Top 28 Bench Assembler Interview Questions and Answers [Updated 2025]
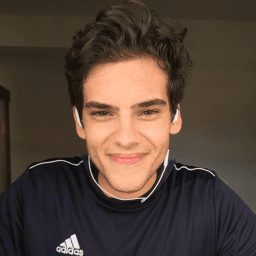
Andre Mendes
•
March 30, 2025
Preparing for a Bench Assembler interview can be daunting, but our updated guide for 2025 is here to help. Dive into the most common interview questions tailored for this role, complete with example answers and practical tips to enhance your responses. Whether you're a seasoned professional or new to the field, this post will equip you with the insights needed to impress any hiring manager.
Download Bench Assembler Interview Questions in PDF
To make your preparation even more convenient, we've compiled all these top Bench Assemblerinterview questions and answers into a handy PDF.
Click the button below to download the PDF and have easy access to these essential questions anytime, anywhere:
List of Bench Assembler Interview Questions
Behavioral Interview Questions
Can you describe a time when you worked in a team environment to assemble components? What was your role and how did you contribute?
How to Answer
- 1
Think of a specific project where teamwork was essential.
- 2
Clearly state your role and responsibilities in the assembly process.
- 3
Highlight your contributions, focusing on skills like communication or problem-solving.
- 4
Mention any positive outcomes or lessons learned from the experience.
- 5
Keep your answer focused and relevant to the Bench Assembler position.
Example Answers
In my previous job, I was part of a team responsible for assembling mechanical devices. My role was to manage the assembly line operations, ensuring that all components were accurately fitted together. I communicated regularly with my teammates to solve any issues quickly, which helped us meet our production targets ahead of schedule.
Tell me about a challenging assembly task you faced. How did you overcome the difficulties?
How to Answer
- 1
Choose a specific assembly task that had issues.
- 2
Explain the nature of the challenge clearly.
- 3
Describe the steps you took to resolve the issue.
- 4
Mention any skills or tools you used to help resolve the problem.
- 5
Conclude with what you learned from the experience.
Example Answers
In my last position, I had to assemble a custom part under a tight deadline. The components were not fitting properly due to a manufacturing error. I took the time to recheck the assembly instructions, then I modified the parts slightly using tools at hand. This adjustment allowed me to complete the assembly on time, and I learned the importance of double-checking components before assembly.
Don't Just Read Bench Assembler Questions - Practice Answering Them!
Reading helps, but actual practice is what gets you hired. Our AI feedback system helps you improve your Bench Assembler interview answers in real-time.
Personalized feedback
Unlimited practice
Used by hundreds of successful candidates
Describe a situation where you had to meet tight deadlines while assembling products. How did you manage your time?
How to Answer
- 1
Identify a specific project with a tight deadline
- 2
Explain the steps you took to prioritize tasks
- 3
Mention any tools or techniques used for time management
- 4
Highlight effective communication with team members
- 5
Conclude with the successful outcome and what you learned
Example Answers
In my last job, we had a major product launch that required us to assemble 500 units in just two days. I prioritized the assembly line tasks by focusing on the most time-consuming components first. I used a checklist to track progress, and communicated regularly with my team to ensure we stayed on schedule. We met the deadline and even received positive feedback on quality.
Can you provide an example of a time when your attention to detail prevented a potential assembly error?
How to Answer
- 1
Think of a specific situation from past experience
- 2
Highlight the details that could have led to an error
- 3
Explain the steps you took to prevent the mistake
- 4
Emphasize the positive outcome from your attention to detail
- 5
Keep your answer focused and relevant to assembly tasks
Example Answers
In my previous role, I was assembling a set of parts for a new product when I noticed that two components looked similar but had different specifications. I double-checked the part numbers and discovered I had the wrong part. By correcting this before assembly, I avoided an error that could have led to product failure.
Have you ever had to train a new employee in assembly techniques? How did you approach the training?
How to Answer
- 1
Start by explaining the context of the training experience.
- 2
Describe specific assembly techniques you taught.
- 3
Mention the training methods you used, like hands-on demonstrations.
- 4
Emphasize patience and adaptability to the learner's pace.
- 5
Conclude with the positive outcome of the training.
Example Answers
In my previous role, I trained a new employee on how to assemble electronic components. I focused on hands-on demonstrations, showing each step of the process while encouraging questions. I made sure to be patient and adjusted my pace to match their understanding, which helped them feel confident. The result was that they quickly became a productive member of our team.
What motivates you in your role as a bench assembler? Can you provide an example of how this has influenced your work?
How to Answer
- 1
Identify key motivations like teamwork, quality workmanship, or meeting deadlines.
