Top 30 Battery Filler Interview Questions and Answers [Updated 2025]
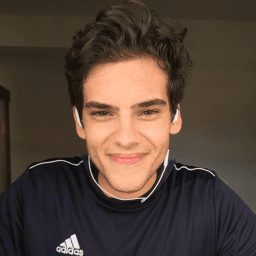
Andre Mendes
•
March 30, 2025
Preparing for a Battery Filler interview and want to stand out? This blog post has you covered with a comprehensive list of the most common interview questions tailored for the Battery Filler role. Dive into expertly crafted example answers and insightful tips that will help you respond confidently and effectively. Whether you're a seasoned professional or new to the field, this guide is designed to boost your interview performance.
Download Battery Filler Interview Questions in PDF
To make your preparation even more convenient, we've compiled all these top Battery Fillerinterview questions and answers into a handy PDF.
Click the button below to download the PDF and have easy access to these essential questions anytime, anywhere:
List of Battery Filler Interview Questions
Behavioral Interview Questions
Can you describe a time when you had to work closely with a team to accomplish a goal as a battery filler?
How to Answer
- 1
Identify a specific project or task where teamwork was crucial.
- 2
Highlight your role and responsibilities within the team.
- 3
Mention the goal you were aiming to achieve together.
- 4
Explain any challenges the team faced and how you overcame them.
- 5
Conclude with the positive outcome and what you learned from the experience.
Example Answers
In my previous position, our team worked on a project to improve the efficiency of battery filling. I was responsible for monitoring the filling process and ensuring quality control. We aimed to reduce filling time by 10%. We faced challenges with equipment malfunctions, but by collaborating closely, we quickly repaired the issues and trained everyone on the backup procedures. As a result, we successfully reduced the filling time by 15%, and I learned the importance of communication in problem-solving.
Tell me about a time when you faced a significant challenge while filling batteries. How did you overcome it?
How to Answer
- 1
Identify a specific challenge in battery filling.
- 2
Explain the steps you took to address the issue.
- 3
Highlight teamwork or communication if applicable.
- 4
Discuss the outcome and any lessons learned.
- 5
Keep your answer focused and concise.
Example Answers
At my previous job, we faced a supply shortage of batteries. I quickly organized a team meeting to assess our options, and we decided to reach out to alternative suppliers. Through effective communication, we secured necessary materials and met our deadlines. This taught us the importance of proactive supplier relationships.
Don't Just Read Battery Filler Questions - Practice Answering Them!
Reading helps, but actual practice is what gets you hired. Our AI feedback system helps you improve your Battery Filler interview answers in real-time.
Personalized feedback
Unlimited practice
Used by hundreds of successful candidates
Give an example of a situation where your attention to detail made a significant difference in your work as a battery filler.
How to Answer
- 1
Identify a specific incident where details were crucial.
- 2
Explain the actions you took due to your attention to detail.
- 3
Describe the positive outcome that resulted from your actions.
- 4
Highlight how this experience has influenced your approach to work.
- 5
Keep the answer focused on your individual contribution.
Example Answers
In my previous job, I noticed a small leak in the battery cell during the filling process. I immediately reported it and corrected the issue before it led to a waste of materials. This attention to detail saved the company both time and costs.
Describe an experience where you had to ensure safety protocols were followed while working with batteries.
How to Answer
- 1
Think of a specific incident where battery safety was crucial.
- 2
Highlight your knowledge of safety protocols related to batteries.
- 3
Explain your actions to ensure compliance with safety measures.
- 4
Emphasize teamwork and communication in enforcing safety.
- 5
Conclude with the outcome that resulted from following these protocols.
Example Answers
In my previous role at the warehouse, I noticed a colleague bypassing the battery charging procedure. I reminded them of the proper safety measures, such as wearing protective gear and following the charging time guidelines. We then ensured that everyone on the team understood the protocols, which prevented any potential accidents.
Describe a time when you had to learn a new technique for battery filling. How did you approach it?
How to Answer
- 1
Identify a specific instance when you learned a new battery filling technique.
- 2
Explain the steps you took to understand the technique thoroughly.
- 3
Mention any resources or support you sought during the learning process.
- 4
Describe how you applied the new technique in your work.
