and then I analyze the details of the design. For example, I once built a custom box by carefully following the blueprint specifications, ensuring all joints were aligned perfectly.
What machinery are you proficient in using for woodworking and why?
How to Answer
- 1
List specific machines you have experience with like table saws, routers, or sanders.
- 2
Explain how you have used each machine in past projects.
- 3
Mention any maintenance or safety protocols you follow while using machinery.
- 4
Highlight any specialized skills, such as joinery or finishing techniques.
- 5
Connect your experience with the requirements of the Wooden Box Maker position.
Example Answers
I am proficient in using table saws and routers. I use the table saw for precise cuts on the wood pieces, ensuring accurate dimensions for my boxes. I follow all safety protocols and perform regular maintenance on the machinery to keep everything in good condition.
How do you deal with common issues like warping or splitting in wood?
How to Answer
- 1
Identify the cause of warping or splitting, such as moisture or temperature changes.
- 2
Use proper wood storage techniques to minimize exposure to fluctuating conditions.
- 3
Select quality wood and allow it to acclimate to the environment before use.
- 4
Consider applying wood stabilizers or finish to protect the surface.
- 5
In case of existing issues, use techniques like humidification or controlled drying to rectify them.
Example Answers
I first identify if the warping is due to moisture imbalance. I make sure to store the wood in a stable environment and allow it to acclimate. If warping occurs, I might use humidification to straighten it if possible.
What safety procedures do you follow when operating woodworking equipment?
How to Answer
- 1
Always wear appropriate personal protective equipment like gloves and goggles.
- 2
Ensure that all safety guards are in place before starting any machinery.
- 3
Keep the work area clean and free of clutter to avoid accidents.
- 4
Follow the operating manual and manufacturer's guidelines for each machine.
- 5
Never remove safety features or override safety mechanisms.
Example Answers
I always wear my gloves and goggles and check that all the safety guards are in place before using any equipment.
What measurement tools do you regularly use, and how do you ensure their accuracy?
How to Answer
- 1
List specific tools like rulers, calipers, and squares you use regularly.
- 2
Explain how you check the calibration of each tool.
- 3
Mention best practices for maintaining tools, like cleaning and storing properly.
- 4
Include examples of how accurate measurements influence your work.
- 5
Discuss any personal methods you employ to double-check measurements.
Example Answers
I regularly use a combination of calipers and a square. I ensure their accuracy by calibrating them before each project and always storing them in a protective case. Accurate measurements are crucial for fitting parts precisely.
What types of wood do you prefer for making durable boxes and why?
How to Answer
- 1
Mention specific types of wood known for durability
- 2
Explain the characteristics that make these woods suitable
- 3
Include any personal experience with these woods if applicable
- 4
Consider mentioning sustainability and sourcing
- 5
Stay concise and focus on practicality in box-making
Example Answers
I prefer using oak and maple for durable boxes. Oak is strong and resistant to wear, while maple has a fine grain that looks beautiful and holds up well over time.
Don't Just Read Wooden Box Maker Questions - Practice Answering Them!
Reading helps, but actual practice is what gets you hired. Our AI feedback system helps you improve your Wooden Box Maker interview answers in real-time.
Personalized feedback
Unlimited practice
Used by hundreds of successful candidates
Behavioral Interview Questions
Can you tell me about a time when your attention to detail saved a project from going wrong?
How to Answer
- 1
Identify a specific project where attention to detail was crucial.
- 2
Describe the mistake or potential issue that arose.
- 3
Explain the specific actions you took to address the issue.
- 4
Highlight the positive outcome resulting from your attention to detail.
- 5
Keep it concise and focused on your role in the situation.
Example Answers
In my previous job, we were building a custom wooden box for a client. I noticed that the measurements were slightly off before we started cutting. I double-checked our plans and caught an error in the dimensions. I corrected it, which saved us from wasting materials and time, ensuring the box was perfect for delivery.
Describe a complex problem you faced in your previous work and how you approached solving it.
How to Answer
- 1
Identify a specific complex problem you encountered.
- 2
Explain the context and impact of the problem clearly.
- 3
Outline the steps you took to analyze and solve the problem.
- 4
Highlight the skills or tools you used in your approach.
- 5
Reflect on the outcome and what you learned from the experience.
