Top 32 Bike Builder Interview Questions and Answers [Updated 2025]
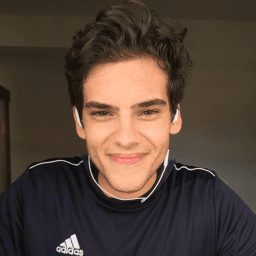
Andre Mendes
•
March 30, 2025
Preparing for a bike builder interview can be daunting, but with the right guidance, you can pedal your way to success. In this blog post, we delve into the most common interview questions for the bike builder role, providing you with insightful example answers and effective tips to craft your responses. Get ready to gear up and impress your potential employers with confidence and expertise.
Download Bike Builder Interview Questions in PDF
To make your preparation even more convenient, we've compiled all these top Bike Builderinterview questions and answers into a handy PDF.
Click the button below to download the PDF and have easy access to these essential questions anytime, anywhere: