Top 29 Table Assembler Interview Questions and Answers [Updated 2025]
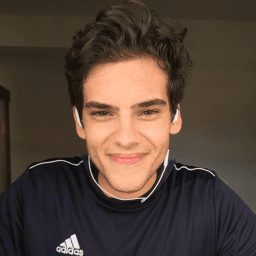
Andre Mendes
•
March 30, 2025
Are you preparing for a Table Assembler job interview and looking to make a strong impression? Our blog post compiles the most common interview questions for this role, providing you with insightful example answers and expert tips on how to respond effectively. Dive in to enhance your interviewing skills and boost your confidence, setting the stage for success in your next Table Assembler interview.
Download Table Assembler Interview Questions in PDF
To make your preparation even more convenient, we've compiled all these top Table Assemblerinterview questions and answers into a handy PDF.
Click the button below to download the PDF and have easy access to these essential questions anytime, anywhere:
List of Table Assembler Interview Questions
Behavioral Interview Questions
Can you provide an example of a difficult situation you encountered while assembling furniture, and how you resolved it?
How to Answer
- 1
Choose a specific example from your experience.
- 2
Focus on the challenge you faced during assembly.
- 3
Explain the steps you took to resolve the situation.
- 4
Highlight what you learned or how it improved your skills.
- 5
Keep your answer structured and concise.
Example Answers
While assembling a complex wardrobe, I discovered that one of the panels was damaged. I contacted the supplier, provided photos, and received a replacement panel within a few days. This taught me the importance of checking items before assembly.
Tell me about a time when you discovered a mistake in the assembly instructions or process. How did you handle it?
How to Answer
- 1
Describe the specific mistake clearly.
- 2
Explain how you noticed the mistake.
- 3
Detail your immediate actions to remedy the situation.
- 4
Highlight any communication with your team or supervisors.
- 5
Conclude with what you learned and how it improved future processes.
Example Answers
I noticed that the assembly instructions for a table omitted a crucial step regarding leg attachments. While assembling, I discovered the legs wouldn't be secure without it. I halted my work and informed my supervisor, and we quickly revised the instructions. We also reviewed the entire batch to ensure quality. This incident improved our instruction accuracy for future assembly projects.
Don't Just Read Table Assembler Questions - Practice Answering Them!
Reading helps, but actual practice is what gets you hired. Our AI feedback system helps you improve your Table Assembler interview answers in real-time.
Personalized feedback
Unlimited practice
Used by hundreds of successful candidates
Describe an instance where you had to manage multiple assembly tasks under a tight deadline. How did you prioritize your work?
How to Answer
- 1
Start with a specific example from a previous job.
- 2
Explain the tasks you were juggling and their deadlines.
- 3
Describe how you assessed which tasks were most critical.
- 4
Talk about the methods you used to stay organized.
- 5
Conclude with the outcome and what you learned from the experience.
Example Answers
In my previous job, I had to assemble three types of furniture for a big order due the next day. I prioritized by starting with the most complex item because it took the longest. I used a checklist to track my progress and allocated more time for difficult tasks. In the end, I completed everything on time, and my supervisor appreciated my efficiency.
Have you ever disagreed with a colleague about the best way to perform an assembly task? How did you handle the disagreement?
How to Answer
- 1
Listen to your colleague's perspective carefully.
- 2
Share your own viewpoint clearly and respectfully.
- 3
Suggest a trial period to test both methods.
- 4
Focus on outcomes rather than personal differences.
- 5
Be open to compromise if it benefits the team.
Example Answers
Yes, I once disagreed with a colleague on the best order to assemble parts. I listened to their reasoning, and we discussed our methods. We decided to try both ways for a week and compare the results. This way, we could choose the method that worked best without conflict.
Tell us about a time you had to quickly adapt to a change in the assembly process or materials. How did you handle it?
How to Answer
- 1
Identify a specific situation where a change occurred.
- 2
Explain the nature of the change clearly.
- 3
Describe the steps you took to adapt quickly.
- 4
Highlight any positive outcomes from your adaptation.
- 5
Reflect on what you learned from the experience.
Example Answers
In my previous role, we switched to new materials that required different tools. I quickly learned how to use the new tools by watching instructional videos and practicing with them during breaks. As a result, we met our production targets without delays, and I helped train others in the process.
