Top 31 Soap Boiler Interview Questions and Answers [Updated 2025]
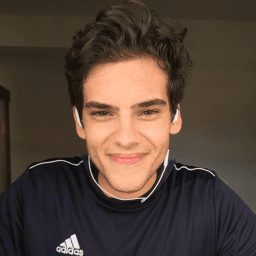
Andre Mendes
•
March 30, 2025
Are you preparing for a Soap Boiler job interview and want to make a lasting impression? This blog post is your essential guide, featuring the most common interview questions for the Soap Boiler role. Dive into expertly crafted example answers and gain valuable tips on how to respond effectively, boosting your confidence and readiness. Get ready to excel in your interview and secure your desired position!
Download Soap Boiler Interview Questions in PDF
To make your preparation even more convenient, we've compiled all these top Soap Boilerinterview questions and answers into a handy PDF.
Click the button below to download the PDF and have easy access to these essential questions anytime, anywhere:
List of Soap Boiler Interview Questions
Behavioral Interview Questions
Have you ever trained new team members in soap boiling techniques? How did you approach this?
How to Answer
- 1
Share specific examples of training you conducted
- 2
Highlight your approach to making the training effective
- 3
Mention any materials or resources you used
- 4
Discuss the feedback process to improve training
- 5
Emphasize the importance of safety and quality control
Example Answers
Yes, I have trained several new team members in soap boiling techniques. I created a detailed training guide that outlined each step of the process, and I conducted hands-on demonstrations to ensure they understood. I also encouraged them to ask questions throughout the process.
Describe an incident where you had to prioritize safety in the soap boiling process.
How to Answer
- 1
Think of a specific incident from past experiences.
- 2
Emphasize the potential hazards during soap boiling.
- 3
Explain the safety measures you implemented.
- 4
Describe the outcome and how it improved safety.
- 5
Highlight the importance of safety culture in the workplace.
Example Answers
In a previous role, I noticed that some boiling containers were not properly secured, which posed a risk of spills. I immediately organized a team meeting to discuss the importance of securing the containers and implemented a checklist for safety checks before processing. This reduced incidents and fostered a culture of safety.
Don't Just Read Soap Boiler Questions - Practice Answering Them!
Reading helps, but actual practice is what gets you hired. Our AI feedback system helps you improve your Soap Boiler interview answers in real-time.
Personalized feedback
Unlimited practice
Used by hundreds of successful candidates
Can you describe a time when you had to work closely with others to achieve a production goal?
How to Answer
- 1
Think of a specific project where teamwork was essential.
- 2
Highlight your role and contributions to the team.
- 3
Mention challenges faced and how you overcame them together.
- 4
Emphasize the outcome and its impact on production.
- 5
Keep your answer focused and relevant to the Soap Boiler position.
Example Answers
In my previous job, we had a deadline to produce a large batch of soap for a major client. I coordinated with both the mixing and packaging teams, organizing daily check-ins to ensure everyone was on track. We faced a supply delay, but by collaborating and shifting production priorities, we completed the order on time and received positive feedback from the client.
Tell me about a challenging situation you faced while boiling soap and how you resolved it.
How to Answer
- 1
Think of a specific incident where something went wrong during soap boiling.
- 2
Explain the technical issue clearly, such as temperature control or ingredient mix-up.
- 3
Describe the steps you took to troubleshoot the problem.
- 4
Focus on your actions and the results of those actions.
- 5
Emphasize what you learned and how you improved your process.
Example Answers
Once, while boiling a batch of soap, I realized the temperature had exceeded the recommended level. I quickly turned down the heat and added cold water to cool the mixture. This helped to stabilize the soap, and we ended up with a good texture. I learned to monitor the temperature closely in future batches.
Give an example of how you handled a quality issue in a batch of soap.
How to Answer
- 1
Identify the specific quality issue encountered.
- 2
Describe the steps taken to analyze the problem.
- 3
Explain the corrective actions implemented to resolve the issue.
- 4
Mention how you prevented similar issues in the future.
- 5
Highlight any positive outcomes from your actions.
Example Answers
In one batch, I noticed that the soap had an unusual texture. I analyzed the ingredients and found that the lye had not fully dissolved. I adjusted the mixing technique to ensure thorough dissolution and tested the next batch. Since then, I have established a new protocol for checking lye consistency.