Example Answers
In my last job as a wooden box maker, we faced a consistent issue with the quality of joints, which led to product returns. I analyzed our joining techniques and discovered that our adhesive wasn't ideal for the humidity levels in our workshop. I researched alternatives, tested a new adhesive, and implemented it across the team. As a result, our joint failures decreased by 50% in three months, and we received positive feedback from clients.
Don't Just Read Wooden Box Maker Questions - Practice Answering Them!
Reading helps, but actual practice is what gets you hired. Our AI feedback system helps you improve your Wooden Box Maker interview answers in real-time.
Personalized feedback
Unlimited practice
Used by hundreds of successful candidates
Give an example of how you collaborated with others to complete a project on time.
How to Answer
- 1
Think of a specific project where teamwork was essential.
- 2
Describe your role and contributions clearly.
- 3
Highlight communication methods used with your team.
- 4
Emphasize any tools or techniques that facilitated your collaboration.
- 5
Conclude with the outcome and how it met the deadline.
Example Answers
In my previous job, we had a deadline to deliver 50 custom wooden boxes for a client. I coordinated with two carpenters and a designer. We held daily briefings to track our progress and used a shared calendar to assign tasks. I focused on cutting and assembling while ensuring everyone was aligned. As a result, we finished the project two days ahead of schedule.
Tell me about a time when you had to quickly learn a new skill or technique.
How to Answer
- 1
Choose a specific skill relevant to woodworking or craftsmanship.
- 2
Describe the context: what was the situation that required fast learning.
- 3
Explain how you approached learning the skill or technique.
- 4
Highlight the outcome: what did you achieve by learning this skill.
- 5
Reflect on what you learned from the experience.
Example Answers
In my previous job, I needed to learn how to use a CNC machine for precision cuts. The project had a tight deadline, so I watched tutorials and practiced on a machine after hours. I successfully completed the project on time, which impressed my supervisor and helped me secure more responsibilities.
Describe a situation where you had a conflict with a colleague and how you resolved it.
How to Answer
- 1
Choose a specific conflict that illustrates your problem-solving skills.
- 2
Focus on your role in the situation and how you took initiative.
- 3
Explain the steps you took to communicate and resolve the issue.
- 4
Highlight the positive outcome or lesson learned from the experience.
- 5
Keep it professional and avoid speaking negatively about the colleague.
Example Answers
In a recent project, I disagreed with a colleague about the design of a wooden box. We discussed our perspectives openly, and I suggested we each present our ideas to the team. This led to a constructive discussion and we ultimately combined the best elements from both designs, improving the final product.
Can you give an example of a creative way you solved a challenge in a project?
How to Answer
- 1
Identify a specific challenge you faced in a project.
- 2
Explain the creative solution you implemented to overcome that challenge.
- 3
Highlight the impact of your solution on the project outcome.
- 4
Be concise and focus on your thought process and innovation.
- 5
Use concrete examples related to woodworking or box making if possible.
Example Answers
During a project to create custom wooden boxes, I faced a challenge with intricate designs that were hard to cut. I solved this by designing a jig that allowed me to accurately profile the wood while keeping my hands safe. This not only improved our output but also ensured precision in every cut.
How do you prioritize tasks when you are given multiple deadlines?
How to Answer
- 1
List all tasks and deadlines to visualize the workload
- 2
Assess the urgency and importance of each task
- 3
Break tasks into smaller steps to simplify management
- 4
Communicate with your team about any potential conflicts
- 5
Use a planner or digital tool to track progress and adjust as needed
Example Answers
I start by listing all my tasks and their respective deadlines. Then, I evaluate which tasks are most urgent and important. I break larger tasks down into smaller ones to make them manageable and ensure I meet deadlines. If I foresee a conflict, I discuss it with my team to find solutions.
Describe a time when you identified a safety hazard and how you handled it.
How to Answer
- 1
Think of a specific incident where you noticed a safety issue.
- 2
Explain clearly what the hazard was and why it was dangerous.
- 3
Describe the actions you took to resolve or mitigate the hazard.
- 4
Mention any protocols you followed, if applicable.
- 5
Highlight the outcome and what you learned from the experience.