Describe a situation where you took the initiative to improve an assembly process on your own.
How to Answer
- 1
Think of a specific time you identified a problem in the assembly process.
- 2
Explain the steps you took to address the problem independently.
- 3
Highlight the positive outcome or improvement resulting from your actions.
- 4
Mention any feedback you received from colleagues or supervisors.
- 5
Keep it concise and focus on your role in the initiative.
Example Answers
In my previous role, I noticed that our assembly line was frequently delayed due to a bottleneck in the packaging stage. I took the initiative to rearrange the workflow, moving the packing station closer to the assembly area. This change reduced our packaging time by 20% and improved overall efficiency. My supervisor praised the change and we implemented it permanently.
How do you ensure effective communication with team members when working on an assembly line?
How to Answer
- 1
Establish clear roles and responsibilities for each team member.
- 2
Use hand signals or color-coded systems for quick visual communication.
- 3
Conduct short daily briefings to discuss goals and any issues.
- 4
Encourage open dialogue and feedback among team members.
- 5
Document processes and changes to keep everyone informed.
Example Answers
I ensure effective communication by establishing clear roles for each member of the assembly line, so everyone knows their responsibilities. Additionally, I use hand signals to convey messages without disrupting the workflow.
Describe a time when you had to work closely with a team to assemble a complex piece of furniture. What was your role and how did you ensure the team was successful?
How to Answer
- 1
Identify a specific project where teamwork was essential.
- 2
Clarify your role and responsibilities within the team.
- 3
Discuss communication strategies you used to keep everyone aligned.
- 4
Mention challenges that arose and how your team overcame them.
- 5
Highlight the final outcome and what you learned from the experience.
Example Answers
In my last job at a furniture store, we had to assemble a large sectional sofa for a client. I was responsible for managing the assembly team. I ensured we had a clear plan and divided the tasks based on each person's strengths. We communicated through regular check-ins to tackle issues quickly. Despite running out of some parts, we reached out to the supplier and resolved it swiftly. The client was extremely happy with the final product, and I learned the importance of teamwork and communication.
Technical Interview Questions
What tools are commonly used in assembling tables, and how do you ensure they are maintained in good working order?
How to Answer
- 1
Mention common tools like drills, screwdrivers, and levels.
- 2
Explain the importance of keeping tools clean and rust-free.
- 3
Discuss regular checks for wear and tear on tools.
- 4
Highlight the significance of proper storage to avoid damage.
- 5
Share tips on following manufacturer guidelines for tool usage.
Example Answers
I use a drill, screwdriver, and level for assembling tables. To maintain these, I keep them clean after use and store them in a dry place to prevent rust.
How do you approach reading and interpreting assembly instructions or blueprints?
How to Answer
- 1
Start by thoroughly reviewing all the instructions before beginning assembly.
- 2
Look for key symbols or terminology that indicate how parts fit together.
- 3
Break down the instructions into manageable steps to avoid feeling overwhelmed.
- 4
Use visual aids or diagrams to cross-reference with the written instructions.
- 5
If confused, don’t hesitate to ask questions or seek clarification.
Example Answers
I always read through the entire set of assembly instructions first to get an overview. Then, I'll highlight critical sections and focus on the diagrams to see how the parts fit together. I find it helps to break down the assembly into smaller steps, checking off each one as I finish.
Don't Just Read Table Assembler Questions - Practice Answering Them!
Reading helps, but actual practice is what gets you hired. Our AI feedback system helps you improve your Table Assembler interview answers in real-time.
Personalized feedback
Unlimited practice
Used by hundreds of successful candidates
What types of materials have you worked with in table assembly, and what are the challenges associated with each?
How to Answer
- 1
Identify different materials like wood, metal, and glass you have experience with
- 2
Highlight the unique challenges for each material, such as weight or fragility
- 3
Emphasize any specific techniques or tools you used for assembly
- 4
Mention safety considerations, especially with heavier or sharp materials
- 5
Share any personal experiences where you solved problems related to these materials
Example Answers
I have worked with wooden tables, which require precision in joining joints, and the challenge is ensuring stability. I also assembled metal tables, dealing with issues like weight and the need for strong fasteners. Finally, glass tables pose challenges with handling and fragility, so I ensured to use protective gloves and proper support.