- 5
Reflect on the outcome and what you learned from the experience.
Example Answers
In my previous job, I had to learn a new automated battery filling system. I approached it by first reading the manuals and watching instructional videos provided by the manufacturer. I also collaborated with a colleague who was experienced in using the system. After a week of practice under supervision, I successfully operated the system independently, which increased our production efficiency by 20%.
Give an example of how you have effectively communicated with other departments (like shipping or quality control) while filling batteries.
How to Answer
- 1
Share a specific situation where you needed coordination with another department.
- 2
Highlight the communication method used, such as email, meetings, or reports.
- 3
Emphasize the importance of clear information exchange to avoid errors.
- 4
Show how your actions improved the process or resolved issues.
- 5
Mention any follow-up actions you took to ensure continued collaboration.
Example Answers
In my previous role, we needed to ensure that the battery filling process met quality standards. I scheduled weekly meetings with the quality control team to discuss any issues, allowing us to address concerns immediately. This open line of communication helped reduce defects by 15%.
Can you describe a conflict you experienced at work related to battery filling and how you resolved it?
How to Answer
- 1
Identify a specific conflict related to battery filling.
- 2
Focus on your role in the situation and actions taken.
- 3
Highlight communication as a key to resolution.
- 4
Mention a positive outcome resulting from the resolution.
- 5
Keep it concise and relevant to the position.
Example Answers
In my previous role, there was a disagreement with a colleague about the proper filling levels for batteries. I proposed we meet to discuss our processes, and during our discussion, we discovered that one of us was misinterpreting the guidelines. After clarifying the guidelines together, we agreed on a standard, which improved our filling accuracy and teamwork.
Tell me about a time when you went beyond your normal duties as a battery filler to ensure quality or safety.
How to Answer
- 1
Think of a specific incident where you identified a potential quality or safety issue.
- 2
Describe the actions you took that were outside your standard responsibilities.
- 3
Focus on the impact of your actions on the team or the overall product quality.
- 4
Use the STAR method: Situation, Task, Action, Result.
- 5
Keep your answer concise and relevant to battery filling.
Example Answers
In my previous job as a battery filler, I noticed a batch of batteries had inconsistent weights. I took the initiative to individually check and record each one, which revealed a malfunctioning scale. By reporting this and recalibrating the equipment, we ensured the entire batch met quality standards.
What motivates you to excel as a battery filler, and how do you maintain that motivation?
How to Answer
- 1
Identify personal connections to the job or industry.
- 2
Emphasize the importance of teamwork and collaboration.
- 3
Discuss personal growth and skill development related to the role.
- 4
Mention setting goals and celebrating achievements.
- 5
Talk about the role of quality and precision in your work.
Example Answers
I am motivated by my passion for renewable energy and the role batteries play in it. I maintain my motivation by setting daily goals and celebrating when I meet them, which keeps me focused.
Don't Just Read Battery Filler Questions - Practice Answering Them!
Reading helps, but actual practice is what gets you hired. Our AI feedback system helps you improve your Battery Filler interview answers in real-time.
Personalized feedback
Unlimited practice
Used by hundreds of successful candidates
Technical Interview Questions
What are the key differences between lead-acid batteries and lithium-ion batteries in terms of filling?
How to Answer
- 1
Explain that lead-acid batteries need water topping regularly but lithium-ion batteries do not require this.
- 2
Mention that lead-acid batteries may need to be filled with electrolyte during maintenance, lithium-ion typically comes pre-filled.
- 3
Discuss the safety considerations in handling both types during filling processes.
- 4
Highlight the environmental impact of both types and how their recycling differs after use.
- 5
Emphasize the weight and density differences affecting storage and handling during filling.
Example Answers
Lead-acid batteries require regular topping with distilled water and might need electrolyte maintenance, while lithium-ion batteries come sealed and do not need any filling during their lifespan.
Can you explain how to properly operate filling equipment used for batteries?
How to Answer
- 1
Understand the specific type of filling equipment being used and its components
- 2
Follow safety protocols and wear appropriate personal protective equipment
- 3
Check the filling equipment for cleanliness and functionality before use
- 4
Calibrate the equipment as needed to ensure accurate filling
- 5
Monitor the filling process to prevent overfilling and ensure quality control.