Describe a time you had to adapt to a change in the production schedule. How did you manage it?
How to Answer
- 1
Identify a specific change in the schedule you faced.
- 2
Explain your initial reaction and how you assessed the situation.
- 3
Discuss the steps you took to adapt and communicate with your team.
- 4
Emphasize the outcome and any lessons learned.
- 5
Keep your focus on problem-solving and teamwork.
Example Answers
In my previous role, our production schedule changed unexpectedly due to a supplier delay. I quickly gathered the team to assess our current projects and prioritize tasks. We focused on completed orders and communicated openly with management about expected timelines. This adaptability allowed us to meet our deadlines with minimal impact, and I learned the importance of having a flexible mindset.
Can you tell me about a time when clear communication helped smooth a difficulty in the production line?
How to Answer
- 1
Identify a specific situation with a communication issue.
- 2
Explain how you communicated clearly to address the problem.
- 3
Focus on the outcome and improvements in the production line.
- 4
Use the STAR method: Situation, Task, Action, Result.
- 5
Emphasize teamwork and how it fostered better results.
Example Answers
In a previous role, we faced delays due to miscommunication about ingredient quantities. I organized a meeting with my team to clarify roles and double-check measurements. After implementing a checklist, we saw a 20% increase in efficiency on the production line.
Can you describe a time when you managed multiple tasks in a tight schedule while boiling soap?
How to Answer
- 1
Identify a specific instance of multitasking during soap boiling.
- 2
Highlight prioritization and time management skills.
- 3
Describe how you handled the pressure to meet deadlines.
- 4
Mention the outcome of your efforts and any lessons learned.
- 5
Use clear and concise language for your explanation.
Example Answers
In my previous job at the soap factory, I had to boil multiple batches while supervising new employees. I prioritized batching based on demand and helped the new hires measure ingredients in the downtime of the boiling process. This ensured we met our production quota for the day.
Tell me about a time when you resolved a conflict in the workplace related to soap production.
How to Answer
- 1
Choose a specific incident that clearly illustrates the conflict.
- 2
Describe the roles of the people involved in the conflict.
- 3
Explain the steps you took to resolve the issue.
- 4
Highlight the positive outcome and any lessons learned.
- 5
Keep it concise and focused on your actions.
Example Answers
In a previous role at a soap manufacturing plant, two team members disagreed over the mixing ratios for an essential oil blend. I facilitated a meeting where each person could present their case. After discussing the potential outcomes, we agreed to conduct small-scale tests to determine the best ratio. This not only resolved the conflict but also led to a superior product, increasing our sales by 15%.
Don't Just Read Soap Boiler Questions - Practice Answering Them!
Reading helps, but actual practice is what gets you hired. Our AI feedback system helps you improve your Soap Boiler interview answers in real-time.
Personalized feedback
Unlimited practice
Used by hundreds of successful candidates
Technical Interview Questions
What finishing techniques do you apply after the soap has been boiled?
How to Answer
- 1
Discuss cooling and molding processes to shape the soap.
- 2
Mention cutting the soap into bars for uniformity.
- 3
Include any additional treatments like curing for hardness.
- 4
Talk about packaging options that preserve freshness.
- 5
Share any quality control checks to ensure the soap meets standards.
Example Answers
After boiling the soap, I pour it into molds and allow it to cool before cutting it into bars. I then cure the bars for a few weeks to ensure they harden properly.
What are the key stages of the soap boiling process and the purpose of each stage?
How to Answer
- 1
Break down the process into clear stages: saponification, boiling, drying, and curing.
- 2
Explain the purpose of each stage briefly and clearly.
- 3
Use specific terminology related to soap making but keep it understandable.
- 4
If possible, relate your answer to practical experience or knowledge you have.
- 5
Conclude with a summary of how these stages contribute to the quality of the soap.
Example Answers
The key stages of the soap boiling process include saponification where fats react with lye to form soap, boiling to ensure complete reaction and homogenization, drying to remove excess moisture, and curing to allow the soap to harden and mature. Each stage is crucial for producing a quality product.
Don't Just Read Soap Boiler Questions - Practice Answering Them!
Reading helps, but actual practice is what gets you hired. Our AI feedback system helps you improve your Soap Boiler interview answers in real-time.