- 2
Reflect on specific experiences that showcase your motivations in action.
- 3
Use quantitative data or outcomes when possible to illustrate your impact.
- 4
Keep your answer concise and focused on a single example.
- 5
Connect your motivation to the overall goals of the team or company.
Example Answers
I am motivated by the sense of teamwork in my role. For example, I once collaborated with my colleagues to streamline our assembly line, which reduced our production time by 15%.
Have you ever participated in peer reviews of assembly work? What did you learn from that experience?
How to Answer
- 1
Share a specific instance of peer review participation.
- 2
Highlight a skill or method you improved through feedback.
- 3
Mention how you applied lessons learned to future tasks.
- 4
Emphasize teamwork and communication during the review process.
- 5
Conclude with the overall importance of peer reviews in quality control.
Example Answers
During my last job, I participated in a peer review of our assembly line's work. I learned the value of attention to detail when a colleague pointed out a consistent misalignment issue. Using that feedback, I adjusted my technique and saw an immediate improvement in the quality of my assemblies. This experience boosted our team's overall efficiency.
Technical Interview Questions
What types of hand tools and power tools are you most experienced with in bench assembly? Can you describe their uses?
How to Answer
- 1
List specific hand tools you've used, like screwdrivers, pliers, and wrenches.
- 2
Mention relevant power tools, such as drills or saws, and explain their roles.
- 3
Include how you ensure safety while using these tools.
- 4
Emphasize your proficiency level with each tool.
- 5
Share any relevant experience or projects where you applied these tools.
Example Answers
I have extensive experience with hand tools like screwdrivers, which I use for assembling parts, and pliers for gripping and twisting wires. I am also proficient with power drills for creating pilot holes and attaching components quickly.
What safety protocols do you follow while performing assembly tasks? Give an example of a safety issue you encountered.
How to Answer
- 1
Identify key safety protocols specific to assembly tasks, like wearing PPE.
- 2
Mention proper lifting techniques to avoid injuries.
- 3
Describe how you keep your workspace organized to prevent accidents.
- 4
Share a specific example of a safety issue with a positive resolution.
- 5
Emphasize your commitment to safety as a priority in assembly.
Example Answers
I always wear the necessary personal protective equipment, like gloves and goggles. Once, I noticed a colleague using a tool without proper guarding, so I stepped in to remind them about the importance of equipment safety. We resolved it quickly and established a tool check before starting assembly.
Don't Just Read Bench Assembler Questions - Practice Answering Them!
Reading helps, but actual practice is what gets you hired. Our AI feedback system helps you improve your Bench Assembler interview answers in real-time.
Personalized feedback
Unlimited practice
Used by hundreds of successful candidates
How do you ensure that you are using the correct components for an assembly task?
How to Answer
- 1
Review the assembly instructions thoroughly before starting
- 2
Double-check parts against a parts list or assembly diagram
- 3
Use a checklist to confirm all components are available
- 4
Organize components by type for easy access during assembly
- 5
Ask a supervisor or colleague to verify if unsure about any part
Example Answers
I always start by carefully reviewing the assembly instructions and cross-referencing each component with the parts list. This helps me confirm I'm using the right parts.
Are you familiar with reading and interpreting assembly diagrams or schematics? Can you give an example?
How to Answer
- 1
Mention specific types of diagrams you have worked with.
- 2
Describe a particular project or task involving assembly diagrams.
- 3
Explain how you ensured accuracy while following the diagrams.
- 4
Highlight any challenges faced and how you resolved them.
- 5
Emphasize the importance of diagrams in achieving successful assembly.
Example Answers
Yes, I have experience with assembly diagrams, particularly in assembling electronic components. For instance, I worked on a project where I had to interpret a circuit schematic to build a control panel. I double-checked all connections for accuracy, which helped me identify and fix a wiring error before it caused issues.
What steps do you take to ensure the quality of your assembled products?
How to Answer
- 1
Follow assembly instructions to the letter and double-check your work.
- 2
Conduct regular inspections during the assembly process to identify any issues early.
- 3
Use quality control tools, like calipers and gauges, for precise measurements.
- 4
Document any defects and improve your process based on past experiences.
- 5
Collaborate with team members to share knowledge and techniques for better quality.
Example Answers
I always strictly follow the assembly instructions and double-check my work to catch any errors. During assembly, I perform regular inspections to ensure everything fits properly, using calipers for precise measurements.
What assembly techniques do you find most effective for ensuring consistent results?
How to Answer
- 1
Use standardized tools for precise measurements.
- 2
Implement a clear step-by-step process for assembly.