Example Answers
To operate battery filling equipment, first ensure you are wearing the necessary safety gear. Then, check the equipment to confirm it is clean and in good working order. Calibrate it according to the manufacturer's instructions, and during operation, closely monitor the filling levels to prevent overfilling.
Don't Just Read Battery Filler Questions - Practice Answering Them!
Reading helps, but actual practice is what gets you hired. Our AI feedback system helps you improve your Battery Filler interview answers in real-time.
Personalized feedback
Unlimited practice
Used by hundreds of successful candidates
What quality control measures do you think are essential when filling batteries?
How to Answer
- 1
Ensure proper cleanliness of the filling area to prevent contamination.
- 2
Implement checks for correct electrolyte levels and specific gravity during the filling process.
- 3
Use calibrated filling equipment to ensure accurate volumes of electrolyte are added.
- 4
Conduct regular inspections of the filled batteries for leaks or defects before sealing.
- 5
Maintain detailed records of each batch for traceability and quality assessment.
Example Answers
I believe essential quality control measures include keeping the filling area clean, checking the electrolyte levels with a hydrometer, and using calibrated equipment for volume accuracy. Additionally, all batteries should be inspected for leaks before final capping.
How would you troubleshoot a malfunctioning battery filling machine?
How to Answer
- 1
Check the machine's power supply and ensure it's connected properly.
- 2
Examine the filling nozzles for blockages or leaks.
- 3
Inspect the settings and calibration to ensure accuracy.
- 4
Review error codes or indicators on the control panel.
- 5
Run a test cycle to see if the malfunction persists and identify patterns.
Example Answers
I would start by checking if the machine is powered on and correctly plugged in. Then I would look at the nozzles for any clogs. After that, I’d verify the machine settings to make sure they are correct.
What is the standard procedure for filling a battery to ensure optimal performance?
How to Answer
- 1
Identify the specific type of battery being filled
- 2
Ensure safety protocols are in place before handling batteries
- 3
Use the correct electrolyte or acid as per manufacturer specifications
- 4
Fill the battery to the designated level without overfilling
- 5
Regularly check and maintain the battery to ensure longevity
Example Answers
To fill a battery properly, I first confirm the type of battery and then follow safety guidelines. I use the recommended electrolyte, fill it to the right level, and avoid overfilling to ensure performance.
What safety precautions should be taken when handling battery acid during the filling process?
How to Answer
- 1
Wear appropriate personal protective equipment, including gloves, goggles, and a face shield.
- 2
Handle battery acid in a well-ventilated area to avoid inhaling harmful fumes.
- 3
Use appropriate containers and tools specifically designed for battery acid to prevent spills.
- 4
Keep neutralizing agents, like baking soda, accessible in case of accidental spills.
- 5
Ensure that emergency washing stations are readily available for immediate response.
Example Answers
I would ensure to wear gloves and goggles while filling the battery acid to protect my skin and eyes. I would also do this in a ventilated area to minimize inhalation of any fumes.
What regulations must be adhered to when filling batteries in your region?
How to Answer
- 1
Research local and federal regulations regarding battery filling.
- 2
Mention safety standards, such as those from OSHA or EPA.
- 3
Discuss environmental regulations regarding battery disposal.
- 4
Highlight any training or certifications required for handling battery chemicals.
- 5
Be aware of specific manufacturer guidelines for battery types.
Example Answers
In my region, we must adhere to OSHA safety standards, which involve proper personal protective equipment and training. We also follow EPA regulations for handling hazardous materials, ensuring safe disposal of any waste.
How would you perform basic maintenance on the battery filling equipment?
How to Answer
- 1
Check the equipment for any visible damage or wear before use.
- 2
Clean the filling nozzles and hoses regularly to prevent blockages.
- 3
Inspect the fluid levels and refill as necessary to ensure proper operation.
- 4
Test the pressure settings and adjust if needed for optimal performance.
- 5
Record any maintenance actions taken to keep a log of upkeep.
Example Answers
I would start by visually inspecting the equipment for any damage. Then, I would clean the nozzles and hoses to ensure they are free from blockages. I would check the fluid levels and refill them as required.