What safety protocols do you follow when assembling tables, and why are they important?
How to Answer
- 1
Identify specific safety gear like gloves and goggles.
- 2
Mention the importance of a clean workspace to avoid accidents.
- 3
Discuss securing tools properly to prevent injuries.
- 4
Emphasize the need for following manufacturer instructions.
- 5
Highlight the importance of team communication during assembly.
Example Answers
I always wear gloves and goggles to protect myself from sharp edges and debris. A clean workspace is crucial to prevent any trip hazards. I also ensure tools are stored safely when not in use.
Describe your process for ensuring quality and consistency in the tables you assemble.
How to Answer
- 1
Review assembly instructions before starting the process
- 2
Use the right tools and materials to avoid mistakes
- 3
Measure components accurately to maintain uniformity
- 4
Inspect each part for quality before assembly
- 5
Perform a final quality check on the assembled table
Example Answers
I start by thoroughly reviewing the assembly instructions to understand all steps clearly. Then, I gather the necessary tools and materials. During assembly, I measure each component to ensure they meet specifications. I inspect all parts for defects before putting them together and conduct a final quality check to confirm everything is aligned and secure.
Can you explain the process of leveling a table and why it is important?
How to Answer
- 1
Start by describing the tools you use, like a level or a measuring tape.
- 2
Explain the importance of stability for the table, such as for safety and functionality.
- 3
Outline the steps to check if a table is level, from placing the level on the surface to adjusting the legs.
- 4
Mention common issues that arise from an unlevel table, like wobbling or uneven surfaces.
- 5
Conclude with how a well-leveled table improves user experience.
Example Answers
To level a table, I first use a spirit level placed on the surface. I check each side to see if the bubble is centered. If it's not level, I adjust the legs until the table is stable. Leveling is crucial because it prevents wobbling and ensures that items placed on the table don’t roll off.
What methods do you use to ensure precise alignment and secure fastening of table parts during assembly?
How to Answer
- 1
Start with proper measurement and marking for accurate alignment of parts.
- 2
Use jigs or fixtures to hold components in place during assembly.
- 3
Choose the right fasteners and tools, ensuring they are adequate for the material.
- 4
Perform a visual inspection to ensure alignment before final fastening.
- 5
Test the stability of the assembled parts by applying light pressure or shaking.
Example Answers
I make accurate measurements and mark where parts should align. I use a jig to hold everything securely while I fasten the pieces together, ensuring each part fits perfectly.
What ergonomic practices do you follow to ensure comfort and safety while assembling tables?
How to Answer
- 1
Maintain a proper posture with your back straight and feet flat on the ground.
- 2
Use ergonomic tools designed to minimize strain on your hands and wrists.
- 3
Adjust your work surface height to avoid bending over or reaching excessively.
- 4
Take regular breaks to stretch and change positions.
- 5
Keep frequently used items within easy reach to avoid unnecessary twisting or bending.
Example Answers
I always keep my back straight and my feet flat on the ground while working. I also adjust my workstation so the table is at waist height to minimize bending.
Have you ever been involved in assembling custom-designed tables? What additional skills does this require?
How to Answer
- 1
Share specific experiences with assembling custom tables or similar furniture.
- 2
Highlight skills like attention to detail, precision, and use of tools.
- 3
Discuss the importance of following design specifications accurately.
- 4
Mention teamwork or coordination with designers if applicable.
- 5
Emphasize problem-solving skills for custom projects.
Example Answers
Yes, I have assembled custom-designed tables for clients. This required careful attention to detail and the ability to follow precise design specifications. I also needed to be skilled with various tools, like drills and saws, to ensure everything fit together perfectly.
Explain the tools and techniques you use for precise measurements during table assembly.
How to Answer
- 1
Start with the essential tools you use like tape measure and square.
- 2
Mention techniques such as double-checking measurements and using marking tools.
- 3
Explain how you ensure accuracy through methodical approaches.
- 4
Highlight the importance of alignment and leveling during assembly.
- 5
Conclude with how these practices improve the final product quality.
Example Answers
I primarily use a tape measure and a carpenter's square for precise measurements. I always double-check my measurements before cutting any pieces, and I make marks with a pencil to ensure accuracy. For assembly, I use clamps to hold pieces in place and adjust them for alignment, which helps create a sturdier table.