Personalized feedback
Unlimited practice
Used by hundreds of successful candidates
What raw materials are essential in soap production, and how do they affect the final product?
How to Answer
- 1
Identify the primary oils and fats used in soap making.
- 2
Mention lye and its role in saponification.
- 3
Discuss how different oils affect the properties of the soap.
- 4
Include optional ingredients like fragrances and colorants.
- 5
Conclude with the significance of each ingredient on the final product.
Example Answers
In soap production, the essential raw materials are oils and fats, such as coconut oil and olive oil, which contribute to the lather and moisturizing properties. Lye, or sodium hydroxide, is crucial for saponification, turning these oils into soap. Each oil has unique qualities: for instance, coconut oil creates a bubbly lather, while olive oil makes a gentle, moisturizing bar.
How do you determine the right proportions of lye and fats in soap making?
How to Answer
- 1
Understand the saponification value of the fats you are using
- 2
Use a lye calculator to ensure accurate measurements
- 3
Consider the desired properties of the final soap, like hardness and moisturizing qualities
- 4
Know how to adjust proportions based on the type of soap you are making
- 5
Always follow safety protocols when handling lye and fats
Example Answers
To determine the right proportions of lye and fats, I first check the saponification values for each fat I'm using. Then, I input these values into a lye calculator to get the exact measurements. This ensures my soap has the right balance of lye and fats for good quality.
Can you explain the chemical reaction that occurs during saponification?
How to Answer
- 1
Define saponification clearly as the process of soap making.
- 2
Mention the reactants: fats or oils and a strong base like sodium hydroxide or potash.
- 3
Describe the reaction where triglycerides react with an alkali to produce glycerol and soap.
- 4
Emphasize that saponification is an irreversible reaction.
- 5
Use a simple analogy if possible, like comparing the process to cooking.
Example Answers
Saponification is the process of making soap where fats or oils react with a strong base, like sodium hydroxide. During this reaction, triglycerides break down into glycerol and soap molecules. It's an irreversible reaction that results in the formation of soap.
What type of equipment do you use for boiling soap and how do you maintain it for optimal performance?
How to Answer
- 1
Identify key equipment used in soap boiling such as kettles and mixers.
- 2
Highlight maintenance practices like regular cleaning and checking for wear.
- 3
Discuss the importance of operating temperatures and pressure monitoring.
- 4
Mention safety checks and proper ventilation during the boiling process.
- 5
Emphasize keeping records of maintenance to track performance.
Example Answers
I use industrial-grade stainless steel kettles and high-shear mixers for boiling soap. I maintain them by cleaning thoroughly after each batch and inspecting seals and gaskets regularly to prevent leaks.
What common problems can occur during the soap boiling process and how do you troubleshoot them?
How to Answer
- 1
Identify typical issues like temperature fluctuations or incomplete mixing.
- 2
Discuss specific troubleshooting steps for each problem.
- 3
Mention the importance of quality materials and their role in the process.
- 4
Provide examples of successful troubleshooting you've implemented in the past.
- 5
Keep your answers focused on practical solutions.
Example Answers
One common problem is temperature fluctuations. If the temperature drops too low, it can cause the soap to harden prematurely. To troubleshoot, I monitor the heat closely and adjust the burner settings down to maintain a steady temperature. I also make sure to use high-quality fats to ensure consistent melting.
What factors do you consider when formulating a new soap recipe?
How to Answer
- 1
Identify the purpose of the soap, like moisturizing or exfoliating
- 2
Choose appropriate oils and fats for desired properties
- 3
Consider fragrance and essential oil selection for aroma
- 4
Account for skin types and sensitivities of potential users
- 5
Include safety measures for lye handling and proper curing times
Example Answers
When formulating a new soap recipe, I first determine the soap's purpose. Then I select oils based on their moisturizing properties, such as olive oil for hydration. I also choose essential oils to add fragrance while considering the skin types of my target audience. Lastly, I ensure to follow proper lye handling protocols to maintain safety.
What safety protocols do you follow while boiling soap, and why are they important?
How to Answer
- 1
Mention personal protective equipment like gloves and goggles.
- 2
Discuss proper ventilation in the work area to avoid fumes.
- 3
Explain the importance of temperature control to prevent burns.
- 4
Highlight the need to follow precise measurements to avoid chemical reactions.