What materials do you typically work with when filling batteries, and what are their properties?
How to Answer
- 1
Identify the main types of batteries you fill.
- 2
Explain the materials used, such as electrolyte solutions and separators.
- 3
Describe the properties of these materials, like viscosity and conductivity.
- 4
Mention safety precautions when handling materials.
- 5
Relate your experience with these materials to specific tasks or outcomes.
Example Answers
I typically work with lead-acid batteries, where I use sulfuric acid as the electrolyte. Sulfuric acid has good conductivity but is highly corrosive, so I always wear protective gear. I also use plastic separators to prevent short-circuits, which are important for maintaining battery efficiency.
How do you ensure that the correct amount of electrolyte is filled in the batteries?
How to Answer
- 1
Use a measuring tool like a graduated cylinder for accuracy
- 2
Follow the manufacturer’s specifications for electrolyte levels
- 3
Inspect the battery visually for any signs of overfilling or underfilling
- 4
Double-check measurements before sealing the battery
- 5
Maintain a clean workspace to avoid contamination
Example Answers
I always use a graduated cylinder to measure the electrolyte, ensuring it matches the manufacturer’s specifications exactly. This helps me avoid overfilling or underfilling the battery.
Don't Just Read Battery Filler Questions - Practice Answering Them!
Reading helps, but actual practice is what gets you hired. Our AI feedback system helps you improve your Battery Filler interview answers in real-time.
Personalized feedback
Unlimited practice
Used by hundreds of successful candidates
What documentation do you keep when filling batteries to ensure compliance and traceability?
How to Answer
- 1
Mention the specific types of records you maintain.
- 2
Include details about safety inspections and compliance checks.
- 3
Explain how you log battery serial numbers and batch numbers.
- 4
Discuss any electronic systems or logs used for tracking.
- 5
Highlight the importance of these documents for regulatory compliance.
Example Answers
I keep a log of battery serial numbers, batch numbers, and the date of filling to ensure traceability. I also maintain records of safety inspections and compliance checks to meet regulatory standards.
Situational Interview Questions
If you notice a potential chemical leak while filling batteries, what steps would you take?
How to Answer
- 1
Immediately stop the filling process and evacuate the area.
- 2
Alert your supervisor or the designated safety officer.
- 3
Identify the source of the leak if it is safe to do so.
- 4
Use appropriate personal protective equipment (PPE) while dealing with the leak.
- 5
Follow the company’s emergency procedures for chemical spills.
Example Answers
If I notice a potential leak, I would first stop filling and evacuate anyone nearby. Then, I would immediately notify my supervisor and ensure that the area is safe. If I can do so safely, I would examine the leak source, using appropriate PPE, and follow our emergency protocol.
In the event of an unexpected power outage during battery filling, how would you handle the situation?
How to Answer
- 1
Ensure the safety of yourself and others first.
- 2
Follow emergency protocols established by the facility.
- 3
Secure the filling machinery to prevent any accidents.
- 4
Check the status of the filling process and document what happened.
- 5
Communicate with supervisors and team members about the outage.
Example Answers
I would first prioritize safety by ensuring everyone is safe and the area is secure. Then, I would follow our emergency protocols to shut down the filling machinery properly. After that, I would document the status of the process before the outage and notify my supervisor about the situation.
Don't Just Read Battery Filler Questions - Practice Answering Them!
Reading helps, but actual practice is what gets you hired. Our AI feedback system helps you improve your Battery Filler interview answers in real-time.
Personalized feedback
Unlimited practice
Used by hundreds of successful candidates
How would you deal with a team member who is consistently making mistakes during the filling process?
How to Answer
- 1
Observe the team member's process to identify specific mistakes
- 2
Communicate directly and respectfully about the mistakes
- 3
Offer assistance and share best practices to improve their skills
- 4
Encourage a culture of learning from mistakes rather than punishment
- 5
Follow up to check progress and provide ongoing support
Example Answers
I would first observe the team member's filling process to pinpoint where the mistakes are occurring. Then, I would have a direct but friendly conversation with them about these errors and offer to help them improve their technique, sharing some tips I've found effective. Finally, I'd check in with them after some time to see how they are progressing.