Don't Just Read Table Assembler Questions - Practice Answering Them!
Reading helps, but actual practice is what gets you hired. Our AI feedback system helps you improve your Table Assembler interview answers in real-time.
Personalized feedback
Unlimited practice
Used by hundreds of successful candidates
What are the different fastening techniques you use, and how do you decide which to apply?
How to Answer
- 1
List common fastening techniques like screws, nails, glue, or dowels.
- 2
Explain the factors you consider, such as material type and application.
- 3
Discuss specific scenarios where each technique is preferred.
- 4
Mention any tools or equipment you use for fastening.
- 5
Conclude with how you ensure durability and stability.
Example Answers
I often use screws for wooden tables as they provide strong joints. For quick assembly, I prefer using dowels. I choose glue for edges where a seamless look is needed. I consider the material and the intended use when selecting a technique.
Situational Interview Questions
Imagine you find out mid-assembly that you are missing a crucial part. What steps would you take to resolve this situation?
How to Answer
- 1
Stay calm and assess the situation.
- 2
Check your workspace or assembly area for misplaced parts.
- 3
Consult the assembly instructions to verify the part's specifications.
- 4
Communicate immediately with your supervisor or team.
- 5
Identify alternative solutions, like sourcing a replacement part quickly.
Example Answers
First, I would stay calm and check my workspace carefully for the missing part. Then, I would look at the assembly instructions to ensure I really do need that part. After confirming, I would inform my supervisor and see if we have spare parts on hand or how quickly we can reorder the missing component.
What would you do if a critical tool breaks down in the middle of assembling a table?
How to Answer
- 1
Stay calm and assess the situation quickly.
- 2
Identify the specific tool that broke and its role in the assembly.
- 3
Look for immediate alternatives, such as using a backup tool or a different method.
- 4
Communicate with your team or supervisor about the situation.
- 5
Document the issue for future reference and troubleshooting.
Example Answers
If a critical tool breaks down, I would first stay calm and quickly determine what tool it is. Then, I'd see if there's a backup available to continue working or if I could modify my method to use a different tool. I'd inform my supervisor about the breakdown and document it for future reference.
Don't Just Read Table Assembler Questions - Practice Answering Them!
Reading helps, but actual practice is what gets you hired. Our AI feedback system helps you improve your Table Assembler interview answers in real-time.
Personalized feedback
Unlimited practice
Used by hundreds of successful candidates
If you notice a repetitive issue in the assembly line process, what steps would you take to suggest and implement improvements?
How to Answer
- 1
Observe the issue carefully to understand its root cause
- 2
Gather data on the frequency and impact of the problem
- 3
Discuss the issue with team members to get their insights
- 4
Propose a clear, specific solution and outline its benefits
- 5
Follow up on the implementation and make adjustments if necessary
Example Answers
I would first observe the assembly line to identify the root cause of the issue. After gathering some data on how often it occurs, I would talk to my teammates to see if they share my concerns. Then I would suggest a specific improvement, like changing a tool or adjusting a process, and explain how it could help speed things up. Finally, I would monitor the results to ensure the solution works.
How would you handle leading a team of assemblers if the original team leader is unavailable?
How to Answer
- 1
Assess the current workflow and any immediate needs.
- 2
Communicate clearly with the team to evaluate their concerns and suggestions.
- 3
Delegate tasks according to each member's strengths and capabilities.
- 4
Maintain morale by encouraging teamwork and providing support.
- 5
Ensure all safety protocols and quality standards are adhered to.
Example Answers
If the team leader is unavailable, I would first check in with the team to understand the immediate tasks and challenges. I'd then assign responsibilities based on each person's strengths to keep production steady and ensure everyone knows their role.
How would you respond to a minor safety incident that occurred during the assembly process?
How to Answer
- 1
Stay calm and assess the situation quickly.
- 2
Ensure that anyone affected receives immediate assistance if needed.
- 3
Document the incident accurately, noting the details.
- 4
Report the incident to a supervisor or safety officer.
- 5
Review safety procedures to prevent future incidents.
Example Answers
I would first make sure everyone is safe and if someone is injured, I would help them before anything else. Then, I would document what happened and report it to my supervisor to ensure it is addressed properly.