Example Answers
During my time at XYZ Company, I noticed that several power tools were not properly secured, posing a tripping hazard. I immediately reported this to my supervisor and we conducted an inspection to secure and organize the tools. This reduced accidents and improved safety protocols in our workshop.
How do you ensure the quality of your work, especially when under tight deadlines?
How to Answer
- 1
Prioritize essential tasks to maintain focus on high-quality outputs.
- 2
Use checklists to ensure all critical quality measures are met before completion.
- 3
Implement a brief review process after completing each project.
- 4
Avoid multitasking to minimize errors and maintain attention to detail.
- 5
Communicate proactively with the team to address any quality concerns early.
Example Answers
I prioritize essential tasks and focus on the quality of the most critical aspects. I always use a checklist to ensure all quality measures are met before finalizing my work, even under tight deadlines.
Don't Just Read Wooden Box Maker Questions - Practice Answering Them!
Reading helps, but actual practice is what gets you hired. Our AI feedback system helps you improve your Wooden Box Maker interview answers in real-time.
Personalized feedback
Unlimited practice
Used by hundreds of successful candidates
Situational Interview Questions
You are running behind on a major order due to a materials shortage. What steps would you take to handle this situation?
How to Answer
- 1
Assess the current inventory and identify which materials are short.
- 2
Contact suppliers to expedite the delivery of required materials.
- 3
Communicate promptly with your customer about potential delays and expected timelines.
- 4
Explore alternative materials or adjustments in design that meet specifications.
- 5
Consider reallocating resources or increasing work hours to catch up once materials are received.
Example Answers
First, I would check our inventory to identify exactly which materials are lacking. Then I would contact our suppliers to find out when we could expect a shipment. I would also inform the customer about the situation and provide an updated timeline. If the materials won't arrive soon, I would look into alternative options that still meet their requirements.
You discover a defect in a batch of boxes that are about to be shipped. How do you address this problem?
How to Answer
- 1
Immediately inform your supervisor about the defect.
- 2
Assess the extent of the defect and identify affected boxes.
- 3
Implement a solution to fix or discard the defective boxes.
- 4
Communicate with the shipping department to delay shipment if necessary.
- 5
Document the defect and any actions taken for quality control.
Example Answers
First, I would inform my supervisor about the defect to ensure transparency. Then, I would inspect the entire batch to determine how many boxes are affected. After that, I would either repair or remove the defective boxes from the shipment. If needed, I would notify the shipping department to delay shipment until the issue is resolved. Finally, I would document the incident for future reference.
Don't Just Read Wooden Box Maker Questions - Practice Answering Them!
Reading helps, but actual practice is what gets you hired. Our AI feedback system helps you improve your Wooden Box Maker interview answers in real-time.
Personalized feedback
Unlimited practice
Used by hundreds of successful candidates
A client requests a custom design that you've never made before. How do you approach this request?
How to Answer
- 1
Listen carefully to the client's ideas and requirements
- 2
Ask clarifying questions to fully understand their vision
- 3
Research similar designs for inspiration or techniques
- 4
Create a prototype or sketch to present to the client
- 5
Maintain clear communication throughout the process
Example Answers
I would start by discussing the client's vision in detail, asking questions to clarify their ideas. Then, I'd research similar designs and techniques to gain insights. Once I have enough information, I would create a rough sketch of the design to ensure it meets their expectations before proceeding.
If your usual supplier is unable to deliver wood on time, how would you manage this issue?
How to Answer
- 1
Assess the urgency of the project and required materials
- 2
Reach out to alternative suppliers to confirm availability
- 3
Communicate with your team or clients about potential delays
- 4
Consider adjusting project timelines if necessary
- 5
Evaluate the reasons for the original supplier's delay to avoid future issues
Example Answers
I would first assess which projects were affected and the level of urgency. Then, I'd contact alternative suppliers to see if they have the materials I need. I'd also keep my team informed about the potential delays.
A critical tool breaks during production. What is your plan to minimize downtime?
How to Answer
- 1
Assess the situation quickly to understand the impact of the breakdown.
- 2
Have a contingency plan in place for tool replacements or repairs.
- 3
Communicate with the team about the issue and next steps.
- 4
Check inventory for spare tools that can be used immediately.
- 5
Document the incident to prevent future occurrences.