- 5
Emphasize clean-up protocols to manage any spills or accidents immediately.
Example Answers
I always wear gloves and goggles to protect my skin and eyes from any splashes. Proper ventilation is crucial; I ensure that the area is well-ventilated to avoid inhaling harmful fumes. Controlling the temperature is important to prevent burns and ensure the soap boils at the right consistency.
How do you test the quality of the final soap product?
How to Answer
- 1
Perform lather tests to check for richness and stability.
- 2
Evaluate the scent to ensure it meets desired specifications.
- 3
Check the pH level to confirm it is skin-friendly (typically 7-10).
- 4
Conduct a visual inspection for consistency and absence of contaminants.
- 5
Assess the hardness and texture by touch to ensure it meets quality standards.
Example Answers
I test the final soap by performing lather tests to ensure it produces a rich foam, checking the scent, and measuring the pH to verify it is safe for skin use.
Don't Just Read Soap Boiler Questions - Practice Answering Them!
Reading helps, but actual practice is what gets you hired. Our AI feedback system helps you improve your Soap Boiler interview answers in real-time.
Personalized feedback
Unlimited practice
Used by hundreds of successful candidates
What measures do you take to minimize the environmental impact of the soap boiling process?
How to Answer
- 1
Use eco-friendly raw materials that are sustainably sourced.
- 2
Implement energy-efficient methods for heating and boiling.
- 3
Recycle waste products and by-products from the soap-making process.
- 4
Minimize water usage and ensure water is treated before disposal.
- 5
Educate your team about environmentally friendly practices.
Example Answers
I prioritize sourcing raw materials that are biodegradable and come from sustainable suppliers, reducing our carbon footprint.
Situational Interview Questions
If you noticed that you were running low on a critical raw ingredient, what steps would you take to address this?
How to Answer
- 1
Identify the ingredient that is running low.
- 2
Check the inventory management system for current stock levels.
- 3
Communicate with your supervisor or the purchasing department immediately.
- 4
Place an urgent order with suppliers if necessary.
- 5
Make adjustments to production schedules if needed to mitigate delays.
Example Answers
I would first identify which ingredient is low, then check the inventory system to confirm the levels. After that, I would inform my supervisor and coordinate with purchasing to place an urgent order with our suppliers. If we anticipate delays, I would adjust the production schedule accordingly.
Imagine you are leading a team and there is a disagreement about the production method. How would you handle this?
How to Answer
- 1
Listen carefully to all team members' perspectives
- 2
Encourage open discussion and identify key concerns
- 3
Facilitate a collaborative evaluation of the pros and cons
- 4
Aim for a consensus or a compromise solution
- 5
Communicate the final decision clearly and respectfully
Example Answers
I would start by ensuring everyone feels heard by inviting each member to share their viewpoint. Then, I would guide the team to discuss the strengths and weaknesses of each method, aiming for consensus. If necessary, I would suggest a trial run of the top options before making a final decision.
Don't Just Read Soap Boiler Questions - Practice Answering Them!
Reading helps, but actual practice is what gets you hired. Our AI feedback system helps you improve your Soap Boiler interview answers in real-time.
Personalized feedback
Unlimited practice
Used by hundreds of successful candidates
What would you do if you realized that the current batch of soap would not meet the deadline due to a production issue?
How to Answer
- 1
Identify the specific production issue immediately
- 2
Communicate the problem to your supervisor and the team promptly
- 3
Assess the impact on the timeline and explore possible solutions
- 4
Implement quick fixes if feasible, or consider alternatives such as overtime
- 5
Document the issue and resolutions for future reference
Example Answers
I would first identify the specific issue causing the delay, then inform my supervisor and the team. Together, we would assess the situation to see if we could implement quick fixes, like adjusting the mixing times or reallocating resources, to meet the deadline.
If a customer reported an issue with your soap product, how would you respond and handle the situation?
How to Answer
- 1
Listen carefully to the customer's issue without interruption
- 2
Apologize sincerely for the inconvenience caused
- 3
Gather all relevant details about the issue
- 4
Offer a solution or replacement if applicable
- 5
Follow up to ensure customer satisfaction after the resolution
Example Answers
I would start by listening to the customer's concerns fully and apologize for any trouble the product caused. Then, I would ask for specifics so I can understand the problem better. Depending on the issue, I would offer to replace the product or provide a refund, ensuring they feel heard and valued.