- 3
Conduct regular quality checks during the assembly process.
- 4
Maintain a clean and organized workspace to avoid errors.
- 5
Ensure proper training for all team members involved in assembly.
Example Answers
I find using standardized tools is essential, as they ensure precise measurements for every part. Additionally, having a clear assembly process helps maintain consistency.
Describe a time when you had to troubleshoot an assembly machine failure. What steps did you take?
How to Answer
- 1
Identify the specific machine and the failure that occurred
- 2
Explain how you diagnosed the problem step by step
- 3
Detail the actions you took to resolve the issue
- 4
Highlight any tools or resources you used
- 5
Mention the outcome and what you learned from the experience
Example Answers
At my previous job, the conveyor belt malfunctioned, causing delays. I noticed it was not moving. I checked the power supply and found a blown fuse. After replacing the fuse, I tested the belt and it worked perfectly. This taught me the importance of regular maintenance checks.
How do you handle fragile materials during the assembly process?
How to Answer
- 1
Always inspect fragile materials before use for any defects or damage.
- 2
Use protective gear like gloves to avoid fingerprints and breakage.
- 3
Handle materials gently, using both hands when necessary to ensure stability.
- 4
Organize your workspace to minimize clutter and accidental impacts.
- 5
Follow specific instructions for each type of fragile material during assembly.
Example Answers
I inspect each fragile component for damage before starting the assembly. I always use gloves to handle materials carefully and minimize risk of breakage.
How do you stay updated on industry standards and regulatory compliance in assembly work?
How to Answer
- 1
Subscribe to industry newsletters and magazines for the latest updates
- 2
Participate in webinars and training sessions offered by professional organizations
- 3
Join relevant forums or groups on social media to share insights with peers
- 4
Regularly review compliance guidelines from regulatory bodies
- 5
Attend local workshops or trade shows to network and learn about new technologies
Example Answers
I subscribe to industry newsletters and regularly read magazines focused on assembly work. This helps me stay informed about the latest standards and practices.
What techniques do you use to identify opportunities for process optimization in assembly tasks?
How to Answer
- 1
Observe the assembly line to pinpoint bottlenecks and slowdowns
- 2
Gather feedback from team members about challenges they face
- 3
Analyze production data to find patterns in errors or delays
- 4
Test small adjustments and measure their impact on efficiency
- 5
Stay informed about industry best practices and incorporate them
Example Answers
I frequently observe the assembly process to identify any workarounds or inefficiencies. For example, I noticed a bottleneck at a particular station and suggested adjusting the workflow, which improved our throughput by 15%.
Don't Just Read Bench Assembler Questions - Practice Answering Them!
Reading helps, but actual practice is what gets you hired. Our AI feedback system helps you improve your Bench Assembler interview answers in real-time.
Personalized feedback
Unlimited practice
Used by hundreds of successful candidates
Situational Interview Questions
If you noticed that a coworker was not following assembly instructions correctly, how would you address the situation?
How to Answer
- 1
Approach the coworker in a private setting to avoid embarrassment.
- 2
Use a friendly tone and express concern for quality and safety.
- 3
Ask questions to understand why the instructions were not followed.
- 4
Offer to help clarify the instructions if needed.
- 5
Suggest reviewing the assembly process together to ensure accuracy.
Example Answers
I would talk to my coworker privately and express that I noticed they might be deviating from the instructions. I would ask if they needed any help understanding the process.
You are given an assembly task with unclear instructions. What steps would you take to complete the task?
How to Answer
- 1
Review all available documentation or instructions carefully.
- 2
Break down the task into smaller components to identify key steps.
- 3
Ask a colleague or supervisor for clarification if necessary.
- 4
Look at similar completed assemblies as reference for guidance.
- 5
Test assemble a small section to ensure the approach is correct.
Example Answers
I would first review any instructions or related documentation I have, then break the task down into smaller parts to see if I can identify some clear steps. If I'm still unclear, I would seek help from a colleague.
Don't Just Read Bench Assembler Questions - Practice Answering Them!
Reading helps, but actual practice is what gets you hired. Our AI feedback system helps you improve your Bench Assembler interview answers in real-time.
Personalized feedback
Unlimited practice
Used by hundreds of successful candidates
How would you handle a situation where multiple assembly tasks are due at the same time and you are overwhelmed?
How to Answer
- 1
Take a deep breath and assess all tasks at hand
- 2
Prioritize tasks based on urgency and importance
- 3
Break down each task into smaller steps for manageability
- 4
Communicate with your supervisor about workload and deadlines
- 5
Focus on completing one task at a time to maintain quality
Example Answers
In a situation where I feel overwhelmed, I would first take a moment to prioritize the tasks. I would identify which ones are urgent and tackle them one at a time, ensuring I maintain the quality of my work.