Example Answers
First, I would assess which tool broke and how it affects production. If possible, I'd use a backup tool while arranging for repairs or replacements. I'd also inform my team to adjust workflow accordingly.
Midway through a project, a client asks for a significant design change. How would you handle this?
How to Answer
- 1
Acknowledge the client's request and show understanding of their needs
- 2
Assess the impact of the design change on the timeline and budget
- 3
Communicate openly about potential implications and additional costs
- 4
Collaborate with the client to find a balanced solution that meets their needs
- 5
Document the changes and confirm the agreement before proceeding
Example Answers
I would start by acknowledging the client's request, ensuring they feel heard. Then, I would evaluate how the change affects our current timeline and budget. After that, I would discuss these factors with the client to agree on the best way to move forward, making sure to document everything clearly.
Your workload increases unexpectedly. How would you adjust your workflow to maintain quality and deadlines?
How to Answer
- 1
Prioritize tasks based on deadlines and complexity
- 2
Communicate with your team about the increased workload
- 3
Break tasks into smaller, manageable steps
- 4
Stay organized using tools for tracking progress
- 5
Consider adjusting your schedule to accommodate peak workload
Example Answers
I would first assess and prioritize my tasks to focus on those that are due soonest or are most complex. I would communicate with my team to ensure we're aligned and might delegate where possible. Breaking down larger tasks would help manage workloads effectively.
You notice a dip in morale among your team. What actions would you take to address this issue?
How to Answer
- 1
Identify specific issues causing low morale through one-on-one conversations.
- 2
Organize team-building activities to strengthen relationships and communication.
- 3
Encourage open feedback where team members can express concerns comfortably.
- 4
Provide recognition for individual and team achievements to boost spirits.
- 5
Implement small changes based on feedback to show responsiveness and care.
Example Answers
I would start by talking to team members individually to understand their concerns. Based on their feedback, I could organize a team-building event to help us reconnect and work better together.
You need to quickly learn a new technique to meet a project requirement. How would you go about this?
How to Answer
- 1
Identify the specific technique you need to learn.
- 2
Research the technique through online resources or videos.
- 3
Practice the technique with small projects or mock tasks.
- 4
Reach out to colleagues or network contacts who are experienced in this area.
- 5
Reflect on your learning and apply it directly to the project.
Example Answers
First, I would pinpoint the exact technique I need to learn, then dive into online tutorials and videos to understand the basics. Next, I would practice with a small wooden box project to apply what I've learned. Finally, if needed, I would consult with a colleague who has experience with this technique for tips.
Upon inspection, you find that some boxes don't meet the quality standards. What steps do you take to rectify the situation?
How to Answer
- 1
Identify specific quality issues with the boxes.
- 2
Assess the root cause of the quality problems.
- 3
Implement immediate corrective actions to address the issues.
- 4
Document the findings and solutions for future reference.
- 5
Communicate with the team about the quality standards and any changes.
Example Answers
First, I would carefully identify the specific issues with the boxes, such as uneven edges or weak joints. Then, I would analyze how these problems occurred, possibly looking at production processes or material quality. After that, I would take corrective actions like reworking the defective boxes or adjusting the machinery settings. I would also document what I found and share the information with my team to prevent recurrence.
Don't Just Read Wooden Box Maker Questions - Practice Answering Them!
Reading helps, but actual practice is what gets you hired. Our AI feedback system helps you improve your Wooden Box Maker interview answers in real-time.
Personalized feedback
Unlimited practice
Used by hundreds of successful candidates
Wooden Box Maker Position Details
Recommended Job Boards
CareerBuilder
www.careerbuilder.com/jobs/wood-box-makerZipRecruiter
www.ziprecruiter.com/Jobs/Wood-Box-MakerThese job boards are ranked by relevance for this position.
Related Positions
- Woodworker
- Cabinetmaker
- Box Worker
- Crate Maker
- Furniture Assembler
- Piano Maker
- Bed Maker
- Mat Maker
- Body Maker
- Barrel Maker
Similar positions you might be interested in.
Ace Your Next Interview!
Practice with AI feedback & get hired faster
Personalized feedback
Used by hundreds of successful candidates
Ace Your Next Interview!
Practice with AI feedback & get hired faster
Personalized feedback
Used by hundreds of successful candidates