If you were asked to scale up production significantly, what considerations would you take into account?
How to Answer
- 1
Evaluate current production capabilities and bottlenecks
- 2
Assess the supply chain for material availability and cost
- 3
Consider workforce requirements and training for increased output
- 4
Implement quality control measures to maintain product standards
- 5
Analyze potential market demand to justify increased production
Example Answers
To scale up production, I would first identify any current bottlenecks in the process that might hinder increased output. Next, I would evaluate our supply chain to ensure we can source the necessary materials at a reasonable cost. I'd also plan for workforce expansion and training to handle the increased production levels, while maintaining strong quality control to uphold product standards. Finally, I would conduct market analysis to confirm that there's sufficient demand for the increased production.
How would you approach training a new employee on the intricacies of soap boiling?
How to Answer
- 1
Start with the basics of soap boiling and its ingredients.
- 2
Demonstrate the entire process step-by-step.
- 3
Provide hands-on training with supervision during initial batches.
- 4
Encourage questions to clarify doubts about the process.
- 5
Review safety procedures and equipment use thoroughly.
Example Answers
I would begin by explaining the ingredients and their roles in soap boiling. Then, I'd demonstrate the full process, allowing the new employee to observe. After that, I'd let them try it themselves under my supervision while encouraging them to ask questions at any point.
If new regulations were introduced affecting soap production, how would you ensure compliance in the process?
How to Answer
- 1
Stay informed about new regulations through industry news and relevant government agencies.
- 2
Implement a compliance management system to track regulation changes and their implications.
- 3
Train staff regularly on compliance procedures and the importance of following regulations.
- 4
Conduct regular audits of the production process to ensure adherence to regulations.
- 5
Document all compliance measures and changes to maintain clear records.
Example Answers
I would actively follow industry updates and regulatory announcements to stay informed. Then, I would implement a compliance tracking system to manage changes effectively. Regular training sessions for staff on these updates would also be a key part of my strategy.
If you were supervising a boiling session and noticed an error being made by a team member, how would you intervene?
How to Answer
- 1
Assess the situation calmly before intervening
- 2
Approach the team member privately to avoid embarrassment
- 3
Use clear and specific language to explain the error
- 4
Offer support and suggest a solution or correction
- 5
Encourage open communication to prevent future mistakes
Example Answers
I would first analyze what the error was and the potential impact. Then, I would approach the team member privately, explain the issue clearly, and help them correct it, ensuring they feel supported in the process.
If you wanted to introduce a new innovative technique in soap boiling, what process would you follow?
How to Answer
- 1
Identify current challenges in soap boiling processes
- 2
Research existing innovative techniques in similar industries
- 3
Develop a prototype of your technique on a small scale
- 4
Test and gather data on efficiency and cost-effectiveness
- 5
Present your findings to stakeholders with clear benefits
Example Answers
First, I would assess the existing soap boiling processes to find areas that could be improved, such as efficiency or environmental impact. Then, I would look at innovations in other industries, like sustainable practices in cosmetics, to inspire my technique. After creating a small-scale prototype, I would run tests and document the results. Finally, I would present the data to management highlighting the expected benefits.
How would you contribute to creating a positive workplace culture in the soap production department?
How to Answer
- 1
Encourage open communication among team members.
- 2
Recognize and celebrate individual and team achievements.
- 3
Promote a supportive team environment through collaboration.
- 4
Be proactive in resolving conflicts and misunderstandings.
- 5
Share positive feedback regularly to boost morale.
Example Answers
I would encourage open communication by setting up regular team meetings where everyone can share their thoughts and ideas, which helps everyone feel valued.
Don't Just Read Soap Boiler Questions - Practice Answering Them!
Reading helps, but actual practice is what gets you hired. Our AI feedback system helps you improve your Soap Boiler interview answers in real-time.
Personalized feedback
Unlimited practice
Used by hundreds of successful candidates
Soap Boiler Position Details
Related Positions
Similar positions you might be interested in.
Ace Your Next Interview!
Practice with AI feedback & get hired faster
Personalized feedback
Used by hundreds of successful candidates
Ace Your Next Interview!
Practice with AI feedback & get hired faster
Personalized feedback
Used by hundreds of successful candidates