Imagine you need to assemble a complex product that requires collaboration with other teams. How would you ensure effective communication?
How to Answer
- 1
Establish clear roles and responsibilities among team members
- 2
Use collaborative tools for real-time updates and document sharing
- 3
Set regular check-in meetings to discuss progress and challenges
- 4
Encourage open feedback and constructive discussion
- 5
Provide visual aids or diagrams to clarify assembly instructions
Example Answers
I would first clarify each team member's role and ensure everyone understands their responsibilities. Then, I would use tools like Slack or Trello for efficient communication and document sharing. Regular check-ins would help us address any issues quickly, and I'd encourage input from everyone to foster a collaborative environment.
If you were asked to improve the assembly process to enhance efficiency, what changes would you suggest?
How to Answer
- 1
Analyze current workflow and identify bottlenecks
- 2
Propose tool or equipment upgrades that could speed up tasks
- 3
Suggest implementing a standardized training program for new hires
- 4
Consider using visual aids or assembly guides to reduce errors
- 5
Recommend regular team feedback sessions to gather improvement ideas
Example Answers
I would start by mapping the current workflow to pinpoint delays, then suggest adding a conveyor belt to streamline part movement. I believe this could reduce the time spent on manual transport.
If a customer complained about a product due to assembly defects, how would you respond and what actions would you take?
How to Answer
- 1
Acknowledge the customer's concern and thank them for their feedback
- 2
Gather details about the defect for clarity
- 3
Explain your process for addressing the issue and assure swift action
- 4
Offer a solution, such as a replacement or refund
- 5
Follow up with the customer after resolution to ensure satisfaction
Example Answers
I would start by thanking the customer for bringing the issue to my attention. I'd ask for specific details about the defect to understand the problem better. Then, I would explain how we handle such complaints and promise to investigate and resolve the issue as quickly as possible. If appropriate, I'd offer a replacement or refund. Finally, I would follow up to ensure the customer is satisfied with the outcome.
If you discovered a new method or tool that could improve your assembly process, how would you present this idea to management?
How to Answer
- 1
Research and document the benefits of the new method or tool.
- 2
Create a clear, concise presentation highlighting key improvements.
- 3
Provide data or examples to support your idea's effectiveness.
- 4
Suggest a trial period to test the new method or tool.
- 5
Encourage feedback and discussion to engage management.
Example Answers
I would document the key benefits of the new tool, create a concise presentation showing potential time and cost savings, and suggest a trial phase to demonstrate its effectiveness.
If a supervisor assigns you a project but resources are limited, how would you prioritize your tasks?
How to Answer
- 1
Assess the project's goals and deadlines to identify critical tasks
- 2
Communicate with your supervisor about resource constraints
- 3
Determine which tasks can be done concurrently to save time
- 4
Focus on high-impact tasks that drive the project forward
- 5
Be flexible and ready to adjust priorities as needed
Example Answers
I would first review the project's goals and identify the critical tasks that must be completed by the deadline. Then, I would discuss the resource limitations with my supervisor to understand which tasks can be modified or delayed. I would prioritize high-impact tasks and see if any can be done simultaneously.
If there is a disagreement among your team regarding the assembly process, how would you facilitate a resolution?
How to Answer
- 1
Encourage open communication by asking each team member to express their viewpoint.
- 2
Summarize the key points of the disagreement to ensure everyone understands.
- 3
Facilitate a discussion to explore possible solutions collaboratively.
- 4
Look for common ground and focus on shared goals.
- 5
Propose a trial period for the suggested solutions to evaluate their effectiveness.
Example Answers
I would start by bringing everyone together and inviting each team member to share their perspective on the assembly process. Then, I would summarize the key points to ensure clarity, followed by guiding a discussion to explore solutions we could agree on.
Bench Assembler Position Details
Recommended Job Boards
ZipRecruiter
www.ziprecruiter.com/Jobs/Bench-AssemblerThese job boards are ranked by relevance for this position.
Related Positions
- Final Assembler
- Production Assembler
- Toy Assembler
- Table Assembler
- Automobile Assembler
- Bicycle Assembler
- Truss Assembler
- Production Line Assembler
- Window Assembler
- Mechanical Assembler
Similar positions you might be interested in.
Ace Your Next Interview!
Practice with AI feedback & get hired faster
Personalized feedback
Used by hundreds of successful candidates
Ace Your Next Interview!
Practice with AI feedback & get hired faster
Personalized feedback
Used by hundreds of successful candidates