You are behind schedule on your filling targets due to equipment failure. How would you prioritize your tasks?
How to Answer
- 1
Assess the situation and identify the critical tasks needed to resume filling.
- 2
Communicate with your team about the equipment failure and ask for input on solutions.
- 3
Focus on repairing or replacing the failed equipment as the highest priority.
- 4
Reallocate resources or shift team members to assist with the critical tasks.
- 5
Monitor progress closely and adjust your plan as needed to meet the targets.
Example Answers
First, I would assess the equipment failure to understand the impact. Then, I’d prioritize fixing the equipment immediately. I would involve my team for their insights and support, reallocating resources to ensure we can resume filling as quickly as possible while keeping everyone informed.
How would you approach a situation where a client demands a specific filling specification that is not standard?
How to Answer
- 1
Listen carefully to the client's requirements and clarify any misunderstandings.
- 2
Explain the standard specifications and why they are important for safety and performance.
- 3
Discuss the implications of deviating from standard specifications, including risks and potential costs.
- 4
Explore alternatives that could meet the client's needs within standard guidelines.
- 5
If necessary, propose a plan to test the requested specification while ensuring compliance with safety standards.
Example Answers
I would first listen to the client's specific requirements to ensure I understand what they need. Then, I'd explain our standard filling specifications and their importance for performance. I would discuss any risks of deviating from these standards and suggest alternative solutions that align with our guidelines.
If you filled a battery incorrectly and it has gone out to a customer, what would be your next steps?
How to Answer
- 1
Acknowledge the mistake and take responsibility
- 2
Immediately inform your supervisor about the issue
- 3
Gather all relevant information about the batch and affected customers
- 4
Coordinate a recall or corrective action plan if necessary
- 5
Communicate transparently with the affected customers
Example Answers
First, I would acknowledge the error and inform my supervisor right away. Then, I would collect all the details about the specific batch and identify which customers received the products. Next, I would work with my team to develop a plan to correct the mistake, such as organizing a recall if needed, and ensure that we communicate clearly with the impacted customers about how we will resolve the issue.
If you identify a more efficient way to fill batteries, how would you propose this change to your manager?
How to Answer
- 1
Clearly outline the current process and its limitations.
- 2
Present your proposed method with specific benefits.
- 3
Use data or examples to support your proposal.
- 4
Suggest a trial implementation to test effectiveness.
- 5
Be open to feedback and further discussion.
Example Answers
I've noticed that our current filling method takes longer than necessary due to manual checks. I propose we automate the monitoring process with a sensor system, which could reduce filling time by up to 30%. I can run a small-scale test to illustrate the potential savings.
How would you manage your schedule if you have to fill batteries and also train new employees at the same time?
How to Answer
- 1
Prioritize your tasks based on urgency and importance
- 2
Allocate specific time blocks for battery filling and training
- 3
Use a checklist to track progress on both tasks
- 4
Communicate with your team about your schedule
- 5
Be flexible to adjust your plan if unexpected issues arise
Example Answers
I would start by prioritizing my responsibilities, ensuring that I have designated time each day for both filling batteries and training. I would create a daily checklist to monitor my progress in both areas.
How would you handle high-pressure situations where production demands increase suddenly?
How to Answer
- 1
Stay calm and focused to think clearly.
- 2
Prioritize tasks based on urgency and importance.
- 3
Communicate with your team to ensure everyone is aligned.
- 4
Utilize available resources efficiently to meet demands.
- 5
Reflect on past experiences to apply effective strategies.
Example Answers
In high-pressure situations, I remain calm and assess what needs to be prioritized. I communicate with my team to make sure we're all on the same page and can tackle the increased demand efficiently.
Battery Filler Position Details
Related Positions
- Battery Loader
- Battery Hand
- Padder
- Button Puncher
- Impregnator
- Starter
- Carbonizer
- Soap Mixer
- Soap Boiler
- Buffer
Similar positions you might be interested in.
Ace Your Next Interview!
Practice with AI feedback & get hired faster
Personalized feedback
Used by hundreds of successful candidates
Ace Your Next Interview!
Practice with AI feedback & get hired faster
Personalized feedback
Used by hundreds of successful candidates