How would you handle discovering an incorrect inventory of parts required for an upcoming assembly?
How to Answer
- 1
Check the inventory records against the actual parts on hand.
- 2
Inform your supervisor immediately to discuss potential impacts.
- 3
Propose a solution to acquire the necessary parts in time.
- 4
Document the discrepancy for future reference and analysis.
- 5
Communicate with team members about any changes to avoid confusion.
Example Answers
If I discovered an incorrect inventory, I would first verify the actual parts against the records. Then, I'd inform my supervisor about the issue to assess its impact on assembly timelines. I would suggest ordering the required parts right away to meet deadlines.
If you were tasked with documenting a new assembly process, what steps would you take to ensure it is clear and comprehensive?
How to Answer
- 1
Identify key steps in the assembly process and list them sequentially
- 2
Use simple language and avoid jargon for clarity
- 3
Include visuals like diagrams or flowcharts to enhance understanding
- 4
Gather feedback from team members on the draft documentation
- 5
Review the documentation for accuracy and completeness before finalizing
Example Answers
I would start by breaking down the assembly process into clear, sequential steps. Then, I would use plain language and incorporate diagrams for clarity. After drafting, I'd seek feedback from my team to ensure nothing is missed and finalize the document after revisions.
How would you approach training a new team member on the assembly line for efficiency and accuracy?
How to Answer
- 1
Start with an overview of the assembly process to give context.
- 2
Demonstrate each step of the process clearly, focusing on key techniques.
- 3
Encourage hands-on practice with close supervision and feedback.
- 4
Introduce tools and safety measures relevant to the assembly tasks.
- 5
Gradually reduce supervision as the new member gains confidence and competence.
Example Answers
I would begin by explaining the entire assembly process, highlighting the critical steps and what to look out for. Then, I'd demonstrate how to perform each task, emphasizing efficiency techniques. After that, I'd let the new member practice while I observe and provide feedback, ensuring they understand all the safety protocols.
Suppose you are asked to assemble an unusually large order of tables in a short amount of time. How would you approach this challenge?
How to Answer
- 1
Break down the task into smaller manageable parts
- 2
Create a prioritized action plan with deadlines
- 3
Organize your workspace and assemble the necessary tools
- 4
Delegate tasks if working with a team
- 5
Stay focused and minimize distractions during the assembly process
Example Answers
I would first assess the order and divide the work into smaller batches, then create a timeline for each batch to ensure timely completion. I would gather all necessary tools and materials, set up an organized workspace, and focus on completing one batch at a time efficiently.
If a customer complains about a wobbly table that you've assembled, how would you address their concern?
How to Answer
- 1
Acknowledge the customer's concern and apologize for the inconvenience.
- 2
Ask the customer specific questions about the issue to understand it better.
- 3
Check the table for any loose screws or assembly errors immediately.
- 4
If possible, fix the issue on the spot or offer to provide a resolution later.
- 5
Ensure the customer is satisfied with the solution and thank them for their feedback.
Example Answers
I would first apologize to the customer for the inconvenience. Then, I would ask them how the table is wobbling and check the legs for any loose screws. If I find something is loose, I would fix it right away. If not, I would offer to return to their home to reassemble it properly.
Don't Just Read Table Assembler Questions - Practice Answering Them!
Reading helps, but actual practice is what gets you hired. Our AI feedback system helps you improve your Table Assembler interview answers in real-time.
Personalized feedback
Unlimited practice
Used by hundreds of successful candidates
Table Assembler Position Details
Recommended Job Boards
ZipRecruiter
www.ziprecruiter.com/Jobs/Table-AssemblerThese job boards are ranked by relevance for this position.
Related Positions
- Production Assembler
- Final Assembler
- Table Maker
- Truss Assembler
- Furniture Assembler
- Window Assembler
- Bench Assembler
- Toy Assembler
- Production Line Assembler
- Automobile Assembler
Similar positions you might be interested in.
Ace Your Next Interview!
Practice with AI feedback & get hired faster
Personalized feedback
Used by hundreds of successful candidates
Ace Your Next Interview!
Practice with AI feedback & get hired faster
Personalized feedback
Used by hundreds of successful candidates